一、高溫合金概述
高溫合金是指以Fe、Ni、Co為基,在600℃以上具有抗氧化和抗腐蝕性能,并在一定應(yīng)力作用下可以長(zhǎng)期工作的金屬材料。圖1為世界高溫合金的發(fā)展趨勢(shì)及其我國研制的合金,高溫合金既是航空發(fā)動(dòng)機(jī)的燃料室、導(dǎo)向器、渦輪葉片和渦輪盤等熱端部件、航天火箭發(fā)動(dòng)機(jī)高溫部件的關(guān)鍵材料,又是工業(yè)燃?xì)廨啓C(jī)、能源、化工等工業(yè)部門所需的高溫耐蝕部件材料,是國民經(jīng)濟(jì)中不可或缺的一類重要材料[1]。
圖1高溫合金的發(fā)展歷程[1]
目前,國際市場(chǎng)上每年消費(fèi)的高溫合金材料近30余萬噸,圖2為主要的消費(fèi)區(qū)域分布,我國高溫合金的市場(chǎng)規(guī)模年增速保持在20~30%,而全球范圍內(nèi)能夠生產(chǎn)航空航天用高溫合金的企業(yè)不超過50家,主要集中在美、英、日、德、法、俄羅斯等國家,例如,美國的GE、PW、Haynes Stellite、Inco Alloys International、Cannon-Muskegon、Westinghouse、Cabot、Martin Marietta、Standard Pressed Steel、Whittaker、Special Metal、Universal-Cyclops Steel、Howmet、Pratt & Whitney,俄羅斯的United Aircraft Company和加拿大的Mond Nickel Company等公司,具有明顯的寡頭特征。
圖2 全球高溫合金消費(fèi)區(qū)域分布(2019年)
自1956年第一爐高溫合金GH3030試煉成功,我國高溫合金的研究、生產(chǎn)和應(yīng)用已經(jīng)歷了六十多年的發(fā)展歷程。目前,在國家發(fā)展與改革委員會(huì)、工業(yè)與信息化部、中國有色金屬工業(yè)協(xié)會(huì)和國防科工局的統(tǒng)籌監(jiān)管下,我國已經(jīng)形成了一些生產(chǎn)裝備比較先進(jìn)、具有一定規(guī)模的生產(chǎn)基地和企業(yè),例如,鋼研高納、撫順特鋼、寶鋼特鋼、中國航發(fā)、萬航模鍛、萬澤股份、圖南股份等,也形成了一批具有自主創(chuàng)新研發(fā)能力的科研院所,比如,鋼鐵研究總院高溫材料研究所、北京航空材料研究院、中科院金屬所、北京航空航天大學(xué)、北京科技大學(xué)、西北工業(yè)大學(xué)等[2]。
根據(jù)中國高溫合金手冊(cè)(2012年),我國高溫合金共列入牌號(hào)194個(gè),其中,等軸鑄造鎳基合金62個(gè),鎳基變形合金43個(gè),鐵基變形合金30個(gè),金屬間化合物基20個(gè),ODS合金5個(gè),粉末冶金高溫合金3個(gè)[3]。我國高溫合金市場(chǎng)占比最大的是變形高溫合金,約為70%,其次是鑄造高溫合金,約為20%;按基體元素來說,占比最大的是鎳基高溫合金,約為整個(gè)市場(chǎng)的80%,其次是鎳-鐵基高溫合金,約為14%,鈷基高溫合金約為6%左右。
二、我國高溫合金的研究進(jìn)展
我國高溫合金經(jīng)歷了仿制、仿創(chuàng)結(jié)合到獨(dú)創(chuàng)的發(fā)展過程,通過吸取發(fā)達(dá)國家的經(jīng)驗(yàn)并結(jié)合我國的實(shí)際情況進(jìn)行自主創(chuàng)新而形成了我國的高溫合金體系。美、英等國家是以公司或廠家自成合金系統(tǒng),而我國是以國家為統(tǒng)一的系統(tǒng),并按合金制備方式、基體元素、強(qiáng)化方式的順序構(gòu)成高溫合金系列和體系。按制備方式有變形高溫合金、鑄造高溫合金(包括等軸晶、定向凝固柱晶和單晶高溫合金)、粉末冶金高溫合金、彌散強(qiáng)化高溫合金、金屬間化合物高溫材料、焊接用高溫合金絲,以及高溫合金基自潤滑材料等;在這些不同合金系列下再分為鐵基、鎳基、鈷基及鉻基高溫合金;在相同的基體下,又分為固溶強(qiáng)化型和時(shí)效強(qiáng)化型[2]。
