特種合金鋼表面處理類別
特種合金鋼表面處理過程中,在外界輸入能量、合金元素或材料,與產(chǎn)品表面交互作用,使得產(chǎn)品表層材料的物理化學(xué)特性發(fā)生劇烈改變。表面處理的微觀實質(zhì)就是材料表層發(fā)生可控的物理化學(xué)變化,具有不同于基體的優(yōu)異性能。
不同的能量輸入方式,使得材料表面產(chǎn)生物理化學(xué)效應(yīng),形成不同的表層結(jié)構(gòu)。根據(jù)特種合金鋼表面處理后產(chǎn)生的效應(yīng),可以將表面處理分為以下3類:
① 機械作用:特種合金鋼表面受到單純機械作用而導(dǎo)致表面改性,如噴丸 、輥壓、孔擠壓等表面形變強化,見圖1(a)。處理后表面具有抗疲勞性能。
② 物理作用:特種合金鋼表面由于能量作用而導(dǎo)致表面產(chǎn)生物理變化或者形成新的涂層,通過物理作用進(jìn)行表面處理的工藝較多,如表面相變強化、熱噴涂、表面離子注入、化學(xué)物理沉積和激光熔覆等表面處理,見圖1(b),(c),(e)。提高表面抗疲勞性能、耐磨、耐蝕性能。
③ 物理化學(xué)作用:特種合金鋼表面在能量 作 用 下 元素滲入擴散、反應(yīng)而導(dǎo)致表面改性,如滲碳、滲氮、碳氮共滲及其他金屬元素滲入等表面處理工藝,如圖1(f)。
圖1 表面處理技術(shù)
表面化學(xué)熱處理技術(shù)
利用某種元素的固態(tài)擴散滲入,來改變特種合金表面層的化學(xué)成分,以實現(xiàn)表面強化的方法稱為表面化學(xué)熱處理強化,也稱為擴散熱處理。包括滲碳及碳氮共滲、滲氮及氮碳共滲、滲硫及硫氮碳共滲、滲鉻、滲鋁及鉻鋁硅共滲、石墨化滲層滲硼、滲金屬等,種類繁多、特點各異。滲入元素或溶入基體金屬形成固溶體,或與金屬元素結(jié)合形成化合物。滲入元素既能改變表面層的化學(xué)成分,又可以獲得不同的相結(jié)構(gòu)。其中滲碳、滲氮等離子化學(xué)熱處理方式可以改變了特種合金鋼零件或構(gòu)件表面狀態(tài),提高耐磨、耐蝕、耐熱性能而應(yīng)用較為廣泛。
一 離子化學(xué)熱處理
離子處理真空爐體
離子化學(xué)熱處理設(shè)備的真空爐體主要有兩大類。一是水冷雙層爐壁,可分為鐘罩式、立式、井式多種規(guī)格,內(nèi)置1~2層隔熱屏(低碳鋼、不銹鋼或鋁合金制造),功率l0~500kW、有效加熱區(qū)直徑300~1700mm、高400~4000mm這種爐型結(jié)構(gòu)簡單、造價低、組合方便,但能耗較大、溫度均勻性較差、無法控制工件處理后的冷卻速度,該爐型主要用于離子滲氮處理;另一類爐型是帶油淬裝置的雙室離子滲碳爐,它的爐溫均勻性好、操作方便、工藝調(diào)節(jié)范圍寬,但結(jié)構(gòu)復(fù)雜、造價高、裝爐量有限(≤300kg),很少用于離子滲氮加工。近年來,隨著真空熱處理設(shè)備制造技術(shù)的發(fā)展和產(chǎn)品需求的提高,設(shè)備制造廠家又相繼開發(fā)了帶對流系統(tǒng)的熱壁真空爐體和帶高壓氣淬裝置的離子滲碳爐。