航空齒輪是發(fā)動機中重要的傳動元件,它的質量和性能嚴重影響發(fā)動機的使用壽命。齒輪性能是由材料的熱處理和機械加工共同決定的,齒輪熱處理是一項復雜的金相組織不斷發(fā)生變化的過程,熱處理的淬火溫度、回火次數(shù)等對齒輪性能有著至關重要的影響,故以12Cr2Ni4A材料的航空齒輪為研究對象,基于deform有限元軟件分析熱處理參數(shù)對航空齒輪性能的影響規(guī)律,優(yōu)化航空齒輪的熱處理工藝,最后基于理論分析進行熱處理試驗,得到在滿足使用要求的條件下,當淬火溫度為800℃、回火2次時齒輪材料的各項性能達到最佳,驗證了熱處理分析的正確性,優(yōu)化了齒面殘余應力分布與微觀組織分布,降低了磨削裂紋的發(fā)生幾率。
01
引言
齒輪工作時轉速高、傳遞功率大,承受著交變和沖擊載荷,齒和齒之間互相嚙合而產(chǎn)生齒面接觸應力、齒根彎曲應力。對齒輪一般有以下幾方面的要求:齒型面有足夠的強度、抗磨損性能、硬度、接觸疲勞性能、高的耐磨性以及良好的綜合力學性能。上述要求通過熱處理來實現(xiàn),12Cr2Ni4A材料熱處理的主要工藝,如表1所示。滲碳前的工藝可以改善零件的性能,滲碳是提高工件表面層含碳量的常用手段,滲碳后材料表層的硬度和耐磨性大幅提高,而芯部的韌性不受影響。深冷處理可以獲得穩(wěn)定的組織,提高材料的使用性能。
表1 12Cr2Ni4A材料熱處理主要工藝
理想中的齒輪金相組織應為細針狀馬氏體、少量奧氏體與粒狀碳化物的組合,在熱處理時要避免發(fā)生碳化物的偏析。這是因為碳化物的偏析可使齒輪形成裂紋源,使材料橫向和縱向力學性能差異增大,影響齒輪的工作性能。此外,要嚴格控制齒輪淬火后的殘余奧氏體含量,使其維持在一個合理的水平,因為奧氏體屬于不穩(wěn)定的金相組織,齒輪在工作過程中,殘余奧氏體會逐漸產(chǎn)生相變,轉變?yōu)轳R氏體或其他組織。奧氏體與其他金相組織的體積密度不同會引發(fā)齒輪微觀尺寸上的變化,齒輪體積的變化則會引起材料內部殘余應力也隨之發(fā)生變化,從而影響齒輪的壽命。文獻以deform為研究工具,分析了均勻傳熱系數(shù)對SCr420H材料的齒輪應變分布的影響,能夠對碳層和應變進行預測,文獻通過deform有限元模擬熱處理過程分析得到了減少工件和模具變形的鍛造工藝,文獻通過有限元分析了溫度、應力等對材料組織的影響,文獻通過試驗分析了回火次數(shù)及溫度等參數(shù)對不同材料的性能的影響,指出回火溫度與次數(shù)對SKD61鋼組織的影響規(guī)律,指出回火是導致材料高延展性的重要因素,文獻研究了淬火溫度對齒面硬度的影響規(guī)律,文獻通過實驗研究了不同的熱處理對納米結構氧化物彌散強化鋼和42CrMoS4鋼的晶粒尺寸的影響。他們雖然研究了熱處理參數(shù)對各種鋼材料性能的影響,但是并未涉及到齒面殘余應力分布和微觀組織分布,也并沒有研究熱處理工藝對磨削過程的影響,因此以12Cr2Ni4A材料的航空齒輪為研究對象,擬對航空齒輪的熱處理工藝進行系統(tǒng)分析,研究淬火、回火工藝對齒面硬度、殘余應力以及組織結構的影響規(guī)律,優(yōu)化熱處理工藝,提高齒輪的使用性能。
02
