摘要
使用MPX-2000型摩擦磨損實(shí)驗(yàn)機(jī)對(duì)TC11合金在不同載荷和納米潤(rùn)滑材料條件下進(jìn)行摩擦磨損實(shí)驗(yàn)。使用SEM、EDS、XRD等手段對(duì)其磨損表面和剖面的形貌、成分、結(jié)構(gòu)進(jìn)行了對(duì)比觀察和分析。結(jié)果表明:將不同種類(lèi)的納米材料添加到摩擦副的滑動(dòng)界面,在TC11合金磨損表面均能形成納米顆粒摩擦層,摩擦層的穩(wěn)定性取決于其組成和各組分的含量。只含MLG的摩擦層因承載能力差而具有較低的穩(wěn)定性,極易破壞。只含F(xiàn)e2O3的摩擦層在低載時(shí)穩(wěn)定性較高,能減少磨損但是不能降低摩擦。同時(shí)含MLG和Fe2O3的雙層摩擦層兼具良好的潤(rùn)滑性和承載能力,穩(wěn)定性強(qiáng),使TC11合金的摩擦磨損性能顯著提高。添加富Fe2O3納米復(fù)合材料的雙層MLG/Fe2O3納米顆粒摩擦層具有更高的穩(wěn)定性,能更有效地提高鈦合金的摩擦學(xué)性能。
關(guān)鍵詞: 材料失效與保護(hù) ; 納米顆粒摩擦層 ; 摩擦磨損 ; TC11合金 ; 石墨烯 ; 穩(wěn)定性
金屬材料及其合金在滑動(dòng)摩擦磨損過(guò)程中,不可避免地在其表面生成一層摩擦層[1]。長(zhǎng)期以來(lái),人們一直認(rèn)為鈦合金耐磨性極差的主要原因是在滑動(dòng)過(guò)程中在表面生成了一層與滑動(dòng)金屬合金具有類(lèi)似性能的性摩擦層,沒(méi)有保護(hù)作用[2,3,4,5]。近年來(lái),國(guó)內(nèi)外一些研究人員在進(jìn)一步研究鈦合金干滑動(dòng)摩擦磨損性能時(shí)發(fā)現(xiàn),鈦合金并不總是具有較差的耐磨性[6,7,8,9,10,11]。在高溫和高速條件下在摩擦磨損過(guò)程中生成的摩擦氧化物,使摩擦層由金屬性為主變成以陶瓷性為主。這種摩擦層能有效避免金屬-金屬直接接觸,使其耐磨性顯著提高。
但是,這種以陶瓷性為主的摩擦層在常規(guī)條件下幾乎不能形成。這種摩擦層的形成消耗摩擦副基材,造成嚴(yán)重的浪費(fèi);更重要的是,這種陶瓷性質(zhì)的摩擦層能有效減少磨損但是并不總是同時(shí)降低摩擦。鑒于此,本文在摩擦副滑動(dòng)界面添加兼具減摩性和抗磨性的納米復(fù)合材料以在鈦合金表面形成功能性的納米顆粒摩擦層,研究這種摩擦層的穩(wěn)定性。
1 實(shí)驗(yàn)方法
1.1 試樣的制備
分別選取TC11鈦合金和GCr15鋼作為銷(xiāo)、盤(pán)材料。將TC11合金在955℃固溶處理30 min,然后在540℃時(shí)效處理2 h,其硬度為HRC 40~42。將GCr15鋼進(jìn)行淬火+回火熱處理,淬火溫度為850℃,保溫時(shí)間為25 min,冷卻介質(zhì)為油,回火溫度為400℃,保溫時(shí)間為2 h,冷卻介質(zhì)為空氣,最終其硬度為HRC 50~52。用線切割將銷(xiāo)、盤(pán)試樣分別加工成直徑為5 mm 長(zhǎng)度為22 mm和直徑為34 mm 厚度為10 mm的試樣。實(shí)驗(yàn)前依次用水砂紙(180#、360#)和金相砂紙(400#、600#)將其打磨,實(shí)驗(yàn)前后均需將其置于丙酮中超聲去油去污,吹干后用精度為10-5 g的電子天平稱(chēng)質(zhì)量。
