七章 腐蝕控制
Vol.7.5 選材、腐蝕試驗及腐蝕控制
7.5.3 覆蓋層保護
7.5.3.5 壓力容器涂裝工藝規程的編制
涂裝工藝規程的擬定是把涂裝工藝和操作規程按設計內容固定下來的一套科學、合理的技術文件形式,這是保證涂層質量的必要條件。完善的涂裝工藝規程應該包括:涂料的品種、涂裝工序及其技術條件、使用的設備和工具、質量標準和工時等,具體內容有:
01 涂裝工序
涂裝工序從被涂物的表面處理開始,直至面漆養護為止,每一步工序都要詳細列出,包括每一工序的干燥時間、工序間的表面處理、每一工序的要點等;
02 技術條件
包括涂料品種的確定,涂裝方法的選擇,作業溫度,涂料干燥的溫度與時間,涂裝用的稀釋劑等,都要做出詳細的規定,這是保證涂層質量的關鍵性內容;
03 設備
涂裝作業中每一工序所使用的設備和工具都應列入操作規程,作為操作人員的施工依據;
04 質量標準
涂裝中每一工序應達到的質量標準是檢查評定涂裝質量的依據。操作人員可根據這些標準進行自檢和互檢,是最終驗收的質量標準;
05 其他
附加說明,可視具體情況加以補充。
涂裝工藝規程的編制無統一格式,一般以適用性文件或工藝卡的形式來擬定涂裝工藝,結合各單位的生產技術水平和被涂物的具體情況靈活編制,形成具有先進的技術水平、合理的、能指導生產的技術文件。因此,在編制涂裝工藝時須了解和熟悉以下幾方面的內容:涂料的性能和用途、涂裝目的和涂層類型、涂裝條件、涂裝行業的技術水平、職業衛生要求。
a.表面處理:
應根據容器鋼材表面不同的銹蝕情況和涂裝設計要求編制合理可行的表面處理施工方案,并嚴格按照施工方案組織施工。
i.基體表面處理方法及質量等級參照GB/T 8923的規定,有產品說明書的按說明書要求進行,有特殊要求的應按規定進行。
ii.涂裝前應對待涂表面進行表面處理,應按下列規定進行預處理:
-對金屬表面進行預檢,如發現漏焊、斷焊、裂縫、拉口、穿孔等缺陷,應報告相關部門進行整改;
-涂裝前應確定待處理表面的銹蝕等級和除銹等級;
-應采用動力或手工工具對焊縫、焊渣、毛刺、邊緣彎角和噴射處理無法到達的區域進行處理。
iii.底層涂料對鋼材表面除銹等級的要求,應符合SHS 01034 附錄B表6.3-2的規定,對銹蝕等級為D級的鋼材表面,應采用噴射或拋射除銹。儲罐、設備內涂層防腐蝕除銹等級應按高一等級處理;
iv.表面不作噴砂處理的螺紋、密封面及光潔面應妥善保護,不得受損;
v.經酸洗處理的設備、管道應立即用水沖洗、中和鈍化及干燥;
vi.基體表面處理的質量經質檢人員檢查確認合格后,方可進入下道工序。如發現有返銹,需重新進行表面處理。
b.表面除銹可以采用下列方法:
i.干噴射法:宜采用石英砂為磨料,以0.4~0.7MPa潔凈干燥的壓縮空氣噴射時,噴射后的金屬表面不得受潮。當金屬表面溫度低于露點溫度以上3℃時,噴射作業應停止。環境露點溫度確定,可參考附錄C;
ii.手動工具除銹法:采用敲銹榔頭等工具除掉鋼表面上的厚銹和焊接飛濺物,再用鋼絲刷、鏟刀等工具刷、刮或磨,除掉鋼表面上松動的氧化皮、疏松的銹和舊涂層等;
iii.動力工具除銹法:用動力驅動旋轉式或沖擊式除銹工具,如旋轉鋼絲刷等,除去表面上松動的氧化皮、疏松的銹和舊涂層等。鋼表面上動力工具和噴射不能達到的地方,必須用手動工具做補充清理。當采用沖擊式工具除銹時,不應造成鋼表面損傷,采用旋轉式工具除銹時,不宜將表面磨的過光。
