堿性鋅酸鹽鍍鋅工藝,其鍍層外觀光亮,具有良好的結(jié)合力、低脆性和耐蝕性。它消除了氰化鍍鋅的毒性,克服了氯化物鍍鋅對耐腐蝕差和鈍化膜在濕熱空氣中易變色的缺陷。以下對12種最常見故障進行全面分析講解,希望能給大家?guī)睃c幫助:
1.低電流密度區(qū)出現(xiàn)黑色或灰色鍍層
2.鑄鐵零件較難沉積上鍍鋅層
3.鍍層呈海綿狀
4.鍍層結(jié)合力差的原因及解決方法
5.沉積速度慢的原因及解決方法
6.鍍液中鋅含量過快積累和陽極鈍化的原因及解決方法
7.鍍鋅層出現(xiàn)粗糙或粗糙發(fā)暗的原因及解決方法
8.鍍層鈍化膜質(zhì)量故障(發(fā)花、變色、變暗等)
9.鋅酸鹽鍍鋅層起泡故障的分析與處理實例
10.鍍層有條紋和氣流狀
11.鋅酸鹽滾鍍鋅,滾筒突然發(fā)生爆炸
12.鋅酸鹽鍍鋅液中鋅濃度快速下降
一、低電流密度區(qū)出現(xiàn)黑色或灰色鍍層
1.原因分析
鉛離子污染:當鍍鋅液中鉛離子的含量超過15m9/L時,鍍液的分散能力下降,鍍層經(jīng)稀硝酸出光后會出現(xiàn)黑色或灰色條紋。鉛離子主要是由劣質(zhì)鋅陽極帶人的,為防止鉛的污染,鋅陽極需用0#鋅或l#鋅。
鐵離子污染:鍍液中鐵離子含量高達50m9/L,如鐵離子含量進一步提高,鍍液就會出現(xiàn)膠體絮狀物,鍍層鈍化后會出現(xiàn)紫藍色,而且鍍層容易出現(xiàn)氣泡。鐵離子主要是由劣質(zhì)氫氧化鈉或工件帶人。因此,要選用白色片堿,帶赤色的氫氧化鈉絕對不可用,工件進入鍍槽前應(yīng)徹底清洗。為調(diào)解陰、陽極面積比例,應(yīng)當使用鎳板或鍍鎳鐵板作為陽極。
銅離子污染:鍍液中銅離子含量高達20m9/L時,得到的鍍鋅層粗糙,光亮度降低,且光亮電流密度范圍隨銅離子含量的增加而逐漸縮小。銅離子主要是由掛勾和洗刷導(dǎo)電銅杠時帶入的。
2.解決方法
硫化鈉處理:取0.19/L~0.59/L化學(xué)純硫化鈉,溶于20倍以上的冷水中,在劇烈攪拌下,緩慢加入到鍍液中,加完后繼續(xù)攪拌20min,使之與鍍液中的重金屬離子充分反應(yīng),生成硫化物沉淀去除。
鋅粉處理:取l9/L~39/L鋅粉,在劇烈攪拌下緩慢加入鍍液中,使之與重金屬離子發(fā)生置換反應(yīng),加完后繼續(xù)攪拌20min,靜止2h后進行過濾,靜置時間不宜過長,否則失去處理意義。
低電流電解處理:取鍍鎳鐵板數(shù)塊作陰極(面積宜大些),以0.1A/dm2~0.2A/dm2的電流密度進行電解處理,處理時間視試鍍后情況而定。使用過的鍍鎳鐵板表面的黑色鍍層必須在酸中退除,然后方可作陽極使用。該方法的優(yōu)點是:操作簡便,不損耗鍍液。
二、鑄鐵零件較難沉積上鍍鋅層
1.原因分析
鑄鐵是含碳量高達2%(質(zhì)量分數(shù))以上的鐵碳合金,材料中的碳只有少量與鐵形成固溶體,大多以石墨或滲碳體的形式存在,由于石墨會降低氫的析出電位,從而阻礙了鋅的沉積,另一方面鑄鐵件表面粗糙,含大量縮孔、氣孔和砂眼,孔隙率也高,有些工件表面未經(jīng)加工,覆蓋有氧化皮,或經(jīng)過酸洗而造成過腐蝕,則導(dǎo)致析氫更嚴重,從而造成鋅離子的陰極還原沉積更困難。