用液相剝離法制備實(shí)驗(yàn)用納米材料,選取膨脹石墨、納米Fe2O3顆粒作為原料制備多層石墨烯(MLG)和MLG/Fe2O3復(fù)合納米材料。將膨脹石墨經(jīng)液相剝離后直接得MLG,若在其中添入納米Fe2O3顆粒,將其吸附到MLG的表面制得MLG/Fe2O3,具體制備過(guò)程如圖1所示。調(diào)節(jié)膨脹石墨和Fe2O3納米顆粒的質(zhì)量比,即可制得具有不同比例(1:2、1:1和2:1)的MLG/Fe2O3復(fù)合材料。
圖1 MLG和MLG/Fe2O3的制備過(guò)程
1.2 摩擦磨損實(shí)驗(yàn)
摩擦磨損實(shí)驗(yàn)在MPX-2000型銷(xiāo)-盤(pán)式摩擦磨損試驗(yàn)機(jī)上完成,參數(shù)如下:大氣、室溫環(huán)境,載荷為20~120 N,間隔20 N,轉(zhuǎn)速為0.5 m/s,滑動(dòng)距離為1.6×103 m,添加納米材料的量為0.3 g,添加納米材料的種類(lèi)包括單獨(dú)添加MLG、Fe2O3以及添加比例為1:2、1:1、2:1的MLG/Fe2O3復(fù)合材料。此外,還進(jìn)行無(wú)任何添加的摩擦磨損實(shí)驗(yàn)用于對(duì)比。滑動(dòng)實(shí)驗(yàn)開(kāi)始前將納米材料直接傾倒在滑動(dòng)界面上,并搖勻。為了防止納米材料的團(tuán)聚或?yàn)R出,對(duì)盤(pán)試樣進(jìn)行適當(dāng)改造,即在盤(pán)中央粘貼一塊圓柱形泡沫,并在盤(pán)周?chē)掣揭粚佑操|(zhì)膠帶,如圖2所示。
圖2 盤(pán)改造的示意圖
根據(jù)公式:W=ΔM/ρL計(jì)算磨損率(W),式中ΔM為磨損失重,ρ為合金密度,L為滑動(dòng)距離。使用試驗(yàn)機(jī)配套軟件每隔0.001 s讀出一個(gè)摩擦系數(shù)值,平均摩擦系數(shù)為所有值的平均數(shù)。在每種試驗(yàn)條件下進(jìn)行3 次,取3次試驗(yàn)數(shù)據(jù)的平均值為最終結(jié)果。
1.3 性能表征
使用D/Max-2500/pc型X射線衍射儀(XRD)分析磨面的物相,采用Cu靶的Kα射線,實(shí)驗(yàn)電流為200 mA、電壓為40 kV、掃描速度為8°/min、衍射角范圍為20~80°。用JSM-7001F型場(chǎng)發(fā)射掃描電子顯微鏡(SEM)觀察磨損表面、剖面的形貌。用SEM附帶的Inca Energy 350型能譜儀(EDS)分析磨面的化學(xué)成分。
2 結(jié)果和討論
2.1 微觀形貌
MLG、Fe2O3及MLG/Fe2O3復(fù)合材料的微觀形貌,如圖3所示。制備的MLG呈納米尺度上的層狀結(jié)構(gòu),石墨烯是多層的,幾乎是透明且皺褶的(圖3a)。在自然狀態(tài)下Fe2O3顆粒嚴(yán)重團(tuán)聚,使其形態(tài)難以區(qū)分(圖3b)。但是在MLG/Fe2O3復(fù)合材料中Fe2O3顆粒的團(tuán)聚程度明顯下降,紡錘狀的Fe2O3顆粒長(zhǎng)短軸方向的尺寸分別為30~70 nm和5~10 nm,均勻地分布在MLG表面(圖3c),表明Fe2O3納米顆粒已經(jīng)成功復(fù)合于MLG。
圖3 納米顆粒的微觀形貌