目前,我國的高溫合金主要存在的問題和不足包括:冶金缺陷多,如黑斑、白斑、碳化物偏聚等;組織均勻性較差;雜質(zhì)元素含量高,降低了強(qiáng)度和使用壽命;成本高,再利用率低。
2019年9月22~25日在湖北黃石召開了由北京科技大學(xué)、東北大學(xué)和大冶特鋼承辦的第十四屆全國高溫合金年會(huì),集中展示了我國近年來在高溫合金研究方面取得的成果,包括變形高溫合金品種發(fā)展及其殘余應(yīng)力控制、鑄造高溫合金的研究發(fā)展、粉末高溫合金及粉末純凈化技術(shù)、金屬間化合物基高溫結(jié)構(gòu)材料的研究與應(yīng)用進(jìn)展等。
1、變形高溫合金
變形高溫合金是指通過鑄造-變形工藝生產(chǎn)的高溫合金,工作范圍為-253~1320℃,包括盤、板、棒、絲、帶、管等產(chǎn)品,例如GH128、GH4169等,廣泛應(yīng)用于航天、航空、能源、石化、核電等工業(yè)領(lǐng)域。近年來,變形高溫合金分別在工藝流程、開發(fā)新合金和新技術(shù)等方面都取得了大量的突破和應(yīng)用成果。
- 工藝流程
國內(nèi)變形高溫合金冶煉通常采用真空感應(yīng)+真空自耗兩聯(lián)或真空感應(yīng)+電渣重熔+真空自耗三聯(lián)的熔煉方式。通過對(duì)真空感應(yīng)爐內(nèi)流槽的水模擬和數(shù)值模擬,并對(duì)結(jié)構(gòu)進(jìn)行優(yōu)化設(shè)計(jì),可以改善流槽內(nèi)流場(chǎng)分布和溫度分布,從而提高鑄錠的質(zhì)量和潔凈度,如圖3所示。
圖3 真空感應(yīng)熔煉流槽優(yōu)化前后對(duì)比[4]
高溫合金鑄錠在凝固過程中會(huì)產(chǎn)生較嚴(yán)重的成分偏析,為減輕和改善成分偏析,提高材質(zhì)的均勻性,除改進(jìn)冶煉工藝外,最重要的技術(shù)措施是進(jìn)行均勻化處理,通過高溫下的長(zhǎng)時(shí)間加熱,促進(jìn)溶質(zhì)元素原子的擴(kuò)散遷移,達(dá)到枝晶干與枝晶間元素濃度差異的最小化。隨著鑄錠尺寸的擴(kuò)大,偏析情況會(huì)受到凝固冷速的影響而相應(yīng)加劇,可以通過對(duì)比不同的均勻化制度下的二次枝晶間距和偏析系數(shù),從而確定最終的均勻化溫度和時(shí)間。
為了提高GH4720Li合金鑄錠的開坯成材率以及棒材的質(zhì)量水平,通過大量熱模擬壓縮試驗(yàn),獲得并建立不同熱變形條件下的數(shù)學(xué)模擬和開裂判據(jù),從而優(yōu)化鍛造工藝參數(shù),包括逐級(jí)降溫及火次變形量合理分配。相關(guān)研究表明,快鍛開坯充分破碎鑄錠鑄態(tài)組織后,再輔之以徑鍛,可以改善棒材表面狀態(tài),提高成材率。
GH4706合金超大型渦輪盤是當(dāng)代E/F級(jí)重型燃機(jī)的核心熱端轉(zhuǎn)動(dòng)部件,鍛件直徑超過2000mm,重量達(dá)6t,是亟待國產(chǎn)化的最關(guān)鍵部件之一。該合金的成分接近于GH4169,是一種γ’相與γ”相強(qiáng)化的Fe-Ni基變形高溫合金。渦輪盤的模鍛既要實(shí)現(xiàn)盤件的熱加工成型又要實(shí)現(xiàn)組織性能控制,二者相互影響、相互制約[4]。2013年,我國自主設(shè)計(jì)研制的世界最大的8*104t模鍛液壓機(jī)(圖4)投入生產(chǎn)并試制成功了直徑為1500mm的GH4738合金渦輪盤鍛件,這為超大型GH4706合金渦輪盤的制備提供了一定的參考經(jīng)驗(yàn),但仍面臨嚴(yán)峻的挑戰(zhàn)。
圖4 “國之重器”8萬噸大型模鍛壓機(jī)
在張北江等人的研究基礎(chǔ)上[5],構(gòu)建了GH4706合金的本構(gòu)關(guān)系與顯微組織演化規(guī)律模型,應(yīng)用數(shù)值模擬技術(shù)進(jìn)行熱加工工藝優(yōu)化,最終實(shí)現(xiàn)了超大型GH4706合金渦輪盤鍛件的國產(chǎn)化,如圖5所示,性能達(dá)到了美國GE-B50A651標(biāo)準(zhǔn)的要求。