2.解決方法
利用噴砂代替強腐蝕:噴砂可以阻止酸洗液滲入疏松內(nèi)孔中,并可避免發(fā)生過腐蝕。
采用閃鍍先鍍上薄層鋅:鍍件入槽后用高于正常電流5倍~l0倍的電流密度進行閃鍍,使其表面先鍍上一薄層鋅(此鋅層可以提高氫的過電位),然后再用3倍~5倍的電流密度繼續(xù)加厚。實踐證明,以上二種方法同時使用效果會更好。
三、鍍層呈海綿狀
1.原因分析
當鋅酸鹽鍍鋅液中添加劑含量不足時,有可能造成鍍鋅層結(jié)晶粗糙,因為鋅酸鹽鍍鋅的添加劑多屬表面活性劑,在電沉積過程中,添加劑在很寬的電位范圍內(nèi)吸附,從而減緩鍍液中鋅離子的放電步驟,提高了陰極極化,使鍍鋅層結(jié)晶細致、光亮。
2.解決方法
鍍液中添加劑含量目前尚未見有適用的準確的分析方法,一般是根據(jù)生產(chǎn)過程中鍍層的質(zhì)量,憑經(jīng)驗或者霍耳槽試驗添加。添加劑不宜過量加入,否則會出現(xiàn)鍍層發(fā)花,鈍化膜發(fā)霧,鍍層起泡,脆性增大,鍍層易變色,結(jié)合力降低等故障。
四、鍍層結(jié)合力差的原因及解決方法
1.原因分析
出現(xiàn)鍍層結(jié)合力差的原因可能有很多,而且可能是一種情況影響的結(jié)果,也可能是多種情況交互在一起引起的。
添加劑添加過量:一般情況下鋅酸鹽鍍鋅層的光亮度稍遜于氯化鉀鍍鋅層,有時為了獲得更光亮的鍍層,就靠多加光亮劑來彌補,結(jié)果鍍層不但達不到預(yù)想的光亮度。而且造成鍍層的結(jié)合力受到嚴重影響。
工件鍍前在鍍槽中停留時間過長:有人認為鋅酸鹽鍍鋅溶液是堿性的,把經(jīng)過前處理的工件掛在鍍槽中,待聚夠一槽后再送電施鍍,這樣工件易產(chǎn)生表面鈍化,從而影響到鍍層的結(jié)合力。
鍍層過厚:對于鍍鋅來說,鍍層過厚,鍍層的內(nèi)應(yīng)力和脆性增大,工件邊緣部位的鍍層出現(xiàn)氣泡,脫皮。所以一般鍍層厚度宜控制在20μm以內(nèi)。
鍍液表面浮有油污:工件入槽后被鍍液表面的油污和光亮劑分解物組成的污物所包圍。從而引起鍍層脫皮。
工件除油不徹底:有人認為鋅酸鹽鍍鋅是堿性的,必定有除油能力,前處理可以馬虎一點。鍍液雖是堿性的,但當有油污的工件入槽后,在其與堿性物質(zhì)起作用之前,鋅離子即搶先放電析出,鋅層沉積在薄層油膜上,結(jié)合力降低。
2.解決方法
針對上述原因分析,對于鍍層結(jié)合力的故障就可以采取相應(yīng)措施,例如控制鍍液中添加劑、光亮劑含量;控制工件在鍍槽中不能停留過久;加強零件的鍍前處理,保持清潔干凈的零件表面;同時注意鍍液表面的潔凈,隨時用厚層手紙吸除鍍液表面的油污等。
五、沉積速度慢的原因及解決方法
1.原因分析
