相較于航空領域,航天領域對于高溫合金部件的制造要求更加苛刻,呈現出更加復雜化、薄壁化、復合化、一體化等趨勢。以高性能液體火箭發動機燃燒室為例,其部件往往暴露在高熱、負荷等工作環境中,因此需要進行高效率的冷卻。傳統的減材或等材加工技術無法勝任此類獨特且巧妙的冷卻系統的制備。
增材制造具有超出傳統鑄造、鍛造制備工藝的成形制造能力,非常適合制備內含復雜內流道、多孔點陣結構等極難加工的結構構件,如火箭推進器耐高溫部件、助推器等,對未來空間探索至關重要,因此受到全世界的關注。
火箭發動機噴嘴頭是助推器的核心構件之一,在傳統設計中,該構件由248 個零部件裝配而成,ArianeGroup 利用增材制造技術將原來的248 個組件合并成一個構件(圖3a),克服了傳統加工工藝(鑄造、焊接及鉆孔等眾多復雜工藝步驟)耗時和在極端負荷環境中存在風險的缺點,真正實現了噴嘴頭一體化設計。DMRL 研究人員使用增材制造技術制備了升級版燃料噴射器(圖3b)。該構件采用66.4°橫截面設計,升級了零件的流道,移除了低應力區域材料,在零件底部引入了超輕網格結構增材制造構件,其抗壓、抗拉及硬度的測試結果優于傳統制造的IN718 構件,展示出增材制造技術在導彈終端的應用潛力。MSFC 利用DLMD 技術成功制備了IN 625 合金的整體推力室(圖3c),該推力室內部形成了完整的通道結構,可用于腔室的通道冷卻噴嘴部分。在主測試階段,噴嘴的壁溫超過732 ℃,證明DLMD 技術制備整體推力室的可行性。換熱器是航天設備長效穩定運行的關鍵部件,AddUp、Sogeclair 和Temisth合作,通過增材制造技術成功制備出薄壁(<0.5 mm)沒有泄漏且存在大量薄鰭片(0.15 mm)的IN 718 合金換熱器(圖3d)。該換熱器可確保對熱量的要求,能獲得與增材制造鋁制外殼相似的質量和性能,完美地體現了增材制造技術在制備復雜、精密部件領域的技術優勢。EOS 與Hyperganic 合作,通過計算機算法和人工智能創建了一件結構極其復雜的Aerospike火箭發動機模型。EOS 采用增材制造技術將其成功制備出來,該發動機高達80 cm(圖3e),其長度只有常規鐘型火箭發動機的1/4,質量只有航天飛機主發動機的2/3,與喇叭形噴嘴相比,這種獨特結構使發動機效率提高了15%。增材制造技術自由制造的特點為該新型火箭發動機的研制掀起了新的熱潮,是火箭推進領域的巨大進步。
圖3 激光增材制造的鎳基高溫合金航天構件
上述案例均極好地展示了增材制造技術作為一體化成形方法的巨大優勢。然而,在制備構件過程中,除考慮材料可用性、制備質量、成本外,還需考慮生產工藝可能構建的構件尺寸及特征分辨率。根據粉末輸送方式的不同,商用金屬增材制造設備可分為2類:基于鋪粉的LPBF 技術和基于同步送粉/絲的DLMD技術。前者成形精度高但零件加工尺寸受限;后者則不受尺寸限制但成形精度略低,后期需要進行加工以滿足使用需求。
免責聲明:本網站所轉載的文字、圖片與視頻資料版權歸原創作者所有,如果涉及侵權,請第一時間聯系本網刪除。
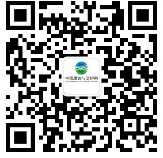
官方微信
《腐蝕與防護網電子期刊》征訂啟事
- 投稿聯系:編輯部
- 電話:010-62316606
- 郵箱:fsfhzy666@163.com
- 腐蝕與防護網官方QQ群:140808414