疲勞是材料(金屬)承受循環(huán)應(yīng)力或應(yīng)變作用時,結(jié)構(gòu)性能下降,并最終導致破壞的現(xiàn)象。疲勞失效是最常見的失效形式之一。文獻中提供的數(shù)據(jù)顯示,各種機械中,疲勞失效的零件占失效零件的60%~70%。疲勞斷裂失效原則上屬于低應(yīng)力脆斷失效,疲勞中難以觀察到明顯的塑性變形,因為這是以局部塑性變形為主,且主要發(fā)生在結(jié)構(gòu)的固有缺陷上。雖然頻率對疲勞失效有一定影響,但多數(shù)情況下疲勞失效主要與循環(huán)次數(shù)有關(guān)。
01 按引起疲勞失效的應(yīng)力特點可以分為: 由機械應(yīng)力引起的機械疲勞和熱應(yīng)力(交變熱應(yīng)力)引起的熱疲勞等 02 從循環(huán)周次可分為: 高周、低周、超高周疲勞 03 根據(jù)載荷性質(zhì)可分為: 拉-壓疲勞、扭轉(zhuǎn)疲勞以及彎曲疲勞等 04 根據(jù)工件的工作環(huán)境可分為: 腐蝕疲勞、低溫疲勞、高溫疲勞等 01 沖擊疲勞 是指重復沖擊載荷所引起的疲勞。當沖擊次數(shù)N小于500~1000次即破壞時,零件的斷裂形式與一次沖擊相同;當沖擊次數(shù)大于105次時的破壞,零件斷裂屬于疲勞斷裂,并具有典型的疲勞斷口特征。在設(shè)計計算中,當沖擊次數(shù)大于100次時,用類似于疲勞的方法計算強度。 02 接觸疲勞 零件在循環(huán)接觸應(yīng)力作用下產(chǎn)生局部永久性累計損傷,經(jīng)過一定循環(huán)次數(shù)后,接觸表面發(fā)生麻點、淺層或深層剝落的過程,稱為接觸疲勞。接觸疲勞是齒輪、滾動軸承和凸輪軸的典型失效形式。 03 熱疲勞 由于溫度循環(huán)產(chǎn)生循環(huán)熱應(yīng)力所導致的材料或零件的疲勞稱為熱疲勞。溫度循環(huán)變化導致材料體積循環(huán)變化,當材料的自由膨脹或收縮受到約束時,產(chǎn)生循環(huán)熱應(yīng)力或循環(huán)熱應(yīng)變。 零件的熱脹冷縮受到固持零件的外加約束而產(chǎn)生熱應(yīng)力; 雖然沒有外加約束,但兩件各部分的溫度不一致,存在著溫度梯度,導致各部分熱脹冷縮不一致而產(chǎn)生熱應(yīng)力。 溫度交變作用,除了產(chǎn)生熱應(yīng)力外,還會導致材料內(nèi)部組織變化,使強度和塑性降低。熱疲勞條件下的溫度分布不是均勻的,在溫度梯度大的地方,塑性變形嚴重,熱應(yīng)變集中較大;當熱應(yīng)變超過彈性極限時,熱應(yīng)力與熱應(yīng)變就不呈線性關(guān)系,此時求解熱應(yīng)力就要按彈塑性關(guān)系處理。熱疲勞裂紋從表面開始向內(nèi)部擴展,方向與表面垂直。 熱應(yīng)力的大小與熱脹系數(shù)成正比,熱脹系數(shù)越大,熱應(yīng)力越大。所以在選材時要考慮材料的匹配,即不同材料熱膨脹系數(shù)的差別不能太大。在相同的熱應(yīng)變條件下,材料的彈性模量越大,熱應(yīng)力就越大;溫度循環(huán)變化越大,即上下限溫差越大,則熱應(yīng)力就越大;材料的熱導率越低,則快速加速或冷卻過程中,溫度梯度越陡,熱應(yīng)力也越大。 04 腐蝕疲勞 腐蝕介質(zhì)和循環(huán)應(yīng)力(應(yīng)變)的復合作用所導致的疲勞稱為腐蝕疲勞。