0 前言
熱噴涂是將一種粉末或絲狀的材料在不同熱源中進行加熱至熔化或軟化態,然后在高速氣流的推動下加速噴到基材表面,凝固后形成具有耐腐蝕、耐熱、耐磨、抗氧化等良好性能的防護涂層加工技術[1]。依據不同熱源形式,熱噴涂技術可分為火焰噴涂、電弧噴涂、爆炸噴涂、等離子噴涂以及其他形式的噴涂技術,另外,當推動氣體溫度較低時,載體氣體加速粒子達到超音速后使其在基材表面發生塑性變形也可以形成涂層,即所謂的冷噴涂技術[2]。熱噴涂技術具有基材和噴涂材料選擇多、噴涂工藝種類多、涂層厚度可從微米級到厘米級、可制備復合材料的涂層、甚至可用于增材制造等優點[3], 從1920年該技術出現到現在,一直是制造業備受關注的方向。在我國熱噴涂的發展始于國防軍工行業, 特別是在導彈、火箭、衛星、坦克零部件及航空發動機葉片、噴火筒、導彈滑軌等部位有重要的應用,后來逐步發展到民用產品,已在電力、冶金、礦采、紡織、印刷、鐵路、醫療、海洋裝備等多個領域得到廣泛的應用[4-7],已成為典型的軍民兩用技術。
但是,任何技術的發展也需要隨著使用要求的提高和社會的進步等因素的影響而不斷前進,在軍事領域這種趨勢往往表現得更為明顯。鑒于此,本文的目的是在總結近年來熱噴涂技術在典型武器裝備的研究應用現狀的基礎上,從技術層面分析了影響熱噴涂發展的關鍵共性技術問題,并展望了該技術在軍事領域的應用前景,尤其是用于增材制造和再制造領域的可行性。
1 航空裝備的防護涂層應用
1.1 航空發動機葉片的熱防護
等離子噴涂技術是利用等離子弧將噴涂材料進行加熱、加速,在基材表面沉積涂層的工藝技術[8], 是目前熱噴涂技術中能量密度較大、噴涂溫度較高的工藝技術之一,也正因其超高溫特性,在熱噴涂應用中可噴涂高熔點材料[9-10]。
隨著航空發動機結構的優化和技術的進步,其內部工作溫度也不斷攀升。目前先進發動機燃燒室高溫區溫度在2 000℃ 左右,其壓氣機出氣溫度高達650℃ 以上,渦輪進氣匣氣流溫度達到1 700℃ 左右[11-12]。因此,現階段普遍采用鈦合金、鎳合金等合金材料制造相關零部件,但依舊存在高溫失效的“卡脖子”問題[13-14]。另外,研究證實改變基材材料只能輕微幅度提升耐溫值,仍不能突破溫度的上限問題。
等離子熱噴涂熱障涂層是航空航天領域應用相對完善的一種表面修復與強化工藝技術[15],其運用等離子噴涂工藝噴涂耐高溫陶瓷涂層在基材表面, 利用陶瓷涂層阻遏基材的高溫反應,涂層隔熱作用提升了熱端部件的耐溫性能[16-17]。例如,Honeywell公司研究的渦輪導向器采用等離子噴涂一種新型熱障涂層,并計劃應用于新型無人機和直升機等航空武器裝備。
為提高發動機效率,在高壓渦輪葉片的葉尖上采用控制葉尖與機匣間隙的立方氮化硼(CBN) 涂層,當間隙縮小125 μm時,耗油率可降低0.5%。美國關于CBN涂層新舊技術的對比表明,抗氧化層目前采用等離子噴涂CoNiCrAlY涂層[18-20],改進型CBN涂層則在此基礎上加入鉿、硅或錸。目前的涂層基材為電鍍NiCoCrAl, 而改進型CBN則為在NiCoCrAlY中加入鉿、硅或錸。目前采用的磨粒為多晶CBN,而改進型則為帶尖角的單晶。以往的擴散層采用鋁化物涂層,而新涂層則采用雙鋁化物或鉑鋁涂層[21]。采用這種新型氮化硼葉尖涂層,可顯著改進涂層抗氧化性,延長涂層壽命。
1.2 飛機起落架的替代鍍鉻技術
為了解決飛機起落過程中受到較大的沖擊載荷與磨損,實際應用中往往在起落架液壓桿表面鍍硬鉻層。但鍍鉻層的硬度會隨時間不斷下降,因此起落架的壽命維持不盡人意,報廢周期短,且鍍鉻工藝因污染環境被列入嚴格限制的技術。針對其工況與技術要求,現階段國內外通常通過超音速火焰噴涂技術實現起落架的表面修復與強化。有研究表明, WC-Co金屬陶瓷作為噴涂材料修復工件,修復后涂層相較于原鍍鉻層硬度提升50%,修復再制造后的零件使用壽命比傳統的鍍鉻零件顯著增長,經濟效益顯著[22]。
