針對(duì)極限規(guī)格鋼板熱處理控制精度低、復(fù)雜工藝實(shí)現(xiàn)困難等問題,東北大學(xué)先進(jìn)軋制及熱處理研究團(tuán)隊(duì)在國家重點(diǎn)項(xiàng)目的支持下,開展了先進(jìn)加熱、淬火、回火新工藝與裝備技術(shù)研究,探索了多場耦合條件下?lián)Q熱機(jī)制,研制出高溫輥底式連續(xù)熱處理爐、多功能輥式淬火機(jī)、高精度中低溫回火爐等核心裝備,開發(fā)出系列高精度、高均勻性熱處理核心技術(shù),構(gòu)建了多級(jí)分布式控制系統(tǒng)與成套工藝數(shù)學(xué)模型,實(shí)現(xiàn)大型熱處理線自動(dòng)化穩(wěn)定生產(chǎn),成套技術(shù)裝備推廣至寶鋼、鞍鋼等26條熱處理線,建成國家級(jí)示范產(chǎn)線2條,國內(nèi)市場占有率穩(wěn)定在60%以上,成為我國大型板帶材熱處理線主流技術(shù)裝備,高品質(zhì)特種鋼板滿足了國家海工、能源、電力、工程機(jī)械、軍工等領(lǐng)域需求,批量出口30余個(gè)國家。
1 背景
我國中厚板年產(chǎn)量已接近9000萬噸,產(chǎn)能過剩和同質(zhì)化競爭問題嚴(yán)重。然而,部分高端高附加值中厚板產(chǎn)品仍依賴進(jìn)口,其中絕大多數(shù)是熱處理產(chǎn)品。熱軋鋼材熱處理按工藝分在線和離線兩種,盡管控軋控冷(TMCP)、即時(shí)溫控等在線熱處理技術(shù)已得到普遍應(yīng)用,但對(duì)于性能均勻性和強(qiáng)度等級(jí)要求較高的低溫壓力容器鋼板、橋梁鋼板、工程機(jī)械用鋼板、耐磨鋼板、高層建筑鋼板等仍需通過正火、調(diào)質(zhì)等手段來改善組織分布,利用強(qiáng)韌化機(jī)制提高整體力學(xué)性能和加工性能,實(shí)現(xiàn)成分減量化。
高端中厚板熱處理生產(chǎn)始終圍繞加熱、冷卻兩個(gè)核心工藝展開。加熱方面,熱處理爐爐溫控制精度直接影響鋼板板形及性能均勻性,一般要求偏差小于±5℃,而對(duì)于某些高端產(chǎn)品,如超高強(qiáng)工程機(jī)械用鋼、低合金耐磨鋼等,一般要求回火爐溫在300℃以下,且要求熱處理爐低溫控溫精度更高。目前國內(nèi)鋼鐵企業(yè)熱處理低溫回火在控溫精度方面仍無法滿足高品質(zhì)鋼材生產(chǎn)需要,研制與開發(fā)新型高精度熱處理爐對(duì)穩(wěn)定生產(chǎn)高品質(zhì)特殊鋼、升級(jí)熱處理裝備技術(shù)水平意義重大。
輥式淬火機(jī)是板帶材熱處理線的核心工藝裝備,常規(guī)的輥式淬火機(jī)(淬火厚度范圍為10-120mm)及其核心淬火工藝技術(shù)被德國、美國、日本少數(shù)公司長期壟斷。進(jìn)口設(shè)備采用壟斷捆綁供貨,價(jià)格高昂,供貨周期長,已成為我國鋼鐵企業(yè)實(shí)現(xiàn)產(chǎn)品結(jié)構(gòu)調(diào)整的巨大障礙。此外,進(jìn)口設(shè)備不具備高品質(zhì)薄規(guī)格板材的生產(chǎn)能力,目前此類熱處理產(chǎn)品僅由瑞典等國外一兩家企業(yè)批量供貨,價(jià)格昂貴,生產(chǎn)技術(shù)完全保密,阻礙了其使用性能的發(fā)揮,限制了我國高端裝備制造等領(lǐng)域的發(fā)展。