腐蝕介質(zhì)與靜應(yīng)力共同作用產(chǎn)生的腐蝕破壞稱為應(yīng)力腐蝕。兩者的區(qū)別在于,應(yīng)力腐蝕只有在特定的腐蝕環(huán)境中才發(fā)生,而腐蝕疲勞在任何腐蝕環(huán)境及循環(huán)應(yīng)力復合作用下,都會發(fā)生腐蝕疲勞斷裂。應(yīng)力腐蝕開裂,有一個臨界應(yīng)力強度因子KISCC,當應(yīng)力強度因子KI≤KISCC,就不會發(fā)生應(yīng)力腐蝕開裂;而腐蝕疲勞不存在臨界應(yīng)力強度因子,只要在腐蝕環(huán)境中有循環(huán)應(yīng)力繼續(xù)作用,斷裂總是會發(fā)生的。 疲勞壽命 當一個材料或機械部件失效時,總壽命通常由三部分組成: 裂紋萌生壽命,大量工程實踐表明,實際服役過程中機械部件裂紋的萌生壽命占據(jù)疲勞壽命的絕大部分(甚至達到總壽命的90%)。 失穩(wěn)擴展至斷裂壽命。 金屬材料的疲勞形式 金屬材料的疲勞主要有以下幾種: 一般的塑性變形 低周疲勞下的塑性變形 高周疲勞下的塑性變形 超高周疲勞下晶粒尺寸的微觀塑性變形 影響材料與結(jié)構(gòu)疲勞強度的因素 01 平均應(yīng)力 02 應(yīng)力集中 由于工作條件或加工工藝的要求,零件常帶有臺階、小孔、鍵槽等,使截面發(fā)生突然變化,從而引起局部的應(yīng)力集中,這將顯著地降低材料的疲勞極限,但實驗表明,疲勞極限降低的程度并不是與應(yīng)力集中系數(shù)成正比。但如果要準確地預測機械部件的疲勞行為,就必須估計高應(yīng)力區(qū)或者含制造缺陷的裂紋萌生壽命。 03 殘余應(yīng)力 文獻研究指出,探討殘余應(yīng)力對金屬疲勞強度的影響,需在高周疲勞下才有意義,因為低周疲勞的高應(yīng)變幅下殘余應(yīng)力將大幅度地松弛,所以在低周疲勞下顯示不出多大的作用。表層殘余壓應(yīng)力對于承受軸向載荷且疲勞裂紋起源于表面的零部件是有益的,但要注意核心部區(qū)域的殘余拉應(yīng)力疊加外載后發(fā)生屈服所引起的殘余應(yīng)力松弛問題。殘余應(yīng)力對零件缺口疲勞強度的作用十分顯著,這是由于殘余應(yīng)力也存在應(yīng)力集中現(xiàn)象和殘余應(yīng)力對疲勞裂紋擴展的影響更大的緣故。但殘余應(yīng)力的應(yīng)力集中不僅與缺口幾何因素有關(guān),還與材料特性有關(guān)。 04 尺寸效應(yīng) 材料的疲勞極限σ-1值通常是用小試樣測定的,試樣直徑一般在7~12mm,而實際構(gòu)件的截面往往大于該尺寸。試驗指出,隨著試樣直徑的加大,疲勞極限下降。其中,強度高的鋼比強度低的鋼下降的快。 05 構(gòu)件表面狀態(tài) 構(gòu)件表面是疲勞裂紋核心易于產(chǎn)生的地方,而承受交變彎曲或交變扭轉(zhuǎn)負荷的構(gòu)件,表面應(yīng)力最大。構(gòu)件表面的粗糙度、機械加工的刀痕都會影響疲勞強度。表面損傷(刀痕、磨痕等)本身就是表面缺口,會產(chǎn)生應(yīng)力集中。使其疲勞極限降低,且材料強度越高,缺口敏感性越顯著,加工表面質(zhì)量對疲勞極限的影響就越大。 06 環(huán)境因素 廣義的高溫疲勞是指高于常溫的疲勞現(xiàn)象。但通常情況下,由于有些零件的工作溫度雖然高于室溫,但并不太高。