一、前言
油氣管道在設計、施工和運營階段都有可能遭受來自外部環境干擾和內部操作不規范而造成的管道本體缺陷,從而影響管道的安全運營。同時,隨著管道業務的不斷深入發展,一系列新的問題使管道的完整性管理也面臨著挑戰[1],研究應對這些問題的技術方法和策略是解決管道本質安全及管道業務發展瓶頸的關鍵 [2]。對于投產運營以后的油氣管道來說,絕大部分都采用埋地敷設的方式,屬于隱蔽工程,管道本體的劃傷、焊接缺陷、材料缺陷等在運營期很難通過地面檢查來識別,而這些缺陷對油氣管道安全運營來說都是潛在的隱患,如 2009 年 12 月 30 日,蘭鄭長成品油管道渭南支線因第三方施工破壞致使管道在試運投產過程中發生柴油泄漏事故,泄漏的柴油由赤水流入渭河,經渭河流入黃河,對黃河造成了嚴重的油污染;青島“11.22”爆燃事故更是暴露出管道本體缺陷給生產運行和社會帶來的危害。
近年來隨著《管道保護法》、《特種 設 備 安 全 法》 等 國 家 法 律 法 規,《油氣輸送管道完整性管理規范》(GB32167-2015)、《壓力管道定期檢驗規則 - 長輸油氣管》(TSG D7003-2010)等相關國家、行業標準規范相繼出臺,以及逐步成熟和推廣應用的管道完整性管理,在控制和監控影響管道完整性的各類威脅中取得了顯著的效果。同時,隨著內檢測技術的發展,識別管道本體缺陷已經成為可能 ,如采用機械原理的幾何檢測器可以識別管道幾何變形,包括凹坑、橢圓變形、屈曲等 ;采用漏磁原理的漏磁檢測器可以識別管道金屬損失,包括劃傷、腐蝕、部分制造缺陷等 ;采用超聲原理的裂紋檢測器可以識別管道存在的裂紋和類裂紋缺陷,包括 HIC、SCC 等;還有很多種特定的缺陷可以通過特殊的檢測工具來識別,如針對輸氣管道環焊縫裂紋開發的電磁超聲檢測器(EMAT)等。這些內檢測技術的發展,進一步提升了管道完整性管理體系發揮的作用,有效保障了油氣管道的本體安全,從而為“事故可防,風險可控”提供了技術保障。
本文將以內檢測技術為核心,基于風險控制理論 和“樹生”事故致因理論的方法 ,考慮到當前管道大數據的現狀 ,探討一種基于內檢測技術的油氣管道安全保障體系,實現主動的預防管理模式(見圖 1)。
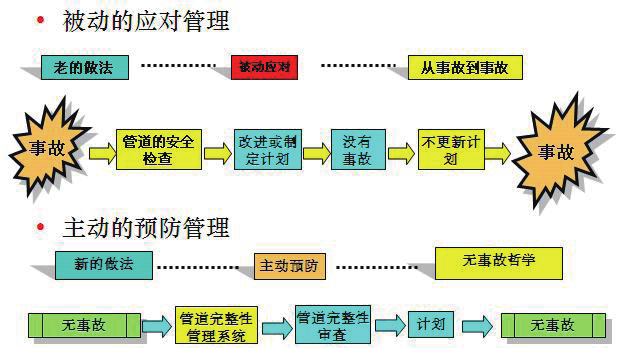
圖1 被動的應對管理與主動的預防管理示意圖
二、國內外管道內檢測現狀
20 世紀 70 年代由于管道檢測技術水平較低,無法準確確定管道的運行狀況和腐蝕情況,管道的維護維修都采用被動的方式,為了保障生產的連續性,只好建設復線(如慶鐵老線和新線,新大老線和復線等)或采取限壓措施來確保管道安全生產,有時甚至提前結束服役年限報廢。這樣,一方面需要昂貴的費用作為代價,另一方面降低管道的輸量,造成管輸能力的浪費。而且部分管道即使采取了降壓措施,因不能了解管道本體的狀況,仍然不能確保管道安全。
