文 | 杜金輝 1 , 呂旭東, 1,2 , 董建新 3 , 孫文儒 4 , 畢中南 1,2 , 趙光普 1 , 鄧群 1 , 崔傳勇 4 , 馬惠萍 1 , 張北江 1
1. 鋼鐵研究總院高溫材料研究所 北京 100081
2. 鋼鐵研究總院高溫合金新材料北京市重點實驗室 北京 100081
3. 北京科技大學(xué)材料科學(xué)與工程學(xué)院 北京 100083
4. 中國科學(xué)院金屬研究所 沈陽 110016
高溫合金是指以 Fe、Ni、Co 為基,能在 600 ℃以上高溫抗氧化和抗腐蝕,并在一定應(yīng)力作用下可長期工作的一類金屬材料。高溫合金既是航空發(fā)動機熱端部件、航天火箭發(fā)動機各種高溫部件的關(guān)鍵材料,又是工業(yè)燃氣輪機、能源、化工等工業(yè)部門所需的高溫耐蝕部件材料,是國民經(jīng)濟不可缺少的一類重要材料。變形高溫合金是指通過鑄造 - 變形工藝生產(chǎn)的高溫合金,包括盤、板、棒、絲、帶、管等產(chǎn)品,該類產(chǎn)品廣泛用于航空、航天、能源、石化、核電等工業(yè)領(lǐng)域。本文從冶煉、均勻化、開坯、鍛造、殘余應(yīng)力控制、探傷幾個方面綜述國內(nèi)變形高溫合金全流程制備工藝的新進展,并介紹 GH4169G、GH4169D、GH4065 和 GH4068 等新研合金,展望 FGH4096 的變形化、NGH5011 的氮化、In718 合金的 3D 打印等新技術(shù)。
1 工藝流程新進展
1.1 冶煉
國內(nèi)變形高溫合金冶煉通常采用真空感應(yīng) + 真空自耗兩聯(lián)或真空感應(yīng) + 電渣重熔 + 真空自耗三聯(lián)的熔煉方式。對于用量最大的變形高溫合金 GH4169 來說,有害元素與夾雜物的含量嚴(yán)重影響合金的性能,純凈度對其使用可靠性有重要影響。真空感應(yīng)熔煉過程中,流槽具有緩沖、分液作用。流槽是位于澆注室內(nèi)用于澆注的過渡裝置,經(jīng)過流槽中的內(nèi)控裝置可將氧化渣上浮,合金液從流槽的出水口流出,再由引流嘴將合金液澆注到模鑄室中的鋼錠模中。通過流槽可以穩(wěn)定注流,改善合金液的流動形態(tài),促進合金液中的夾雜物上浮與分離等。目前國內(nèi)的流槽結(jié)構(gòu)較為簡單,只是一個簡單的長形包,內(nèi)控裝置只是簡單的擋板,基本為真空感應(yīng)爐自帶的流槽結(jié)構(gòu),遠遠發(fā)揮不出流槽應(yīng)具備的功能和作用。根據(jù)流槽的設(shè)計和優(yōu)化準(zhǔn)則,通過水模擬和數(shù)值模擬對真空感應(yīng)爐內(nèi)流槽進行優(yōu)化設(shè)計,使合金熔液在流槽內(nèi)的停留時間大于優(yōu)化前合金熔液停留時間,可增加夾雜物上浮的機會,減小死區(qū)的比例,改善流槽內(nèi)流場分布和溫度分布,從而提高鑄錠的質(zhì)量和潔凈度,如圖 1 所示。其中,圖 1a 和 b 為優(yōu)化前后流槽去除夾雜物能力的對比,圖 1c 和 d 為與之相對應(yīng)的停留時間分布(residence time distribution,RTD)曲線變化。
圖1 真空感應(yīng)熔煉流槽優(yōu)化前后的對比
流槽內(nèi)鋼水流動狀態(tài)的研究方法主要有以下 3 種:實際測定、物理模擬、數(shù)學(xué)模擬。借助水模擬和數(shù)值模擬實驗,得到了內(nèi)控裝置擋墻、擋壩在流槽中對流場的作用規(guī)律,優(yōu)化出長形流槽。通過對國外、國內(nèi)普遍采用與自主設(shè)計的方形流槽鋼液流動數(shù)值模擬的對比分析,發(fā)現(xiàn)自主設(shè)計的方形流槽在夾雜物去除能力上具有優(yōu)勢。
圖2 真空自耗過程的傳熱示意圖
真空感應(yīng)熔煉可以得到確定的合金成分,真空自耗重熔可以保證鑄錠的微觀組織。國內(nèi)利用 Procast 軟件,對真空自耗過程進行數(shù)值模擬,圖 2 為真空自耗過程的傳熱示意圖。通過建模和有限元數(shù)值模擬,定量地描述了鑄錠重熔過程中一次、二次樹枝晶的分布狀態(tài),見圖 3。
圖3 鑄錠一次、二次樹枝晶枝晶間距(PDAS和SDAS)的分布狀態(tài)
1.2 均勻化
高溫合金鑄錠在凝固過程中會產(chǎn)生較嚴(yán)重的成分偏析,為減輕和改善成分偏析,提高材質(zhì)的均勻性,除改進冶煉工藝外,最重要的技術(shù)措施是進行均勻化處理,通過高溫下的長時間加熱,促進溶質(zhì)元素原子的擴散遷移,達到枝晶干與枝晶間元素濃度差異的最小化 。對于高合金化GH4720Li合金,Al 和 Ti 總含量高達 7.5%(質(zhì)量分數(shù)),鑄錠中不可避免地存在著成分偏析和枝晶間共晶相,這對合金鑄錠在開坯過程中的熱塑性及棒材乃至鍛件的組織均勻性都有不利影響 。因此,在熱加工前,必須通過高溫均勻化處理:(1)消除以 Ti為主的元素偏析;(2)使共晶相回溶;(3)同時保證不出現(xiàn)晶界弱化而影響開坯鍛造的熱塑性。鑄錠經(jīng)過合理的均勻化后,才能進行鍛造開坯。