目前,厚度大于120mm的特厚鋼板主要采用傳統(tǒng)淬火池(槽)等設(shè)備生產(chǎn),通過攪拌池內(nèi)冷卻水加速鋼板表面換熱效率。由于對(duì)流換熱過程受淬火裝置容積限制,冷卻強(qiáng)度偏低,鋼板板面各處冷卻強(qiáng)度分布不均。隨著淬火裝備技術(shù)的發(fā)展,連續(xù)輥式淬火方式在中厚規(guī)格鋼板(4mm<鋼板厚度<120mm)淬火生產(chǎn)過程中應(yīng)用普遍,將其引入到特厚鋼板淬火生產(chǎn)中,結(jié)合特厚鋼板淬火生產(chǎn)工藝特點(diǎn),實(shí)現(xiàn)按工藝路徑淬火和厚向均勻冷卻將是一條可行之路。然而,目前在特厚鋼板淬火領(lǐng)域,專用連續(xù)輥式冷卻系統(tǒng)的應(yīng)用尚屬空白。
針對(duì)上述問題,2011鋼鐵共性協(xié)同創(chuàng)新中心設(shè)立了“極限規(guī)格板材離線熱處理工藝技術(shù)與裝備”研究方向。圍繞極限規(guī)格鋼板熱處理多場耦合協(xié)同控制、高強(qiáng)均勻淬火技術(shù)、先進(jìn)加熱-淬火-回火熱處理裝備和系列高品質(zhì)板材熱處理產(chǎn)品幾個(gè)方面開展攻關(guān),取得了如下成果。
2 主要研究內(nèi)容
2.1特種鋼板高溫輥底式熱處理爐
2.1.1研發(fā)出極限溫度1200℃的大型熱處理爐高效、高均勻脈沖加熱系統(tǒng),提出新型復(fù)合脈沖燃燒控制技術(shù)
為滿足鋼板橫向-縱向加熱均一、加熱工藝高精度制定及實(shí)現(xiàn)、高效節(jié)能等生產(chǎn)及研發(fā)需求,深入研究高溫?zé)崽幚頎t燒嘴特性及其布置對(duì)燃燒加熱均勻性和爐內(nèi)熱平衡的影響,通過建立基于FLUENT的明火固溶爐數(shù)值仿真平臺(tái),開發(fā)數(shù)值分配優(yōu)化技術(shù)。為獲得最優(yōu)的燒嘴分布方案,分析得出最佳的水平脈沖射流形成的旋流場,實(shí)驗(yàn)獲得脈沖射流速度、射流頻率、射流火焰長度等系列工藝參數(shù)對(duì)均勻加熱的影響機(jī)制,如圖1所示。開發(fā)了板材在爐內(nèi)熱處理全過程溫度歷程預(yù)測及評(píng)價(jià)技術(shù),為特種鋼板高均勻熱處理加熱奠定了重要技術(shù)基礎(chǔ)。
基于高精度均勻化脈沖加熱技術(shù),集成開發(fā)出基于水平脈沖射流的最優(yōu)分布的成套燒嘴系統(tǒng),實(shí)現(xiàn)板材加熱均勻化,使?fàn)t溫均勻性更高的同時(shí)提高換熱效率。開發(fā)出新型復(fù)合式燃燒控制技術(shù),建立了新型復(fù)合式脈沖燃燒控制策略,根據(jù)負(fù)荷需求量或變換燃燒(脈寬)時(shí)間,或變換燃燒停止(消隱)時(shí)間,進(jìn)而計(jì)算整個(gè)脈沖周期,實(shí)現(xiàn)全負(fù)荷范圍的高精度控制和高效、高均勻性換熱。研發(fā)的新型脈沖燃燒控制技術(shù)可以使得溫度控制精度達(dá)到±3℃以內(nèi),響應(yīng)速度更快,抗干擾能力更強(qiáng)。
