汽車涂裝一般指轎車、客車、載貨汽車等各種類型汽車車身以及零部件的涂裝。汽車作為現代化的交通工具之一,其外表面90%以上是涂漆面,涂層質量(外觀、鮮映性、光澤、顏色等)的優劣是人們對汽車質量的直觀評價,因此它是直接影響汽車人市場的競爭力。另外,涂裝質量也是提高汽車產品的耐腐蝕性并延長使用壽命的主要措施之一,所以,無論是汽車制造還是汽車維修行業,都將汽車表面涂裝列為重要的工作。
二 行業資訊
汽車等涂裝生產流水線如使用溶劑涂料產生大量VOC,還有重金屬問題。歐洲汽車涂裝用覆膜技術替代涂裝,涂裝盡量采用水性與粉末涂料,遠低于歐洲排放法規要求。一些先進的汽車涂裝生產線進一步提出零VOC排放的概念。
據專家介紹,由于伴隨著全球對環保涂料的要求越來越高,更為環保的水性和粉末涂料已經成為涂料市場熱門產品,其中,全球對環保潮流的要求是推動粉末涂料發展的一大動力,由于生產廠家都在尋找降低產品VOC的途徑,因此在某些領域粉末涂料自然替代了液體涂料。粉末涂料的VOC含量低,清除容易,過噴的涂料可回收再利用;施工后涂膜基本上不產生針孔,通常比液體涂料容易施工,形成的涂膜耐久性好。環保優勢和技術優勢是粉末涂料替代傳統溶劑型涂料的關鍵所在。
另一方面,水性涂料也在虎視眈眈,近年來,涂料中可揮發的有機化合物對于環境及人體的危害日益引起人們的關注,而水性涂料相對于傳統溶劑型涂料能極大地減少VOC的排放,可有效降低對環境的影響,還有助于降低職業病發生的潛在概率,減少火災風險和儲存隱患,簡化及降低企業通風、水處理等方面的流程及成本等,這一切需求也都為水性涂料的發展奠定了一定基礎。
“2010年后,隨著中國軌道車輛產品逐步打入國際市場,一些國外用戶尤其是發達國家的用戶紛紛要求車輛涂裝采用水性涂料。預計到2020年,國內鐵路客車、城鐵客車和在我國境內制造的國際軌道車輛將達到近8萬輛,對涂料的需求量較大。目前這部分的市場份額為溶劑型涂料81267噸、稀釋劑23424噸,水性漆只占12.3%,市場潛力很大。”長春軌道客車股份有限公司高級工程師郝博介紹說。2007年該公司首次在輕軌車上采用雙組分環氧底漆、雙組分聚氨酯中涂漆、聚氨酯面漆等系列水性涂料進行整車涂裝,達到了預期效果。
據專家介紹,中國的涂料品牌想要突破層層強手,進入世界的排名行列,還是需要一段的時間和努力。在中國,更為環保的粉末涂料和水性涂料或將替代傳統溶劑型涂料地位,未來似乎很有希望。
三 涂裝的目的及特點
(一)汽車涂裝的目的:
1、保護作用
從主體上講制造汽車90﹪用的是鋼材、假設不給汽車涂漆的話大家可想而知。汽車的壽命就大大折扣、所以說汽車涂漆的必要性。涂膜可以保護愛車不受到腐蝕、隨著新型材料上市涂膜保護的作用越來越大比如:高耐劃傷性能、彈性、耐污染性等等。
2、美觀作用
從漆膜漂亮的外觀、美澤華麗的柔和、多彩多樣追趕潮流的氣息。從上世紀50年代從單一顏色至今。汽車油漆從素色漆—金屬漆—珍珠漆也有了不同的視角改觀、從而提升汽車美觀、外觀美給予人美感。
3、價值作用
