摘要
對AZ31B鎂合金進行超聲滾壓表面處理,利用電化學測試手段評價了改性后合金的耐蝕性能,通過SEM和白光干涉儀觀察分析了合金處理層微觀組織、表面形貌以及腐蝕后表面形貌。結果表明,經過表面處理后,鎂合金表層晶粒發生明顯細化且表面平整,表面腐蝕產物分布均勻且致密性高,去除腐蝕產物后表面點蝕坑細小密集。在浸泡前期,經表面處理試樣的鈍化膜層電阻Rf為9020 Ω,遠大于未經表面處理試樣的14.8 Ω。在浸泡中期,未經表面處理試樣的阻抗譜圖上出現擴散過程引起的阻抗特征,此時鈍化膜層電阻Rf為22.9 Ω,遠遠小于經表面處理試樣的19800 Ω。在浸泡后期,表面處理試樣鈍化膜層電阻Rf為31400 Ω,而未經表面處理試樣的為11400 Ω。超聲表面滾壓處理降低了鎂合金表面粗糙度及晶粒尺寸,進而增加了鎂合金在溶液中鈍化膜的均勻性和致密性,阻滯了鎂合金表面的電化學反應過程,延緩了鎂合金的腐蝕。
關鍵詞: 鎂合金; 超聲滾壓; 阻抗譜; 表面形貌; 電化學; 腐蝕機理
近年來,隨著人口老齡化的增長,老年人數量迅速增長,因骨質疏松所導致的骨折數量大幅度增加[1]。許多外部治療對骨折來說過于復雜,必須通過內部植入物固定。目前,常用的永久性承力骨骼植入物如不銹鋼、Ti和鈷鉻合金存在力學性能不相容[2]、釋放有毒金屬離子[3]、不可自行降解等缺點。相比之下,Mg及其合金的力學性能如Young's彈性模量 (E=41~45 GPa) 與人骨的力學性能相似 (E=15~25 GPa),減少了應力遮擋效應。此外,Mg2+是人體中常見的代謝物,鎂合金在人體內降解所產生的鎂離子會促進骨細胞再生,因此鎂合金具備良好的生物相容性[4]。然而過快的腐蝕速率使得鎂合金作為骨植入材料在生物體內存在時間較短,難以滿足骨骼生長對力學性能的要求。因此,提高鎂合金耐蝕性有著十分重要的意義[5-10]。
表面處理能夠在很大程度上影響鎂合金的耐蝕性[11,12]。Denkena等[13]研究滾球拋光加工對鎂鈣合金在0.9% (質量分數) NaCl溶液中腐蝕行為的影響,通過拋光工藝使得在鎂鈣合金次表層產生高殘余壓應力,從而使腐蝕速率降低了約100倍。Salahshoor等[14]研究了拋光處理對生物醫用鈣鎂合金在模擬體液中腐蝕行為的影響,認為經過拋光的鎂合金表面展示出更加均勻的腐蝕以及更少的腐蝕產物。劉蒙恩等[15]研究了高能噴丸對AZ31鎂合金在5% (質量分數) NaCl溶液中耐蝕性的影響,結果表明,經噴丸處理的表面形成厚度約150 μm的塑性變形區,極大地細化了表層晶粒,但是由于在噴丸過程中表面形成了大量的裂紋,使得腐蝕接觸面增大,導致噴丸試樣的腐蝕速率明顯高于未噴丸試樣的。超聲表面滾壓強化技術是在噴丸與拋光的基礎上發展的一種金屬表面改性方法[16]。相比較傳統的滾壓和噴丸處理,超聲表面滾壓處理 (USRP) 能夠實現表面沖擊和光整同時進行,近年來已經在疲勞延壽、表面改性等熱門研究領域得到廣泛關注和應用[17-20]。
