近些年來,能源和環境問題已成為人類關注的焦點,通過降低汽車重量來達到節能減排成為汽車生產企業的重要工作。應用鋁合金零件已成為實現汽車輕量化的重要途徑,副車架做為支承前后車橋、懸掛的支架,國外主機廠在中高端車型上使用鋁合金副車架,輕量化效果顯著。介紹了兩種鋁合金副車架成型方式:一種是壓力鑄造、鋁管液壓成型或鋁板沖壓焊接等單一的工藝直接成型;另一種是由鑄造成型、擠壓成型、鋁管液壓成型、鋁板沖壓等兩種或兩種以上工藝組合。
汽車保有量的快速增長帶來了能源和環境的雙重危機,汽車輕量化是實現節能減排的有效途徑。鋁合金材料具有密度小、成形性好、耐腐蝕性能優良的特點,成為實現汽車輕量化的重要途徑,鑄造鋁合金和變形鋁合金在汽車車身、底盤和動力總成上得到大量應用。世界鋁業協會報告表明:汽車所有能耗的60%來自汽車自重,整車每減重10%,可降低油耗10%~15%。鋁合金的特性使它非常適合用于生產汽車零件。副車架做為汽車底盤重要零部件,歐系、美系和日系等高端車型上已成熟的使用鋁合金代替鋼鐵生產副車架。本文就汽車鋁合金副車架的應用現狀和成型工藝作簡要介紹。
1、副車架輕量化途徑
圖1所示為汽車副車架輕量化技術途徑。副車架傳統生產工藝是先將鋼板沖壓變形,通過二氧化碳氣體保護焊接后成形,由于工藝簡單實用,至今仍然被用于中低端車型上。隨著對汽車品質要求的提高,國外主機廠將生產航空航天零件的液壓成型工藝用來生產汽車全框式副車架,采用鋼管液壓成型不僅可以減少生產工序,降低零件成本,而且液壓成形的零件精度、材料利用率和零件強度更高,因此現在國內外中高端車型上常被應用。鋁合金材料憑借良好的成形性能和輕量化效果,現在在奧迪、寶馬、奔馳、英菲尼迪、謳歌等國外中高端主機廠車型副車架上得到使用,成為實現汽車輕量化的有效途徑。
圖1 副車架輕量化技術途徑
2、鋁合金副車架成形工藝
汽車底盤副車架屬于重要的結構安全件,它連接和固定著懸架系統、轉向系統、發動機等總成零件,對其強度、剛度、模態、操穩等性能要求較高。為了降低副車架重量實現汽車輕量化,國內外各主機廠一直研究并且有的廠家已成熟地應用了多種不同成形工藝的鋁合金副車架。當前用于生產汽車鋁合金零部件的成形工藝有壓鑄成形、擠壓成形、鍛造成形、鋁管液壓成形和鋁板沖壓成形等,下面針對鋁合金副車架已成熟應用的各種成形工藝進行介紹。
2.1壓鑄成形
壓鑄成形是在一定壓力作用下使鋁合金熔體填充型腔,壓鑄成形零件具有組織致密、力學性能高、尺寸精密、加工余量小等特點,是汽車上應用最多的鋁合金零件成形工藝。鋁合金壓鑄成形根據副車架不同部位對強度、剛度、模態、安裝等要求,可生產出結構復雜的零件,滿足副車架各個部位不同性能的要求。相比傳統鋼板沖焊成形副車架,在降低重量的同時,減少了零件數量、焊接和組裝工序,提高了零件生產效率。但是鑄造鋁合金材料強度較鋼板的低很多,需通過對結構的調整和工藝的控制來滿足副車架總成性能要求。壓鑄鋁合金副車架常用材料為Al-Si系合金(例如Al-Si11、Al-Si7-Mg0.3、Al-Si7-Mg、Al-Si9-Mg-Mn等),最終零件的抗拉強度能達到270N/mm2以上。
圖2列舉了一部分車型應用的壓鑄成形鋁合金副車架。現在采用鋁合金壓鑄成形副車架的車型有歐系的大眾途觀、老款邁騰、大眾CC、奧迪Q3、奔馳C級、路虎攬勝,日系的英菲尼迪Q50以及美系的克萊斯勒200C等等車型。國內自主品牌廣汽也已通過高抽真空鑄造工藝研發出鋁合金副車架,并在傳祺系列車型的后副車架上成功應用。
圖2 一部分車型的壓鑄成形鋁合金副車架
2.2液壓成形