2.2 磨損率和摩擦系數(shù)
圖4給出了不同添加狀況下TC11合金隨載荷變化的磨損率。無(wú)任何添加時(shí),TC11合金的磨損率在全部載荷范圍內(nèi)呈線性增長(zhǎng)趨勢(shì)。在摩擦副滑動(dòng)界面上添加不同類(lèi)型的納米材料后,合金的磨損率顯著變化。單獨(dú)添加MLG時(shí),TC11合金磨損率隨載荷變化呈現(xiàn)出的線性增長(zhǎng)趨勢(shì)與未添加時(shí)的類(lèi)似,但是磨損率數(shù)值較高,且增長(zhǎng)較快。單獨(dú)添加Fe2O3納米顆粒時(shí),在載荷為20~60 N條件下磨損率為極低值,當(dāng)載荷高于60 N時(shí)磨損率急速上升,其值在單獨(dú)添加MLG與未添加時(shí)之間。添加不同比例的MLG/Fe2O3復(fù)合納米材料時(shí),TC11合金的磨損率在20~100 N內(nèi)始終保持為0。隨著載荷增大到120 N,對(duì)于比例為1:1和2:1的復(fù)合材料潤(rùn)滑劑磨損率快速升高,而添加MLG/Fe2O3(1:2)時(shí)TC11合金的磨損率仍為極低值。
圖4 使用不同納米潤(rùn)滑材料時(shí)TC11合金的磨損率與載荷的關(guān)系
圖5給出了未添加與添加不同類(lèi)型納米材料時(shí)TC11合金/GCr15鋼滑動(dòng)體系在不同載荷下的平均摩擦系數(shù)。未添加納米材料及單獨(dú)添加MLG、載荷為120 N時(shí),平均摩擦系數(shù)均較高,且數(shù)值相當(dāng)。單獨(dú)添加Fe2O3納米顆粒時(shí)平均摩擦系數(shù)在60 N條件下很高,在80 N時(shí)降低至略高于未添加及單獨(dú)添加MLG時(shí)的水平。添加不同比例的MLG/Fe2O3納米復(fù)合材料時(shí),平均摩擦系數(shù)發(fā)生顯著變化。在100 N下無(wú)論何種比例,平均摩擦系數(shù)均極低,載荷增大到120 N,除添加MLG/Fe2O3(1:2)時(shí)平均摩擦系數(shù)仍極低,在其余情況下開(kāi)始極快地增大。
圖5 在納米潤(rùn)滑材料和載荷不同的條件下滑動(dòng)體系的平均摩擦系數(shù)
比較不同添加狀況下的摩擦磨損行為,TC11合金具有較差的干滑動(dòng)摩擦磨損性能;單獨(dú)添加MLG其摩擦磨損性能不但沒(méi)有改善,反而更差。選擇Fe2O3納米顆粒作為潤(rùn)滑材料時(shí)低載條件下耐磨性有所提高,但是減摩性很差,在高載下與未添加及單獨(dú)MLG時(shí)相當(dāng)。但是,MLG/Fe2O3納米復(fù)合材料的人工引入可顯著改善鈦合金的摩擦磨損性能,在100 N高載下磨損率和摩擦系數(shù)均保持極低值,其中富Fe2O3納米潤(rùn)滑材料(1:2)使TC11合金在更高載荷下仍具有優(yōu)異的摩擦學(xué)性能。
2.3 磨損表面物相分析
圖6 給出了未添加與添加不同類(lèi)型納米材料時(shí)TC11合金在不同載荷下磨面的XRD分析結(jié)果。可以看出,未添加及單獨(dú)添加MLG納米材料時(shí),TC11合金的滑動(dòng)界面上除了Ti未出現(xiàn)其他物相。當(dāng)納米Fe2O3顆粒作為潤(rùn)滑材料時(shí),在60 N載荷下出現(xiàn)較強(qiáng)的Fe2O3衍射峰,當(dāng)載荷增大到80 N時(shí)Fe2O3的衍射峰消失,磨面上的物相幾乎全為金屬Ti(圖6a)。添加不同比例的MLG/Fe2O3納米復(fù)合材料時(shí)在100 N載荷下磨面上均出現(xiàn)了MLG和Fe2O3衍射峰,載荷增大至120 N時(shí)添加MLG/Fe2O3(1:2)的TC11合金磨面上仍由MLG和Fe2O3衍射峰,其他比例下衍射峰均消失(圖6b)。