圖5 直徑為2100mm的超大型GH4706合金渦輪盤鍛件[4]
殘余應(yīng)力源自材料制備過程中內(nèi)部不均勻的塑性變形,本質(zhì)上是殘留在材料內(nèi)部的晶格畸變。在再結(jié)晶溫度附近進(jìn)行的熱變形,是難以形成高水平殘余應(yīng)力的;即便在低溫鍛造或鍛后冷卻中形成的殘余應(yīng)力通常也可以在后續(xù)的高溫固溶處理中得以釋放。因此,高溫合金盤鍛件一般在鍛造成型后需要在固溶處理后快速冷卻,以確保γ’或γ”相不發(fā)生粗化。圖6為不同的殘余應(yīng)力測(cè)試技術(shù)對(duì)應(yīng)的測(cè)試深度和分辨率。對(duì)于高溫合金盤鍛件,需要測(cè)試分析距表層10mm甚至更深的內(nèi)部殘余應(yīng)力,分辨率要求為mm級(jí),因此主要方法包括中子衍射法(neutron diffraction)、輪廓法(contour method)、深孔法(deep-hole drilling)和超聲法(ultrasonic)。
圖6 各種殘余應(yīng)力測(cè)試方法的測(cè)試深度和空間分辨率[6]
鋼鐵研究總院的畢中南等人總結(jié)了高溫合金渦輪盤鍛件內(nèi)部殘余應(yīng)力的測(cè)試方法,闡明了固溶、淬火、時(shí)效、零件加工等制備工藝過程中殘余應(yīng)力的演化規(guī)律與機(jī)制[6]。
超聲檢測(cè)作為無損檢測(cè)的一種重要方法,利用探頭發(fā)出的超聲波進(jìn)入工件內(nèi)部傳播,當(dāng)內(nèi)部存在聲學(xué)特性與基體不同的不連續(xù)或不均勻組織時(shí),在界面處就會(huì)發(fā)生傳播方式和信息的變化,從而為無損檢測(cè)和評(píng)價(jià)提供定性和定量分析的依據(jù)。范興義、林時(shí)錢等人對(duì)盤鍛件組織的晶粒尺寸與超聲雜波之間的關(guān)系進(jìn)行了充分研究,以確定影響檢測(cè)結(jié)構(gòu)的主要原因和適宜的檢測(cè)參數(shù)。
- 新合金
王慶增、陳國勝、孫文儒等人在對(duì)P強(qiáng)化和P、B復(fù)合強(qiáng)化機(jī)理研究的基礎(chǔ)上,發(fā)展了GH4169G合金,該合金在保持GH4169合金優(yōu)異的綜合性能的同時(shí),將使用溫度提高了30℃,達(dá)到680℃;并使650℃下的使用壽命提高了3倍以上;同時(shí)焊接和熱加工性能與GH4169合金相當(dāng),具有廣闊的應(yīng)用前景。
GH4169D合金是在GH4169合金的基礎(chǔ)上,通過降低Fe含量,加入固溶強(qiáng)化元素W和Co,調(diào)整Al、Ti含量及其比例,并適當(dāng)提高Nb含量和調(diào)整微量元素含量而研制成功的,成功填補(bǔ)了世界上2個(gè)最廣泛應(yīng)用高溫合金---650℃用GH4169和750℃用GH4738合金之間長(zhǎng)期存在的空白。
在依托鑄鍛工藝發(fā)展高性能渦輪盤材料方面也取得了重要進(jìn)展,相繼研制了GH4065、GH4079和GH4975等高性能變形高溫合金渦輪盤材料,特別是GH4065合金的綜合性能達(dá)到了粉末冶金材料的水平,有望為我國先進(jìn)航空發(fā)動(dòng)機(jī)熱端轉(zhuǎn)動(dòng)部件的選材提供成熟可靠的解決方案。
GH4282合金在保持一定數(shù)量的沉淀強(qiáng)化γ’相的基礎(chǔ)上,通過控制γ’相的結(jié)構(gòu)、組成和析出動(dòng)力學(xué),解決了高強(qiáng)度時(shí)效強(qiáng)化燃燒室合金中由于γ’相的大量析出導(dǎo)致的冷加工和焊接困難的問題,該合金在650~950℃范圍內(nèi)保持了極佳的高溫強(qiáng)度和熱穩(wěn)定性,同時(shí)對(duì)焊接和冷加工性能進(jìn)行了很好的平衡和優(yōu)化。
- 新技術(shù)
我國開發(fā)了氮化物強(qiáng)化高溫合金NGH5011,并針對(duì)內(nèi)生彌散氮化物強(qiáng)化合金的氮化工藝流程中涉及的N在表面的吸附溶解、在基體的均勻擴(kuò)散、反應(yīng)界面的氮化物析出等關(guān)鍵物理化學(xué)過程開展了系統(tǒng)研究工作。
