摘要
針對(duì)鎂合金的微弧氧化膜,對(duì)微缺陷的形成及其影響因素、微缺陷對(duì)微弧氧化膜性能及應(yīng)用的影響、微缺陷的識(shí)別技術(shù)、后處理手段進(jìn)行了總結(jié)與分析。最后,提出了鎂合金微弧氧化膜及其他金屬防護(hù)層中微缺陷問題的未來研究方向和思路。
關(guān)鍵詞: 鎂合金 ; 微弧氧化膜 ; 微缺陷 ; 影響 ; 缺陷檢測(cè) ; 處理技術(shù)
金屬材料在制造過程中會(huì)產(chǎn)生偏析、夾雜、氣孔、熱裂紋等缺陷[1,2]。這些缺陷的存在將使金屬材料具有偏離理想結(jié)構(gòu)的非均勻性,對(duì)其結(jié)構(gòu)及性能都將產(chǎn)生一定影響[3]。為了滿足金屬材料及其裝備在各種復(fù)雜服役條件下的環(huán)境適應(yīng)性要求,開發(fā)與利用適當(dāng)?shù)慕饘俜雷o(hù)手段尤為重要。腐蝕防護(hù)層作為金屬防護(hù)的重要手段,廣泛應(yīng)用于各種金屬材料的腐蝕控制工程中。然而,在大多數(shù)工程應(yīng)用中,金屬材料的防護(hù)層也會(huì)因缺陷的存在,環(huán)境適應(yīng)性大打折扣,服役壽命顯著降低,不但會(huì)造成資源浪費(fèi),維修維護(hù)成本增大;而且會(huì)導(dǎo)致環(huán)境污染,影響產(chǎn)品質(zhì)量,增大安全風(fēng)險(xiǎn),甚至可能成為限制高新技術(shù)發(fā)展與應(yīng)用的關(guān)鍵因素[4]。所以,開展金屬防護(hù)層體系中的微缺陷對(duì)材料性能損傷問題的研究,不但有利于促進(jìn)表面科學(xué)與工程技術(shù)的發(fā)展,而且也將提高金屬腐蝕控制工程技術(shù)水平,既具有理論價(jià)值又具有技術(shù)應(yīng)用價(jià)值。
鎂合金以其質(zhì)輕、性能優(yōu)異、加工成本低、易于回收等優(yōu)點(diǎn),成為裝備制造業(yè)輕量化、環(huán)?;?、高性能化發(fā)展的首選,在機(jī)械、航空航天、汽車、電子、生物醫(yī)療等領(lǐng)域有著巨大的應(yīng)用潛力[5]。然而,由于鎂合金的耐蝕性較差,其進(jìn)一步的推廣應(yīng)用也受到了一定限制。在現(xiàn)有的鎂合金表面處理技術(shù)中,微弧氧化 (MAO) 技術(shù)形成的陶瓷膜具有耐磨、耐高溫、電絕緣性能好、與鎂合金基材結(jié)合力強(qiáng)等諸多優(yōu)點(diǎn),被譽(yù)為最有前景的鎂合金表面處理技術(shù)。盡管如此,在鎂合金微弧氧化膜的加工過程中,難以避免微缺陷的產(chǎn)生。微缺陷的存在大大削減了鎂合金微弧氧化膜的耐蝕性,使其難以滿足大多數(shù)工程應(yīng)用的需求。鎂合金微弧氧化膜的缺陷問題是眾多金屬防護(hù)層中缺陷問題的典型代表。因此,開展鎂合金微弧氧化膜中的微缺陷研究,不僅可以為提升鎂合金微弧氧化膜質(zhì)量提供技術(shù)支撐,而且有利于認(rèn)識(shí)金屬防護(hù)層中微缺陷的損傷作用。目前,已有大量針對(duì)微弧氧化鎂合金的文獻(xiàn)綜述發(fā)表[6-8],但大多聚焦于成膜機(jī)理、膜層性能、應(yīng)用及封孔處理手段等內(nèi)容。但從鎂合金微弧氧化膜的微缺陷問題出發(fā)進(jìn)行探討與研究的文章較少。
本文基于微缺陷在金屬防護(hù)層中存在的普遍性,著眼于鎂合金微弧氧化膜體系的微缺陷問題,對(duì)微缺陷的形成及其影響因素、微缺陷對(duì)膜層性能及應(yīng)用的影響、微缺陷的識(shí)別和后處理技術(shù)等進(jìn)行了總結(jié)與分析。并對(duì)鎂合金微弧氧化膜及其他金屬防護(hù)層的微缺陷研究進(jìn)行了展望,以期對(duì)金屬防護(hù)層的設(shè)計(jì)優(yōu)化及合理使用提供理論與技術(shù)支持。
1 微缺陷存在的普遍性
在金屬材料冶煉、加工成型過程中,常常會(huì)引入雜質(zhì)、裂紋、氣孔等缺陷 (圖1)[2]。這些缺陷或引起金屬化學(xué)成分及組織結(jié)構(gòu)的不均勻,或引起物理狀態(tài)的不均勻,最終極可能導(dǎo)致金屬的電化學(xué)不均勻 (電位分布差異),從而構(gòu)成腐蝕微電池[4]。同樣的,金屬防護(hù)層的制備過程中也會(huì)出現(xiàn)微米或納米尺度的微缺陷。在這里,金屬防護(hù)層中的微缺陷可劃分為物理結(jié)構(gòu)缺陷與化學(xué)構(gòu)造缺陷。其中,物理結(jié)構(gòu)缺陷主要指結(jié)構(gòu)上的不均與缺失,以微孔、微裂紋、粗糙等不同形態(tài)存在[9-12]?;瘜W(xué)構(gòu)造缺陷主要指具有高化學(xué)活性或電化學(xué)活性的非均勻相結(jié)構(gòu)與化學(xué)組成[13,14]。這些化學(xué)構(gòu)造缺陷或優(yōu)先與腐蝕環(huán)境中的物質(zhì)反應(yīng),發(fā)生化學(xué)溶解[13];或與體系其他部分構(gòu)成腐蝕微電池,發(fā)生電化學(xué)溶解[14],最終都將導(dǎo)致涂層與保護(hù)膜的局部受損。
圖1 金屬表面的缺陷示意圖[2]
雖然微缺陷在金屬的防護(hù)層中普遍存在,但其并非一定會(huì)成為導(dǎo)致防護(hù)層失效的最終原因。在實(shí)際應(yīng)用中,具有微缺陷的金屬防護(hù)層也會(huì)出現(xiàn)均勻腐蝕失效或與微缺陷無關(guān)的局部腐蝕,這主要與腐蝕環(huán)境及防護(hù)體系性質(zhì)有關(guān)。即便如此,在環(huán)境載荷下,微缺陷作為金屬防護(hù)層防腐性能的“薄弱環(huán)節(jié)”,仍具有導(dǎo)致防護(hù)層失效的風(fēng)險(xiǎn),如何提高缺陷防護(hù)層的環(huán)境適應(yīng)性也是值得關(guān)注的問題。
金屬防護(hù)層的種類多樣,不同防護(hù)層體系的作用機(jī)理及其防護(hù)性能也有較大的差別。金屬防護(hù)層大致分為鈍化膜、轉(zhuǎn)化膜及涂層3類。鈍化膜的結(jié)構(gòu)特征與金屬及其氧化物的化學(xué)性質(zhì)密切相關(guān)[15],比如金屬M(fèi)g、Fe、Cu表面形成的鈍化膜疏松且不連續(xù),具有明顯的物理結(jié)構(gòu)缺陷。轉(zhuǎn)化膜主要指通過化學(xué)或電化學(xué)處理在金屬表面形成具有一定厚度的非電子導(dǎo)體膜[16],如陽極氧化膜等。在其成膜過程中,也難免產(chǎn)生微孔、裂紋等微缺陷[17,18]。與鈍化膜、轉(zhuǎn)化膜相比,涂層具有較大的厚度,因而在中、大型設(shè)備的腐蝕防護(hù)中應(yīng)用十分普遍。通過添加不同的顏料或添加劑,涂層將表現(xiàn)出不同的防護(hù)機(jī)理:物理屏障、陰極保護(hù)、緩蝕劑防護(hù)等。同樣的,由于材料自身性質(zhì)、局部反應(yīng)不均等原因,涂層在制備工藝過程中常常會(huì)產(chǎn)生微缺陷,如有機(jī)涂層[19,20]、金屬涂層[21]、復(fù)合涂層[22]等。可見,無論是薄膜還是厚膜,或是具有更大厚度的涂層,都不可避免地存在著微缺陷。這將極大地制約著防護(hù)層及其防護(hù)體系服役壽命的延長(zhǎng),影響著結(jié)構(gòu)件、裝備的運(yùn)行安全。
微缺陷導(dǎo)致的鎂合金微弧氧化膜耐蝕性降低,成為了限制其發(fā)展及推廣的重要因素,在眾多金屬防護(hù)層缺陷問題中具有典型性與代表性。對(duì)鎂合金微弧氧化膜的微缺陷問題進(jìn)行分析討論,也將有利于加強(qiáng)對(duì)金屬防護(hù)層中這一共性問題的認(rèn)識(shí)。
2 微弧氧化及其微缺陷的形成