隨著材料、電子信息及計算機技術的發展,檢測器探頭小型化、縮小探頭間距、提高處理器的采樣速率以及超大容量存儲器的工業應用等得以實現,使得對油氣管道無損探傷的精度和置信度也越來越高。同時,在 1999 年華盛頓州 Bellingham 汽油管道爆炸事故、2000年新墨西哥州 Carlsbad 天然氣管道爆炸事故等眾多油氣管道事故的推動下,各個國家完善了管道完整性管理相關的立法和標準規范要求,這些都促進了基于內檢測的完整性管理技術和安全保障技術的全面、快速發展,利用超聲、漏磁、機械振動、陀螺儀、渦流等原理的管道內檢測技術也從無到有,從低精度到高精度,從理論試驗研究走向了工業應用,并建立了眾多內檢測服務公司。
同時,當前基于光學原理的無損檢測技術在對管道內表面腐蝕、斑點、裂紋等進行快速定位與測量過程中,具有較高的檢測精度且易于實現自動化。相比其他檢測方法,該方法在實際應用當中有很大的優勢,其中在管道內檢測中采用較為普遍的光學檢測技術包括 CCTV 攝像技術、工業內窺鏡檢測技術和激光反射測量技術。
目前,比較有影響力的國際內檢測服務公司主要有德國的 Rosen、美國GE PII、BakerHuges、T.D.Williamson、荷蘭 PipeSurvey 以及國內的中油管道檢測技術有限責任公司等,還有一些新興的檢測公司,如英國的天祥集團、NDTGlobal、Penspen 等,這些公司在不同方面有著各自的獨特優勢,如 Rosen 在新技術研發方便具有獨特的優勢,其可以包括設備零件在內的整裝設備生產,對于新技術的應用反應速度快,能夠及時完成設備的更新換代;GE PII 則形成了比較成熟的技術體系和服務系統,在現場服務、數據分析等方面的優勢比較顯著,且逐步形成了全球內檢測服務網絡。在全球內檢測市場份額方面,德國的 Rosen 和美國 GE PII 這兩家檢測服務公司平分了超過 60% 的內檢測市場,其次為 BakerHuges、T.D.Williamson 等近 100家內檢測公司占據剩余的 40% 的內檢測市場。
三、基于數據對齊的風險管理
隨 著 管 道 發 展 到 大 數 據 時 代、信息技術的發展和數據管理系統的完善,在實現管道本體屬性數據、生命周期運營管理數據、以及周邊環境數據對齊并納入數據庫的條件下,形成了管道大數據。所謂管道大數據就是:
以管道內檢測數據為基線,實現將內檢測信息、外檢測數據、設計施工資料數據、歷史運維數據、管道環境數據和日常管理數據等的校準、對齊整合,使各類數據均可對應各環焊縫信息,形成統一的數據庫或數據表 。從管道大數據的定義可知,管道大數據的核心在于整合管道相關的各類基礎數據,其價值在于從大數據中挖掘潛在的安全隱患和提供制定維護維修決策的依據,而實現管道大數據價值的技術基礎在于數據對齊。
對于分散、雜亂無章的數據,再多也不能稱之為大數據,因為隨著數據量的增大,如果不能實現這些數據的價值,那么不僅僅會增加數據管理和維護的成本,而且還會掩蓋有價值的數據信息,從而成為管理的負擔。