圖6 在納米潤(rùn)滑材料和載荷不同的條件下TC11合金的磨面XRD圖譜
結(jié)合上述TC11合金的摩擦磨損行為,磨面上的Fe2O3氧化物可有效阻止摩擦副材料之間的直接接觸,顯著降低了鈦合金的磨損率,改善了其耐磨性,但是減摩性較差。而當(dāng)磨面上Fe2O3和MLG同時(shí)存在時(shí)磨損率和摩擦系數(shù)均保持極低值,TC11合金的摩擦與磨損性能都明顯改善,且發(fā)生輕微-嚴(yán)重磨損轉(zhuǎn)變的臨界載荷也比單獨(dú)添加Fe2O3時(shí)的高。特別是添加MLG/Fe2O3(1:2)時(shí),即使在120 N高載下磨面上仍同時(shí)存在Fe2O3和MLG,這與磨損率和摩擦系數(shù)相符。
2.4 磨損表面的形貌
圖7給出了未添加與添加不同類(lèi)型納米材料時(shí)TC11合金在不同載荷下的磨損表面形貌。圖7表明,未添加納米顆粒時(shí)TC11合金磨面上出現(xiàn)了犁溝、黏著痕跡、塑性撕裂及一些碎顆粒(圖7a),是典型的磨粒磨損和黏著磨損特征。單獨(dú)添加MLG時(shí)在同等載荷下磨面形貌與未添加時(shí)的類(lèi)似,但是磨損程度更為嚴(yán)重,犁溝寬、變形強(qiáng)、碎顆粒的尺寸大(圖7b)。選擇納米Fe2O3顆粒作為潤(rùn)滑材料時(shí),磨面形貌隨載荷的變化發(fā)生顯著的變化。在60 N下磨面較為平整(圖7c),磨面上出現(xiàn)大量的Fe和O元素(圖8a)。它們均來(lái)源于添加的Fe2O3顆粒,F(xiàn)e2O3顆粒黏著在一起。隨著載荷增大到80 N磨損表面變得起伏不平(圖7d),微觀形貌與未添加及單獨(dú)添加MLG時(shí)的類(lèi)似,發(fā)生了磨粒、黏著磨損。
圖7 在納米潤(rùn)滑材料和載荷不同的條件下TC11合金的磨面形貌
圖8 圖7中標(biāo)記區(qū)域的EDS分析
當(dāng)添加不同比例的MLG/Fe2O3納米復(fù)合材料時(shí),在不同載荷下磨面的形貌表現(xiàn)出兩種典型特征:一種是不在同一平面上的黑色、灰色區(qū)域覆蓋于磨損表面;另一種類(lèi)似于未添加納米材料或只添加MLG、Fe2O3(高載)時(shí)的形貌特征。當(dāng)添加1:1和2:1的MLG/Fe2O3時(shí),在100 N載荷下磨損表面呈現(xiàn)第一種形貌特征(圖7f、h),在120 N下呈現(xiàn)第二種形貌特征(圖7g、i)。而當(dāng)添加的MLG/Fe2O3比例為1:2時(shí),即使在120 N高載下也仍呈現(xiàn)第一種形貌(圖7e)。對(duì)應(yīng)前面的XRD分析,可判斷第一種形貌中的黑色、灰色區(qū)域主要由MLG和Fe2O3組成,其EDS分析表明黑色區(qū)域含有大量的C和少量的Fe、O元素(圖8b),這意味著,該區(qū)域以MLG為主導(dǎo)并混入了少量的Fe2O3;而灰色區(qū)域中的主要元素為Fe、O,還含少量的C和適量的Ti、Al元素(圖8c)。這些結(jié)果表明,在這一區(qū)域Fe2O3是主導(dǎo)成分,少量MLG摻雜在其中。該區(qū)域較薄,EDS已穿透該區(qū)域并掃描到了基體。
