涂料是一種經濟有效的防腐材料,由于其施工簡便,使用方法靈活,適應性強,廣泛應用于化工、石化、建筑、交通、能源等領域中,涂料不僅用于涂刷設備、管道和建筑物外壁起保護、標志與裝飾作用,也用作設備和構筑物內壁的防腐蝕涂層。但由于涂料選用、表面處理、施涂工藝、使用維護等不當,有可能發生腐蝕破壞。
1
耐腐蝕涂層防護機理和附著性
耐腐蝕涂層主要有下列兩種防護機理:
(1) 通過物理屏障以切斷與環境聯系,形成一層高電阻薄膜,使氧、水及介質的離子不易滲透進去,
(2) 通過添加顏料與填料起緩蝕鈍化和犧牲陽極保護作用,或起延遲涂層老化效果。
涂層對金屬基體的附著性是決定涂層腐蝕破壞的關鍵因素之一。
涂層附著機理有機械附著、極性附著和化學附著。其中相對重要的是機械附著。
機械附著取決于被涂表面粗糙度,粗糙的表面具有較好的機械粘附性。可通過噴砂或酸洗磷化工藝控制,以對涂裝表面的機械附著提供優化的粗糙度。涂層如完全取決于機械粘結,要求其有較深的錨紋結構,對基體的黏結比化學或極性黏結更為有效。
大多數涂裝是在維修現場進行,錨紋深度超過0.25~0.50mm將有利于黏結。要求涂層厚度滿足對基體的黏結和防護還取決于涂料的性質與環境的嚴酷程度。
極性附著取決于涂料中樹脂對基體的吸引力。樹脂的吸引行為好似軟磁鐵的極性吸引。樹脂粘合劑與金屬表面之間的吸引程度可確定極性附著的數值。如環氧類樹脂具有優異的附著性,這是由于其羥基的極性對金屬表面顯示很大的吸引力,但不同樹脂對金屬表面的極性吸引和黏附能力有較大差異。
雖然已知涂裝基底的潤濕對附著是重要的,這是根據涂層對鋼最終黏結必須要有緊密的分子接觸。
化學附著實際上是涂料與金屬基體之間的化學反應。如磷酸乙烯基底漆在金屬、樹脂、防腐顏料之間發生反應,以便產生牢固的附著的耐腐蝕涂層。環氧基有很大的化學親和力,加上羥基的極性吸引,使環氧涂料具有獨特的黏結能力。
2
涂層腐蝕破壞類型
起白、粉化
起白是由于涂層表面暴露于大氣環境所呈現的白色粉化現象。由于紫外線、水分、氧和化學藥劑同涂層的反應,使其變質或降解造成了起白。起白的速率決定于成膜物質的類型、顏料的類型以及顏料同成膜物質的比率。高含量顏料的涂層常常起白較快。
金紅石型的二氧化鈦可能是阻礙起白的較好的顏料之一。環氧涂料主要用于抗化學藥品和溶劑,而對耐候風化性能較差,容易起白。
變色
變色或褪色是由成膜物質或由顏料選擇不當造成的。例如,對于成膜物質,白色酚醛涂料可以變黃,而丙烯涂料將較長時間保持白色。
變色或褪色可能由表面起白或由帶色顏料的破損引起。其中顏料由紫外線或化學環境的反應而分解或降解。如鉻酸鉛黃通過光照逐漸降解變色,從亮黃變到褐黃色。鐵藍由于和堿反應而降解。變色或褪色可以通過改進涂料的配方而消除或減小。
通過選擇成膜物質和顏料可以控制因粉化引起的變色。合適的顏料可達到抗光照和耐化學侵蝕。此外,改良創新的配方應該能提供涂料合理組成的性能平衡。選擇著色的顏料對涂料配方至關重要。
一個好的涂料配方由于不適當選擇染色顏料,可能造成變色問題。但在化學環境中,涂層防腐比防變色更為重要。
開裂
開裂是一種涂層破壞的形式,它與涂膜老化過程中的收縮有關。當膜的收縮應力大于內聚力時,因膨脹的差異,促進涂膜破裂。
一般硬而脆的膜比韌性的膜更容易開裂。過厚的膜將加劇開裂。涂膜開裂也可能由膜中不合適的溶劑釋出。
涂層的開裂可以選用有韌性的涂料或添加增韌劑來預防,這種涂層應足以抵拒在特殊使用條件下給定表面的收縮應力。如有裂痕也可通過選擇底漆、面漆或中間漆其膨脹和收縮同樣速率的涂料配方。
開裂破壞不是由黏結缺陷造成,則可采用合適的涂料重涂,橋接裂縫處,直接覆蓋老涂層。如果開裂破壞是與低劣的黏結性有關,則應全面鏟除老涂層再重涂。
脫皮、脫層