鋼鐵研究總院高溫材料研究所利用增材制造技術(shù),成功制備出3D-In718合金的燃?xì)鉁u輪盤和整體葉輪,零件致密度達(dá)到99.9%,組織性能均遠(yuǎn)優(yōu)于鑄件,室溫、高溫拉伸強(qiáng)度、塑性和持久性能均可滿足鍛件標(biāo)準(zhǔn)。
此外,采用電渣重熔連續(xù)定向凝固冶煉+3D鍛造制坯+等溫鍛造的新型鑄鍛工藝技術(shù)成功制備了變形FGH4096合金渦輪盤。
2、鑄造高溫合金
鑄造高溫合金具有較寬的成分范圍,根據(jù)使用溫度又分為三類:在-253~650℃使用的等軸晶鑄造高溫合金,如K4169;在650~950℃使用的等軸晶鑄造高溫合金,如K419;以及在950~1100℃使用的定向凝固柱晶鑄造高溫合金,如DD402。航空發(fā)動(dòng)機(jī)機(jī)匣是典型的中低溫條件下使用的等軸晶高溫合金鑄件,結(jié)構(gòu)復(fù)雜化、尺寸精確化和薄壁輕量化是發(fā)展趨勢(shì),從而精密成形和凝固組織的協(xié)同控制是急需解決的重大技術(shù)難題。
等軸晶鎳基高溫合金主要以γ相為基體,通過添加Al、Ti、Nb和Ta等元素形成體積分?jǐn)?shù)可達(dá)70%的γ’相或γ”相進(jìn)行強(qiáng)化,并以C、B和Zr作為晶界強(qiáng)化元素在晶界偏聚或形成碳化物或硼化物來提高合金的綜合性能。等軸晶鑄造高溫合金的發(fā)展方向主要為:根據(jù)合金化理論和冶金原理,結(jié)合計(jì)算機(jī)模擬技術(shù)設(shè)計(jì)具有良好綜合性能的新型材料;針對(duì)不同合金的用途,通過對(duì)現(xiàn)有合金成分的調(diào)整來獲得優(yōu)異特定性能;改進(jìn)和提高合金的冶煉工藝,提高合金的冶金質(zhì)量;通過新型工藝技術(shù)改善鑄件的質(zhì)量和力學(xué)性能。
采用傳統(tǒng)的“經(jīng)驗(yàn)試錯(cuò)”方法,成本高、周期長(zhǎng)、難度大,基于計(jì)算材料學(xué)、大數(shù)據(jù)處理、機(jī)器學(xué)習(xí)、高通量試驗(yàn)等手段開展合金成分設(shè)計(jì)將會(huì)成為一大趨勢(shì)。基于電子空位理論、結(jié)合次數(shù)和合金元素的d軌道能發(fā)展和完善的相計(jì)算可以模擬和預(yù)測(cè)合金中TCP相的析出規(guī)律,而如何建立合金成分與高性能之間的量化關(guān)系是目前單晶合金設(shè)計(jì)的關(guān)鍵。傅恒志、介子奇等人研究了K4169高溫合金的熔體凝固特性,獲得了熔體過熱溫度對(duì)形核過冷度的影響規(guī)律,如圖7所示,并進(jìn)一步驗(yàn)證了熔體超溫處理可明顯細(xì)化晶粒尺寸、改善析出相的形貌和分布,有效減輕合金元素偏析,從而改善鑄態(tài)高溫合金的綜合力學(xué)性能[7]。
圖7 熔體過熱溫度對(duì)K4169高溫合金形核過冷度的影響[7]
利用JMatPro、Thermal-calc和Panda軟件可以較準(zhǔn)確地計(jì)算出不同成分的鎳基高溫合金的初熔溫度、合金密度,以及不同平衡態(tài)下的相組成及含量,并預(yù)測(cè)出熱處理窗口和糊狀區(qū)間等,在此基礎(chǔ)上,制定合適的熱力學(xué)判據(jù),篩選出滿足要求的合金成分進(jìn)行試驗(yàn)測(cè)試,可以節(jié)省合金的開發(fā)時(shí)間和成本。
通過鑄件成型模擬技術(shù),可以模擬充型過程中的溫度場(chǎng)分布,從而合理設(shè)計(jì)冒口和澆注系統(tǒng),優(yōu)化澆注工藝參數(shù),并預(yù)測(cè)縮孔、冷隔、欠鑄和縮松等缺陷及其冷卻后的殘余應(yīng)力,為實(shí)際生產(chǎn)提供理論指導(dǎo)。目前,鑄件成形模擬技術(shù)的發(fā)展已經(jīng)較為成熟,典型的商用模擬軟件有:ProCAST、MAGMA、AFSolid和PAM-CAST等。柳百成等人提出了利用計(jì)算機(jī)技術(shù)改造鑄造行業(yè),在鑄造過程宏、微觀模擬仿真領(lǐng)域開展了大量研究,并開發(fā)了一系列工程應(yīng)用的數(shù)值模擬軟件[8]。