管道內檢測是對管道的一次全面的體檢,也是管道大數據得以實現其價值,完成數據對齊的關鍵。管道內檢測除了識別管道本體缺陷外,還能識別管道的各類特征,如三通、閥門、環焊縫、套管等。其中,根據內檢測報告的焊縫編號與建設施工期的焊接記錄中的焊口編號對齊,可以實現內檢測數據與建設施工期的數據整合;通過內檢測地面定標點和識別的各類典型特征,可以實現內檢測數據與外檢測數據、日常管理數據、以及其他歷史資料數據(如換管、修復等)的對齊。從而實現以內檢測數據為核心,將施工焊接記錄、管材信息、外檢測、地面特征等對齊起來,從而發揮兩個方面的作用,一是將大數據進行了有效的整合,更加有效地實現大數據的價值;另一方面是通過數據對齊可以識別一些潛在的危險,如施工記錄中缺失的焊口記錄、短管的記錄、連頭口的記錄等。
通過數據對齊技術,以內檢測環焊縫號為基準,識別建設期和運營期不合規的特征(如某些管道存在的斜接彎頭、預載的打孔盜油閥門、凹坑、劃傷等)及其位置,建立風險管理臺賬,從風險專家評估風險轉變為數據分析人員分析風險,關注數據相關性,識別潛在的風險 。這種模式可以減少人為的主觀性,基于風險的理念合理配置資源,同時也有利于保障管理的連續性,減小政策變化或變更管理給管道運營安全帶來的影響。通過這種模式,實現管道大數據的管理和從大數據中挖掘潛在的風險也是構建管道安全保障體系的重要工作。
四、內檢測在油氣管道生命周期內的作用
管道內檢測在管道安全生產全生命周期內都發揮著重要的作用,其中包括:
1.新建管道質量控制
由于長輸油氣管道基本都是采用埋地的方式敷設,建設施工完成后就成為隱蔽工程,以前對于管道驗收都是驗收相關的資料、地面標識、路權等資料信息,缺乏對于管道本體完整性情況的驗收,質量控制非常困難,以致在新建管道投產初期往往因為面臨各類完整性威脅導致事故頻發,呈現“浴盆曲線”的初期事故多發期。
通過打壓試驗,發現了很多缺陷,但是打壓對于處于臨界狀態的缺陷暴露不出來,同時會促使一些處于臨界狀態下的缺陷的擴展(見圖 2),因此為了更好地控制管道建設施工質量,管道內檢測是一種非常有效的質量控制手段,在新建管道投產初期就應當開展基線檢測,對于基線檢測發現的缺陷,分析其原因,并作為新建管道質量控制的一部分 。
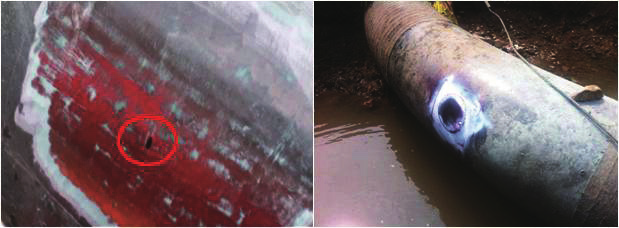
圖2 某新投產管道內檢測發現的針孔缺陷已經開始滲油(左),采用補丁修復(右)
2.運行期的安全保障
通過周期性的管道內檢測,可以在管道本體缺陷導致管道失效前,識別該缺陷尤其在管道內腐蝕比較集中的管道上,這種方式可以準確預測腐蝕速率,從而實施精準的維護維修策略 [19],避免泄漏事故的發生。同時,通過這種方式還可以延長管道的壽命 [20],這也是為什么管道運營商和政府監管部門非常重視管道內檢測的原因 [1]。近幾年針對老管道開展的內檢測工作,及時發現了管道本體的缺陷,進行針對性的修復,避免了大量泄漏事故(見圖 3),如馬惠線管道內檢測報告 70% 以上的缺陷上百處,10% 以上的缺陷幾萬處,部分70% 以上的缺陷,在修復過程中剝開防腐層后,發現針孔微滲漏,這些缺陷的及時識別與治理,有效確保了管道的安全運營。