隨著汽車誕生人類對汽車顏色不斷要求產生價值觀、包括不同油漆品種也出現了涂裝工藝技術上的大改進。比如去4S站買車同樣的車型油漆品種不一價位有所變動一般金屬漆、珍珠漆比素色漆要高1000~3000元不等還要看汽車品牌價值。
4、識別作用
廣義講什么事物都有區分、汽車車身的顏色特種體現不同的用途。包括國際上選用色彩來區別事物。列如部隊用的軍車、工程車、消防車等等。
(二)汽車涂裝的特點
汽車涂裝的目的是使汽車具有優良的外觀和裝飾性、保光保色性、耐腐蝕性、延長其使用年限,因而具有鮮明的特點:
(1)汽車涂裝屬于高級保護性涂裝,所得涂層必須具有極優良的耐腐蝕性、耐候性、耐酸耐堿性,以及耐雜物等的侵蝕作用,有廣泛的適應性。
(2)汽車涂裝(主要是汽車車身的涂裝)又屬于高級裝飾性涂裝,必須進行精心的涂裝設計和具備良好的涂裝環境及條件,才能使涂層具有良好的裝飾性。汽車的裝飾性主要靠涂裝,取決于涂裝質量,并直接影響汽車的商品價值。
(3)汽車涂裝是最為典型的工業涂裝,必須選用合理、高效的前處理方法,干燥方法及工藝準備。
(4)汽車涂裝為多涂層涂裝體系,各單一涂層的涂裝質量和工藝控制尤其重要。
四 汽車用涂料
汽車用涂料主要是指涂裝和修補轎車、載重汽車、客車和其他改裝汽車等所用的涂料及輔助材料。汽車用涂料用量大,品種多,且具備獨特的施工性能和漆膜性能,目前已經成為一種專用涂料。汽車用涂料一般可按汽車上的使用部位及涂層所起的功能來分類:(1)表面處理用材料:主要包括清洗劑和磷化處理劑;(2)汽車用底漆;(3)汽車用中涂;(4)汽車用面漆;(5)輔助材料:包括溶劑、固化劑、膩子、拋光蠟等。
(一) 汽車用底漆
底漆是直接涂飾在經過表面處理的工件表面上的第一道漆,它是整個涂層的基礎。其特點為:
(1)對經過表面處理的工件表面應有很好的附著力,所形成的底漆漆膜應具有極好的機械強度。
(2)底漆本身必須是抗腐蝕劑,底漆涂層必須具有極好的耐腐蝕性、耐水性和抗化學性。
(3)與中間涂層或面漆涂層的配套良好。
(4)能適應汽車涂裝工藝的流水線生產特點,具有良好的施工性能。
汽車用底漆主要分溶劑型底漆和電泳底漆(水性底漆)。客車用底漆主要是溶劑型底漆,以環氧酯、環氧聚酰胺、環氧聚氨酯涂料為主,要求耐鹽霧性能500h以上。水性底漆以陰極電泳涂料為主,主要用于轎車、微型車燈車身的涂裝。
(二) 汽車用中間涂層
汽車用中間涂層主要指膩子和中涂。
1 膩子
膩子是一種專供填平表面用的含顏填料較多的涂料,刮涂在底漆涂層上。刮膩子僅能提高工件表面的平整度,起填充作用;但膩子涂層易老化、開裂、脫落,成膜后內部孔徑較多,易造成中涂和面漆下滲,影響外觀,再加上手工涂刮和打磨,勞動強度大。只有通過提高加工技術和管理水平來提高表面的平整度,提高汽車最終的涂裝效果。
目前一般采用不飽和聚酯膩子(俗稱原子灰)。
2 中涂
中涂是涂面漆前的最后一道中間涂層,它的漆基含量介于底漆和面漆之間,涂膜是光亮和半光亮。
中涂的功能:(1)增強底漆和面漆之間的結合力;(2)增加涂層總厚度,提高豐滿度;(3)提高底面漆的耐腐蝕能力和耐候性;(4)填補底材表面的微小缺陷;(5)提高面漆的裝飾性能。