常見的組織模擬方法有:第一性原理、分子動(dòng)力學(xué)法、Monte Carlo、元胞自動(dòng)機(jī)法、相場(chǎng)法、有限元等。例如,將蠕變損傷的晶體模型耦合到相場(chǎng)模型中,可實(shí)現(xiàn)蠕變3個(gè)階段的組織演化和性能的同步模擬,得到蠕變組織演化過程及蠕變曲線,如圖8所示,這為高溫合金蠕變模擬提供了新的途徑,有利于以性能為導(dǎo)向的微觀組織優(yōu)化模擬工作的開展。
圖8 相場(chǎng)模擬得到的950℃、300MPa蠕變條件下γ’相的演化過程[7]
單晶高溫合金消除了晶界,具有優(yōu)異的高溫蠕變、抗氧化和抗腐蝕性能,其研發(fā)起始于20世紀(jì)70年代的美國Pratt & Whitney公司,自20世紀(jì)80年代PWA1480單晶高溫合金成功研制和應(yīng)用以來,國外單晶合金迅猛發(fā)展,在2000年左右研制了第四代單晶合金。從第一代發(fā)展到第四代單晶高溫合金,工作溫度已經(jīng)提高到1827℃,遠(yuǎn)高于初熔溫度(1280~1330℃),同時(shí)Re、Ru等貴金屬元素的含量不斷增加,成本也越來越高。
我國單晶合金的研制起步較晚,且多以仿制為主。近年來,我國單晶高溫合金研制與應(yīng)用取得了顯著進(jìn)展,并自主研制了第三代單晶合金DD33、DD9以及第四代單晶合金DD91、DD15等,已經(jīng)具備了單晶高溫合金新材料、新工藝自主研發(fā)能力,特別是在軍民融合相關(guān)政策的引導(dǎo)和推動(dòng)下,出現(xiàn)了一批高溫合金相關(guān)的民營企業(yè),其中大多數(shù)聚焦于單晶高溫合金母合金和單晶葉片的生產(chǎn)。
目前,單晶高溫合金的成分設(shè)計(jì)方面的研究主要集中在英、德和日本等國家的大學(xué)和科研院所,且設(shè)計(jì)空間越來越小,提高綜合性能的難度越來越大,國外根據(jù)實(shí)際用途開始研發(fā)各種“定制”合金。例如,GE公司為了降低第二代單晶合金中Re含量,發(fā)展了性能接近Rene? N5的Rene? N515合金(1.5%Re),并逐漸替代Rene? N5應(yīng)用于航空發(fā)動(dòng)機(jī)渦輪葉片。
晶粒細(xì)化可大幅度提高鑄件低周疲勞性能,減少力學(xué)性能的分散度,改善機(jī)械加工性能。其主要機(jī)制是促進(jìn)形核和抑制晶粒長(zhǎng)大,常用的方法有熱控法(FGP、Grainix法)、動(dòng)力學(xué)法(鑄型攪動(dòng)、電磁振動(dòng)和脈沖電流等)、化學(xué)法(細(xì)化劑)等。北京航空材料研究院、北京航空航天大學(xué)等對(duì)單晶高溫合金的低周疲勞、高周疲勞、蠕變性能等方面都做了大量的分析研究[9,10]。此外,在一些新型工藝如反重力鑄造技術(shù)、增材制造等方面也取得了一定的進(jìn)展。
3、粉末高溫合金
圖9為國內(nèi)外先后研制出的四代粉末高溫合金,我國目前已研制出以FGH4095合金為代表的第一代高強(qiáng)型粉末高溫合金和第二代損傷容限型FGH4096合金,近年來正在研制高強(qiáng)損傷容限第三代粉末高溫合金,并對(duì)第四代粉末高溫合金進(jìn)行了初步探索研究[11]。
圖9 國內(nèi)外粉末高溫合金的發(fā)展[11]
高品質(zhì)高溫合金粉末,是先進(jìn)航空發(fā)動(dòng)機(jī)粉末渦輪盤研制和生產(chǎn)的基礎(chǔ)和保障。目前高溫合金粉末制備主要有Ar氣霧法制粉(AA粉)和等離子旋轉(zhuǎn)電極法制粉(PREP粉)2種方法。北京航空材料研究院的張國慶課題組等人開展了一系列Ar氣霧化高溫合金粉末的制備裝置和技術(shù),用以制備粉末高溫合金渦輪盤件等熱端部件,同時(shí)也為3D打印增材制造提供原材料。他們分別在合金霧化過程、制粉過程粒度控制(圖10)、O含量控制、非金屬夾雜控制等方面取得了一定的成果和經(jīng)驗(yàn)。
