高溫爐管廣泛應用于制氫轉化爐和乙烯裂解爐,是石化裝置的核心構件。高溫爐管在其服役過程中的環境極其惡劣,長時間受到高溫和應力的作用極易產生損傷,導致高溫爐管的強度和穩定性急劇下降。蠕變損傷是高溫爐管主要的損傷形式之一,隨著服役時間的累積以及因操作不當而引起局部超溫或因開停車而受到熱應力的作用,容易產生蠕變開裂,當裂紋達到一定尺寸時,爐管隨即破裂失效。單個的爐管意外破裂后,其泄漏出來的高溫高壓氣體,往往會影響附近正在服役的其他爐管,造成連鎖反應。爐內任何一根爐管的損壞,均將導致整個裝置的緊急停車。除造成巨大的經濟損失外,還會引發火災、爆炸和人身傷亡等事故,安全隱患巨大。因此,開展高溫爐管開裂的定期檢測具有重要的意義。
考慮到高溫爐管材質的特殊性以及服役工況的復雜性,高溫爐管的在役檢測多通過超聲檢測方法來實現,但常規直接接觸式超聲檢測方法在檢測高溫爐管時,存在耦合效果較差,回波能量低,信噪比低等問題,不利于判斷爐管內裂紋特征?;诖耍袊胤N設備檢測研究院和北方華錦化學工業集團有限公司的檢測人員設計開發了一套水耦合超聲檢測方案,以加工有不同深度人工刻槽的HP40材質轉化爐用高溫爐管為檢測試件進行試驗,并結合現場某乙烯裂解爐爐管檢測數據,驗證水耦合超聲檢測方案檢測高溫爐管的可行性。
1 高溫爐管損傷機理及其檢測方法
01 高溫爐管的損傷機理和過程
高溫爐管的常用材料是HK和HP系列耐熱合金,常應用于制氫轉化爐爐管、乙烯裂解爐爐管。高溫爐管普遍服役于高溫(800~1200℃)和高壓(2.5~5MPa)的工況下,在高溫時效后耐熱合金的組織會發生變化,即使作用于材料的應力小于該溫度下的材料的屈服極限,也會產生塑性變形,即產生蠕變,最終引起爐管性能的衰退。蠕變損傷是高溫爐管主要的損傷形式之一,爐管蠕變取決于很多因素,主要受溫度、時間和應力大小的影響,內部超溫過熱、內外壁溫度梯度引起的熱應力及開停爐的內應力是引起蠕變損傷的直接原因。
根據應變率與時間的變化關系,蠕變一般分為蠕變初級階段、蠕變穩定階段和蠕變加速階段,在發展至蠕變穩定階段時,爐管一般需要停止使用。金屬材料在蠕變的過程中可以發生不同的斷裂形式,按斷裂時塑性變形量的大小,可以分為沿晶蠕變斷裂、穿晶蠕變斷裂和延縮性斷裂,材料抗蠕變的能力通常以蠕變溫度和蠕變強度來衡量。研究表明,爐管由于蠕變損傷而斷裂的特征表現為在小應力和高溫度作用下,在爐管金屬材料中晶粒之間的晶界處首先萌生空洞,隨著應力作用空洞不斷變大、變多,通過聚集和連接在爐管內壁產生大量微小的裂紋,微小裂紋進一步擴展會形成宏觀裂紋,并沿著爐管的徑向和軸向擴展,最終導致爐管斷裂失效。
以某煉油廠制氫轉化爐爐管為例, 其外徑為140mm,壁厚為13.5mm,工作壓力2.05MPa,正常工作溫度為800~900℃,超溫時可達1100℃,材質為HP型(ZG4Cr25Ni35Nb),工作介質為天然氣和水蒸氣。該轉化爐于2009年12月投用,共有爐管176根,設計壽命為10萬小時,累計運行4萬小時后,于2016年1月連續發生兩次爆管事故,兩根爐管開裂的宏觀形貌和局部放大如圖1所示,可以看到爐管的開裂均為縱向開裂,開裂部位已蠕脹鼓包,縱向主裂紋邊緣區及其前端分布有多條粗細、長短不均的小裂紋。
(a) 宏觀形貌 (b) 局部放大
圖1 遼寧某煉油廠制氫轉化爐爐管開裂形貌
對宏觀裂紋前端的爐管截面進行解剖分析,發現裂紋主要萌生于爐管內表層并沿壁厚方向向外壁擴展,部分裂紋已貫穿,如圖2所示。
圖2 遼寧某煉油廠制氫轉化爐爐管開裂解剖
02 檢測方法
考慮到材質的特殊性以及服役工況的復雜性,高溫爐管內壁裂紋的常規檢測方法存在以下難點:
1. 考慮到爐管材質為非鐵磁性且裂紋由內壁產生,因此不適合采用磁粉、滲透、渦流等表面檢測方法;
2. 考慮到爐管內部填充了催化劑,因此不適合采用射線檢測方法;
3. 高溫爐管的在役檢測多通過超聲檢測方法來實現,但是爐管的外表面多呈楊梅粒子狀態,且直徑較小曲率較大,耦合效果較差,回波能量低,信噪比低,因此常規直接接觸式超聲檢測方法在檢測時不利于判斷爐管內裂紋特征。