圖3 歷年基于內檢測結果進行的管道修復中發現的典型管道腐蝕情況
由于打孔盜油形式呈現多樣化,且技術越來越成熟,反偵察能力也急速的提升,往往通過地面巡護、監管等很難100% 防控住打孔盜油,尤其對于一些預埋的盜油閥,采用地道、滴取等方式偷油,現有的防護手段很難排查,管道內檢測也成為解決這種難題的有效方法之一,如山東地區某原油管道內檢測及時識別了一些極其隱蔽(見圖 4)或者打完孔后未曾盜油的閥門 20 余處。
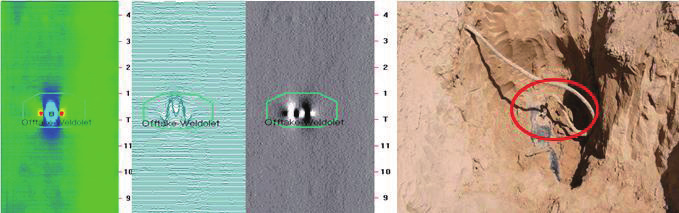
圖4 打孔盜油漏磁信號(左)和開挖的打孔盜油閥門(右)
3.管道判廢的依據
慶鐵新線和老線通過管道內檢測發現管道本體存在大量的螺旋焊縫和環焊縫缺陷,在慶鐵三線和四線投產前,根據工程適用性評價結果,開展了大量的修復工作,有效降低了泄漏事故率。
同時,基于內檢測結果,綜合考慮管道物理壽命和經濟壽命 ,為慶鐵新線和老線的廢棄、慶鐵三線和四線的規劃建設提供了依據,根據類比也為不可內檢測管道(見圖 5),如任京線,也提供了判廢的依據。
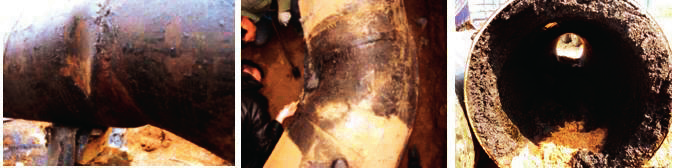
圖5 因屈曲、彎頭曲率半徑太小和結蠟太厚等原因不具備內檢測條件示意圖
五、安全保障體系的構建
當前,保障油氣管道的安全技術較多,如泄漏監測技術、安全預警技術、視頻監控技術、應變監測技術、高后果區識別技術等,分別從降低失效風險、控制失效后果等多個方面著手構建了相應的安全保障技術體系。盡管這些技術在一定程度上對于保障管道安全運營發揮了積極的作用,但是基本都處于事中和事后處置或維護的階段,尚未提升到預知維護和風險預控的階段。管道內檢測技術是一種識別管道本體缺陷為主,兼可監測管道狀態(如中心線檢測(IMU)可監測管道的應力變化情況)的技術,可以有效實現油氣管道預知維護和風險預控。
綜合上述內容,油氣管道安全保障體系就是以管道內檢測為中心,以內檢測報告的焊縫編號和坐標信息為基準,將所有相關的基礎數據實現數據對齊,基于這些數據的統計分析來指導預知性的維護維修、應急管理和風險管理,從而保障油氣管道的安全運營。該體系的構架如圖 6 所示。
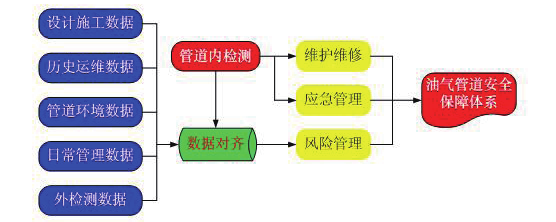
圖6 基于內檢測的油氣管道安全保障體系示意圖
其中,基于內檢測構建的安全保障體系主要有以下幾個方面的優點:
1.提高管理者的認知,梳理管理的重點
基于內檢測的油氣管道安全保障體系可以讓管理者明白管道存在什么問題、哪些區域不能發生泄漏、如何預防泄漏的發生、發生泄漏后可能造成多大的影響、以及發生泄漏后如何應對等。其中,安全保障體系的關鍵在于解決如何維護維修和應急,投入多少、投入什么、以及投在什么地方能發揮有限資源的最大價值方面的問題。
基于內檢測的油氣管道安全保障體系雖然基本實現預知的維護維修 ,但由于認知、技術發展等方面的局限性,不等于不需要應急,而是提高應急的針對性和降低應急的成本。
