根據有關統計,大約有80%以上的結構強度破壞是由疲勞破壞造成的。而航空發動機零件由疲勞破壞造成的失效所占比例更大。航空發動機零件失效,大多數因強度失效、磨損失效和腐蝕失效等材料表面不能勝任苛刻工作條件所致,而且大多數發生在零件的表面和近表面,或者先從表面開始向內部擴散所致,進而顯著影響發動機的性能與壽命。對零部件進行適度的表面強化或硬化,能阻止已有裂紋的擴展和新裂紋的產生,從而提高疲勞強度。因此,對于強調高安全性、長壽命、低壽命期成本的航空發動機來說,采用表面處理提高其部件,特別是葉片的抗疲勞能力特別重要。為此,國外研制和驗證了諸如激光沖擊強化、激光熔覆、低塑性拋光技術等表面處理技術,且取得了一定的效果。本文將重點綜述由Lambda公司開發研制的低塑性拋光技術。
低塑性拋光技術原理與特點
低塑性拋光技術(LPB)是以機械噴丸與機械滾壓原理為基礎,通過少量的冷作或塑性變形產生深層高殘余壓應力的新表面強化技術。它可以采用傳統的多軸計算機數控(CNC)機床刀具,通過改變壓力、進給、刀具特性,全新地控制殘余應力的分布。
低塑性拋光工作原理是通過1個自由旋轉的球形工具的一系列滾動產生累積的塑性應變或者冷作,進而產生接近材料屈服強度的殘余壓應力。該球形工具是由1個球形液體浮動座支承,不與支承座相接觸,由液壓作動筒使其對工件表面施加滾壓載荷,施加的載荷由CNC軟件控制。來自球體的壓力在材料上形成塑性變形,由于變形區受周圍材料的約束從而留下殘余壓應力,無材料損失,只是表面向內位移千分之幾英寸。傳統噴丸的多次隨機丸粒沖擊則會產生20%,甚至超過100%的冷作,形成有較高位錯密度的表面嚴重變形層,對受壓層的熱穩定性和機械穩定性產生危害。
低塑性拋光技術是1種改進的預防原始設備制造商(OEM)部件裂紋形成的方法,雖然與噴丸技術具有在部件的關鍵區域形成殘余壓應力層的相同目的,但是該技術具有以下特點:
(1)由低塑性拋光處理后在表面形成的“安全區”的深度是1.0mm,而由噴丸處理后在表面形成的“安全區”的深度僅為0.10mm,相差10倍。當外來物損傷或者腐蝕發生時,經噴丸處理后的表面腐蝕可能繼續擴展到部件更深處,形成裂紋,導致該部件報廢。
(2)在室溫(屬于冷加工)下采用噴丸技術通過小球狀材料撞擊修理的部件表面,形成凹坑且產生殘余壓應力,而這些凹坑使部件材料更加松散,使修理功效大打折扣。而在恒定的較高溫度(不屬于冷加工)下采用低塑性拋光技術修理的部件表面,施加殘余壓力精準且將壓力傳遞到部件足夠深處,且不會引起部件變形。
(3)低塑性拋光技術,對表面的凹凸度具有一定的撫平作用,使工件光潔度Ra的改善優于5μm;
能夠保證零件表面各處應力大小適中,可以避免腐蝕擴展到部件更深的區域,從而極大地減輕部件的損傷。
(4)與傳統機械加工相比,低塑性拋光技術可以用較低的成本,在零件表面生成用于消除施加的拉伸力的殘余應力分布,提供最佳的疲勞性能。
(5)低塑性拋光技術不需要采用特殊的或昂貴的設備,只要將低塑性拋光設備與磨床、車床或者機器人連接,在其表面以精確的壓力滾壓即可,一次性完成零件加工,無需檢驗。施壓設備與圓珠筆的外形相類似,只是尺寸較大,工具的底槽中有1個硬球,硬球在液壓力的推動下滾壓部件而實現拋光即可,從而很大程度上減少了人為錯誤的發生。
(6)低塑性拋光技術可用于鐵合金、鈦合金、合金鋼、不銹鋼、鎳合金、鋁合金、鑄鐵等金屬,適用范圍非常廣。
低塑性拋光技術目前在NASA、美國海軍及空軍資助下進行了一系列的應用研究。