為滿足工業(yè)生產(chǎn)需要,需將 GH4720Li 合金鑄錠直徑由406mm 擴大到 508mm。通過 GH4720Li 合金直徑 508mm 鑄錠與直徑 406mm 鑄錠的枝晶分布及 Ti 元素偏析情況的對比分析(見表 1 及圖 4)發(fā)現(xiàn),隨著錠型的擴大,偏析情況會受到凝固冷速的影響而相應(yīng)加劇,二次枝晶間距略微增大,枝晶變得稍微粗大、Ti 元素的偏析系數(shù)(K)有所增加,但增加幅度較小,尤其是二次枝晶間距分布范圍差距也小,直徑 508mm鑄錠二次枝晶間距范圍為 98~161μm,直徑 406mm 鑄錠二次枝晶間距范圍為 80~160μm。
圖4 直徑406和508mm的GH4720Li合金鑄錠中心部位縱向高倍組織
為了優(yōu)化出 GH4720Li 合金直徑 508mm 鑄錠最佳均勻化制度,本課題組設(shè)計了 3 種不同的均勻化制度:制度 1 為(T-10℃)、30h+(T+10℃)、40h;制度 2 為 T、70h;制度 3為(T-10℃)、30 h+(T+10℃)、60 h (其中 T 為 γ′全溶溫度),通過平均偏析系數(shù)和析出相對比來研究 Ti 元素的分布。由表 2 可見,經(jīng)過 3 種不同的均勻化制度處理后其枝晶間和枝晶干的 Ti 元素分布均勻,而且 Ti 元素的 K 都大大減少。3 種均勻化制度中,經(jīng)制度 3 均勻化后的 Ti 元素的 K 最小,經(jīng)制度 2 均勻化后的 Ti 元素的 K 最大。由此可以看出,制度3 的均勻化效果最佳。
1.3 開坯
高合金化高溫合金普遍具有熱變形抗力大、塑性低、可變形溫度區(qū)間窄等特點。為了提高 GH4720Li 合金鑄錠的開坯成材率以及棒材的質(zhì)量水平,需要從材料本身和工藝條件 2個方面來提高合金開坯時的熱塑性:在預(yù)處理的基礎(chǔ)上,進一步調(diào)整、優(yōu)化快鍛機開坯工藝參數(shù),特別是要選擇更為合理的火次加熱溫度及明確每火次變形量分配原則,從而可以從快鍛工藝上減少鑄錠開裂的傾向。
通過大量熱模擬壓縮實驗研究了不同變形溫度、變形量和變形速率下,GH4720Li 鑄錠的熱塑性、流變應(yīng)力規(guī)律、再結(jié)晶規(guī)律,建立了熱塑性與變形條件的數(shù)學(xué)模型,獲得不同熱變形條件下的開裂判據(jù),優(yōu)化鍛造工藝參數(shù)。通過實際鍛造開坯過程對數(shù)學(xué)模型進行校驗。利用數(shù)值模擬方法對快鍛開坯過程的工藝參數(shù)進行優(yōu)化(圖 5),包括逐級降溫及火次變形量合理分配。
圖5 GH4720Li合金快鍛開坯數(shù)值模擬
快鍛開坯充分破碎鑄錠鑄態(tài)組織之后,再輔之以徑鍛,可以改善棒材表面狀態(tài),提高成材率。徑鍛以表面變形為主,更有利于棒材外緣再結(jié)晶,會明顯提高棒材的表面質(zhì)量;同時徑鍛開坯時表面變形量大,會造成一定程度的表面溫升,表面溫升能補償表面溫降,進而減少表面溫降造成的開裂。如果表面溫升過大,又會導(dǎo)致已再結(jié)晶細化的晶粒發(fā)生長大。因此探索 GH4720Li 合金徑鍛開坯工藝的重點是制定合理的快鍛和徑鍛變形量分配方案,以實現(xiàn)動態(tài)再結(jié)晶晶粒細化以及棒材表面質(zhì)量的提升。從而確定合理可行的 GH4720Li 合金徑鍛加熱溫度、錘寬、送進速率、下壓量以及轉(zhuǎn)角等關(guān)鍵工藝參數(shù),開發(fā)出 GH4720Li合金徑鍛新工藝(圖 6)。
1.4 模鍛
GH4706合金超大型渦輪盤是當(dāng)代 E/F 級重型燃機的核心熱端轉(zhuǎn)動部件,鍛件直徑超過 2000mm、重量達 6t,是亟待國產(chǎn)化的最關(guān)鍵部件之一。GH4706 合金是一種 γ‘相與 γ“相強化的 Fe-Ni 基變形高溫合金,成分接近于 GH4169 合金,具有力學(xué)性能優(yōu)異、可鍛性良好、變形強度適中、可制備大錠型、成本相對低廉等優(yōu)點 。
渦輪盤的模鍛既要實現(xiàn)盤件的熱加工成型又要實現(xiàn)組織性能控制,二者均很重要、缺一不可,同時二者又互相影響、互相制約,這一特點隨著渦輪盤鍛件直徑的增大而體現(xiàn)得更為突出。為了實現(xiàn)超大型渦輪盤鍛件的熱加工成形,對現(xiàn)有鍛造設(shè)備的潛能已挖掘至極限,渦輪盤鍛件的組織和性能隨著其尺寸的增大而表現(xiàn)出衰減的趨勢,原因在于受設(shè)備能力的制約,熱加工工藝參數(shù)的制定往往無法兼顧組織和性能的最優(yōu)化。
研制直徑大于 2000mm 的高溫合金渦輪盤鍛件的另一技術(shù)關(guān)鍵在于模鍛成形過程中的載荷控制,即能否在國內(nèi)現(xiàn)有最大噸位的鍛壓機上獲得幾何尺寸滿足要求的模鍛件。目前,國內(nèi)采用一火整體模鍛成形,生產(chǎn)成熟度最高的大型高溫合金渦輪盤為直徑 1200mm 的GH4698 合金鍛件,利用的是國內(nèi)最早裝備的 3×104t 水壓機。值得指出,此前國內(nèi)研制的直徑 2200mm 的 GH2674合金渦輪盤鍛件是利用 4000t 快鍛機采用局部成型工藝碾壓鍛制而成,這一方法在組織、性能均勻性控制上存在不可避免的缺陷,不適合于制備渦輪盤等在長期復(fù)雜應(yīng)力環(huán)境下工作的轉(zhuǎn)動件。2013 年,我國自主設(shè)計研制的世界最大的 8×104t 模鍛液壓機投入試生產(chǎn),并試制成功了直徑 1500mm 的 GH4738 合金渦輪盤鍛件,為超大型 GH4706 合金渦輪盤鍛件的制備提供了一定的參考經(jīng)驗。但是,實現(xiàn)高溫合金渦輪盤鍛件的直徑由 1500mm 向 2000mm 以上跨越仍面臨很大的挑戰(zhàn)。