2.1.2研制出新一代無結(jié)瘤、耐高溫、長壽命、低成本爐底輥,開發(fā)出特殊鋼板表面質(zhì)量控制技術(shù)
特種鋼板固溶處理時(shí),爐溫一般超過1100℃,輥底式熱處理爐的輥必須具備耐熱溫度高、高溫承載力強(qiáng)的性能。傳統(tǒng)輥底爐采用耐熱合金爐輥,這類爐輥生產(chǎn)中極易結(jié)瘤,結(jié)瘤物粘附在爐輥上不易脫落,造成鋼板產(chǎn)生凹坑、麻點(diǎn)、擦劃傷等缺陷,不僅破壞產(chǎn)品外觀形象,還帶來巨大的人工修磨工作量;此外,耐熱合金爐輥造價(jià)高,僅爐輥一項(xiàng)就可占整體輥底爐全部價(jià)格的20%-30%,直接增大了熱處理爐的投資。為解決該問題,項(xiàng)目完成單位通過對(duì)結(jié)瘤物形成機(jī)理以及成分構(gòu)成進(jìn)行分析,提出研制新一代高溫耐磨纖維爐輥以及開發(fā)板材高表面質(zhì)量控制技術(shù)。研發(fā)內(nèi)容涉及纖維輥強(qiáng)度及穩(wěn)定性設(shè)計(jì)、纖維輥硬度及耐磨性調(diào)優(yōu)、纖維輥冷卻技術(shù)、鋼板表面氧化皮抑制技術(shù)以及爐內(nèi)氣氛精確控制技術(shù)。
纖維輥強(qiáng)度及穩(wěn)定性設(shè)計(jì)。鋼板熱處理品種和規(guī)格多變,加之爐內(nèi)氣流擾動(dòng)、輥道速度實(shí)時(shí)大范圍調(diào)整等因素,對(duì)爐輥強(qiáng)度及運(yùn)行穩(wěn)定性提出了嚴(yán)峻考驗(yàn)。針對(duì)纖維輥生產(chǎn)時(shí)易產(chǎn)生的纖維片脫落、輥體鼓脹和輥身裂紋等問題,創(chuàng)新開發(fā)出環(huán)形鋼片“魚骨式”結(jié)構(gòu)、纖維片快速壓裝裝置和纖維輥快速換輥機(jī)構(gòu),顯著提升了輥身強(qiáng)度和耐用性,簡化了纖維輥壓裝和更換流程。
纖維輥硬度及耐磨性調(diào)優(yōu)。對(duì)比分析不同纖維片配方對(duì)纖維輥高溫狀態(tài)下硬度及耐磨性的影響,不斷優(yōu)化纖維片成分及配比,減少鋼板氧化皮壓入,提高爐輥使用壽命。通過實(shí)驗(yàn)室測試和生產(chǎn)測試結(jié)合,開發(fā)出平均壽命長達(dá)5萬噸/根的爐輥。開發(fā)的爐輥如圖2所示。
研制的新一代爐輥替代了傳統(tǒng)的耐熱合金爐輥,顯著提升了產(chǎn)品質(zhì)量,降低了熱處理爐裝備的投資及維護(hù)費(fèi)用。爐輥首次投資成本降低70%,成套設(shè)備投資成本可節(jié)約20%。同時(shí)這種爐輥絕熱性好,大大降低了熱負(fù)荷需求,節(jié)省了能源介質(zhì)消耗。
2.1.3研制出高溫輥底式熱處理爐成套裝備,建立了系統(tǒng)的特殊鋼板高溫?zé)崽幚砉に囍贫润w系