1.3 直升機的冷噴涂防護應用
美軍在2012年曾公布,將美國陸軍研究實驗室經過多年研究開發的冷噴涂等技術應用于直升機防沙塵沖蝕和腐蝕結構修復,可大幅度降低直升機維護成本。具體是在直升機旋翼漿葉的前緣利用高速火焰噴涂技術涂覆碳化鎢-鈷涂層,在直升機旋翼漿葉前緣以外的區域冷噴涂鈮涂層,這種涂層可以承受沙漠地區惡劣環境。
美軍還正在軍用直升機其他主要部件上進行冷噴涂技術腐蝕防護應用研究,特別是對鎂合金主傳動裝置和尾槳變速箱體等的腐蝕結構進行冷噴涂修復。研究表明, 采用這種冷噴涂防護技術, 在ZE41A、AZ31B和AZ91D鎂合金表面沉積0.30~0.375mm純鋁涂層,耐鹽霧腐蝕時間達1 000h左右,應用于直升機鎂合金傳動箱,可使傳動箱的腐蝕防護性能提高約22%,運營與維護成本減少15%。
2 武器裝備的隱身涂層應用
隱身技術是降低目標可探測性、完善防空武器體系、提高縱深打擊能力的重要手段,在武器裝備表面涂覆隱身材料是目前使用最多、最有效的技術之一[23]常隱身涂層包括雷達波隱身、紅外隱身、激光隱身、聲納隱身和兼容性隱身(可稱多功能隱身)等涂層,目前,隱身涂層技術正朝著多頻譜、寬頻帶的方向發展[24]。
隱身涂層的制備較多地采用粘結劑復合隱身材料以涂刷的形式實現涂覆,也有采用溶膠-凝膠或化學鍍的方式制備涂層。近幾年,人們發現采用熱噴涂的方法在制備隱身涂層方面具有很大的潛力[25]。因為噴涂粒子在工藝過程中能獲得高動能、高熱能,并在基材表面沉積高質量涂層,使粒子與基材緊密結合,同時涂層厚度可調控。除此之外,無機陶瓷粉末涂層具有優越的隔熱效果和硬度[26-29],綜上,熱噴涂工藝在耐高溫吸波材料制備涂層領域具有很大的發展潛力。例如,YUAN等[30] 通過低溫高速火焰噴涂技術在Al基材沉積 α-Fe/環氧樹脂復合材料粒子,成功制備了含量為70%的 α-Fe、厚度為1.5mm的涂層,并檢測發現在12.8~14.5GHz頻段內其反射率為-10dB, 頻寬為2.65GHz。 B?GARD等[31] 分析了由大氣等離子噴涂制備的BaCoTiFe10O9 涂層,結果表明大氣等離子噴涂制成的涂層在電磁波吸收方面有廣闊的前景。另外, NANOBASHVILI等[32] 通過水穩等離子噴涂技術沉積B4C涂層,其優越的微波吸收能力主要體現在35GHz頻率下,且吸收比例高達82%。
3 艦船裝備的防腐與防滑非晶涂層應用
防滑涂層對大型艦船的人員安全以及艦載機作業,尤其是艦船飛行甲板作業有著非常重要的作用, 飛行甲板防護涂層的好壞直接影響載機艦(如航母、兩棲攻擊艦等大型艦船) 的在航率和飛機起降架次率,是使用要求最高、磨損率最高的一類防滑涂層。以美國為例,美國海軍目前有10艘航空母艦在役,每年有近34.4萬m 2 的艦艇表面需要使用防滑涂料,費用在5 600萬美元以上;當前的使用壽命僅18個月,維護和更換不僅影響防滑表面的使用,而且耗費巨大。因此,載機艦飛行甲板防滑涂層的研究一直是航母使用國關注的重點。
現役海軍大型艦船上應用的甲板和艙室涂層材料絕大多數采用樹脂基涂料[33],也有少部分采用金屬基材料[34],而金屬基涂層普遍有耐磨、不發生老化、摩擦因數穩定、與基底結合力強、施工和高溫下不會揮發有毒氣體等優點。在金屬基涂層中,近年來新發展的熱噴涂非晶態金屬基涂層非常值得關注[35-36]。非晶態金屬的原子整體上排列無規律,具有短程有序、長程無序的特點,沒有位錯、晶界、相界等傳統晶態金屬的固有缺陷。因此,非晶態金屬基涂層與傳統的金屬基涂層相比,具有強度高、質量輕、耐腐蝕、耐磨損等特點。