出現(xiàn)鍍鋅層沉積速度慢的原因也有很多,在前面也做過一些分析,如果考慮到實際操作上的各種因素,其原因可能有:前處理不徹底,工件表面覆蓋有氧化膜,影響了鋅離子的正常沉積;零件導(dǎo)電不良,電流在導(dǎo)線上有消耗,分配到工件表面的電流過小;高碳鋼、鑄鐵等零件表面含碳量高,降低氫的析出電位,使得工件表面析氫加速,造成電流效率降低;零件綁扎過密,鍍鋅時工件局部遭到屏蔽而導(dǎo)致鍍層過薄;鍍液的溫度偏低,不允許使用正常的電流密度,影響了沉積速度;鍍液中氫氧化鈉含量偏高,電流效率相應(yīng)降低;鍍液中添加劑含量偏低,影響了鍍液的分散能力,造成零件表面鍍層局部顯得過薄;電流密度偏低影響沉積速度等。
2.解決方法
解決上述故障的方法,就是針對性的采取一些措施,如加強鍍前處理,保證零件表面的氧化皮去除干凈;注意電鍍掛具的導(dǎo)電和槽內(nèi)分布,保證零件的電流線的分布均勻;保持鍍液成分、溫度和電流密度處于規(guī)范和標準范圍內(nèi)。這樣就達到鍍鋅層沉積的正常速度。
六、鍍液中鋅含量過快積累和陽極鈍化的原因及解決方法
1.故障原因
這種故障產(chǎn)生的原因主要是陽極的問題,而造成陽極快速溶解的原因有:鍍液中氫氧化鈉含量偏高時,鋅陽極化學(xué)溶解速度加快,造成鍍液中鋅離子增加很多,因為鋅酸鹽鍍鋅的陰極電流效率是比較低的,鋅的實際消耗少于鋅陽極的溶解;實際上是鋅陽極這種自然溶解而破壞了鍍液中氫氧化鈉和鋅含量的正常比例。
在有些情況下,鋅陽極表面出現(xiàn)了陽極鈍化現(xiàn)象,雖然鋅陽極鈍化能增加陰極極化,提高分散能力,但陽極鈍化影響了鋅離子的溶解,使得鍍液中的鋅離子得不到補充,電鍍沉積速度受到了嚴重影響。
引起鋅陽極鈍化的原因有:鍍液中氫氧化物濃度過低,陽極面積過小,陽極面積與陰極面積之比應(yīng)不小于1.5:1否則較易發(fā)生鈍化。
2.解決方法
分析鍍液成分,調(diào)整鍍液中氫氧化鈉的濃度到正常;另外通過控制鋅陽極和不溶性鎳陽極的比例;在停鍍時將鋅陽極從槽中取出等措施消除鍍液中鋅離子增加的問題。同時也能解決鋅陽極的鈍化問題。
七、鍍鋅層出現(xiàn)粗糙或粗糙發(fā)暗的原因及解決方法
1.原因分析
按正常情況下氧化鋅與氫氧化鈉的比例為l:(10~12),過高或過低即會出現(xiàn)上述故障。即鍍鋅層粗糙是氧化鋅比例偏低而氫氧化鈉比例偏高造成的,這種比例失調(diào)還會出現(xiàn)電鍍沉積速度緩慢、允許電流密度上限降低、工件表面析氫加重等故障。反過來,氧化鋅比例偏高而氫氧化鈉比例偏低也會造成鍍鋅層的粗糙與發(fā)暗,這時還會出現(xiàn)工件邊緣部位有氣泡,沉積速度緩慢,分散能力和深鍍能力降低,電流升不上去,鍍層結(jié)合力差等問題。
2.解決方法
調(diào)整上述兩種情況的故障,一般在日常維護中既要控制好氧化鋅與氫氧化鈉的比例,又要考慮到氧化鋅與氫氧化鈉的實際含量,即使氧化鋅的比例偏低,也不直接添加氧化鋅,而是調(diào)節(jié)鋅陽極的面積,暫停使用不溶性陽極,溶液中鋅含量就會很快上去。當氧化鋅含量高了,可以以鍍鎳鐵板代替鋅陽極板,添加氫氧化鈉至l209/L,這一故障即能很快獲得解決。