針對(duì)特種鋼板輥底式熱處理爐成套裝備集成開發(fā)技術(shù)難點(diǎn),基于高效、高精度脈沖加熱技術(shù)及系統(tǒng),開發(fā)與之匹配的燃?xì)馀c空氣系統(tǒng)裝置集成、密封保溫裝置集成、多傳動(dòng)變頻同步系統(tǒng)等成套裝備技術(shù),形成整套專利技術(shù)和專有技術(shù)訣竅。開發(fā)的燃燒介質(zhì)供給系統(tǒng)采用總路自保壓裝置與支路調(diào)壓裝置結(jié)合,通過熱值儀檢測熱值波動(dòng)調(diào)整支路燃?xì)饬髁浚瑫r(shí)設(shè)計(jì)裝置可實(shí)現(xiàn)根據(jù)負(fù)荷變化提前控制空氣管路的流量前饋調(diào)整,從而保證壓力恒定。針對(duì)混合煤氣熱值波動(dòng)嚴(yán)重等問題,開發(fā)了自適應(yīng)空燃比調(diào)整手段,實(shí)現(xiàn)燒嘴穩(wěn)定燃燒時(shí)最佳空燃比自動(dòng)精確調(diào)節(jié),確保了不銹鋼板材加熱質(zhì)量的穩(wěn)定性。
高溫?zé)崽幚頎t的爐體密封性是爐子保溫設(shè)計(jì)中非常重要的環(huán)節(jié),直接影響爐內(nèi)燃料消耗及鋼板的熱處理質(zhì)量。項(xiàng)目研發(fā)了高溫固溶爐的爐殼分體制備技術(shù)、爐殼防膨脹松動(dòng)技術(shù)以及爐門雙室隔離技術(shù)。1200℃時(shí)爐壁溫升小于40℃,為保證爐內(nèi)溫度均勻性、提高熱處理爐效率提供了很好的保證。為保證輥底式高溫?zé)崽幚淼拿芊庑浴⒈匦裕档鸵驙t內(nèi)壓力高造成的熱量損失,研發(fā)了微正壓控制技術(shù)。開發(fā)出以爐膛壓力控制為內(nèi)環(huán)、排煙引射控制為外環(huán)的雙閉環(huán)排煙自動(dòng)壓力控制技術(shù),解決了排煙手動(dòng)控制時(shí)爐壓波動(dòng)大、煙氣溫度過高等問題,顯著降低煙氣波動(dòng)對(duì)爐體密封性影響和燒嘴燃燒效率的影響。
基于上述關(guān)鍵裝置集成開發(fā)的高溫輥底式熱處理爐由爐體、加熱系統(tǒng)、燃?xì)庀到y(tǒng)、助燃空氣系統(tǒng)、排煙系統(tǒng)、輥道系統(tǒng)、冷卻水系統(tǒng)等部分組成,采用明火加熱方式。燃?xì)馐褂酶呓够旌厦簹猓瑹鞛樽陨眍A(yù)熱式低NOx燒嘴,排煙方式為單燒嘴100%引射排煙+輔助旁通排煙。爐內(nèi)輥道單獨(dú)傳動(dòng),可實(shí)現(xiàn)工藝路徑靈活控制,如圖3所示。
研制裝備通過集成均勻化加熱控制方法、工藝智能化控制系統(tǒng),形成了大型高溫輥底式熱處理爐裝備設(shè)計(jì)、工藝調(diào)試、模型開發(fā)等設(shè)計(jì)制造規(guī)范。研發(fā)裝備解決了傳統(tǒng)高溫輥底爐的薄規(guī)格板加熱易變形問題,滿足了特殊鋼板材多樣化熱處理工藝的需求。
2.2極限規(guī)格鋼板輥式淬火裝備技術(shù)
極薄、超寬、特厚等極限規(guī)格熱處理鋼板,是熱軋鋼板中的高附加值產(chǎn)品,廣泛應(yīng)用于機(jī)械化工、水電核電、海洋工程、國防軍工等領(lǐng)域。此類鋼板單重大、寬厚比大,其高強(qiáng)度、高均勻性淬火是行業(yè)公認(rèn)的技術(shù)難題。通過理論及實(shí)驗(yàn)研究,結(jié)合工業(yè)化實(shí)踐,創(chuàng)新開發(fā)出極薄、超寬、特厚鋼板高平直度、高均勻性淬火工藝技術(shù)及裝備,形成了系列創(chuàng)新成果。