液壓成形工藝是利用液體作為傳力介質,通過模具使工件成形的一種塑性加工技術。液壓成形工藝可以減少零件數量、零件生產工序和模具數量,降低生產成本,同時提高零件剛度與強度。鋁合金材料伸長率較低,在向鋁管內充液快速加壓過程中易造成鋁管補料不足而起皺或開裂,鋁管液壓成形難度大。
如圖3所示,大眾汽車在其豪華車型輝騰上應用了鋁管液壓成形前副車架,重量僅為10.5kg,輕量化效果顯著,選用的鋁管材料牌號為Al-Mg3-Mn,材料抗拉強度可達到200N/mm2以上。
圖3 輝騰車型的鋁管液壓成形副車架
2.3多種工藝組合應用
2.3.1鑄造成形+擠壓成形
擠壓成形可生產截面復雜、壁薄等特點的零件,使零件尺寸精度高、表面質量好、強度較高。將鑄造和擠壓成形結合起來用于生產汽車副車架,不但可以滿足對副車架個別復雜部位結構設計的要求,同時可滿足副車架對強度和剛度的要求。汽車底盤常用擠壓鋁合金有5754(Al-Mg3-Mn)、6060(Al-MgSi0.5)、6005A、6063等。
鑄造+擠壓成形副車架通常使用擠壓成形工藝生產橫梁或縱梁;在副車架需要與車身或底盤其他部位連接的部位,結構變化較為復雜,采用鑄造成形工藝較為合適。通過MIG焊接將兩種鋁合金零件組裝在一起。如圖4所示,在雪鐵龍C5、凱迪拉克CTS和克萊斯勒Concorde等車型上,已應用這種組合工藝生產副車架。
圖4 幾種車型上采用鑄造+擠壓成形工藝生產的鋁合金副車架
2.3.2鑄造成形+擠壓成形+液壓成形
圖5中所示的奧迪A6及其同平臺下的A4和Q5等車型使用的鋁合金前副車架,其前橫梁結構簡單但強度要求較高,使用擠壓鋁合金型材滿足了強度和成形要求;左/右縱梁為鋁合金管液壓成形,保證了零件強度和結構要求;與車身、底盤和發動機等零件連接的部位需要相對復雜的結構,使用壓鑄鋁合金零件能夠滿足要求。三種工藝成形的零件通過MIG焊接組合在一起。
圖5中所示的寶馬5系和7系的后副車架,其后橫梁使用擠壓鋁合金型材;前橫梁則使用的是液壓成形鋁合金管;縱梁兩端需與車身連接,同時要為懸架系統控制臂提供安裝支座,鑄造工藝可同時鑄造完成,無需再焊接連接接頭和襯套等零件。
圖5 幾種車型上的鑄造+擠壓+液壓成形的副車架
2.3.3鋁板+其他組合工藝成形
與鋼板相比,鋁合金板雖然伸長率低、硬度小、沖壓成形性低,但各主機廠比較看重鋁合金板的輕量化的優點,通過克服設計和工藝上的難點,現已在汽車車身覆蓋件上大量應用鋁合金。國外主機廠也一直研究在副車架上使用鋁合金板代替鋼板生產零件。用鋁合金板代替鋼板,通過增加板料厚度和結構優化設計,來彌補鋁合金板在強度上的不足。如圖6所示,將鋁合金板與擠壓成形、鑄造成形和液壓成形工藝結合起來生產副車架也已得到實際應用。生產副車架常用的材料有6061、5754(Al-Mg3-Mn)等鋁合金厚度2.5mm~5mm板材。
圖6 幾種車型上采用鋁板+其他成形工藝生產的副車架
3、結束語
國外汽車主機廠越來越多的通過應用鋁合金來實現汽車減重。而國內鋁合金副車架受制于結構設計開發能力和鋁合金生產工藝水平的限制,同時國內自主研發的品牌車型主要是面向中低端市場,無法承擔較高的零件生產成本,故在國內自主研發的品牌車型中應用鋁合金副車架的較少。國內自主品牌汽車主機廠應逐步掌握鋁合金副車架的設計、工藝技術和積累生產經驗,逐步推廣鋁合金副車架的應用。
免責聲明:本網站所轉載的文字、圖片與視頻資料版權歸原創作者所有,如果涉及侵權,請第一時間聯系本網刪除。
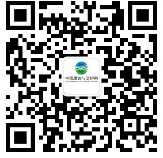
官方微信
《腐蝕與防護網電子期刊》征訂啟事
- 投稿聯系:編輯部
- 電話:010-62316606-806
- 郵箱:fsfhzy666@163.com
- 腐蝕與防護網官方QQ群:140808414