第二相顆粒是鋼材強韌化的重要方法,可以同時兼顧鋼材的強度、韌性以及其他服役性能。隨著近年來對鋼材強度要求的提高,研究人員開發出了一大批新型鋼鐵材料,第二相顆粒強韌化在這些新型鋼材中亦發揮了重要作用。但與此同時,在這些新型鋼鐵材料中,第二相顆粒強韌化也面臨著諸多挑戰與機遇:納米尺度顆粒的表征與調控、第二相顆粒與多相微觀組織的相互作用以及鋼材服役性能的優化等等。通過汽車輕量化用鋼、超高強度馬氏體時效鋼、核反應堆用鋼、高模量鋼等不同鋼材,總結了第二相顆粒對新型鋼鐵材料的強度、韌性、焊接性、成形性、抗氫致延遲斷裂、蠕變、抗輻射損傷等性能的影響,并結合這些新型鋼鐵材料獨特的微觀組織、制備工藝、服役環境等特點,分析了其第二相顆粒強韌化的機理以及尚待解決的問題,旨在為鋼中第二相顆粒強韌化領域的進一步研究與發展提供參考。
鋼中第二相顆粒的增強機理
鋼中的第二相顆粒可以阻礙位錯運動、孿生等變形過程,實現強化。以對位錯運動的阻礙作用為例,第二相顆粒增強機制主要分為切過機制與Orowan機制。
當第二相顆粒為可變形微粒時,增強機制為切過機制,即位錯可以切過顆粒,使其與基體一起變形。在切過機制中,位錯與第二相顆粒間的相互作用非常復雜,包括化學強化、堆垛層錯強化、模量強化、共格強化、有序強化等。第二相顆粒半徑越大或體積分數越大,切過機制的增強作用也越明顯。
當第二相顆粒不可變形時,增強機制為Orowan機制(也稱繞過機制,如圖1)。在位錯的運動過程中,位錯受顆粒阻擋而發生彎曲,產生反向應力τ=T/bR,b為伯氏矢量大小,R為位錯線的曲率半徑。當R=λ/2時(λ為顆粒間距),反向應力最大,此時的臨界分切應力為τc=T/2bλ。在實際材料中,常常通過減小顆粒尺寸或提高顆粒體積分數的方法來減小顆粒間距λ,從而獲得更好的強化效果。在位錯繞過第二相顆粒后,會形成位錯環包圍第二相顆粒, 進一步阻礙其他位錯在該滑移面上的運動,如圖1b。
圖1 第二相顆粒增強的Orowan機制:(a)位錯繞過顆粒之前,發生彎曲;(b)位錯繞過顆粒后,形成位錯環
第二相顆粒通常還存在細化晶粒的作用。根據霍爾-佩奇公式,晶粒半徑越小,材料的強度越高。另外,細晶強化一般不會造成材料韌性的下降。許多含第二相顆粒的鋼材都利用了這種強化機制。
第二相顆粒強韌化在新型鋼材中的應用
01 汽車輕量化用鋼
1.1 低合金高強度鋼
低合金高強度鋼(HSLA鋼)是指利用Nb、Ti、V等微合金化元素產生的析出強化與晶粒細化作用,獲得的具有較高強度的低碳鋼。HSLA鋼在汽車減重、節能等方面發揮了重要作用,至今仍廣泛應用于車輛的底盤、車身加強件等場合。
HSLA鋼的強化主要來自微合金化元素所形成的碳氮化物沉淀,強化機制包括了以Orowan機制為主的析出強化作用與熱機械軋制過程中的晶粒細化作用。具體而言,在熱機械軋制過程中,碳氮化合物能夠抑制奧氏體晶粒長大、再結晶等過程,在形變奧氏體中積累更多的變形帶、位錯等鐵素體形核位置,使鐵素體晶粒得到細化。終軋過后,HSLA鋼中固溶態的微合金元素會在冷卻、卷取等過程中繼續析出,其析出方式包括在奧氏體冷卻過程中析出、在奧氏體-鐵素體界面處相間析出、在鐵素體中均勻析出等等。相間析出(圖2)形成的析出物尺寸與析出物間距通常都很小,析出強化效果優異,是近幾年的研究熱點之一。研究發現,要想獲得最佳的相間析出強化效果,應提升碳化物形成驅動力,并降低奧氏體-鐵素體界面移動速度。