脫皮或剝落是涂層大截面脫落露出裸金屬的破壞,脫層是脫皮發生在涂層之間的破壞。其共同原因與它們低劣的附著性有關。
脫皮與脫層的主要原因有:
(1) 低劣的表面處理:欲涂裝表面若處理不徹底,殘存有水分、油脂、污物、銹跡、鱗皮、舊涂層等將嚴重影響底漆乃至涂層系統的附著性。但涂層的附著性涉及環境的嚴酷和涂層的厚薄等因素。
為了確保金屬基層與底漆最初的結合,表面必須得到徹底的清理。其中最嚴重的表面污染為緊密附著的軋屑,如果水分和氧滲透到軋屑下,則將容易引起腐蝕和涂層開裂失效。
(2) 選用不合適的底漆:底漆是涂層系統的基礎,因此必須選用有最大機械或物理附著的底漆,否則選用不合適的底漆將使涂層脫皮。
底漆應具有良好的濕潤性和良好的滲透性能。在某些情況下,如涂裝表面難于干燥,應選用能適應于濕表面有粘結性的底漆。
(3) 不良的氣候環境處理:高濕度、低溫(低于露點溫度)或高溫(大于35℃)、大風等情況下進行涂敷,可能由于不合適的固化或表面污染造成涂層失效。又如采用不合適的溶劑稀釋,當表面干燥時會造成局部樹脂沉淀而引起黏結不良。
(4) 不適當的涂敷工藝:為了基體防護,底漆必須達到相對無針孔的均勻涂層。如噴涂時當霧化壓力太大時,在其噴嘴可能產生干噴涂,因而會造成多孔的涂層。
如果噴槍離工件太遠也會產生干噴涂,甚至會引起過噴或噴濺,以及會減小膜的厚度。應按產品說明進行噴涂。
(5) 涂層厚度過厚或過薄:由于涂膜固化時伴有蒸發、冷卻、聚合等過程,故會引起收縮,而收縮又會使涂層間產生應力。
如果這種應力增大到超過涂膜的粘結力時,則將在涂層的薄弱處出現涂層間脫皮或造成涂層與金屬基體脫層而引起破壞,但如黏結力很大,能阻止界面收縮,但產生的內應力又會引起龜裂。
尤其當涂膜變得較厚時,由于逐次涂膜的內在應力累積,最終超過黏結力,而引起脫皮或脫層。一般認為過大的涂層厚度常會發生脫皮或脫層問題,然而,并不意味著較薄涂層是可靠的,較薄涂層有時也會造成涂層破壞。
(6) 涂層之間不相容:選用涂料時如上下層涂料不相容,或底面漆不配套,會產生脫層。這是由于成膜樹脂與上道涂層之間極性附著不匹配引起的,或上層的溶劑咬住下層的涂膜。
為了防止這種涂層破壞,涂裝系統應避免從多個供應商提供涂料,以防混雜應用,最好采用同類型涂料,或除非根據使用經驗某幾種涂料有相溶性可以采用,建議按涂料供應商的說明進行涂裝。
(7) 涂層之間有污染:涂層之間有污染將引起脫層。因為涂層表面殘存有污染,如灰塵、水分、鹽類結晶等,再在其上涂敷則將影響上下涂層間的黏結。
(8) 化學侵蝕:如果由兩個或多個涂層組成的涂裝系統,由于暴露于化學或高濕環境中,面涂層會發生變質或軟化,可能在涂層薄弱處發生脫層破壞。這種破壞可以通過選用耐蝕的涂料予以防止。
上述脫層脫皮的失效分析僅是從工藝上找原因,理論上應從有缺陷或擦傷的涂層鋼在有電解液環境中發生陽極和陰極腐蝕反應考慮,應盡可能避免膜下陰極反應發生,阻礙水、氧、電子到達反應區,以及減少陰極反應表面的催化作用。
為防止涂層脫皮脫層,應盡可能保證表面處理質量,徹底去除底面或層間的各種污染,不應在不良氣候環境下涂敷,選用粘結力強的底漆,底面漆應配套等。
鼓泡
鼓泡或起泡是涂層破壞的形式之一,更被視為涂層腐蝕破壞的先兆。鼓泡是涂層與基面間存在某種氣體,氣體膨脹力超過了涂膜與基體的黏結力,就會鼓起。
引起鼓泡的具體原因如下:
(1) 當涂層系統暴露或浸入高濕或水的環境中,由于水或水氣滲透進入涂膜,在金屬基體處積聚,產生相應的滲透壓,如發生腐蝕反應,引起容積膨脹,使涂層鼓泡。
當鼓泡內壓力在垂直方向上大大超過涂層界面上的黏結力時,將發生龜裂或剝離。在一般用于防腐的有機涂層暴露于水溶電解液中,水吸收率約為0.1%~3%范圍,水吸收將造成涂層腫脹起泡。