圖10 不同粒徑粉末顆粒軌跡圖[11]
4、金屬間化合物基高溫合金
金屬間化合物是由2種或2種以上金屬元素或金屬元素與類金屬元素按照一定原子比組成的化合物。共價(jià)鍵和金屬鍵的共存使得金屬間化合物在較長(zhǎng)范圍內(nèi)存在長(zhǎng)程有序的超晶格結(jié)構(gòu)。在高溫下,金屬間化合物的位錯(cuò)遷移率相對(duì)降低,從而具有較高的高溫強(qiáng)度。比較典型的有Ti-Al、Ni-Al、Nb-Si,它們有著優(yōu)異的高溫強(qiáng)度和較低的密度,但也存在室溫?cái)嗔秧g性低、高溫抗氧化性差等問題,使其在應(yīng)用上受到限制,也成為該領(lǐng)域研究的難點(diǎn)和重點(diǎn)。
近年來,我國在金屬間化合物基高溫合金材料的基礎(chǔ)研究與工程應(yīng)用方面取得了重要的進(jìn)展,以TiAl、Ti3Al、Ti2AlNb、Ni3Al基合金為代表,在性能和工藝方面進(jìn)步顯著,并研發(fā)出一些具有自主知識(shí)產(chǎn)權(quán)的新型高溫結(jié)構(gòu)材料,為我國高性能航空發(fā)動(dòng)機(jī)的研制做出了重要的貢獻(xiàn)。Nb-Si基合金在凝固工藝和抗氧化涂層的基礎(chǔ)研究方面也取得了顯著的進(jìn)展,并逐漸向?qū)嵱没咏@纾赥i-Al系金屬間化合物高溫合金方面取得的重要進(jìn)展有:新一代高鈮含量TiAl合金成分設(shè)計(jì)與組織、性能關(guān)系研究發(fā)現(xiàn)新的規(guī)律和機(jī)制;二代TiAl合金工程應(yīng)用取得突破;Ti3Al和Ti2AlNb合金工藝進(jìn)步顯著,應(yīng)用范圍不斷擴(kuò)大[12]。
三、高溫合金專家簡(jiǎn)介
師昌緒——中國高溫合金材料的開拓者
師昌緒(1920-2014),1957年負(fù)責(zé)主持我國高溫合金方面的工作,并研制出我國第一個(gè)鐵基高溫合金GH135,領(lǐng)導(dǎo)研制出我國第一代空心氣冷鑄造鎳基高溫合金M17渦輪葉片,獲得國家級(jí)獎(jiǎng)勵(lì)10余項(xiàng)。1980年當(dāng)選中國科學(xué)院院士,1994年當(dāng)選中國工程院院士,1995年當(dāng)選第三世界科學(xué)院院士,2010年榮獲國家最高科學(xué)技術(shù)獎(jiǎng),2015年被評(píng)為感動(dòng)中國2014年度人物。他參與創(chuàng)辦或主編了Journal of Materials Science and Technology、能源材料、中國科學(xué)基金、自然科學(xué)進(jìn)展、金屬學(xué)報(bào)等期刊。
胡壯麒
胡壯麒(1929-2016),長(zhǎng)期從事高溫合金的研制及亞穩(wěn)態(tài)新材料和新工藝的研究,為我國科技和國防事業(yè)做出了重要貢獻(xiàn)。他先后在發(fā)動(dòng)機(jī)一級(jí)渦輪葉片K17G鑄造鎳基合金、抗熱腐蝕DZ38G定向凝固鎳基高溫合金、單晶鎳基高溫合金非平衡凝固行為等方面都有重大科研成果,并發(fā)展了一系列性能優(yōu)異的新材料,包括高溫合金、定向結(jié)晶和單晶合金、金屬間化合物和亞穩(wěn)態(tài)材料。1985年獲得國家科技進(jìn)步獎(jiǎng)一等獎(jiǎng),1986年獲得國家科技進(jìn)步獎(jiǎng)二等獎(jiǎng),1995年當(dāng)選為中國工程院院士,2003年獲何梁何利基金科學(xué)與技術(shù)進(jìn)步獎(jiǎng),2004年被中國金屬學(xué)會(huì)高溫合金學(xué)術(shù)委員會(huì)授予杰出貢獻(xiàn)獎(jiǎng)。
仲增墉
