調質金相檢驗 調質是將亞共析鋼加熱超過Ac3以上30-50℃,當工件淬火溫度正常,保溫時間足夠,且冷卻速度也較高,過冷奧氏體在淬火過程中未發生分解,則淬火后得到的組織應是板條狀馬氏體和針片狀馬氏體。在中高溫回火過程中,馬氏體中析出碳化物,獲得回火索氏體或回火屈氏體。 1.1 調質組織與評定 為確保高強度螺栓淬火時奧氏體化充分,淬火組織均勻,無未溶鐵素體及非馬氏體組織,必須充分重視淬火態組織的金相檢驗。對10.9級及以上高強度螺栓而言,淬火組織的均勻性尤為重要。 國外的高強度螺栓熱處理非常重視鋼的充分奧氏體化,確保其組織的均勻性,以獲得最佳的強韌性配合,保障螺栓服役時安全可靠。國內高強度螺栓制造商對此尚未引起足夠重視,普遍存在的問題是螺栓淬火加熱保溫不足,奧氏體化不充分。 評定調質處理的質量一般采用GB/T 13320—2007《鋼質模鍛件金相組織評級圖與評定方法》。該標準適用于經過調質處理的結構鋼件,不適用于脫碳、過熱、過燒等組織的評定。 標準要求試樣應在冷態下用機械方法制取;若采用熱切時,必須將熱影響區完全去除。制樣過程中,不能出現因受熱而導致的組織改變現象。試樣拋光后用體積百分數2%~5%的硝酸酒精溶液侵蝕。 金相組織按1~8級評定,1級組織最好,8級組織最差。該標準第三組評級圖,適用于結構鋼調質處理件,尤其是高強度螺栓的調質檢驗。 被評定的調質組織介于兩個級別之間時,以下一級為判定級別,例如大于3級小于4級時,則判為4級。調質的金相組織分析,在光學顯微鏡下用500倍觀察,合格級別由供需雙方協商約定,沒有約定的以1級~4級為合格。生產實踐表明,在低溫環境下服役的螺栓,1級~3.5級為驗收標準。 如果在評級時有爭議,可以參考力學性能檢驗結果進行判定。 1.2 螺栓的調質及組織 GB/T 3098.1—2010《緊固件機械性能螺栓、螺釘和螺柱》強調對8.8級及以上產品的材料要求應有足夠的淬透性,以確保螺栓螺紋截面的心部在淬硬狀態、回火前獲得體積分數約90%的馬氏體。 為保證良好的淬透性,對于8.8級、螺紋直徑超過20mm的螺栓需采用標準規定的合金鋼材料淬火并回火。 淬火后馬氏體的粗細可按JB/T 9211—2008《中碳鋼與中碳合金結構鋼馬氏體等級》進行評定。由于奧氏體化溫度不同,馬氏體形態和大小不一樣。1級屬于奧氏體化溫度偏低,淬火組織是隱針馬氏體、細針馬氏體和體積分數不大于5%的鐵素體;而8級則屬于過熱組織,是粗大的板條馬氏體+粗片針馬氏體。 正常淬火時控制在3~5級,其組織為細小的板條馬氏體+片狀馬氏體,6級具有較高的沖擊韌性、屈服強度和抗拉強度,適用于較大規格且要求淬透性高的螺栓。 圖1為40Cr鋼板條狀及針狀馬氏體4級,圖2為45鋼板條狀及針狀馬氏體5級,圖3為SCM435鋼板條狀及針狀馬氏體4級,以上均為正常淬火組織。 圖1 板條狀及針狀馬氏體(40Cr,4級) 圖2 板條狀馬氏體混合體5級 圖3 板條狀及針狀馬氏體4級 回火索氏體組織實際上是在α相基體上分布的極小顆粒狀碳化物,如圖4、圖5所示。回火溫度根據高強螺栓等級要求,一般在450-600℃,具體溫度范圍視鋼的化學成分有所區別。 圖4 回火索氏體 圖5 回火索氏體 因為合金元素的加入會減緩馬氏體的分解、碳化物的析出和聚集以及殘余奧氏體的轉變等過程,回火溫度將移向更高。 調質的缺陷組織 2.1 淬火過熱組織 淬火加熱溫度偏高致使奧氏體晶粒長大,淬火后得到粗大的馬氏體組織,如圖6所示。一旦出現粗大針狀馬氏體,即使采用合理的回火溫度進行回火,也不能獲得較好的綜合力學性能,具有該組織的螺栓在使用過程中極有可能發生早期斷裂失效。 圖6 粗大的馬氏體組織(42CrMo,8級) SWRCH35K正常淬火溫度不超過870℃。圖7試樣為920℃淬火時,晶粒急劇長大,不同晶粒內平行的馬氏體位向是不同的,奧氏體化相應提高,淬火后殘余奧氏體相對多一些。粗大馬氏體組織綜合性能差,也容易淬裂。 圖7 粗大馬氏體及少量殘余奧氏體 2.2 淬火欠熱組織 高強度螺栓正常淬火后得到的組織應是板條狀馬氏體和針片狀馬氏體。