綜上所述,表面處理能夠提高鎂合金的耐蝕性,目前,應用超聲滾壓表面處理技術在提高40Cr鋼和鋁合金耐蝕性方面研究甚多[21-24],但是采用超聲滾壓表面處理技術來提高鎂合金腐蝕性能的相關研究鮮有報道。因此,本文以醫用鎂合金AZ31B作為實驗材料,首先采用USRP對鎂合金表面進行改性處理,然后對改性前后鎂合金的電化學腐蝕行為進行研究,最后通過對改性前后鎂合金腐蝕形貌觀察,分析超聲表面滾壓對鎂合金腐蝕性能的影響機理,從而為選取合適的超聲滾壓工藝參數來提高鎂合金在人體生理環境下的耐蝕性奠定基礎。
1 實驗方法
本實驗所用材料為商用擠壓態AZ31B鎂合金棒料,直徑D為30 mm,化學成分 (質量分數,%) 為:Zn 0.52,Al 2.96,Si 0.16,Cu 0.006,Mn 0.31,Fe 0.003,Ni 0.001,Mg余量。
1.1 實驗步驟
使用數控車床對毛坯件外圓進行粗加工處理,然后使用超聲表面滾壓設備對預處理工件外圓進行超聲表面滾壓處理,滾壓進給量為0.01 mm/r,主軸轉速為600 r/min,靜壓力為30 N,振幅為10 μm,滾壓長度為10 mm。超聲表面滾壓加工簡圖如圖1所示。將未經和經過超聲滾壓處理試樣均切割成如圖2和3所示大小,分別用于表面形貌觀察和腐蝕性能測試,以及金相組織觀察。電化學測試時,所有試樣除測試面外,其余面使用環氧樹脂密封。將未經超聲滾壓處理的試樣記為試樣1,經超聲滾壓處理的試樣記為試樣2,貼標簽密封保存備用。
圖1 超聲表面滾壓加工示意圖
圖2 用于形貌觀察和腐蝕性能測試的試樣
1.2 表面形貌及微觀組織表征
使用白光干涉ZeGage? Plus光學輪廓儀對試樣1及試樣2表面3D形貌沿軸向取樣420 μm進行測量。
利用光學顯微鏡 (OM) 和場發射掃描電子顯微鏡 (FE-SEM,Quanta 600FEG) 觀察試樣1和2沿截面方向的微觀結構。試樣的預處理為:(1) 使用800#水磨砂紙沿一方向將取樣時的切痕磨掉,然后依次使用1000#,2000#,3000#和5000#水磨砂紙打磨表面;(2) 使用金相拋光機去除5000#砂紙所帶來的劃痕,拋光布使用植絨布,使用W2.5金剛石拋光膏拋光至鏡面;(3) 最后使用金相浸蝕液腐蝕25 s,清水沖洗后酒精清洗,冷風吹干。浸蝕液成分為:10 mL硝酸+30 mL乙酸+40 mL蒸餾水+120 mL無水乙醇。
圖3 用于微觀組織觀察的試樣
1.3 腐蝕性能測試與腐蝕形貌表征
實驗介質為PBS磷酸鹽緩沖液,由1.15 g/L Na2HPO4,0.2 g/L KH2PO4,8 g/L NaCl和0.2 g/L KCl組成。電化學實驗在Zennium X化學工作站上進行。輔助電極為10 mm×10 mm×0.1 mm的鉑片電極,參比電極為R232飽和甘汞電極,工作電極為鎂合金試樣。
腐蝕電化學性能測試時,試樣在浸蝕液中浸泡3,24,48,96,144和360 h后進行腐蝕電化學測試,并使用恒溫水浴鍋將溫度設置為37 ℃來模擬人體體溫,每24 h更新55%的溶液來模擬人體體液更新[25]。在自腐蝕電位下進行阻抗測試,測試頻率范圍為105~10-2 Hz,正弦擾動電壓為10 mV。低頻 (小于66 Hz) 每十位區間取5個點,每個取樣點測試5次;高頻 (大于66 Hz) 每十位區間取10個點,每個取樣點測試10次。所有的電化學測試均在室溫下進行。
