1 前言
流體作用下的金屬材料容易發(fā)生沖刷腐蝕。這種腐蝕在海洋環(huán)境及石油管道運(yùn)輸中十分常見(jiàn),其在工業(yè)磨損中所占比重大于5%[1]。沖刷腐蝕是金屬表面與腐蝕性流體之間由于高速相對(duì)運(yùn)動(dòng)而產(chǎn)生的金屬損壞現(xiàn)象,是沖刷磨損和電化學(xué)腐蝕交互作用的結(jié)果[2]。沖刷與腐蝕協(xié)同作用造成的金屬材料失重遠(yuǎn)大于沖刷和腐蝕單獨(dú)作用之和[3-8]。一般來(lái)說(shuō),機(jī)械磨損在金屬的沖刷腐蝕中占主要作用[9-12];而電化學(xué)腐蝕在整個(gè)沖刷腐蝕中發(fā)揮著重要作用[12-14]。
沖刷腐蝕是一個(gè)十分復(fù)雜的過(guò)程,影響腐蝕速率的因素有很多,主要包括:液體流速[5,15-17]、流體含沙量[3,5,15,16]、沙粒大小[15,16]、沖刷角[6,9,14,18]、流體pH值[18]、溶液溫度[16,17,19]、材料的組成[3,14]、材料的微觀結(jié)構(gòu)[4,20,21]和熱處理制度[22]等。
2 國(guó)內(nèi)外研究狀況
目前,國(guó)內(nèi)外學(xué)者對(duì)沖刷腐蝕進(jìn)行了較深入的研究,主要采用電化學(xué)測(cè)試手段及失重方法研究了不同流體力學(xué)條件、環(huán)境因素、材料性質(zhì)對(duì)金屬?zèng)_刷腐蝕的影響作用。丁一剛等[23]對(duì)國(guó)內(nèi)外液/固兩相流的沖刷腐蝕研究進(jìn)行了綜述,重點(diǎn)論述了沖刷腐蝕的影響規(guī)律及其危害性。近幾年來(lái),有研究者[24,25]開(kāi)始使用計(jì)算機(jī)建模的方法模擬沖刷腐蝕實(shí)驗(yàn),以期揭示流體力學(xué)因素對(duì)沖刷腐蝕的影響規(guī)律,從而找到減少流體中金屬?zèng)_刷腐蝕的方法。隨著金屬材料的研究開(kāi)發(fā),對(duì)金屬進(jìn)行表面改性處理以增強(qiáng)其抗沖刷腐蝕的性能成為沖刷腐蝕研究的趨勢(shì)[20,26,27]。
本論文主要對(duì)沖刷腐蝕機(jī)理、影響沖刷腐蝕的因素等進(jìn)行概括,并從元素含量、熱處理制度及金屬基復(fù)合材料發(fā)展等幾個(gè)方面綜述提高金屬材料防沖刷腐蝕性能的幾種方法,重點(diǎn)介紹沖刷腐蝕的國(guó)內(nèi)外最新研究進(jìn)展,為金屬?zèng)_刷腐蝕的研究與防護(hù)提供依據(jù)和幫助。
3 沖刷腐蝕的機(jī)理
3.1 沖刷腐蝕的組成
由機(jī)械磨損和電化學(xué)腐蝕的相互作用引起的金屬材料的腐蝕速率大于兩者單獨(dú)作用時(shí)的腐蝕速率之和[6,10]。研究[11,18]表明,沖刷腐蝕速率KEC可表示為:
其中,KC0和KE0分別為單獨(dú)的電化學(xué)腐蝕速率和沖刷磨損腐蝕速率,ΔKC和ΔKE分別為沖刷磨損對(duì)電化學(xué)腐蝕的加強(qiáng)及電化學(xué)腐蝕對(duì)沖刷磨損的增強(qiáng)部分。KC0可通過(guò)測(cè)定靜止溶液中金屬材料的腐蝕速率得到,KE0可通過(guò)測(cè)定電極施加陰極保護(hù)后的沖刷磨損速率得到[28,29];KC可通過(guò)極化曲線或者電化學(xué)阻抗譜 (EIS) 計(jì)算得到,最后求得ΔKE。式 (1) 可用于分析不同環(huán)境因素和材料性質(zhì)對(duì)沖刷腐蝕速率及機(jī)理的影響。鄭玉貴等[30,31]探討了沖刷磨損與電化學(xué)腐蝕交互作用規(guī)律、影響因素及沖刷引起的“腐蝕增量”和腐蝕引起的“沖刷增量”的產(chǎn)生機(jī)制。結(jié)果表明,沖刷磨損對(duì)電化學(xué)腐蝕的影響主要在于影響O2、腐蝕產(chǎn)物等的傳質(zhì)過(guò)程,同時(shí)使材料鈍化膜減薄、破裂,使材料發(fā)生變形,并形成沖蝕坑,從而加速電化學(xué)腐蝕。電化學(xué)腐蝕對(duì)沖刷磨損的作用主要表現(xiàn)在粗化電極表面,弱化材料的晶界、相界,使材料中耐磨的硬化相暴露,突出基體表面,從而促進(jìn)沖刷磨損。
3.2 沖刷腐蝕中的沖刷磨損部分
一般來(lái)說(shuō),機(jī)械磨損在金屬的沖刷腐蝕中占主要作用[9-12]。機(jī)械強(qiáng)度性質(zhì)是影響金屬材料沖刷磨損失重的最主要因素[11,12]。
Jana等[18]認(rèn)為沖刷磨損速率KE可表示為:
其中,c為沙含量,Ui為流體流速,EM為無(wú)因次侵蝕率。根據(jù)Finnie第一和第二模型[32]及沙粒的反彈效應(yīng),EM與以理想行為撞擊電極的沙粒百分含量、回彈系數(shù)、金屬材料的密度、硬度及沖刷角有關(guān)。
從式 (2) 可以看出,機(jī)械磨損主要受流體流速和溶液含沙量影響,并與沖刷角、沙粒及金屬的性質(zhì)有關(guān)系。然而,Meng等[10]和Hu等[33]發(fā)現(xiàn),流體速率較高時(shí)或者溶液中沙含量達(dá)到臨界值后,沖刷腐蝕速率并不隨流體流速及沙含量的增大而加劇。因此推測(cè),式 (2) 僅在流速較低、沙含量較小的條件下成立。
3.3 沖刷腐蝕中的電化學(xué)腐蝕部分
Neville等[13-15]使用電化學(xué)手段對(duì)液/固流體中合金的腐蝕和機(jī)械沖刷進(jìn)行了較深入的研究,結(jié)果表明電化學(xué)腐蝕在整個(gè)沖刷腐蝕中發(fā)揮著重要作用。電化學(xué)腐蝕一般包括金屬的溶解、鈍化、過(guò)鈍化及點(diǎn)蝕4個(gè)部分。本體溶液中,金屬的電化學(xué)腐蝕主要與溶液中腐蝕離子的種類及濃度、氧含量、溫度、pH值及金屬本身的性質(zhì)有關(guān)。流體中,除了以上因素影響金屬的電化學(xué)腐蝕外,由于流體對(duì)金屬表面基體及鈍化膜造成破壞,金屬的電化學(xué)腐蝕與流體流速、溶液中沙含量、沙粒大小、沖刷角等有關(guān)系。