2.5 納米顆粒摩擦層的穩(wěn)定性
圖9給出了未添加與添加不同類(lèi)型納米材料時(shí)TC11合金在不同載荷下的磨損剖面形貌。在任何納米潤(rùn)滑材料和載荷條件下,TC11合金的磨面上都形成一層不同于基體材料的摩擦層。未添加任何納米材料時(shí)摩擦層厚度不均勻且不連續(xù),金屬Ti為摩擦層的主要成分。這意味著,該摩擦層為以金屬性為主的摩擦層,對(duì)磨損表面不具保護(hù)作用,因此磨損率、摩擦系數(shù)都較高。在摩擦層的下方,存在著明顯的塑性變形區(qū)域(圖9a)。當(dāng)單獨(dú)添加MLG納米材料時(shí)摩擦層形態(tài)和成分與未添加時(shí)類(lèi)似(圖9b),也沒(méi)有保護(hù)作用,甚至加劇了磨損,摩擦層下方的塑性變形更為嚴(yán)重。在添加Fe2O3納米顆粒、載荷60 N條件下亞表面未出現(xiàn)塑性變形,磨面上覆蓋著一層3~5 μm厚的摩擦層,而并非嵌插在基體中(圖9c),似乎與以金屬性為主的摩擦層不屬于同一類(lèi)型。根據(jù)XRD分析結(jié)果,這是由Fe2O3組成的人造陶瓷性摩擦層,可保護(hù)磨損表面,有效降低了磨損。隨載荷增大至80 N,以陶瓷性為主的摩擦層又重新被金屬性為主的摩擦層替代(圖9d)。
圖9 在納米潤(rùn)滑材料和載荷不同的條件下TC11合金的磨損剖面形貌
當(dāng)添加不同比例的MLG/Fe2O3納米復(fù)合材料時(shí)摩擦層出現(xiàn)了雙層結(jié)構(gòu),結(jié)合前面的EDS分析,下層摩擦層以Fe2O3為主導(dǎo),而上層摩擦層則以MLG為主導(dǎo)。在添加1:2的MLG/Fe2O3納米復(fù)合材料時(shí),這種雙層MLG/Fe2O3納米顆粒摩擦層直至120 N仍存在(圖9e、f),而添加比例為1:1和2:1時(shí)在100 N下雙層摩擦層存在(圖9g、i),在120 N下消失(圖9h)。
在不同載荷下納米顆粒摩擦層存在與否主要取決于其穩(wěn)定性,可用發(fā)生輕微-嚴(yán)重磨損轉(zhuǎn)變時(shí)的臨界載荷衡量。圖10給出了添加不同類(lèi)型納米材料時(shí)臨界載荷的比較。單獨(dú)添加MLG時(shí)臨界載荷小于20 N,表明只含MLG的納米顆粒摩擦層穩(wěn)定性極差,在滑動(dòng)之初就已破壞。添加Fe2O3納米顆粒時(shí)臨界載荷增大至60 N,納米顆粒摩擦層的穩(wěn)定性也相應(yīng)提高。其主要原因是,F(xiàn)e2O3較高的硬度使其具有較好的承載能力[12],在一定載荷范圍內(nèi)含F(xiàn)e2O3的納米顆粒摩擦層能穩(wěn)定存在,從而有效保護(hù)鈦合金基體,耐磨性顯著提高,但是較高的摩擦系數(shù)值意味著摩擦層的潤(rùn)滑能力較弱。載荷超過(guò)60 N時(shí)沿著滑動(dòng)方向的剪切應(yīng)力隨著接觸應(yīng)力的增大而增大,無(wú)潤(rùn)滑摩擦層在較高剪切應(yīng)力作用下容易破壞,因此發(fā)生嚴(yán)重的磨損。當(dāng)在滑動(dòng)界面上添加MLG/Fe2O3納米復(fù)合材料時(shí),TC11合金在高載下仍具有極低的磨損率和摩擦系數(shù)。