淬火欠熱是淬火加熱溫度過低或保溫不足,奧氏體未均勻化,導致淬火后的組織為馬氏體和未溶鐵素體,如圖8所示。即使通過回火也不能消除鐵素體。 圖8 馬氏體和未溶的鐵素體 45鋼在Ac1~Ac3保溫,圖9鐵素體仍留在基體內。同時由于淬火溫度低,保溫時間短,奧氏體均勻化差,冷卻時局部發生屈氏體轉變。 圖9 淺灰色馬氏體+黑色團絮狀屈氏體+白色塊顆粒狀鐵素體 2.3 欠淬透組織 淬火溫度正常且保溫時間足夠,但冷卻速度不夠以至于不能淬透,結果沿工件截面各部位將得到不同的組織,即使表面是馬氏體,往中心會逐步出現非馬氏體組織。非馬氏體組織有屈氏體、貝氏體等,心部為屈氏體和鐵素體等組織。 在低合金鋼中出現的非馬氏體組織一般不是屈氏體,而是上貝氏體,如圖10所示。該組織為馬氏體基體上分布有少量貝氏體,用金相方法較容易檢驗出這種缺陷。 圖10 心部組織回火索氏體+上貝氏體 中碳調質組織形態取決于淬火態組織,加熱不足而殘留在馬氏體組織中的塊狀鐵素體,或冷卻不足而在晶界處析出網狀或半網狀鐵素體,都是有害的。 值得注意的是,加熱不足引起的未溶鐵素體與冷卻不足時先析出鐵素體在形態上是有區別的,前者呈圓鈍塊狀或厚薄不均勻斷續網狀(圖11),而后者是新形成的先共析鐵素體,形態上比較纖細,分布在奧氏體晶界上(圖12)。 圖11 淬火欠熱組織(40Cr) 圖12 淬火冷卻不足組織(40Cr) 常見熱處理淬火缺陷 螺栓調質熱處理工藝中淬火缺陷最為常見,如硬度不足、變形、開裂等。產生缺陷的原因很多,需從各方面分析,金相檢驗是常用的方法。 3.1 淬火裂紋 淬火時在螺栓中引起的內應力是造成變形與開裂的根本原因。當內應力超過材料的屈服強度時,便引起變形;當內應力超過材料的斷裂強度時,便造成開裂。只有拉應力是使裂紋萌生和擴展的必要條件。淬火裂紋原因可以從兩方面考慮,一是有哪些因素造成了較大的應力;二是材質有沒有缺陷,致使強度和韌性降低。 3.1.1 淬火裂紋特征 多數情況下裂紋由表面向心部擴展,宏觀形態較平直。 從宏觀與微觀看裂紋兩側均無脫碳,但如果在氧化性氣氛中進行過高溫回火,則淬火裂紋兩側會有氧化層(圖13)。 圖13 裂紋兩側嚴重脫碳 3.1.2 內應力增大引發正常組織淬火裂紋 設計不合理,如有尖角、截面突然變化,易引起應力集中。 冷卻太強烈,如本應采用快速淬火油,卻選擇了水溶液,不該冷透時冷透等。 淬火時冷卻方式不當,淬火后未及時回火。 3.1.3 組織缺陷引起淬火裂紋 淬火溫度偏高,奧氏體晶粒粗大,淬火后形成較粗大的馬氏體,容易開裂。特別是粗大的高碳馬氏體,常伴有顯微裂紋。 鋼材存在網狀碳化物等脆性相,淬火時易沿脆性碳化物網開裂。在晶界處有沿晶界分布的碳化物網絡,磨削時也容易磨裂。 鋼材有折疊或粗大夾雜物等缺陷,淬火時易沿此缺陷形成裂紋。 鋼材中存在嚴重偏析,淬火后組織不均勻,內應力較大且不均勻,容易開裂。 由于緊固件表面脫碳,淬火時表層體積膨脹小,受到兩相應力,容易形成龜裂。 3.2 淬火硬度不足 加熱溫度不足,冷卻時形成屈氏體,當屈氏體很少時,硬度無明顯變化,但金相組織容易鑒別。 淬火冷卻速度不足,淬火組織中除馬氏體外,還有屈氏體或貝氏體組織。屈氏體或貝氏體越多,硬度越低。 表面脫碳,淬火時不易形成馬氏體,或形成低碳馬氏體,如圖14所示。 圖14 表面脫碳鐵素體和低碳馬氏體 淬火過熱,過熱組織馬氏體粗大,殘余奧氏體量明顯增多,硬度也降低。 螺栓淬火回火后性能達不到技術要求,影響因素是多方面的,對其進行質量分析是一個復雜的過程。這里只是強調金相檢驗時應注意有無影響強韌性的不利因素,諸如晶粒粗大、非金屬夾雜物、網狀滲碳體、網狀鐵素體、淬火組織中的非馬氏體組織以及低倍檢測中的顯微偏析造成的組織不均勻等。
免責聲明:本網站所轉載的文字、圖片與視頻資料版權歸原創作者所有,如果涉及侵權,請第一時間聯系本網刪除。
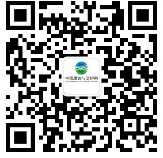
官方微信
《腐蝕與防護網電子期刊》征訂啟事
- 投稿聯系:編輯部
- 電話:010-62316606-806
- 郵箱:fsfhzy666@163.com
- 腐蝕與防護網官方QQ群:140808414