微弧氧化又稱為等離子體電解氧化 (PEO),是在陽極氧化的基礎(chǔ)上發(fā)展起來的金屬表面處理技術(shù)[23]。微弧氧化利用高壓放電產(chǎn)生的等離子體放電為驅(qū)動(dòng)力,在金屬表面原位形成一層具有一定厚度的氧化陶瓷膜。微弧氧化技術(shù)廣泛應(yīng)用于Al、Mg、Ti及其他輕質(zhì)合金的表面防護(hù)處理中[24]。其中,對(duì)于鎂合金而言,微弧氧化被稱為最具有前景的表面處理技術(shù)之一。
一般地,鎂合金微弧氧化膜的主要化學(xué)成分為MgO。MgO的化學(xué)穩(wěn)定性較差,極易在腐蝕環(huán)境中發(fā)生化學(xué)溶解,造成鎂合金微弧氧化膜的受損。同時(shí),大量微缺陷存在于鎂合金微弧氧化膜中,這些微缺陷將增大腐蝕介質(zhì)的浸蝕面,同時(shí)為腐蝕介質(zhì)的傳遞提供短途通道,加速了膜層的提前失效。微缺陷的產(chǎn)生是由材料性質(zhì)與工藝特征造成的必然結(jié)果。一方面,MgO的低PB比 (0.81<1) 決定了微弧氧化膜疏松結(jié)構(gòu)的形成。另一方面,在微弧氧化工藝過程中,高能等離子體放電活動(dòng)也為微缺陷的形成創(chuàng)造了條件[25]。鎂合金微弧氧化膜中的微缺陷屬于物理結(jié)構(gòu)缺陷,主要有兩種存在形式:微孔與微裂紋。微孔的形成與高壓、高溫條件下的氣體逸出及熔融態(tài)氧化物的噴發(fā)有關(guān),微裂紋的形成則與熔融氧化物接觸冷電解液凝固收縮產(chǎn)生的熱應(yīng)力有關(guān)[26,27]。因此,在鎂合金微弧氧化膜的生長(zhǎng)過程中,微缺陷的形成是難以避免的。
3 鎂合金微弧氧化膜中微缺陷的影響因素
3.1 基材的影響
基材對(duì)微缺陷的影響主要體現(xiàn)在基材成分及表面狀態(tài)兩個(gè)方面。首先,基材成分會(huì)參與微弧氧化成膜。因此,基材成分對(duì)微弧氧化膜的結(jié)構(gòu)特征及化學(xué)組成均會(huì)產(chǎn)生顯著的影響。一般來說,AZ系列鎂合金的微弧氧化成膜致密度優(yōu)于AM系列[28]。在鎂合金中適量引入Ca、Nd、Ce等可以提高微弧氧化膜的致密度,減少微缺陷的生成[29-31]。
除基材的化學(xué)成分外,基材的表面狀態(tài) (包括粗糙度、晶粒尺寸等) 對(duì)微弧氧化膜的結(jié)構(gòu)也具有非常顯著的影響[32,33]。研究[32]表明,在微弧氧化過程中,其放電現(xiàn)象與基材的粗糙度密切相關(guān),基材表面粗糙度越高,微弧氧化膜中的微缺陷越多。通過一些預(yù)處理手段,如激光表面重熔 (LSR)、表面機(jī)械研磨處理 (SMAT)、超聲冷鍛 (UCFT)、超聲滾壓預(yù)處理 (UIRP) 等技術(shù)[34-37],對(duì)鎂合金表面進(jìn)行晶粒細(xì)化將有利于減少微缺陷的生成,制備出更為致密的微弧氧化膜。
3.2 電參數(shù)的影響
在微弧氧化工藝控制過程中,電參數(shù)主要包括電源類型、工作模式、電流密度/電壓大小、占空比及頻率等。不同的電參數(shù)將直接影響微弧氧化過程中的放電行為,進(jìn)而影響膜層的物理結(jié)構(gòu)及化學(xué)成分。用于鎂合金微弧氧化處理工藝的電源類型通常為脈沖型電源,主要分為單極和雙極兩種。與單極脈沖電流相比,雙極脈沖電流改善了等離子體的熱條件,減少了強(qiáng)等離子體放電的發(fā)生 (B型放電),從而減少了大尺寸微孔的生成[38]。恒流模式與恒壓模式為微弧氧化最普遍使用的電源工作模式。通常情況下,恒流模式下制備的微弧氧化膜微缺陷尺寸小于恒壓模式下所得。在恒流模式下,低電流密度制備的微弧氧化膜一般都很薄,致密度高,缺陷少。隨著電流密度的升高,放電能量也將升高,最終導(dǎo)致大孔徑缺陷的生成。類似的,在恒壓模式下,膜層的微孔尺寸會(huì)隨電壓的升高而增加[39]。提高頻率能夠在一定程度上減小孔隙缺陷的尺寸,從而生成致密的微弧氧化膜[40]。而占空比對(duì)微缺陷的影響較小,高占空會(huì)在一定程度上降低膜層的致密性[39]。
3.3 溶液參數(shù)及氧化時(shí)間的影響
微弧氧化的電解液成分不僅可以改變膜層的化學(xué)組成,還能通過改變微弧放電行為影響微缺陷的形成。例如,KF的加入能夠降低起弧電壓,使得氧化膜更容易被擊穿,從而在鎂合金表面生成更為致密的微弧氧化陶瓷膜[41]。同時(shí),也會(huì)在膜層中形成MgF2,提高膜層的化學(xué)穩(wěn)定性[42]。在硅酸鹽電解液體系中加入3-氨基丙基三甲氧基硅烷 (APTMS)、甘油、三乙醇胺 (TEA) 等有機(jī)化合物,有利于通過改變微弧氧化過程中的放電行為,得到微裂紋更少、微孔尺寸更小的微弧氧化膜[43]。在電解液中加入氧化石墨烯,可以降低體系的擊穿電壓與放電能量,減少大尺寸微孔的形成[44]。
在其他參數(shù)不變的情況下,隨著氧化時(shí)間的延長(zhǎng),膜層的厚度與致密度均會(huì)有上升趨勢(shì),但在氧化時(shí)間超過最優(yōu)值后,厚度與致密度將有所下降。如果氧化時(shí)間過長(zhǎng),膜層結(jié)構(gòu)可能會(huì)被完全破壞,膜層質(zhì)量顯著降低[45]。
4 微缺陷對(duì)微弧氧化鎂合金性能與應(yīng)用的影響
在大多數(shù)應(yīng)用條件下,微缺陷的存在會(huì)削弱微弧氧化膜的局部防腐性能,最終導(dǎo)致鎂合金基材腐蝕的發(fā)生,為結(jié)構(gòu)件的正常服役帶來安全隱患。但在實(shí)際中,也不乏利用鎂合金微弧氧化膜中的微缺陷達(dá)到科學(xué)研究與工程應(yīng)用目的的實(shí)例。
4.1 微缺陷的危害性
4.1.1 降低微弧氧化鎂合金體系的防腐性能
在運(yùn)輸、施工、服役過程中,機(jī)械損傷或環(huán)境載荷作用可能會(huì)導(dǎo)致鎂合金微弧氧化膜中微缺陷的擴(kuò)展與新缺陷的生成。比較而言,環(huán)境載荷作用較為復(fù)雜,一方面,來源于環(huán)境中的腐蝕性因素,如高溫、紫外輻射、Cl-等;另一方面,來源于環(huán)境力學(xué)因素,如機(jī)械磨損、沖擊、壓力、拉應(yīng)力等。在實(shí)際服役環(huán)境中,可能是腐蝕性因素或者力學(xué)因素單獨(dú)作用,也可能是兩者耦合作用。
在環(huán)境載荷作用下,微缺陷將成為鎂合金微弧氧化膜中的薄弱環(huán)節(jié)。一方面,微孔與微裂紋為腐蝕介質(zhì)的傳遞提供了“傳遞通道”與更大的接觸面積,成為腐蝕介質(zhì)快速到達(dá)基材表面的“捷徑”;另一方面,在環(huán)境力學(xué)因素的作用下,微缺陷處往往能造成應(yīng)力集中[46],加速鎂合金微弧氧化膜的機(jī)械損傷,成為膜層過早失效的突破口。此外,研究[47,48]表明,膜層分解與基材腐蝕生成的腐蝕產(chǎn)物Mg(OH)2會(huì)在膜層中產(chǎn)生內(nèi)應(yīng)力,也會(huì)導(dǎo)致固有缺陷的擴(kuò)展與新缺陷的產(chǎn)生,甚至造成膜層的剝離。鑒于微缺陷的存在導(dǎo)致了微弧氧化膜耐蝕性能的降低,在較為苛刻的服役環(huán)境中,微弧氧化膜較少作為鎂合金腐蝕防護(hù)層單獨(dú)使用。
4.1.2 降低微弧氧化鎂合金體系的力學(xué)性能
一旦微缺陷誘發(fā)了鎂合金基材的局部腐蝕的出現(xiàn),這些腐蝕區(qū)域也可能成為應(yīng)力集中源,將縮短整個(gè)結(jié)構(gòu)體系的疲勞壽命。另一方面,局部腐蝕將削弱材料結(jié)構(gòu)的承載面積,致使體系靜強(qiáng)度、疲勞強(qiáng)度、剛度等力學(xué)性能下降[49]。最終,造成微弧氧化鎂合金結(jié)構(gòu)件,甚至整個(gè)材料體系剩余強(qiáng)度與剩余壽命的顯著降低。
4.2 微缺陷的可用性