其原因是,在磨損表面上形成了雙層MLG/Fe2O3納米顆粒摩擦層,其形成過(guò)程及結(jié)構(gòu)模型如圖11所示。靠近基體的以Fe2O3納米顆粒為主導(dǎo)的摩擦層具有良好的承載能力,一方面承受試驗(yàn)載荷,另一方面也支承著其上的摩擦層。靠近磨損表面以MLG為主的摩擦層起潤(rùn)滑劑作用,具有較低的剪切力,并使其下的摩擦層不受破壞。總之,兩者的協(xié)同使雙層MLG/Fe2O3納米顆粒摩擦層兼具潤(rùn)滑和承載的能力,在較高的載荷下仍不破壞而穩(wěn)定存在,臨界載荷至少達(dá)100 N,穩(wěn)定性顯著提高,有效改善了鈦合金的摩擦磨損性能。
圖10 在納米潤(rùn)滑材料不同的條件下臨界載荷的比較
圖11 雙層MLG/Fe2O3納米顆粒摩擦層的形成機(jī)理示意圖
比較添加不同比例納米復(fù)合材料時(shí)的臨界載荷可以發(fā)現(xiàn),比例為1:2時(shí)臨界載荷不低于120 N,即在該載荷下仍發(fā)生輕微磨損,這種MLG/Fe2O3納米顆粒摩擦層穩(wěn)定性最佳。究其原因,可以比較100 N下添加不同比例復(fù)合材料時(shí)TC11合金的剖面形貌。比例為1:2時(shí)雙層摩擦層中以Fe2O3為主導(dǎo)的下層摩擦層最厚,表明摩擦層中Fe2O3相對(duì)含量高,具有更強(qiáng)的承載能力,因此在更高載荷下能穩(wěn)定存在,有效保護(hù)基體。這就意味著,添加富Fe2O3納米復(fù)合材料時(shí)的雙層MLG/Fe2O3納米顆粒摩擦層,具有更強(qiáng)的穩(wěn)定性,可更有效地改善TC11合金的摩擦磨損性能;只添加Fe2O3納米顆粒時(shí)摩擦層的穩(wěn)定性并非十分理想,表明MLG在改善鈦合金的摩擦學(xué)性能中起至關(guān)重要的作用。
3 結(jié)論
(1) 在摩擦副滑動(dòng)界面上添加不同類(lèi)型的納米材料時(shí)TC11合金磨損表面均形成納米顆粒摩擦層,摩擦層的穩(wěn)定性取決于其組成成分和含量。
(2) 只含MLG納米顆粒的摩擦層因承載能力差而具有低的穩(wěn)定性,不能改善鈦合金的摩擦學(xué)性能。只含F(xiàn)e2O3納米顆粒摩擦層在低載時(shí)穩(wěn)定性較好,能減少磨損但是不能降低摩擦。同時(shí)含MLG和Fe2O3的雙層納米顆粒摩擦層兼具良好的潤(rùn)滑性和承載能力,穩(wěn)定性搞,使TC11合金的摩擦磨損性能顯著提高。
(3) 添加富Fe2O3納米復(fù)合材料時(shí)形成的雙層MLG/Fe2O3納米顆粒摩擦層含有更多的承載組分,具有較高的穩(wěn)定性,更能有效地保護(hù)基體材料,在高載下磨損率和摩擦系數(shù)仍然極低。
免責(zé)聲明:本網(wǎng)站所轉(zhuǎn)載的文字、圖片與視頻資料版權(quán)歸原創(chuàng)作者所有,如果涉及侵權(quán),請(qǐng)第一時(shí)間聯(lián)系本網(wǎng)刪除。
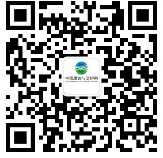
官方微信
《中國(guó)腐蝕與防護(hù)網(wǎng)電子期刊》征訂啟事
- 投稿聯(lián)系:編輯部
- 電話:010-62316606-806
- 郵箱:fsfhzy666@163.com
- 中國(guó)腐蝕與防護(hù)網(wǎng)官方QQ群:140808414