電子束表面熔覆技術(shù)已經(jīng)成為當(dāng)前的研究熱點(diǎn),其能量密度高、加工速度快、功率參數(shù)可控性好和綠色環(huán)保等優(yōu)點(diǎn)廣泛應(yīng)用于各個(gè)領(lǐng)域。 電子束表面處理是以加速電子為載體的入射能量, 在極短的時(shí)間內(nèi)作用于材料表面薄層內(nèi),由此引發(fā)快速熔化、凝固、汽化、應(yīng)力波、沖擊波和增強(qiáng)擴(kuò)散等物理化學(xué)現(xiàn)象, 使材料能獲得普通熱處理方法難以達(dá)到的物理、化學(xué)及力學(xué)性能 ,最終得到基體表面具有特定合金成分及特定性能的改性層。 本文對(duì)電子束熔覆技術(shù)的原理、研究現(xiàn)狀和存在的問(wèn)題進(jìn)行了綜述。
1 電子束熔覆改性技術(shù)的原理
1.1 電子束材料表面加熱機(jī)理
當(dāng)高速的電子束流掃射被處理的基體表面時(shí),電子能穿過(guò)基體的表面到達(dá)距離表面的一定深度,將能量傳遞給基體的金屬原子, 致使金屬原子的震動(dòng)加劇,該過(guò)程是把電子的動(dòng)能轉(zhuǎn)化為熱能,從而使被處理基體的表層溫度迅速升高。 電子束焊接時(shí)熱量在被掃射材料表面下的某一薄層下析出, 該薄層被稱(chēng)為電子穿透層,如圖 1 所示,電子穿透層的厚度跟電子加速電壓的平方成正比,跟基體材料的密度成反比,一般都在 1mm 以內(nèi)。 當(dāng)電子撞擊到基體表面時(shí)首先穿越電子穿透層, 此時(shí)電子的動(dòng)能幾乎不變, 僅極少部分能量被彈性散射電子帶走或損耗于二次電子發(fā)射,因此電子不能對(duì)穿透薄層進(jìn)行加熱。當(dāng)電子進(jìn)入基體內(nèi)部后, 穿透至電子行程的那一厚度上,由于在次表層擴(kuò)散受阻,從而引起能量傳輸,將動(dòng)能轉(zhuǎn)化為熱能使基體表面發(fā)生熔化 。
1.2 電子束熔覆改性原理
電子束熔覆技術(shù)作為涂層預(yù)置后的改性處理方法,電子束熔覆前,需將涂層預(yù)置在基體上,根據(jù)要求:厚度一般為幾微米到幾毫米。然后利用高能量密度電子束熱源經(jīng)聚焦后對(duì)預(yù)置涂層材料表面進(jìn)行處理, 瞬間可把涂層由室溫加熱至奧氏體化溫度或熔化溫度,使涂層全部熔化,基體表層部分熔化,增加涂層與基體之間的粘結(jié)強(qiáng)度,改善涂層性能 。 電子束熔覆時(shí)只有嚴(yán)格控制能量密度, 才能精確保證涂層及基體熔化深度。 能量密度過(guò)大會(huì)導(dǎo)致基體熔化深度加大,涂層成分嚴(yán)重稀釋?zhuān)砻娲植诙仍黾印?能量密度過(guò)小會(huì)導(dǎo)致涂層未充分重熔, 進(jìn)而造成涂層與基體之間的粘結(jié)強(qiáng)度降低。 圖 2 為電子束熔覆改性原理示意圖。
1.3 電子束熔覆改性特點(diǎn)
電子束熔覆技術(shù)是近期發(fā)展起來(lái)的新技術(shù),其在表面熔覆改性方面主要有以下幾個(gè)特點(diǎn): 電子束能量密度高,利用率高,僅需毫秒間就可將金屬材料表面由室溫加熱至奧氏體化溫度或熔化溫度, 且冷卻速度可達(dá) 10 6 ~10 8 ℃/s ;與激光相比使用成本低。電子束處理設(shè)備一次性投資比激光少 ( 約為激光的1/3) ,其運(yùn)行成本比激光低一半左右 ;電子束能量和能量密度的調(diào)節(jié)很易通過(guò)調(diào)節(jié)加速電壓、 電子束流和電子束的匯聚狀態(tài)來(lái)完成 , 整個(gè)過(guò)程易于實(shí)現(xiàn)自動(dòng)化;電子束加熱深度和尺寸范圍比激光大。 電子束加熱時(shí)熔化層至少幾個(gè)微米厚, 能量沉積范圍較寬,而且約有一半電子作用區(qū)幾乎同時(shí)熔化;電子束加工是在真空條件下進(jìn)行的,既不產(chǎn)生粉塵,也不排放有害氣體和廢液,對(duì)環(huán)境幾乎不造成污染,加工表面不產(chǎn)生氧化, 特別適合于加工易氧化的金屬及合金材料,以及純度要求極高的半導(dǎo)體材料。