Yu等[34]研究了Q235碳鋼在長(zhǎng)江水、黃河水和塔里木河水3種水體中的沖刷腐蝕行為。其中,塔里木河水由于Cl-,SO42-和HCO3-等腐蝕性離子含量遠(yuǎn)高于其它兩種水體,在其它條件不變的情況下,Q235鋼在塔里木河水溶液中的沖刷腐蝕總速率接近其在長(zhǎng)江水中沖刷腐蝕失重的兩倍。
流體力學(xué)因素對(duì)類似于不銹鋼的鈍化金屬的極化曲線影響較大,這與不銹鋼表面快速形成的附著力較強(qiáng)的鈍化膜有關(guān)。當(dāng)電極表面無(wú)鈍化膜形成時(shí),機(jī)械磨損對(duì)金屬材料的自腐蝕電位和電化學(xué)腐蝕速率影響較小。而對(duì)于能夠形成鈍化膜的金屬材料,在一定的腐蝕環(huán)境中發(fā)生機(jī)械磨損時(shí),鈍化膜因溶液中粒子高頻率的沖擊而受損;當(dāng)鈍化膜的破壞/再鈍化交替發(fā)生時(shí),電極表面的電化學(xué)反應(yīng)速率迅速增加,從而加速了不銹鋼的腐蝕速率[12,35]。Jiang等[36]研究不銹鋼在20%H2SO4溶液中的沖刷腐蝕時(shí)發(fā)現(xiàn),機(jī)械磨損使得其腐蝕電勢(shì)負(fù)移約400 mV,陽(yáng)極電流密度增大約兩個(gè)數(shù)量級(jí)。這一結(jié)果與Li等[37]研究不銹鋼在10%H2SO4溶液中鈍化電流密度隨溶液流速增加迅速升高的研究結(jié)論相吻合。與不銹鋼相比,低合金鋼的腐蝕速率則不易受流體沖刷的影響,主要因?yàn)榈秃亢辖痣y以形成致密的氧化膜[12]。
3.4 沖刷磨損與電化學(xué)腐蝕的相互作用
Stack等[38]分別研究了X52鋼在水溶液、80%油水混合液、油溶液中的沖刷腐蝕行為后,根據(jù)沖刷磨損與電化學(xué)腐蝕在整個(gè)沖刷腐蝕中的貢獻(xiàn)程度,將沖刷腐蝕機(jī)制分為以下4類:(1) KC/KE<0.1時(shí)為沖刷磨損控制,(2) 0.1≤KC/KE<1時(shí)為沖刷磨損-電化學(xué)混合控制,(3) 1≤KC/KE<10時(shí)為電化學(xué)-沖刷磨損混合控制,(4) KC/KE≥10時(shí)為電化學(xué)控制。
Stack等[38]的研究發(fā)現(xiàn),一定條件下,水溶液中沖刷腐蝕主要由電化學(xué)-沖刷磨損控制,在油水混合液中腐蝕主要由沖刷磨損-電化學(xué)控制,而在純?cè)腿芤褐袆t由沖刷磨損控制。這是由于Fe2+和Fe3+在油中的溶解度較小,油的比重增大時(shí),鋼的溶解受阻,電化學(xué)腐蝕過(guò)程受到抑制[16]。
流體沖刷加劇金屬電化學(xué)腐蝕主要包括兩方面[28]:(1) 增強(qiáng)了O2的傳質(zhì)過(guò)程,加速了鈍化金屬的鈍化或者再鈍化過(guò)程及非鈍化金屬的電化學(xué)腐蝕過(guò)程,促使金屬表面形成的腐蝕產(chǎn)物脫落,從而加速腐蝕;(2) 機(jī)械力作用于金屬電極表面,削薄或者破壞表面鈍化膜。此外,沖刷造成材料表面出現(xiàn)凸凹不平的沖蝕坑,增加了材料的比表面積,從而導(dǎo)致腐蝕加劇[31]。與靜態(tài)相比,動(dòng)態(tài)條件下X60鋼在10%H2SO4溶液中的陰極極化曲線多了一個(gè)斜率較小的“平臺(tái)段”,向溶液中充入N2除氧,該“平臺(tái)段”下移,流速增大平臺(tái)段上移[39]。動(dòng)態(tài)條件下,氧去極化成為一個(gè)主要的陰極過(guò)程。
腐蝕對(duì)沖刷的影響主要在于粗化材料表面,造成微湍流的形成,同時(shí)溶解掉材料表面的加工硬化層,降低其疲勞強(qiáng)度,從而促進(jìn)沖刷[31]。
4 沖刷腐蝕的研究裝置
實(shí)驗(yàn)室研究沖刷腐蝕的裝置主要有3類:旋轉(zhuǎn)圓盤 (柱) 電極 (RDE/RCE)[16,17,19,40-45],管路裝置[46,47]和噴射式裝置[6,9,13,35,38,48]。
一般來(lái)說(shuō),使用RDE和RCE研究水動(dòng)力流體條件對(duì)金屬?zèng)_刷腐蝕影響時(shí),旋轉(zhuǎn)圓盤或圓柱很難使得底部的沙粒全部均勻懸浮在溶液中,因此,實(shí)驗(yàn)中改變沙粒含量時(shí),腐蝕速率隨沙含量的變化不顯著;噴射式裝置則可以用于研究流體中固體粒子的機(jī)械撞擊對(duì)腐蝕的影響。RDE和RCE分別用于產(chǎn)生層流與湍流,當(dāng)旋轉(zhuǎn)速度夠高時(shí),RDE也可以產(chǎn)生過(guò)渡或者相對(duì)的湍流[16]。除了這3種裝置外,泥漿罐[49]、旋轉(zhuǎn)籠[50]以及Coriolis測(cè)試儀也可用于研究沖刷腐蝕。
鄭玉貴等[30,31]對(duì)研究沖刷腐蝕裝置的各類實(shí)驗(yàn)方法及設(shè)備的優(yōu)缺點(diǎn)進(jìn)行了總結(jié),認(rèn)為在實(shí)驗(yàn)室條件下,RDE裝置由于設(shè)備簡(jiǎn)單、價(jià)格低廉、測(cè)試用液量小 (一般可小于4 L)、實(shí)驗(yàn)周期短等優(yōu)點(diǎn)使用最為廣泛。此外,噴射式裝置由于可以精確控制沖擊液流的流速、沖刷角并可獲得很高的流速,使用也較為常見(jiàn)。管流裝置由于整套系統(tǒng)占據(jù)空間大,實(shí)驗(yàn)所需溶液量大,泵需要持續(xù)運(yùn)轉(zhuǎn),實(shí)驗(yàn)周期長(zhǎng),對(duì)閥門、管件以及密封的可靠性要求高,整套裝置的費(fèi)用和實(shí)驗(yàn)費(fèi)用均較高,較少使用。
5 沖刷腐蝕的研究方法
目前,國(guó)內(nèi)外研究沖刷腐蝕的方法主要分為兩大類:實(shí)驗(yàn)測(cè)試和數(shù)值模擬。
5.1 實(shí)驗(yàn)測(cè)試
