高強度鋁合金由于密度小、強度高、韌性和耐蝕性良好、可加工性及焊接性優良等綜合性能,在航空航天、機械和汽車制造業等領域得到了廣泛應用。多數高強度鋁合金材料需要通過熱處理獲得高強度與高韌性以滿足使用需求,而在熱處理強化過程中,快速的淬火冷卻使得材料內部形成巨大溫差,冷卻結束后在構件內部形成較大的殘余應力,在加工、儲存及長時間使用過程中會發生殘余應力的釋放與松弛,從而帶來零件的精度超差或尺寸不穩定等問題。目前降低與消除殘余應力的方法主要有:時效處理、振動時效、深冷處理、機械拉伸(壓縮)法等。
深冷處理過程也被稱上坡淬火或反淬火,按工藝可劃分為深冷急熱法與冷熱循環法,可廣泛用于鋁合金構件殘余應力的減小與控制。本文對國內外鋁合金深冷處理的研究與應用進行總結分析,討論了不同類型鋁合金工件深冷處理的工藝選擇和適用場合。
1.殘余應力的產生
工件在沒有外力的作用下內部存有的保持工件自身平衡的應力被稱為殘余應力。一般來講,鋁合金在淬火過程中不發生組織轉變,所以其構件殘余應力主要來自于淬火冷卻過程的熱應力,應力的演變過程如圖1所示。
熱應力是由于材料不同部位存在溫度差別而導致熱脹和(或)冷縮的不一致所引起的應力。對于2D內外兩層簡化模型,在淬火冷卻開始前(見圖1a),在長時間高溫條件下,材料內部溫度均勻,不存在熱應力;在淬火冷卻初期(見圖1b),鋁合金工件進入淬火冷卻介質后,由于金屬表面與淬火冷卻介質溫差很大,散熱很快,使得表層溫度下降很快,而內部依靠熱傳導方式散熱,溫度下降較慢,在表層與心部形成巨大溫度差。在熱脹冷縮的作用下,工件因溫度下降而體積收縮,表面溫度下降較多因而體積收縮較多,心部溫度下降較少因而體積收縮較少。因內外收縮量不同,相互發生作用力,此時表面因受到心部抵制收縮力而長大,所以此時外部受拉應力,心部受壓應力。在應力的作用下,心部金屬由于溫度較高、屈服強度較低,發生塑性變形,從而釋放一部分應力。
淬火冷卻第二階段(見圖1c),由于金屬表層溫度已經較低,與淬火冷卻介質熱交換較少,所以此時表層溫度下降速度放慢。而里層金屬與表層溫差較大,里層金屬溫度下降速度較表層快,使得表層收縮得少,心部收縮得多,內外層相互漲縮的牽制力減小,使得內應力減少,出現表層溫度低于心部,但內應力為零的情況。
隨著工件繼續冷卻(見圖1d),當金屬內部的溫度也降至較低溫度時,構件整體的抗變形能力提升,心部金屬溫度下降且產生相比表層金屬更大的收縮,而該收縮受到表層金屬的牽制,且整體無法產生塑性變形,內應力不會消減,此應力留在工件內部,最終造成工件表層受壓應力,心部受拉應力的殘余應力狀態。
圖1 2D簡化模型淬火過程應力演變示意
2.殘余應力對構件的影響
殘余應力的存在嚴重影響工件的加工精度與尺寸穩定性。
以2D簡化模型為例,淬火冷卻完成后,沿著中心線的殘余應力分布如圖2a所示,在中心區域為拉應力,外部為壓應力。當沿著中間線進行加工時,表層金屬被切除,這時原始的應力平衡受到破壞,在殘余應力的作用下加工面發生微小凹陷,同時部分應力被釋放,剩余的殘余應力重新分配并創造了新的平衡(見圖2b),加工面的凹陷宏觀表現為尺寸精度的降低。
(a)殘余應力分布示意 (b)殘余應力重新分配示意
圖2 殘余應力對加工精度的影響
同時殘余應力的變化是導致構件尺寸不穩定的重要原因。尺寸穩定性表示材料在熱處理與加工完畢后,在工作環境條件下,不受外力作用或在低于其彈性極限的應力作用下抵抗永久變形的能力。構件在儲存及長時間使用過程中會發生殘余應力松弛,使構件的尺寸形狀發生微小變化,從而導致尺寸不穩定,而構件形變量的大小取決于殘余應力值的大小。
3.鋁合金深冷處理技術的提出與發展
使用深冷處理進行鋁合金殘余應力的控制與消除可追溯到20世紀30年代,在早期使用中,通常將工件埋在干冰中,之后快速浸入100℃開水,由于當時缺乏系統、基礎的研究未能廣泛應用。直到20世紀50年代末,美國鋁業公司對鋁合金深冷處理技術開展了深入研究,應用了液氮與蒸汽分別作為冷卻與升溫介質并進行了公開報道,深冷處理技術開始廣泛應用于航空航天,國防和高精度成像系統中關鍵部件的殘余應力消除。同時,深冷處理技術經常用于具有關鍵公差的鋁合金部件的生產過程,比如光學試驗臺等在高精度環境中工作的組件。在Bodycote熱處理威斯敏斯特加州工廠,采用液氮和沸水對多種鍛鋁進行殘余應力的消除,該過程作為商業與軍用、航空等產品的一個特殊的工藝過程。2013年發布了鋁合金產品的深冷處理標準AMS2767《uphill quenching of aluminum alloyproduct》。