圖2 相間析出的細小彌散碳化物: (a)TEM照片 (b)高分辨TEM照片
盡管Nb、Ti、V都能起到細晶強化與析出強化作用。但由于在奧氏體中溶解度的不同,這些元素及其析出物在HSLA鋼中的主要作用也不同。例如,Ti的氮化物主要用于避免奧氏體重新加熱過程中的晶粒粗化,Nb的碳氮化物主要用于控制未再結晶區溫度范圍與A3轉變溫度,V的碳氮化物主要用于產生析出強化效果。在實際生產中,結合不同微合金化元素的優勢(例如Nb的細晶強化與V的析出強化),可以獲得更好的強化效果。但也有研究指出,Ti的加入會消耗大量Nb、V、N等元素,形成強化作用較弱的大顆粒,對Nb、V的析出強化效果造成不利影響。
HSLA鋼中的第二相顆粒與焊接性能、低溫韌性等也有著重要關系。首先,由于第二相顆粒提升了HSLA鋼的強度,HSLA鋼可適當采用較低的碳含量與總合金元素含量,防止脆性相的形成,從而保證焊接性能與低溫韌性。同時,氮化鈦等析出物可以成為針狀鐵素體在晶內的形核點,這些細小的針狀鐵素體能夠減小有效晶粒尺寸,提升HSLA鋼的焊接性能與低溫韌性。
1.2 先進高強度鋼
隨著汽車輕量化要求的不斷提升,研究人員開始探索強度更高的先進高強度鋼(AHSS鋼)。其中,第一代AHSS鋼(例如雙相鋼)已經廣泛應用到了汽車制造行業,第二、三代AHSS鋼的研發則仍是近幾年的熱點。
雙相鋼(DP鋼)屬于第一代AHSS鋼,其微觀組織主要由鐵素體與馬氏體兩相組成,其中,馬氏體保證了鋼材較高的拉伸強度,鐵素體則保證了鋼材較好的韌性。目前,商業化生產的DP鋼強度最高達1180MPa,延伸率仍保持在5%以上,可用于車輛的保險桿等部件。
DP鋼中的第二相顆粒強韌化主要也依靠Nb、V等微合金元素。據報道,國內外大多數雙相鋼的Nb含量在0.03%左右,V含量通常不超過0.1%。通過優化熱處理工藝,一方面,可以使大多數彌散的碳氮化物顆粒在鐵素體中析出,提升微觀組織中鐵素體的屈服強度,從而提升材料的屈服強度;另一方面,少量相對較大的碳氮化物顆粒在馬氏體中析出,可以降低馬氏體碳含量,提高馬氏體韌性,同時也可以減小鐵素體與馬氏體間的強度差別,降低界面處的應變不協調性,從而減小鐵素體-馬氏體界面處形成微裂紋的風險,提升DP鋼的韌性。此外,DP鋼中常常存在擴孔性能與高延伸率不匹配的問題,主要就是馬氏體與鐵素體間的應變不協調性導致的,上述第二相顆粒強韌化機制可以有效降低應變不協調性,從而提升DP鋼的擴孔性能。
第二代AHSS鋼中的孿晶誘發塑性鋼(TWIP鋼)同時具備高抗拉強度(可達1000MPa)與高延伸率(可達50%),有望實現高強度復雜汽車零部件的室溫成形。通過添加一定量的C與Mn元素(Mn含量(質量分數,下同)通常為15%~25%),TWIP鋼具有室溫穩定的奧氏體組織,在變形過程中,奧氏體內部形成大量孿晶,阻礙位錯滑移,產生動態霍爾-佩奇效應,從而使TWIP鋼擁有非常高的加工硬化率。盡管如此,TWIP鋼存在低屈服強度、高氫致延遲斷裂風險等缺點,限制了其實際應用。