八、鍍層鈍化膜質(zhì)量故障(發(fā)花、變色、變暗等)
目前鍍鋅進行鈍化處理的工藝主要低鉻彩色鈍化和三價鉻鈍化,在鈍化后有時放置一夜或幾天時間,鈍化膜的表面就會出現(xiàn)雨點狀白點,大小不一,鈍化膜也變暗變淡,光亮度下降。
1.原因分析
實際上發(fā)生這種故障的原因更復(fù)雜,可能有鍍液的問題;前處理不良的問題;基材有麻點,鍍后出光等清洗不良的問題;鈍化液成分比例失調(diào)的問題;鈍化膜老化時間不夠的問題;環(huán)境的問題,空氣中水蒸氣、酸霧嚴重使得鈍化膜色澤變化和腐蝕等。
2.解決方法
針對上述可能的原因,逐條采取措施。調(diào)整鍍液成分到工藝規(guī)范,并且對鍍液進行鋅粉、硫化鈉處理,再進行電解處理;加強除油、活化等前處理工序;加強鍍后清洗和出光工序;嚴格控制鈍化溶液成分和鈍化工藝參數(shù),控制好鈍化膜的色彩;加強鈍化后老化工藝的控制;改善工作環(huán)境,鍍后零件盡快入庫等。尤其要注意的是鈍化后的老化問題,因為熱水槽老化溫度過高(>70℃),就會使得鈍化膜中的六價鉻溶解,形成耐蝕性很差的多孔鈍化膜。就容易出現(xiàn)鍍鋅層鈍化膜表面的雨點狀白點,鈍化膜變暗變淡,光亮度下降的故障。嚴格控制鈍化老化工序(60℃),這種故障就可以消除,生產(chǎn)恢復(fù)到正常。
其他環(huán)節(jié)也會出現(xiàn)鈍化質(zhì)量的故障的問題,如某廠堿性鋅酸鹽鍍鋅液,低鉻鈍化的滾鍍鋅工藝生產(chǎn)線,出現(xiàn)了鈍化膜發(fā)花,表面有許多大塊不規(guī)則灰黑色斑塊的故障。經(jīng)分析是由于鍍鋅后的清洗槽中白色絮狀沉淀較多,出光槽溶液呈黃棕色,pH值接近4,這些都可能帶來電鍍故障,由于清洗不干凈和出光液pH高,造成電鍍零件表面堿性鍍液的清洗不夠,出光液的出光作用下降,導(dǎo)致鈍化膜發(fā)花等故障。通過增加一道熱水洗,將出光液pH調(diào)至l左右后,故障排除,生產(chǎn)恢復(fù)到正常。
九、鋅酸鹽鍍鋅層起泡故障的分析與處理實例
首先我們從零件的制備加工檢查,沒有發(fā)現(xiàn)出現(xiàn)起泡的可疑環(huán)節(jié),所以重點考慮電鍍各個工序的影響。
零件表面的油污,一般是經(jīng)化學(xué)除油、電解除油清除干凈。但若操作不當或者除油液成分失調(diào),可能會有少量油珠殘留在零件表面,這就可能引起鍍鋅層的起泡。
零件若酸洗除銹時間過長,可能由于過腐蝕也會引起鍍層的起泡。
此外,鍍前活化不充分,沒有活化,零件表面形成了一層薄氧化膜,也會導(dǎo)致鍍層結(jié)合力變差而起泡。
因此,堿性鋅酸鹽鍍鋅前處理要嚴格控制。
前處理流程為:化學(xué)除油→熱水洗→冷水洗→酸洗除銹→2次流動水洗→電解除油→熱水洗→流水洗→鍍前活化→2次流動水洗→鍍鋅。
除油液要定期加料;酸洗液、鍍前活化液要定期更換,而且要嚴防銅雜質(zhì)的危害。
(1)電鍍工序中引起鍍層起泡的可能因素。