基于上述情況,為克服常規直接接觸式超聲檢測方法聲耦合效果差等問題,檢測人員提出了一種水耦合超聲檢測方案,實現爐管蠕變裂紋的檢測。
2 水耦合超聲檢測方案設計
本方案采用一對“超聲波發射/接收探頭”對高溫爐管進行水耦合穿透法檢測,如圖3所示。將探頭用水徑向(相對于爐管軸線)耦合在爐管上,發射探頭發出的超聲波波束進入水層中并在水/鋼界面發生反射和折射,折射的聲波以一定的角度在爐管中傳播并在鋼/水界面再次發生反射和折射,折射的聲波再次通過水層最終被接收探頭接收。當爐管內無缺陷時,發射探頭發出的超聲波經爐管內傳播后,直接被接收探頭接收,接收的能量如圖4a所示;當發射探頭發出的超聲波遇到爐管內裂紋的阻礙時,接收探頭接收到的超聲波能量會降低甚至完全消失,如圖4b所示。因此,通過對比接收探頭接收到的能量大小,可以初步判斷爐管內是否存在裂紋,以及裂紋在壁厚方向的高度。
圖3 水耦合超聲檢測方案設計
(a) 無缺陷阻礙時的接收能量 (b) 有缺陷阻礙時的接收能量
圖4 超聲波能量圖
本設計方案中,實現爐管的水耦合超聲檢測需要解決聲波入射角度的計算、探頭的固定、充水耦合等問題,超聲波信號的發射、接收、模數轉換、顯示、數據分析模塊可以利用現有的超聲檢測儀器實現。下面以管外徑R=109mm,管壁厚T=10mm,管內徑r=89mm 爐管為例,給出具體實施方案。
探頭固定裝置(瓦塊)的設計
設計的探頭固定裝置為“瓦塊”,用來保證超聲波能以一定的角度和路徑在爐管中傳播。瓦塊弧面內徑為109mm,與爐管外徑一致,瓦塊中部鉆有兩“探頭孔”,用以固定超聲探頭,孔內徑略大于探頭外徑。“探頭孔”的加工要求對稱性良好,以免造成耦合不佳或入射角偏移。瓦塊中水層的深度需要滿足探頭聚焦的要求。瓦塊的結構設計和實物如圖5所示。
(a)瓦塊結構設計圖
(b)瓦塊實物圖
圖5 探頭固定裝置(瓦塊)
進/出水裝置的設計
為了將聲波能量從超聲探頭傳遞至爐管內部,實際檢測時需要在探頭和爐管之間充水作為耦合劑。由于高溫爐管一般為立式安裝,水在重力的作用下向下流失,會影響甚至完全阻礙超聲能量的傳播。
為克服上述困難,將進水口設計在瓦塊的底部,出水口設計在瓦塊中部“探頭孔”的兩側。正常工作時,水在高處重力的作用下,自瓦塊底部流入,從瓦塊中部“探頭孔”流出,并與爐管之間形成耦合水層。當水壓較低時,水會在瓦塊底部和側面流出,此時的耦合效果較差;當水壓足夠時,水會在瓦塊的底部、側面和頂部同時溢出,此時的耦合效果能滿足現場檢測的要求。
(a)示意圖
(b)實物圖
圖6 進/出水裝置
聚焦深度與入射角度的計算
根據聲波振動方向與傳播方向的關系可以把聲波分為縱波和橫波。由于橫波無法在液體介質(水)中傳播,因此入射波選用縱波,傳播過程中的縱波,在兩種不同介質的界面處會發生一些相關的變化,如反射、折射和透射等,并伴隨著聲波的波形轉換,如圖7所示。
圖7 聲波的入射與折射
根據斯奈爾定律可知,入射縱波與法線的夾角,與折射縱波以及折射橫波與法線的夾角滿足以下公式:
為避免第二介質(爐管)中縱波與橫波的互相干擾,縱波入射角度應選在第一臨界角和第二臨界角之間,使得爐管中只存在橫波傳播,不存在縱波傳播。
已知爐管外徑R=109mm,內徑r=89mm,超聲波在水中的聲速CL1=1480m/s,超聲波在爐管中的橫波聲速CS2=3230m/s,聚焦深度(超聲波主聲束距離爐管內壁的距離)δ=5mm,則可計算得出縱波入射角度αL為24.59°。
3 試驗驗證
采用雙通道數字超聲波檢測儀,檢測試件采用刻有人工刻槽的HP40材質的轉化爐用高溫爐管,爐管規格為φ109mm×10mm,爐管內壁刻有5個人工縱向矩形刻槽,刻槽寬度為0.2mm,長度為20mm,深度分別為1.0、2.0、4.0、6.0、8.0mm,聚焦深度設計為5mm,刻槽示意圖和刻槽爐管試件水耦合超聲檢測裝置如圖8所示。
(a) 爐管刻槽示意圖 (b) 爐管試件水耦合超聲檢測裝置
圖8 刻槽爐管試件及檢測裝置
水耦合試驗
進水壓力的大小會影響超聲傳感器與爐管之間水耦合的效果,為驗證進水壓力與耦合效果之間的關系,分兩步進行試驗:
首先,不使用進/出水裝置,將爐管、瓦塊和探頭完全浸沒于水槽中,對爐管無缺陷部位進行檢測,如圖9a所示,得到的波形信號可以分為四部分,如圖9b所示。第一部分為“始波信號”,出現在屏幕左部,其特征是幅值極高,且由于檢測增益較大的緣故,其占寬較大。第二部分為“噪聲信號”,出現在屏幕中部,其特征是幅值很低且波形雜亂無規律;根據超聲波傳感器“一發一收”的設計方案,該部位對應聲波在爐管中傳播的聲程,此處尚未接收到超聲信號,但容易受到儀器板卡、信號線等外部噪聲的干擾。第三部分為管束內橫波以最短路徑傳播至接收探頭的“直通波”,是屏幕右部的第一個峰值信號;其特征是速度最快、能量最為集中,且峰值的大小與缺陷的關系最為密切。第四部分為管束內反射波、折射波、變形波等“遲到信號”,出現在屏幕右部;其特征是波形幅值無明顯規律,但均滯后于“直通波”。由工程經驗可知,此種耦合狀態下的“直通波”信號最強,此時將其調整為80%滿屏高并保持增益等檢測參數不變。
(a)浸沒示意圖
(b)波形信號
圖9 浸沒狀態下檢測試驗
然后,使用進/出水裝置,將爐管立于地面,瓦塊側貼于爐管表面,同時將水箱置于瓦塊上方不同的高度,利用重力供水耦合,如圖10a所示。以水位H=6m為例,得到的“直通波”波幅高度只有40%滿屏高,如圖10b所示。此時,調節水位H并記錄“直通波”波幅高度與不同水位之間的關系,結果發現:當水位在0.2~2m之間時,耦合效果與完全浸沒時一致,檢測效果較好;當水位超出或者低于這個范圍時,檢測結果均會受到影響。
(a)立式示意圖
(b)波形信號(水位6m)
圖10 立式水耦合狀態下檢測試驗
人工缺陷檢測試驗
連接檢測系統,將檢測水位固定為1m,設置無缺陷部位“直通波”為100%滿屏高并對5個人工縱向矩形刻槽進行檢測,可以看出“始波信號”和“噪聲信號”均無明顯變化,“直通波”隨著刻槽深度的增加而降低,“遲到信號”無明顯規律。
對接收探頭“直通波”信號的波幅高度進行均值統計,得到超聲波信號穿透不同深度的人工刻槽缺陷后的剩余能量和 “直通波”信號波幅高度衰減曲線,如圖11所示,可以看出“直通波”信號的剩余能量隨人工缺陷的深度的增加而遞減。根據“直通波”信號幅值的高低可推斷爐管蠕變裂紋的大致深度。
圖11 接收探頭超聲信號波幅高度衰減曲線
4 現場檢測應用
為了進一步驗證水耦合超聲檢測方案的應用性能,對某乙烯裂解爐爐管進行現場檢測試驗。根據現場爐管規格(φ114mm×14mm)和聚焦深度(7mm)加工探頭固定裝置(瓦塊)并配套電驅動裝置后,將“直通波”設置為100%滿屏高進行快速掃查,如圖12所示。
(a) 瓦塊及電驅動裝置
(b) 信號采集系統
圖12 現場檢測試驗
現場檢測發現,多數爐管的“直通波”在80%滿屏高以上波動,但某根爐管的某處“直通波”衰減至40%滿屏高,判定為疑似缺陷。對該部位割管后進行PT檢測,發現內壁為兩條裂紋,長度分別為20mm和7mm,均平行于軸線方向,如圖13所示。
圖13 疑似缺陷的PT驗證結果
從現場試驗數據可以看出,利用設計的水耦合超聲檢測方案能夠實現爐管內壁裂紋的檢測。
結論
為克服常規直接接觸式超聲檢測方法聲耦合效果差等問題,設計開發了一套水耦合超聲檢測方案,采用一對“穿透法”對高溫爐管進行水耦合超聲波透射法檢測。以加工有不同深度人工刻槽的HP40材質轉化爐用高溫爐管為檢測試件進行試驗,試驗得到了檢測信號隨裂紋深度的衰減規律,根據接收探頭“直通波”信號幅值的高低可初步推斷爐管管壁內蠕變裂紋的大致深度。結合現場某乙烯裂解爐爐管檢測數據,進一步驗證了水耦合超聲檢測方案的應用性能。
免責聲明:本網站所轉載的文字、圖片與視頻資料版權歸原創作者所有,如果涉及侵權,請第一時間聯系本網刪除。
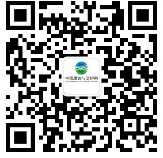
官方微信
《中國腐蝕與防護網電子期刊》征訂啟事
- 投稿聯系:編輯部
- 電話:010-62316606-806
- 郵箱:fsfhzy666@163.com
- 中國腐蝕與防護網官方QQ群:140808414