(2) 由于在涂敷和涂膜干燥過程中,如有溶劑不合適釋出將會發生鼓泡。如涂料組成含有兩種或多種溶劑,最慢揮發的是親水的一種溶劑;當親水溶劑少量集聚,在涂膜形成最后階段,會發生析出,因而形成起泡。如乙二醇醚或酯為低揮發性溶劑,易引起涂層起泡。
(3) 由于涂料中含有空氣泡或揮發物,在膜形成時留下孔洞,如有水和可溶鹽滲入,易發生起泡。
(4) 由于低劣的表面處理形成低凹氣阱,或表面殘留可溶性鹽,如濕法噴砂殘留的緩蝕劑結晶,遇潮氣極易吸水,涂敷后涂膜容易鼓泡。
(5) 施涂工藝不當,如被涂表面未干透含有濕氣就涂敷。又如每道涂層施涂間隔時間太短,前道涂層未經干透,就涂第二道,致使揮發氣體封裹在涂層下。或在低于露點溫度下施工涂敷,以及涂料攪拌不充分,未經完全熟化等,均會造成涂膜起泡。
(6) 選用的涂料對基體或涂層之間的黏結力很低,在這種情況下,某些部位由于水滲透積聚或成膜過程中釋出氣體而發生鼓泡。如聚氨酯漆中含異氰酸酯會與底面濕氣反應生成二氧化碳,導致起泡。
(7) 由于涂料中顏料不耐環境侵蝕,從而使涂膜變質多孔,水氣易滲入涂膜下積聚液體和氣體,會發生鼓泡。
(8) 當涂敷在相對粗糙表面上相對快速干燥時也會發生涂層鼓泡。
(9) 電滲透引起鼓泡,例如存在電偶會產生電位梯度,在電位梯度影響下,水可以透過膜,將會發生鼓泡。
另外,容器內壁、地下管線等涂層鋼常常擦傷,需采用陰極保護。不僅直接的還是雜散的陰極保護電流通過涂層,均可能引起涂層鼓泡。
(10) 在涂層與基體交界面局部處,積聚的氫氣會產生鼓泡。不管是由酸性介質腐蝕陰極析出的氫(如富鋅底漆與水反應生產氫氣),還是儲存石腦油、汽油、煤油等儲罐以及烴生產中設備含硫化氫如滲入涂層多會放出氫,均可能造成涂層鼓泡。
鼓泡情況多是由于水透過涂膜在與基體交界處局部積聚。并且氧穿透涂層,在交界面上發生電化學腐蝕,反應速率由氧對涂層滲透率控制。為防止涂層鼓泡應選用黏結性優異的底漆與配套的抗水分滲透強的面涂料,此外,應保證表面處理的質量,不得有殘存的銹跡及任何雜物,并確保涂底漆前徹底干燥。
還應確保涂敷工藝,如涂敷前涂料要充分攪拌,底層不宜太厚,施涂每層涂料間隔不小于12小時,應保證上道涂層已固化,方可涂敷下一道。如施涂后發現局部起泡,應對起泡處徹底清理,重涂,如大面積起泡,則應全面返工。
起皺
起皺是涂層破壞的形式之一。起皺從涂層外貌看,不是平直的干透的表面,而寧可說是表面不平有微微聳起的現象。
起皺是由于涂層表面快速干燥,而涂層其余部分還未干透,造成涂層內外膨脹率不一而引起。另外,如對水冷器涂層上道漆未干透,即涂下道,或當下道涂敷的溶劑快速溶脹軟化上道涂膜時,也可能產生起皺。
涂敷過厚,有時也可能產生起皺。這時如涂層下受到嚴重銹蝕,則將導致對基體失去黏結力。為防止起皺,應規范涂敷工藝,注意涂敷間隔,控制每道涂層厚度,熱固化應控制好烘干溫度。
銹蝕
涂膜的銹蝕是由于涂層有損傷或有微孔而造成基體金屬腐蝕顯露銹跡。
銹蝕表現形式主要有:
(1) 斑點狀銹蝕 在涂層破損和擦傷部位總會發生這類銹蝕。大多數涂層幾乎不能避免這種銹蝕,即使富鋅涂層對該銹蝕也難以防止。
(2) 針孔狀銹蝕 在涂層表面上,不管是分散的還是集中的均顯示很微小的銹點。當涂料中含有如砂子那樣的微粒時會發生針孔狀銹蝕。也可能因不當的涂敷施工,在涂膜中留存微孔或空隙,以及由于涂層過薄等造成。
(3) 瘤狀銹蝕 這是針孔狀銹蝕進一步發展的結果,由于處于微孔的涂膜下腐蝕產物擴張,造成了突破針孔的瘤狀銹蝕。這是由于表面處理不當或選用的底漆不足以阻止銹蝕。
(4) 膜下銹蝕 由于涂膜局部脫皮、脫層與剝落引起了銹蝕在涂膜下的擴展傳播,于是造成了較大面積涂膜的破損。由于膜下腐蝕產物膨脹,涂層受張應力迫使其進一步脫層或剝落。
造成膜下銹蝕原因為低劣的表面處理、不良的底漆、薄的涂膜,以及這些因素的綜合。膜下銹蝕可從縫隙腐蝕機理進行解釋,也可認為是陽極性底層破壞。