由于汽車工業對汽車漆涂層的高硬度、高裝飾性和高耐候性、抗劃痕性的要求,對中涂的要求也越來越高,因而中涂漆在提高復合涂層的外觀裝飾性、耐石擊性和耐候性等方面起到了很大的作用。
中涂漆一般采用丙烯酸、聚酯樹脂體系,為了提高中涂漆的耐石擊性,歐美國家先后開發了聚酰胺封閉異氰酸酯、聚羥基化學物和乙酰乙酯混合物封閉異氰酸酯等耐石擊涂料。
3 汽車用面漆
汽車面漆是汽車多層涂層中最后涂層用的涂料。它直接影響汽車的裝飾性、耐候性、保光保色性、耐化學品性、抗沾污性及外觀,因而對汽車用面漆的質量要求非常高。
A. 汽車用面漆選用條件
根據汽車的使用條件,產品品種和設計要求,在選擇汽車用面漆或制定面漆技術條件時,應從以下幾個方面來考慮:
(1)外觀:符合生產條件的漆膜厚度和硬度、光澤、流平性、豐滿度、清晰度、色彩鮮明度,以保證汽車車身具有高質量的協調的外形。
(2)硬度和抗崩裂性:面漆漆膜應堅硬,具有足夠的硬度,以防止涂層在汽車行駛中由于路面砂石的沖擊和磨擦時產生劃痕。一般烤漆130-140℃/30min,雙組分自干或低溫70-80℃/30-60min。
(3)耐候性:汽車用面漆涂膜在熱帶地區長期曝曬(≥12月),只允許輕微的失光和變色,不得有起泡、開裂和銹點。人工老化1000h,面漆失光率≤15%,變色或粉化≤1級。
(4)耐潮濕性和防腐蝕性:面漆與底漆、中涂配套后,浸泡在水中或暴露在相對濕度高的空氣中,面漆層不起泡、不變色、不失光。雙組分丙烯酸聚氨酯涂料中面配套后,40℃/10d,面漆漆膜基本無變化。
(5)耐化學品性:主要是面漆與底漆、中涂配套后,具有一定的耐酸、堿、機油、汽油、剎車液、冷凍液、肥皂液和各種洗滌劑的能力。
(6)施工性能:要求汽車面漆具有良好的施工性能,在裝飾性要求高的場合,面漆干透后應具有優良的拋光性能;面漆液應具有較好的重涂性和修補性。
(7)耐高溫性、抗寒性:汽車面漆應能適應高寒高熱地區的氣候條件要求。丙烯酸聚氨酯汽車面漆一般均能通過-40℃至50℃的溫變試驗,滿足用戶的要求。
B. 國內外汽車用面漆樹脂品種
目前各國使用的汽車用面漆,均以丙烯酸樹脂、聚酯樹脂為主,鑒于客車涂料特有的要求,國內外均采用丙烯酸聚氨酯汽車面漆。它兼有丙烯酸涂料和聚氨酯涂料各自獨特的優點,是客車涂料的首選涂料品種。其特點如下:
(1)汽車用丙烯酸涂料的特點
a.耐候性優良,保光保色性好,在紫外光的照射下不易發生斷鏈,分解或氧化等化學變化。漆膜不黃變,其顏色和光澤可以長期保持恒定;
b.樹脂是無色透明,所以制得的清漆漆膜完全透明無色。制造淺色漆是色澤鮮艷,能制得純白色漆膜;
c→.可制得中性涂料,與鋁銀漿、珠光顏料等無反應,因而能制得色澤非常鮮艷的金屬閃光漆,且耐候性特別優異;
d.耐化學品性好,可耐一般的酸、堿、醇、汽油和機油;
e.耐熱性、耐寒性和耐溫變性優良;
f.優良的機械性能和附著力,漆膜堅硬;
g.具有優良的拋光性能,能制得平整光滑、清晰光亮的漆膜外觀。因而丙烯酸涂料是一種優良的裝飾性涂料。
國外汽車用金屬閃光漆幾乎都采用丙烯酸樹脂體系,美國通用、福特和克萊斯勒三家汽車公司及其國外分公司所采用的汽車面漆也是以丙烯酸樹脂為主。