張北江等研究表明,提高鍛前加熱溫度可以降低設(shè)備載荷,降低壓機壓下速率也能夠降低合金的變形抗力,但會延長總的鍛壓時間進而加劇坯料熱量的散失。因此,要獲得最低的鍛造載荷,最佳的壓下制度是變形初期采用較高的壓下速率以縮短總鍛壓時間,當(dāng)設(shè)備載荷飽和后轉(zhuǎn)入恒壓狀態(tài),以最大限度地發(fā)揮設(shè)備潛力。鑒于此,構(gòu)建了 GH4706合金的本構(gòu)關(guān)系與顯微組織演化規(guī)律模型,應(yīng)用數(shù)值模擬技術(shù)進行熱加工工藝優(yōu)化,在解決超大型 GH4706 合金渦輪盤鍛件的載荷控制基礎(chǔ)上,最大限度優(yōu)化鍛件組織和性能。最終利用高可靠度的數(shù)值模擬技術(shù),充分挖掘我國 8×104t 噸油壓機的設(shè)備潛力,實現(xiàn)了超大型GH4706 合金渦輪盤鍛件的國產(chǎn)化(圖7),盤件性能達到了美國 GE-B50A651標(biāo)準(zhǔn)的要求。
圖7 直徑2100 mm超大型GH4706合金渦輪盤鍛件實物照片
1.5 殘余應(yīng)力
變形高溫合金盤鍛件制備過程中形成的殘余應(yīng)力會在不同工序間不斷演化傳遞,最終對高溫合金盤件的加工和使役性能造成重要影響。因此有必要掌握變形高溫合金盤鍛件全部工藝過程殘余應(yīng)力的影響因素、分布特征、演化規(guī)律與內(nèi)在機制,才能預(yù)判其對后續(xù)加工變形及使用性能的影響,進而優(yōu)化、精化制備工藝;這同樣也是實現(xiàn)航空發(fā)動機正向設(shè)計、壽命預(yù)測的重要基礎(chǔ)。經(jīng)過深入、細致的研究工作,總結(jié)了高溫合金渦輪盤鍛件內(nèi)部殘余應(yīng)力的測試方法,闡明了固溶、淬火、時效、零件加工等制備工藝過程中殘余應(yīng)力的演化規(guī)律與機制。
對于高溫合金鍛件而言,表層殘余應(yīng)力與冷加工工藝和噴丸工藝相關(guān),會影響零件的疲勞性能,但是要研究殘余應(yīng)力對盤件整體結(jié)構(gòu)的影響,需要測試分析距離表面 10 mm 甚至更深的內(nèi)部殘余應(yīng)力,分辨率要求為毫米級。圖 8顯示,可以滿足要求的方法主要包括中子衍射法(neutron diffraction)、輪廓法(contour method)、深孔法(deep-holedrilling)和超聲法(ultrasonic)。
圖8 各種殘余應(yīng)力測量方法的測量穿透與空間分辨率
為了獲得足夠的強化水平,高溫合金盤鍛件在鍛造成形后常需要在固溶處理后以一定速率快速冷卻,以確保 γ”或 γ’強化相在此過程中不發(fā)生粗化。研究表明,影響高溫合金鍛件中殘余應(yīng)力的最主要工序是固溶處理后的快速冷卻過程(或鍛后冷卻)。淬火應(yīng)力形成的本質(zhì)原因是鍛件不同區(qū)域之間的體積差異,這既包括溫度不同引起的熱膨脹差,也包括相變引起的體積變化。
綜上所述,高溫合金盤鍛件制備工藝過程中的內(nèi)部殘余應(yīng)力主要產(chǎn)生于固溶或鍛后淬火過程形成的溫度梯度,主要以弦向和徑向應(yīng)力為主,沿輪廓呈“內(nèi)拉外壓”特征分布,其量級與淬火態(tài)合金的室溫屈服強度水平相當(dāng)。強化相的析出行為會改變合金冷卻過程中不同溫度下的膨脹系數(shù)和強度水平,從而對殘余應(yīng)力分布和量級產(chǎn)生重要影響。
另外,在研究過程中還發(fā)現(xiàn) GH4169合金中 γ“相在服役過程的變體選擇粗化現(xiàn)象 。γ”相作為 GH4169 合金的主要強化相,在基體中有 3 種位向關(guān)系的變體,其尺寸、形貌和分布狀態(tài)是決定合金力學(xué)性能的關(guān)鍵因素。在一定溫度作用下,GH4169 合金中的 γ“相會發(fā)生擴散控制的粗化現(xiàn)象。然而前期研究通常只考慮溫度和時間對組織失穩(wěn)的影響,忽略了合金實際制備和服役過程中應(yīng)力的作用。長時服役后的 GH4169合金渦輪盤中發(fā)生的 γ”相粗化存在變體選擇現(xiàn)象:1 種或 2 種位向關(guān)系的γ“變體被擇優(yōu)保留下來,其余位向關(guān)系的變體消失。通過電子背散射衍射(EBSD)結(jié)合掃描電鏡(SEM)研究發(fā)現(xiàn),γ”相的變體選擇行為受到外加應(yīng)力和晶粒取向的影響,如圖 9 所示。經(jīng)熱力耦合作用的 GH4169 合金多晶材料中,多數(shù)晶粒內(nèi)具有γ“ γ位向關(guān)系的γ”
