1 高強鋁合金的發(fā)展歷程
高強鋁合金一般指含銅2×××系、含鋅7×××系鋁合金, 但后者依據(jù)強度的不同, 也分為中強7×××鋁合金(如7020, 7011, 7051等)和高強7×××鋁合金(如7050,7010,7075 等)。 迄今為止, 被廣泛應(yīng)用于 航空工業(yè)的鋁合金主要涉及2×××系(Al-Cu)和7×××系(Al-Zn-Mg-Cu),其他系列的鋁合金, 如Al-Mg-Si 系(6×××系)、Al-Li合金等也有一定應(yīng)用,但總體用量較少。 在航天領(lǐng)域, 除上述系列外, 還包括3×××系、5×××系、8×××系鋁合金, 在鐵路、公路與水上交 通運輸領(lǐng)域大量應(yīng)用5×××系鋁合金。
高強鋁合金主要以航空需求為背景不斷發(fā)展, 百年鋁材百年航空, 鋁合金滿足了不同時代飛機和 尖端裝備的發(fā)展要求。 隨著飛機設(shè)計思想的不斷創(chuàng) 新, 先進飛機的構(gòu)件制造對鋁合金提出了越來越高 的要求, 特別是現(xiàn)代飛機的輕量化、寬敞化、舒適 化、長壽命、高可靠和低成本的發(fā)展需求, 推動了高 強鋁合金的發(fā)展。 按照鋁合金的成分-工藝-組織- 性能特征, 可將航空鋁合金的發(fā)展歷程大體劃分為5個階段, 即第一代高靜強度鋁合金, 第二代高強耐 蝕鋁合金, 第三代高強、高韌、耐蝕鋁合金, 第四代 高強高韌耐蝕、高耐損傷鋁合金, 以及新一代高強、高韌、低淬火敏感性鋁合金。 各階段鋁合金的特征性能、關(guān)鍵技術(shù)與特征微結(jié)構(gòu), 以及典型合金如表 1 所示。
20世紀初至50年代末, 隨著鋁合金沉淀硬化效應(yīng)的發(fā)現(xiàn)和峰值時效技術(shù)的發(fā)展產(chǎn)生了第一代高靜強度鋁合金。 1906年,Wilm首先發(fā)現(xiàn) Al-Cu 合金的沉淀硬化現(xiàn)象。 Al-Cu-Mg系合金通過淬火后形成的過飽和固溶體在隨后的停放過程中會析出高密 度 Al2Cu ( θ′ )和 Al2CuMg (S′)相, 使合金的硬度獲得大幅度提升, 從而揭開了高強鋁合金發(fā)展的序幕。1923年, Sander和Meissner又發(fā)現(xiàn)Al-Zn-Mg合金 通過淬火-人工時效熱處理后, 形成的主要強化相 MgZn2 (η′相)比Al-Cu-Mg系合金中的θ′和S′相尺寸更小、分布更彌散, 沉淀硬化效應(yīng)更顯著。 圖1顯示 了經(jīng)典的 θ (Al2Cu)相演變的結(jié)構(gòu)變化示意圖。 研究表明, 在時效的初級階段, GP區(qū)僅僅是一層或 兩層原子的厚度, 但是其密度高達 1017~1018 cm-3, 這 種微結(jié)構(gòu)能夠為合金提供高的強度。
此后,研發(fā)了人工峰值時效的7075-T6和7178- T6等高強鋁合金。 2024-T3,7075-T6和7178-T6鋁 合金滿足了飛機最初階段提高強度安全系數(shù)、減輕 結(jié)構(gòu)重量和提高航程為目標替代木材的靜強度設(shè) 計需求, 一般將其作為第一代高強鋁合金的典型代表。 成立于1935年的鋁業(yè)協(xié)會(The Aluminum As- sociation)于1954年建立鋁合金牌號注冊制度, 2024, 7075 等作為最早注冊的鋁合金沿用至今, 已廣泛應(yīng)用于航空航天、武器裝備及高端裝備制造領(lǐng)域。
值得指出的是, 由于超音速飛機的發(fā)展,特別是軍機的高速/高加速度性能的不斷提升, 耐熱鋁合金也一直在發(fā)展。代表性的合金是美國鋁業(yè)公司20世紀50年代末期發(fā)展的2618 (Al-Cu-Mg-Fe-Ni 系)和2219合金。后者在航天領(lǐng)域有大量應(yīng)用, 主要用 做燃料儲箱和火箭鍛環(huán)。2618鋁合金至今在軍機 上仍在使用, 也曾被歐洲協(xié)和式超音速客機大量采用,主要用于制造飛機的蒙皮、耐熱結(jié)構(gòu)件等, 以適應(yīng)協(xié)和式超音速客機2M(>2450 km/h)以上高速飛 行時氣動加熱環(huán)境的要求。 但隨著協(xié)和式超音速客機退出航空客運市場, 世界各航空制造大國短期內(nèi)尚無發(fā)展新一代超音速客機和運輸機的計劃, 因此 民機對 Al-Cu-X 系列耐熱鋁合金的需求有所減少, 而超音速軍機的制造與發(fā)展仍將對其有一定的需求量。
上世紀60年代,基于過時效原理,使晶界相不連續(xù)析出的T73,T76時效熱處理技術(shù)促進了第二 代耐蝕高強鋁合金的發(fā)展。 鋁合金的疲勞和應(yīng)力腐 蝕失效引起的飛機失事促使飛機設(shè)計對高強鋁合 金提出了抗疲勞和耐腐蝕性能的要求。 特別是 7××× 系鋁合金強度級別比 2×××系高, 其抗應(yīng)力耐蝕性能 差的矛盾更加突出。 提高抗應(yīng)力耐蝕性能的關(guān)鍵是 在 7×××系鋁合金中發(fā)明的過時效熱處理技術(shù), 使晶 界析出相不連續(xù)分布, 通過降低強度提高抗應(yīng)力腐 蝕性能。 合金狀態(tài)為 T73, 使得 7×××系合金除滿足 飛機設(shè)計靜強度外, 還滿足了耐腐蝕性能的要求。 為減小 T73 處理帶來的較大強度損失, 接著又研發(fā) 出 T76 熱處理工藝, 更好地協(xié)調(diào)了 7×××系合金的 高強度與耐蝕性能。 7075-T73/T76 等成為第二代高 強耐腐蝕鋁合金的典型代表。