2.實現應急保障目標化,優化應急物資儲備
通過內檢測可以清晰了解管道本體的狀況,預測管道發生泄漏的可能性有多大、發生泄漏后的泄漏量有多大、發生泄漏后的影響范圍有多大、需要采取什么樣的應急技術(如焊接套筒、換管或者封堵)等,從而可以有效地識別在應急過程中可能遇到的風險,制定針對性的應急策略,如針對腐蝕缺陷,在應急方面考慮滲漏、小泄漏的維搶修措施,應急物資儲備方面只需要考慮管道卡具、套筒等的維搶修物資;針對焊縫缺陷,在應急方面就需要考慮破裂的維搶修措施,應急物資儲備方面也需要考慮不停輸封堵、換管等維搶修措施和儲備管子、封堵頭等維搶修物資。
同時,結合數據對齊的成果,還可以幫助管理者識別應急的重點部位,對高后果區管段中存在的缺陷修復優先,并在修復之前作為應急的重點監控對象。
3.促進技術發展,保障安全運營
根據數據對齊識別的建設期預留的潛在風險和運營期內檢測識別的管道本體缺陷,可以預測近期和遠期管道可能發生失效的類型和趨勢,并預測可能發生失效的區域。對于這些預測的失效類型可以開展針對性的技術研究,從而完善安全保障的技術體系,如當前需求的高強鋼在役焊接、非開孔封堵的換管技術、凹坑缺陷的修復技術等方面的研究。
同時,內檢測技術也存在一定的局限性,如輸油氣管道焊縫裂紋、針孔腐蝕等缺陷檢測技術還有待進一步的研究。
六、總結與展望
在油氣管道運行全壽命周期過程中,管道內檢測能有效識別管道在運行過程中影響管道本體運行安全的威脅 [21],從而針對這些威脅,采取有針對性的運行管理和維護措施,將有限的資源投入到最需要關注的管段上,明晰管理的重點方向,達到預防式管理的目的,確保管道安全運行,降低運行與維護成本。同時,基于當前內檢測技術存在的局限性,如焊縫缺陷、裂紋、針孔類缺陷等在檢出率和識別率等檢測指標方面還不能達到預定的目標,因此,在構建油氣管道安全保障體系時還需要著手開展電磁超聲內檢測技術、電磁渦流內檢測技術、超聲裂紋內檢測技術等方面的研究工作,提高對于裂紋、焊接缺陷、針孔缺陷等識別能力,并完善數據對齊技術,提高大數據的應用價值,使其能夠更好地揭示風險。
作者簡介
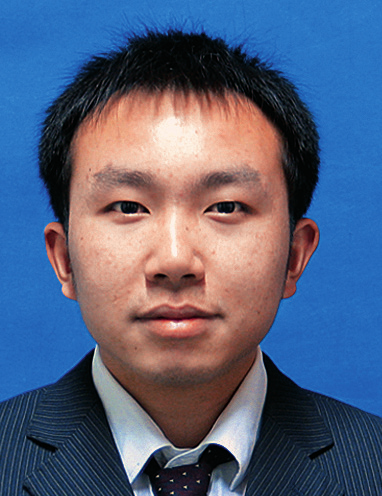
戴聯雙,1983 年,高級工程師,現在中國石油管道公司從事管道完整性管理、管道風險評價及管道內檢測等相關工作。
免責聲明:本網站所轉載的文字、圖片與視頻資料版權歸原創作者所有,如果涉及侵權,請第一時間聯系本網刪除。
相關文章
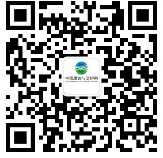
官方微信
《腐蝕與防護網電子期刊》征訂啟事
- 投稿聯系:編輯部
- 電話:010-62316606-806
- 郵箱:fsfhzy666@163.com
- 腐蝕與防護網官方QQ群:140808414
點擊排行
PPT新聞
“海洋金屬”——鈦合金在艦船的
點擊數:8135
腐蝕與“海上絲綢之路”
點擊數:6475