iv.被油脂污染的金屬表面,除銹前,可采用溶劑或堿洗的方法去除油污,油污去除后,應用水或蒸汽沖洗。
v.表面舊涂層可以用下列方法清除:
-機械法;
-火燒法:對薄壁容器應有防止殼體變形的措施,并不適用于經過熱處理的設備;
-熱堿溶解法:采用本法時應有排放殘液的措施,并不適用于耐堿腐蝕的涂層;
-脫漆劑法:采用本法時應有排放殘液和保護操作人員皮膚的措施,脫漆完成后應用汽油沖洗、擦凈后才能進行涂裝。
c.噴砂處理規定:
i.噴砂處理時,應采取妥善措施,防止粉塵擴散;
ii.壓縮空氣應干燥潔凈,壓縮空氣流應經過脫水脫油的處理,不得含有水分和油污,并經以下方法檢查合格后方可使用:將白布或白漆靶板置于壓縮空氣流中1分鐘,其表面目視觀察應無油、水等污跡。空氣過濾器的填料應定期更換,空氣緩沖罐內積液應及時排放;
iii.應按附錄A的規定選用合適的磨料和設備進行表面處理。磨料應具有一定的硬度和沖擊韌性,磨料必須凈化,使用前應經篩選,不得含有油污。天然砂應選用質堅有棱的金剛砂、石英砂、硅質河砂等,其含水量不應大于1%。嚴禁使用海砂。
iv.噴砂處理薄鋼板時,磨料粒度和空氣壓力應適當;
v.要求達到Sa2.5級和Sa3級時,不宜使用河砂作為磨料;
vi.當噴嘴出口端的直徑磨損量超過起始內徑的20%時,噴嘴不得繼續使用;
vii.磨料需要重復使用時,循環使用的磨料應有專門回收裝置,并必須符合有關規定;
viii.磨料的堆放地及施工現場應平整、罩實,防止磨料受潮、雨淋或混入雜質;
ix.表面噴射處理后,應采用潔凈的壓縮空氣吹掃、真空吸塵器清理或使用棉紗、棉布擦拭所有待涂的鋼表面,并應盡快實施底涂;
x.噴砂槍氣流的出口壓力宜為0.5~0.8MPa。
d.容器鋼表面經處理后表面粗糙度應符合下列要求:
i.采用涂料涂裝時,錨紋深度應為40~80μm。對有機富鋅涂料為40~60μm、對無機富鋅涂料為60~80μm;
ii.表面粗糙度尚應符合設計文件和所用涂料規定的要求;
iii.表面清潔度和表面粗糙度可按附錄D進行測定。測定時,也可參照現場制作的樣板或圖像樣本,但現場制作的樣板應采取適當的措施妥善保護。容器鋼表面經處理后表面清潔度必須符合下列要求:
-采用磨料噴射處理的鋼表面應達到Sa2.5級或Sa3級;
-采用手工或動力工具處理的局部鋼表面應達到St3級;
-表面可溶性氯化物殘留量不得高于30mg?m-2。測定方法見附錄D。
e.表面處理質量抽查:
i.宏觀檢查主要被處理表面是否有漏除部位,并應注意轉角部位除銹質量和表面油污、浮塵的清除;
ii.局部抽樣檢查應將除銹表面與GB/T 8923中的典型樣片照片進行對比檢查。設備應逐臺檢查,每臺抽查5處,每處檢查面積不小于100cm2。附屬鋼結構按類別進行檢查,每類不少于5處,每處檢查面積不小于100cm2;
iii.發現不合格應重新處理,直至合格。
免責聲明:本網站所轉載的文字、圖片與視頻資料版權歸原創作者所有,如果涉及侵權,請第一時間聯系本網刪除。
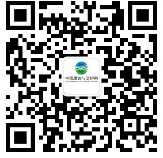
官方微信
《中國腐蝕與防護網電子期刊》征訂啟事
- 投稿聯系:編輯部
- 電話:010-62316606-806
- 郵箱:fsfhzy666@163.com
- 中國腐蝕與防護網官方QQ群:140808414