(2)汽車用聚氨酯涂料的特點
a.硬度高,具有機械耐磨性和韌性;
b.兼有保護和裝飾性;
c.漆膜附著力強,對多種物面均有優良的附著力;
d.漆膜具有彈性,而且可調;
e.漆膜具有優良的耐化學品性,耐酸堿性,能低溫固化,節省能源;
f.光澤度高,耐候性好,漆膜耐溫變性好,可與許多樹脂混溶,制成各種改性圖來哦,大幅度提高和改進涂料的性能。
綜上所述,丙烯酸聚氨酯涂料正是綜合了丙烯酸樹脂涂料和聚氨酯涂料的各自優點,以滿足汽車涂料的要求。
五 涂裝工藝
汽車本身的涂裝工藝屬于裝飾、保護性多層涂裝,是汽車涂裝中工序最多、涂裝質量要求最高的涂裝工藝。
(一) 常用的涂裝工藝體系
常用的涂裝工藝體系按涂層來分可分為二涂層體系(底漆+面漆);三涂層體系(底漆+中涂+面漆或金屬閃光漆/罩光清漆);四涂層體系(底漆+中涂+面漆+罩光清漆,適用于對涂裝要求更高的豪華車)。
一般最常見的是三涂層體系,裝飾性要求高的轎車車身、大客車和旅游車車身、載重汽車的駕駛室等一般采用三涂層體系。
按干燥條件來劃分,可分為烘干體系和自干體系。烘干體系適用于大批量流水線生產的汽車涂裝;自干體系適用于小批量生產的汽車涂裝和大型特種汽車車身涂裝。
大型客車、旅行車車身一般涂裝工藝如下:
前處理(除油,除銹,清洗,表調)⇒磷化⇒清洗干燥⇒底漆⇒干燥⇒膩子粗刮⇒(干燥,打磨,擦凈)⇒膩子細刮(干燥,打磨,擦凈)⇒中涂(干燥,打磨,擦凈)⇒修整(快干中涂,干燥,打磨,擦凈)⇒面漆(干燥或罩光)⇒分色(干燥)
(二) 漆前表面處理工藝
為了獲得優質涂層,涂漆前需對被涂物表面進行的前處理工作,均稱為漆前表面處理。漆前表面處理是涂裝工藝的基礎,它對整個涂層的質量有著很大的影響,主要包括表面清理(除油,除銹,除塵等)和磷化處理兩個部分。
表面清理有以下幾種方法:
(1)用熱堿液清洗和用有機溶劑擦洗除去油污;在玻璃鋼表面先用320-400目砂紙先打磨,然后用有機溶劑清洗除去脫膜劑;車身表面的黃銹應用磷酸配制的清洗液擦洗,以保證涂層有優良的防腐蝕性,以及涂層與被涂物表面有良好的附著力。
(2)對經清洗過的被涂金屬制件表面進行各種化學處理以提高漆膜的附著力和耐腐蝕性能。對鋼板制件進行特種化學處理,以提高漆膜和基材的結合力。
(3)采用機械方法清除被涂物的機械加工缺陷和創造涂膜所需的粗糙度。
磷化處理方式有整體噴射和整體浸式。采用薄膜型鋅鹽快速磷化處理,磷化膜質量1-3g/m,膜厚1-2μm,結晶粒度1-10μm,可采用低溫25-35℃或中溫50-70℃進行磷化。
(三) 涂裝
1 噴涂底漆
底漆涂層是整個涂層的基礎,汽車涂層與金屬的結合力和防腐蝕主要是靠它來實現。底漆應選用防銹性能強(鹽霧≥500h),與基材的附著力強(能同時適應多種基材),與中涂或面漆結合力好,涂膜機械性能好(沖擊≥50cm,韌性≤1mm,硬度≥0.5)的涂料作為底漆。
采用空氣噴涂的方法(也可選用高壓無氣噴涂)噴涂底漆,可采用濕碰濕的方法連噴二道,施工粘度20-30s,每道間隔5-10min,噴完后閃蒸5-10min進烘房,底漆干膜厚度40-50μm 。