為防止上述銹蝕,除應保證表面處理和涂層質量外,涂敷前涂料必須過濾,并要避免涂層破損和擦傷。此外,應選用富鋅底漆,也可在涂料配方中添加0.1%~3%的緩蝕劑,緩蝕劑應在基面形成保護膜,有效阻止陰極反應進行。
絲狀腐蝕
絲狀腐蝕是膜下腐蝕的特例,如在涂有清漆的鋼上,在高濕度(65%~90%)下最容易發生。絲狀腐蝕發生首先在涂層上要有局部缺陷或擦傷破損,其次要有穿透涂膜的電解液。
絲線狀腐蝕產物在漆膜下面可無序地蔓延,其腐蝕線跡通常沿直線或橢圓形發展。
為防止絲狀腐蝕,應避免涂鍍層破損或擦傷,以及控制濕度,如對儀器保管應處于<55%濕度狀態。
化學侵蝕
當面涂層不耐環境中化學品或溶劑的侵蝕,就會發生面膜的分解或溶解。如果底漆或中間漆對環境敏感,則完工的涂層因失去對基體的黏結力而脫皮。
此外,導致化學侵蝕對涂層下金屬的破壞,一般由膜上的針孔和較薄的涂層引起。對涂層的化學侵蝕可以造成邊緣破損或斑點銹蝕。
如果涂層發生化學分解或溶脹,則應將全部涂層進行噴砂處理,再用新的和更耐腐蝕的涂料涂敷。
如果破損由針孔和較薄的涂層引起,則應根據侵蝕的嚴重程度進行處理,如大于25%表面受到侵蝕,則應將全部涂層用噴砂處理至合適程度,再用新的和更耐腐蝕的涂料涂敷至所需的涂層厚度。
如果涂層破損僅為總表面的百分之幾,并確定其余的涂層完好健全,則僅對破損的表面施以局部清理和局部涂敷。最好對全部表面至少追加一道涂層。
超溫破壞
有機涂層一般多使用于常溫,最高也只能用于100℃以下,如使用環境高于100℃,應選用有機硅的耐溫漆,或無機富鋅漆,或鋁粉漆。
如對含蠟的重質油罐和原油罐底部裝有加熱盤管,管內通180℃蒸汽,應選用耐高溫耐油防腐涂料,否則會造成失效。另外,超溫破壞只是在操作不當的情況下才能發生。
如采用氨基環氧涂層的水冷器,一般運行3~4年不會出現問題。但有時停車操作時,先關水閥門,后關物料閥門,這就會使涂層短時遠遠超過它所能承受的溫度,即會使涂層變色,甚至起皮脫層。
沖蝕和磨耗
一般涂層抗沖蝕和磨耗性能較差,如涂層水冷器的管口由于受到湍流沖擊,磨耗較快,經常需要修補。但聚氨酯與橡膠類涂料系彈性較好材料,抗沖蝕和磨耗較好。
焊接對涂層的破壞
緊鄰焊縫的涂層存在著破損問題。焊接熔融會干預擾亂涂層的黏結力,甚至加速膜下腐蝕。
焊接噴濺會造成凹凸不平缺陷,必須進行清理才能涂敷,否則會引起膜下腐蝕、瘤狀銹蝕與脫皮等。對焊接產生的熔融物應先刮除或鑿去,最好磨削到較平的表面,再進行噴砂清理。
邊緣破壞
涂層破壞通常從邊緣開始,因為涂層一般在邊緣處最薄弱。涂層邊緣破壞通常從銹蝕起始,最后銹蝕在涂膜下蔓延。
如果涂層邊緣已喪失抗拒破壞的能力,應對全部邊緣追加涂敷。補救措施為,經局部清理后,再用足夠的涂料重涂達到合適的厚度。
電偶引起的破壞
涂鍍層中如存在兩種電位差的材料,由于電偶腐蝕會造成涂鍍層破壞。如儲油罐為防靜電采用噴鋁后再用添加碳黑或石墨粉的涂料封孔,這就會造成鋁作為陽極而加速腐蝕,使涂鍍層剝離破壞。
又如馬口鐵上涂有機清漆的食品罐頭或容器,當鍍錫層有缺陷而暴露鐵,在酸性食品電解液中,錫為陰極,鐵作陽極而產生電偶腐蝕,使涂鍍層剝離。
3
涂層鋼腐蝕破壞過程
大多數設備、管道與鋼結構涂層多用于大氣、冷卻水、油品、土壤等環境,水分、氧、化學氣體等會透過涂層并侵蝕鋼。這種侵蝕一般在50~100℃溫度下進行。水分和氣體透過涂層不僅是通過針孔與其它顯微缺陷,而且也可以通過涂膜本身。
主要促發穿透涂膜的動力是滲透壓和電滲透壓,以及恒熱產生的涂膜分子的運動和振動。涂層鋼破壞可以采用階段性的腐蝕步驟進行分析:
(1) 起泡實際上是涂層鋼腐蝕破壞的第一階段。起泡通常被忽視,一般表面沒有鐵銹的痕跡。