低塑性拋光技術是Lambda公司的專利技術,始于1996年,并得到了NASA的投資和支持。該項技術于2004年實現了商業化,2009年獲得了美國聯邦航空管理局(FAA)授權用于航空發動機部件修理,2011 年12 月獲得了FAA頒發的補充型號證書(STC)。低塑性拋光技術最初只是用于渦輪發動機金屬部件的加工,目前已擴展應用于飛機部件的加工。
Ti-6Al-4V壓氣機葉片上的應用
Lambda公司在對激光噴丸強化與低塑性拋光技術對比研究中發現,激光噴丸強化風扇及壓氣機葉片的進氣邊可以提高損傷容限,以FOD深度來說,至少提高了1個數量級。雖然通過激光噴丸強化獲得的高數量級穿透厚度壓應力能夠延緩疲勞裂紋的起始及生長,但是需要昂貴的特殊激光系統才能實現。在對比試驗研究中,采用低塑性拋光技術通過受控深度模擬進氣邊FOD,對實際風扇葉片疲勞性能進行試驗評估。為了獲得適當的模擬外物損傷(FOD) 深度,在試驗中記錄了使用過的葉片在使用中所產生的FOD 的尺寸及位置分布。 在使用中進氣邊產生的FOD 深度范圍是0.005~0.50mm。觀察到的95%的FOD都小于0.50mm。如果在檢驗過程中發現FOD深0.13mm,則取下葉片進行返修或更換。為了保守起見,選擇0.50mm為本葉片中含有的最小FOD深度。
通過在葉片進氣邊加載產生疲勞過程中產生最大應力的位置上機械加工60°“V”形槽,模擬的0.50mm和1.2mm深的FOD。設計了LPB加工的CNC 路徑并且建立了LPB 參數,從葉片的進氣邊到距葉片進氣邊6.4mm弦面的公稱距離產生穿透厚度的-689MPa公稱壓縮應力。沒有FOD時,經過LPB處理,疲勞強度比未經過處理的葉片提高207MPa,接近材料的屈服強度。除了1個例子外,經過LPB處理的葉片在沒有FOD條件下,在這么高的應力狀態下試驗,大多數都在低塑性拋光技術處理過的區域外斷裂,通常是在燕尾榫頭區域。
在1個未經過低塑性拋光技術處理的葉片上制造1個深0.5mm的模擬FOD后,疲勞強度從689MPa降低到241MPa,降低了65%。在經過LPB處理的葉片上制造1個相同深度0.5mm的FOD后,疲勞強度等于未經過LPB處理、沒有FOD 葉片的強度。LPB處理后,1.27mm深的FOD使疲勞強度降低到620MPa,僅比未經過處理的葉片的疲勞強度小10%。
經過LPB處理的葉片即使有0.5mm的FOD的疲勞強度,接近材料的拉伸屈服強度。低塑性拋光技術產生的高壓應力抑制了裂紋的起始和生長,提高了有和沒有FOD的疲勞強度。然而,這種優點對于大多數表面損傷的情況都很明顯。穿透厚度的壓應力以應力向或進入受壓區的方式添加了施加的拉伸應力偏差,從而造成較高的允許變化應力。利用AFGROW法則進行的以斷裂機理為基礎的疲勞壽命分析證明,對于薄板中穿透厚度受壓區的邊緣裂紋生長來說,持久極限一般等于壓應力的數量級,容許的損傷(裂紋)深度約等于穿透厚度受壓區的寬度(從邊緣測量)。
目前,低塑性拋光技術在F402-RR-408發動機和CFM56-7發動機第1級低壓壓氣機葉片上得到了應用,以提高抗外物損傷容限和高循環疲勞延長航空發動機葉片的使用壽命。CFM56-7發動機的第1級壓氣機的每1個葉片的成本約為1000美元,因腐蝕和裂紋損傷引起的非計劃維修的費用遠遠高于其成本。為了解決因各種腐蝕、侵蝕、裂紋應力損傷、外來物損傷而引起的發動機修理問題,達美技術運營公司與Lambda 公司合作在達美航空公司位于亞特蘭大的維修廠為LPB設備配備通用的數控機床,用于CFM56-7發動機部件的維修。 在維修過程中使用1個特殊的控制盒,將軟件生成的部件壓力分布圖信息傳輸給數控設備,當維修人員將零件固定好后,按下按鈕啟動控制盒,然后控制盒將會按照設好的精確壓力滾壓部件。整套裝置采用閉環反饋系統感知液壓力,因此可以實時讀出所施加壓力的精確數值。目前,達美技術運營公司正在研究如何將低塑性拋光技術應用于其他部件,還在研發飛機其他部件的表面處理技術,以期獲得更多的STC。
