事故背景
某油井于2016年7月投產(chǎn),該井最大井斜為75°,井斜深度為2851m,井垂深度為1595.01m,油井內(nèi)采出原油中H2S質(zhì)量濃度為116mg·L-1,CO2質(zhì)量分?jǐn)?shù)約為8%,油田地面原油為重質(zhì)油,油層溫度為53~64℃,地層水礦化度為10625mg·L-1。油井的生產(chǎn)層位為60~100,無注水支持,自投產(chǎn)以來共進(jìn)行了兩次酸化作業(yè)。2018年該井日產(chǎn)油體積為37m3·d-1,日產(chǎn)氣體積為198.2m3·d-1,日產(chǎn)水體積為0.48m3·d-1,其中水的質(zhì)量分?jǐn)?shù)為1.1%。2018年1月工作人員在油井起出管柱和下管柱作業(yè)時發(fā)現(xiàn)距井口2432.56m處的2-7/8″油管存在多處腐蝕并穿孔,該油管材料為L80鋼。
為查明該油管腐蝕穿孔的原因,筆者對其進(jìn)行了檢驗(yàn)和分析。
理化檢驗(yàn)
宏觀觀察
宏觀觀察發(fā)現(xiàn),2-7/8″油管處于4號封隔器以上的環(huán)空部分,且有50°左右的井斜。油管腐蝕段長度為5.85m,油管表面附有紅褐色和黃褐色的腐蝕產(chǎn)物層和油漬。在距離油管頂端0.9m處有兩個明顯的腐蝕孔,分別呈雨滴狀(最大直徑為1.5mm)和橢圓形(長軸長度約為4mm,短軸長度約為2mm),腐蝕孔四周管壁由外向內(nèi)減薄,且管壁表面附有質(zhì)地疏松的腐蝕產(chǎn)物,如圖1所示。
圖1 油管腐蝕孔宏觀形貌
油管失效段外壁有多處裂紋,如圖2所示。
圖2 油管外壁裂紋處宏觀形貌
分別用石油醚和酒精清洗油管外壁后,裂紋處的腐蝕產(chǎn)物脫落,形成了新的腐蝕孔或腐蝕坑,如圖3所示。
圖3 油管清洗前后的宏觀形貌
將油管在腐蝕孔密集區(qū)域沿軸向?qū)Π肫书_,由圖4可見,油管內(nèi)壁未腐蝕,但在剖面上存在腐蝕坑,且腐蝕由管外向管內(nèi)的擴(kuò)展,呈現(xiàn)出向外腐蝕特征。
圖4 油管內(nèi)壁宏觀形貌
化學(xué)成分分析
在失效油管未腐蝕處取樣,根據(jù)API SPEC 5CT-2018 Casing and Tubing進(jìn)行化學(xué)成分分析。
表1 失效油管的化學(xué)成分(質(zhì)量分?jǐn)?shù))%
由表1可見,油管正常管段的化學(xué)成分符合技術(shù)要求。
金相檢驗(yàn)
在失效油管的完好部位取樣,試樣經(jīng)鑲嵌、研磨、拋光,使用體積分?jǐn)?shù)為4%的硝酸酒精溶液浸蝕后,根據(jù)GB/T 13298-2015?金屬顯微組織檢驗(yàn)方法?采用Zeiss observer A1m型金相倒置顯微鏡觀察顯微組織。
圖5 失效油管的顯微組織形貌
由圖5可見,油管的顯微組織為鐵素體+珠光體,未見明顯的夾雜物。正常情況下,L80鋼顯微組織為回火索氏體+極少量鐵素體+極少量屈氏體。回火索氏體是馬氏體在500~650℃時回火形成的以鐵素體為基體且內(nèi)部分布著碳化物 (包括滲碳體)球粒的復(fù)相組織,具有更好的力學(xué)性能。由此可見,失效油管金相組織異常。
能譜分析
分別取失效油管外壁表面裂紋處、油管外壁腐蝕孔處、外壁表面黃色處和外壁表面紅色處腐蝕產(chǎn)物試樣,分別編為1,2,3,4號,采用OXRORD X-MaxN型能譜儀(EDS)對上述試樣進(jìn)行微區(qū)成分分析,分析位置和分析結(jié)果分別如圖6和表2所示。