掛具選擇不當會引起鋅鍍層起泡,這一點往往易被人們忽略。一般是用焊錫或銅將掛鉤與桿子焊接在一起,再浸塑、浸漆,或用聚氯乙烯薄膜包扎。若包扎破損,焊接處易受電解質(zhì)腐蝕,腐蝕產(chǎn)物附著在零件表面、零件自上而下便產(chǎn)生帶狀密集小泡,因此,應(yīng)經(jīng)常檢查掛具焊接處是否破損以防止掛具腐蝕而引起鍍層起泡。
鍍液操作或維護不當導(dǎo)致鋅鍍層起泡。鍍液中添加劑含量過高,易夾雜在鍍層中使得內(nèi)應(yīng)力驟增,導(dǎo)致鍍層起泡;鍍液中重金屬雜質(zhì),如鉛、銅等含量過高,使鋅層中夾雜過多的鉛、銅等雜質(zhì),鍍層與基體結(jié)合不良而起泡;光亮劑香草醛加入過多,鍍層的光亮性雖好,但脆性增大,導(dǎo)致鍍層起泡,此外,操作條件控制不當如溫度太低,電流密度太大,也會導(dǎo)致鍍層夾雜有機雜質(zhì),引起起泡。
鍍后鈍化工序的影響。鍍后出光、鈍化操作不當,清洗不徹底,出光液、鈍化液殘留在鍍層內(nèi),烘烤老化也容易引起鍍鋅層起泡。
(2)采取措施,嚴格控制鍍鋅工序消除起泡故障。
①生產(chǎn)廠首先把好了原材料關(guān),選用性能優(yōu)良的鋅酸鹽鍍鋅原料和添加劑,并且在添加劑加入鍍槽前,先進行霍耳槽實驗。
②加強鍍鋅槽液的維護,嚴格控制添加劑及光亮劑的補充量,以“少加勤加”為原則,或者根據(jù)霍耳槽試驗計量補加。
③將掉入鍍槽內(nèi)的零件及時撈出,銅掛鉤一律不能浸入鍍液中。
④檢查鋅陽極的純度,采用0號鋅或1號鋅,不用2號鋅。
⑤嚴格按鋅酸鹽電鍍鋅工藝規(guī)程,控制電流密度和溫度,冬季適當加溫至15℃以上,并盡可能減少添加劑及光亮劑的用量。
⑥嚴格控制零件鍍鋅層厚度,尤其是零件邊角的厚度太厚,特別容易發(fā)生鍍層起泡。
⑦定期對鍍液中有機物和重金屬雜質(zhì)進行大處理(加人lmL/L過氧化氫,攪拌30min,將鍍液加溫至60℃~70℃,再加入專用活性炭59/L~l09/L,鋅粉19/L~29/L,充分攪拌30min~60min,靜置4h,過濾,調(diào)整鍍液成分,即可試鍍),保證鍍鋅溶液處在一個好的工作狀態(tài)。
⑧加強鍍后處理工序,加強各道工序的漂洗,經(jīng)常更換浸泡用熱水,可大大減少因后處理不當而產(chǎn)生的起泡現(xiàn)象。
⑨嚴格控制老化溫度,避免鍍鋅層與基體因熱脹冷縮差異太大而起泡。
有些情況下,不一定是電鍍工序過程出現(xiàn)了鍍層起泡的現(xiàn)象,電鍍生產(chǎn)的周圍環(huán)境也可能引起電鍍層的起泡。如某廠堿性鋅酸鹽鍍鋅每年4月份~5月份總是發(fā)生鍍鋅層嚴重起泡的故障,而且開始找不出原因,只得每年停產(chǎn)一個多月。后來通過觀察分析發(fā)現(xiàn),當鍍液表面浮有一些微小的絲狀物時,鍍層起泡就嚴重,而當時的季節(jié)正是廠區(qū)周圍梧桐樹的開花期,其花瓣呈微小絲狀的物質(zhì)飄蕩,或多或少落人的鍍鋅槽。當采取措施阻擋了花瓣微小絲狀物的影響后,這種鍍鋅層起泡的故障就消除了。這說明出現(xiàn)電鍍故障,有時候除了電鍍工藝生產(chǎn)之外,還要從周圍的環(huán)境可能的影響考慮。