前者是在冷壁爐的基礎(chǔ)上增加炭氈或硅酸鋁纖維保溫層、熱輻射加熱裝置及循環(huán)風(fēng)扇,提高了加熱區(qū)的溫度均勻性和工件混裝能力,降低能耗,工藝調(diào)節(jié)范圍大大提高,工件的升溫及冷卻速度均能較好控制,特別適于離子氮碳共滲等處理后需快冷的工件;后者多為單室結(jié)構(gòu),離子滲碳結(jié)束后通過高壓氣體淬火(國內(nèi)生產(chǎn)的設(shè)備最高氣冷壓強已達(dá)6bar, lbar=0.1MPa),消除了油淬對爐膛帶來的污染,工件光潔、形變量小,設(shè)備結(jié)構(gòu)和操作過程得以簡化。
離子化學(xué)熱處理電源
實際應(yīng)用較多的仍然是直流電源,電壓0~1000V連續(xù)可調(diào),滅弧系統(tǒng)主要采用限流電阻加上LC振蕩滅弧,少數(shù)采用電子開關(guān),但由于直流電源的固有特性,明顯存在一些不足:滅弧較慢,易燒蝕工件;由于空心陰極效應(yīng),引起狹縫和小孔過熱;無功損耗較大;工藝參數(shù)不易調(diào)節(jié);對電網(wǎng)干擾較大。脈沖電源的開發(fā)和應(yīng)用促進(jìn)離子化學(xué)熱處理技術(shù)發(fā)展。目前,脈沖電源的最大峰值電流已達(dá)300A,輸出電壓0~1500V,脈沖頻率10~20kHz,導(dǎo)通比0.15~0.8連續(xù)可調(diào),滅弧時間<10μs。
離子化學(xué)熱處理技術(shù)今后的發(fā)展趨勢之一為復(fù)合處理的擴大應(yīng)用。離子化 學(xué)熱處理滲層質(zhì)量高、綜合力學(xué)性能好,但形成表面強化層厚度有限、硬度梯度大、性能單一,不能滿足各種零部件的服役條件要求,只有采用復(fù)合處理技術(shù)才能解決這一矛盾。因此,復(fù)合處理技術(shù)得到了高度重視,如離子滲氮;氣相沉積(PVD, PCVD),離子滲氮;表面淬火(感應(yīng)淬火、激光表面淬火等),低溫鍍鐵;離子轟擊強化以及各種多元共滲和復(fù)合滲等。
二 特殊合金鋼滲碳工藝
滲碳的作用和過程
特種合金鋼滲碳工藝具有非常重要的實用價值。軸承、齒輪、模具、工具等特種合金鋼產(chǎn)品表層承受磨損、疲勞、機械負(fù)載及化學(xué)腐蝕等負(fù)荷作用,通過滲入碳等元素達(dá)到高的表面硬度、高的耐磨性和疲勞強度及耐蝕性。不必通過合金化或其他復(fù)雜工藝手段對特種合金鋼進(jìn)行處理。不僅降低成本,而且能夠保持心部淬火后的強韌性,使產(chǎn)品能承受沖擊載荷。符合節(jié)能、降耗,可持續(xù)發(fā)展的方向。滲碳一般選擇優(yōu)質(zhì)低碳或中碳合金鋼,它具有冷加工性能、耐沖擊、滲碳后耐磨、接觸疲勞壽命高等優(yōu)點。
滲碳處理對特種合金鋼選用具有一定要求。適合滲碳鋼的適宜含碳量在0.10%~0.25%,可以保證心部在淬火及低溫回火后仍具有足夠的韌性和塑性。