上世紀70年代,合金純凈化和微合金化理論和 技術(shù)推動了第三代高強高韌鋁合金的發(fā)展。飛機安 全壽命設(shè)計對航空高強鋁合金提出了斷裂韌性的要求。 隨著對Fe,Si雜質(zhì)影響鋁合金韌性規(guī)律研究 的不斷深入, 60 年代末期,美國首先成功研制了低 雜質(zhì)含量的 7475 合金。 與 7075 合金相比, 該合金的 Zn, Mg 和 Cu 主合金成分的含量差別很小, 主要區(qū) 別是大幅降低 Fe, Si 等雜質(zhì)含量, 使粗大初生相和 過剩相數(shù)量減少、尺寸細化, 使合金具有高強度的同時, 也具有優(yōu)異的斷裂韌性。 70 年代初期, 隨著對Cr,Mn和Zr等微合金化元素作用機理研究的不斷深入, 在美國海軍和空軍的支持下, 美國鋁業(yè)公司(Alcoa)研制了低雜質(zhì)含量、并用 Zr 微合金化的7050合金, 歐洲也研制了成分和性能與之相當?shù)?7010 合金。 這些高強鋁合金基本上都采用了過時 效熱處理技術(shù)(如T74和T76), 具有高的強度、高的耐應(yīng)力腐蝕性能和斷裂韌性。 特別值得指出的是,7050鋁合金的淬火敏感性低于7075,當7050-T74板材的厚度提高到 150 mm 時,其強度仍然可達約500MPa, 具有比7075-T74更低的淬火敏感性。
經(jīng)典的 2024 鋁合金, 也通過降低 Fe 和 Si 雜質(zhì)含 量, 提高合金純度和冶金質(zhì)量, 發(fā)展了系列改進牌 號, 如 2124, 2224, 2324 等[8]. 合金純凈化和微合金化 理論和技術(shù)推動了第三代高強、高韌鋁合金的發(fā)展。
上世紀 80 年代中期, 2219合金通過調(diào)整 Fe 和Si 雜質(zhì)總量與 Fe/Si 比, 發(fā)展形成 2519 合金, 2219和2519 合金被用作超音速飛機的多種構(gòu)件、緊固件和蒙皮的制造,2519合金還被廣泛用做兩棲突擊車的 裝甲。
上世紀70年代末至80年代末,能源危機促使飛機設(shè)計向強烈減重方向發(fā)展, 要求武器裝備增加 射程和提高有效載荷。高比強度和高比模量材料的需求推動了Al-Li合金的研制和應(yīng)用。 Al-Li合金因其密度低、比模量高等優(yōu)點,引起了材料工作者極大的興趣。隨著Al-Li合金熔煉和鑄造技術(shù)的發(fā)展,國外發(fā)展了進入工程應(yīng)用的Al-Li 合金。歐美國家研發(fā)的是 Al-Li-Cu 系合金,如2090,2091,8090和8091等, 俄羅斯開發(fā)了密度更低的 Al-Li-Mg 系合金,如1420和1421等。1420和1421合金在俄羅 斯軍機和航天器上得到了較廣泛的應(yīng)用。
上世紀 80 年代末至 90 年代末, 鋁合金成分高 合金化與優(yōu)化設(shè)計及組織精確調(diào)控技術(shù)的發(fā)展推 動了第四代高強、高韌、耐蝕、高耐損傷鋁合金材料 的研發(fā)。 發(fā)展新一代大型飛機提出了更高的安全性 要求, 飛機的損傷容限設(shè)計設(shè)有“破損-安全”結(jié)構(gòu)要 求, 對飛機主體結(jié)構(gòu)破損后的剩余強度以及從初始 裂紋到臨界裂紋擴展的壽命提出了明確要求, 因而 對鋁合金材料的疲勞裂紋擴展速率、斷裂韌性、抗 應(yīng)力腐蝕性能等提出了更高的綜合要求。 新型鋁合 金材料研發(fā)遇到的首要難題就是強度與斷裂韌性、 耐蝕性和疲勞裂紋擴展速率間的矛盾。 雖然 70 年代 后期, Alcoa 聯(lián)合 Boeing 公司研制了 7050 的改型合 金 7150, 但直到 80 年代, Alcoa 才成功研制了 7150- T77 材料的三級時效精密熱處理技術(shù), 第一次實現(xiàn) 在不犧牲合金強度的同時, 滿足斷裂韌性、抗腐蝕 性能和抗疲勞性能要求的目標, 因此, 7150-T77 材 料獲得了廣泛應(yīng)用[3,18]. 隨后發(fā)展的 7055-T77 合金 其強度比 7150-T77 合金高約 30~50 MPa, 而韌性、 耐蝕性能相當, 是目前使用的強度最高的航空鋁合 金材料[19]. 與 Alcoa 研發(fā)的 7055 合金同期發(fā)展且性 能相近的, 還有法國鋁業(yè)公司的 7449 鋁合金等。
針對飛機蒙皮的高耐損傷性能要求, Alcoa 通過進 一步降低 Fe 和 Si 等雜質(zhì)含量、添加微合金化元素、 優(yōu)化主合金成分及采用先進的熱處理制度等技術(shù) 途徑, 成功研制了高耐損傷的 2524-T3 材料。 超強高韌耐蝕的 7055-T77 合金和高耐損傷的 2524-T39 合金成功應(yīng)用于B777的上翼壁板和機身蒙皮, 被視 為第四代航空鋁合金材料的典型代表。鋁合金的微合金化在上世紀 90 年代以后引起了人們的極大興趣。 微合金化元素也突破 Cr, Mn, Ti和 Zr 的范圍, 向其它元素(Sc, Er 和 Ag 等)擴展。