實(shí)驗(yàn)測(cè)試研究主要包括:采用極化曲線[16,38,51]、循環(huán)極化曲線[52]、恒電位階躍 (Potentiostatic measurements)[33,53]、EIS[16,22,27,42,54]和電化學(xué)噪聲 (EN)[55]等電化學(xué)技術(shù)準(zhǔn)確測(cè)取金屬?zèng)_刷腐蝕過(guò)程中的腐蝕速率,使用掃描電鏡 (SEM)[8,54]、光學(xué)顯微鏡[8]、共焦激光掃描顯微鏡 (CLSM)[56]、透射電鏡 (TEM)[27,56,57]、X射線衍射 (XRD)[58]和X射線光電子能譜 (XPS)[56]等測(cè)試技術(shù)觀察腐蝕前后電極表面微觀結(jié)構(gòu)和成份變化;綜合上述方法的測(cè)試結(jié)果可判斷沖刷腐蝕的類型。此外,失重法[38,59]也廣泛地被用于定量地計(jì)算金屬的沖刷腐蝕總速率。這些方法可用于研究不同環(huán)境因素如流體條件、材料性質(zhì)等對(duì)低碳鋼、不銹鋼等材料沖刷腐蝕的影響。于福洲等[60]通過(guò)采用劃傷電極法來(lái)測(cè)定金屬的再鈍化動(dòng)力學(xué)參數(shù),從而發(fā)展了一種用于快速評(píng)價(jià)合金耐沖刷腐蝕性能的新方法。
5.2 數(shù)值模擬
在目前的沖刷腐蝕研究中,采用計(jì)算流體動(dòng)力學(xué) (CFD) 軟件進(jìn)行數(shù)值模擬,是使用最為廣泛的數(shù)值模擬方式。
通過(guò)模擬金屬材料在沖刷條件下的腐蝕進(jìn)行腐蝕機(jī)理研究,對(duì)流態(tài)進(jìn)行數(shù)值仿真模擬計(jì)算,可以減少實(shí)驗(yàn)和設(shè)計(jì)工作的盲目性和工作量,降低消耗并增加可靠度。Stack等[24,25,61,62]在此方面進(jìn)行了較深入的系統(tǒng)研究,將CFD軟件模擬技術(shù)和有限元技術(shù)用于模擬材料的失重從而評(píng)估不同參數(shù)對(duì)沖刷腐蝕過(guò)程的影響,繪制出Fe彎管上沖刷磨損控制的部位與電化學(xué)腐蝕占主導(dǎo)地位的部位圖[61]。
除采用CFD軟件外,部分研究者自主設(shè)計(jì)軟件,用來(lái)模擬沖刷腐蝕。林玉珍和雍興躍[63-68]等較早地采用數(shù)值計(jì)算與實(shí)驗(yàn)研究相結(jié)合的方法,通過(guò)確定不同流動(dòng)體系中不同流態(tài)的流體力學(xué)模型,在分析流動(dòng)腐蝕過(guò)程不同的動(dòng)力學(xué)主控因素及其在協(xié)同效應(yīng)中的相對(duì)影響程度的基礎(chǔ)上,建立流動(dòng)腐蝕動(dòng)力學(xué)模型,結(jié)合沖刷腐蝕實(shí)驗(yàn),研究了雙相不銹鋼、碳鋼在不同流動(dòng)體系下的沖刷腐蝕機(jī)理,結(jié)果發(fā)現(xiàn)模擬計(jì)算得到的腐蝕速率與實(shí)測(cè)值基本一致。此外,Zhang等[69]在沖刷腐蝕建模方面也做了一些工作。
6 影響金屬?zèng)_刷腐蝕的主要因素
6.1 流體環(huán)境對(duì)沖刷腐蝕的影響
流體環(huán)境中,金屬基體在靜態(tài)溶液中形成的表面氧化膜難以持續(xù)存在,腐蝕加劇[9,35]。流體對(duì)金屬?zèng)_刷腐蝕的影響主要表現(xiàn)為正應(yīng)力和剪切應(yīng)力的競(jìng)爭(zhēng)效應(yīng)。機(jī)械磨損、電化學(xué)腐蝕、以及兩者的協(xié)同作用主要決定于電解液、金屬本身的性質(zhì)和摩擦學(xué)條件[12]。
Meng等[10]研究了液體流速、沙含量及溫度對(duì)不銹鋼沖刷腐蝕行為的影響。實(shí)驗(yàn)發(fā)現(xiàn),水流速率和沙介質(zhì)對(duì)腐蝕速率的影響較大,溫度影響最小。Hussain等[70]認(rèn)為金屬表面的去鈍化及再鈍化過(guò)程與單位時(shí)間內(nèi)沙粒撞擊電極表面的動(dòng)力學(xué)總能量EK有關(guān)。
式中,N為沙粒單位時(shí)間內(nèi)撞擊電極表面的次數(shù),mav為沙粒的平均質(zhì)量,V為沙粒的運(yùn)動(dòng)速率。
6.1.1 流速對(duì)沖刷腐蝕的影響 在沖刷腐蝕過(guò)程中,流體流速發(fā)揮著重要的作用,其影響著傳質(zhì)過(guò)程尤其是腐蝕粒子Cl-的傳遞[10]。
流速對(duì)沖刷腐蝕的影響可分為3種情況[71]:(1) 流速較低且沒(méi)有誘發(fā)對(duì)流的情況下,傳質(zhì)主要由自然對(duì)流引起,金屬表面鈍化膜保護(hù)金屬免于嚴(yán)重的電化學(xué)腐蝕,金屬鈍化占主導(dǎo)地位,沖刷磨損相對(duì)較弱;電化學(xué)腐蝕在整個(gè)沖刷腐蝕過(guò)程中占主導(dǎo)地位,沖刷腐蝕主要受電化學(xué)腐蝕機(jī)制控制[54]。(2) 在中等流速時(shí),誘發(fā)的對(duì)流導(dǎo)致傳質(zhì)的增加,液體流動(dòng)引起的剪切力使得電極表面的鈍化膜不再穩(wěn)定,腐蝕速率迅速增大,此時(shí),沖刷磨損開(kāi)始占據(jù)主導(dǎo)作用。(3) 在更高的沖刷速率下,金屬表面難以形成有效的保護(hù)膜,腐蝕速率達(dá)到較高值,且不再發(fā)生變化,此時(shí)會(huì)產(chǎn)生機(jī)械流體效應(yīng),并且材料的損傷機(jī)制變得格外復(fù)雜。楊帆等[52]采用循環(huán)極化曲線檢測(cè)BFe30-1-1銅鎳合金在不同流速人工海水中電極表面鈍化膜的完整性時(shí)發(fā)現(xiàn),在低流速 (低于2 m/s) 或靜止條件下,材料表面存在較完整的保護(hù)膜,而高流速 (3 m/s) 下保護(hù)膜破裂。對(duì)于UNS S32654和UNS S31603兩種不銹鋼,臨界速度都在4~7 m/s之間[53]。低于臨界流速時(shí),電化學(xué)腐蝕在整個(gè)沖刷腐蝕過(guò)程中占主導(dǎo)地位,沖刷腐蝕主要受電化學(xué)腐蝕機(jī)制控制[54];高于臨界流速時(shí),金屬的沖刷腐蝕受電化學(xué)腐蝕與沖刷磨損機(jī)制控制。當(dāng)溶液流速增至7 m/s時(shí),電極表面會(huì)發(fā)生彈性變形并出現(xiàn)劃痕[53]。不同沖刷條件下,金屬的流速臨界值不同。高流速下沙粒撞擊的動(dòng)力學(xué)能量的增大及撞擊次數(shù)的增加,將產(chǎn)生較大的瞬態(tài)腐蝕電流。