對于重載荷的滲碳零件,含碳量可達(dá)到0.25%~0.3%,進(jìn)一步提高心部強度。中高碳鋼不適宜進(jìn)行滲碳處理;中高碳合金鋼臨界溫度低于滲碳溫度,加熱到滲碳溫度勢必晶粒粗大,強度降低而影響使用壽命,不適合滲碳。滲碳用鋼要求較高冶金質(zhì)量,高純凈度、高均勻性、細(xì)晶粒化。保證產(chǎn)品各向同性并防止應(yīng)力集中而導(dǎo)致裂紋。選用低碳鋼進(jìn)行表面滲碳處理,滲碳濃度及其梯度和滲碳深度可以調(diào)節(jié),滲碳時間與滲碳深度關(guān)系如圖2,一般滲層深度在0.4mm以上。表面滲碳需在900℃以上保持較長時間,鋼中均添加鉻、鎳、鉬、錳等元素防止?jié)B碳過程中晶粒長大,滲碳后進(jìn)行淬火加低溫回火處理,獲得高硬度、高耐磨的表面及強韌的心部。
圖2 滲碳時間和滲碳深度的關(guān)系
滲碳工藝主要類型可分為氣體滲碳、固體滲碳、液體滲碳、離子滲碳。均包括以下3個過程。
① 分解:滲碳介質(zhì)的分解產(chǎn)生活性碳原子。
② 吸附:活性碳原子被鋼件表面吸收后即溶到表層奧氏體中,使奧氏體中含碳量增加。
③ 擴散:表面含碳量增加便與心部含碳量出現(xiàn)濃度差,表面的碳遂向內(nèi)部擴散。碳在鋼中的擴散速度主要取決于溫度,同時與工件中被滲元素內(nèi)外濃度差和鋼中合金元素含量有關(guān)
滲碳過程的關(guān)鍵問題
問題 |
預(yù)防工藝措施 |
碳濃度梯度問題;滲碳零件要求其碳濃度梯度小,保證滲碳零件沿截面的組織變化平穩(wěn)。碳濃度梯度在硬度上就為硬度梯度。對重要的鋼制零件,除了規(guī)定滲碳層的濃度、滲碳層深度外,往往還要規(guī)定滲碳工藝。碳濃度梯度與滲碳溫度、時間及滲碳介質(zhì)直接相關(guān)。不同的滲碳方法所采用的滲碳介質(zhì)是不同的。一般采用真空滲碳、離子滲碳時,碳濃度梯度小,氣體滲碳則可通過調(diào)節(jié)甲醇和丙酮(或煤油)的滴量來控制碳濃度梯度;固體滲碳則無法控制。 |
批量生產(chǎn)的齒輪應(yīng)盡量避免采用固體滲碳,采用固體滲碳時應(yīng)嚴(yán)格執(zhí)行操作工藝,裝爐量適當(dāng),催滲劑、木炭要混合均勻。滲碳箱放在爐內(nèi)溫度均勻的中間位置,滲碳過程中間適當(dāng)調(diào)換滲碳箱位置。氣體滲碳時,要注意爐內(nèi)氣氛充分循環(huán)、爐溫要均勻,清除齒面油污,裝爐量不宜過多,滲碳爐密封性能要好,漏氣的爐膛及時更換,定期檢修滲碳爐。淬火后滲碳齒輪表面硬度偏低將會導(dǎo)致齒輪耐磨性和抗疲勞性能降低,對齒面抗摩擦、磨損性能具有不利影響。 |
表面硬度偏低問題;導(dǎo)致硬度偏低主要原因為表面脫碳。通過金相檢查發(fā)現(xiàn)脫碳層是源于滲碳后正火或淬火過程中缺乏防護(hù)措施而產(chǎn)生的表面脫碳現(xiàn)象;冷卻速度太低,在顯微鏡下觀察,表層組織不是馬氏體組織,而是索氏體組織,金相觀察時針狀馬氏體耐腐蝕明顯,而索氏體較暗,易于腐蝕,顯微硬度計檢測明顯硬度差別大;齒輪滲碳溫度、淬火溫度偏高,造成淬火后表面殘余奧氏體量過多;齒輪材料淬透性差及淬火冷卻介質(zhì)冷卻能力不足;淬火后回火溫度過高,保溫時間過長。 |