水和化學氣體透過涂膜,這些溶質離子在涂膜與基體間產生滲透壓,并形成濃度梯度,直至涂膜產生鼓泡。起泡也取決電化學反應,也由于電滲梯度水擴散通過涂膜。腐蝕開始后,由于腐蝕區域與被保護區域之間的電位差,使被吸引的水分進一步通過涂膜。因此,電滲透也是造成起泡的原因。有關起泡評定可參看ASTM D714-56標準。
(2) 銹蝕是涂層鋼腐蝕破壞的第二階段。起泡后,有時可以發現鐵銹斑點或是針孔狀銹蝕,有關涂層銹蝕評定可參看ASTM D610-68或美國鋼結構涂裝協會(SSPC)標準Vis-2。
(3) 涂層脫離是涂層鋼腐蝕破壞的第三階段。由于銹蝕使涂層氣泡破裂,甚至發生片狀剝離或脫皮,其結果使鋼表面直接暴露于環境中,腐蝕即以不可抑制的速率發生,由于對底面的化學侵蝕,強制鄰接的涂層發生分離。
對這個過程可認為是由于很大的氣泡造成的。一旦涂層系統失去屏障,鋼將直接受到侵蝕。這種侵蝕不是均勻的,而是局部的。
(4) 點蝕是涂層鋼腐蝕破壞的第四階段。涂層脫離后主要發生點腐蝕,也只有當陽極部位相對于陰極部位較小時才可能發生。
點腐蝕造成了鋼結構局部弱化。由于腐蝕電池變得更為活性,促使點腐蝕進一步發展成深孔直至穿孔,使電解質即能侵入鋼結構背面的新鮮金屬。
(5) 結構喪失是涂層鋼腐蝕破壞的最后階段。由于未保護底面受到化學侵蝕,腐蝕以最劇烈的速度發展。點蝕孔變為腐蝕坑,并快速擴展到正面和反面,最終造成鋼結構喪失功能。
4
涂層失效原因及防護措施
涂層破壞失效原因大致可分為環境介質因素、涂料選用因素、表面處理與涂敷施工因素等。根據其破壞發生原因,可以針對性提出防護措施。
水分和氧的滲透
因為涂層總有一定的透氣性,其氣孔平均直徑為10-5~10-7cm,而水和氧的分子平均直徑只有幾個埃,比涂膜樹脂分子間的平均空隙小,所以水、氧等容易透過涂層。
涂層不僅存在分子滲透性,還存在離子滲透性,水分子可離解成H+與OH-,這些離子能和構成涂層的聚合物電離基進行離子交換,并從聚合物密度較小部位或空隙處擴散進入,或經涂膜微氣孔在毛細管作用下進入,或經填料或顏料與基料間界面滲入。
由于水對涂膜的不斷滲入,會在涂層與鋼基體界面形成積水層,再加氧的進入,造成了膜下腐蝕的條件。因此,水分透過涂膜到基體是控制膜下腐蝕過程的要素。
水分透過涂膜的推動力是滲透壓和電滲透壓,通過由熱造成聚合物內分子的運動和振動下幫助輸送。水化的極性基團,例如羥基和其它基團,經與氫結合可增加水汽透過涂膜的速率,而涂膜內交聯鍵合的密集可減少水汽的滲透率。
除了特殊的化學基團與鍵合外,還有涂膜的某些有機組成對化學溶劑或水分侵蝕敏感。例如對水性乳劑涂膜,配方時應小心采用表面活性劑和其它添加劑,不幸的是,固化后這些添加物留在涂膜內,如長期暴露于水分中,會使涂膜腫脹、衰變與軟化。
另外,填料的種類和含量對水分的滲透有較大影響。如惰性的無機粉末等填料,云母、石墨、碳黑等,加入到聚合物中,能減少水和介質的滲透率。纖維狀填料,如石棉、玻璃纖維、碳纖維等也有同樣的作用。尤其是鱗片狀填料,如玻璃鱗片、不銹鋼鱗片等,加入到涂層中能大大減少水和介質的滲透率。這是由于鱗片相互平行分散排列,增加了水與介質滲透過程的途徑,延長了介質到達金屬基體的時間。因此采用鱗片涂料常是防止水分和氧的滲透的有效方法。
化學介質侵蝕
化學介質對涂膜的侵蝕是不可逆的,會導致聚合物網狀結構交聯間鍵合或鏈段的化學溶脹與擴大,當空間達到酸堿分子能夠滲透進去時,會破壞涂層與基體之間分子吸附力與機械咬合力,使涂層失效。
一般說來,酚醛涂料耐酸,環氧涂料耐堿,環氧酚醛涂料耐酸耐堿,氯化橡膠涂料耐酸又耐堿,漆酚涂料耐酸不耐堿。
化學介質不僅對有機涂膜,而且對無機填料與顏料均會干涉到化學侵蝕。顏料對環境情況敏感,尤其是活性的金屬性顏料應予考慮,雖然惰性的顏料(如二氧化鈦、硫酸鋅、碳酸鈣等)大量作為加強物,能減緩水分透過涂膜的速率。