吳成紅等[72]認(rèn)為增大流速也有其有益的一面,如增大流速可以減少腐蝕性物質(zhì)在金屬表面的累積,從而避免點(diǎn)蝕和縫隙腐蝕的發(fā)生。另外,增大流速可以改善鈍化劑或抑制劑通過(guò)流動(dòng)邊界層到達(dá)金屬表面的能力,從而促進(jìn)金屬的鈍化,起到抑制腐蝕,保護(hù)金屬基體的作用。
此外,Ruff等[73]總結(jié)了影響金屬機(jī)械磨損的因素,其中最主要的是含沙流體的流速;機(jī)械磨損隨流體的流速增大,以沙粒速率的平方或立方的速率加速磨損。在Bitter的模型[74]中,機(jī)械磨損正比于沙粒速率的平方。
6.1.2 沙含量的影響 流體中的沙粒加速了金屬的腐蝕。沙粒對(duì)電極表面氧化膜的沖擊破壞使得金屬裸露在流體中,或者沙粒沖擊電極表面使得氧化膜難以形成,導(dǎo)致電化學(xué)腐蝕及其與沖刷磨損的協(xié)同效應(yīng)部分對(duì)整個(gè)電極失重貢獻(xiàn)很大[15]。有研究[17,19,53]發(fā)現(xiàn),在不加沙的條件下,Al合金和不銹鋼的電化學(xué)腐蝕主要由O2的擴(kuò)散步驟控制,增大電極轉(zhuǎn)速,O2擴(kuò)散速率加快,電極表面形成氧化膜;在加沙條件下,電極轉(zhuǎn)速增大時(shí),合金的電化學(xué)腐蝕加劇。
沖刷腐蝕速率隨著溶液中沙含量的增加而上升[27]。Zhang等[9]在研究了乙二醇/水溶液體系中3003鋁合金的沖刷腐蝕后指出,隨著沙含量的增加,沖刷腐蝕總速率增大,其中機(jī)械磨損部分的失重增加較多,而電化學(xué)腐蝕部分基本不變。這一研究結(jié)果得到了Stack等[24]的證實(shí)。其采用CFD模型來(lái)模擬室溫下粒子濃度對(duì)90°彎管的沖刷腐蝕的影響,結(jié)果表明,隨著沙濃度的升高,電化學(xué)腐蝕在整個(gè)沖刷腐蝕的比重下降。
沖刷腐蝕程度并不隨著含沙量的升高而一直加劇。Meng等[10]和Hu等[33]研究了不銹鋼從鈍化態(tài)到偽鈍態(tài)的腐蝕轉(zhuǎn)換行為,并證明了沙含量臨界值的存在。在腐蝕體系由流體引發(fā)的電化學(xué)腐蝕到?jīng)_刷腐蝕的轉(zhuǎn)變中,沙含量及流體流速存在臨界值,表明電極表面在低含沙量和低流速下形成的鈍化膜消失[53]。Zheng等[75]認(rèn)為,溶液中沙含量在臨界值以下時(shí),沖刷腐蝕速率隨沙含量增大而加劇,當(dāng)沙含量高于臨界值時(shí),沖刷腐蝕速率達(dá)到穩(wěn)定,不再隨沙含量增大而增加。在Hu等[53]的研究中,臨界含沙量為60~100 mg/L;高于臨界值時(shí),兩種不銹鋼電流明顯增大,并且波動(dòng)頻率變大,這主要源于沖刷腐蝕由流體引發(fā)的電化學(xué)腐蝕機(jī)制轉(zhuǎn)換為沖刷腐蝕機(jī)制。含沙量低于60 mg/L時(shí),電流的上升主要源于電化學(xué)反應(yīng) (如點(diǎn)蝕的產(chǎn)生)。在含沙量為60~200 mg/L時(shí),沙粒對(duì)電極表面的撞擊有效地破壞了表面的氧化膜,導(dǎo)致電流上升。然而,Neville等[15]發(fā)現(xiàn)沙含量更高 (15%和20%,質(zhì)量分?jǐn)?shù)) 時(shí),合金由于沖刷腐蝕導(dǎo)致的失重下降,可能由于碰撞沙粒和反彈沙粒之間的相互干擾所致[72]。
6.1.3 沙粒大小對(duì)沖刷腐蝕的影響 沖刷腐蝕速率隨著溶液中沙含量及沙粒尺寸的增加而增大[11,16]。沙含量一定時(shí),沙粒尺寸的改變引起沙濃度的相應(yīng)變化[45]。沙粒粒徑較小 (<50 μm) 時(shí),電化學(xué)腐蝕占主導(dǎo)地位,沖刷腐蝕速率與沙粒的大小無(wú)關(guān);沙粒粒徑超過(guò)100 μm時(shí),這種無(wú)關(guān)性減弱[71],且金屬電化學(xué)行為表現(xiàn)為鈍化[45]。
Zheng等[75]研究了2.4%NaCl溶液中加入尺寸約6.6 μm的海泥對(duì)碳鋼沖刷腐蝕行為的影響。研究發(fā)現(xiàn),與尺寸38 μm的沙粒加劇沖刷腐蝕相比,溶液中海泥含量越高,金屬?zèng)_刷腐蝕失重反而越少,作者認(rèn)為由于海泥顆粒較小,粘附在電極表面起到了隔絕金屬與溶液的屏障作用。Luo等[76]研究沙粒尺寸對(duì)表面涂有涂料的合金在含沙的1%NaCl的自來(lái)水中的沖刷腐蝕行為的影響,發(fā)現(xiàn)了兩個(gè)臨界沙粒尺寸。沙粒尺寸低于第一個(gè)臨界直徑 (FCD,80 μm) 時(shí),材料的沖刷腐蝕失重隨沙粒尺寸增加變化不大。當(dāng)沙粒尺寸大于FCD小于第二個(gè)臨界直徑 (SCD,410 μm) 時(shí),沖刷腐蝕引起的失重隨沙粒尺寸增大呈指數(shù)增加。沙粒直徑大于FCD時(shí),沖刷腐蝕速率隨沙粒尺寸增大基本保持不變。作者認(rèn)為,沙粒的撞擊力與慣性力及粘滯阻力有關(guān),慣性力大小正比于沙粒直徑的立方,而粘滯阻力正比于沙粒直徑的平方,慣性力使得沙粒以原來(lái)的方向前進(jìn),粘滯阻力則阻礙沙粒前進(jìn)。因此,單個(gè)沙粒的有效撞擊力隨直徑增大而增加。能使金屬材料產(chǎn)生裂縫或者使填料脫離涂料的沙粒最小撞擊能對(duì)應(yīng)FCD。小沙粒則僅僅影響流體的密度和液體介質(zhì)的流動(dòng)狀態(tài)。