對已造成齒輪表面含碳量低的齒輪采取適當(dāng)增碳處理;選擇淬透性合適的材料和適當(dāng)冷卻能力的冷卻介質(zhì),淬火冷卻;預(yù)先采取措施,減少淬火后的殘余奧氏體量,對含有過多殘余奧氏體的滲碳齒輪,進(jìn)行一次650~670℃ , 3h以上的高溫回火,析出部分合金碳化物,從而降低重新加熱淬火時的奧氏體穩(wěn)定性,促使奧氏體向馬氏體轉(zhuǎn)變;齒輪滲碳冷卻或重新加熱淬火時應(yīng)在保護(hù)氣氛下進(jìn)行,對已經(jīng)發(fā)生氧化現(xiàn)象的齒輪應(yīng)去除氧化皮,進(jìn)行表層滲碳后再進(jìn)行淬火;齒輪表層硬度偏低應(yīng)重新淬火,用合適溫度進(jìn)行回火。齒輪心部硬度偏低,齒輪材料的屈服點降低,易產(chǎn)生心部塑性變形,使齒輪表面硬化層抗剝落性能及齒根彎曲疲勞性能降低。 |
鋼的心部硬度偏低問題;特種合金鋼,諸如心部硬度偏低產(chǎn)生原因:齒輪材料淬透性差,齒輪材質(zhì)差,鋼材內(nèi)部帶狀組織嚴(yán)重;齒輪滲碳后,直接淬火前預(yù)冷溫度過低或滲碳后重新加熱淬火時淬火溫度偏低;冷卻速度不夠,金相組織觀察,不是低碳馬氏體組織,而是索氏體組織;心部有大量未熔鐵素體存在,是由于加熱溫度偏低或加熱時間不足造成。 |
選用冷卻性能好的冷卻介質(zhì)淬火,保證心部獲取低碳馬氏體組織;選擇適當(dāng)?shù)拇慊饻囟群图訜釙r間,保證心部獲得均勻的奧氏體,從而淬火后獲取馬氏體組織;選用淬透性好、材質(zhì)好的特種合金鋼作為滲碳齒輪材料。 |
等離子滲碳工藝
等離子滲碳爐在運行期間爐體加熱區(qū)十分清潔。處理工件后無炭黑產(chǎn)生,其原因有如下兩點:①由于滲碳期間強滲周期較短;②因為碳?xì)浠衔锓肿拥募ぐl(fā)和離化僅在陰極壓降區(qū)域發(fā)生,即直接在工件附近進(jìn)行。碳流量僅僅取決于帶電的等離子數(shù)值時(電流密度),用于氣體滲碳對爐體條件的傳統(tǒng)要求不能應(yīng)用于等離子滲碳之中。對于未生產(chǎn)的冷態(tài)等離子設(shè)備,須待首批工件達(dá)到工藝溫度后方可進(jìn)行滲碳處理,這樣所得到的結(jié)果才會與隨后其他所有爐次相同。此外,在等離子滲碳中,用增加滲碳循環(huán)次數(shù)來逐漸改變滲碳作用,避免在氣體滲碳中常發(fā)生的爐體燒壞現(xiàn)象。等離子滲碳處理無內(nèi)氧化,因而在低合金鋼表面區(qū)域附近避免了低硬度的屈氏體產(chǎn)生。其結(jié)果是改善了工件在等離子滲碳后的力學(xué)性能,如耐磨性及抗疲勞強度等。
若等離子滲碳過程可以被調(diào)整或校正的話,可抑制碳化物在平滑表面或 (正常矩形)尖角處的生成。在短的強力循環(huán)周期內(nèi)適當(dāng)?shù)乜刂铺剂髁縿t是一個決定性的因素。在低壓滲碳過程中,尖角處的碳化物形成是一個主要問題。應(yīng)用等離子滲碳由于采用了諸如低電流密度特殊監(jiān)測及很短的強循環(huán)周期等技術(shù),可以消除上述缺陷。16MnCr鋼制構(gòu)件經(jīng)930℃等離子滲碳后層深1mm, 870℃加熱油中淬火冷卻,160℃回火1h,只在最外端的尖角處顯現(xiàn)出少量碳化物。表面碳濃度是使用特殊顯微探頭來測量的,測得結(jié)果為靠近邊棱尖端的碳濃度為0. 9%C,而平面處為0.75%C。另一個特殊情況是在氣體滲碳中氫的活動能力較強,這只能靠用輔助處理的辦法予以減少。而應(yīng)用等離子滲碳,即使是在滲碳后期,氫的含量也十分缺乏,因此也就避免了所處理工件氫脆的產(chǎn)生。這是因為在等離子滲碳處理強循環(huán)期間,擴散進(jìn)入鋼中的任何形式的氫,在隨后擴散階段無等離子產(chǎn)生及真空的條件下,均從鋼中逸出。氫量至少減到即使有氫化物形成元素存在的情況下,也不會形成氫化物。