在上世紀 90 年代中期, 由于 Ag 在 2×××系鋁合金中微合金化形成新相的原子團簇或新相作用機理和效應(yīng)的發(fā)現(xiàn),成功研制了原型合金C415和C417.該系含 Ag 合金具有良好的塑性、韌性和耐熱性能, 可在 200 °C高溫下長期使用。 含有 0.15%~0.6% (質(zhì)量分數(shù))的 Ag, 厚度達 152 mm 的高損傷容限 2139-T8×板材性能優(yōu)于 2×24-T3×, 在超音速軍機上得到了應(yīng)用。
隨著對 Zr 和 Sc 在鋁合金中微合金化作用機理 研究的不斷深入, 俄羅斯和美國都開發(fā)了一系列的含 Zr 和 Sc 的 2×××系、7×××系, 以及5×××系鋁合金, 并在戰(zhàn)機、艦載機及航天器上得到廣泛應(yīng)用。同時期, 隨著Al-Li-Cu系合金的研究和微合金化技術(shù)的發(fā)展, 美、俄等國開展了新一輪 Al-Li 合金 的研究。 俄羅斯主要開發(fā)了 1460 合金, 美國主要開發(fā)了 Weldlite 系列合金和 2097, 2197 和 2195 等 Al- Li 合金。 2097-T861 合金已在 F-16 飛機的后機身 隔框、中機身大梁上應(yīng)用。2198-T8×合金具有高 強、高損傷容限及高熱穩(wěn)定性, 良好的成形和焊接 性能。 21 世紀初, 研發(fā)了 2098, 2198, 2099 和 2199 等新一代 Al-Li 合金。
進入21世紀以來, 在大規(guī)格高性能鋁合金材料的強烈需求牽引下, 鋁合金成分與多相組織對性能影響機理與材料制備過程多物理場調(diào)控方法等研 究不斷深入的有力推動, 促使新一代高強高韌低淬 火敏感性鋁合金的產(chǎn)生與發(fā)展。飛機的先進性、經(jīng)濟性和舒適性設(shè)計, 以及航 空公司面臨的環(huán)保和降低飛機運行成本等方面的 壓力, 使飛機減重和提高燃油效率成為航空工業(yè)十 分緊迫的課題。 除降低合金的密度外, 構(gòu)件設(shè)計減 重也是實現(xiàn)飛機減重增效的一種有效方法。 構(gòu)件整 體化、大型化可免去大量傳統(tǒng)的鉚接, 既實現(xiàn)了結(jié) 構(gòu)減重, 又提高了可靠性。 構(gòu)件整體制造對鋁合金 材料的規(guī)格/截面厚度、綜合性能以及均勻性都提出了更高需求。
制備大規(guī)格、厚截面、性能均勻的鋁合金材料遇到的首要難題是高強鋁合金的淬火敏感性隨強度升高而增加。以7050合金的成分-強度-淬火敏感 性為參照, 通過降低Cu和Mg含量, 提高Zn含量,發(fā)展先進的噴淋淬火等可控快冷技術(shù), 建立析出相 η 的熱力學(xué)參數(shù)和析出動力學(xué)行為,發(fā)展了高強高韌 低淬火敏感性 7040, 7085, 7140 和 7081 等新一代低 淬火敏感性鋁合金。如圖2所示, 7085鋁合 金與此前應(yīng)用的高強 7075,7050 等鋁合金相比, 其淬火敏感性明顯降低。與美國鋁業(yè)公司7085合金同期發(fā)展且性能相近的, 還有法國鋁業(yè)公司的 7140 合金、德國愛勵鋁業(yè)公司的7081合金等。
在提高2524合金材料的耐損傷性能的基礎(chǔ)上, 針對其強度偏低的問題, 通過 Cu 和 Mg 主成分 優(yōu)化設(shè)計和降低 Fe, Si 和 Ti 雜質(zhì)含量, 美鋁和法鋁 又相繼研發(fā)出了具有高強高損傷容限特性的 2026 和 2027 合金。 其擠壓件(12~82 mm 厚)和板材(12~ 55 mm厚)較2024合金的性能分別提高20%~25% 和 10%.
為了滿足大型飛機的機身蒙皮、機翼壁板(蒙 皮)的先進焊接(如激光焊、攪拌摩擦焊)和蠕變時效 成形制造要求, 法鋁研發(fā)了 Al- Mg- Si 系的 6056/ 6156, 2022和2023等鋁合金。
隨著復(fù)合材料性能的不斷提升,其在航空航天 結(jié)構(gòu)上的應(yīng)用已從次要承力件向主承力件擴展, 如 B787 和 A350 最新型飛機都大量使用了復(fù)合材料, 這給航空鋁合金的發(fā)展帶來了前所未有的競爭態(tài) 勢。 設(shè)法降低高強鋁合金密度、提高比強度和比模 量再次成為鋁合金研發(fā)的重要方向。 在本世紀初, 美鋁-波音提出了《航空 20/20 創(chuàng)議》, 歐盟也相應(yīng)地 啟動了機身整體制造計劃, 這些研發(fā)計劃提出將鋁合金成分設(shè)計、材料制備與大規(guī)格構(gòu)件制造流程相 結(jié)合, 開展材料/結(jié)構(gòu)的一體化創(chuàng)新研發(fā), 將現(xiàn)有飛機結(jié)構(gòu)減重20%, 效率提高 20%的目標。 因此,高強 鋁合金出現(xiàn)了宛如百花爭艷的發(fā)展局面。最近研發(fā)的低Li含量 Al-Cu-Li合金2050和2060體現(xiàn)了新一代高強鋁合金降低密度的發(fā)展趨勢。 厚至152 mm的2050-T851板材, 性能不僅優(yōu)于7050-T7451, 而且密度更低, 強度、韌性、疲勞裂紋擴展抗力及耐熱性提高, 替代 7050 合金可減重 5%.
