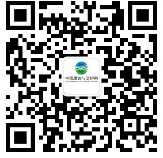
官方微信
《中國(guó)腐蝕與防護(hù)網(wǎng)電子期刊》征訂啟事
- 投稿聯(lián)系:編輯部
- 電話:010-62313558-806
- 郵箱:fsfhzy666@163.com
- 中國(guó)腐蝕與防護(hù)網(wǎng)官方QQ群:140808414
酸性硫酸鹽鍍錫后出現(xiàn)一些情況如錫鍍層光亮細(xì)致,存放時(shí)變色。
(1)可能原因:鍍后處理不當(dāng),清洗不凈
原因分析:對(duì)于光亮鍍錫而言,鍍后處理十分重要,若鍍層表面殘留的鍍液清洗不凈或錫鍍層在存放和轉(zhuǎn)運(yùn)過(guò)程中遭受氧化和污染,都將直接影響其可焊性
處理方法:a.按下列工藝進(jìn)行鍍后處理:鍍錫工件→水洗→專用清洗劑(或5%磷酸三鈉)清洗→水洗→鈍化(Cr03:50g/L;H2S04:1~2g/L;常溫;10~20s)→水洗→熱純水洗(60℃以上)→甩干→60~70℃烘干;(鈍化工藝也可采用專用鈍化劑進(jìn)行鈍化。)
b.嚴(yán)格清洗操作,加強(qiáng)清洗水和化學(xué)槽液的維護(hù)保養(yǎng)。
(2)可能原因:有機(jī)雜質(zhì)積累過(guò)多
原因分析:有機(jī)分解產(chǎn)物或光亮劑中的某些組分積累過(guò)多,使鍍層內(nèi)夾雜物增多,以致工件在空氣中極易變色泛黃。
處理方法:定期用3~5g/L活性炭吸附有機(jī)雜質(zhì)。
(3)可能原因:光亮劑過(guò)多
原因分析:若光亮劑過(guò)多,鍍層內(nèi)夾雜的光亮劑太多,鍍層內(nèi)應(yīng)力大,出現(xiàn)發(fā)黃、變脆、脫落,有時(shí)甚至鍍不上鍍層,嚴(yán)重影響鍍層的結(jié)合力和可焊性。
處理方法:a.電解除去多余的光亮劑;b.用活性炭吸附,除去多余的光亮劑。
(4)可能原因:溫度過(guò)高
原因分析:光亮鍍錫溫度一般在10~20℃下進(jìn)行,如果溫度超過(guò)25℃,就會(huì)影響鍍層的光亮度,超過(guò)30℃,不利于光亮劑吸附,而且載體光亮劑析出,使其他光亮劑失效。亞錫鹽的氧化水解和光亮劑消耗均隨溫度升高而加快,若溫度過(guò)高(超過(guò)35℃),Sn2+氧化速度加快,鍍液渾濁,鍍層粗糙,光亮劑消耗增加,光亮區(qū)變窄,嚴(yán)重時(shí)鍍層變暗,出現(xiàn)花斑,可焊性降低。低溫有利于整體光亮及良好的均鍍性,但溫度過(guò)低,工作電流密度范圍縮小,鍍層易燒焦。加入穩(wěn)定劑能提高使用溫度的上限值。
處理方法:采用制冷或停鍍,降低鍍液溫度至標(biāo)準(zhǔn)值。
(5)可能原因:電流密度過(guò)大
原因分析:光亮鍍錫電流密度一般控制在1~4A/dm2。電流密度過(guò)大,鍍層疏松、粗糙、多孔、邊緣易燒焦,脆性增加;電流密度過(guò)小,沉積速度過(guò)低,鍍層光亮度低,不能獲得全光亮的鍍層。對(duì)于滾鍍電子元器件,電流密度一般控制在工藝范圍的下限。
處理方法:準(zhǔn)確測(cè)量受鍍工件面積,合理設(shè)定電流值。
(6)可能原因:鍍液渾濁
原因分析:鍍液中的膠狀物與Sn2+共沉積到鍍層中,使鍍層變色,對(duì)錫鍍層的可焊性將有一定的影響。
處理方法:詳見酸性硫酸鹽鍍錫故障分析:鍍錫液渾濁的處理方法。
責(zé)任編輯:王元
《中國(guó)腐蝕與防護(hù)網(wǎng)電子期刊》征訂啟事
投稿聯(lián)系:編輯部
電話:010-82387968
郵箱:ecorr_org@163.com
中國(guó)腐蝕與防護(hù)網(wǎng)官方 QQ群:140808414
注:本稿為中國(guó)腐蝕與防護(hù)網(wǎng)版權(quán)所有,未經(jīng)允許, 嚴(yán)禁用于商業(yè)用途。轉(zhuǎn)載時(shí)請(qǐng)務(wù)必以超鏈接形式標(biāo)明文章原始出處和作者信息及本版權(quán)聲明。
官方微信