等離子滲碳技術(shù)優(yōu)點:不需對爐體進(jìn)行調(diào)節(jié);設(shè)備利用率高;生成無內(nèi)氧化的有利碳層結(jié)構(gòu);高合金鋼滲碳、淬火無軟點產(chǎn)生;滲層均勻性好;表面碳勢可進(jìn)行粗略及精確控制;具有極好的再現(xiàn)性;較短的滲碳周期;可用于較高的滲碳溫度;用簡單的屏蔽方法進(jìn)行局部滲碳;無環(huán)境污染;組成生產(chǎn)線的能力強。
三 特殊合金鋼滲氮工藝
滲氮工藝的作用和類別
滲氮是一種以氮原子滲入鋼件表面 ,形成一層以氮化物為主的滲層的化學(xué)熱處理方法。滲氮有三個基本過程:活性氮原子的產(chǎn)生、表面的吸收和氮原子的擴散。滲氮不僅可以提高工件表面的硬度、耐磨性以及耐疲勞性,而且還可以提高工件在腐蝕介質(zhì)中工作的耐蝕性。
常用的滲氮方法有:固體滲氮 、 液 體 滲氮、氣體滲氮、脈沖氣體滲氮 (氣體周期改變)、直流等離子體滲氮(又稱輝光離子氮化)、脈沖等離子體滲氮(電源周期供電)等。從滲入的機理來看,主要有兩大類:第一類基于濃度梯度:如液體滲氮、氣體滲氮等,這類滲氮通常采用電爐將采用的含氮介質(zhì)加熱,通過含氮介質(zhì)傳遞熱能,使被處理零件達(dá)到處理溫度,以濃度梯度作為氮元素滲入的驅(qū)動力。第二類基于電場的作用:如直流等離子體滲氮、脈沖等離子體滲氮等。在一定的真空條件下,通過微量的含氮氣體,利用輝光放電產(chǎn)生電子和離子,離子直接轟擊零件傳遞熱能,使被處理零件達(dá)到處理溫度,通過離子、活性原子與表面的復(fù)雜作用將氮元素滲入金屬表面。氮元素與零件的表面相互作用不盡相同,但在滲入金屬內(nèi)部后滲層深度的增長仍然符合擴散定律。
調(diào)質(zhì)處理后零件基體為回火索氏體組織,滲氮層深度可提高20%以上,硬度也有所提高,進(jìn)而提高基體強度和韌性及疲勞性能。為了減少零件滲氮后變形,在半精加工和精加工中增加一次消除加工應(yīng)力退火處理。溫度一般取550~600℃,保溫3~5h,變形量可控制在0.1%以下。
常規(guī)滲氮工藝
① 一段滲氮法、二段滲氮法、三段滲氮法
一段滲氮法又稱等溫滲氮。作為最初的滲氮工藝是在同一滲氮溫度下,長時間保溫的一種滲氮方法。滲氮溫度一般保持在480~530℃之間。工藝操作簡單,工件變形小;缺點是由于較長的工藝時間,滲層淺,易產(chǎn)生脆性層。為了縮短滲氮的時間,且保持較高的硬度,二段滲氮方法得到發(fā)展。二段滲氮工藝首先在500℃左右滲氮一段時間,使工件表面形成高度彌散的氮化物顆粒,保證一定的硬度。后升高到550℃左右繼續(xù)滲氮,加速氮原子擴散,以縮短滲氮時間,變形較一段滲氮大。三段滲氮是在二段氮化的基礎(chǔ)上發(fā)展起來的,進(jìn)一步縮短氮化時間。
② 催滲滲氮