只有當溫度高于0.5Tm(Tm為以熱力學溫度表示的熔點),或在再結(jié)晶溫度以上時,出現(xiàn)了蠕變與機械疲勞復合的疲勞現(xiàn)象,這時才稱為高溫疲勞。 07 載荷類型 不同載荷下疲勞極限的大小順序為:旋轉(zhuǎn)彎曲<平面彎曲<壓縮載荷<扭轉(zhuǎn)載荷。在腐蝕介質(zhì)中,加載頻率的裂紋擴展的作用比較明顯。在室溫和試驗環(huán)境下中,常規(guī)頻率 (0.1~100Hz) 對鋼和黃銅的裂紋擴展幾乎沒有任何影響。在試驗中一般而言,如果試驗加載頻率低于250Hz,頻率對金屬材料的疲勞壽命的影響就較小。 08 材料缺陷 脆性材料不存在應(yīng)力降低或加工硬化現(xiàn)象,一旦出現(xiàn)缺口,在較小的名義應(yīng)力條件下就可能發(fā)生斷裂。經(jīng)驗表明,當存在缺口時,金屬的疲勞極限降低,并且塑性越差,缺口對疲勞極限的影響越大。 09 加工方式 文獻中指出,在疲勞試驗試樣的制備過程應(yīng)是導致試驗數(shù)據(jù)離散性最重要的環(huán)節(jié),如車、銑和校直等機械加工方式都與試樣的最終制備質(zhì)量有關(guān)。正是由于制備方式和熱處理因素會影響材料的疲勞性能,尤其是熱處理的影響較大,因而即使是同一批次和尺寸、形貌完全相同的試驗也很難完全重復以前的疲勞試驗結(jié)果。由此可見,工件的生產(chǎn)加工因素會導致零部件的實際疲勞壽命偏離分析計算的期望壽命值。 10 材料屬性 疲勞試驗數(shù)據(jù)的離散性 試驗設(shè)備和試樣本身是造成疲勞試驗數(shù)據(jù)(或結(jié)果)離散性的根本原因。據(jù)文獻分析介紹,在測定零構(gòu)件的疲勞壽命時,名義載荷相對實際載荷有3%的誤差,就會使疲勞壽命產(chǎn)生60%的誤差,極端情況可能會導致120%的壽命誤差。而對于疲勞試驗機來說,3%誤差是完全允許的。不過文中也提到,在靜力破壞試驗中,即使對強度分散性較大的鑄造材料和玻璃等,也不像疲勞壽命那樣存在嚴重的分散性。 結(jié)構(gòu)疲勞設(shè)計方法的發(fā)展 安全壽命法 設(shè)計應(yīng)力低于疲勞極限,認為結(jié)構(gòu)中無缺陷。 失效安全法 設(shè)計應(yīng)力與平面缺陷情況下的剩余強度有關(guān),該設(shè)計方法允許存在可接受的缺陷。 安全裂紋法 允許存在確定性可預測的擴展裂紋。 局部失效法 能夠解決金屬疲勞分析中的一些問題,目前在法國廣泛應(yīng)用。20世紀90年代超高周疲勞試驗技術(shù)的興起,充分說明一些微觀缺陷(如夾渣、氣孔、鍛造形成的大尺寸晶粒等)對材料的疲勞壽命也具有重要的影響。 對于鋼材料,在缺少材料的疲勞試驗數(shù)據(jù)時,可由材料的拉伸強度極限做出近似的S-N曲線。把疲勞極限與拉伸強度和試樣斷裂伸長率聯(lián)系起來是具有較高精度的一種估算方法。
免責聲明:本網(wǎng)站所轉(zhuǎn)載的文字、圖片與視頻資料版權(quán)歸原創(chuàng)作者所有,如果涉及侵權(quán),請第一時間聯(lián)系本網(wǎng)刪除。
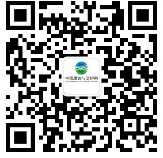
官方微信
《腐蝕與防護網(wǎng)電子期刊》征訂啟事
- 投稿聯(lián)系:編輯部
- 電話:010-62316606-806
- 郵箱:fsfhzy666@163.com
- 腐蝕與防護網(wǎng)官方QQ群:140808414