第二相析出顆粒強化可以有效提升TWIP鋼的屈服強度。需要注意的是,TWIP鋼中的Mn含量很高,這可能會使碳氮化物的性質發生改變,比如增大釩碳化物在奧氏體中的溶解度,TWIP鋼中的最佳碳化物形成元素與熱處理工藝也因此變得難以確定。Scott等發現,在TWIP鋼中,Nb、V等元素主要以Orowan機制產生強化,而這些元素對屈服強度的貢獻則各不相同(圖3)。由圖可知,在合金元素含量小于0.1%時,Ti的強化效果最佳,但如果繼續增加Ti含量,鋼材中就會形成大的碳化釩夾雜物,強化效果也因此達到飽和,約150MPa,在3種元素中,V元素可以將屈服強度提升約250MPa,提升幅度最大。此外,由于TWIP鋼在變形過程中會形成大量孿晶與堆垛層錯,這些缺陷與碳化物之間的相互作用也值得深入研究。Yen等研究了含V4C3析出物的TWIP鋼,發現不全位錯與變形孿晶都能以類似于Orowan機制的方式繞過碳化物,同時,碳化物對孿晶移動的阻力會隨孿晶厚度的減小而增大。
由于TWIP鋼的強度與延伸率都很高,其冷成形零件的殘余應力非常大,因而TWIP鋼零部件的氫致延遲斷裂風險也往往很大。添加Al元素可以緩解TWIP鋼的延遲斷裂風險,但往往會降低TWIP鋼的屈服強度。研究表明,釩碳化物等第二相顆粒可以作為TWIP鋼中的有效氫陷阱,有望在提升TWIP鋼屈服強度的同時,降低延遲斷裂風險。不過,也有研究發現,在含Ti的TWIP鋼中,一旦存在尺寸較大的氮化鈦顆粒,材料的抗氫致延遲斷裂能力反而會出現下降。
圖3 TWIP鋼中不同合金元素對屈服強度的增強效果
淬火-配分鋼(Q&P鋼)屬于第三代AHSS鋼,綜合了低合金成分、高強度、高延展性的特點,受到廣泛關注。在熱處理過程中,Q&P鋼需要先淬火(Q)至馬氏體開始轉變溫度(Ms)與轉變終了溫度(Mf)之間,隨后在該溫度或高于該溫度的條件下保溫,進行配分(P)處理,在配分過程中,碳原子從過飽和馬氏體中向未轉變的奧氏體中擴散,提高了奧氏體穩定性,因而在冷卻至室溫后,Q&P鋼中通常可以保留10%~20%的亞穩殘余奧氏體,在變形過程中,這些殘余奧氏體逐漸轉變為馬氏體,產生相變誘發塑性(TRIP效應),從而實現高強度與高延伸率的結合。
02 馬氏體時效鋼
馬氏體時效鋼主要依靠納米金屬間化合物析出強化。類似的超高強鋼還包含合金碳化物強化的二次強化鋼、過渡碳化物強化的低合金鋼、納米析出強化的鐵素體鋼。本小節主要介紹其中的馬氏體時效鋼。
馬氏體時效鋼具有合金含量高、碳含量極低的成分特點,其主要強化來源就是無碳/超低碳馬氏體高位錯密度以及基體中納米金屬間化合物析出相。其韌性主要源于其無碳/超低碳馬氏體基體。值得指出的是,在高碳馬氏體中,碳原子引起馬氏體晶格嚴重畸變,導致位錯滑移體系大量減少。位錯很難在高碳馬氏體裂紋尖端產生和滑動,引起脆性斷裂。不同于高碳馬氏體,無碳/超低碳馬氏體的位錯的滑移系同一般鐵素體并無太大區別,只是其位錯密度比一般鐵素體要高, 位錯增殖能力不強,導致拉伸時加工硬化率和均勻延伸率都比鐵素體低。但是,位錯可以在無碳/低碳馬氏體的裂紋尖端產生及運動,引起裂紋鈍化及提高韌性。所以,在具備高強度的同時,馬氏體時效鋼也兼顧了高韌性,在飛機起落架等關鍵場合發揮著重要的作用。