美國國防部高級研究計劃局(DARPA)聯合能源部開啟“高性能防腐材料”項目,該項目以研發硬度極高的非晶態鐵基金屬材料為目標,將其作為惡劣環境中的腐蝕防護的噴涂材料。在項目進展中研制出兩種非晶態鐵基金屬材料,命名為SAM2X5、 SAM1651(或稱SAM7)。其耐腐蝕性相比于最優質不銹鋼及Ni金屬可提高至4至5倍,且有更好的耐磨損性能[37]。另外,研究人員在超音速火焰噴涂工藝下制備的SAM2X5與SAM7非晶涂層,并采用Triga核反應器做中子吸收能力檢測,科研人員發現SAM2X5和SAM7中子吸收能力極高(最優質不銹鋼及Ni基合金的7倍、硼鋼的3倍)。另外,鐵基非晶涂層在較強的中子輻射工況中表現出穩定的非晶結構,預測以上兩種非晶涂層能有效安全地儲存4 000~10 000年,在運輸核廢料和安全儲存方面也存在巨大的應用前景。
綜上所述,高性能防腐材料的研究取得階段性成果,隨后以DARPA為首又啟動了“海軍先進非晶涂層”(NAAC) 項目[38],采用熱噴涂技術制備出有紋理的非晶態金屬涂層,其具有摩擦系數高,耐磨損等特點,綜合性能超過現有的防滑涂層體系,將其應用在“近海戰斗艦”的濕態任務區甲板[39-40]。 “近海戰斗艦”的濕態任務區是位于艦艉的寬大艙室,主要用于剛性充氣艇的收放,需要間歇性接觸海水,還會遭受小艇收放時對甲板產生的磨損,因此被認為是檢驗涂層防滑、耐磨和耐腐蝕性的合適平臺。 A&A熱噴涂公司是NAAC研發項目的成員單位之一,該公司公布開發的非晶態金屬涂層于2009年展開了試驗艦的應用測試,其中包括大型艦船的飛行甲板,目前該應用研究方向還在持續推進當中[41]。
非晶態金屬基涂層具有優于樹脂基和晶態金屬基涂層的綜合性能,尤其是具有超長的使用壽命,可以大大減少艦艇涂層維護更換時間和費用,提高艦艇在航率。一旦在施工效率上和涂層綜合質量上進一步突破,則可在海軍艦艇上大規模推廣應用。
4 熱噴涂在增材制造領域的應用
4.1 增材制造技術展現巨大軍事應用潛力
3 D打印(或稱增材制造)的概念最早由美國麻省理工學院在20 世紀90 年代初提出。 21 世紀以來,3D打印技術得到迅速發展,引起了持續的關注[42-43]。英國學者認為,3D打印技術和數字化生產模式將納入第三次科技革命范疇,成為新工業革命的強大推動力;2012 年,以美國DARPA為首構建的國家增材制造科研機構,將增材制造技術列入革新美國制造業首位技術,全力推動這項技術深入探索和廣泛普及, 推進武器裝備的快速設計、制造及維修。
2012年,洛克希德·馬丁公司采用電子束增材制造技術,實現3m長的F-35機翼鈦合金零部件成型。中國王華明院士團隊也曾利用激光熔覆技術成功打印出飛機用大型鈦合金結構件[44]。通用電氣公司將增材制造技術應用于制造發動機葉片,其中加工1.22m長的鈦合金零件促使每臺發動機成本減削2.5萬美元。密歇根大學開發出的增材制造設備可滿足戰場部署需求,能夠迅速高效地完成受損葉片等發動機零部件的修復工作。美國材料試驗協會(ASTM) 國際委員會針對Ti-6Al-4V的增材制造方法制定了F2924-12標準[45]。這是第一個增材制造的材料標準,對推動其廣泛普及具有重要意義。波音、通用電氣等大型企業都致力于將此技術應用到實際生產中。波音公司運用增材制造技術生產了F-15、F-18等軍用飛機以及民用飛機共計10類產品的零部件。此外,美國海軍已決定運用增材制造技術制造某型水聲換能器超過50%部件。美國國家航空航天局(NASA)正在將3D打印技術廣泛應用于新一代重型運載火箭—“航天發射系統”(SLS)的研制中[46],包括利用3D打印機制造系統零件等。