相變體會被擇優(yōu)保留,另外 2 種 γ“相變體趨于消失。進一步研究發(fā)現(xiàn),γ”粗化過程中 3 種 γ“相變體均保持圓盤狀,并在各自 c 軸方向承受較大但無差異的壓應(yīng)力;熱力耦合條件下,外加應(yīng)力與 γ”相及周邊 γ 基體間的內(nèi)應(yīng)力疊加,導(dǎo)致不同 γ“相變體的 γ”/γ錯配應(yīng)變發(fā)生改變,引起 3 種 γ“相變體的彈性應(yīng)變能出現(xiàn)差異。從而,彈性應(yīng)變能相對較低的 γ”相變體尺寸長大的阻力變低,發(fā)生擇優(yōu)粗化;彈性應(yīng)變能較高的γ“相變體尺寸長大受到抑制,會在 Gibbs-Thomson 效應(yīng)的作用下逐漸溶解于基體。GH4169 合金中 γ”相的變體選擇會導(dǎo)致合金高溫強度和蠕變抗力降低。
圖9 GH4169合金熱力耦合作用后γ“相變體選擇行為與晶粒取向的關(guān)系
1.6 探傷
超聲檢測作為無損檢測的一種重要方法,被廣泛應(yīng)用于航空航天、鋼鐵冶金等工業(yè)領(lǐng)域,用于檢查材料內(nèi)部氣孔、裂紋、夾雜等缺陷。變形高溫合金是航空航天領(lǐng)域大量采用的轉(zhuǎn)動類零件用材料,其超聲檢測顯得尤為重要。探頭發(fā)出的超聲波進入工件內(nèi)部進行傳播,當(dāng)工件內(nèi)部存在聲學(xué)特性與基體不同的組織不連續(xù)或不均勻時,超聲波在界面上發(fā)生傳播方式和信息的改變,由此可以對材料內(nèi)部組織不連續(xù)或不均勻進行分析,從而為無損檢測和評價提供定性、定量依據(jù)。
GH4169 合金盤鍛件組織致密,晶粒尺寸 0.022~0.0078mm,一般要求檢出直徑 0.8 或 0.4mm 甚至更小當(dāng)量平底孔大小的缺陷,這對超聲檢測方法和儀器本身均提出了較高要求。在超聲波檢測過程中盤鍛件因局部組織的差異會呈現(xiàn)不同的雜波顯示,而國內(nèi)標(biāo)準(zhǔn)中未對不超標(biāo)信號做出規(guī)定,因此有必要對盤鍛件組織尤其是晶粒尺寸與超聲雜波之間的關(guān)系進行充分研究,以確定影響檢測結(jié)果的主要原因和適宜的檢測參數(shù)。圖10 為渦輪盤超聲 C 掃圖。
圖10 渦輪盤超聲C掃圖
實驗結(jié)果表明,某種固溶熱處理制度的 GH4169 合金試樣雜波幅度均在 10% 以下;與鍛態(tài)試樣相比,不同固溶熱處理試樣底波降低幅度不同,溫度越高,底波降低幅度越大,經(jīng) 1050 ℃熱處理的 5# 試樣底波降低幅度大于 4# 試樣,3# 試樣次之,如表 3 所示。因此,在試樣表面狀態(tài)、檢測參數(shù)一致的前提下,GH4169 合金渦輪盤的晶粒尺寸在一定程度內(nèi)可通過超聲檢測進行表征,晶粒尺寸越小,底波降低幅度越大。
綜上所述,對于渦輪盤中出現(xiàn)的局部雜波,采用 10 和 5 MHz 探頭、0.4 mm 當(dāng)量的檢測靈敏度均可將雜波檢出,且 10 MHz 探頭信噪比優(yōu)于 5 MHz 探頭,故更適合選用;與 5 MHz 相比,采用 10 MHz 探頭進行底波監(jiān)控,可獲得更為精確的底波幅值,可以作為定量比較晶粒尺寸的參考依據(jù)。
2 新合金
2.1 GH4169G合金
傳統(tǒng)觀點認為,P 是高溫合金中典型的有害元素 。國內(nèi)于 1990 年代初期發(fā)現(xiàn)了 P 可將 GH4169 等合金持久壽命提高 3 倍以上,并將其穩(wěn)態(tài)蠕變速率降低一個數(shù)量級以上。隨后又發(fā)現(xiàn) P、B 具有更加強烈的復(fù)合強化作用,即 P、B 復(fù)合加入可以更加強烈地提高 GH4169 合金的持久蠕變性能。P、B 的復(fù)合強化作用直到 750 ℃仍很顯著,表明其可以提高合金的工作溫度。在對 P 強化以及 P、B 復(fù)合強化機理深入研究的基礎(chǔ)上,通過進一步研究 P、B 對合金組織、性能以及加工工藝的影響,發(fā)展了 GH4169G 合金 。GH4169G 合金在全面保持了 GH4169 合金優(yōu)異的綜合使用性能的基礎(chǔ)上,將使用溫度提高了30 ℃,達到680 ℃;650 ℃下的使用壽命提高3倍以上,長壽命特點十分突出;同時焊接和熱加工等工藝性能與GH4169合金基本相當(dāng)。因此,它適合于制作對綜合使用性能和工藝性能要求比較全面的整體葉盤,以及對壽命和安全可靠性要求較高的部件,具有比較廣闊的應(yīng)用前景。
2.2 GH4169D合金