十、鍍層有條紋和氣流狀
1原因分析及處理方法
(1)陰極電流效率低
鋅酸鹽鍍鋅液,當陰極電流密度在1A/dm2、溫度在20℃左右時,陰極電流效率約為85%左右;當陰極電流密度在2A/dm2時,同等溫度下,陰極電流效率低于80%,若繼續(xù)增大陰極電流密度,則陰極電流效率將進一步降低。由于陰極電流效率低,陰極大量析氫,致使鍍層產(chǎn)生氣流、條紋。若鍍液的溫度低,陰極電流效率會更低,該現(xiàn)象將更加明顯處理方法:a.合理設(shè)定電流密度,參考值如下
溫度陰極電流密度
20℃以下0.8A/dm2
20℃以上1.5A/dm2
30℃左右1.5~2A/dm2
b.控制鍍液在15℃以上;
c.適量加入表面活性劑,加速氫氣析出
十一、鋅酸鹽滾鍍鋅,滾筒突然發(fā)生爆炸
1.原因分析
(1)陰極大量析氫
鋅酸鹽滾鍍鋅的陰極電流效率較低,一般在70%~80%,電鍍過程中產(chǎn)生許多氫氣,而這些氫氣又不能及時通過滾筒眼子排出,所以電鍍一定時間后,滾筒內(nèi)產(chǎn)生大量氫氣聚積。如果滾筒不是全浸式的,則筒內(nèi)同時有空氣存在。此外,如果陽極面積小,陽極電流密度大,使陽極發(fā)生鈍態(tài),產(chǎn)生大量氧氣。氫氣、氧氣和空氣的混合,并成一定的體積比(爆炸極限),使?jié)L筒爆炸具備了必要的條件。
鋅酸鹽鍍鋅液的溶液電阻較大,當滾鍍時間一長,鍍液溫度升至40℃以上。溫度高,在滾鍍中摩擦易產(chǎn)生火花,火花是引起爆炸的必要條件。
如果上述兩個條件同時具備,即發(fā)生爆炸。
2.解決方法:
a.采用全浸式的滾筒電鍍;
b.若使用半浸式滾筒電鍍,每隔30min停止電鍍一會,讓滾筒聚積的氣體散發(fā)出去,然后再繼續(xù)電鍍。
十二、鋅酸鹽鍍鋅液中鋅濃度快速下降是什么原因?如何處理?
1.原因分析:
①苛性堿含量不足,因而鋅酸鹽的水解作用加強,氫氧化鋅沉淀;
②陽極鈍化與陽極電流效率過低。
2.解決方法:
①向電解液中加苛性堿,并使氧化鋅含量增加到配方中規(guī)定濃度;
②清理陽極并增大其面積。
投稿聯(lián)系:編輯部
電話:010-62313558-806
郵箱:ecorr_org@163.com
中國腐蝕與防護網(wǎng)官方 QQ群:140808414
免責(zé)聲明:本網(wǎng)站所轉(zhuǎn)載的文字、圖片與視頻資料版權(quán)歸原創(chuàng)作者所有,如果涉及侵權(quán),請第一時間聯(lián)系本網(wǎng)刪除。
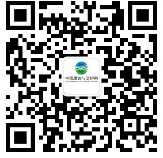
官方微信
《腐蝕與防護網(wǎng)電子期刊》征訂啟事
- 投稿聯(lián)系:編輯部
- 電話:010-62316606-806
- 郵箱:fsfhzy666@163.com
- 腐蝕與防護網(wǎng)官方QQ群:140808414