活性顏料一般用于耐腐蝕涂料,包括鉛丹、鉛白、堿性鉻酸鋅、鋅粉、氧化鋅、磷酸鋅、鉬酸鋅、鉻酸鍶、鉛酸鈣等。這些顏料通過多種方式起到單一或綜合的抗腐蝕作用。歸納如下:
(1) 起物理屏障作用;
(2) 部分溶解滲透與水中,成堿性使鋼鈍化(除鋅粉和氧化鋅外);
(3) 在涂膜分解前和酸反應,形成難溶鹽,并轉化為惰性產物(所有含鉛成分顏料);
(4) 吸收或反射紫外線光,使有害能量減至較少(鋁粉、鋅粉和氧化鋅);
(5) 有助于氧化反應,形成鈍性氧化物,緊密接觸與金屬基體上(鉻酸鹽、磷酸鹽、鉬酸鹽、鉛丹);
(6) 提供犧牲陽極保護(高濃鋅粉、鋁粉)。
顏料或填料還必須具有耐成膜物質和不與侵蝕性化學劑反應的性能。對堿性敏感顏料,如鉻酸鉛、鋅黃、鉬酸鹽、鉻橙、鉻綠和含鋁的顏料,應當不適用于堿性環境。
對酸性敏感顏料,如鋅及某些同酸急劇反應的堿性顏料如碳酸鈣,應當不適用于強酸性環境。
然而,因為不適當選用涂料和顏料而造成涂層失效破壞通常不太會發生。這是由于大多數涂料在制造廠已對涂料組成做了試驗,直到涂料完全可靠才投入商用。但關鍵是雖采用了合格的涂料和正確的涂敷工藝,如干涉到不妥當或低劣的表面處理,以及涂層厚度不足,則將是造成涂層失效,其破壞原因可能超過75%。
有機溶劑溶脹
水可以侵蝕和溶脹對水有親和力的活性劑團的材料,這包括羥基和其它顯現氫鍵的基團。這些基團在涂膜中對水羥基的親和力比其相互有更強的親和力。因此,當聚合物羥基和水優先形成氫鍵,氫鍵中間鏈發生斷裂,這樣聚合物鏈分離,容許另外的水分子從分離的鏈中間滲透進入,爾后更進一步滲透,直至更多的水透入。最終將發生聚合物的溶脹或溶解。類似的理論也可說明聚合物在有機溶劑中溶解的原因。
一般來說,樹脂的極性分子不被非極性溶劑侵蝕,反過來也一樣。極性聚合物如聚醚、聚酰胺、聚乙烯醇等,不溶或難溶于烷烴、苯、甲苯等非極性溶劑中,但可以溶解或溶脹于水、醇、酚等極性溶劑。
溶劑型的涂料(乙烯基、氯化橡膠)容易溶解于該溶劑中,而化學轉化的涂料(環氧、尿烷、醇酸)很少受溶劑的影響,因為它們的交聯鍵和鄰接的骨干聚合物鏈中間有較大的附加吸引力。
對涂層不希望有溶劑侵蝕,僅當溶劑與水分、化學藥劑或其它侵蝕物質結合,它將較容易滲透涂層,雖然它處于變稀的軟化狀態。如石化廠的裝苯、二甲苯、乙二醇等溶劑儲罐內壁一般不采用有機涂料涂敷,因有溶脹作用,但可采用無機富鋅涂料防護。又如石腦油含有高含量的芳香烴(溶解性好的溶劑),其儲罐應采用較強耐溶劑性的涂料,如環氧酚醛漆或富鋅漆。
表面處理
涂裝前的表面處理至關重要,它關系到涂層的質量與使用壽命。
鋼表面的軋屑或鱗皮應在涂敷前去除,因為在戶外風化或潮濕環境,水分將透過涂層以及軋屑間裂紋直至鋼基體。由于軋屑與鋼鐵之間電位差為0.2~0.3V,軋屑是陰極,會造成鋼基體加速侵蝕,腐蝕產物在軋屑底擴展膨脹,促使涂層剝離。
鋼表面如有油、脂、蠟等污染,將嚴重影響或完全抑止涂膜與基體接觸,妨礙黏結。因為這些污染本身不可能與金屬粘結,而是把涂層與基體隔開。
灰塵、化學沉積物、噴砂后殘留的粉塵、砂粒和其它污染,實際上減少涂層的黏結力,并加速膜下腐蝕,這是由于這些污染提供燈芯作用,加速水分透過涂膜。在浸液情況下,截留的水溶污染會產生滲透電池,導致涂層起泡和脫層等破壞。
噴砂清理是為去除鋼表面污染、施涂耐化學侵蝕涂層的最好的預處理方法。它還可以增加表面粗糙度,粗糙的表面提供與涂膜齒狀或錨紋黏結。但更重要的是它提高了表面積2~10倍或更多,較大的表面積有機會提供涂層和清理后金屬之間較好的吸引與較大的黏結力。
事實上,在所有情況下發生黏結力,不管涂料的類型,分子間吸引的原子間距離必須很小(比10埃更小),以便使涂層與基體表面達到緊密的接觸。