GH4169D 合金的研制成功填補了世界上 2 個最廣泛應(yīng)用高溫合金——650 ℃用GH4169 合金和 750 ℃用 GH4738 合金之間長期存在的空白。GH4169D 合金是在 GH4169 合金基礎(chǔ)上,通過降低 Fe 的含量,加入固溶強化元素 W 和 Co,調(diào)整 Al+Ti 含量以及 Al、Ti 比,并適當(dāng)提高 Nb 含量以及調(diào)整微量元素含量而研制成功的 。與 GH4169 合金相比,GH4169D 合金主要強化相由 γ“相轉(zhuǎn)變?yōu)榱?γ‘相,650 ℃以上熱穩(wěn)定性顯著增加,因而合金使用溫度得到顯著提高;與其它 γ’相強化的合金,如 GH4738相比,GH4169D 合金中的 γ‘相析出速率明顯減慢,使其熱加工性能和焊接性能得到顯著改善。因此,GH4169D 合金兼具了 GH4169 合金高強度、良好的熱加工和焊接性能,以及 GH4738 合金使用溫度高的綜合優(yōu)點,其長期使用溫度可達 704 ℃,是未來高性能航空發(fā)動機頗具潛力的關(guān)鍵材料,也被稱為下一代 GH4169 合金。GH4169D 合金雖然是在GH4169合金成分基礎(chǔ)上發(fā)展起來的,但與 GH4169 合金相比,GH4169D 合金具有完全不同的相組成。眾所周知,GH4169 合金是以 γ”相強化為主,輔以 γ’相強化,晶界由 δ 相組成。而GH4169D 合金則以 γ‘相強化為主,晶界相最初也被認為δ相,后經(jīng)研究證實,晶界相主要為具有 η-Ni3Ti 的結(jié)構(gòu)的Ni3Al0.5Nb0.5 (或者稱為 η-Ni6AlNb)相。所以與 GH4169 合金相比,GH4169D合金無論是化學(xué)成分、基體強化相還是晶界析出相,都發(fā)生了非常大的改變,是完全不同的 2 種合金,其相析出、溶解規(guī)律以及對性能的影響機理也有所不同,GH4169D 和 GH4169 合金的組織對比如圖 11 所示。
通過物理化學(xué)相分離以及X 射線衍射等實驗,Wang 等對 γ’相和η-Ni3Al0.5Nb0.5 的相組成做了進一步確定。結(jié)果證實,標(biāo)準(zhǔn)熱處理條件下 γ‘相的質(zhì)量分數(shù)可占 GH4169D 合金 的 22%~27%,η-Ni3Al0.5Nb0.5 可占到 1.5%~7%,其質(zhì)量分數(shù)隨著熱處理制度和化學(xué)成分的變化會有所不同。γ' 相 和 η-Ni3Al0.5Nb0.5 相 中均含有一定量的 Nb,其原子分數(shù)分別達到 9% 和 13%,由于 Nb 在鎳基基體中具有較低的擴散系數(shù),這被認為是GH4169D 合金中 γ’相的析出速率要慢于其它常見 γ‘相強化合金的重要原因。通過調(diào)整 GH4169D 合金中 γ’相和 η-Ni3Al0.5Nb0.5 相不同的分配比例,進而得到合金不同的綜合性能,可應(yīng)用于不同服役環(huán)境部件的制備。
圖11 GH4169D和GH4169合金經(jīng)標(biāo)準(zhǔn)熱處理后的組織
2.3 GH4065合金
在依托鑄鍛工藝發(fā)展高性能渦輪盤材料方面也取得了重要進展,研制了GH4065、GH4079 和 GH4975 等高性能變形高溫合金渦輪盤材料,特別是 GH4065合金的綜合性能達到粉末冶金材料的水平,有望為我國先進航空發(fā)動機熱端轉(zhuǎn)動部件的選材提供成熟可靠的解決方案。采用鑄鍛工藝制備高合金化高溫合金大尺寸鍛件,需要掌握通過化學(xué)成分優(yōu)化來降低高合金化材料枝晶偏析傾向性的原理與方法;解決大尺寸自耗重熔錠熔鑄過程穩(wěn)定性問題;實現(xiàn)熱模鍛造條件下的鍛件組織和性能高效控制。
針對先進航空發(fā)動機對熱端轉(zhuǎn)動部件的需求,新型高性能變形高溫合金的研制工作充分總結(jié)現(xiàn)有渦輪盤材料設(shè)計的成功經(jīng)驗及存在的問題,在對一系列模型合金的力學(xué)性能和工藝性能進行對比和篩選的基礎(chǔ)上,最終以成熟的粉末冶金渦輪盤材料 FGH4096 的化學(xué)成分為基礎(chǔ),針對鑄鍛工藝路線的要求進行全面優(yōu)化,研制了新型的 GH4065 合金,其典型成分如表 4 所示。作為對照,表中同時列出了國內(nèi)研制的主要高合金化變形高溫合金的化學(xué)成分。
時效狀態(tài)下GH4065合金與FGH4096合金的 γ‘相體積分數(shù)均為 42%,低于 GH4720Li 合金的 45%。GH4065 合金的 γ’相平衡溶解溫度為 1119 ℃,因此比 GH4720Li 和 GH4975 合金具有更大的熱加工溫度窗口。在 FGH4096 合金基礎(chǔ)上,GH4065 合金針對鑄鍛制備工藝的特殊要求對化學(xué)成分進行了以下幾方面的優(yōu)化:
(1) 主元素方面。在保證 γ/γ‘錯配度不變的情況下,優(yōu)化各固溶強化元素與 γ’相形成元素之間的比例,特別是相對于粉末冶金 FGH4096 合金限制了 Nb 的加入量,以有效降低材料熔鑄過程中的枝晶偏析傾向性。GH4065 合金中允許加入質(zhì)量分數(shù)達到 1.0% 的 Fe,一方面可以改進熔煉過程中 Nb 等合金元素的加入方法;另一方面,可以實現(xiàn)與產(chǎn)量最大的 Fe-Ni 基合金 GH4169 共用坩堝,方便返回料的回收利用,因而有助于提高生產(chǎn)效率和降低生產(chǎn)成本。
(2) 間隙元素方面。GH4065 與粉末冶金 FGH4096 合金相比最大的差別是 C 含量大幅度降低,成分上限控制在質(zhì)量分數(shù) 0.01% 的水平,僅為粉末冶金 FGH4096 合金的 1/3~1/5,低于同樣采用低間隙元素設(shè)計的 GH4720Li 合金。