淬火工藝對齒輪性能的影響
12Cr2Ni4A材料的淬火溫度在(780~840℃范圍內,利用DE-FORM-3D建立了不同淬火溫度下的齒輪熱處理仿真模型,在其余工藝不變的前提下,研究淬火溫度對齒面殘余應力和硬度的影響規(guī)律。
在齒面隨機選擇若干組點,取其殘余應力的平均值作為研究對象。不同淬火溫度下殘余應力沿齒厚方向的變化情況,如圖1所示。隨著淬火溫度的升高,殘余壓應力有逐漸下降的趨勢,到達820℃之后,變化趨于平緩。原因在于,隨著淬火溫度不斷升高,齒輪中的熱應力不斷增加,由于熱應力會導致材料表面產(chǎn)生拉應力,因此隨著淬火溫度的不斷提高,材料表面的殘余壓應力逐漸下降。當淬火溫度繼續(xù)升高,材料的相變應力隨之增加,與熱應力發(fā)生中和,使得材料表面的殘余應力趨于平穩(wěn)。
圖1 淬火溫度對硬度和殘余應力的影響
在齒面上隨機選擇若干組點,取其硬度的平均值作為研究對象。圖 1 顯示了不同淬火溫度下齒輪硬度沿齒厚方向的變化情況。隨著淬火溫度的升高,齒輪的硬度不斷增加,在 820℃時表面硬度達到了最大值 HRC 62.1,隨后齒面硬度變化趨于平穩(wěn)。原因在于,隨著淬火溫度的升高,材料內部合金元素的碳化物逐漸溶解,碳在奧氏體中的均勻度也慢慢提高。淬火后,馬氏體中碳的飽和度也不斷增大,因此隨著淬火溫度的不斷升高齒輪的硬度不斷增大,此后隨著馬氏體中碳的逐漸飽和,齒面硬度的變化也趨于平緩。
03
回火工藝對齒輪性能的影響
回火工藝主要是消除或減小殘余應力,使材料組織細化,提高材料使用性能。回火后的組織以回火馬氏體為主,硬度較淬火馬氏體稍小。回火工藝中,相比于回火時間,回火次數(shù)、回火溫度對于材料組織性能的影響更明顯。文中建立了不同回火工藝下的齒輪熱處理仿真模型,研究回火工藝對齒面硬度和組織性能的影響。
固定其余工藝不變,12Cr2Ni4A材料在不同回火溫度下的齒面硬度變化分布,如圖2所示。隨著回火溫度的提高,齒面硬度有所上升,在 400℃時齒面硬度達到最大值 HRC 61.1。隨著回火溫度繼續(xù)提高,齒面硬度有所下降,550℃時,齒面硬度下降到為 HRC 54.3。出現(xiàn)上述現(xiàn)象的原因在于:隨著溫度上升,組織中馬氏體分解,但此時殘余奧氏體向下貝氏體轉變,而下貝氏體的硬度要高于殘余奧氏體,材料硬度反而有所上升;當溫度超過 400℃時,馬氏體分解的速度大于下貝氏體生成的速度,材料的硬度明顯下降。
圖2 回火溫度對于硬度的影響
選擇原有熱處理工藝,研究回火次數(shù)對齒面殘余應力的影響規(guī)律。12Cr2Ni4A材料在不同回火次數(shù)下的齒面殘余應力曲線,如圖3所示。隨著回火次數(shù)的增加,材料結構變形逐漸恢復,齒面殘余壓應力有所下降,齒輪內部的殘余應力得到了有效釋放,說明材料組織結構的穩(wěn)定性得到增強,對于提高齒輪的力學性能有一定的幫助。
圖3 回火次數(shù)對于殘余應力的影響
04
熱處理工藝優(yōu)化試驗
試驗方案與設備:從淬火溫度對齒面硬度、回火次數(shù)對材料金相組織的影響規(guī)律出發(fā),建立熱處理優(yōu)化方案的驗證試驗。結合仿真分析與生產(chǎn)經(jīng)驗,設置3個淬火溫度,分別為800℃、820℃和840℃,回火次數(shù)設置為 0、1、2次,其余熱處理工藝參數(shù)維持不變,試驗方案, 如表2所示。