噴砂應選用石英砂、金剛砂,不得含有油污,含水量小于1%,按GB 8923-88標準,經噴砂清理后應達到Sa2.5級,錨紋深度應達40~70μm。如室外噴砂不符合一級防爆廠區安全與環保原則,可采用濕法噴砂。有時也可以采用磷化處理。某些場合噴砂清理不經濟也不適宜,可考慮采用銹面底漆直接涂敷在帶銹鋼鐵上做底漆使用。
涂層厚度
涂層太薄明顯比較厚的更早被破壞,因為容易出現漏點和針孔,而且水、氧容易更快的穿透薄膜。
事實上,上世紀由美國鋼結構涂裝協會(SSPC)推斷認為,涂層每增加臨界最小涂層厚度25μm,將增加保護壽命20個月。研究表明,如果最初最小涂層厚度達到上述要求,則能得到一定的保護。
但對所有涂料類型或環境,這種涂層厚度并不是一成不變,對于更耐腐蝕或最少滲透性的涂層,以及較溫和的環境可以較薄些。但對臨界最小涂層厚度只有通過好的表面處理才可做到。
早年認為,在溫和的使用環境,最初最小的涂層厚度,對油基涂層為250μm、對醇酸涂層為130μm、對酚醛涂層為160μm、對乙烯基涂層為85μm、對氯化橡膠涂層為110μm、對環氧涂層為115μm。
但對嚴酷的使用環境,有必要適當增加涂層厚度,但近年隨著新穎耐蝕性優異的涂料問世,不一定要采用較厚的涂層,而對嚴酷環境下設備與管道防護需要采用涂層較厚的重防腐涂料。如根據GB 50046《工業建筑防腐蝕設計規范》規定(單位為μm):
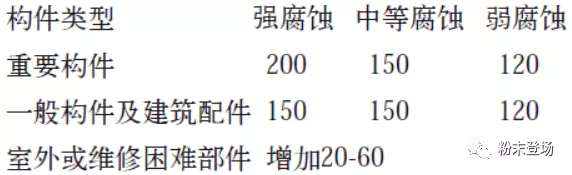
根據SH 3022-1999《石油化工設備和管道涂料防腐蝕規范》規定(單位為μm):
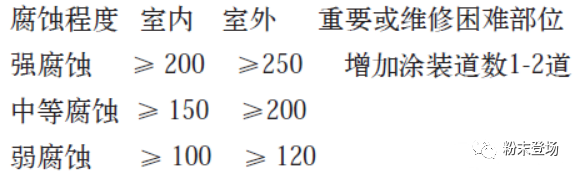
涂料選用
所采用的涂料應符合相關質量標準規定,應選擇合適的涂層配套體系,底漆、中漆、面漆應根據設計規定和產品說明書。
底漆要求附著力強,中漆要求滲水性和透氣性小,面漆要求耐腐蝕性好。不同廠家,不同品種的涂料,不宜混合使用。涂料選用應按設備和管道的使用環境而定。
隨著科學技術的發展,原有傳統的涂料,如油基涂料、醇酸涂料等逐步淘汰,技術新穎,性能優越的防腐涂料不斷問世。對石化行業設備、管道、鋼結構及構筑物等選用的涂料舉例如下:
(1) 換熱器涂料 國內多采用環氧氨基、環氧酚醛、環氧呋喃等涂料,如TH847系列,以及漆酚鈦涂料,底漆2道、面漆4道。德國索卡酚和日本米通均為環氧、酚醛和有機硅的三元共混體系。
(2) 油罐內壁涂料 對水線下內壁多采用環氧煤瀝青、環氧富鋅、環氧酚醛或玻璃鱗片環氧涂料,目前多采用涂層與犧牲陽極聯合保護。
對水線上內壁多采用導靜電涂料,可采用環氧富鋅漆為底漆,以本征型或添加型填料的環氧防靜電漆為面漆。
對石腦油、航煤油罐應采用噴鋁加環氧或聚氨酯抗靜電封閉涂料。含油污水罐應采用環氧玻璃鋼內襯或環氧玻璃鱗片涂料。
(3) 油罐外壁涂料 要求涂料具有耐水、耐候、耐化學腐蝕和防濕熱、防鹽霧、防霉性能,可采用富鋅底漆、環氧云鐵中漆、丙烯酸、聚氨酯或氟碳面漆等。為隔熱降溫,可選用涼涼隔熱膠等,其組成為特種酮類改性環氧富鋅底膠、特種酮類改性云鐵中膠、改性丙烯酸酯類+稀土氧化物+多孔玻璃粉+TiO2顏料組成的面膠。
(4) 戶外鋼結構涂料 一般工業大氣的鋼結構可采用醇酸類涂料(底1、面2),對腐蝕嚴重需耐磨的平臺、樓梯,可采用聚氨酯或丙烯酸聚氨酯涂料(底1、面3);對環境特別惡劣又重要的戶外鋼結構可選用氟碳型涂料,一般常采用環氧富鋅底漆1道、環氧云鐵中漆1道、氟碳面漆2道,這三種涂料相互兼容結合良好,防腐性能佳,耐用壽命長。
(5) 地下管道涂料 常采用涂層與陰極保護相結合方法,其中涂層為環氧煤瀝青、聚氨酯瀝青、熔融環氧粉末涂料等。
(6) 鋼筋混凝土涂料 常采用氯化橡膠涂料、聚氨酯涂料。對水下環境宜采用環氧煤瀝青涂料。