2 刮膩子
刮膩子的目的是消除被涂物的不平整度。
膩子應刮在干透的底漆層上,一次涂刮的厚度一般不超過0.5mm,應采用新型的大面積刮涂膩子法。這種方法膩子易形成大面積平整,在不影響生產進程的前提下,提議每刮一次膩子均應干燥后打磨平整,然后再刮下一次膩子,膩子以刮2-3次為好,先厚刮再薄刮,這樣可增強膩子層的強度和進一步提高平整度。
采用機器打磨膩子的方法,砂紙選用180-240目。
3 噴涂中涂
采用靜電噴涂或空氣噴涂法,噴涂中涂,能提高涂層的抗石擊性,提高與底漆的附著力,改善被涂物表面的平整度和光滑度,以提高面漆的豐滿度和鮮映性。
中涂一般濕碰濕連續噴涂二道,施工粘度18-24s,每道間隔5-10min,噴完后閃蒸5-10min進烘房,中涂干膜厚度40-50μm。
4 噴面漆
采用靜電噴涂或空氣噴涂法,噴涂的汽車面漆,能形成耐候性、鮮映性和光澤優良的漆膜。
六 涂料的選擇
(一)底漆
一般的環氧酯底漆,耐鹽霧性能為200h左右,如選用環氧聚酰胺底漆,則耐鹽霧性能達500h以上;如采用底材磷化處理+環氧聚酰胺底漆、底材為鍍鋅板或鋁合金板,則耐鹽霧性能達800h以上。
(二)中涂
一般采用丙烯酸聚氨酯或聚酯聚氨酯中涂,半光或高光的裝飾性中涂,可以有效的提高面漆涂層的豐滿度,同時防止面漆下滲,提高面漆的清晰度和光澤等。
(三)面漆
一般均采用丙烯酸聚氨酯或聚酯改性丙烯酸聚氨酯面漆。
金屬閃光漆:采用以金庫鋁粉和丙烯酸樹脂為主體配制的閃光漆,罩光清漆為丙烯酸聚氨酯清漆。
珠光漆:底色漆樹脂為丙烯酸樹脂,顏色同珠光漆(單組分);珠光漆采用進口珠光,主體樹脂為丙烯酸樹脂(單組分);罩光清漆為丙烯酸聚氨酯清漆。
七 汽車涂裝用幾種最新涂料與涂裝工藝
日益嚴格的環保法規的頒布實施及汽車市場日趨激烈的競爭,加快了汽車涂裝材料和涂裝技術不斷更新與發展的步伐。為適應市場的新需要和用戶對不同質量、價格的要求,汽車涂料供應商采用新技術、新工藝和新材料來滿足汽車主機廠的需求。在達到環保法規和涂層質量要求的前提下,降低汽車涂裝成本的工作變得越來越重要。本文介紹了目前國際上已經應用于汽車涂裝中的幾種最新涂料與涂裝工藝,希望這些技術能盡快在國內汽車涂裝生產線上得到應用。
(一) 耐候性陰極電泳底漆
陰極電泳漆具有涂裝效率高、經濟安全、污染少、防腐蝕性能好、可完全實現自動化管理等特點,在汽車涂裝上得到了迅速的普及應用。近幾年圍繞節能和環保的要求,陰極電泳漆技術的發展速度很快。無鉛、無錫陰極電泳漆,低溫烘烤型陰極電泳漆,高泳透力、低溶劑含量的陰極電泳漆,高銳邊防腐性的陰極電泳漆等已經在涂裝生產線上得到成熟應用。但由于現用陰極電泳漆主體樹脂(環氧樹脂)的耐候性能差,隨著汽車產品種類的增多及質量要求的提高,有些只涂電泳漆的零部件及總成不但要具有較高的耐腐蝕性能,還要具有一定的耐候性能(比如商用車車架總成等),因此國外涂料開發商開發了耐候性陰極電泳漆。
目前有兩種技術路線可以提高電泳漆的耐候性能。
1 耐紫外線(UV)陰極電泳漆
