各國汽車整車防腐蝕標準
汽車由各種金屬零部件和非金屬零部件組成,在使用過程中不可避免地會遇到腐蝕問題,給社會造成了巨大的經濟損失。隨著社會的發展和人類生活水平的提高,人們對汽車舒適性和耐久性的要求也日益提高;另外,隨著消費者維權意識的不斷加強,因汽車腐蝕導致的召回事件也越來越多,這就要求汽車整車的防腐蝕性能必須與其使用壽命相適應。為此,發達國家的汽車廠商都制定了針對汽車整車的防腐蝕標準,見表1。
汽車防腐蝕應對措施
2.1 汽車產品設計過程中的防腐蝕措施
2.1.1 汽車產品用板材的選擇
車身板材的選擇非常重要,世界各國汽車行業普遍使用單面鍍鋅鋼板或雙面鍍鋅鋼板提高車身的耐腐蝕性能。根據瑞典腐蝕研究所的調查,7~ 10 μm厚的鍍鋅層具有良好的耐腐蝕性,2~5 μm厚的鋅-鎳層防腐能力小于7年。在青島海洋腐蝕研究所的腐蝕試驗場,發現采用相同涂裝工藝、但板材不同的2 個轎車車門8 年后的腐蝕情況出現了明顯差別:冷軋板車門由于空腔部位沒有泳上電泳漆或電泳漆膜偏薄,在第3年就已經出現銹蝕;而采用鍍鋅板的車門8 年后基本無腐蝕,見圖1。
目前國內絕大部分汽車廠的車身仍全部采用冷軋鋼板,只有個別合資企業生產的轎車車身車門等部位采用鍍鋅鋼板。因此,車身外表面用板材推薦采用電鍍鋅板和熱鍍鋅板等,車身內表面用板材推薦采用電鍍鋅、熱鍍鋅、鋁板、塑料和復合材料等。
目前為滿足車身輕量化的需求,高強度鋼板和超高強度鋼板、鋁合金板、復合材料(包括玻璃纖維、碳纖維和天然纖維增強塑料,熱塑性塑料和熱固性塑料)等在汽車上的應用會越來越廣泛。
2.1.2 汽車車身結構的設計
為保證整車防腐質量,車身結構設計應特別注意以下幾個方面。
2.1.2.1 接縫處的設計
接縫處的設計要保證外觀平整、光滑,且便于密封和/或防腐處理;同時,應按照汽車行進方向和水飛濺方向設計接縫開口,使之朝向水難以進入的方向,見圖2。
2.1.2.2 板斷面部位的設計
在圖3中,設計方式
①色圈內區域的漆膜易產生邊角效應,漆膜變薄,同時棱邊漆膜容易被石擊破壞,不利于車身的防腐;
②和③的設計方案比較好,板斷面底部漆膜有一個保護面,還可以采用噴涂PVC 的方式來防止漆膜過早腐蝕;
設計方式④的圈內的區域容易堆積淤泥并因此引起銹蝕,不利于車身防腐。
目前,歐洲市場的汽車普遍采用第②種設計方式。
2.1.2.3 工藝孔的設計
眾所周知,目前車身(駕駛室)100%采用電泳涂裝,為了保證良好的涂裝性(泳透性),車身(駕駛室)必須合理設置工藝孔的位置、大小和數量。
一般應遵循以下幾條原則。
a.通常電泳工藝孔的間距設置為150~200 mm。間距為150 mm 時,孔的直徑φ為15 mm;間距為200 mm時,孔的直徑φ為20 mm;
b.在封閉區域,內、外板應該交叉開孔;
c.車身搭接的板材之間一般要有3 mm左右的間隙;
d.盡量“借用”總裝裝配孔、焊接定位孔和沖壓定位孔;
e.增設電泳工藝孔時,盡量使其兼備排液孔及防氣泡孔的功能,以便使白車身出槽(脫脂、磷化、純水洗等)時攜帶的液體在工藝時間內及時排除,一般瀝液時間≤30 s。