降低 C 含量可以使鋼錠中的一次碳化物尺寸和數(shù)量都大幅度下降,同時有效減輕碳化物形成元素 Nb 和 Ti 元素的枝晶偏析傾向性。一次碳化物尺寸和數(shù)量的減小可以改善因碳化物不均勻分布導(dǎo)致的奧氏體晶粒尺寸分散性大的問題,同時作為主要的疲勞裂紋源,碳化物尺寸和數(shù)量的減少還可以顯著提高材料的疲勞性能。GH4065 合金對 B 元素的最大加入量做出了限制以解決大尺寸鋼錠熔鑄過程中 B 的宏觀偏析問題,通過優(yōu)化Zr 等微量元素的加入量來改善合金高溫持久性能。
2.4 GH4282合金
GH4282 合 金 在 保 持 一 定 數(shù) 量 的沉淀強化 γ‘相的基礎(chǔ)上,通過控制γ’相的結(jié)構(gòu)、組成和析出動力學(xué),解決了高強度時效強化燃燒室合金中由于γ‘相的大量快速析出導(dǎo)致的冷加工和焊接困難的難題 。與 GH4141 合金相比,GH4282 合金在具有相當(dāng)?shù)臒釓娦阅軛l件下,空冷后合金板材室溫塑性達到 50%,其冷加工性能與固溶合金相當(dāng);合金焊接性能優(yōu)異,不需要特殊的焊前焊后熱處理;其 700~900 ℃長期時效 1000 h 后沒有 TCP 相析出,室溫拉伸塑性保持在 20% 以上。可見,合金在 650~950 ℃范圍內(nèi)保持了極佳的高溫強度和熱穩(wěn)定性,同時可對焊接和冷加工性能進行很好的平衡和優(yōu)化 。
表 4 還列出了目前國內(nèi)外主要的時效強化型燃燒室合金的主要化學(xué)成分 。可見,與歐美系列的 GH4738 和GH4141 合金相比,GH4282 合金具有很好的繼承性,GH4282 合金主要對 Co、Mo、Ti 和 C 元素進行了調(diào)整。其中 Co元素含量一般控制在 10%~20% 之間,主要用于增加基體對 γ’相和固溶強化元素的溶解能力,GH4282 合金中取其下限進行控制;Mo元素作為大尺寸原子,具有強的固溶強化能力和難遷移擴散的特點,在 GH4282 合金中 Mo 元素首先對基體進行固溶強化,同時 Mo 元素參與γ‘相形成,對 γ’相進行強化并影響其形成和長大過程。在低于 8.5% 的范圍內(nèi),隨著 Mo 元素含量增加,合金持久性能增加明顯,表明 Mo 元素對基體和γ‘相進行了有效強化,在大于8.5%的范圍內(nèi),Mo 元素增加,合金持久性能降低,其機制目前還不確定,可能是因為 Mo 元素對基體固溶強化達到極限的同時,影響了 γ’相與基體的共格錯配度,進而弱化了 γ‘相的強化效率;Al 和 Ti 元素作為 γ’相形成元素,其含量直接影響 γ‘相數(shù)量。從表 4 還可以看出,與 GH4738 和 GH4141 合金相比,GH4282 合金降低了 Ti 含量,進而降低了 γ’相數(shù)量,這在一定程度上對合金的加工性能和高溫強度起到了平衡作用。
2.5 Ni-Co基合金
自 2006 年,Sato 等發(fā)現(xiàn)在鈷基合金體系中可析出穩(wěn)定的L12結(jié)構(gòu)γ‘相,使得發(fā)展時效強化鈷基高溫合金成為可能。由于該類合金具有更高的 γ’強化相體積分數(shù)、熱加工窗口較寬、凝固偏析傾向較小等優(yōu)勢,國際上已經(jīng)形成了發(fā)展此類合金的熱潮。美國 GE、Allvac、英國 R&R 和日本 NIMS 等均對該合金體系開展了大量研究工作,它已成為 750 ℃以上使用的高代次航空發(fā)動機渦輪盤選材。近年來,通過自主設(shè)計合金成分和小錠型實驗,證明該合金 γ‘強化相體積分數(shù)達到 50%,熱加工窗口明顯寬于鎳基變形高溫合金,同時具有良好的組織穩(wěn)定性,其性能接近第三代粉末高溫合金水平,可以作為具有高的使用性能和良好工藝性的渦輪盤材料。圖 12 為時效強化 Ni-Co 基合金的透射電鏡(TEM)照片。
圖12 時效強化鈷基合金在900 ℃退火72 h的TEM像
GH4068 合金是一種新型 Ni-Co 基鑄鍛變形高溫合金,其承溫能力可達750℃,接近最強商用粉末變形高溫合金(ME3 和 RR1000)的水平。該合金的設(shè)計理念為:強化“中溫區(qū)(服役溫度區(qū)間)”、弱化“高溫區(qū)(變形加工區(qū))”,該設(shè)計思路(如圖 13 所示)解決了難變形合金強化易、變形難的瓶頸問題,在 U720Li 合金(目前承溫能力最高的鑄鍛變形高溫合金)基礎(chǔ)上,通過對主元素(如 Co 和 Ti)調(diào)整,制備出超過 750℃鑄鍛變形高溫合金,使其在低溫和中溫區(qū)的強度比原合金有很大提升,但在高溫區(qū)低于原合金。
圖13 GH4068合金的成分設(shè)計思路
研究表明,在低溫低應(yīng)力下,新型Ni-Co 基變形高溫合金主要通過位錯切割 γ’相形成大量層錯;當(dāng)蠕變溫度升高或加載載荷較高時,合金中的位錯運動速率提高,合金的變形主要以層錯和孿生方式進行;當(dāng)蠕變溫度高于 725 ℃時,合金中的 γ‘相開始發(fā)生粗化,并且部分小尺寸的 γ’相溶解,促使 γ‘相之間的基體通道增大,更加有利于位錯的繞過;因此,當(dāng)蠕變溫度達到 815℃時,合金的主要蠕變變形方式為位錯繞過機制,如圖 14 所示。
圖14 不同蠕變條件下GH4068合金的變形機制