17-4PH不銹鋼壓氣機葉片中的應用
低塑性拋光技術在美國海軍的T56發動機第1級壓氣機17-4PH不銹鋼壓氣機葉片進行了低塑性拋光技術和噴丸技術高循環疲勞、腐蝕性疲勞、一般腐蝕性疲勞試驗研究。具體是采用葉片邊緣形狀的厚截面試驗件,研究低塑性拋光技術與噴丸技術在高循環疲勞、損傷容限和鹽水腐蝕疲勞的特性(圖1)。試驗結果驗證:采用LPB,通過在1.0mm深度內施加壓縮殘余應力,大幅度提高了高循環疲勞和腐蝕疲勞性能。與噴丸T56葉片試驗件相比,低塑性拋光技術大幅度提高葉片邊緣抗外物損傷能力。基本疲勞強度是930MPa,僅比噴丸狀態的965MPa略低。相反,由于LPB引入了接近屈服強度的殘余壓應力,因此產生了1240MPa的疲勞強度(彎曲中),超過材料的拉伸屈服強度1033MPa。當用EDM(放電加工)制造一個深0.25mm、長0.76mm的FOD時,未經過LPB的HCF性能下降得非常大。有FOD的噴丸和基本疲勞強度分別僅為275MPa和172MPa。而有相同FOD、表面經過LPB處理的試樣的疲勞強度一般1033MPa,與沒有FOD的材料的基本強度相當。
腐蝕環境對燃氣渦輪發動機零件能夠產生很嚴重的影響,造成腐蝕凹坑和HCF壽命中很大的缺陷。鐵基不銹鋼中的鹽霧腐蝕凹坑是常見的疲勞裂紋起始處。鹽霧腐蝕凹坑是由于暴露在海洋大氣或蒸汽渦輪機環境中造成的。腐蝕坑的深度及相應的應力強度因數是由燃氣渦輪發動機暴露的時間、溫度、及使用環境決定的。鹽腐蝕坑一般會使持久極限降低到未經過腐蝕值的一半。如果有FOD 或侵蝕,經常會使腐蝕的影響加劇。
疲勞試驗過程中,我們將厚截面彎曲試樣暴露在腐蝕介質中,來監控(疲勞循環過程中)強烈腐蝕對HCF行為的影響。將一塊浸有酸性鹽溶液(3.5%NaCl,pH3.5)的無化學品吸收性墊綁在試樣的計量截面上,并用薄塑料膜進行密封,防止蒸發。所有其他試驗條件與前面研究厚截面HCF 行為的描述一樣。在酸性鹽溶液中試驗的沒有FOD的低應力磨削的基本疲勞強度一般是689MPa。含有0.25mm FOD的基本疲勞強度僅為69 MPa。經過比較,經過LPB 處理的樣品僅在腐蝕環境下的疲勞強度超過1102MPa,比沒有FOD以及有0.25mm FOD的基本狀態好。雖然沒有建立完全的SN曲線,但是,當FOD深度增加到0.50mm和0.76mm時,HCF性能的進一步缺陷是很小的。
結束語
航空發動機經常受到疲勞、外物損傷、腐蝕疲勞和摩擦疲勞的影響。即使是小的外物損傷、腐蝕坑或者其他表面損傷都能夠使疲勞失效集結,造成空難性的后果。避免疲勞失效所需的檢驗和維護成本每年估計都是幾十億美元。通過設計和改變材料一般都是使用巨大的成本有限地改善疲勞。低塑性拋光技術可以在傳統的機械加工車間環境中,在原始的制造階段或大修及修理過程中,采用傳統的CNC機床較低成本地完成。因而,它具有廣闊的發展和應用前景。
免責聲明:本網站所轉載的文字、圖片與視頻資料版權歸原創作者所有,如果涉及侵權,請第一時間聯系本網刪除。
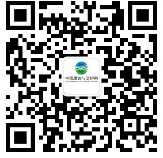
官方微信
《腐蝕與防護網電子期刊》征訂啟事
- 投稿聯系:編輯部
- 電話:010-62316606-806
- 郵箱:fsfhzy666@163.com
- 腐蝕與防護網官方QQ群:140808414