3 D打印技術面臨的多方面問題和挑戰至今仍未得到突破性進展。一是成本方面,較為昂貴的3D打印設備延緩了其普及應用的趨勢。二是成型材質方面,化學聚合物為3D打印主流成型材料,在此基礎上的成品模型物理性能不高,在安全方面也存在短板,金屬材料的3D打印目前還存在很多技術難題,材料適用面不夠廣。三是精度、速度和效率方面,逐層打印不能有效保證3D打印的精度要求;低下的工作效率不能有效普及在大規模生產中,除此之外,由于工作原理限制,兼顧精度與速度問題在目前仍沒有有效的解決。四是產業產權方面,現有的知識產權保護機制不能解決普及3D打印技術出現的產品復制和產品擴散問題,制造業面對的盜版風險大增,難以適應未來市場需求變化和技術發展趨勢。
4.2 熱噴涂增材制造的優勢應用方向
學界大量的注意力集中在3D打印,打印材料早些年以塑料為主,近些年以金屬和陶瓷材料為主的3D打印技術也得到了快速發展。其中除了基于激光束、電子束等高能束流的金屬和陶瓷3D打印技術之外,熱噴涂(包括冷噴涂)技術也是3D打印技術的一個發展分支,在實現特定條件的厚成形、特種材料的零件直接制造等特殊領域表現出了獨特的優勢,從而受到越來越多的關注,尤其是在對噴涂厚成形、材料、成形機理及關鍵技術等方面開展了較多的基礎性研究工作。例如冷噴涂區別于激光3D打印工藝,具有避免高溫化學反應、粒子選擇范圍廣、成本低等優勢[47-50]。當前,國外有關于冷噴涂增材制造銅、鈦和不銹鋼零件的相關研究,研究涂層厚度大于5mm的銅塊材抗拉強度達200MPa,達到其鑄態組織的強度[51]。美軍陸軍研究室協同南達科他礦業及理工學院研發新一代混合冷噴涂系統,并期望將此技術延伸至國防領域。除此之外,具有優秀厚成形能力的鐵基非晶涂層也成為了目前的一個研究重點, BRANAGAN等[52] 利用電弧噴涂技術以6.35mm的碳鋼平板為基材、SHS7170粉芯絲為噴涂材料制備了20mm厚的鐵基非晶納米晶涂層。
5 結論與展望
熱噴涂技術走過了近100年的發展歷程,雖然在噴涂材料、工藝及設備等方面均取得了長足的進步,面對日益增長的工業需求,該技術一定會繼續發展下去,在軍事領域也不例外。分析認為,今后關于熱噴涂技術的研究可主要集中在以下方面:
(1) 以具體軍事應用需求為牽引,開展先進涂層材料及噴涂設備工藝的開發。面對更多更廣泛的軍事應用領域,熱噴涂技術在新材料性能提升、涂層組織性能缺陷調控和新型設備開發等方面進行深入的研究工作,尤其是需要在涂層殘余應力、界面結合強度、組織結構缺陷等薄弱環節上取得技術突破。熱噴涂的工藝特點決定了涂層成形過程中產生的本征殘余應力(或稱固有應力、驟冷應力) 為拉應力, 這對于高性能涂層的制備及安全服役極為不利;在基體表面進行噴涂,通常形成的是一種典型的異質雙層或多層結構,特別是涂層/基體結合部位,通常以機械嵌合為主要的界面結合機制,該界面處的拉伸結合強度通常難以提升到百兆帕量級,進而嚴重限制了該技術的應用范圍;另外涂層微觀結構結構中的微孔隙和氧化夾雜等缺陷也會影響涂層材料性能的發揮。因此,亟待開發新工藝、新技術以實現涂層殘余應力的有效調控、界面結合強度的大幅提高、少缺陷甚至無缺陷的涂層組織的可控制備,進而拓展熱噴涂技術的應用領域。
(2) 充分挖掘熱噴涂在增材制造與再制造領域的應用潛力,開辟新領域。隨著智能制造的進一步發展成熟,新的信息技術、控制技術、材料技術等被廣泛應用到制造領域,3D打印技術也將被推向更高的層面。除將其引入商業市場擴大其產業化規模外,還大力拓展該技術在軍事領域中的應用。熱噴涂也需要充分利用這一發展契機,充分挖掘熱噴涂技術可以實現軍事領域3D打印和增材再制造的應用場合,掌握技術前沿、放眼未來開展前瞻性的技術開發和升級換代,以點帶面,以此引領該技術在制造領域的長久發展,以推動武器裝備保障模式和作戰樣式的發展進步。
參考文獻
[1] 梅雨菲,周寧,劉正欽,等.常用制備耐磨涂層的熱噴涂技術[J].教育現代化,2016(12):84-85.