GH4068合金在中溫區(qū)蠕變的主要變形機制是位錯切割 γ’相形成層錯和微孿晶,如圖 15 所示。蠕變過程中層錯的形成是由于全位錯 a/2<110> 滑移過程中遇到 γ‘相時分解成 a/3<12 1>和 a/6<112> 不 全 位 錯,a/3<12 1>位錯切入 γ’相中,而 a/6<112> 位錯則留在 γ/γ‘相界面處,從而形成了層錯。由于 GH4068 合金的層錯能低,因此變形過程中更容易形成層錯。當(dāng)加載載荷較大時,拖拽位錯運動的應(yīng)力也相應(yīng)提高。并且,層錯的寬度受應(yīng)力影響,當(dāng)應(yīng)力提高時,層錯寬度變寬,因此,存在于不同 γ′相中的層錯由于被拉寬而連接到一起形成連續(xù)層錯,所以在中溫變形過程中,GH4068 合金變形組織中出現(xiàn)大量在基體和第二相中廣泛存在的連續(xù)層錯。
圖15 GH4068合金中溫區(qū)蠕變變形組織
3 新技術(shù)
3.1 FGH4096合金變形化
針對先進航空發(fā)動機用高合金化程度的鎳基渦輪盤鑄錠偏析嚴(yán)重、組織均勻性難控制的特點,開發(fā)了電渣重熔連續(xù)定向凝固冶煉 +3D 鍛造制坯 + 等溫鍛造制備難變形渦輪盤的新型鑄鍛工藝技術(shù),該技術(shù)已成功用于制備高性能、低成本、零缺陷的變形 FGH4096 合金渦輪盤,其中 3D 鍛造制坯是指采用常規(guī)鍛造設(shè)備在坯料三維方向依次完成特定變形量的鍛造過程為一個循環(huán)的 3D 鍛造,在一個鍛造循環(huán)里每個方向都可以當(dāng)一次鍛造端面,兩次鍛造側(cè)面,最后回到坯料的原始形狀,通過多個循環(huán)的鍛造解決高合金化合金坯料因變形量不足和冷模組織造成的組織均勻性問題,為后續(xù)模鍛提供組織完全均勻的坯料。
電渣重熔連續(xù)定向凝固鑄錠無大尺寸 η相、大尺寸硼化物偏析以及碳氮化物條帶,鑄錠具有優(yōu)異的熱加工塑性;鍛坯采用 3D 鍛造工藝制備,大幅度消除變形過程中接觸錘砧的表面變形死區(qū),坯料微觀組織無各向異性,晶粒尺寸范圍10~16 μm;渦輪盤鍛件采用等溫鍛造,鍛件不同部位晶粒組織均勻細小,超聲波檢測的可探性高。
圖16 FGH4096電渣重熔連續(xù)定向凝固鑄錠(直徑270 mm)中部宏觀低倍組織
FGH4096 合金定向凝固鑄錠中部宏觀低倍組織如圖 16 所示,定向柱狀晶軸向取向偏離度≤ 20°。合金凝固后的枝晶間距是衡量偏析程度的重要參數(shù),枝晶間距越小即枝晶干排列越緊密,合金偏析程度越低,而且凝固過程中枝晶間區(qū)域的減小也使得枝晶間析出相尺寸減小,其中二次枝晶間距是衡量微觀偏析的重要參數(shù)。從鑄錠中間 R/2 (R 為鑄錠的半徑)處截取試樣觀察鑄態(tài)微觀組織,如圖 17 所示,F(xiàn)GH4096 合金定向凝固鑄錠中二次枝晶排列緊密,枝晶間距約 100μm。
圖17 FGH4096合金定向凝固鑄錠R/2處微觀組織(R為鑄錠半徑)
變形 FGH4096 合金渦輪盤采用等溫模鍛,模具溫度接近坯料溫度,材料流動性和充填性好,同時坯料為晶粒尺寸10 μm 的細晶坯料,熱變形抗力小,鍛件的殘余應(yīng)力較低。目前制備了數(shù)批件直徑 630 mm 渦輪盤及擋板鍛件、渦輪軸等,鍛件超聲波可探性較好,超聲波水浸檢驗雜波水平控制在低于昺0.4-21dB,鍛件探傷一致性和穩(wěn)定性好。圖18 為變形 FGH4096 合金等溫鍛造渦輪盤鍛件(直徑 630 mm)縱剖面微觀組織。
3.2 NGH5011合金
氮化現(xiàn)有的高溫合金體系和強化原理下,燃燒室合金長時耐溫能力(以 100h、40 MPa 持久溫度表征) 在近 30 年內(nèi)無法突破 1000 ℃的服役溫度。開發(fā)新型燃燒室合金,顯著提高燃燒室用高溫合金的長時耐溫能力,需要突破現(xiàn)有合金體系或創(chuàng)新強化技術(shù)。目前可用于燃燒室的新材料主要有氧化物彌散強化合金、陶瓷、難熔金屬合金和復(fù)合材料等新材料,這些合金在 1100 ℃以上都表現(xiàn)出較高的高溫強度。但是上述材料都有諸多不可克服的問題,距離部件的成熟制備還有很大距離。
新型內(nèi)生彌散氮化物強化高溫合金采用 TiN 作為強化相,其 1100 ℃、100h 持久強度比傳統(tǒng)高溫合金高 2~3 倍,可滿足未來 1100 ℃以上航空發(fā)動機主燃燒室、加力燃燒室和噴口等部件用合金的選材。該合金實現(xiàn)內(nèi)生氮化物彌散強化是在部件制備成型后,因此在獲得高溫強度的同時,還兼顧了部件的加工、焊接性能,解決了目前燃燒室合金中使用性能和高溫性能對立的矛盾。內(nèi)生彌散氮化物強化合金的相關(guān)研究在 1970年就見報道,其中 Kindlimann 和 Ansell在不銹鋼基體中首次進行了內(nèi)生彌散氮化物強化技術(shù)。隨后 Petrova 對高溫合金內(nèi)生氮化物強化技術(shù)進行了深入廣泛的研究,其研究一直持續(xù)到 2000 年后,涉及 Fe、Ni 和 Co 3 種基體,研究了不同氮化物形成元素的氮化物強化效果,最終研制出比較成熟的合金 ВЖ155。