使用SEM觀察浸泡360 h后的鎂合金試樣表面腐蝕形貌和去除腐蝕產物后的表面形貌,其中,表面腐蝕形貌觀察之前使用無水乙醇進行超聲清洗;觀察去除腐蝕產物后的表面形貌之前將試樣放入鉻酸溶液 (200 g/L CrO3+10 g/L AgNO3) 中浸泡5 min以去除試樣表面所覆蓋的腐蝕產物,腐蝕產物去除后立即使用無水乙醇進行超聲清洗15 min,冷風吹干。
2 實驗結果
2.1 加工表面形貌
圖4a~c分別為AZ31B鎂合金在車削和USRP加工后的表面三維形貌及輪廓曲線。表面輪廓曲線測試位置位于三維形貌圖中虛線AB處。從圖4a和c可以看出,車削后試樣表面上沿切削方向存在呈近似周期性凹凸分布,輪廓波峰與波谷處尖銳過渡,其中最低谷與最高峰的最大高度差Sz為6.107 μm,均方根Sq為1.008 μm。而從圖4b和c可以看出,USRP處理對車削表面起到削峰填谷的作用,車削表面走刀痕跡被消除,表面輪廓曲線更加平緩,最大峰值與最大谷值之間的距離顯著降低,其中Sz為2.953 μm,Sq為0.219 μm。試樣1的輪廓算術平均高度Sa為802 nm,而試樣2的Sa為158 nm,僅為試樣1的1/5。
圖4 鎂合金AZ31B在車削和USRP加工后的表面三維形貌及表面輪廓
2.2 晶粒尺寸分布
圖5a為試樣1的顯微組織,鎂合金母材由大小不均的等軸晶組成,表層晶粒大小和基體晶粒大小幾乎看不出差別。而對于經USRP處理后的鎂合金變形層試樣2 (圖5b),顯然由于高頻超聲滾壓的影響,材料表層的顯微組織尺寸顯著減小,晶粒壓扁拉長,晶粒內部存在大量孿晶,晶界增多且更致密,與基體存在顯著區別。
圖5 滾壓前后鎂合金試樣的微觀組織形貌
2.3 電化學阻抗譜測試結果
為獲得兩種AZ31B鎂合金試樣在浸泡不同時間后的阻抗特性,進行了電化學阻抗譜測試,測得的Nyquist圖如圖6a和b所示。從圖6a可以看出,在浸泡2,24,48,144,240及360 h后,高頻區和低頻區各有一個容抗弧,且隨著時間的推移,高頻弧徑逐漸減小,而低頻弧徑出現增加-減少-增加的交替變化,且在240 h時達到最大。而當浸泡時間為96 h時,試樣1的Nyquist圖上除高頻和中頻的兩個容抗弧之外,低頻還出現了Warburg阻抗。從圖6b可以看出,試樣2的阻抗譜圖在所有的浸泡時間下均出現兩個容抗弧,且隨著時間的推移,高頻弧徑逐漸減小,而低頻弧徑同樣出現增加-減少-增加的交替變化,且在360 h時達到最大。可以看出,在經過360 h的浸泡之后,試樣2的弧徑遠大于試樣1的。
圖6 兩種鎂合金試樣在37 ℃浸泡不同時間后的Nyquist圖
2.4 腐蝕表面形貌
經過360 h浸泡之后,試樣1和2表面腐蝕形貌分別如圖7a和b所示。可以清晰看到,試樣1的腐蝕產物均勻性差,隨處可見較大的孔洞存在。相比之下,試樣2的腐蝕產物較均勻致密,且未見到較大孔洞的存在,表面被花瓣狀的腐蝕產物完全覆蓋。清除腐蝕產物后的表面形貌如圖8a和b所示。可以看出兩者的表面均以點蝕為主,其中試樣1表面存在著大小不一的點蝕坑,體積相差甚大,點蝕坑沿縱向發展。而試樣2中點蝕坑細小密集,且沿橫向發展。
圖7 兩種試樣在PBS中浸泡360 h后的表面腐蝕形貌