回顧高強鋁合金的發(fā)展歷程可知, 飛機與航天器的結(jié)構(gòu)設(shè)計與高強鋁合金的發(fā)展相互促進, 既提升了高強鋁合金的基礎(chǔ)與應(yīng)用研究水平,又提高了裝備的結(jié)構(gòu)效率、壽命和可靠性。
2 高強鋁合金材料的研究熱點與發(fā)展趨勢
一代材料一代裝備, 現(xiàn)代鋁合金材料正朝著高綜合性能、低密度、大規(guī)格、高均勻性和材料/結(jié)構(gòu)一體化方向發(fā)展, 為航空航天、交通運輸和高端裝 備的高性能制造提供支撐。 大規(guī)格高綜合性能鋁合金材料是現(xiàn)代航空、航天、交通運輸輕量化發(fā)展的基礎(chǔ)材料, 也是高強鋁合金材料科學(xué)與工程研究的 熱點。
如上所述, 新型高強鋁合金的研發(fā)及現(xiàn)有材料 性能的提升都與鋁合金成分的創(chuàng)新相關(guān)。 但是, 當成分確定后, 實現(xiàn)高綜合性能的特征微結(jié)構(gòu)需經(jīng)過 復(fù)雜的制備工藝流程才能最終獲得, 其間冶金遺傳 效應(yīng)顯著, 各個制備環(huán)節(jié)均會影響微結(jié)構(gòu)的形成和 演變, 從而最終決定材料的綜合性能及其均勻性。 高強鋁合金材料的重要特征微結(jié)構(gòu)可概括為: 在 Al 基體上彌散分布著凝固形成的微米結(jié)晶相、高溫沉 淀析出的亞微米或納米彌散相、時效析出的納米亞 穩(wěn)相。 基體組織可概括為: 固溶體、晶粒、亞晶粒、晶 界/亞晶界、胞狀結(jié)構(gòu)、織構(gòu)、無沉淀析出帶、空位與 位錯等。 多尺度的第二相和復(fù)雜結(jié)構(gòu)的基體決定了鋁合金的性能,如圖 3所示。 值得注意的是, 除 第二相、晶粒等組織結(jié)構(gòu)外, 鋁合金材料宏/微觀織 構(gòu)也是研究人員關(guān)注的因素。
粗大初生相主導(dǎo)合金的斷裂。 微米級初生相 (0.5~10 μm)是Al熔體凝固結(jié)晶時首先在熔體中形 成的, 但在加工過程中不能消除。 非平衡結(jié)晶相是 熔體非平衡凝固結(jié)晶時形成的, 主合金元素(Zn, Mg 和 Cu)未能完全進入鋁基固溶體, 以鋁化物或 共晶相形式存在于凝固組織中。 非平衡結(jié)晶相 經(jīng)均勻化-形變-固溶處理, 可逐漸溶入 Al 基體中, 剩余部分為殘余結(jié)晶相。 Al 熔體中 Fe 和 Si 雜質(zhì)元素可與Al和其他合金元素形成多種不溶初生相、難溶非平衡結(jié)晶相, 其相界面上易形成空位、孔洞和裂紋, 降低材料的塑性、韌性和耐疲勞性能。 但合適的Fe和Si含量及其比例,也可提高材料的韌性與疲勞極限。
彌散相抑制基體再結(jié)晶從而主導(dǎo)了基體組織,包括晶界/亞晶界,對材料韌性、抗應(yīng)力腐蝕性能產(chǎn) 生協(xié)同效應(yīng)。 彌散相是鋁合金中微量過渡族元 素或稀土元素在鑄錠過程中先固溶于Al基體, 經(jīng)均勻化熱處理析出的亞微米或納米鋁化物第二相(10~ 200 nm)。 如圖4所示, Al-Zn-Mg-Cu合金引入Zr, Cr 和 Yb 多元微合金化元素后(單個添加或復(fù)合添 加), 形成共格或非共格的高熔點鋁化物。 這些高熔點鋁化物不但能有效釘扎晶界并形成彎曲的亞晶界, 而且可以改善合金的淬火敏感性。 所以該類相可主導(dǎo)材料的韌性、耐蝕性能和疲勞性能。
晶內(nèi)時效析出相(約10 nm)主導(dǎo)合金的強韌化, 晶界時效析出相主導(dǎo)合金的局部(應(yīng)力)腐蝕開裂。 納米時效亞穩(wěn)相是合金固溶淬火后經(jīng)時效處理沉 淀析出形成的第二相, 隨時效溫度升高和時間延長, 析出相形態(tài)、結(jié)構(gòu)及成分發(fā)生復(fù)雜變化。 隨著時效析出亞穩(wěn)相數(shù)量提高, 鋁合金強度提高, 但時效析出相相應(yīng)在晶界進一步富集成鏈狀,晶界斷裂成為斷裂的主導(dǎo)因素,合金的斷裂韌性和耐蝕性(應(yīng)力 腐蝕抗力)降低。 調(diào)控晶內(nèi)、晶界時效析出狀態(tài), 可在強度、韌性和耐應(yīng)力腐蝕性能方面找到最佳點。
鋁合金材料塑性加工的變形溫度、變形程度和 變形速度決定了基體組織的微結(jié)構(gòu)特征、織構(gòu)和形 變儲能, 以及材料固溶熱處理的具體工藝參數(shù)。 熱 加工過程中要使合金產(chǎn)生均勻塑性變形, 一般要防止發(fā)生動態(tài)再結(jié)晶, 合金固溶處理時也應(yīng)盡量避免 發(fā)生再結(jié)晶。 研究發(fā)現(xiàn), 對高強 7×××鋁合金采用逐 級升溫固溶、形變熱處理等方法, 既有利于抑制 再結(jié)晶, 又能促進 S 相(Al2CuMg)溶解, 從而提高合 金的強韌性和耐蝕性, 如圖 5所示, 同時降低淬火 敏感性。