當(dāng)沙粒尺寸達(dá)到臨界值后,電極表面的沖刷磨損速率不會(huì)隨沙粒尺寸的增大而增大;可能的一種解釋為顆粒大的沙粒易發(fā)生碎裂,導(dǎo)致實(shí)際的撞擊能小于實(shí)驗(yàn)條件下理論的撞擊能[77]。沙粒濃度恒定時(shí),隨著沙粒尺寸減小,相鄰兩次撞擊的時(shí)間隨之變小,導(dǎo)致金屬的再氧化大大減小。而相鄰兩次撞擊之間的時(shí)間決定再鈍化速率,從而最終決定去鈍化速率[21]。
另外,沙粒本身的性質(zhì)也會(huì)影響金屬?zèng)_刷腐蝕速率。隨著電極材料硬度與沙粒硬度比值的增大,機(jī)械磨損速率迅速降低,而電化學(xué)腐蝕速率則與該硬度比值無(wú)關(guān)[12]。根據(jù)相關(guān)的磨損實(shí)驗(yàn)結(jié)果,要使得材料的耐磨性有較大的提高,材料硬度與磨料硬度的比值應(yīng)達(dá)到0.8以上[78]。
6.1.4 溫度的影響 流體溫度升高,一方面使得O2擴(kuò)散速率增大,金屬表面易于生成鈍化膜;另一方面,流體粘度降低,撞擊能增大,電極表面的損壞程度加劇,導(dǎo)致電荷轉(zhuǎn)移速率增大[53,79]。當(dāng)溫度從18 ℃升至50 ℃時(shí),海水的粘度從1.09×10-2 cm2/ s降低至0.451×10-2 cm2/s[53]。表明溫度較高時(shí),沙粒的運(yùn)動(dòng)受液體流動(dòng)的影響較小,導(dǎo)致更多的沙粒撞擊金屬表面。此外,溫度上升,熱力學(xué)驅(qū)動(dòng)力增大,金屬的反應(yīng)活性升高[10,53]。采用SEM觀察發(fā)現(xiàn),隨著溶液溫度上升,電極表面腐蝕區(qū)域范圍擴(kuò)大,裂縫和腐蝕點(diǎn)數(shù)目增多[35]。Tian等[16]研究石油運(yùn)輸過(guò)程中溫度對(duì)X65鋼腐蝕的影響發(fā)現(xiàn),X65鋼的自腐蝕電位隨溫度的上升而負(fù)移,且陽(yáng)極極化電流密度隨溫度增高而迅速增大,表明陽(yáng)極反應(yīng)速率明顯增大。
Ping等[80]研究了不同高溫環(huán)境對(duì)17-4PH不銹鋼在H2SO4介質(zhì)中沖刷腐蝕行為的影響。結(jié)果表明,隨著溫度的升高,17-4PH不銹鋼微觀結(jié)構(gòu)也隨之改變,460 ℃時(shí)17-4PH不銹鋼微觀結(jié)構(gòu)主要為馬氏體, 610 ℃則包括馬氏體和奧氏體。在溫度由400 ℃上升到610 ℃過(guò)程中,材料硬度先隨溫度升高而增大,460 ℃時(shí)達(dá)到最大值,此時(shí)具有最佳的抗沖刷腐蝕能力。此后,材料硬度隨溫度上升而降低。
6.1.5 沖刷角 (攻角) 的影響 含沙流體中,流體沖刷作用對(duì)沖刷磨損影響較大[81]。流體沖刷角對(duì)沖刷腐蝕的影響主要表現(xiàn)為剪切應(yīng)力和正應(yīng)力。剪切應(yīng)力通過(guò)削薄甚至移除鋼表面的氧化膜而增強(qiáng)沖刷腐蝕過(guò)程。正應(yīng)力則是通過(guò)撞擊或損傷電極表面而產(chǎn)生孔洞。沖刷角小于45°時(shí),剪切應(yīng)力占主導(dǎo)地位;大于45°時(shí),正應(yīng)力占主導(dǎo)地位[11]。
Tang等[11]發(fā)現(xiàn),沖刷角從30°增至45°時(shí),腐蝕速率隨沖刷角增大而增大,45°增至90°的過(guò)程中,沖刷腐蝕速率先隨沖刷角增大而降低,然后隨其增大而增大。邢建東等[78]研究了18-8不銹鋼和T8高碳鋼在含沙的低濃度H2SO4溶液流體中的沖刷腐蝕行為。結(jié)果表明,兩種鋼的沖刷腐蝕速率均在沖刷角為45°時(shí)達(dá)到最大。Sasaki等[82]研究發(fā)現(xiàn),沖刷角較小 (50°) 時(shí),易產(chǎn)生較粗糙的電極表面,與光滑的金屬表面相比,表面點(diǎn)蝕坑更深且直徑更小,因此粗糙表面更容易產(chǎn)生可以發(fā)展到正常生長(zhǎng)階段的點(diǎn)蝕坑,從而降低點(diǎn)蝕電勢(shì);沖刷角較大 (90°) 時(shí),更容易發(fā)生點(diǎn)蝕。
邢建東等[78]認(rèn)為金屬材料在攻角約為45°時(shí)沖刷腐蝕速率達(dá)到最大,其主要原因是材料在此角度下的機(jī)械磨損達(dá)到最大值,從而使腐蝕與磨損的交互作用也達(dá)到最大值。因此,對(duì)于在這一角度下使用的材料,應(yīng)注重提高其耐磨性。Heitz[83]研究發(fā)現(xiàn),在液/固雙相流沖刷腐蝕條件下,脆性材料沖刷腐蝕速率隨顆粒沖刷角度的增大而增加,最大沖蝕率發(fā)生在90°,這一研究結(jié)果得到了Zheng等[56]的證實(shí);延性材料則最大沖蝕率發(fā)生在攻角為15°~40°之間。
6.1.6 pH值、含氧量對(duì)沖刷腐蝕的影響 溶液的pH值不同,金屬的沖刷腐蝕速率也不同。這是由于表面生成膜的成分及其性質(zhì)不同所致。例如,在一定流速下當(dāng)溶液pH值降低到3.6,在銅鎳合金表面不能形成保護(hù)膜,耐沖刷能力降低。
有鈍化特性的金屬只有當(dāng)介質(zhì)中加入了足夠的氧化劑,才能產(chǎn)生鈍態(tài)。而不具有鈍化特性的金屬,O2的存在 (特別是在中性條件下) 將加速陽(yáng)極金屬的溶解。對(duì)銅合金而言,在脫氧的海水和淡水中,其腐蝕速率大為降低[72]。因此,在一定條件下O2的卷入會(huì)促進(jìn)腐蝕,而在另一些條件下則有可能促進(jìn)材料鈍化,減緩腐蝕[16]。
6.1.7 環(huán)境因子的協(xié)同作用 條件參數(shù)之間的相互作用關(guān)系是十分重要的[33,53]。Meng等[10]采用正交實(shí)驗(yàn)和方差分析方法定量研究了不同環(huán)境參數(shù)及其相互作用對(duì)材料總失重的影響,采用的三因素水平分別為實(shí)驗(yàn)溫度為20 和50 ℃,液體流速為7和20 m/s,沙含量為5×10-6和5×10-5 (質(zhì)量分?jǐn)?shù))。