雖然在環(huán)境載荷的作用下,微缺陷的存在可能會(huì)導(dǎo)致鎂合金微弧氧化膜的過早失效,但是并非所有的應(yīng)用環(huán)境都對(duì)材料體系的耐蝕性能具有高要求。例如,當(dāng)微弧氧化鎂合金用于骨內(nèi)植入器械和血管支架時(shí),微缺陷發(fā)揮了巨大作用。圖2為隨植入時(shí)間的延長(zhǎng),有無微弧氧化處理的ZX50鎂合金植入體分解行為的μCT圖像??梢?,微弧氧化膜可減緩鎂合金植入體在一定時(shí)間內(nèi)的腐蝕,以提供足夠的機(jī)械強(qiáng)度對(duì)血管或受損骨骼進(jìn)行有效支撐[50]。隨后,在微缺陷的作用下,微弧氧化鎂合金在體液環(huán)境中逐漸無毒降解。這樣,避免了植入體取出手術(shù),極大地緩解了病人的生理痛苦和經(jīng)濟(jì)負(fù)擔(dān)[51]。
圖2 微弧氧化鎂合金植入體針隨時(shí)間的μCT圖像 (3D重建)[50]
此外,微缺陷的存在為微弧氧化膜提供了更高的自由表面能和粗糙度,有利于有機(jī)物在其表面通過機(jī)械咬合結(jié)構(gòu)牢固附著。因此,微弧氧化還被作為鎂合金表面有機(jī)涂覆的前處理手段,以解決有機(jī)涂層與鎂合金結(jié)合力較低的問題[52]。微弧氧化膜中的微缺陷還被作為承載藥物與緩蝕劑的容器,從而制備出具有特殊性能的膜層。例如,Bordbar-Khiabani等[53]將鎂合金微弧氧化膜作為倍他米松磷酸鈉 (BSP) 的藥物載體,實(shí)驗(yàn)結(jié)果表明所得PEO/BSP涂層具有較好的耐蝕性和藥物傳遞性能。整體看來,由于鎂合金微弧氧化膜在耐蝕性方面的局限性,功能膜將逐漸成為其重要發(fā)展方向之一。
總的來說,微缺陷具有存在的普遍性、隱蔽性,影響的雙重性、潛在性。在涂層與保護(hù)膜的工程應(yīng)用中,微缺陷問題往往被忽略。因此,對(duì)微缺陷進(jìn)行有效識(shí)別與分析,將有利于科學(xué)避免與合理利用微缺陷。
5 微缺陷的識(shí)別技術(shù)研究
在金屬防護(hù)層的研究中,常用的測(cè)試手段主要包括物理結(jié)構(gòu)分析技術(shù)、化學(xué)構(gòu)造分析技術(shù)及電化學(xué)測(cè)試技術(shù)。然而,傳統(tǒng)的測(cè)試技術(shù)大多局限于2D空間或宏觀層面上的分析檢測(cè),難以滿足對(duì)微缺陷識(shí)別及其引起的膜層性質(zhì)非均勻性的研究。因此,隨著現(xiàn)代分析測(cè)試技術(shù)的發(fā)展,一些新型現(xiàn)代測(cè)試與分析技術(shù)開始在微缺陷研究方面展開應(yīng)用。
5.1 物理結(jié)構(gòu)測(cè)試技術(shù)
傳統(tǒng)的掃描電子顯微鏡 (SEM) 等測(cè)試技術(shù)很難為研究人員提供微缺陷在3D空間的分布信息。隨著數(shù)字與圖像技術(shù)的發(fā)展,X-CT技術(shù)等3D定量測(cè)試技術(shù)已在微弧氧化膜的微缺陷研究中得到了應(yīng)用[48,54,55]。它們可以直接而定量化地表征微弧氧化膜微缺陷在3D空間的尺寸大小、數(shù)量及分布特征[56],對(duì)微缺陷的識(shí)別與研究具有十分重要的意義。
5.2 化學(xué)構(gòu)造測(cè)試技術(shù)
微缺陷分布的不均勻,也意味著成膜過程中放電現(xiàn)象的不均勻,即能量傳輸與物質(zhì)傳遞的不均勻。因此,微弧氧化膜的化學(xué)構(gòu)造也將存在差異性。利用微區(qū)化學(xué)測(cè)試技術(shù),可以測(cè)定微弧氧化膜表面的化學(xué)分布,以達(dá)到研究微缺陷的目的。此外,這些技術(shù)還可應(yīng)用于其他金屬防護(hù)層的化學(xué)構(gòu)造缺陷的檢測(cè)中。常見的微區(qū)化學(xué)測(cè)試技術(shù)有電子背散射衍射 (EBSD)[57]、飛行時(shí)間二次離子質(zhì)譜 (TOF-SIMS)[58]、掃描電鏡透射模式 (STEM)[59]、Raman光譜[59]等。
5.3 電化學(xué)測(cè)試技術(shù)
近年來,微區(qū)電化學(xué)技術(shù)的發(fā)展與應(yīng)用,為檢測(cè)微缺陷在介質(zhì)中的局部電化學(xué)行為提供了可能[60],主要包括以下幾種。
掃描電化學(xué)顯微鏡 (SECM) 是一種能夠同時(shí)提供溶液中樣品表面的局部形貌、化學(xué)構(gòu)造及電化學(xué)信息的測(cè)試技術(shù)[61],是涂層與保護(hù)膜微缺陷研究的有力手段。掃描振動(dòng)電極技術(shù) (SVET) 可以提供微尺度下電極表面電流密度或電位梯度的信息。近年來,SVET被廣泛應(yīng)用于涂層與保護(hù)膜微缺陷的定位、微缺陷的形成和發(fā)展的監(jiān)測(cè)等領(lǐng)域[60]。局部電化學(xué)阻抗譜 (LEIS) 作為一種相對(duì)新穎的局部電化學(xué)測(cè)量方法,可以通過提供試樣上特定位置的阻抗數(shù)據(jù)來研究非均勻腐蝕[62]。掃描開爾文探針技術(shù) (SKP) 是在真空或大氣中測(cè)量金屬表面接觸電位差的方法,以此探索表面的局部電化學(xué)狀態(tài)。掃描開爾文探針力顯微鏡技術(shù) (SKPFM) 是原子力顯微鏡 (AFM) 和SKP的結(jié)合,通過SKPFM可以觀察到局部表面的形貌和Volta電位的變化[63]。絲束電極 (WBE) 技術(shù)是一種適用于實(shí)際現(xiàn)場(chǎng)監(jiān)測(cè)和高電阻環(huán)境的測(cè)試手段。目前,WBE已被成功應(yīng)用于垢下腐蝕、陰極剝離監(jiān)測(cè)以及流動(dòng)條件下微缺陷的形成與擴(kuò)展過程。
除WBE技術(shù)外,上述電化學(xué)局部化技術(shù)都是掃描探針技術(shù)。探針與測(cè)試表面的距離、試樣自身的表面高度差、探針的尺寸及其移動(dòng)時(shí)的攪拌作用均會(huì)對(duì)測(cè)試結(jié)果的準(zhǔn)確性產(chǎn)生影響[64]。此外,作為一種微觀測(cè)試技術(shù),現(xiàn)有的微區(qū)電化學(xué)測(cè)試仍需要進(jìn)一步提高測(cè)試精度與分辨率,特別是實(shí)現(xiàn)納米尺度的測(cè)試,以達(dá)到對(duì)微缺陷的電化學(xué)響應(yīng)的精確捕捉。
5.4 數(shù)值模擬
由于微弧氧化膜加工工藝的復(fù)雜性,數(shù)值模擬已被廣泛用于微弧氧化膜加工過程熱力學(xué)與動(dòng)力學(xué)的研究中[25,65-67]。而在實(shí)際應(yīng)用中,由于微缺陷體積小、隱蔽性高的特點(diǎn),現(xiàn)有的監(jiān)測(cè)技術(shù)往往難以反映微弧氧化膜中微缺陷的精確信息。在這種情況下,使用數(shù)值模擬技術(shù)對(duì)微缺陷演化行為及其所誘發(fā)的微弧氧化膜失效過程進(jìn)行研究,必將逐漸成為代替微缺陷實(shí)際監(jiān)測(cè)的重要手段。然而,由于腐蝕體系的復(fù)雜性,如何正確建立數(shù)學(xué)模型也是數(shù)值模擬中的重要難題。
綜合上述的測(cè)試技術(shù),針對(duì)微缺陷的測(cè)試技術(shù)主要向著3D、微觀測(cè)試及數(shù)值計(jì)算的方向發(fā)展。在微缺陷問題的研究中,如何選用合適的測(cè)試技術(shù)也是值得關(guān)注的問題。
6 鎂合金微弧氧化膜微缺陷后處理技術(shù)
在微弧氧化過程中,微缺陷的產(chǎn)生是難以避免的,工藝條件優(yōu)化僅僅能減少微缺陷的形成,并不能從根本上解決鎂合金微弧氧化膜中的缺陷問題。因此,大量研究聚焦于通過后處理技術(shù)對(duì)微缺陷進(jìn)行封閉,以提高鎂合金微弧氧化膜的環(huán)境適應(yīng)性。