大規(guī)格高性能鋁合金材料制備面臨挑戰(zhàn), 需要發(fā)展系列制備技術(shù),以達到組織細化、均勻化、亞穩(wěn) 化以及高綜合性能化的目標。近幾年,重點發(fā)展了 大錠坯的高潔凈化熔煉與均質(zhì)鑄造技術(shù)、大規(guī)格材 料的均勻強流變加工技術(shù)、均勻組織的熱處理精細 調(diào)控技術(shù)。此外, 為了減少或避免在制造過程中產(chǎn)生性能和材料損失, 設(shè)法發(fā)展材料/構(gòu)件一體化成形/成性多種制備加工技術(shù), 使材料制備與構(gòu)件制造兩者融合, 已形成了重要的發(fā)展趨勢。
2.1 高綜合性能鋁合金材料成分與組織模式的設(shè)計與制備
隨著相圖與第一性原理等材料計算軟件(如 Thermo-Calc, NAMD,Materials Studio 等)的推廣使 用, 加上現(xiàn)代微結(jié)構(gòu)與性能測試技術(shù)的進步,為研究主合金成分元素總量及其配比以及微合金化元 素的作用規(guī)律提供了方便。 在理論計算結(jié)果指導(dǎo)下 開展鋁合金主成分與微合金化成分的創(chuàng)新設(shè)計, 將 淘汰傳統(tǒng)“炒菜式”的合金設(shè)計方法。 不斷完善鋁合 金微結(jié)構(gòu)-性能理論與表征方法, 發(fā)展特征微結(jié) 構(gòu)-綜合性能關(guān)聯(lián)新原理與表征方法, 以探求材料高強度、高韌性、高模量、高耐腐蝕、高抗疲勞、高 耐損傷、高耐熱等性能的特征微結(jié)構(gòu)模式已成為鋁 合金研究的方向。 將鑄造、塑性加工及熱處理過程 中微觀組織與內(nèi)應(yīng)力演化仿真模擬、成形有限 元模擬與裝備適應(yīng)[67~69]以及性能評價系統(tǒng)相結(jié)合, 有力地促進了多尺度微結(jié)構(gòu)精細調(diào)控新原理與新 技術(shù)的發(fā)展。 總之, 將理論計算、模擬和實驗相結(jié)合, 新牌號合金的研發(fā)、性能的提升與應(yīng)用所需時 間可大大縮短, 效率大幅提高。
高合金化7×××系鋁合金材料的發(fā)展, 在發(fā)揮該 系合金高強特性的基礎(chǔ)上, 探索成分、析出相對強 韌性和淬透性協(xié)同的作用規(guī)律與機理。如圖6所示, 通過改變 Al-8Zn-xMg-1.6Cu 合金的 Mg 含量 (1#—1.0%, 2#—1.4%, 3#—2.0%), 可以調(diào)控合金的硬度與淬火敏感性。
而通過調(diào)整微量元素Cr, Mn, Ti和Zr, Sc等在高強 7×××鋁合金中的含量和種類, 能夠有效改善合 金的晶粒結(jié)構(gòu)、韌性和抗應(yīng)力腐蝕性能以及淬火敏 感性。 例如, 以 Zr 為微量添加元素的合金(如 7050, 7055, 7085等)比以Cr和Mn為微量添加元素的合金 (如7075, 7049等)具有更好的抗應(yīng)力腐蝕性能。 更重要的是, 含 Zr 的高強鋁合金具有較低的淬火敏 感性, 所以這類合金能廣泛應(yīng)用于大規(guī)格構(gòu)件的承 力件。 研究表明, 含 Cr 和 Mn 的彌散粒子相界面 和基體不共格, 從而使得淬火析出平衡相能夠優(yōu)先 在這種粒子的相界面上析出; 而含Zr的彌散粒子(Al3Zr)則具有與基體共格的界面,大幅降低了淬火 過程中平衡相在含 Zr 彌散粒子界面上析出的可能性。也有研究表明, 部分Al3Zr彌散粒子也能誘導(dǎo)淬火過程中平衡相的析出。 這是由于在再結(jié)晶發(fā)生的過程中, 晶界的遷移會導(dǎo)致 Al3Zr 彌散粒子發(fā)生共 格-不共格轉(zhuǎn)變, 如圖7所示。 不共格的Al3Zr 彌散 粒子相界面則會誘導(dǎo)淬火析出相的析出, 合金則變 得具有淬火敏感性。 所以淬火敏感性控制可以轉(zhuǎn)換 成彌散粒子種類或再結(jié)晶分數(shù)的控制。
綜上所述, 為了尋求均勻分布的微觀組織, 宜采用強應(yīng)變加工、分級固溶與淬火、多級時效、積 分時效熱處理等技術(shù), 以提高韌性、耐蝕、抗疲勞等本征性能, 以及淬透性、深沖性和可焊性等工藝性能。
2×××系高強鋁合金材料的發(fā)展, 在現(xiàn)有合金強韌性與抗疲勞特性的基礎(chǔ)上, 一方面需要不斷揭示 合金成分及析出相種類對強韌性作用規(guī)律與機理,如圖8所示, 當Cu/Mg比達到4.9時,可同時析出S相和 ω 相, 有利于提高韌性; 另一方面通過降低與優(yōu)化雜質(zhì)含量, 控制塑性變形和再結(jié)晶, 發(fā)展新的熱機械處理技術(shù), 可提升該類合金材料的強韌性和 耐損傷性能。