耐UV陰極電泳漆通過調整涂料配方,將原有的芳香族異氰酸酯改換成脂肪族異氰酸酯,并加入UV穩定劑和UV穩定的顏料來提高耐候性能。涂料開發商用不同方法(包括大氣曝曬、人工加速老化試驗)測試了該涂料的耐UV性能,結果都證明該陰極電泳漆耐UV性能達到了與粉末中涂相當的水平。耐UV陰極電泳漆的開發是一個技術進步,已在國外某生產線上得到了應用。耐UV陰極電泳漆與現用陰極電泳漆性能的不同點列于表1中。
性能 | 不同點 |
原漆及施工性能 | 耐UV陰極電泳漆的烘干溫度高5 ℃,烘干時間長5 min,其他性能一樣 |
漆膜性能 | 耐UV陰極電泳漆的漆膜厚度(25~30 µm)稍厚,加熱減量在10%左右,有優異的漆膜外觀(Ra≤0.2 µm),耐UV性能與粉末中涂相當,其他性能與現用極陰極電泳漆相當 |
2 分層陰極電泳漆
分層陰極電泳漆的主體樹脂是環氧樹脂和耐候性樹脂的混合。在漆膜烘烤過程中,不同的成分通過分層電沉析體現各自的機能,上層具有高耐候性能,下層具有高防腐性能(見圖1)。主要通過控制樹脂特性Sp值,使環氧樹脂和耐候性樹脂在涂膜固化時發生分離。分層陰極電泳漆膜能耐400 h人工老化試驗,保光率為80%,漆膜的耐腐蝕性能與現用電泳漆相當,已在日本輕型車和商用車生產線上得到了應用,國內某商用車車架涂裝線在3年前也應用了該種電泳漆。
目前,國內高檔商用車和面包車采用金屬漆涂裝工藝,為降低涂裝成本和VOC排放,可以將中涂層取消。要保證達到原有涂層質量,有兩種技術措施:一是改變底色漆和罩光漆的性能,采用新的中涂、面漆涂裝工藝;二是使電泳漆具有耐候性能,而底色漆和罩光漆的性能不變。如果在陰極電泳漆涂層上直接噴面漆(金屬底色漆和罩光漆),則由于金屬底色漆阻止UV的能力差,易引起電泳涂層表面光氧化和粉化,導致面漆附著力降低、漆膜脫落和早期粉化,而使用耐候性電泳漆可以克服這一缺陷。使用耐候型陰極電泳漆的綜合成本將有所增加,如果其成本與現用電泳漆相當,推廣應用的可能性會更大。
(二) UV和熱雙固化清漆
罩光清漆雖然已有粉末罩光清漆(含漿狀粉末罩光清漆)、水性清漆、高固體分和超高固體分清漆,且都已商品化并獲得工業應用,但全世界的汽車涂料開發商還在進一步開發新的環保型罩光清漆。紫外線(UV)和熱雙固化清漆就是最近幾年開發出來的新品種。
近10年來,世界環保法規不僅對揮發性有機化合物(VOC)的排放量有限制,而且對CO2的排放量也要限制,同時對面漆涂膜的功能性(如耐酸雨、抗劃傷性)和外觀裝飾性也提出了更高要求。近幾年開發的UV和熱雙固化罩光清漆用于汽車外表面涂裝,在環保、節能、涂膜性能(外觀裝飾性、耐酸雨和抗劃傷性)和涂裝成本等方面都有較強的競爭力。日本已有采用UV和熱雙固化涂料的摩托車零部件生產線。該清漆可同時用于金屬件和非金屬件,生產線修補也可使用。
新開發的UV和熱雙固化清漆具有以下特征:
a .雙組分、固體成分含量高(>70%)。
b.與專用的聚異氰酸酯齊聚物組合,在涂布過程中有效組分能很好混合。
c.根據需要可高溫(140 ℃)烘干,也可低溫(90 ℃或低于90 ℃)烘干,與普通清漆相比,可縮短烘干時間10~15 min。