6.1 水熱處理
水熱處理是一種最簡(jiǎn)單的微弧氧化膜后處理手段,主要是將微弧氧化樣品浸入熱水中進(jìn)行封閉。通過水熱處理,微弧氧化膜表面覆蓋一層Mg(OH)2膜,對(duì)微弧氧化膜中的微缺陷進(jìn)行封堵[68]。然而,經(jīng)過水熱處理,微弧氧化膜成分MgO也將被消耗,使膜層變薄。另一方面,Mg(OH)2的堆積也會(huì)帶來膜層內(nèi)應(yīng)力的產(chǎn)生,可能會(huì)誘發(fā)膜層的機(jī)械損傷。
6.2 封涂處理
封涂處理是在微弧氧化膜表面形成一層新的防護(hù)層,以實(shí)現(xiàn)對(duì)微弧氧化膜疏松外層的有效封堵。常用的封涂方法包括溶膠-凝膠法、有機(jī)涂層封閉、化學(xué)鍍、離子鍍等[69,70]。溶膠-凝膠法具有環(huán)境友好、成本低、工藝簡(jiǎn)單等特點(diǎn),是一種應(yīng)用較為廣泛的微弧氧化鎂合金后處理手段[71]。通過溶膠-凝膠法,可在微弧氧化膜表面形成SiO2-ZrO2膜、SiO2膜、TiO2膜等陶瓷膜。另一種常用的封涂處理方法是有機(jī)涂層封閉[72,73]。由于微弧氧化膜外層的多孔性及有機(jī)材料的高流動(dòng)性,有機(jī)層會(huì)與微弧氧化膜表面的孔隙緊密結(jié)合,更加有利于封閉效果的提升。
值得注意的是,大多數(shù)封涂技術(shù)都會(huì)改變鎂合金微弧氧化膜原有的表面狀態(tài),膜層固有的耐磨、耐高溫等性能也可能會(huì)由此削減甚至喪失。因此,根據(jù)應(yīng)用需求,對(duì)后處理技術(shù)進(jìn)行科學(xué)的設(shè)計(jì)與選用至關(guān)重要。
6.3 緩蝕劑浸漬
緩蝕劑浸漬法是鎂合金微弧氧化膜后處理的重要手段之一。在微弧氧化膜的腐蝕失效過程中,緩蝕劑也會(huì)逐漸流失或被稀釋,難以維持理想的緩蝕效果。因此,緩蝕劑浸漬封閉的方法很少被單獨(dú)使用,一般在完成緩蝕劑浸漬后,需要進(jìn)行再次的封涂處理,以防止緩蝕劑的過早流失[73,74]。
現(xiàn)有的微弧氧化鎂合金后處理技術(shù)仍無法滿足其大規(guī)模工業(yè)應(yīng)用的要求。同時(shí),后處理技術(shù)可能會(huì)在賦予鎂合金微弧氧化膜新性能的同時(shí),削減其原有性能。因此,開發(fā)一種保留膜層優(yōu)秀性能的高效的后處理技術(shù)仍是亟待解決的技術(shù)問題。
7 結(jié)論與展望
微缺陷導(dǎo)致金屬防護(hù)層過早失效、誘發(fā)基材局部腐蝕,是當(dāng)今金屬防護(hù)技術(shù)開發(fā)與應(yīng)用中面臨的共性問題。本文基于微缺陷在金屬防護(hù)層中存在的普遍性,針對(duì)鎂合金微弧氧化膜中的微缺陷問題展開了討論,內(nèi)容涵蓋了微缺陷的形成及其影響因素、微缺陷對(duì)膜層性能及應(yīng)用的影響、微缺陷的識(shí)別技術(shù)、后處理手段等方面。在鎂合金微弧氧化膜及其他金屬防護(hù)層缺陷問題的未來研究中,開展下列工作具有重要的意義。
(1) 開展微缺陷的多層次、跨尺度的識(shí)別與研究。微缺陷的存在會(huì)導(dǎo)致微弧氧化膜結(jié)構(gòu)的非均勻性,這種微觀性質(zhì)的非均勻性也會(huì)導(dǎo)致膜層宏觀性質(zhì)的變化。因此,對(duì)微弧氧化膜物理結(jié)構(gòu)與化學(xué)構(gòu)造展開多層次、跨尺度的識(shí)別與研究是基礎(chǔ)與關(guān)鍵,有助于從源頭揭示微缺陷的作用機(jī)制。此外,應(yīng)聯(lián)合利用多種現(xiàn)代分析測(cè)試技術(shù),全面揭示微缺陷誘發(fā)的微弧氧化膜失效和基材局部腐蝕機(jī)理。
(2) 加強(qiáng)對(duì)微缺陷的合理利用及再處理技術(shù)的研究。對(duì)于鎂合金微弧氧化膜而言,現(xiàn)有的微缺陷處理技術(shù)仍無法滿足大多數(shù)工業(yè)應(yīng)用的要求。因此,有必要進(jìn)一步加強(qiáng)對(duì)微弧氧化膜微缺陷處理技術(shù)的開發(fā)。另外,如何進(jìn)一步利用微缺陷以達(dá)到某種科學(xué)研究與工程應(yīng)用目的,也是值得研究的問題。
(3) 研發(fā)動(dòng)態(tài)感知微缺陷的實(shí)時(shí)傳感技術(shù)。微缺陷的形成與微弧氧化工藝參數(shù)密切相關(guān),因此,在生產(chǎn)階段實(shí)現(xiàn)對(duì)微缺陷的及時(shí)調(diào)控將有利于從源頭實(shí)現(xiàn)對(duì)微缺陷的控制。研發(fā)動(dòng)態(tài)感知微缺陷的實(shí)時(shí)傳感技術(shù),用于微弧氧化膜制備過程中的實(shí)時(shí)監(jiān)檢測(cè),將有利于在生產(chǎn)階段實(shí)現(xiàn)對(duì)微弧氧化膜質(zhì)量的實(shí)時(shí)控制與精準(zhǔn)調(diào)節(jié),也將有利于推動(dòng)材料智能制造 (如3D打印) 技術(shù)水平的提升。
(4) 強(qiáng)化對(duì)金屬防護(hù)層中微缺陷問題的重視程度。鎂合金微弧氧化膜是眾多金屬防護(hù)層體系微缺陷問題的典型代表,在其他金屬防護(hù)層中,微缺陷也普遍存在,且其對(duì)防護(hù)層體系性質(zhì)、性能的影響也是不容忽視的。強(qiáng)化對(duì)金屬防護(hù)層中微缺陷的關(guān)注,建立相應(yīng)的微缺陷檢測(cè)評(píng)估及度量標(biāo)準(zhǔn),完善材料服役過程中微缺陷檢測(cè)網(wǎng)絡(luò)的建立,將對(duì)金屬防護(hù)層的設(shè)計(jì)優(yōu)化及科學(xué)使用帶來積極的推動(dòng)作用。
參考文獻(xiàn)
1 Sander G, Tan J, Balan P, et al. Corrosion of additively manufactured alloys: A review [J]. Corrosion, 2018, 74: 1318
2 McCafferty E. Introduction to Corrosion Science [M]. New York: Springer, 2009
3 Hu G X, Cai X, Rong Y H. Fundamental of Materials Science [M]. Shanghai: Shanghai Jiaotong University Press, 2010
3 胡賡祥, 蔡珣, 戎詠華. 材料科學(xué)基礎(chǔ) [M]. 上海: 上海交通大學(xué)出版社, 2010
4 Lin Y Z, Yang D J. Corrosion and Corrosion Control Principle [M]. Beijing: Sinopec Press, 2007
4 林玉珍, 楊德鈞. 腐蝕和腐蝕控制原理 [M]. 北京: 中國石化出版社, 2007
5 Wang Y C, Zhou F, Ge Y F, et al. Recent progress on the surface modification and protection of magnesium alloys [J]. Mater. China, 2020, 39: 100
5 王悅存, 周凡, 葛延峰等. 鎂合金表面改性與防護(hù)研究進(jìn)展 [J]. 中國材料進(jìn)展, 2020, 39: 100
6 Liu Y, Liu S M, Yu L P, et al. Summary on corrosion behavior and micro-arc oxidation for magnesium alloys [J]. J. Chin. Soc. Corros. Prot., 2015, 35: 99