MEI Yufei,ZHOU Ning,LIU Zhengqin,et al.Common technology on thermal spraying to prepare wear-resistant coatings [J].Education Modernization,2016(12):84-85.(in Chinese)
[2] YIN S,MORTEN M,LI W Y,et al.Gas flow,particle acceleration,and heat transfer in cold spray:A review [J].Journal of Thermal Spray Technology,2016,5:1-23.
[3] MEGHWAL A,ANUPAM A,MURTY B S,et al.Thermal spray high-entropy alloy coatings:A review [J].Journal of Thermal Spray Technology,2020,29(5):857-893.
[4] ANG A,AHMED R,BERNDT C C.Biomaterials:Thermal spray processes and applications[J].Journal of Thermal Spray Technology,2018,27(8):1205-1211.
[5] RAVI S A,JAGADEESWARA R C,VETRIVENDAN E,et al.Evaluation of thermal spray alumina coatings on nickel electrode connector for reprocessing applications[J].Transactions of the Indian Institute of Metals,2018,71(2):297-307.
[6] KHOSLA C,KAUR S,BALA N.Investigations of thermal sprayed HAP and HAP-TiO2 composite coatings for biomedical applications[J].Anti-corrosion Methods and Materials,2019,66(1):74-87.
[7] KANG A S,GREWAL,J S,CHEEMA G S.Effect of thermal spray coatings on wear behavior of high tensile steel applicable for tiller blades[J].Materials Today:Proceedings,2017,4(2):95-103.
[8] MARTIN J,AKODA K,NTOMPROUGKIDIS V,et al.Duplex surface treatment of metallic alloys combining cold-spray and plasma electrolytic oxidation technologies[J].Surface & Coatings Technology,2020,392(25):125756.
[9] MA X Q,CHO S,TAKEMOTO M.Acoustic emission source analysis of plasma sprayed thermal barrier coatings during four-point bend tests[J].Surface and Coatings Technology,2001,139:55-62.
[10] 吳濤,朱流,酈劍,等.熱噴涂技術與現狀及發展[J].國外金屬熱處理,2005,26(4):2-6.
WU Tao,ZHU Liu,LI Jian,et al.Research progress in thermal spray technology[J].Heat Treatment of Metals Abroad,2005,26(4):2-6.(in Chinese)
[11] 吳朝軍,吳曉峰,楊杰.熱噴涂技術在我國航天領域的應用 [J].金屬加工(熱加工),2009(18):23-26.
WU Chaojun,WU Xiaofeng,YANG Jie.Application of thermal spraying in the field of space flight in China[J].Machinist Metal Forming,2009(18):23-26.(in Chinese)
[12] TRAEGER F,AHRENS M,VABEN R,et al.A life time model for ceramic thermal barrier coatings[J].Materials Science and Engineering,2003,358(1-2):255-265.
[13] SHI Z W,WEI H,ZHANG H Y,et al.Characterization and crystallographic analyses of new three-fold Ti(O,C)nanotwins in a hot-pressed Nb-Ti-Al alloy[J].Materials Characterization,2019,139:56-62.
[14] ZHANG X,GAO H,WEN Z,et al.Low cycle fatigue failure analysis of a Ni-based single crystal superalloys at 850 ℃ [J].Advanced Engineering Materials,2019,21(2):1800647.
[15] LASHMIA P G,ANANTHAPADMANABHANB P V,UNNIKRISHNANC G,et al.Present status and future prospects of plasma sprayed multilayered thermal barrier coating systems [J].Journal of the European Ceramic Society,2020,40(8):2731-2745.