圖6 失效油管EDS分析位置
表2 失效油管EDS分析結(jié)果(質(zhì)量分?jǐn)?shù))%
由表2可見,1~4號試樣中鐵、氧、碳、硅、鋁含量均較高,推測其中存在鐵的氧化物、鐵碳酸鹽及砂石成分;1~4號試樣中均含有少量的氯和硫,2號試樣中含有較多的氟。
物相分析
在1,3,4號試樣中先后加入石油醚和酒精,分別進(jìn)行過濾、干燥處理后采用D8 Advance型X射線衍射儀對1~4號試樣進(jìn)行X射線衍射(XRD)測試,掃描角度2θ為3°~80°,采樣步寬為0.02,波長為1.54056nm,結(jié)果如圖7所示。
圖7 1~4號試樣的XRD測試結(jié)果與標(biāo)準(zhǔn)圖譜對比
可見1號試樣的主要物相為Fe3C、FeS,2號試樣主要物相為Fe3C、Al(OH,F(xiàn))3、FeS,3號試樣主要物相為FeCO3、CaMg(CO3)2、SiO2,4號試樣主要物相為SiO2、Fe3O4、FeCO3。
拉伸性能測試
根據(jù)API SPEC 5CT-2018,在失效油管未腐蝕部位截取尺寸為19mm(寬度)×50.8mm(標(biāo)距)的試樣,采用ZWICK Z600型雙立柱萬能材料試驗(yàn)機(jī)進(jìn)行拉伸性能測試,結(jié)果如表3所示。
表3 失效油管拉伸性能測試結(jié)果
可見失效油管除了屈服強(qiáng)度低于API SPEC 5CT-2018的要求之外,其抗拉強(qiáng)度和斷后伸長率均符合該標(biāo)準(zhǔn)的要求。
分析與討論
由化學(xué)成分分析結(jié)果可知,失效油管的化學(xué)成分符合相關(guān)標(biāo)準(zhǔn)的要求。由能譜分析結(jié)果可知,腐蝕產(chǎn)物中存在碳、氧、硫、氯、氟,表明失效油管所處環(huán)境存在H2S、CO2、Cl-和F-等促進(jìn)腐蝕的因素。
由物相分析結(jié)果可知,油管大面積脫落的疏松物質(zhì)(腐蝕產(chǎn)物)主要成分是Fe3C,同時還有FeS、鐵的氧化物、Al(OH)3和FeCO3。為提高油井產(chǎn)能,生產(chǎn)人員采用酸化作業(yè)來清除井筒孔眼中酸溶性顆粒、鉆屑和結(jié)垢。當(dāng)酸化作業(yè)結(jié)束后,未排凈的殘酸和原油在封隔器以上的環(huán)空底部,油管處于封隔器以上的環(huán)空部分。由于油管內(nèi)壁和外壁處原油流速不同,在油管外壁形成了“靜止”的區(qū)域,形成液體滯留區(qū),而在油管內(nèi)壁處原油是流動態(tài),腐蝕速率相對緩慢,因此油管外壁先發(fā)生腐蝕。殘酸中含有的H+、Cl-、F-等易誘發(fā)和促進(jìn)腐蝕的離子,形成了電解質(zhì)溶液。
腐蝕初期,鐵在電解質(zhì)溶液中首先發(fā)生了溶解,由于L80鋼中的鐵素體比Fe3C具有更負(fù)的電位,在腐蝕過程中鐵素體相作為陽極優(yōu)先溶解,F(xiàn)e3C作為陰極保留下來并積聚在試樣表面,形成了疏松的Fe3C。隨著腐蝕時間的延長,F(xiàn)e2+和CO23-的濃度超過FeC3的溶度積,從而在油管外壁表面沉積形成FeCO3保護(hù)膜,但是由于Cl-、F-吸附在油管外壁表面,這妨礙形成完整的FeCO3保護(hù)膜,而地層中存在的Ca2+、Mg2+置換FeCO3晶體點(diǎn)陣的Fe2+導(dǎo)致晶格畸變形成CaMg(CO3)2,這進(jìn)一步降低了腐蝕產(chǎn)物的致密性。