6 劉胤, 劉時(shí)美, 于魯萍等. 鎂合金的腐蝕與微弧氧化膜層研究 [J]. 中國腐蝕與防護(hù)學(xué)報(bào), 2015, 35: 99
7 Cui X J, Ping J. Research progress of microarc oxidation for corrosion prevention of Mg-alloys [J]. J. Chin. Soc. Corros. Prot., 2018, 38: 87
7 崔學(xué)軍, 平靜. 微弧氧化及其在鎂合金腐蝕防護(hù)領(lǐng)域的研究進(jìn)展 [J]. 中國腐蝕與防護(hù)學(xué)報(bào), 2018, 38: 87
8 Darband G B, Aliofkhazraei M, Hamghalam P, et al. Plasma electrolytic oxidation of magnesium and its alloys: Mechanism, properties and applications [J]. J. Magnes. Alloy., 2017, 5: 74
9 Véliz B, Bermejo S, Orpella A, et al. Impedance modeling of silica nanoparticle metal insulator metal capacitors [J]. Electrochim. Acta, 2018, 280: 62
10 Ranade S, Forsyth M, Tan M Y J. The initiation and propagation of coating morphological and structural defects under mechanical strain and their effects on the electrochemical behaviour of pipeline coatings [J]. Prog. Org. Coat., 2017, 110: 62
11 Su Y Y, Li K Z, Hou X H, et al. Surface defects repairing of sprayed Ca-P coating by the microwave-hydrothermal method [J]. Ceram. Int., 2018, 44: 21699
12 Wang H W, Stack M M, Lyon S B, et al. The corrosion behaviour of macroparticle defects in arc bond-sputtered CrN/NbN superlattice coatings [J]. Surf. Coat. Technol., 2000, 126: 279
13 Xu P, Zhang C, Wang W, et al. Pitting mechanism in a stainless steel-reinforced Fe-based amorphous coating [J]. Electrochim. Acta, 2016, 206: 61
14 Zhang C, Chan K C, Wu Y, et al. Pitting initiation in Fe-based amorphous coatings [J]. Acta Mater., 2012, 60: 4152
15 Song G, Atrens A, St John D, et al. The anodic dissolution of magnesium in chloride and sulphate solutions [J]. Corros. Sci., 1997, 39: 1981
16 Cao C N. Principles of Electrochemistry of Corrosion [M]. Beijing: Chemical Industry Press, 2008
16 曹楚南. 腐蝕電化學(xué)原理 [M]. 北京: 化學(xué)工業(yè)出版社, 2008
17 Zhang Y J, Yan C W, Wang F H, et al. Electrochemical behavior of anodized Mg alloy AZ91D in chloride containing aqueous solution [J]. Corros. Sci., 2005, 47: 2816
18 Wang S X, Peng H L, Shao Z S, et al. Sealing of anodized aluminum with phytic acid solution [J]. Surf. Coat. Technol., 2016, 286: 155
19 Deflorian F, Fedrizzi L, Rossi S, et al. Defect dimension evaluation in organic coated galvanized steel by electrochemical impedance spectroscopy [J]. J. Appl. Electrochem., 2002, 32: 921
20 Gupta G, Birbilis N, Cook A B, et al. Polyaniline-lignosulfonate/epoxy coating for corrosion protection of AA2024-T3 [J]. Corros. Sci., 2013, 67: 256
21 Liu M M. The effect of sealing treatment on the corrosion and erosion-corrosion of high-velocity oxy-fuel Fe-based amorphous coating [D]. Shenyang: University of Science and Technology of China, 2019
21 劉明明. 封孔處理對(duì)HVOF鐵基非晶涂層的腐蝕和沖蝕行為的影響研究 [D]. 沈陽: 中國科學(xué)技術(shù)大學(xué), 2019
22 Guo J W. Microstructure and corrosion degradation behavior of magnesium alloy with microarc oxidation and hydrothermal process treated [D]. Harbin: Harbin Institute of Technology, 2019
22 郭君巍. 微弧氧化及水熱復(fù)合改性鎂合金的組織與腐蝕降解行為 [D]. 哈爾濱: 哈爾濱工業(yè)大學(xué), 2019
23 Wang H B, Fang Z G, Jiang B L. Microarc Oxidation Technology and Its Applications in Sea Environments [M]. Beijing: National Defense Industry Press, 2010
23 王虹斌, 方志剛, 蔣百靈. 微弧氧化技術(shù)及其在海洋環(huán)境中的應(yīng)用 [M]. 北京: 國防工業(yè)出版社, 2010
24 Walsh F C, Low C T J, Wood R J K, et al. Plasma electrolytic oxidation (PEO) for production of anodised coatings on light weight metal (Al, Mg, Ti) alloys [J]. Trans. IMF, 2009, 87: 122