對具有高強、高韌、耐蝕、可焊等高綜合性能特性 的2519合金的成分進行優(yōu)化設(shè)計后得到2519A, 經(jīng)采用熱機械處理、間斷二次時效等技術(shù), 細化了 第二相、提高了時效析出相的分布密度, 大幅度提 高了合金的力學(xué)性能與抗彈性能, 如圖9所示。
Al-Li 合金材料的發(fā)展, 在評估該系列合金的密 度-比模量-比強度-各向異性的基礎(chǔ)上, 進一步優(yōu)化 Li 和 Cu 含量, 同時發(fā)展高潔凈度大規(guī)格材料真空熔鑄、控制軋制塑性變形技術(shù),以提高韌性、耐蝕性、 耐損傷性能和超塑性成形性能, 并降低材料的各向 異性。 除用 Li 元素合金化降低密度外, 人們還研究了 Al-Mg-Sc 合金, 但該合金由于強度較低, 還難以用于航空材料。
2.2 大規(guī)格/厚截面鋁合金材料的均質(zhì)制備
合金組織的非均勻性短板效應(yīng)是大規(guī)格/厚截 面材料設(shè)計與制備的難點和關(guān)鍵。 高強鋁合金材料 尺寸規(guī)格大、合金元素含量高, 組織與性能的宏/細觀不均勻性往往顯著。 凝固、加工、熱處理中流場、 溫度場和應(yīng)力場的不均勻作用, 往往會造成大規(guī)格 鑄錠成分的宏觀不均勻性及非平衡結(jié)晶相和雜質(zhì) 相等組織的細觀不均勻性; 厚截面材料形變與再結(jié) 晶組織的宏/細觀不均勻性; 熱處理組織與殘余應(yīng)力 的宏/細觀不均勻性。 為研究合金成分與組織引發(fā)的 材料本征特性和制備環(huán)境引發(fā)的多場分布不均勻 兩方面作用規(guī)律與機理, 近些年來, 研發(fā)了宏/細觀 組織均勻化的熔鑄、塑性加工、熱處理等關(guān)鍵制備技術(shù)。
2.2.1 高合金化大鑄錠的高潔凈化熔煉與均質(zhì)鑄造
大規(guī)格/厚截面高性能鋁材首先需要能穩(wěn) 定地生產(chǎn)出高品質(zhì)大鑄錠。 航空工業(yè)所需超高強度 鋁合金由于合金化程度高, 結(jié)晶范圍寬, 氧化、吸氣 嚴重, 易含氣夾雜, 成分宏/微觀分布均勻性難以控 制, 并且鑄造時極易開裂, 成品率低。 寬型厚截面、 大扁錠及大直徑高合金化均質(zhì)無裂紋鑄錠的熔煉、 鑄造技術(shù)一直是世界鋁加工界設(shè)法要解決的熱點問題。
高潔凈化鑄坯要求鑄錠的雜質(zhì)與氫含量越少、 潔凈度越高越好。 航空材料的氣體和雜質(zhì)含量都有 相應(yīng)的標準, 無熱裂和冷裂, 成品率高。 不同寬厚比 和直徑的 7×××系、2×××系鋁合金大錠坯成品率根 據(jù)規(guī)格各加工廠都有自己的指標要求。
因此, 對大錠凝固理論和過程進行了比較深入 的研究, 如熔體的凝固規(guī)律, 鑄錠的顯微組織、表面 特性、應(yīng)力應(yīng)變分布和變形規(guī)律等。 發(fā)展了多種先 進的 Al 熔體高潔凈化、晶粒細化、表面亮化的熔鑄 技術(shù), 如爐底電磁攪拌、多級氣渣雜聯(lián)除、變溫熔鑄、電磁-超聲復(fù)合外場鑄造、油氣混合潤滑鑄造、微 震鑄造、矮結(jié)晶器鑄造等技術(shù)。
2.2.2 大規(guī)格坯錠的均勻流變塑性加工
我國已先后建設(shè)了大規(guī)格材料加工的大型裝備, 并不斷研發(fā)了一些大規(guī)格合金材料的塑性加工技術(shù)。 針對 600~850 mm 開口度、4000 mm 寬以上的軋機, 10000~12000 t 預(yù)拉伸機, 12500 t 擠 壓 機, 40000~ 80000 t 的鍛壓機, 不僅要保證板材、型材、鍛件的幾何尺寸精度和表面質(zhì)量, 而且還要使塑性變形深 入、均勻, 控制材料的動態(tài)回復(fù)與動態(tài)再結(jié)晶并得 到預(yù)期的微觀組織和性能。 因此, 將產(chǎn)學(xué)研用結(jié)合, 針對不同合金和規(guī)格的產(chǎn)品, 開展了鋁合金超厚板 和中厚板的鍛軋、角軋、非對稱軋制, 型材等溫擠 壓, 模鍛件等溫鍛造等塑性加工技術(shù)的研究。
鋁合金厚板高向性能低是國際鋁加工界一直設(shè)法要解決的難題。 非對稱內(nèi)剪切軋制是一條值得 研究的技術(shù)途徑。 德國科布倫茨鋁合金材料加 工廠研發(fā)的蛇形軋制技術(shù),不同于平輥軋制與傳統(tǒng)的非對稱軋制, 能使厚板內(nèi)外層同時經(jīng)受剪切變 形, 消除厚板中間層因變形不能深入而留下的組 織, 可大幅提高厚板高向組織與性能的均勻性。 此外, 經(jīng)蛇形軋制產(chǎn)生的剪切組織和織構(gòu)組態(tài), 將會 引起板材強韌性、耐蝕性、抗疲勞、耐損傷及成形加 工性能的一系列變化, 該技術(shù)正在研發(fā)中。
2.2.3 大規(guī)格/厚截面材料組織性能均勻性的熱處理調(diào)控