國內(nèi)開發(fā)了氮化物強化高溫合金NGH5011,在該合金基礎(chǔ)上針對內(nèi)生彌散氮化物強化高溫合金的氮化工藝流程中涉及的 N 在表面的吸附溶解、N 在基體的均勻擴散、反應(yīng)界面上氮化物的析出等關(guān)鍵物理化學(xué)過程,開展了高溫合金內(nèi)生氮化物彌散強化技術(shù)的系統(tǒng)研究工作。
將 NGH5011 合金氮化后的力學(xué)性能與其它燃燒室用高溫合金進行比較,以評估其力學(xué)性能。表 5 所示是各種合金的室溫拉伸、1100 ℃高溫拉伸及1100 ℃和 30 MPa 下持久性能的對比。
可見,新型內(nèi)生氮化物彌散強化高溫合金相對于傳統(tǒng)高溫合金的高溫性能優(yōu)勢明顯。相對于氧化物彌散強化高溫合金 MGH956,NGH5011 合金在瞬時拉伸性能上表現(xiàn)出一定優(yōu)勢,其 1100 ℃、30 MPa 持久壽命不及粗晶條件下的MGH956 合金,但略高于細晶 MGH956合金。綜上所述,氮化后的 NGH5011 合金在室溫拉伸、高溫拉伸和高溫持久等方面表現(xiàn)出優(yōu)異的綜合性能。
3.3 增材制造3D-In718
激光增材制造是基于“離散 - 堆積”、“添加式制造”的基本概念發(fā)展起來的金屬零件全密度快速直接制造技術(shù)。各種類型的激光增材制造技術(shù),如激光熔覆沉積技術(shù)(laser engineerednet shaping,LENS)、選擇性燒結(jié)技術(shù)(selective laser sintering,SLS)、直接激光成形技術(shù)(direct laser forming,DLF)等,本質(zhì)上都是利用送粉或鋪粉方式逐點逐層添加沉積,實現(xiàn)三維任意形狀高性能金屬零件的近凈成形。作為一項短周期、低成本的綠色數(shù)字制造技術(shù),激光增材制造技術(shù)具有快速、柔性、高性能等諸多優(yōu)勢,在航空、航天、核電、石化、船舶等高端裝備制造中有巨大的發(fā)展?jié)摿蛷V闊前景。
它將先進材料技術(shù)與先進制造技術(shù)融為一體,既能保證零件的形狀和尺寸精度,又能保證零件的表面光潔度、成分、組織和性能達到使用要求。
鋼鐵研究總院高溫材料研究所利用增材制造技術(shù),成功制備出 3D-In718 合金的燃氣渦輪盤(直徑 150 mm)和整體葉輪(直徑 220 mm),如圖 19 所示,直接成形零件致密度達到 99.9%,組織和性能均遠優(yōu)于鑄件,室溫、高溫拉伸強度和塑性、持久性能均可滿足鍛件標(biāo)準(zhǔn),燃氣渦輪盤力學(xué)性能如表 6 所示,其中解剖部分包含2 組實驗數(shù)據(jù)。
圖19 增材制造3D-In718燃氣渦輪盤和整體葉環(huán)
4 結(jié)束語
高溫合金既是航空發(fā)動機熱端部件、航天火箭發(fā)動機各種高溫部件的關(guān)鍵材料,又是工業(yè)燃氣輪機、能源、化工等工業(yè)部門所需的高溫耐蝕部件材料,是國民經(jīng)濟不可缺少的一類重要材料。變形高溫合金通過鑄造-變形工藝生產(chǎn),包括盤、板、棒、絲、帶等產(chǎn)品,廣泛用于航空、航天、能源、石化、核電等工業(yè)領(lǐng)域。本文主要介紹了變形高溫合金的制備工藝流程、新合金研制以及新技術(shù) 3 個方面在國內(nèi)近 10 年的最新進展。
航空、航天動力系統(tǒng)和燃氣輪機需要變形高溫合金的高溫力學(xué)性能和耐蝕性能實現(xiàn)穩(wěn)定、高效的動力輸出;而隨著海洋工程裝備、石化裝置、核電設(shè)施等高端制造業(yè)進入新的發(fā)展階段,也需要國產(chǎn)耐溫、抗蝕性能優(yōu)異的變形高溫合金保證裝備的可靠運行。為此,國內(nèi)需要構(gòu)建重點牌號變形高溫合金的全方位成分 - 工藝 - 組織 - 性能譜,揭示出合金性能及生產(chǎn)工藝的共性和特性;在成規(guī)模、批量生產(chǎn)中研究提高航空、航天動力系統(tǒng)和燃氣輪機用關(guān)鍵變形高溫合金的工程化技術(shù)水平和質(zhì)量穩(wěn)定性;針對海洋工程裝備、石化裝置、核電設(shè)施等重大需求,研究開發(fā)變形高溫合金的適用性能和生產(chǎn)技術(shù),并逐步得到應(yīng)用。因此,伴隨綠色制造、智能制造技術(shù)的方興未艾和裝備升級,在國民經(jīng)濟中占據(jù)重要地位的變形高溫合金產(chǎn)品必將向低成本、高均質(zhì)、近成形、長壽命的方向迅猛發(fā)展,全面提升我國變形高溫合金產(chǎn)業(yè)技術(shù)進步是大勢所趨。
免責(zé)聲明:本網(wǎng)站所轉(zhuǎn)載的文字、圖片與視頻資料版權(quán)歸原創(chuàng)作者所有,如果涉及侵權(quán),請第一時間聯(lián)系本網(wǎng)刪除。
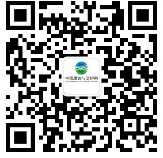
官方微信
《腐蝕與防護網(wǎng)電子期刊》征訂啟事
- 投稿聯(lián)系:編輯部
- 電話:010-62316606-806
- 郵箱:fsfhzy666@163.com
- 腐蝕與防護網(wǎng)官方QQ群:140808414