25 Ma X, Blawert C, H che D, et al. A model describing the growth of a PEO coating on AM50 Mg alloy under constant voltage mode [J]. Electrochim. Acta, 2017, 251: 461
26 Chen H, Wang C C, Kang Y B, et al. Research status of micro-arc oxidation of magnesium alloy [J]. Surf. Technol., 2019, 48(7): 49
26 陳宏, 王成成, 康亞斌等. 鎂合金微弧氧化的研究現(xiàn)狀 [J]. 表面技術(shù), 2019, 48(7): 49
27 Wang R Q, Wu Y K, Wu G R, et al. An investigation about the evolution of microstructure and composition difference between two interfaces of plasma electrolytic oxidation coatings on Al [J]. J. Alloy. Compd., 2018, 753: 272
28 Cakmak E, Tekin K C, Malayoglu U, et al. The effect of substrate composition on the electrochemical and mechanical properties of PEO coatings on Mg alloys [J]. Surf. Coat. Technol., 2010, 204: 1305
29 Dou J H. Preparation and corrosion resistance of degradable composite coating on magnesium alloy for orthopedics [D]. Ji’nan: Shandong University, 2018
29 竇金河. 醫(yī)用鎂合金表面可降解復(fù)合膜層的制備及其耐蝕性的研究 [D]. 濟(jì)南: 山東大學(xué), 2018
30 Song Y L, Liu Y H, Yu S R, et al. Plasma electrolytic oxidation coating on AZ91 magnesium alloy modified by neodymium and its corrosion resistance [J]. Appl. Surf. Sci., 2008, 254: 3014
31 Muhaffel F, Mert F, Cimenoglu H, et al. Characterisation and corrosion behaviour of plasma electrolytic oxidation coatings on high pressure die cast Mg-5Al-0.4Mn-xCe (x=0, 0.5, 1) alloys [J]. Surf. Coat. Technol., 2015, 269: 200
32 Yoo B, Shin K R, Hwang D Y, et al. Effect of surface roughness on leakage current and corrosion resistance of oxide layer on AZ91 Mg alloy prepared by plasma electrolytic oxidation [J]. Appl. Surf. Sci., 2010, 256: 6667
33 Wang Y, Lu D H, Wu G L, et al. Effect of laser surface remelting pretreatment with different energy density on MAO bioceramic coating [J]. Surf. Coat. Technol., 2020, 393: 125815
34 Wang L Q, Zhou J S, Liang J, et al. Microstructure and corrosion behavior of plasma electrolytic oxidation coated magnesium alloy pre-treated by laser surface melting [J]. Surf. Coat. Technol., 2012, 206: 3109
35 Gheytani M, Aliofkhazraei M, Bagheri H R, et al. Wettability and corrosion of alumina embedded nanocomposite MAO coating on nanocrystalline AZ31B magnesium alloy [J]. J. Alloy. Compd., 2015, 649: 666
36 Chen L L, Gu Y H, Liu L, et al. Effect of ultrasonic cold forging technology as the pretreatment on the corrosion resistance of MAO Ca/P coating on AZ31B Mg alloy [J]. J. Alloy. Compd., 2015, 635: 278
37 Wei Z, Ma B J, Li L, et al. Effect of ultrasonic rolling pretreatment on corrosion resistance of micro-arc oxidation coating of Mg-alloy [J]. J. Chin. Soc. Corros. Prot., 2021, 41: 117
37 魏征, 馬保吉, 李龍等. 鎂合金表面超聲滾壓預(yù)處理對(duì)微弧氧化膜耐蝕性能的影響 [J]. 中國腐蝕與防護(hù)學(xué)報(bào), 2021, 41: 117
38 Hussein R O, Zhang P, Nie X, et al. The effect of current mode and discharge type on the corrosion resistance of plasma electrolytic oxidation (PEO) coated magnesium alloy AJ62 [J]. Surf. Coat. Technol., 2011, 206: 1990
39 Cui X J, Wang R, Wei J S, et al. Effect of electrical parameters on micromorphology and corrosion resistance of micro-arc oxidation coating on AZ31B Mg alloy [J]. J. Chin. Soc. Corros. Prot., 2014, 34: 495
39 崔學(xué)軍, 王榮, 魏勁松等. 電參數(shù)對(duì)AZ31B鎂合金微弧氧化膜微觀形貌及耐蝕性的影響 [J]. 中國腐蝕與防護(hù)學(xué)報(bào), 2014, 34: 495
40 Zou B, Lü G H, Zhang G L, et al. Effect of current frequency on properties of coating formed by microarc oxidation on AZ91D magnesium alloy [J]. Trans. Nonferrous Met. Soc., 2015, 25: 1500