中厚鋼板高強(qiáng)度均勻化淬火的關(guān)鍵在于開發(fā)冷卻能力大且冷卻介質(zhì)均勻分布的噴嘴結(jié)構(gòu)。但由于流速較高(25m/s),湍流流動(dòng)形態(tài)復(fù)雜,大型超寬噴嘴(最寬達(dá)5m)研發(fā)十分困難。基于有限元模擬,系統(tǒng)分析了大型噴嘴進(jìn)水方式、均流裝置、噴嘴形狀等結(jié)構(gòu)參數(shù)對(duì)介質(zhì)流量分布的影響,開發(fā)出具有自水冷和多重阻尼的整體超寬狹縫式噴嘴、內(nèi)嵌式多排傾斜高密圓孔噴嘴、內(nèi)嵌式多排弧面多角度傾斜高密圓孔噴嘴等系列高性能射流噴嘴,滿足了1.5-300℃/s冷速范圍內(nèi)高均勻性淬火需求。
開發(fā)出柔性化冷卻系統(tǒng),具備冷卻區(qū)長度方向流量分區(qū)控制、噴嘴寬向多腔體獨(dú)立供水控制、噴嘴寬向水凸度控制、鋼板頭尾流量特殊控制等功能,實(shí)現(xiàn)整板長度方向、寬度方向的冷速和冷卻均勻性可控,不僅能夠?qū)崿F(xiàn)復(fù)雜的熱處理工藝過程,還實(shí)現(xiàn)了節(jié)水、節(jié)能,滿足了不同規(guī)格、鋼種熱處理對(duì)冷卻制度和冷速的需求,實(shí)現(xiàn)了按工藝路徑冷卻。
研制成功系列多功能中厚規(guī)格鋼板輥式淬火成套裝備及配套水處理系統(tǒng),適用于3-300mm厚、最寬5m、最長26m的碳素鋼淬火及NAC、不銹鋼固溶、高溫合金熱處理等工藝需求,成為我國中厚鋼板熱處理線上的主流淬火裝備。
系統(tǒng)研究了鋼板淬火溫降過程中組織演變規(guī)律,以及熱應(yīng)力和組織應(yīng)力相互作用對(duì)淬火殘余應(yīng)力和畸變的影響規(guī)律,開發(fā)出鋼板寬向水凸度控制和縱向自由冷卻單元控制的流量分區(qū)控制技術(shù)、冷速動(dòng)態(tài)高精度調(diào)控及冷卻參數(shù)快速響應(yīng)技術(shù)、鋼板上下表面非對(duì)稱冷卻技術(shù)、應(yīng)力演變及殘余應(yīng)力控制技術(shù)、全流域殘水控制技術(shù)等核心技術(shù),在國內(nèi)首次實(shí)現(xiàn)3-10mm極限薄規(guī)格鋼板連續(xù)穩(wěn)定生產(chǎn),如圖4所示,解決了傳統(tǒng)薄鋼板淬火后產(chǎn)生的叩頭叩尾、橫/縱向瓢曲、中浪、邊浪等板形問題。
針對(duì)傳統(tǒng)輥式淬火機(jī)高壓段瞬時(shí)冷卻能力不強(qiáng)、常壓段持續(xù)冷卻能力不強(qiáng)等問題,系統(tǒng)開發(fā)出高壓高強(qiáng)度快冷技術(shù)、冷速大范圍調(diào)節(jié)技術(shù)、冷卻路徑控制技術(shù)、低壁面溫度持續(xù)冷卻技術(shù)等淬火技術(shù)。鋼板在高壓區(qū)大冷卻強(qiáng)度下大幅提升厚向溫度梯度;在常壓區(qū)持續(xù)強(qiáng)制表面換熱,大幅提升心部冷速和厚向冷卻均勻性。與傳統(tǒng)淬火相比,厚規(guī)格鋼板心部冷速提高1倍以上,目前300mm級(jí)大斷面超厚鋼板連續(xù)輥式淬火裝備技術(shù)已成功在河鋼舞鋼投產(chǎn),高品質(zhì)厚規(guī)格鋼板生產(chǎn)提供了必要條件,如圖5所示。
2.3高精度中低溫回火爐技術(shù)和裝備