圖8 兩種試樣在PBS中浸泡360 h并去除腐蝕產物后的表面腐蝕形貌
3 討論
3.1 阻抗行為
Nyquist圖上高頻容抗弧一般體現電荷轉移過程所引起的溶液與電極表面的阻抗特性,而低頻容抗弧體現電極表面多孔膜層的阻抗特性[26,27]。在PBS溶液中浸泡2 h后,從圖9a可以看出試樣1和試樣2在高頻和低頻各有一個容抗弧;從圖9b中可以看出在高頻段,試樣2的阻抗值略大于試樣1的,而在低頻區,試樣2的阻抗值遠大于試樣1的,這表明此時試樣2表面膜層對基體的保護作用遠遠大于試樣1的。這主要是因為在浸泡初期,試樣1表面凹凸不平,致使表面存在不連續的多孔鈍化膜,在沒有鈍化膜覆蓋的鎂合金表面與溶液直接接觸;而對于試樣2來說,由于表面粗糙度低且晶粒細化,致使表面快速的形成連續且均勻致密的鈍化膜[28],使得帶電粒子穿越鈍化膜的阻抗遠遠大于試樣1的。在沒有鈍化膜覆蓋的鎂合金表面和溶液界面有雙電層的存在,其性質可由一個電阻和一個電容并聯來表征。考慮到電極表面的實際物理特征,鈍化膜電阻應與雙電層串聯成一個單元后再與氧化膜電容并聯[29],見圖10a所示的溶解模型,其等效電路如圖10c所示。而對于試樣2來說,由于表面均勻且晶粒細化,致使表面快速且完全的形成致密的鈍化膜[30],因此溶液中的陰離子幾乎均勻地穿越鈍化膜來到達鎂合金基體表面,其溶解模型可由圖10b來表示,其性質可由鈍化膜層的阻抗和溶液與鎂合金表面之間的阻抗串聯來表征,見圖10d所示的等效電路。其中,Rs代表溶液電阻,Rct表示鎂合金陽極和PBS溶液之間界面的電荷轉移電阻,Rf表示鎂合金陽極表面所覆蓋的多孔鈍化膜層電阻,Qdl表示鎂合金陽極和電解液之間的雙電層電容,Qf表示鎂合金陽極表面多孔鈍化膜與溶液之間的雙電層電容。由等效電路所得擬合曲線如圖11實線所示,其中各元器件值列于表1中。可知,在浸泡2 h之后,試樣1的Rf為14.8 Ω;而試樣2的Rf為9020 Ω,遠遠大于試樣1的。
圖9 浸泡2 h后試樣1和試樣2的Bode圖
圖10 滾壓前后鎂合金試樣在PBS溶液中的溶解模型及等效電路
圖11 浸泡24,48,和96 h后兩種鎂合金試樣的Bode圖
表1 兩種鎂合金試樣浸泡不同時間后的阻抗擬合結果
在浸泡中期,如圖11所示,試樣2仍出現兩個容抗弧,分別位于低頻和高頻區,這表明試樣2的溶解模型并沒有發生改變,改變的僅僅是元器件值,所以其等效電路可由圖10d表示。相反,在浸泡96 h后,從圖11e和f可以看出,此時在試樣1的Nyquist圖中 (圖6a) ,緊接著中高頻的容抗弧后,在低頻出現傾斜角約為π/4的Warburg擴散阻抗直線[27];從圖11e可以看出,此時試樣1出現了3個時間常數,分別是代表著電荷傳遞過程的高頻弧、表示膜層阻抗的中頻弧以及表示擴散所引起的低頻弧徑。從圖11f可以看出,試樣1的中頻段阻抗值遠遠小于試樣2的。這是由于溶液中的攻擊性離子破壞了表面鈍化膜薄弱位置,造成鈍化膜破裂,基體直接與溶液接觸,使得反應離子可順利通過宏觀孔到達膜層/基體金屬界面,從而在電極表面附近引起濃度差,相對于電遷移來說,擴散起到了主導作用,因此阻抗譜上出現Warburg阻抗。此時等效電路可由圖12來進行表征[27],其中,ZW表示電極表面由擴散所引起的阻抗值,各元器件值如表1中所列。可以明顯看到,在浸泡96 h之后,試樣1的膜層電阻僅為22.9 Ω,而由電遷移所引起的電荷轉移電阻卻高達5440 Ω,這說明此時電遷移過程受到極大抑制。