馬氏體時效鋼的熱處理工藝主要包含了固溶處理和時效處理兩部分。在高溫固溶處理過程中,各析出相全部溶解在奧氏體中。在快速淬火過程中,母相奧氏體切變形成含高位錯密度的板條馬氏體,在時效處理中,這些高密度位錯可以作為形核點,促進高密度納米析出物的形成。在典型的18Ni馬氏體時效鋼中,通過調整Co、Mo、Ti的合金含量,可以改變其主要納米析出物Ni3Ti與Ni3Mo顆粒的尺寸與密度,得到屈服強度范圍在1400~2400MPa的馬氏體時效鋼。其中,Co的主要作用是降低Mo在基體中的溶解度,促進Ni3Mo納米顆粒的析出,充分提升馬氏體時效鋼的強度。
不過,馬氏體時效鋼也存在一些缺點。一方面,Ni3Ti與Ni3Mo等納米析出物與馬氏體基體間形成半共格或非共格界面,所以更傾向于在位錯、晶界等缺陷處非均勻形核,其尺寸、密度、分布的優化受到限制;另一方面,為保證非均勻形核時的納米析出物密度,馬氏體時效鋼中必須添加較高含量的Co元素,這樣一來,馬氏體時效鋼的成本非常昂貴。
近幾年,新型無Co馬氏體時效鋼的研究取得了較好的進展。北京科技大學呂昭平教授團隊通過析出物點陣錯配最小化的設計思路,開發出了價格低廉、抗拉強度2.2GPa、延伸率8.2%的無Co馬氏體時效鋼(圖4)。這種新型鋼材主要以Ni(Al,Fe)共格納米析出物進行強化,通過合金成分調節,該析出物與馬氏體基體間的點陣錯配度僅為0.03%±0.04%,可以在馬氏體中均勻形核,實現極高密度(1024m-3)、極細小(2.7nm)且均勻分布的納米析出強化,強化效果優異。與此同時,由于該合金不再依賴Ni3Ti與Ni3Mo強化,采用廉價的Al取代了昂貴的Co與Ti元素,其生產成本大大降低。
此外,共析出納米強化也有望用于改進馬氏體時效鋼非均勻形核、成本昂貴的缺點。共析出納米強化同時采用多種共格析出物,例如bcc-Cu、B2-NiAl、L21-Ni2AlTi等,以獲得高密度、小尺寸、均勻分布的納米析出物,不同析出物之間也會產生相互作用,使材料具備更優異的力學性能。以Cu/NiAl共析出納米強化鋼為例,其抗拉強度可達1.9GPa,延伸率達10%,斷面收縮率達40%。隨著合金成分的變化,Cu/NiAl的共析出機制也會隨之發生變化:當Cu含量較高時,基體中先形成富Cu納米析出物,在其生長過程中,Ni與Al元素會偏聚到析出物與基體的界面上,進而抑制富Cu納米析出物的生長,同時,NiAl納米析出物會在界面處不均勻形核;當Cu含量較低時,先形成NiAl基納米析出物,在析出物生長過程中,其內部的Cu也會偏聚至析出物與基體的界面,在界面處形成Cu納米析出物。通過合金成分的調節,Cu/NiAl共析出強化鋼中可以獲得尺寸小于5nm的析出物。
圖4 新型無Co馬氏體時效鋼:(a)應力-應變曲線 (b)共格納米析出物的高分辨TEM照片
03 核反應堆用鋼
為應對全球氣候變化問題,核電站的發展日益受到關注,核電安全也始終是大眾的關注焦點。核反應堆服役時,結構材料需要經受高溫、高應力、高輻射、化學腐蝕環境等非常惡劣的條件,可靠的結構材料在核電安全中起到了至關重要的作用。目前來看,鋼材在核電用結構材料中占有重要地位。同時,研究發現,鋼材中的第二相析出顆粒不但有望提升材料的抗蠕變性能,而且能夠增強材料的抗輻射損傷性能,本章將主要介紹在氧化物彌散強化鐵素體鋼(ODS鋼)基礎上進一步開發出的納米結構鐵素體合金(NFA合金)。