d.無UV固化的內表面和陰影部位也具有較好的性能。
e.施工范圍寬,更有利于生產線使用。
雙固化型清漆在施工工藝、涂膜性能、經濟性和環保等方面有以下優點:
a.施工工藝:UV和熱固化可并用;可改善內表面/陰影區域的涂裝性能。
b.涂膜性能:極好的外觀裝飾性、優異的抗劃傷和耐蝕(酸雨)性。
c.經濟性:烘干室長度可縮短;改造現有設備投資費用最低。
d.環保方面:節能、高固含量(>70%),可降低VOC揮發量。
(三) 汽車緊固件陰極電泳涂裝工藝
近幾年,國外汽車公司(如GM和Ford)的部分緊固件采用陰極電泳涂裝進行表面處理,以替代電鍍工藝后的鈍化處理。眾所周知,陰極電泳涂裝機械化程度高、環保、漆膜具有優異的耐腐蝕性能,在汽車車身及零部件涂裝上已應用數年,是比較成熟的工藝。隨著陰極電泳涂料的更新換代,具有一定耐候性的陰極電泳涂料、邊緣耐腐蝕性陰極電泳涂料等也在生產線上得到了實際應用。隨著各國環保法規的日趨嚴格,無鉛、無錫陰極電泳涂料及低溶劑含量的陰極電泳涂料在國內外生產線也已普遍應用。
國外汽車緊固件采用電泳涂裝已有20年的歷史了,最早是使用陽極電泳涂裝替代傳統的浸漆。為解決緊固件在擰緊時漆膜脫落的問題,1999年改成陰極電泳涂裝。現美國(通用、福特、克萊斯勒)已有5個電泳槽在使用。用于汽車緊固件的主要是黑顏色,建筑用標準件有其他顏色。
采用陰極電泳涂裝工藝的優點如下:
a.有利于環保。鍍鋅后鈍化液含有六價鉻,而陰極電泳漆是水性涂料,有利于環保。
b.提高產品的耐腐蝕性和耐濕熱性能。傳統的電鍍鋅+鈍化工藝,鹽霧試驗達到144 h左右,達克羅涂覆耐腐蝕性能可以達到500~1 000 h,但成本比較高,且膜層耐潮濕性差(耐濕熱240 h)、不耐磨;陰極電泳涂裝通過采用不同的工藝方案,耐鹽霧性能可達到240~1 000 h以上、耐濕熱500 h以上。
c.漆膜磨擦系數適宜,不影響產品裝配。
(四) 結束語
為滿足日益嚴格的環保法規要求,目前歐州汽車涂裝中100%的底漆、60%以上的中涂、40%以上的金屬底色漆均采用水性涂料,罩光漆采用2K高固體分涂料,水性罩光漆和粉末罩光漆在試用中。現歐州比較成熟的涂裝工藝是:無鉛陰極電泳→水性中涂→水性底色→高固體分(2K)罩光漆。采用該工藝后VOC排放可降到30 g/m2左右,符合歐洲環保法規要求。但采用水性涂料設備投資大、能耗高,同時對施工環境(溫度、濕度)要求比較嚴格,因此國內老涂裝線應用水性涂料的難度較大。在汽車涂裝材料向環保、節能、低成本方向發展的今天,采用新的中涂、面漆涂裝工藝將是主機廠涂裝工藝的發展趨勢。主機廠可以根據涂裝線的現狀因地制宜地選擇幾種不同的涂裝工藝。
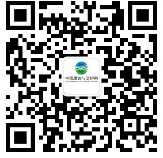
官方微信
《中國腐蝕與防護網電子期刊》征訂啟事
- 投稿聯系:編輯部
- 電話:010-62313558-806
- 郵箱:fsfhzy666@163.com
- 中國腐蝕與防護網官方QQ群:140808414