表2 試驗方案設計
工件材料選擇 12Cr2Ni4A,尺寸為60mm(長)×40mm(寬)× 30mm(高)。熱處理試驗是在石家莊科鑫齒輪加工廠進行的。部分樣件和硬度檢測裝置,如圖4所示。
圖4 熱處理試驗樣件和硬度檢測裝置
試驗結果分析:淬火溫度對試件表面硬度的影響: 取試件 5、2、8(淬火溫度分別為 800℃、820℃、840℃,回火次數(shù)均為1次)進行顯微硬度的檢測,每個試件表面測量3個點,取其硬度的平均值作為該試件表面的硬度值,測量結果分別,如圖5所示。
圖5 試件5、試件2、試件8表面硬度及淬火溫度與表面硬度間的關系
從圖6可以看到,隨著淬火溫度的提高,試件表面的顯微硬 度呈逐漸上升的趨勢,試驗結果與仿真分析得到的結果是一致的。試驗樣件的表面硬度值要高于對應淬火溫度下的仿真數(shù)據(jù),最大相對誤差為 5.6%。
圖6 試件1、試件5、試件9的金相組織
回火次數(shù)對金相組織的影響:對試件 1、5、9(回火次數(shù)分別為 0、1、2 次,淬火溫度 800℃)進行金相組織檢測。首先對試件進行線切割處理,再依次進行研磨、拋光、化學腐蝕,完成金相樣件的制備。
在金相顯微鏡下對試件進行組織觀測,如圖6(×100)所示。
隨著回火次數(shù)的增加,材料組織的均勻度逐漸提高,組織更加細化。具體來講:0次回火的材料組織為板狀馬氏體+殘余奧氏體+顆粒狀碳化物,1次、2次回火的組織為針狀馬氏體+少量殘余奧氏體+顆粒狀碳化物。2次回火后的組織分布更加均勻,馬氏體細化程度更高。板條狀馬氏體的組織性能較差,降低了材料的力學性能,在工件的磨削過程中,很容易產(chǎn)生磨削裂紋。而針狀馬氏體組織性能良好,均勻分布的針狀馬氏體可以很好地提升材料的力學性能,從而有效防止磨削裂紋的發(fā)生。
05
結論
(1)淬火溫度由原有的 820℃降至 800℃,回火后,材料表面的殘余壓應力由15.5MPa提高至21MPa,齒面硬度由HRC 65下降至HRC 64。在硬度滿足使用要求的前提下,提高齒面殘余壓應力,可有效預防磨削裂紋的產(chǎn)生;
(2)回火溫度與回火時間保持不變,回火次數(shù)在原有1次的基礎上增加到2次,2次回火后,齒面殘余壓應力略有下降,但回火后材料的組織分布更加均勻,材料的力學性能得到加強,提高材料的抗疲勞能力。
免責聲明:本網(wǎng)站所轉載的文字、圖片與視頻資料版權歸原創(chuàng)作者所有,如果涉及侵權,請第一時間聯(lián)系本網(wǎng)刪除。
相關文章
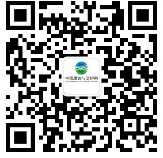
官方微信
《腐蝕與防護網(wǎng)電子期刊》征訂啟事
- 投稿聯(lián)系:編輯部
- 電話:010-62316606-806
- 郵箱:fsfhzy666@163.com
- 腐蝕與防護網(wǎng)官方QQ群:140808414
文章推薦
點擊排行
PPT新聞
“海洋金屬”——鈦合金在艦船的
點擊數(shù):8148
腐蝕與“海上絲綢之路”
點擊數(shù):6486