ODS鋼的主要特點就在于利用Y2O3顆粒,同時提升鋼材的抗蠕變與抗輻射損傷性能。不過,受到溶解度限制, 傳統的熔煉技術無法在鋼材中引入Y元素,即便引入Y之后,鋼材中的Y原子也很難形成氧化物,無法發揮預期作用。20世紀80年代,Fisher等發現,通過Y2O3粉末與富鐵合金粉末的機械合金化(MA)與熱固結處理,可以獲得具有納米尺度析出物的ODS鋼,這種ODS鋼同時具備了高準靜態強度、高蠕變強度與高抗輻射損傷性能。目前,機械合金化是ODS鋼(與NFA合金)的主要制備手段。最近的研究發現,在機械合金化時,高能球磨可以使Y2O3溶于富鐵合金粉末,在隨后的熱固結處理中再析出細小的氧化物納米團簇,相比于傳統ODS鋼中尺寸較大的氧化物顆粒,此類氧化物納米團簇對蠕變強度、抗輻射損傷性能的增強效果更加明顯。通過調整合金成分與工藝參數,可以獲得非常高密度的氧化物納米團簇,為區別于傳統ODS鋼,此類鋼材稱作NFA合金。目前,除Y2O3外,NFA合金中還會添加一定量的Ti,以降低氧化物納米團簇尺寸。
氧化物納米團簇對NFA合金抗蠕變性能的增強機制主要有以下幾個方面。首先,NFA合金中的氧化物納米團簇具有非常高的熱穩定性,例如,在1200℃保存24h后,14YWT合金中氧化物納米團簇的密度仍未發生明顯改變。第二,在高溫下,這些細小的、高密度的、穩定的氧化物納米團簇能夠阻礙位錯的滑移、攀移,減緩位錯的回復過程,抑制位錯蠕變機制。第三,晶界處大量彌散的氧化物納米團簇還可以提升NFA合金的擴散蠕變強度。
中子或帶電粒子的輻射會引起輻射硬化/軟化、輻射脆性、輻射腫脹、與蠕變壽命下降等現象,導致鋼材性能惡化。 圖5對比了NFA合金與回火馬氏體鋼中的輻射損傷機制。回火馬氏體鋼的抗輻射損傷性能較差,首先,輻射會在微觀組織中形成大量自間隙原子位錯環與細小析出物,導致輻射硬化與輻射脆性;輻射還會在微觀組織中形成孔洞,導致輻射腫脹;此外,輻射所產生的He會在晶界處積累,促進蠕變孔洞的形成,降低材料的蠕變壽命。相比之下,NFA合金中存在大量細小且穩定的氧化物納米團簇,可以作為輻射缺陷的湮滅位置,有效抑制輻射腫脹等現象;同時,氧化物納米團簇保證了鋼材在高溫高輻射的環境下仍具有高位錯密度,高密度納米團簇與位錯能夠將He分散到細小的氣泡中,避免晶界處He聚集而導致沿晶斷裂。
圖5 NFA合金(a)與回火馬氏體鋼(TMS) (b)中子輻射損傷機制
04 高模量鋼
為實現鋼結構件的輕量化,必然要減小結構件的厚度。然而,結構件的剛度對其厚度十分敏感,為避免由幾何失穩所導致的災難性屈曲(buckling),鋼材的楊氏模量需要得到進一步提高。常規的鋼材強韌方法,包括固溶強化、析出強化、晶界強化等,并不能有效提高材料整體的楊氏模量。現今唯一有效增強鋼材楊氏模量的方法則是將某種陶瓷作為增強相加入到鋼材中,引入的方法既可從外部引入(ex-situ),例如采用粉末冶金方法,也可在鋼材內部由化學反應原位生成(in-situ)。這樣制備出的陶瓷增強鋼,又叫做高模量鋼,具有傳統金屬材料所欠缺的諸多優點,例如高模量、低密度、高硬度以及良好的耐磨性,同時鋼本身作為基體亦使其具有可靠的塑性及延伸率。因此高模量鋼既可以被用于需要耐熱耐磨的發動機或剎車部件,例如活塞和剎車盤等,又可作為高強度高模量部件的材料,例如底盤、曲軸、連桿等。對陶瓷種類的選擇,主要依據其是否具有高強度、高模量、低密度、高耐磨以及高熔點等屬性,因而常見的陶瓷材料主要是C、O、B等的化合物,包括TiC、TiB2、SiC、WC、SiO2、Al2O3、NbC等。此外,所選取的陶瓷不能與鋼材本身發生化學反應生成新的組織,因為該組織極有可能會影響該復合材料的力學性質。