f.增設電泳工藝孔時要考慮是否影響整車的密封性。
圖4為某轎車B柱開工藝孔的簡要說明。
2.2 汽車涂裝技術的防腐蝕措施
2.2.1 汽車耐腐蝕涂層結構
根據汽車總成及零部件在車上的位置、使用工況和涂層性能(包括耐腐蝕性能)要求不同,使用的涂裝材料及采用的涂裝工藝也不同。國內外各大汽車公司都有相應的關于汽車油漆涂層的企業標準,國內目前有效的標準是汽車行業標準QC/T484-1999《汽車油漆涂層》。
該標準根據汽車零部件的使用條件和涂漆質量要求,將涂層結構分為10 個組、17 個等級,每個級別都規定了不同的耐腐蝕性能。
隨著汽車工業的不斷發展,該標準亟需修訂。作者根據多年的工作經驗、大量試驗結果及目前汽車涂裝材料的性能,按汽車各個部位推薦幾種耐腐蝕的涂層結構及涂層所能達到的耐腐蝕性能,見表2。
注:
a.為必須采用的工藝;
b.為可以取消的工藝;
c.載貨車車架推薦采用環氧電泳涂料+噴涂快干聚脲底面合一涂料,中性鹽霧時間≥720 h,耐候性能≥500 h;
d.鑄鍛件涂裝要根據鑄鍛件表面粗糙度確定最佳膜厚。
經驗值是,涂膜厚度為產品材質表面粗糙度值的3倍以上,才能獲得良好的耐腐蝕性能。
2.2.2 汽車特殊部位的防腐措施
2.2.2.1 車底噴涂PVC涂料、裙邊噴涂抗石擊涂料汽車底板和輪罩等部位在汽車行駛過程中經常受到泥沙、碎石、鹽和污水等撞擊腐蝕,一般需要噴涂PVC 車底涂料;另外,轎車車門裙邊、發動機艙蓋和A 立柱等部位距離地面較近,一般要噴涂抗石擊涂料。
2.2.2.2 PVC焊縫密封
為提高車身抗腐蝕能力,所有粘接、焊縫或接縫部位在電泳涂裝后都應涂覆密封膠,避免水等介質的浸入而造成腐蝕。
2.2.2.3 內腔注蠟(灌蠟)、發泡
汽車內腔部位(如乘用車的前翼子板支撐板、立柱空腔、和車門下部空腔等)因焊接形成的焊縫、夾層和空腔由于屏蔽作用,電泳漆膜較薄、防腐蝕能力較差。為此,通常對這些部位進行噴蠟或注蠟(灌蠟)處理(內腔防銹蠟);高檔客車和微型車等進行發泡處理來提高整車耐腐蝕性能。
2.3 汽車儲運過程中的防腐蝕措施
為保證汽車(尤其是出口汽車)涂層在儲運過程中完好如初、無銹蝕現象產生,目前在儲運過程中普遍應用的防腐蝕措施有以下幾種,這些措施可以有效防止海水、鹽霧、高溫/高濕和日曬對涂層的侵蝕。
a.車身(駕駛室)噴涂面漆保護蠟、車身保護膜、貼附塑料保護膜、車身護衣等;
b.發動機和變速器等部位噴涂發動機保護蠟;
c.其它底盤件(如車架、車橋、傳動軸等)噴涂底盤防銹蠟;
d.車門、行李廂等活動鉸鏈處等噴涂合頁蠟。
汽車涂層耐腐蝕試驗方法及評價
3.1 試驗室樣板、樣件涂層的耐蝕性評價
20世紀90年代以前,都采用單純的中性鹽霧試驗來考核汽車涂層的耐蝕性能,依據的標準是GB/T-1771《色漆和清漆耐中性鹽霧試驗的測定》。第1版標準GB/T-1771-1991只有鹽霧試驗方法,沒有評價方法;目前最新版本是GB/T-1771-2007,增加了采用ISO方法對試驗結果進行評價的內容。
