太陽能光伏發電已成為世界上最具發展前景的新能源產業。相對于多晶硅和非晶硅太陽能電池來說,單晶硅作為光伏發電材料 ,具有較高的光電轉換效率和突出的商業優勢,已成為太陽能光伏發電的主流。直拉法(Czochralski,CZ)是制備單晶硅主要方法之一,直拉單晶爐的構成包 括爐體系統、真空系統、氣體系統、熱場系統和電氣控制系統等。其中,熱場系統是單晶硅生長最重要的條件之一,單晶硅的品質直接受熱場溫度梯度分布的影響。
熱場部件主要由炭素材料(石墨材料和炭/炭復合材料)組成,按照功能分為支撐件、功能件、發熱體、保護件、保溫材料等,如圖1所示。隨著單晶硅尺寸的不斷增大,對熱場部件的尺寸要求也越來越大,炭/炭復合材料由于其尺寸穩定性、 力學性能優異等因素成為單晶硅用熱場材料的首選。
在直拉單晶硅過程中,硅料的熔融會產生硅蒸氣和熔融硅飛濺, 造成炭/炭熱場材料的硅化侵蝕, 炭/炭熱場材料的力學性能和使用壽命受到嚴重影響。因此,如何降低炭/炭熱場材料的硅化侵蝕,提高 其使用壽命成為單晶硅生產廠家和炭/炭熱場材料生產廠家共同關注的課題之一。 碳化硅涂層由于其優異的抗熱震性能、耐磨性能等特點成為炭/炭熱場材料表面涂層防護的首選。
本文從單晶硅生產用炭/炭熱場材料出發,首先 介紹了碳化硅涂層的主要制備方法和優缺點,在此基礎上,針對炭/炭熱場材料的特點,綜述了碳化硅涂層在炭/炭熱場材料的應用及研究進展, 并對炭/ 炭熱場材料表面涂層防護提出了建議和發展方向。
1 碳化硅涂層的制備技術
1.1 包埋法
包埋法常用于 C/C-SiC 復合材料體系中碳化硅內涂層的制備,該方法首先用混合粉體將炭/炭復合材料包裹起來, 進而在一定溫度下進行熱處理, 混合粉料與試樣表面發生一系列復雜的物理化學反應形成涂層。其優點是過程簡單,只需一個單一過程就可以制備出致密、無裂紋基體的復合材料;從預成型到最終產品,尺寸變化小;對任何纖維增強結構都適用;涂層和基體間能形成一定的成分梯度,與基體結合較好。但亦存在缺點,如高溫下易發生化學反應使纖維受損, 炭/炭基體的力學性能下 降;涂層的均勻性很難控制,由于重力等因素使得涂層上下不均勻。
1.2 漿料涂覆法
漿料涂覆法是將涂層材料與黏結劑配成混合料,均勻涂刷在基體表面,烘干后在惰性氣氛中將涂刷好的試件進行高溫燒結,即可得到所需涂層。其優點是過程簡單易操作,涂層厚度易控制;缺點是涂層與基體之間存在較差的結合強度,且涂層的抗熱震性差,涂層均勻性較低。
1.3 化學氣相反應法
化學氣相反應法是在一定溫度下將固體硅料蒸發為硅蒸氣,進而硅蒸氣擴散進入基體的內部與表面,與基體中的碳原位反應生成碳化硅的一種工藝方法。其優點有爐內氣氛均勻,被涂物質各處具有一致的反應速度、沉積厚度等;工藝過程簡單易操作,可通過改變硅蒸氣壓、沉積時間等參數來控制涂層厚度。不足之處在于試樣受在爐內擺放位置的影響較大,且爐內的硅蒸氣壓達不到理論的均勻度,從而導致涂層厚度不均勻。
1.4 化學氣相沉積法
化學氣相沉積法是以碳氫化合物作為氣源,以高純N2/Ar作為載氣,將混合氣體引入化學氣相反應爐內,碳氫化合物在一定的溫度和壓力下經分解、合成、擴散、吸附、解析等反應,在炭/炭復合材料基體表面生成固體薄膜的過程。其優點在于涂層的密度、純度可控;對形狀較復雜的工件同樣適用;通過調節沉積 參數,可以控制產物的晶體結構、表面形貌等。缺點是沉積速率太低、工藝過程復雜、生產成本高,并可 能存在涂層缺陷,如裂紋、網狀缺陷和面缺陷等。
綜上可知,包埋法限于其工藝特點,適合實驗室和小尺寸材料的研制生產;涂覆法由于其工藝一致性較差,不適合批量化產品的生產;CVR 法能夠滿足大尺寸產品的批量化生產, 但是對設備和工藝要求較高;CVD 法是理想的碳化硅涂層制備方法,但由于其工藝控制難度較大,成本相對CVR法較高。
2 碳化硅涂層在炭/炭熱場材料中的應用及研究進展
2.1 在坩堝制備中的應用及研究進展
炭/炭坩堝在單晶熱場中,主要作為硅料的承載容器,與石英坩堝接觸,如圖2所示。炭/炭坩堝工作溫度在1450℃左右,受到固體硅(二氧化硅)和硅蒸氣的雙重侵蝕,最終由于坩堝變薄或者出現環向裂紋等,造成坩堝失效。