(7) 綠色防腐涂料 由于傳統防腐涂料在施工過程中有溶劑揮發,會造成環境污染和資源浪費,為此開發了一些具有環境友好、使用安全的綠色防腐涂料。主要包括高固體分涂料、水性涂料、粉末涂料等。
高固體分涂料具有固含量高達85%,一次涂敷有較高膜厚,揮發成分少,涂層針孔少,抗滲透性好。
水性涂料以水做溶劑,具有干燥快、效率高、性能佳,且有大幅降低VOC排放、無毒無味、不燃特點。
粉末涂料具有無溶劑、無污染、涂膜機械強度高特點。此外納米涂料因有超細粒徑,故有較高的結合強度和抗滲耐蝕耐磨性能,以及涂膜表面耐洗刷與自潔性好。
施涂工藝
涂料的施工質量關系到施涂設備和管道的使用壽命。根據有關規定和實際經驗,施涂環境溫度宜為5~35℃,最佳施工溫度為5~25℃。相對濕度不宜大于85%,最好在60%以下。
被涂物表面溫度應比露點溫度高3℃。不應在風沙、雨雪天室外施工。對儲罐等容器內涂敷應使用除濕機進行通風和控制濕度。涂敷前涂料應過濾,并攪拌均勻。
施涂可采用刷涂、滾涂、空氣噴涂或高壓無氣噴涂。刷涂時層間應縱橫交錯往復進行,直到均勻為止。
噴涂時應控制合適的壓力和噴嘴與被涂表面距離。刷涂、滾涂、噴涂均應均勻,不得漏涂,如采用同一涂料進行多層涂刷時,宜將同一涂料調成不同顏色,可防止漏涂。
表面如有凹凸不平、焊縫波紋,應刮涂膩子,打磨平整,再涂底漆。設備和管件應在氣密或強度試驗合格后才進行涂敷,對焊縫區應預留,試驗后再作補涂。
5
涂裝質量的檢測和涂層鋼腐蝕的檢驗
為確保涂層鋼安全使用,避免過早腐蝕損壞,應嚴格進行表面處理控制和涂料施工控制,而必須按有關標準進行檢驗。
如美國鋼結構涂裝協會(SSPC)制定了幾十個涂裝體系標準和選擇導則,國際標準化組織(ISO)推出了ISO 12944鋼結構防護涂料系統的涂裝規格與工藝標準。
我國涂裝標準也參照有關國際標準。表面處理控制噴砂清理至少達到SSPC-SP10或ISO 8501-1或GB 8923-88標準Sa2.5級、清潔度要求高于ISO 8502-3規定的2級、表面可溶性鹽檢測參考ISO 8502-9。
涂料施工控制中,環境監控用濕度計和露點儀、涂層膜厚檢測用磁性檢測儀、涂層漏點檢測用電火花檢測儀等。
為研究涂層的保護性能,必須檢驗涂層鋼的腐蝕情況,通常采用電測方法。電測提供的數據對涂層壽命預測有一定參考意義。諸如DC檢測涂層的導電性和阻抗,在恒定頻率下測定等效AC電阻和耐蝕組分的電容比率、涂層的AC特性也用于估算透過涂層的吸水量。掃描技術有益于提供涂層的電性能。
放射性示蹤劑檢測水分子和鹽離子滲透或擴散性能尤為可取。絕緣技術可用于測定涂層的玻璃轉變溫度,以及測定涂層結構和組織,以便控制涂層的質量。
有人曾對涂層金屬進行腐蝕電位測定及其應用性研究,認為腐蝕電位移向正方向,表示陰極/陽極表面積比率增大,也表示氧和水通過涂層并到達金屬/涂層交界面。而腐蝕電位移向負方向,表示陽極/陰極表面積比率增大,發展為全面腐蝕。當正電位隨時間增大,由于氧還原反應在金屬涂層交界面局部發展,處于堿性狀態是有意義的。但當負電位不斷增大,表示在涂層下發生銹蝕,則表征涂層壽命受到限制。
免責聲明:本網站所轉載的文字、圖片與視頻資料版權歸原創作者所有,如果涉及侵權,請第一時間聯系本網刪除。
相關文章
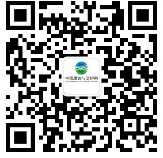
官方微信
《腐蝕與防護網電子期刊》征訂啟事
- 投稿聯系:編輯部
- 電話:010-62316606-806
- 郵箱:fsfhzy666@163.com
- 腐蝕與防護網官方QQ群:140808414
點擊排行
PPT新聞
“海洋金屬”——鈦合金在艦船的
點擊數:8148
腐蝕與“海上絲綢之路”
點擊數:6486