圖12 浸泡96 h后試樣1的等效電路
在浸泡后期,從圖13可以看到,試樣1和試樣2均存在兩個容抗弧,分別位于低頻和高頻。試樣1的Warburg擴散阻抗消失是由于鈍化膜的自我修復功能,使得局部破壞位置自行修復,重新對基體提供保護。從表1可以明顯看到,經過360 h的浸泡之后,試樣2表面膜層電阻達到了31400 Ω,而試樣1的表面膜層電阻僅為11400 Ω。同時,從圖7和8的表面腐蝕形貌可以看出,試樣1的表面鈍化膜呈不均勻性,局部呈多孔特征;而試樣2表面腐蝕形貌則呈均勻分布特征。
圖13 浸泡144,240,和360 h后兩種鎂合金試樣的Bode圖
3.2 腐蝕機理
USRP處理顯著降低了鎂合金表面粗糙度,溶液與合金的接觸面積減小,因此降低了局部腐蝕的幾率。由于USRP處理后晶界增多且均勻分布,從而導致鎂基體與晶界處的第二相形成大量微小電偶腐蝕,從而加速了鈍化膜的均勻生長。
由于超聲滾壓使得鎂合金表層發生嚴重壓縮變形,變形層存在較大殘余壓應力,縮短了原子之間的距離,在單位體積內的原子數增多,從而使鈍化膜易于形成且更加致密[31],最終導致溶液中的攻擊性離子 (Cl-) 穿過膜層的阻力增大,從而在后期的腐蝕過程中鈍化膜不會破裂而暴露基體。進而腐蝕后的表面點蝕體積小且分布更加均勻,使得膜層與基體的界面緩慢且平滑的移動,因此其界面移動模型可由圖14a來表示。相反,晶粒粗大,表面粗糙的未處理試樣會導致在溶液中所形成的鈍化膜致密性差且不均勻,使得溶液中大量攻擊離子進入膜層孔隙中[32],造成電極表面附近反應物濃度與PBS溶液本體濃度存在明顯差別,因此就會出現反應物從溶液本體向電極表面的擴散過程,從而使得此處電極表面的孔蝕坑不斷的沿縱向發展,其界面移動模型可由圖14b來表示。
圖14 鎂合金試樣1和2在PBS溶液中的界面移動模型
4 結論
(1) 經USRP沖擊與光整加工后,鎂合金表面粗糙度明顯降低,加工表面形貌更加均勻,表層晶粒壓扁拉長,晶粒細化。
(2) 經USRP工藝處理后,AZ31B鎂合金耐蝕性顯著提高。其鈍化膜層阻抗值隨時間變化幅度小且遠遠大于未經USRP處理試樣的膜層阻抗值;腐蝕表面產物分布均勻且致密,去除腐蝕產物表面點蝕細小密集且分布均勻。
(3) 鎂合金耐蝕性改善的主要原因是USRP處理后晶粒細化、晶界增多,顯著提高鎂合金鈍化膜層的致密性及均勻性。此外,表面粗糙度降低,極大降低了浸泡樣品與溶液的接觸面積,從而導致合金耐蝕性的提高。
免責聲明:本網站所轉載的文字、圖片與視頻資料版權歸原創作者所有,如果涉及侵權,請第一時間聯系本網刪除。
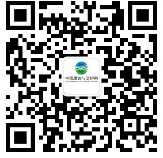
官方微信
《中國腐蝕與防護網電子期刊》征訂啟事
- 投稿聯系:編輯部
- 電話:010-62316606-806
- 郵箱:fsfhzy666@163.com
- 中國腐蝕與防護網官方QQ群:140808414