在同時(shí)考慮溫度、流體速度和沙含量3個(gè)環(huán)境因素對(duì)材料沖刷腐蝕速率 (失重) 的影響時(shí),得到各環(huán)境因素對(duì)腐蝕速率的貢獻(xiàn)比重。例如,流速的貢獻(xiàn)比重如下:
其中,V(%) 表示流速的貢獻(xiàn)比重,SSV表示流速的影響,SSS為沙含量的影響,SST為溫度的影響,SSVS為液體流速與沙含量的協(xié)同影響,SSVT為水流速率與溫度的協(xié)同影響,SSTS為溫度和沙含量的協(xié)同影響,SSTVS為三者的協(xié)同影響。
其中,
WHV和WLV分別為8次實(shí)驗(yàn)高、低流速時(shí)的材料失重平均值,WG為8種實(shí)驗(yàn)條件下材料失重的平均值。同樣可以計(jì)算出其它6個(gè)環(huán)境因素的影響值。
運(yùn)用該模型計(jì)算得到對(duì)UNS S31603不銹鋼影響最大的環(huán)境因素為溶液流速,這與Luo等[76]的研究結(jié)果一致;然后是沙含量及其與溶液流速協(xié)同作用的影響;在高流速和高沙粒含量時(shí),沙含量與溶液流速協(xié)同作用較強(qiáng)。上述協(xié)同作用并不僅僅受某個(gè)因素影響,當(dāng)沒(méi)有足夠的撞擊動(dòng)力學(xué)能量時(shí),脆性粗糙面不能移動(dòng),所以推測(cè)兩者協(xié)同作用的迅速增加主要受臨界撞擊動(dòng)力學(xué)能量的影響。
7 沖刷腐蝕的防護(hù)
7.1 金屬元素含量及合金種類
7.1.1 元素含量 金屬中特定元素的存在及其含量會(huì)對(duì)金屬抗沖刷腐蝕能力產(chǎn)生很大的影響[53,84,85]。Meng等[10]研究發(fā)現(xiàn),UNS S32654鋼的耐沖刷腐蝕能力比UNS S31603鋼強(qiáng)。這主要由于兩種合金的元素含量不同 (表1),尤其是Cr,Mo和N的含量差異使得兩種合金抗電化學(xué)腐蝕能力不同,從而使得耐沖刷腐蝕能力存在差異。Hu等[53]認(rèn)為金屬中C,Mo和N的添加可減慢電極表面去鈍化時(shí)的溶解速率,因而表現(xiàn)出良好的再鈍化性能。在靜態(tài)海水溶液中,合金中Mo,N和Cr含量的升高對(duì)減小局部腐蝕有重要的作用。
表1 UNS S32654鋼和UNS S31603鋼中的元素組成[10]
研究[10,53,20,85-87]表明,合金中Mo,Ni和Cr等元素的含量對(duì)合金的抗沖刷腐蝕性能有較大的影響。
Wu等[88]研究含Mo不銹鋼在H2SO4中的沖刷腐蝕機(jī)理時(shí)發(fā)現(xiàn),Mo含量的增加能增強(qiáng)其抗電化學(xué)腐蝕及沖刷腐蝕能力。一方面,Mo與Cr具有相似的電子結(jié)構(gòu),金屬活性較低,難以與介質(zhì)形成復(fù)合物,同時(shí)阻礙了Fe與溶液中陰離子形成穩(wěn)定的化合物;另一方面,不銹鋼中Mo可消除電極表面的活性位點(diǎn),形成含MoO42-或者M(jìn)o10O4110-的鈍化膜或吸收腐蝕產(chǎn)物的膜,從而抑制點(diǎn)蝕的發(fā)生;此外,Mo含量的升高使得不銹鋼由單相奧氏體向奧氏體與富Mo鐵素體中間相轉(zhuǎn)變,顯微硬度增大,因而使得不銹鋼抗沖刷腐蝕性能增強(qiáng)。合金中Mo和Ni的存在可加強(qiáng)電極表面鈍化能力[53,85]。Ilevbare等[86]研究了不銹鋼合金中Mo對(duì)合金性能的影響,認(rèn)為Mo可能以鉬酸鹽的形式融入金屬的氧化膜中,改變了氧化膜的離子選擇性,使得Cl-難以通過(guò);同時(shí),Mo的存在可以增加電極表面鈍化膜的厚度。
在金屬基體中加入Cr后,由于形成更好的保護(hù)鈍化膜、碳化物和硬沉淀,合金的抗沖刷腐蝕能力增強(qiáng)[20]。Barker等[87]研究了不同Cr含量鋼的抗沖刷腐蝕能力,Cr含量8%以上的鋼普遍具有馬氏體、雙相和亞穩(wěn)奧氏體的混合結(jié)構(gòu),具有高加工硬化的潛力,有較強(qiáng)的抗沖刷腐蝕的能力。
Ni可以穩(wěn)定不銹鋼的奧氏體相進(jìn)而增強(qiáng)電極表面的鈍化能力[86]。王國(guó)華[89]通過(guò)對(duì)經(jīng)過(guò)950 ℃,60 min時(shí)效處理的S31803和S32750鋼的金相組織進(jìn)行觀察,發(fā)現(xiàn)含有22%Cr和3%Mo的S3180鋼組織為α+γ,未發(fā)現(xiàn)σ相的析出;含有25%Cr和4%Mo的S32750鋼組織除了α+γ,還有σ相。導(dǎo)致這樣的結(jié)果是因?yàn)樵陔p相不銹鋼中提高Cr和Mo等鐵素體形成元素的含量,既縮短了相形成的孕育期,同時(shí)提高了σ相穩(wěn)定存在的上限溫度。
7.1.2 合金種類 吳成紅等[72]將金屬的耐沖刷腐蝕性分為3類:(1) 金屬如鈦合金、鎳合金在整個(gè)實(shí)驗(yàn)流速范圍內(nèi)表面能形成致密的保護(hù)膜,有很好的抗沖刷能力;(2) 不銹鋼、鎳鉻合金在高速和中速范圍內(nèi)表面形成保護(hù)膜,有很好的抗沖刷能力,但在低速下不形成保護(hù)膜,抗沖刷能力較差;(3) 銅合金在低速下有很好的抗沖刷性,但在高速和中速下,其保護(hù)膜易被沖刷破壞。因此,針對(duì)不同的環(huán)境,選擇不同的金屬材料,可以減緩沖刷腐蝕。
7.2 熱處理制度 (微觀結(jié)構(gòu))
7.2.1 σ相 鋼中γ相具有韌性好、形變強(qiáng)化能力高等特點(diǎn),α相硬度也較低,σ相卻具有較脆、硬度較高的特點(diǎn)。金屬的耐磨性與硬度有很大的相關(guān)性[56]。雙相不銹鋼的溫度和熱處理時(shí)間會(huì)對(duì)鋼中σ相的析出產(chǎn)生重要的影響[89]。研究人員通過(guò)對(duì)經(jīng)850 ℃不同熱處理時(shí)間的S31803雙相不銹鋼試樣進(jìn)行金相分析,發(fā)現(xiàn)時(shí)效初期5 min內(nèi)沒(méi)有σ相析出,隨著時(shí)效時(shí)間的延長(zhǎng),σ相的體積分?jǐn)?shù)升高,但析出速率逐漸減小。脆性σ相的析出,降低了雙相不銹鋼的塑性、韌性以及耐蝕性。