該類鋁合金材料熱處理主要也包括 均勻化、固溶淬火及時效。 均勻化處理不僅需要溶 解沿厚向差別大的非平衡結(jié)晶相, 而且需要調(diào)控 Cr, Mn, Ti 和 Zr 等微合金化元素的高熔點彌散相的均勻析出, 以獲得最佳的控制再結(jié)晶的組織。 固溶處理要高溫溶解已析出的溶質(zhì)原子, 消除過剩相或加工過程中產(chǎn)生的第二相。 因此, 研發(fā)了分(多)級均勻化與固溶技術(shù)。 研究發(fā)現(xiàn), 7×××系鋁合金 鑄錠均勻化處理的冷卻速率不僅影響其變形行為 和固溶處理后的再結(jié)晶分數(shù), 如圖 10所示, 并最終影響成品的強度和延伸率。
淬火過程中, 由于厚板中心層晶界和相界上平衡相的非均勻析出, 導(dǎo)致合金在時效過程中無法提供足夠的強化相從而使整體構(gòu)件性能下降, 產(chǎn)生短板效應(yīng); 淬火殘余應(yīng)力大, 且分布不均勻, 即使采用預(yù)拉伸仍難以消除殘余應(yīng)力及其不均勻分布。 寬幅薄板淬火后往往板型差、翹曲, 大型擠壓型材淬火后扭曲變形、性能不均勻, 超長中空型材立式淬火上、下性能不均勻。 因此, 研究中厚板輥底固溶淬火-預(yù)拉伸、薄板氣墊爐固溶-淬火、中空型材臥式連續(xù)淬火、鍛件預(yù)壓縮、薄板輥矯的板型控制與殘余應(yīng)力消減技術(shù)已成為高端鋁材制備的熱點。
時效是決定最終性能的關(guān)鍵工序, 在提高材 料綜合性能方面已研發(fā)了一系列的時效技術(shù)。 美 鋁公司研發(fā)了 T77 回歸再時效(RRA)技術(shù), 該技術(shù) 的溫度-時間關(guān)系示意圖如圖 11 所示, 在調(diào)控鋁合 金的強度、韌性與耐蝕性方面取得了很大成功。 如圖 12所示, 通過 RRA 處理, 在提高韌性與耐蝕性 能的同時, 強度甚至可以高于 T6 態(tài)材料。 但該技術(shù) 時效溫度窗口窄, 難以在工程上解決多級時效過程 中厚截面材料宏/細觀組織性能不均勻的難題。 因此, 同時研發(fā)了集溫度、時間、外場等多因素產(chǎn)生累積效應(yīng)的多種中厚板時效熱處理技術(shù), 如積分時效、高溫預(yù)析出、多次時效處理等。 如圖13所示, 這些時效方法的共同特點是, 在大規(guī)格材料中 實現(xiàn)晶界相非連續(xù)析出, 晶內(nèi)相高密度析出, 減小 無沉淀析出區(qū)的寬度, 以保證高的綜合性能及其均勻性。
2.3 材料/構(gòu)件成形/成性一體化制備加工
采用大規(guī)格鋁合金材料制造整體構(gòu)件, 可以實現(xiàn)減重增效, 材料利用率大幅度提高, 材料與構(gòu)件制造技術(shù)的融合趨勢十分明顯。 整體大構(gòu)件的制造 過程十分復(fù)雜, 容易使材料消耗大, 其性能在制造 過程中損失大, 因此, 發(fā)展了材料/構(gòu)件成形/成性一體化制備技術(shù), 如框梁主承力結(jié)構(gòu)件局部選擇性增強、整體壁板構(gòu)件蠕變時效成形、超塑性成形 與固態(tài)擴散連接、激光焊接、攪動摩擦焊接等大規(guī)格構(gòu)件制造技術(shù)。
目前, 世界上最大的客機 A380 機翼整體上壁板(圖 14[137])采用超強 7055 鋁合金厚板, 先在平面狀 態(tài)下銑削出加強筋, 然后用蠕變時效成形技術(shù)實現(xiàn) 最終的成形/成性, 長達 33 m, 最寬處達 2.8 m, 厚度 在 3~28 mm 內(nèi)變化, 內(nèi)部加強筋條結(jié)構(gòu)復(fù)雜。 該結(jié)構(gòu)極大地提高了機身的可靠性、耐久性、耐損傷容限和承載能力, 使飛機服役年限提高到 40~50 年。
然而, 現(xiàn)代飛機大量使用的具有空氣動力學(xué)曲率要求的 2×××系鋁合金壁板、蒙皮卻還未見應(yīng)用蠕 變時效成形技術(shù)的報道。 其中一個重要原因是 2××× 系合金在蠕變時效成形過程中會出現(xiàn)所謂析出相應(yīng)力位向效應(yīng), 如圖 15所示。 Al-4Cu 合金在應(yīng)力時效時, 會出現(xiàn) Al2Cu (θ相)在平行于晶體有效 壓應(yīng)力的方向上不析出, 而在垂直方向上大量析出 的現(xiàn)象。 析出相應(yīng)力位向效應(yīng)會造成材料性能下降, 制約了蠕變時效成形在高性能 2×××系鋁合金構(gòu) 件上的應(yīng)用。
3 我國高強鋁合金材料的發(fā)展與應(yīng)用概況