90年代中期,德國大眾PV1210循環交變腐蝕試驗方法被普遍用來考核涂層(當時只考核試驗室樣板及樣件涂層的耐腐蝕性能)的耐腐蝕性能,比單純的鹽霧試驗更接近汽車涂層的實際使用工況;日本馬自達公司也有相應的循環腐蝕試驗方法。
3.2 整車涂層耐腐蝕性能評價
2000年以后,海南汽車試驗研究所起草了汽車行業標準QC/T732-2005《乘用車強化腐蝕試驗方法》,2005年7月1日實施,用來考核整車涂層耐腐蝕性能,試驗場地是海南瓊海,目前只能對乘用車涂層耐腐蝕性能進行考核。德國大眾考核整車道路循環腐蝕試驗的方法是EP003.09,試驗場地在美國的鳳凰城。有關試驗方法的對比見表3~表5。
每種試驗方法的試驗條件各不相同,筆者通過大量試驗得出了幾種試驗方法之間的對比關系,見表6。
無論采用QC/T732 方法還是采用EP003.09 方法,做完整車道路腐蝕試驗后,都要拆車按評價等級進行腐蝕評價,見圖5。
3.3 涂裝線現場拆車進行泳透力測試
電泳質量(尤其是車身內部、縫隙、空腔部位的電泳漆膜厚度),直接影響整車的耐腐蝕性。目前,最普遍、也是最有效的辦法是對電泳涂裝后的整車進行剖車,驗證電泳涂裝的泳涂性,并根據泳透力結果,對產品設計進行修正。某汽車公司的評價方法是:在電泳涂裝前確定車身內表面(內腔)每個部位需檢測膜厚的位置及檢測的點數,然后剖解電泳涂裝后的被涂物(車身),按規定的部位及檢測點數測定漆膜厚度,與目標膜厚進行比較,合格率達到90%以上為合格。
圖6(圖中1~9是檢測的位置)是某轎車后車門內表面檢測部位及檢測點數的示意圖。
目前,國內外汽車公司公認的車身內表面、內腔電泳漆膜厚度的標準是:乘用車,車身內表面膜厚≥12μ m、內腔膜厚≥10 μm;中重型車,駕駛室內表面膜厚≥10 μm、內腔膜厚≥8 μm。
結束語
與國外先進汽車企業相比,國內汽車企業在產品設計、制造工藝、防護工藝和材料選擇等方面還存在一定差距。在汽車防腐技術方面,整車防腐水平與國外相當,但底盤零部件的防腐水平較低。雖然近年來已經對汽車防腐性能的重要性有了一定認識,但在企業產品開發體系中還沒有成立專門的腐蝕評價部門,在產品設計過程中也缺乏腐蝕評審流程。所以應盡快轉變國內汽車企業的觀念,提高企業對汽車防腐性能的認識,建立企業自己的腐蝕評價體系已是當務之急。
更多關于材料方面、材料腐蝕控制、材料科普等等方面的國內外最新動態,我們網站會不斷更新。希望大家一直關注中國腐蝕與防護網http://www.ecorr.org 責任編輯:王元 《中國腐蝕與防護網電子期刊》征訂啟事
投稿聯系:編輯部
電話:010-62313558-806
郵箱:ecorr_org@163.com
中國腐蝕與防護網官方 QQ群:140808414
免責聲明:本網站所轉載的文字、圖片與視頻資料版權歸原創作者所有,如果涉及侵權,請第一時間聯系本網刪除。
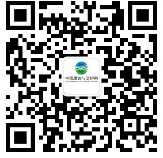
官方微信
《腐蝕與防護網電子期刊》征訂啟事
- 投稿聯系:編輯部
- 電話:010-62316606-806
- 郵箱:fsfhzy666@163.com
- 腐蝕與防護網官方QQ群:140808414