然而,耐蝕性和耐磨性很多情況下都是矛盾的[90]。Zheng等[91,92]的研究發(fā)現(xiàn),由于σ相硬度較高,且與金屬基體電化學(xué)性質(zhì)接近,可以增強(qiáng)不銹鋼的抗沖刷腐蝕性能。兩種σ相增強(qiáng)的S1和S2不銹鋼 (熱處理溫度和時(shí)間分別為850 ℃,5 h和950 ℃,8 h) 在10%H2SO4 (質(zhì)量分?jǐn)?shù)) 和15%含沙量及不同流速條件下沖刷72 h后發(fā)現(xiàn),與316不銹鋼相比,含較少量及較小尺寸σ相的S1鋼僅在低流速時(shí)有較強(qiáng)的抗沖刷磨損性能,而σ相含量較高且尺寸較大的S2鋼在所有流速下皆表現(xiàn)出較強(qiáng)的抗沖刷磨損性能。在沖刷磨損占主導(dǎo)地位的情況下,較小的沖刷磨損在很大程度上決定了材料具有較低的沖刷腐蝕總速率。
此外,材料的凝固速率能在很大程度上影響鋼的主要組成元素在γ相與σ相之間的分布,進(jìn)而影響其抗沖刷腐蝕性能[28]。
7.2.2 非晶態(tài)合金 電化學(xué)腐蝕弱化材料的晶界、相界,使材料中耐磨的硬化相暴露、突出基體表面,使之易折斷甚至脫落,促進(jìn)沖刷[31]。金屬的非晶態(tài)不存在明顯的晶界,有較高的硬度,金屬表面噴涂無(wú)定型態(tài)金屬能增強(qiáng)其在一定條件下的耐沖刷腐蝕性能[56,57]。急冷處理產(chǎn)生的驟冷合金相,因未能充分進(jìn)行有序向無(wú)序轉(zhuǎn)化,會(huì)凍結(jié)在按組成比形成置換式統(tǒng)計(jì)原子的無(wú)序狀態(tài),而形成非晶態(tài)合金。
Zheng等[56]采用高速氧燃熱噴涂技術(shù)在304不銹鋼表面噴涂Fe54.2Cr18.3Mo13.7Mn2.0W6.0B3.3C1.1Si1.4非晶態(tài)合金 (AMC),并對(duì)比了該涂層與304不銹鋼在含沙的3.5%NaCl溶液中的沖刷腐蝕行為。研究表明,AMC在高流速?zèng)_刷條件下形成的鈍化膜保護(hù)性能比304不銹鋼更好。雖然304不銹鋼的耐均勻腐蝕性能優(yōu)于AMC,但是AMC抗點(diǎn)蝕能力遠(yuǎn)高于304不銹鋼,其抗沖刷腐蝕性能更強(qiáng),適合用于含Cl-較高的海水泵的沖刷腐蝕防護(hù)中。并認(rèn)為,由于304不銹鋼為晶體結(jié)構(gòu),晶界和相界首先發(fā)生腐蝕,引起表面顆粒和相的凸出,沙粒撞擊電極表面將導(dǎo)致顆粒和相脫落。
7.3 硬質(zhì)顆粒摻雜
陶瓷具有較高的硬度、耐磨、耐蝕、耐熱和抗高溫氧化性能,因此,合金中摻雜陶瓷粒子可以大大改善其耐磨損性能。硬質(zhì)顆粒WC及TiC 作為硬質(zhì)相摻入合金中使用較多,TiN 也有一些研究[93]。不同的硬質(zhì)相在合金中表現(xiàn)出不同的性質(zhì)。WC顆粒具有高強(qiáng)度、高潤(rùn)濕性能和低熱膨脹系數(shù)[94],與鐵基金屬的潤(rùn)濕角為零,且與其它金屬陶瓷顆粒(如TiC 等)相比易于獲得,是目前廣泛摻雜的粒子之一[95]。金屬基體表面涂覆摻雜WC的合金涂層可大大改善金屬基體耐沖刷腐蝕的能力[20]。WC顆粒可通過(guò)鑄造、燒結(jié)等方法獲得[95]。基體一般選擇相對(duì)較軟的金屬材料,能保證較高的耐蝕性、良好的沖擊韌性和斷裂韌性[30]。
7.3.1 硬質(zhì)顆粒摻雜對(duì)合金抗沖刷腐蝕能力的影響 Xu等[27]使用表面處理技術(shù)將納米粒子SiO2和SiC摻雜在鎳合金中,通過(guò)SEM觀察摻雜的兩種粒子對(duì)鎳合金微觀結(jié)構(gòu)的影響,發(fā)現(xiàn)呈球狀的SiO2均勻地分布在鎳合金的奧氏體基體中,未與基體發(fā)生界面反應(yīng),處于化學(xué)惰性狀態(tài)。而SiC則呈稍大的球狀及較小的條狀顆粒分布在晶界以及Ni的合金點(diǎn)陣中。在流速為3.45 m/s的3.5%NaCl溶液中沖刷一段時(shí)間后,發(fā)現(xiàn)316不銹鋼失重質(zhì)量是摻雜SiO2的鎳合金的7倍;摻雜SiO2合金表面僅有少量的點(diǎn)蝕坑,無(wú)裂縫或孔洞,其抗沖刷腐蝕能力最強(qiáng)。合金中納米粒子SiO2和SiC的摻雜可填補(bǔ)合金微觀結(jié)構(gòu)中的裂縫、溝及孔洞,同時(shí)由于納米粒子能作為隔離缺陷、腐蝕萌生及擴(kuò)大的物理屏障,摻雜后能增強(qiáng)合金的抗沖刷腐蝕能力。在流體中,納米粒子SiO2由于與鎳合金點(diǎn)陣鍵能較大,從而可以抵抗沙粒撞擊時(shí)的“微觀切斷效應(yīng) (micro-cutting)”。
Neville等[15]研究發(fā)現(xiàn)溶液中沙粒粒徑較大時(shí),金屬基復(fù)合材料抗沖刷腐蝕能力不一定優(yōu)于不銹鋼。含WC顆粒的鎳合金與UNS S31603不銹鋼的失重比在沙粒粒徑比較大時(shí)約為2.8,而在沙粒粒徑比較小時(shí)為0.6。觀察兩種沙粒的微觀結(jié)構(gòu)發(fā)現(xiàn),粗沙比細(xì)沙形狀更接近球形。細(xì)沙既可以劃傷單獨(dú)的WC顆粒,也可能撞擊基體 (摻雜顆粒的粘合劑)。細(xì)沙顆粒劃傷基體粘合劑相,WC顆粒抑制劃痕的擴(kuò)展,起到保護(hù)作用。粗沙在材料表面留下的劃痕較細(xì)沙大,并且可以同時(shí)傷害金屬基復(fù)合材料 (MMCs) 表面的兩相 (WC顆粒和基體相),WC顆粒起不到抑制劃痕發(fā)展的作用。與MMCs不同的是,UNS S31603不銹鋼不含硬質(zhì)相,微觀結(jié)構(gòu)主要為奧氏體,依靠晶界給材料提供保護(hù)力。當(dāng)不銹鋼在粗沙流體中沖刷腐蝕時(shí),晶界為顆粒提供支撐,從而使材料強(qiáng)度提高,不會(huì)發(fā)生過(guò)于嚴(yán)重的腐蝕。此外,不銹鋼在粗沙撞擊時(shí)表現(xiàn)出較好的抗沖刷腐蝕的另一個(gè)原因是,粗沙粒撞擊下不銹鋼表面附近顯微硬度變大,而在使用細(xì)沙撞擊時(shí)并無(wú)此發(fā)現(xiàn)。Levin等[96]研究發(fā)現(xiàn),沖刷撞擊后,沖刷磨損表面下的材料會(huì)經(jīng)歷彈性變形,距表面一定距離地方的顯微硬度會(huì)增強(qiáng)。