國內有關鋁合金深冷處理的研究工作開始于20 世紀90 年代末期,開展了很多工藝性研究,已經取得了比較重要的研究成果,并在鋁合金工件殘余應力消除與尺寸穩定化控制方面開展了應用,同時對鋁合金深冷處理的微觀機理也進行了一定的研究。
4.鋁合金深冷處理技術研究進展
從溫度變化與宏觀應力的變化趨勢來看,由于深冷處理過程中構件的狀態是從低溫快速升至高溫,與淬火過程相反,也被稱為反淬火,能夠產生與淬火相反的熱應力,所以理論上能夠創建一個新的應力狀態或分布,從而實現殘余應力的控制與消除。低溫與高溫之間溫度差越大,升溫速度越快,得到的反淬火應力越大,殘余應力消除的效果越明顯。因此,為了得到更大的溫差,目前深冷處理均采用液氮作為冷卻介質,而在升溫介質、溫度與使用環節方面存在一定差異。
在深冷處理環節方面主要分為以下兩種類型(見圖3):I在淬火后立刻進行深冷處理(見圖3a),處理次數1次或多次,之后進行時效強化;II在時效強化后進行深冷處理(見圖3b),處理次數1次或多次。
(a)淬火后深冷處理 (b)時效后深冷處理
圖3 深冷處理使用環節示意
國內外不同研究中所采用的升溫介質或設備差異較大,所得到的殘余應力消除效果也存在較大差異,如附表所示。其中采用高壓熱氣流進行快速整體升溫時殘余應力的消除率可達86%,但該方法需要設計制造專用供氣裝置與氣流噴射工裝(見圖4),且對于存在封閉內腔等結構產品并不適用。比較容易實現且投入較少的方式為采用開水和空氣爐進行加熱,殘余應力的消除率分別可達29%、40.7%;而采用高溫有機介質,相關研究表明其殘余應力的消除率可達58%,在實際使用過程中,為保證工件表面清潔,需增加清洗工序。
(a)
(b)
圖4 采用高壓熱氣流與液氮進行深冷處理的設備與工裝
不同深冷處理方式對不同材料殘余應力消除文獻數據統計
對于深冷處理消除淬火殘余應力的效果,相關研究指出:針對本身殘余應力較低的工件,如采用熱水或有機淬火液進行淬火的產品,深冷處理的效果會不太明顯。另外,也有研究結果表明,在時效強化后進行深冷處理(使用環節II),雖然殘余應力消除率不高,但對于尺寸穩定性依然有明顯的積極作用,可以在加工過程中進行,用來保證產品尺寸精度。
5.深冷處理工藝的缺點與不足
(1)價格相對昂貴與傳統的機械變形消除應力的方法相比,深冷處理過程價格相對昂貴,冷卻過程需要消耗大量的液氮,同時升溫過程需要專用設備、工裝與介質。
(2)產品對象受限 與其他消除殘余應力的方法一樣,深冷處理的應用同樣受限于產品對象的尺寸結構等因素。比如為達到最佳應力消除效果,需設計制造專用高壓熱氣流裝置,但對于一些結構復雜、尺寸較大的產品很難實現。
(3)應力消除效果受限前文提到為達到消除殘余應力的最佳效果,應在工件固溶后盡快進行深冷處理。而實際生產過程中,為了保證工件的尺寸精度,往往需要在固溶后進行人工或機械矯正、尺寸測量等工序,對于深冷處理的效果存在一定影響。
6.結語
國內外鋁合金深冷處理技術研究結果表明:
(1)深冷處理能夠有效減少鋁合金構件內部的殘余應力,提高尺寸穩定性。
(2)在鋁合金構件完成固溶處理后盡快進行液氮深冷處理,之后快速轉移至高溫熱氣流設備中進行上坡淬火,在此條件下殘余應力消除率最高,采用熱水或循環空氣電爐進行加熱效果次之。
(3)多次冷熱循環處理的效果普遍優于單次上坡淬火處理,一般推薦的次數為2~3次。
免責聲明:本網站所轉載的文字、圖片與視頻資料版權歸原創作者所有,如果涉及侵權,請第一時間聯系本網刪除。
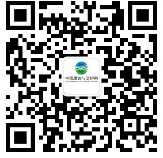
官方微信
《中國腐蝕與防護網電子期刊》征訂啟事
- 投稿聯系:編輯部
- 電話:010-62316606-806
- 郵箱:fsfhzy666@163.com
- 中國腐蝕與防護網官方QQ群:140808414