鐘增墉,1961年開始從事高溫合金研究和制造工作,負(fù)責(zé)研制成功了一系列難變形高溫合金關(guān)鍵新材料,其中渦噴六發(fā)動(dòng)機(jī)渦輪葉片用GH37鎳基高溫合金,使60年代初國家急需軍工材料立足于國內(nèi),獲得國防工辦和冶金部的嘉獎(jiǎng);渦噴十三發(fā)動(dòng)機(jī)用高熱強(qiáng)(950℃)難變形鎳基高溫合金GH220獲冶金部科技進(jìn)步一等獎(jiǎng);成功研制了GH118(950℃)、GH38A、GH43、GH49、GH33和GH527等航空航天用高溫合金;并首創(chuàng)了電渣熔煉高溫合金工藝,達(dá)到了當(dāng)時(shí)的國際水平;在國際上首先提出了高溫合金的鎂微合金化及其理論,改善了高溫合金材料的性能;高溫合金中彎曲晶界的形成及其作用研究、高熱強(qiáng)合金中TCP相析出、影響及控制的研究等都達(dá)到了較高水平。
傅恒志
傅恒志(1929~),材料及冶金學(xué)專家。1988年,他創(chuàng)建了中國國內(nèi)唯一的凝固技術(shù)國家重點(diǎn)實(shí)驗(yàn)室。1993年,成為中國首批入選由世界著名科學(xué)家、教育家組成的國際高校科學(xué)院院士。1995年,當(dāng)選為中國工程院院士,并同年當(dāng)選俄羅斯宇航科學(xué)院外籍院士。2013年,獲得第三屆中國機(jī)械工程學(xué)會(huì)“中國鑄造終身成就獎(jiǎng)”。先后獲得國家科技進(jìn)步二等獎(jiǎng)1項(xiàng),國家發(fā)明獎(jiǎng)3項(xiàng),國家優(yōu)秀教學(xué)成果二等獎(jiǎng)1項(xiàng),省部級(jí)獎(jiǎng)12項(xiàng),發(fā)表論文1100余篇,出版專著7本。
黃伯云
黃伯云,1999年當(dāng)選為中國工程院院士,2007年當(dāng)選為發(fā)展中國家科學(xué)院院士,“十五”國家863計(jì)劃新材料領(lǐng)域?qū)<椅瘑T會(huì)主任,兼任中國材料研究學(xué)會(huì)理事長(zhǎng)。他領(lǐng)導(dǎo)創(chuàng)建了粉末冶金國家重點(diǎn)實(shí)驗(yàn)室、粉末冶金國家工程中心、輕質(zhì)高強(qiáng)國防科技重點(diǎn)實(shí)驗(yàn)室以及有色金屬先進(jìn)結(jié)構(gòu)材料與制造協(xié)同創(chuàng)新中心等一系列創(chuàng)新平臺(tái),并獲得留學(xué)回國人員成就獎(jiǎng)、何梁何利科學(xué)與技術(shù)進(jìn)步獎(jiǎng)、全國國防科技工業(yè)系統(tǒng)先進(jìn)工作者、中青年有突出貢獻(xiàn)專家、全國杰出專業(yè)技術(shù)人才、“CCTV2005年感動(dòng)中國”十大人物、全國勞動(dòng)模范、全國優(yōu)秀共產(chǎn)黨員等榮譽(yù)稱號(hào)。
柳百成
柳百成(1933.2~ ),鑄造及材料工程專家。他長(zhǎng)期從事用信息技術(shù)提升鑄造行業(yè)技術(shù)水平及提高鑄造合金性能的研究,致力于振興中國制造業(yè)及推廣先進(jìn)制造技術(shù)等戰(zhàn)略研究。曾主持及參加多項(xiàng)國家重大科技項(xiàng)目、973項(xiàng)目,先后獲部委級(jí)科技進(jìn)步一等獎(jiǎng)、二等獎(jiǎng)等十余項(xiàng)獎(jiǎng)勵(lì),國外獎(jiǎng)勵(lì)2項(xiàng)及發(fā)明專利2項(xiàng)。1999年當(dāng)選為中國工程院院士,2002年獲光華工程科技獎(jiǎng),2011年、2015年先后獲得中國機(jī)械工程學(xué)會(huì)中國鑄造杰出貢獻(xiàn)獎(jiǎng)及中國鑄造終身成就獎(jiǎng),2017年被評(píng)為海歸中國夢(mèng)年度人物獎(jiǎng)。
干勇
干勇,1947年8月出生,冶金材料專家。1994年至今任連鑄技術(shù)國家工程研究中心主任,2001年4月至今任鋼鐵研究總院院長(zhǎng),同年當(dāng)選為中國工程院院士。他長(zhǎng)期從事冶金、新材料及現(xiàn)代鋼鐵流程技術(shù)研究,是我國材料、冶金、現(xiàn)代鋼鐵流程的學(xué)術(shù)帶頭人之一。先后獲國家科技進(jìn)步二等獎(jiǎng)2項(xiàng)及省部級(jí)科技進(jìn)步一等獎(jiǎng)5項(xiàng),獲準(zhǔn)專利24項(xiàng),其中發(fā)明專利15項(xiàng),發(fā)表論文140余篇,出版著作3部。