2 電子束表面熔覆改性技術(shù)研究現(xiàn)狀
電子束雖然在工業(yè)中的應(yīng)用有幾十年的歷史,但是在表面熔覆改性方面的應(yīng)用則始于 20 世紀(jì) 70年代初期。 由于該技術(shù)在不斷的改進(jìn)和完善, 已經(jīng)成為材料表面改性方面一個(gè)強(qiáng)有力的工具。國(guó)內(nèi)外的相關(guān)機(jī)構(gòu)對(duì)電子束熔覆進(jìn)行了廣泛而深入的研究。
2.1 國(guó)外研究現(xiàn)狀
電子束表面熔覆技術(shù)在國(guó)外研究地區(qū)主要集中在北美、歐洲及亞洲。 主要內(nèi)容包括以下幾個(gè)方面。
2.1.1 電子束熔覆工藝及強(qiáng)化機(jī)理研究
Weisenburger 采用高速火焰熱噴涂方法用鎳基合金制備 CoNiCrAlY 涂層,再進(jìn)行電子束重熔研究。結(jié)果表明:距離表層 30~40μm 范圍內(nèi)氣孔被徹底消除, HVOF 涂層表面粗糙度由 62μm 下降至 3.7μm ,而 VPS 涂層表面粗糙度也從 47μm 下降至 8μm ,高溫氧化試驗(yàn)涂層氧化膜增長(zhǎng)尺度減小。 重熔的CoNiCrAlY 涂層作為電子束物相沉積熱障涂層與基體間的粘結(jié)層,近表層氣孔的消除、快速熔凝的表層細(xì)小晶粒和表面粗糙度的降低對(duì) EB-PVD 熱障涂層的形成十分有利。 粘結(jié)層中氧化物 (TGO) 的生長(zhǎng)導(dǎo)致熱障涂層 (TBC) 中應(yīng)力的引入,并最終導(dǎo)致TBC 涂層撕裂。 電子束處理有助于 HVOF 涂層中TGO 的生成方式由脫離式轉(zhuǎn)變?yōu)檫B續(xù)式。
2.1.2 電子束表面熔覆層相組成控制的研究
Eunsub 采用 Ti-6Al-4V 鈦合金作為基體,在其表面電子束熔覆 Ti+B 4 C , 研究改性層硬質(zhì)相分布。結(jié)果表明表面熔覆后的改性層中均勻分布大量的硬質(zhì)相 TiC 和 TiB ,且改性層耐熱性能得到提高。 AGTyurin 等在建筑類(lèi)鋼材 45 鋼和 20 鋼表面預(yù)涂混合粉末涂層 VK6 和 T15K6 ,之后用電子束掃描熔覆處理。 結(jié)果顯示:在 0.8mm 深的熱影響區(qū)形成了魏氏組織。 改性 層呈現(xiàn)出樹(shù) 枝狀 結(jié) 構(gòu) ,硬 度 達(dá) 到1700 HV , 在包含一些碳化物粒子的區(qū)域硬度達(dá)2500~2700HV ,改性層的耐磨性也得到提高。 IgbalM 等將合金粉末碳化硼涂覆在低碳鋼 (MS) 基體上,利用電子束對(duì)其進(jìn)行表面熔覆處理。 研究表明:經(jīng)過(guò) 10keV , 50~100mA 的電子束掃描后, 合金粉末熔入基體中;經(jīng)過(guò) XRD 分析,基體熱影響區(qū)中含有碳化硼成分; SEM 分析顯示基體纖維組織中鐵素體轉(zhuǎn)變?yōu)橹В楣怏w重結(jié)晶后得到細(xì)化,基體的硬度是處理前的 6 倍。
2.1.3 電子束表面熔覆制備合金層耐磨性的研究