[16] MILLER R A.Thermal barrier coatings for aircraft engines:History and directions[J].Journal of Thermal Spray Technology,1997,6(1):35-42.
[17] WRIGHT P K,EVANS A G.Mechanisms governing the performance of thermal barrier coatings [J].Curr Opiu Solid State Mater Sci,1999,4(3):255-265.
[18] CHEN H,FAN M,ZHU W,et al.High temperature oxidation behaviour of combustion flame sprayed CoNiCrAlY coatings[J].Surface & Coatings Technology,2020,385:125431.
[19] CALIARI F R,MIRANDA F S,REIS D A P,et al.Supersonic plasma spray deposition of CoNiCrAlY coatings on Ti-6Al-4V alloy[J].Journal of Thermal Spray Technology,2017,26(5):880-889.
[20] JIANG J,ZHAO H,ZHOU X,et al.Oxidation resistance of vacuum plasma sprayed CoNiCrAlY coatings modified by filtered cathodic vacuum arc deposition aluminizing [J].Journal ofThermal Spray Technology,2013,23(1):69-74.
[21] PAULETTI E,D′ OLIVEIRA A S C M.Influence of Pt concentration on structure of aluminized coatings on a Ni base superalloy[J].Surface and Coatings Technology,2017,332:57-63.
[22] HAZRA S,SABIRUDDIN K,BANDYOPADHYAY P P.Plasma and HVOF sprayed WC-Co coatings as hard chrome replacement solution[J].Surface Engineering,2012,28(1):37-43.
[23] AHMAD H,TARIQ A,SHEHZAD A,et al.Stealth technology:Methods and composite materials [J].Polymer Composites,2019,40(12):4457-4472.
[24] CHENG H F,HUANG D Q.Research progress in multi-spectrum compatible stealth materials [J].Journal of Aeronautical Materials,2014,34(5):93-99.
[25] ZHOU S,LIU D Q,CHENG H F,et al.A multilayer film based selective thermal emitter for infrared stealth technology [J].Advanced Optical Materials,2018,6(23):1-8.
[26] MOHAMMED M,ZAIDAN S,SMICH H.Investigation of ceramic coating by thermal spray with diffusion of copper [J].Acta Physica Polonica A,2018,134(1):248-251.
[27] LI C Y,XIE T F,YAO B Q,et al.Polycrystalline Ho:Lu AG laser ceramics:Fabrication,microstructure,and optical characterization [J].Transactions of the Indian Institute of Metals,2017,100(5):2081-2087.
[28] VAIBHAV K B,RAMESH M R.Thermal analysis of a plasma sprayed ceramic coated diesel engine piston[J].Transactions of the Indian Institute of Metals,2018,71(2):319-326.
[29] CHEN P H,LIU Z L,LI R Q,et al.Thermal-sprayed coating of optimally mixed ceramic powders on stainless steel with enhanced corrosion resistance [J].Journal of Iron and Steel Research International,2018,25(2):207-212.
[30] YUAN X J,WANG H G,HOU G L,et al.Nano alpha-Fe/epoxy resin composite absorber coatings fabricated by thermal spraying technique [J].IEEE Trans Magn,2006,42(9):2115.
[31] BéGARD M,BOBZIN K,BOLELLI G,et al.Thermal spraying of Co,Ti-substituted ba-hexaferrite coatings for electromagnetic wave absorption applications [J].Surface & Coat Technology,2009,203(20/21):3312.
[32] NANOBASHVILI S,MATEJICEK J,ZACEK F,et al.Plasma sprayed coatings for RF wave absorption[J].Journal of Nuclear Materials,2002,(307-311):1334-1338.
[33] ALI A,JAMIL M I,JIANG J,et al.An overview of controlled-biocide-release coating based on polymer resin for marine antifouling applications[J].Journal of Polymer Research,2020,27(4):1-17.
[34] WANG Y,ZHENG Y G,KE W,et al.Corrosion of high-velocity oxy-fuel(HVOF)sprayed iron-based amorphous metallic coatings for marine pump in sodium chloride solutions [J].Materials and Corrosion,2012,63(8):685-694.
[35] WANG S L,CHENG J C,YI S H,et al.Corrosion resistance of Fe-based amorphous metallic matrix coating fabricated by HVOF thermal spraying[J].Transactions of Nonferrous Metals Society of China,2014,24(1):146-151.