宮聲凱
宮聲凱(1956.7~),北京航空航天大學(xué)教授,兼任中國腐蝕學(xué)會(huì)副理事長(zhǎng)、中國金屬學(xué)會(huì)高溫材料分會(huì)副理事長(zhǎng)。他長(zhǎng)期從事新型金屬間化合物基合金、單晶葉片及熱障涂層研究。發(fā)明了新型高承溫、低密度低錸Ni3Al基單晶合金和超高溫?zé)嵴贤繉樱谎兄瞥龅某瑲饫鋯尉~片,支撐了我國新型發(fā)動(dòng)機(jī)研制,相關(guān)成果獲得包括國家技術(shù)發(fā)明一等獎(jiǎng)在內(nèi)的省部級(jí)以上科技獎(jiǎng)勵(lì)8項(xiàng),授權(quán)發(fā)明專利80余項(xiàng),發(fā)表SCI論文近300篇。
參考文獻(xiàn)
[1] 師昌緒、鐘增墉,我國高溫合金的發(fā)展與創(chuàng)新[J],金屬學(xué)報(bào),2010,45(11):1281-1288
[2] 中國高溫合金50年1956~2006,師昌緒、仲增墉主編,冶金工業(yè)出版社,2006年
[3] 中國高溫合金手冊(cè),中國金屬學(xué)會(huì)高溫材料分會(huì),中國標(biāo)準(zhǔn)出版社,2012年
[4] 杜金輝、呂旭東、董建新、孫文儒、畢中南、趙光普、鄧群、崔傳勇、馬惠萍、張北江,國內(nèi)變形高溫合金研制進(jìn)展[J],金屬學(xué)報(bào),2019,55(9):1116-1134
[5] 張北江、黃爍、張文云、田強(qiáng)、陳石富,變形高溫合金盤材及其制備技術(shù)研究進(jìn)展[J],金屬學(xué)報(bào),2019,55(9):1095-1115
[6] 畢中南、秦海龍、董治國、王相平、王鳴、劉永泉、杜金輝、張繼,高溫合金盤鍛件制備過程殘余應(yīng)力的演化規(guī)律及機(jī)制[J],金屬學(xué)報(bào),2019,55(9):1161-1176
[7] 張軍、介子奇、黃太文、楊文超、劉林、傅恒志,鎳基鑄造高溫合金等軸晶凝固成形技術(shù)的研究和進(jìn)展[J],金屬學(xué)報(bào),2019,55(9):1145-1160
[8] 許慶彥、楊聰、閆學(xué)偉、柳百成,高溫合金渦輪葉片定向凝固過程數(shù)值模擬研究進(jìn)展[J],金屬學(xué)報(bào),2019,55(9):1176-1186
[9] 張健、王莉、王棟、謝光、盧玉章、申健、樓瑯洪,鎳基單晶高溫合金的研發(fā)進(jìn)展[J],金屬學(xué)報(bào),2019,55(9):1077-1095
[10] 李嘉榮、謝洪吉、韓梅、劉世忠,第二代單晶高溫合金高周疲勞行為研究[J],金屬學(xué)報(bào),2019,55(9):1196-1205
[11] 張國慶、張義文、鄭亮、彭子超,航空發(fā)動(dòng)機(jī)用粉末高溫合金及制備技術(shù)研究進(jìn)展[J],金屬學(xué)報(bào),2019,55(9):1133-1145
[12] 宮聲凱、尚勇、張繼、郭喜平、林均品、趙希宏,我國典型金屬間化合物基高溫結(jié)構(gòu)材料的研究進(jìn)展與應(yīng)用[J],金屬學(xué)報(bào),2019,55(9):1067-1177
免責(zé)聲明:本網(wǎng)站所轉(zhuǎn)載的文字、圖片與視頻資料版權(quán)歸原創(chuàng)作者所有,如果涉及侵權(quán),請(qǐng)第一時(shí)間聯(lián)系本網(wǎng)刪除。
-
標(biāo)簽: 高溫合金, 殘余應(yīng)力, 單晶高溫合金
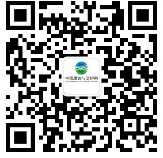
官方微信
《中國腐蝕與防護(hù)網(wǎng)電子期刊》征訂啟事
- 投稿聯(lián)系:編輯部
- 電話:010-62316606-806
- 郵箱:fsfhzy666@163.com
- 中國腐蝕與防護(hù)網(wǎng)官方QQ群:140808414