41 Liu F, Yu J, Song Y W, et al. Effect of potassium fluoride on the in-situ sealing pores of plasma electrolytic oxidation film on AM50 Mg alloy [J]. Mater. Chem. Phys., 2015, 162: 452
42 Ryu H S, Mun S J, Lim T S, et al. Microstructure evolution during plasma electrolytic oxidation and its effects on the electrochemical properties of AZ91D Mg alloy [J]. J. Electrochem. Soc., 2011, 158: C266
43 Pak S N, Yao Z P, Ju K S, et al. Effect of organic additives on structure and corrosion resistance of MAO coating [J]. Vacuum, 2018, 151: 8
44 Zhang Y, Chen F, Zhang Y, et al. Influence of graphene oxide additive on the tribological and electrochemical corrosion properties of a PEO coating prepared on AZ31 magnesium alloy [J]. Tribol. Int., 2020, 146: 106135
45 Gu Y H, Bandopadhyay S, Chen C F, et al. Effect of oxidation time on the corrosion behavior of micro-arc oxidation produced AZ31 magnesium alloys in simulated body fluid [J]. J. Alloy.Compd., 2012, 543: 109
46 Tang J W, Shao Y W, Zhang T, et al. Effect of cyclic pressure on degradation Behavior of epoxy coating in simulated deep ocean environment [J]. J. Chin. Soc. Corros. Prot., 2011, 31: 275
46 唐俊文, 邵亞薇, 張濤等. 循環(huán)壓力對(duì)環(huán)氧涂層在模擬深海環(huán)境中失效行為的影響 [J]. 中國腐蝕與防護(hù)學(xué)報(bào), 2011, 31: 275
47 Wang Y, Huang Z Q, Yan Q, et al. Corrosion behaviors and effects of corrosion products of plasma electrolytic oxidation coated AZ31 magnesium alloy under the salt spray corrosion test [J]. Appl. Surf. Sci., 2016, 378: 435
48 Chen Z N, Ji H T, Geng X Q, et al. 3-D distribution characteristics of the micro-defects in the PEO coating on ZM6 mg-alloy during corrosion [J]. Corros. Sci., 2020, 174: 108821
49 Chen Y L. Corrosion Control and Strength Assessment of Naval Aircraft Structures [M]. Beijing: National Defense Industry Press, 2009
49 陳躍良. 海軍飛機(jī)結(jié)構(gòu)腐蝕控制及強(qiáng)度評(píng)估 [M]. 北京: 國防工業(yè)出版社, 2009
50 Fischerauer S F, Kraus T, Wu X, et al. In vivo degradation performance of micro-Arc-oxidized magnesium implants: A micro-CT study in rats [J]. Acta Biomater., 2013, 9: 5411
51 Xu H T, Hu T, Wang M L, et al. Degradability and biocompatibility of magnesium-MAO: The consistency and contradiction between in-vitro and in-vivo outcomes [J]. Arab. J. Chem., 2020, 13: 2795
52 Toorani M, Aliofkhazraei M, Mahdavian M, et al. Effective PEO/Silane pretreatment of epoxy coating applied on AZ31B Mg alloy for corrosion protection [J]. Corros. Sci., 2020, 169: 108608
53 Bordbar-Khiabani A, Yarmand B, Mozafari M. Functional PEO layers on magnesium alloys: Innovative polymer-free drug-eluting stents [J]. Surf. Innov., 2018, 6: 237
54 Zhang X, Aliasghari S, Němcová A, et al. X-ray computed tomographic investigation of the porosity and morphology of plasma electrolytic oxidation coatings [J]. ACS Appl. Mater. Interfaces, 2016, 8: 8801
55 Lu X P, Blawert C, Tolnai D, et al. 3D reconstruction of plasma electrolytic oxidation coatings on Mg alloy via synchrotron radiation tomography [J]. Corros. Sci., 2018, 139: 395
56 Zhao P X, Wu W, Dan Y. Application of spatial-resolution technology for in-situ monitoring of metal corrosion [J]. J. Chin. Soc. Corros. Prot., 2020, 40: 495
56 趙鵬雄, 武瑋, 淡勇. 空間分辨技術(shù)在金屬腐蝕原位監(jiān)測(cè)中的應(yīng)用 [J]. 中國腐蝕與防護(hù)學(xué)報(bào), 2020, 40: 495
57 Mingo B, Guo Y, Němcová A, et al. Incorporation of halloysite nanotubes into forsterite surface layer during plasma electrolytic oxidation of AM50 Mg alloy [J]. Electrochim. Acta, 2019, 299: 772