烏克蘭的 Pogrebnjak 等人主要研究了強(qiáng)流脈沖電子束對(duì)材料結(jié)構(gòu)的影響, 提高了表面熔覆層對(duì)于各種材料表面的性能。 他們采用電子束蒸鍍金屬薄膜與 HCPEB 后處理結(jié)合的方法, 在純鐵表面實(shí)現(xiàn)了鉬、鉭、鋁、鉻等元素的合金化,最終提高了純鐵的耐腐蝕性和耐磨性。 Zenker 等研究了在較軟基體上,利用電子束熔覆高硬度合金粉末,結(jié)果表明,經(jīng)電子束掃描后,基體與涂層之間熔為一體,其涂層的表面硬度、強(qiáng)度和耐磨性都有所提高。
2.2 國(guó)內(nèi)研究現(xiàn)狀
國(guó)內(nèi)電子束表面熔覆技術(shù)起步落后于國(guó)外工業(yè)發(fā)達(dá)國(guó)家,這方面的研究尚處于起步階段。目前國(guó)內(nèi)研究?jī)?nèi)容主要涵蓋以下幾個(gè)方面。
2.2.1 電子束表面熔覆對(duì)材料表面力學(xué)性能提高的研究
葉宏等人在 AZ91D 鎂合金基體上采用真空電子束熔覆制備了鋁涂層。 AZ91D 鎂合金基體的硬度 為 60 ~80 HV0.05 , 噴 鋁 層 的 硬 度 為 40 ~45HV0.05 。 經(jīng)電子束熔覆處理后,涂層與基體結(jié)合良好,主要由熔覆區(qū)、合金化區(qū)和熱影響區(qū) 3 部分組成。 在涂層表面,由于 Mg 溶入 Al 中產(chǎn)生固溶強(qiáng)化,使鋁層的硬度提高到 115HV0.05 左右。 中間 Al-Mg合金化層因存在大量 Mg 17 Al 12 、 Mg 2 Al 3 等金屬間化合物 , 硬度最高 , 達(dá)到 220HV0.05 。 在熱影響區(qū) , 由于基體金屬快速熔凝產(chǎn)生晶粒細(xì)化, 從而導(dǎo)致硬度增加,約為 130HV0.05 。 鎂合金材料表面硬度的顯著提高,有利于材料表面耐磨性能的提高。 陸斌鋒等用(Cr , Fe)7 C 3 和 52Cr 3 C 2 -48Fe( 質(zhì)量分?jǐn)?shù)為 52%Cr ,8%C- 和 40%Fe) 混合粉作為原料粉預(yù)置于 903 鋼表面上,經(jīng)電子束熔覆后,合金層的顯微硬度在 1020~1080HV0.5 ,約為基體顯微硬度 (350HV0.5) 的 2.3~3.1 倍。 合金層的相對(duì)耐磨性也比基體提高了 10.5倍。 這說(shuō)明在低合金鋼表面電子束熔覆合金層能顯著提高基體的耐磨損性。 王英對(duì) ZL109 鋁硅合金采 用 直 徑 為 0.8 mm 0Cr25Ni20 和 直 徑 為1.0mm 的 1Cr18Ni9Ti 作為涂層, 然后進(jìn)行表面熔覆處理,發(fā)現(xiàn)其表面硬度達(dá) 55~60HRB ,是基體硬度的 4~6 倍,與高鎳鑄鐵基本相當(dāng),但其耐磨性能高于高鎳鑄鐵。 劉科等人采用 45 鋼作為基體,以鈷基碳化鎢粉末 (WC-12Co) 作為涂層,經(jīng)過(guò)電子束熔覆后,改性層的平均硬度為 1280HV ,最高硬度可達(dá) 1450HV ,且改性層的深度更大,其耐磨性也提高了 10~12 倍。 石其年在 45 鋼表面用 WC/Co+TiC涂層粉末進(jìn)行電子束熔覆后, WC/Co 合金化層的耐磨性比常規(guī)淬火提高了 52 倍, Ni 、 Cr 粉末合金層的耐磨性約為常規(guī)處理的 2~7 倍。
2.2.2 電子束表面熔覆制備合金層耐腐蝕性的研究
張可敏等人將 Ti 粉末預(yù)涂在 316L 不銹鋼表面后,采用 10 次強(qiáng)流脈沖電子束進(jìn)行后處理,在電子束對(duì)表面涂層快速加熱熔化、 混合及增強(qiáng)擴(kuò)散效應(yīng)的作用下,部分鈦熔入基體表層形成一層富鈦層,其在模擬體液中的耐腐蝕性得到了顯著提高。 同樣馬廷濤利用 9310 滲碳軸承鋼作為基體, Ti 粉作為涂層,經(jīng)電子束 10 次強(qiáng)流脈沖熔覆后,耐腐蝕性有了一定的提高。 曹輝在純鎂上利用強(qiáng)流脈沖電子束表面滲透 Al ,發(fā)現(xiàn)其耐腐蝕性顯著提高,維鈍電流降低 2 個(gè)數(shù)量級(jí)以上,并且隨著轟擊次數(shù)的增加,腐蝕性能得到改善。