極薄高強(qiáng)鋼板強(qiáng)度和硬度高、板形要求高,我國依賴JFE、SSAB等公司進(jìn)口。為獲得較高強(qiáng)度,此類鋼板需進(jìn)行回火處理。但國內(nèi)輥底式低溫回火爐控溫精度僅為±15℃,無法滿足高強(qiáng)薄板±5℃以內(nèi)的溫度均勻性要求。
高速熱風(fēng)循環(huán)加熱方式是有效的解決途徑。回火爐采用強(qiáng)制對(duì)流加熱技術(shù),加熱過程中高速的爐氣直接沖擊金屬進(jìn)行加熱,輔以特殊的爐型結(jié)構(gòu)將與鋼板熱交換過的爐氣回收加熱,形成爐內(nèi)氣流的高速循環(huán)。
針對(duì)強(qiáng)制對(duì)流加熱的技術(shù)特點(diǎn),研究了不同溫度下爐內(nèi)熱交換過程和強(qiáng)制對(duì)流加熱條件下鋼板的加熱規(guī)律,利用有限元模擬仿真爐氣導(dǎo)流、均流系統(tǒng),分析裝備結(jié)構(gòu)參數(shù)、氣流壓力和流量等對(duì)均流的影響,優(yōu)化了爐內(nèi)熱空氣導(dǎo)流、均流裝備結(jié)構(gòu),新型的集氣室結(jié)構(gòu)設(shè)計(jì)使氣流流動(dòng)過程中的能量損耗小、各噴箱處的氣流壓力均勻。建立了在線鋼板溫度實(shí)時(shí)跟蹤和基于灰色異步粒子群加熱優(yōu)化的工藝數(shù)學(xué)模型及數(shù)據(jù)庫。通過對(duì)爐內(nèi)熱交換的研究,確定了鋼板換熱的特性,建立了鋼板外部綜合傳熱熱流計(jì)算模型。利用工業(yè)試驗(yàn),確定了爐膛總括熱吸收率計(jì)算模型。為使?fàn)t溫接近真實(shí),建立考慮爐段間溫度耦合的爐膛溫度計(jì)算模型。在此基礎(chǔ)上,建立了在線加熱數(shù)學(xué)模型,實(shí)現(xiàn)了出爐測量溫度與計(jì)算溫度的相對(duì)誤差在1%以內(nèi)。
針對(duì)鋼板加熱優(yōu)化目標(biāo)的多維性,提出灰色關(guān)聯(lián)分析法GRA與異步粒子群算法APSO組合,建立了高溫固溶爐的灰色異步粒子群加熱優(yōu)化策略。所建策略繼承了GRA高維多目標(biāo)決策和APSO并發(fā)求解的能力,為熱處理爐加熱優(yōu)化提供了新的求解方法。結(jié)合高精度回火爐設(shè)備特點(diǎn),建立了爐溫設(shè)定和板速設(shè)定動(dòng)態(tài)優(yōu)化補(bǔ)償策略,實(shí)現(xiàn)了加熱規(guī)程的優(yōu)化,有效保證了鋼板出爐溫度命中率。
最終形成了具有特色的高精度回火爐裝備:高速熱風(fēng)強(qiáng)制對(duì)流加熱,低溫時(shí)換熱效率高,加熱均勻;加熱溫度范圍100-600℃,100-300℃加熱均勻性好,升溫速度快;爐溫控制精度±3℃之內(nèi),爐溫均勻性±3℃之內(nèi);加熱器可采用燃?xì)鉄旎螂娂訜崞鳎訜岷箐摪灞砻尜|(zhì)量好,滿足高性能鋼材高品質(zhì)、高效率、低能耗、低成本生產(chǎn)的需要,如圖6所示。
2.4調(diào)質(zhì)鋼板組織調(diào)控與高端產(chǎn)品開發(fā)