58 Zhang S D, Wu J, Qi W B, et al. Effect of porosity defects on the long-term corrosion behaviour of Fe-based amorphous alloy coated mild steel [J]. Corros. Sci., 2016, 110: 57
59 Friedemann A E R, Thiel K, Ha linger U, et al. Investigations into the structure of PEO-layers for understanding of layer formation [J]. Appl. Surf. Sci., 2018, 443: 467
60 Karavai O V, Bastos A C, Zheludkevich M L, et al. Localized electrochemical study of corrosion inhibition in microdefects on coated AZ31 magnesium alloy [J]. Electrochim. Acta, 2010, 55: 5401
61 Pilbáth A, Szabó T, Telegdi J, et al. SECM study of steel corrosion under scratched microencapsulated epoxy resin [J]. Prog. Org. Coat., 2012, 75: 480
62 Huang V M, Wu S L, Orazem M E, et al. Local electrochemical impedance spectroscopy: A review and some recent developments [J]. Electrochim. Acta, 2011, 56: 8048
63 J ensson M, Thierry D, Lebozec N. The influence of microstructure on the corrosion behaviour of AZ91D studied by scanning Kelvin probe force microscopy and scanning Kelvin probe [J]. Corros. Sci., 2006, 48: 1193
64 Wang W, Zhang X, Wang J. Heterogeneous electrochemical characteristics of biofilm/metal interface and local electrochemical techniques used for this purpose [J]. Mater. Corros., 2009, 60: 957
65 Jiang M, Chai Y S, Zhou J, et al. Temperature field distribution of micro-arc oxidation process based on COMSOL [J]. Surf. Technol., 2017, 46(5): 17
65 姜曼, 柴永生, 周京等. 基于COMSOL的微弧氧化過程溫度場(chǎng)分布研究 [J]. 表面技術(shù), 2017, 46(5): 17
66 Ma X, Blawert C, H che D, et al. Investigation of electrode distance impact on PEO coating formation assisted by simulation [J]. Appl. Surf. Sci., 2016, 388: 304
67 Ma X, Blawert C, H che D, et al. Simulation assisted investigation of substrate geometry impact on PEO coating formation [J]. Surf. Coat. Technol., 2018, 350: 281
68 Peng F, Wang D, Tian Y, et al. Sealing the pores of PEO coating with Mg-Al layered double hydroxide: enhanced corrosion resistance, cytocompatibility and drug delivery ability [J]. Sci. Rep., 2017, 7: 8167
69 Liu P, Liu Q F, Huang D Q, et al. Research progress of pore sealing technology for micro-arc oxidation films [J]. Surf. Technol., 2019, 48(7): 61
69 劉朋, 劉群峰, 黃德群等. 微弧氧化膜封孔技術(shù)研究進(jìn)展 [J]. 表面技術(shù), 2019, 48(7): 61
70 Duan H P, Du K Q, Yan C W, et al. Electrochemical corrosion behavior of composite coatings of sealed MAO film on magnesium alloy AZ91D [J]. Electrochim. Acta, 2006, 51: 2898
71 Zeng D P, Liu Z Y, Bai S, et al. Influence of sealing treatment on the corrosion resistance of PEO coated Al-Zn-Mg-Cu alloy in various environments [J]. Coatings, 2019, 9: 867
72 Yang J J, Blawert C, Lamaka S V, et al. Corrosion protection properties of inhibitor containing hybrid PEO-epoxy coating on magnesium [J]. Corros. Sci., 2018, 140: 99
73 Li Z X, Yang W B, Yu Q L, et al. New method for the corrosion resistance of AZ31 Mg alloy with a porous micro-arc oxidation membrane as an ionic corrosion inhibitor container [J]. Langmuir, 2019, 35: 1134
74 Ivanou D K, Yasakau K A, Kallip S, et al. Active corrosion protection coating for a ZE41 magnesium alloy created by combining PEO and sol-gel techniques [J]. RSC Adv., 2016, 6: 12553
免責(zé)聲明:本網(wǎng)站所轉(zhuǎn)載的文字、圖片與視頻資料版權(quán)歸原創(chuàng)作者所有,如果涉及侵權(quán),請(qǐng)第一時(shí)間聯(lián)系本網(wǎng)刪除。
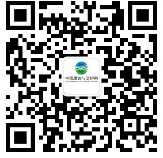
官方微信
《中國腐蝕與防護(hù)網(wǎng)電子期刊》征訂啟事
- 投稿聯(lián)系:編輯部
- 電話:010-62316606-806
- 郵箱:fsfhzy666@163.com
- 中國腐蝕與防護(hù)網(wǎng)官方QQ群:140808414