為了縮短滲氮的時間,在滲氮介質(zhì)中添加一種或幾種起催滲作用的物質(zhì),即催滲滲氮:如加氮滲氮、加鈦滲氮等。加氮滲氮是在氨氣中加入氮氣,氮氣占混合氣體的30%~90%。不僅可以顯著縮短滲氮時間,而且還改善滲層組織,降低脆性。加鈦滲氮是在工件上鍍一層鈦后再滲氮,也可提高滲速。近年來發(fā)展起一種新的滲氮方法——電解氣相催滲滲氮。即將一定成分的電解氣體進(jìn)入滲氮爐中起到催滲作用,一般工藝時間可以縮短1/2~2/3。
③ 預(yù)氧化催滲氣體滲氮
氣體滲氮在工業(yè)上應(yīng)用較為廣泛,但滲氮周期長,成本高。研究表明,工件經(jīng)短時氧化后,表面會形成氧化薄膜,具有較強的催滲作用,能使N原子的滲入顯著加快。如在580℃下經(jīng)預(yù)氧化,滲氮兩次循環(huán)處理工藝(預(yù)氧10min,滲氮3h)可使采用滲氮溫度580℃,時間為6h時所形成的0. 29mm滲氮層厚度提高到0. 55mm,使氮化層的硬度梯度分布顯著獲得改善。
④ 等離子滲氮及復(fù)合化
離子滲氮是將工件置于輝光放電裝置的真空容器中,以工件為陰極,容器壁或另設(shè)金屬板作為陽極,充一稀薄的含氮氣體,在直流高壓的電場的作用下使氣體原子電離成離子撞擊工件陰極表面上,并向內(nèi)部擴散形成滲氮層的過程。離子氮化不僅能實現(xiàn)可控氮化、可局部硬化、使用純氫、氮氣為氣源無環(huán)境污染等優(yōu)點,且離子滲氮不生成脆性相,滲層致密,與氣體滲氮相比具有更高的耐磨性、耐蝕性和抗疲勞性能。離子滲氮要比氣體滲氮滲速快、熱效率高、設(shè)備維修費用低。近年來,離子滲氮技術(shù)發(fā)展迅速,離子滲氮與其他熱處理工藝相結(jié)合,進(jìn)行工件表面改性,提高工件的硬化質(zhì)量。如離子氮化與PVD離子鍍覆TiN工藝復(fù)合,可得到結(jié)合力良好的復(fù)合鍍層。處理后工件表面硬度極高,而且硬度梯度平緩,具有一定厚度硬度較高的擴散層支撐,有利抗磨性能提高,復(fù)合鍍層有良好的回火穩(wěn)定性,具有一定的耐蝕性。應(yīng)用于冷作模具和熱作模具等。除此之外,還有感應(yīng)淬火+離子滲氮復(fù)合處理;激光+離子氮化復(fù)合處理;表層硬化質(zhì)量的提高同時,其耐磨性、耐蝕性也隨之提高。此類復(fù)合處理作為新的表面處理技術(shù)廣泛地應(yīng)用于工模具中。
注:文章、作品、圖片版權(quán)歸作者享有,如有作者來源標(biāo)記有誤或涉及侵權(quán),請原創(chuàng)作者聯(lián)系小編刪除。
免責(zé)聲明:本網(wǎng)站所轉(zhuǎn)載的文字、圖片與視頻資料版權(quán)歸原創(chuàng)作者所有,如果涉及侵權(quán),請第一時間聯(lián)系本網(wǎng)刪除。
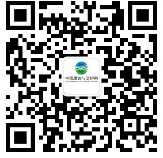
官方微信
《中國腐蝕與防護(hù)網(wǎng)電子期刊》征訂啟事
- 投稿聯(lián)系:編輯部
- 電話:010-62313558-806
- 郵箱:fsfhzy666@163.com
- 中國腐蝕與防護(hù)網(wǎng)官方QQ群:140808414