張永輝等用化學氣相滲透工藝及原位反應制備了一種復合涂層炭/炭復合材料坩堝,該復合涂層由碳化硅涂層 (100~300μm)、 硅涂層(10~20μm)及氮化硅涂層(50~100μm)組成,可有效抑制含硅蒸氣對炭/炭復合材料坩堝內型面的侵蝕。在生產使用過程中,該復合涂層炭/炭復合材料坩堝的單爐次損耗為 0.04 mm,使用壽命可達180爐次。
王金鐸等采用化學反應法,在高溫燒結爐內,以二氧化硅和金屬硅為原料,控制二者的質量比,在一定溫度條件及載氣的保護下,在炭/炭復合材料坩堝的表面生成一層均勻的碳化硅涂層。結果表明,經高溫處理后,不僅提高了碳化硅涂層的純度和強度,并且能夠大幅度提高炭/炭復合材料表面的耐磨損強度,防止了單晶硅爐內 SiO 蒸氣以及揮發氧原子對坩堝表面的腐蝕,使用壽命相比于無碳化硅涂層的坩堝提高了 20%。
2.2 在導流筒中的應用及研究進展
導流筒位于坩堝上方(如圖1所示),在拉晶過程中,其溫度場上下內外差異較大,尤其底部外型面距離熔融硅料最近,溫度最高,受硅蒸氣腐蝕最為嚴重。
廖寄喬等發明了一種工藝簡單、抗氧化性好的導流筒抗氧化涂層及制備方法,首先在導流筒基體上原位生長一層碳化硅晶須,再制備致密的碳化硅外層,從而在基體和致密的碳化硅表層之間形成SiCw過渡層,如圖3所示,其熱膨脹系數介于基體和碳化硅之間,可有效地降低由于熱膨脹系數不匹 配產生的熱應力。
分析表明, 隨著 SiCw 含量的增 加,涂層中的裂紋尺寸和數量降低,在1100 ℃空氣 中氧化10h后, 涂層樣品的失重率僅在 0.87%~8.87%, 碳化硅涂層的抗氧化性能和抗熱震性能被 大幅度提高,且整個制備過程是通過化學氣相沉積連續完成的,碳化硅涂層的制備被大大簡化,整個導流筒的綜合性能得到加強。
蔣建純等提出一種直拉單晶硅用石墨導流筒基體強化及表面涂層方法,采用刷涂法或噴涂法將所得碳化硅漿料均勻涂覆于石墨導流筒表面,涂覆厚度 30~50 μm,再置于高溫爐中進行原位反應,反應溫度為 1850~2300 ℃, 保溫2~6h, 從而制得SiC 外層,可應用于24 in(60.96 cm)的單晶生長爐中使用,使用溫度在1500 ℃,使用 1500h 發現該石墨導流筒表面并無開裂、落粉現象。
2.3 在保溫筒中的應用及研究進展
保溫筒作為單晶硅熱場系統的關鍵元件之一,主要作用是減少熱量損失并控制熱場環境的溫度梯度。作為單晶爐內壁保溫層支撐件,由于硅蒸氣腐蝕導致產品掉渣和開裂,最終導致產品失效。
廖寄喬等為進一步增強 C/C-SiC 復合材料保溫筒的抗硅蒸氣腐蝕能力,將制得的 C/C-SiC復合材料保溫筒制品放入化學氣相反應爐中,采用化學氣相沉積工藝在 C/C-SiC復合材料保溫筒制品表面制得致密的碳化硅涂層,結果表明,采用此工藝 可有效抑制硅蒸氣對C/C-SiC復合材料芯部炭纖維的侵蝕,與炭/炭復合材料相比,抗硅蒸氣腐蝕能力提高了5~10倍, 并大幅度提高了保溫筒的使用壽命及熱場環境的安全性。
3 結論與展望
碳化硅涂層因其優異的高溫抗氧化性能在炭/ 炭熱場材料中的應用越來越廣泛。隨著單晶硅生產用炭/炭熱場材料尺寸的不斷增大,如何提高熱場材料表面碳化硅涂層的均勻性,提高炭/炭熱場材料的使用壽命成為亟待解決的問題。
另一方面,隨著單晶硅產業的發展,對高純度炭/炭熱場材料的需求也越來越大,反應時在內部炭纖維上也生長了SiC納米纖維。實驗制備的 C/C-ZrC 和 C/C-SiC-ZrC復合材料燒蝕30s后,C/C-ZrC 復合材料的質量燒蝕率和線燒蝕 率分別為-0.32 mg/s 和 2.57 μm/s;而 C/C-SiC-ZrC復合材料的質量燒蝕率和線燒蝕率分別為-0.24mg/s 和 1.66 μm/s,生長了 SiC 納米纖維的 C/C-ZrC復合材料展示了更優異的耐燒蝕性能。后期將研究不同碳源對生長 SiC 納米纖維的影響以及SiC納米纖維增強 C/C-ZrC 復合材料耐燒蝕性能的機理。
免責聲明:本網站所轉載的文字、圖片與視頻資料版權歸原創作者所有,如果涉及侵權,請第一時間聯系本網刪除。
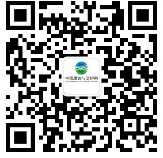
官方微信
《中國腐蝕與防護網電子期刊》征訂啟事
- 投稿聯系:編輯部
- 電話:010-62316606-806
- 郵箱:fsfhzy666@163.com
- 中國腐蝕與防護網官方QQ群:140808414