[36] ZHOU Z,WANG L,HE D Y,et al.Microstructure and wear resistance of Fe-based amorphous metallic coatings prepared by HVOF thermal spraying [J].Journal of Thermal Spray Technology,2010,19(6):1287-1293.
[37] 洪偉宏.國外航母甲板防滑涂料技術現狀及發展趨勢[J].艦船科學技術,2015,12:166-169.
HONG Weihong.Situation and development trend of foreign aircraft carrier deck anti-slip coating technology [J].Ship Science and Technology,2015,12:166-169.(in Chinese)
[38] 何磊,趙滿,喬貝貝.美軍航母腐蝕防控技術研制與應用進展[J].艦船科學技術,2017,8:189-193.
HE Lei,ZHAO Man,QIAO Beibei.Progress in development and application of aircraft carrier corrosion prevention and control technology in U.S.Navy [J].Ship Science and Technology,2017,8:189-193.(in Chinese)
[39] VICTOR K C.The repair of magnesium rotorcraft components by cold spray [J].Journal of Failure Analysis and Prevention,2008,8(2):164-175.
[40] CHE H,LIBERATI A,VO P,et al.Cold spray of mixed Sn-Zn and Sn-Al powders on carbon fiber reinforced polymers [J].Materials Science Forum,2018,941:1892-1897.
[41] CASS W.Machining cold spray additive manufacture for the UH-60 main transmission sump[J].Annual Forum Proceedings-AHS International,2018:25-38.
[42] YEE L Y,SWEE L S,WAI YEE Y.A review of 3D printing processes and materials for soft robotics[J].Rapid Prototyping Journal,2020,26(8):1345-1361.
[43] TARUNPREET S,SANJEEV K,SHANKAR S.3D printing of engineering materials:A state of the art review [J].Materials Today:Proceedings,2020,28(3):1927-1931.
[44] WANG H M,JIANG P,LIU Y F.State of the art and prospects on laser surface modifications of titanium alloys for the aerospace industries[J].Proceedings of SPIE-the International Society for Optical Engineering,2002(4915):167-172.
[45] 景綠路.國外增材制造技術標準分析[J].航空標準化與質量,2013(4):44-48.
JING Lülu.Analysis on foreign additive manufacturing technology standards[J].Aeronautic Standardization & Quality,2013(4):44-48.(in Chinese)
[46] 楊開.NASA 對3D打印的火箭發動機燃燒室進行點火試驗 [J].航天制造技術,2018(3):71.
YANG Kai.The conducted ignition test on 3D printed rocket engine by NASA [J].Aerospace Manufacturing Technology,2018(3):71.(in Chinese)
[47] ALKHIMOV A P,KOSAREV V F,PAPYRIN A N.A method of ‘cold’ gas-dynamic deposition[J].Soviet Physics Doklady,1990,35(12):1047-1049.
[48] 李文亞,黃春杰,余敏,等.冷噴涂制備復合材料涂層研究現狀[J].材料工程,2013(8):1-10.
LI Wenya,HUANG Chunjie,YU Min,et al.State-of-the-art of cold spraying composite coatings [J].Journal of Materials Engineering,2013(8):1-10.(in Chinese)
[49] ALKHIMOV A P,KOSAREV V F,PAPYRIN A N.A methodof ‘cold’ gas-dynamic deposition[J].Soviet Physics Doklady,1990,35(12):1047-1049.
[50] ASSADI H,GARTENR F,STOLTENHOFF T,et al.Bonding mechanism in cold gas spraying [J].Acta Materialia,2003,51(15):4379-4394.
[51] SOVA A,GRIGORIEV S,OKUNKOVA A,et al.Potential of cold gas dynamic spray as additive manufacturing technology[J].The International Journal of Advanced Manufacturing Technology,2013,69(9-12):2269-2278.
[52] BRANAGAN D J,BREITSAMETER M,MEACHAM B E,et al.High-performance nanoscale composite coatings for boiler applications[J].Journal of Thermal Spray Technology,2005,14(2):196-204.
免責聲明:本網站所轉載的文字、圖片與視頻資料版權歸原創作者所有,如果涉及侵權,請第一時間聯系本網刪除。
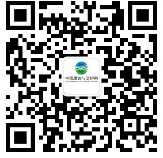
官方微信
《中國腐蝕與防護網電子期刊》征訂啟事
- 投稿聯系:編輯部
- 電話:010-62316606-806
- 郵箱:fsfhzy666@163.com
- 中國腐蝕與防護網官方QQ群:140808414