3 存在的問(wèn)題和發(fā)展前景
通過(guò)研究, 電子束熔覆技術(shù)可使基體表面局部熔化區(qū)以極快的速度冷卻, 形成急速凝固的表面微觀組織結(jié)構(gòu),晶粒細(xì)化甚至形成微晶、非晶態(tài)固體。表面非晶層的形成可使材料表面變得光滑致密,表面力學(xué)性能得到很大改善, 同時(shí)也可提高表面耐腐蝕性、抗氧化性和隔熱性能。但電子束熔覆技術(shù)還存在一些欠缺, 今后可從以下幾方面進(jìn)一步開(kāi)展電子束熔覆技術(shù)的研究工作。
(1) 電子束與表層金屬熱力耦合機(jī)理。 與激光熔覆技術(shù)的研究相比還有一定差距, 電子束與材料之間的耦合作用機(jī)制還需進(jìn)一步深入研究。 數(shù)值模擬技術(shù)可以優(yōu)化電子束熔覆工藝, 將熔覆過(guò)程的溫度場(chǎng)、殘余應(yīng)力場(chǎng)及流場(chǎng)進(jìn)行數(shù)值模擬,即可把握和控制電子束熔覆工藝的過(guò)程。
(2) 電子束熔覆技術(shù)的缺陷。 電子束熔覆技術(shù)與等離子束噴涂在成本和工藝上有相對(duì)的優(yōu)勢(shì),但是該工藝對(duì)微小及薄壁零件進(jìn)行熔覆時(shí), 由于電子束的溫度場(chǎng)瞬間溫度較高, 易造成薄壁零件的熔化或變形,這也是今后要解決的問(wèn)題。
(3) 電子束 3D 打印技術(shù)。 電子束熔覆技術(shù)大部分僅限于二維平面使用,在未來(lái)的發(fā)展中,電子束熔覆技術(shù)可以用于三維產(chǎn)品, 也就是電子束 3D 快速成型技術(shù)。 通過(guò)計(jì)算機(jī)程序控制電子束按零件截面輪廓信息有選擇性地熔化金屬粉末, 一層一層的堆積,直至整個(gè)零件全部熔化完成,最后去除多余的粉末,得到所需的三維產(chǎn)品。與激光及等離子束快速成形技術(shù)相比, 電子束快速成形技術(shù)具有能量利用率高、加工速度快、功率大、運(yùn)行成本低和高真空保護(hù)等優(yōu)點(diǎn), 是高性能復(fù)雜粉末冶金件的理想快速制造技術(shù),在航空航天、汽車(chē)制造及生物醫(yī)學(xué)等領(lǐng)域有著廣闊的發(fā)展前景。
更多關(guān)于材料方面、材料腐蝕控制、材料科普等方面的國(guó)內(nèi)外最新動(dòng)態(tài),我們網(wǎng)站會(huì)不斷更新。希望大家一直關(guān)注中國(guó)腐蝕與防護(hù)網(wǎng)http://www.ecorr.org
責(zé)任編輯:王元
《中國(guó)腐蝕與防護(hù)網(wǎng)電子期刊》征訂啟事
投稿聯(lián)系:編輯部
電話:010-62313558-806
中國(guó)腐蝕與防護(hù)網(wǎng)官方 QQ群:140808414
免責(zé)聲明:本網(wǎng)站所轉(zhuǎn)載的文字、圖片與視頻資料版權(quán)歸原創(chuàng)作者所有,如果涉及侵權(quán),請(qǐng)第一時(shí)間聯(lián)系本網(wǎng)刪除。
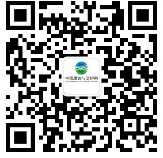
官方微信
《中國(guó)腐蝕與防護(hù)網(wǎng)電子期刊》征訂啟事
- 投稿聯(lián)系:編輯部
- 電話:010-62316606-806
- 郵箱:fsfhzy666@163.com
- 中國(guó)腐蝕與防護(hù)網(wǎng)官方QQ群:140808414