我國高強鋁合金的研發(fā)主要受國內(nèi)航空航天工程發(fā)展的牽引作用和國外高強鋁合金相關(guān)技術(shù)發(fā)展的推動作用, 其 60 多年的發(fā)展, 也大致經(jīng)歷了 5 個階段, 并與國際差距逐漸縮小。 如表 2 所示, 我國研制和生產(chǎn)的鋁合金材料支撐了不同時代的各種類型戰(zhàn)機、導(dǎo)彈、衛(wèi)星、飛船等裝備的研制與批產(chǎn), 在高強鋁合金材料研發(fā)生產(chǎn)方面積累了豐富的生 產(chǎn)技術(shù)和工藝, 為保障國家安全作出了貢獻。 隨著 大飛機、載人航天、登月、高鐵等重大工程的啟動, 通過從國外引進與消化吸收, 并結(jié)合國內(nèi)制造, 基本上建成了具有國際先進水平的高強鋁合金材料生產(chǎn)的裝備和加工基地。
但是,我國鋁材研發(fā)的總體基礎(chǔ)比較薄弱。 我國自己研發(fā)的鋁合金牌號極少, 規(guī)格非常有限。 大飛機設(shè)計所需要生產(chǎn)的鋁合金材料產(chǎn)品的品質(zhì) 有待穩(wěn)定, 需逐步取得適航認證, 并建立自己的航空標準。
幾十年來, 我國鋁合金材料的研究和開發(fā)取得了很大的進展, 形成了我國自己的第一代、第二代、 第三代鋁合金材料及其批量生產(chǎn)的能力, 并研發(fā)了 如LC4, LC9, LY12, 2A12, 2A16, 7A04, 7B04, 7A50 和 7B50 等系列鋁合金, 形成了這些鋁合金材料的成 分與系列熱處理狀態(tài)[140]. 以某型號戰(zhàn)機為例, 所用鋁合金多屬第三代高強、高韌、耐蝕鋁合金材料, 全屬自主研發(fā), 形成了戰(zhàn)機批量生產(chǎn)需要的供貨能 力。 首次實現(xiàn)國產(chǎn)高純鋁合金在型號上的批量應(yīng) 用, 提高了國產(chǎn)航空鋁合金生產(chǎn)和應(yīng)用的整體水平, 加速了國產(chǎn)航空鋁合金的更新?lián)Q代, 豐富了戰(zhàn) 機用先進鋁合金材料體系。
大飛機工程所需高性能大規(guī)格第三代、第四代 鋁合金材料以及新一代高強、高韌、低淬火敏感性 鋁合金材料的研制與生產(chǎn)正在組織攻關(guān), 并取得了 很大進展。
4 發(fā)展我國高強鋁合金材料的建議
大規(guī)格高綜合性能鋁合金材料是我國國民經(jīng)濟和國防工業(yè)發(fā)展所需的一種量大的關(guān)鍵結(jié)構(gòu)材 料, 其發(fā)展需遵循材料自身的發(fā)展規(guī)律, 并結(jié)合國 家工程需求目標, 確定其發(fā)展方向。 我國缺乏專門 從事鋁合金材料的研究機構(gòu), 需要進一步加強產(chǎn)學(xué) 研用合作模式。 研究工作需突破跟蹤仿制模式, 要處理好解決現(xiàn)實問題與創(chuàng)新發(fā)展的辯證關(guān)系。
一方面需加強大規(guī)格高性能材料及其生產(chǎn)的 工藝技術(shù)和機理研究, 確保產(chǎn)品品質(zhì)的一致性、穩(wěn)定性能夠滿足國家工程的要求, 以及大飛機的適航 認證的要求; 另一方面要重視新一代鋁合金的前 沿性、基礎(chǔ)性的研究工作。 最近的研究發(fā)現(xiàn), 在 Al-Zn-Mg-Cu 合金淬火過程中, 會析出一種類似于 T1 (Al2CuLi)的強化相,這為開展低淬火敏感性鋁合 金的創(chuàng)新設(shè)計和材料研發(fā)提供了新信息。 總之, 在 對國際上的高強鋁合金材料的發(fā)展和知識產(chǎn)權(quán)情 況深入分析的前提下, 應(yīng)明確目標, 集中力量搶占 未來發(fā)展的若干基礎(chǔ)和應(yīng)用研究的制高點。 我們深 信, 不久的將來我國不僅是普通鋁合金材料生產(chǎn)的 大國, 而且也是高端高強鋁合金材料研發(fā)與生產(chǎn)的強國。
更多關(guān)于材料方面、材料腐蝕控制、材料科普等等方面的國內(nèi)外最新動態(tài),我們網(wǎng)站會不斷更新。希望大家一直關(guān)注中國腐蝕與防護網(wǎng)http://www.ecorr.org
責任編輯:王元
《中國腐蝕與防護網(wǎng)電子期刊》征訂啟事
投稿聯(lián)系:編輯部
電話:010-62313558-806
郵箱:ecorr_org@163.com
中國腐蝕與防護網(wǎng)官方 QQ群:140808414
免責聲明:本網(wǎng)站所轉(zhuǎn)載的文字、圖片與視頻資料版權(quán)歸原創(chuàng)作者所有,如果涉及侵權(quán),請第一時間聯(lián)系本網(wǎng)刪除。
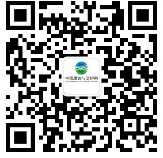
官方微信
《腐蝕與防護網(wǎng)電子期刊》征訂啟事
- 投稿聯(lián)系:編輯部
- 電話:010-62316606-806
- 郵箱:fsfhzy666@163.com
- 腐蝕與防護網(wǎng)官方QQ群:140808414