此外,溫度較高時(shí),因?yàn)殡娀瘜W(xué)腐蝕作用,基體相的相對(duì)較快腐蝕導(dǎo)致WC顆粒不受保護(hù),使金屬腐蝕加劇[20]。
然而,Zheng等[91]指出,硬質(zhì)顆粒摻雜并非適合于所有合金。碳化物與基體較大的電化學(xué)性質(zhì)差異將導(dǎo)致較嚴(yán)重的相界晶間腐蝕,因而不適合用于強(qiáng)腐蝕性的介質(zhì)中。
7.3.2 影響金屬基復(fù)合材料抗沖刷磨損的因素 金屬基復(fù)合材料抗沖刷磨損能力主要取決于材料的點(diǎn)陣韌性和材料中增強(qiáng)粒子的硬度,并與硬質(zhì)相 (增強(qiáng)粒子) 的體積分?jǐn)?shù)、尺寸和分布有關(guān)[26,94]。陶瓷粒子的獨(dú)特性能使得金屬基復(fù)合材料成為沖刷腐蝕環(huán)境下的良好選擇[26,97]。設(shè)計(jì)金屬基陶瓷顆粒摻雜材料的一個(gè)重要步驟是確定陶瓷顆粒之間的最佳平均自由程[26]。Cooper等[98]認(rèn)為平均自由程較大時(shí),材料強(qiáng)度變小;因?yàn)殡S著基體層變厚,陶瓷顆粒之間失去接觸,強(qiáng)度取決于基體本身的微觀結(jié)構(gòu)。就抗沙粒磨損性能而言,硬質(zhì)顆粒對(duì)粘結(jié)金屬的“陰影保護(hù)效應(yīng)”理論認(rèn)為,金屬陶瓷的抗磨粒磨損性能決定于復(fù)合層的硬質(zhì)陶瓷顆粒間的距離。距離越小,則陶瓷相對(duì)粘結(jié)相的保護(hù)效應(yīng)就越強(qiáng),復(fù)合層越耐磨。然而,陶瓷相含量并非越高越好。因?yàn)檫^(guò)高的陶瓷相含量將降低陶瓷相顆粒與基體的結(jié)合強(qiáng)度,易于造成陶瓷相的剝落而失效。因此,針對(duì)各種技術(shù)工藝和使用情況,陶瓷相有其最佳含量[95]。
陶瓷顆粒尺寸對(duì)材料耐磨性也會(huì)產(chǎn)生重要影響。對(duì)摻雜WC硬質(zhì)顆粒的合金而言,一般認(rèn)為,在松散硬質(zhì)磨料中,WC硬質(zhì)合金的耐磨性隨WC顆粒尺寸的減小而增加;而對(duì)于承受沖擊載荷、對(duì)抗壓強(qiáng)度要求高的各類工具,則一般選用韌性較好的粗顆粒[95]。此外,為了增強(qiáng)涂層的耐磨性能,可采用大小顆粒搭配使用的方法來(lái)減少硬質(zhì)相的間距,加強(qiáng)大顆粒WC之間 (粘結(jié)金屬) 的耐磨性,避免沙粒將基體磨損后又將硬質(zhì)相撞出。在WC硬質(zhì)合金的制備過(guò)程中,若WC顆粒燒損程度較低,則可盡量保持WC顆粒原始形貌,從而有效提高材料的耐磨性能,Xu等[27]的研究結(jié)果證實(shí)了這一點(diǎn)。
8 展望
(1) CFD軟件建模。通過(guò)實(shí)驗(yàn)數(shù)據(jù),建立系統(tǒng)的數(shù)據(jù)庫(kù),用統(tǒng)計(jì)的方法進(jìn)行數(shù)據(jù)分析,可為未來(lái)沖刷腐蝕模型的建立提供指導(dǎo)方向,可以更加清楚地理解流速、沙含量以及溫度等因素對(duì)合金腐蝕性能的影響。
(2) 新的測(cè)試方法的使用。傳統(tǒng)沖刷腐蝕主要采用失重、極化曲線和EIS等方法研究環(huán)境因素對(duì)沖刷腐蝕的影響。有研究表明,聲發(fā)射可測(cè)取材料局部腐蝕產(chǎn)生的超聲彈性波,是研究高低溫下腐蝕現(xiàn)象的強(qiáng)有力工具[71],預(yù)計(jì)能給出沙粒撞擊頻率和能量分布。根據(jù)聲發(fā)射活動(dòng)的強(qiáng)弱可以判斷腐蝕的快慢。此外,可以使用先進(jìn)的顯微技術(shù)來(lái)研究沖刷腐蝕過(guò)程中材料力學(xué)性能的變化,構(gòu)建不同變量之間的函數(shù)關(guān)系[38]。
(3) 耐沖刷腐蝕材料的發(fā)展。通過(guò)類似等離子噴焊 (PTA)、熱噴涂、激光堆焊等耐磨堆焊技術(shù),激光熔覆,鑄滲等手段向合金摻雜納米陶瓷顆粒,對(duì)材料表面進(jìn)行改性處理,提高基體的抗沖刷腐蝕能力[20,27,95]。此外,金屬表面噴涂添加了強(qiáng)化填充物的涂料,也可用于金屬?zèng)_刷腐蝕的防護(hù)[76,99]。其中,涂料對(duì)材料沖刷腐蝕防護(hù)性能的影響與加工處理的溫度及處理時(shí)間有關(guān)[99]。在實(shí)際沖刷腐蝕防護(hù)中,應(yīng)根據(jù)腐蝕環(huán)境、介質(zhì)性質(zhì)、溶液流速等,綜合考慮材料的耐蝕性和耐磨性,做出合適的選擇。
參考文獻(xiàn)
免責(zé)聲明:本網(wǎng)站所轉(zhuǎn)載的文字、圖片與視頻資料版權(quán)歸原創(chuàng)作者所有,如果涉及侵權(quán),請(qǐng)第一時(shí)間聯(lián)系本網(wǎng)刪除。
-
標(biāo)簽: 沖刷腐蝕, 機(jī)理, 環(huán)境因素
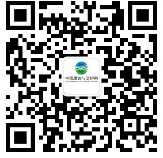
官方微信
《中國(guó)腐蝕與防護(hù)網(wǎng)電子期刊》征訂啟事
- 投稿聯(lián)系:編輯部
- 電話:010-62316606-806
- 郵箱:fsfhzy666@163.com
- 中國(guó)腐蝕與防護(hù)網(wǎng)官方QQ群:140808414