由于油管外壁附著的不均勻的腐蝕產(chǎn)物和無機(jī)鹽垢不致密,缺氧區(qū)的垢下金屬會與垢外富氧的陰極區(qū)產(chǎn)生電位差形成腐蝕電流,垢下金屬進(jìn)一步發(fā)生陽極溶解,加速金屬腐蝕。雖然環(huán)境中的H2S不直接參加陰極反應(yīng),但是會作為加速氫離子放電的催化劑加速反應(yīng)。由于在環(huán)空的底部的殘酸和原油處于相對靜止?fàn)顟B(tài),油管表面附著的微生物會釋放出部分H2S,加上油管所處環(huán)境中H2S含量較高,因而發(fā)生H2S腐蝕形成FeS附著于油管外壁表層。
外壁附著的黃色腐蝕產(chǎn)物中有SiO2和CaMg(CO3)2,由此可推測油管外壁表面存在泥沙(酸化作業(yè)時由地層返排至環(huán)空部位),存在垢下腐蝕。通常情況下,當(dāng)原油中含水率大于40%時,油管發(fā)生CO2腐蝕的傾向才較大,而該油井原油含水量小于10%,發(fā)生CO2腐蝕的傾向不大。腐蝕產(chǎn)物中存在一定量的CO2腐蝕產(chǎn)物,推測是由于油氣開采時伴生CO2溶解于水中與鐵腐蝕的中間產(chǎn)物發(fā)生反應(yīng)所導(dǎo)致。
失效油管的顯微組織為珠光體+馬氏體,并非L80鋼正常的顯微組織(回火索氏體+極少量鐵素體+極少量屈氏體),結(jié)合失效油管力學(xué)性能測試結(jié)果可知,油管材料的屈服強(qiáng)度偏低,隨著鐵在電解質(zhì)中不斷溶解,在環(huán)空壓力和油井液柱壓力的共同作用下,疏松多孔的Fe3C和與鋼鐵表面粘合力差的FeS被“壓迫”在油管外壁的腐蝕坑處,腐蝕介質(zhì)由外向內(nèi)滲透,導(dǎo)致腐蝕進(jìn)一步向管壁內(nèi)表面發(fā)展,而外表面卻保持比較完整。當(dāng)油管的管壁被全部腐蝕,在油井液柱壓力的作用下,疏松的腐蝕產(chǎn)物脫落,油管就形成了大面積的腐蝕孔直至腐蝕出現(xiàn)穿孔。
結(jié)論及建議
L80鋼油管失效管段處于相對靜態(tài)的環(huán)空區(qū)域,在CO2腐蝕、H2S腐蝕和垢下腐蝕綜合作用下,油管外壁形成不致密腐蝕產(chǎn)物,殘酸中含有的H+、Cl-、F-等離子加速了腐蝕進(jìn)程,在油管外壁形成腐蝕坑,當(dāng)油管的管壁被全部腐蝕,在油井液柱壓力的作用下,疏松的腐蝕產(chǎn)物脫落,油管就形成了腐蝕孔直至腐蝕出現(xiàn)穿孔。
建議加強(qiáng)對油管材料的控制,同時嚴(yán)格控制酸化作業(yè)過程,減少酸液的殘留。
免責(zé)聲明:本網(wǎng)站所轉(zhuǎn)載的文字、圖片與視頻資料版權(quán)歸原創(chuàng)作者所有,如果涉及侵權(quán),請第一時間聯(lián)系本網(wǎng)刪除。
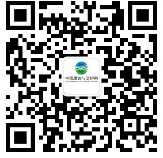
官方微信
《中國腐蝕與防護(hù)網(wǎng)電子期刊》征訂啟事
- 投稿聯(lián)系:編輯部
- 電話:010-62316606-806
- 郵箱:fsfhzy666@163.com
- 中國腐蝕與防護(hù)網(wǎng)官方QQ群:140808414