高模量鋼的強化機理可分為直接強化和間接強化。前者主要通過負荷轉移的方式來實現,亦即材料整體所承擔的負荷會由基體經過鋼/陶瓷界面而轉移到強度更高的陶瓷。這種方式使得增強相分擔了大部分的外加載荷,從而使得材料整體具有更高的強度。直接強化的效率不僅受增強相的體積分數或形貌(較高長寬比通常優于球形顆粒)的影響,還主要取決于界面的強度,因為界面充當了負荷由基體向陶瓷顆粒轉移的介質。據此分析,傳統粉末冶金方法不僅會導致非共格界面(較弱)的形成,還可能使得界面處形成孔隙,嚴重影響界面的整體強度。這樣制備出的高模量鋼在形變過程中會率先發生界面脫粘并導致直接強化模式的失效。相比之下,在鑄造凝固過程中通過共晶反應可以原位生成新的增強相,據此制備出的原位高模量鋼(例如鐵基TiB2增強鋼)具有更高的界面強度(共格界面)以及負荷轉移效率,其拉伸性能會優于粉末冶金所制備的相同(成分、微觀組織形貌)材料。
間接強化則由兩相的熱膨脹系數的差異導致。由于鋼的熱膨脹系數通常遠大于陶瓷,在冷卻過程中(例如淬火、退火降溫)基體將產生更大程度的收縮從而對陶瓷產生擠壓。由于基體和陶瓷模量的差異,基體冷卻產生的形變無法有效傳遞至陶瓷,導致兩相界面處(基體一側)發生明顯的形變梯度,該梯度必將導致幾何必需位錯的形成并伴隨新的殘余應力。換句話說,高模量鋼的間接強化的直接原因是界面處的幾何必需位錯。實驗發現陶瓷增強材料的屈服強度在壓縮過程中明顯高于其在拉伸過程,證明了殘余應力的存在。然而與直接強化相比,間接強化更難進行定量分析,主要原因在于幾何必需位錯的不均勻分布及其對材料整體強度貢獻的機理尚不成熟。
結語
作為同時提升強度與韌性的有效方法,第二相顆粒強韌化在各類鋼材中都起到了至關重要的作用,而在新型鋼材中,更高的性能要求與復雜的微觀組織也給第二相顆粒強韌化帶來了更大的發揮空間與更多的挑戰。以汽車用鋼為例,很多新型鋼材已經在鋼廠實現量產,卻因為焊接性能、低溫韌性、抗氫致延遲斷裂性能等方面的限制,無法在汽車產業推廣。第二相顆粒強韌化不但能夠保證新型鋼材的強度與韌性,也為改進這些實際服役性能提供了有效方法。同時,新型鋼材中涉及的復相組織析出物、氫與第二相顆粒的相互作用、納米共析出強化等研究課題也對科研人員提出了更高的要求。未來,隨著原子尺度實驗表征技術、模擬技術的不斷發展,人們對第二相顆粒強韌化認識的不斷深入,第二相顆粒有望更好地發揮其強韌化作用,推動更多新型鋼材走向實際應用。
免責聲明:本網站所轉載的文字、圖片與視頻資料版權歸原創作者所有,如果涉及侵權,請第一時間聯系本網刪除。
相關文章
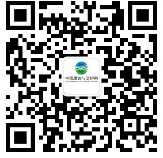
官方微信
《中國腐蝕與防護網電子期刊》征訂啟事
- 投稿聯系:編輯部
- 電話:010-62316606-806
- 郵箱:fsfhzy666@163.com
- 中國腐蝕與防護網官方QQ群:140808414
點擊排行
PPT新聞
“海洋金屬”——鈦合金在艦船的
點擊數:7130
腐蝕與“海上絲綢之路”
點擊數:5741