針對(duì)熱軋鋼材形變和相變過程組織調(diào)控方法獨(dú)立、手段單一、強(qiáng)度和韌性難以同時(shí)提高的行業(yè)共性問題,率先提出晶粒細(xì)化、析出粒子納米化、相變?nèi)嵝曰{(diào)控原理,開發(fā)成功“溫控-形變”耦合高滲透性軋制技術(shù),發(fā)展了細(xì)晶、析出和相變的綜合強(qiáng)韌化理論,創(chuàng)建了連鑄-軋制-熱處理全流程組織控制方法、析出物控制方法、力學(xué)性能控制方法和組織性能預(yù)測方法。成功開發(fā)出系列高等級(jí)減量化鋼鐵材料熱軋及熱處理產(chǎn)品,包括:
1)在常規(guī)C-Mn鋼中加入少量Cr、B元素,建立低成本成分體系,開發(fā)出100mm厚以下高韌性型、抗高溫磨損型、納米析出型等系列低合金耐磨鋼板NM360-NM600,其典型組織為回火馬氏體+殘余奧氏體+納米碳化物析出,耐磨性能是同級(jí)別瑞典SSAB的1.3倍、德國Dil l ingen的1.7倍,性能均勻性是日本JFE的2.77倍,滿足了嚴(yán)寒、高溫等特殊工況條件下的使用需求,應(yīng)用于大型挖掘機(jī)、盾構(gòu)機(jī)和掘進(jìn)機(jī)等裝備關(guān)鍵部件制造,填補(bǔ)了國內(nèi)空白,如圖7所示;
2)開發(fā)出系列100mm厚以下高級(jí)別(屈服強(qiáng)度最高達(dá)1300MPa)結(jié)構(gòu)用鋼,Q960級(jí)典型熱處理組織為回火索氏體+大量納米碳化物組成的多相組織,Q1300級(jí)典型組織為回火馬氏體+殘余奧氏體+大量納米碳化物組成的多相組織,成品力學(xué)、焊接、成型性能達(dá)到或優(yōu)于瑞典SSAB同級(jí)別鋼板水平,滿足了大噸位起重機(jī)、混凝土泵車等高端工程機(jī)械設(shè)備制造的需求,打破了SSAB長達(dá)20余年的壟斷局面,并成功的出口到歐美等發(fā)達(dá)國家和地區(qū),如圖8所示。
3)開發(fā)出系列高強(qiáng)度海工特厚鋼板和大線能量焊接鋼板,突破國產(chǎn)化生產(chǎn)、應(yīng)用瓶頸,成功應(yīng)用于全球最深半潛鉆井平臺(tái)、南海荔灣油氣田、國產(chǎn)二代破冰船、國產(chǎn)大型水面水下艦艇等重點(diǎn)工程關(guān)鍵裝備上。
3 結(jié)語
基于中心產(chǎn)學(xué)研開發(fā)平臺(tái),東北大學(xué)先進(jìn)軋制與熱處理團(tuán)隊(duì)研發(fā)成功系列鋼板離線熱處理成套技術(shù)與裝備,開發(fā)出海工、能源、工程機(jī)械等系列高等級(jí)鋼板產(chǎn)品,填補(bǔ)了國內(nèi)空白,滿足了重點(diǎn)領(lǐng)域?qū)Ω叨颂胤N鋼板的需求,提升了國家自主保障能力。
免責(zé)聲明:本網(wǎng)站所轉(zhuǎn)載的文字、圖片與視頻資料版權(quán)歸原創(chuàng)作者所有,如果涉及侵權(quán),請(qǐng)第一時(shí)間聯(lián)系本網(wǎng)刪除。
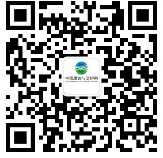
官方微信
《中國腐蝕與防護(hù)網(wǎng)電子期刊》征訂啟事
- 投稿聯(lián)系:編輯部
- 電話:010-62313558-806
- 郵箱:fsfhzy666@163.com
- 中國腐蝕與防護(hù)網(wǎng)官方QQ群:140808414