在石油化工行業, 熱壁加氫反應器已普遍取代了冷壁加氫反應器。這些熱壁加氫反應器大部分是由2.25Cr1Mo鋼制成的。加氫反應器在高溫高壓、臨氫條件下工作時, 構件材料面臨著介質腐蝕、應力腐蝕、氫腐蝕、氫脆、回火脆化等一系列問題。同時反應器內的硫化型固定床催化劑,由于積碳、金屬沉積或活性組分狀態的變化,催化劑的活性存在下降的情況、影響長周期運行。因此,加氫反應器工藝保護措施的制定尤為重要。
反應器工藝保護措施
01防止氫致開裂
正常操作過程中,在高溫高壓操作條件下,反應器的鋼材內部溶解大量氫原子。氫氣在鋼材中的溶解度隨溫度的降低而降低,隨壓力的降低而降低。在裝置停工過程中如果降溫速度過快,氫氣來不及從鋼材內部擴散出來,而出現過飽和狀態,超過鋼材的安全氫濃度,就會導致機械性能下降,甚至開裂。
由于氫氣在母材與奧氏體不銹鋼堆焊層中的溶解度和擴散速度不同,將在過渡層上吸存大量的氫,且因二者的線膨脹差別較大,而形成很大殘余應力使母材與堆焊層出現剝離現象。因此,在裝置停工過程中,需進行一定的“恒溫氫解”操作,防止損壞設備。
在裝置停工過程中,反應系統熱氫帶油結束之后,首先以0.5-1.0MPa/h速度將高分壓力降低至操作壓力的1/3左右,以10-20℃/h速度降低反應器入口溫度(一般比正常操作溫度低20-50℃),恒溫氫解12h,然后將反應溫度降低至250℃,恒溫氫解12h。
02防止連多硫酸應力腐蝕
奧氏體不銹鋼在高溫、硫化氫存在的條件下,設備與介質接觸的表面會形成一層腐蝕產物FeS。在停工過程中,當反應系統降溫降壓后有水汽冷凝下來或打開設備進行檢查檢修時,設備和管線內部的金屬表面與濕空氣接觸,FeS與水和氧氣接觸發生化學反應,生產亞硫酸和連多硫酸。連多硫酸會引起奧氏體不銹鋼晶間腐蝕,在晶間拉伸應力和連多硫酸作用下引起連多硫酸應力腐蝕開裂(PSCC)。
在裝置停工過程中需對反應器加以保護。裝有催化劑的反應器,先充氮氣保護,保守氮氣微正壓。卸催化劑必須在氣封閉的條件下進行,卸完催化劑后,反應器及內構件要立即進行中和清洗。中和清洗的中和液一般適用1.5%-2.0%的Na2CO3溶液,不得適用NaOH等強堿,以避免導致鋼材應力腐蝕開裂,中和液中Cl-濃度不能超過20ppm。在中和液中增加0.5%的硝酸鈉,可以防止氯化物應力腐蝕開裂。
強制循環中和清洗時間為4h以上,靜止浸泡時間在6h以上,噴淋沖洗應該保持表面堿液濕潤2h以上,并用塑料布覆蓋,沖洗時候順序從上往下,每個角落都要沖洗到,拆下的內構件應盡快放入堿液中浸泡,時間不小于6h。中和清洗完畢后,用軟化水清洗干凈,清洗完后反應器用干燥空氣吹掃。
03防止回火脆性
熱壁結構與冷壁結構相比有許多優點,冷壁結構不僅有效容積利用率低(一般只有50%~60%),而且在使用中比熱壁結構更易產生局部過熱,給安全操作帶來危險,甚至被迫停產。
回火脆化是由于金相改變所致的韌性減少,長期在343℃—593℃條件下使用或在此溫度范圍內緩慢冷卻而導致材料的韌性劣化的現象,造成的損傷會導致災難性的脆斷。
受影響的材料主要包括2.25Cr1Mo 低合金鋼,3Cr1Mo以及高強度低合金CrMoV 轉子鋼。回火脆化不會顯著影響C0.5Mo 和1.25Cr0.5Mo合金鋼,但是其他高溫損傷機理會促進金相改變,從而改變材料的硬度或高溫延性。
為了使啟動和關閉時出現脆斷的可能性最小化,許多煉廠采用增壓程序把系統壓力限制在最大設計壓力的25%內,使溫度低于最小增壓溫(MPT)。
采用2.25Cr1Mo 低合金鋼制造的反應器,遵規定的最低加壓溫度為93℃ , 在開停工工過程中都嚴格地執行了熱態開停工方案,即在反應器壁溫度大于93℃時,才能升高壓力至反應系統設計壓力的1/4以上,同時升降溫速度要30℃/h。
加氫催化劑工藝防護措施
01監測控制原料金屬含量,防止催化劑失活
催化劑的失活可以分為兩種,一種是暫時性失活,可以通過再生的方法恢復其活性;另一種是永久性失活,無法恢復活性。金屬元素沉積在催化劑上,會促使催化劑永久失活。常見的使催化劑中毒的金屬有鉛、鐵、鎳、釩、砷、鈉、鋅、鈣等。
鉛中毒主要發生在重整原料預加氫過程,原料油中混有含鉛汽油,會造成加氫催化劑鉛中毒。
鐵、鎳、釩等重金屬有機物在臨氫條件下發生氫解,生產的金屬以硫化物形式沉積在催化劑孔口和表面,造成催化劑失活、床層壓降上升。一般加氫反應器需裝填加氫脫金屬劑,原料中的鐵離子含量控制在1.0mg/kg以內。
砷對加氫催化劑有中毒作用,含砷1.2%的催化劑,再生后的脫氮活性僅為新鮮催化劑的70%。一般汽油加氫類裝置應設置脫砷反應器,柴油加氫類裝置應重點監控常減壓柴油中的砷含量。
鈉、鋅、鈣等堿性金屬或堿土金屬對催化劑酸性中心具有中和作用,進而造成催化劑中毒。在加氫過程中,這些金屬的化合物很快發生氫解,沉積在催化劑顆粒之間和孔口,造成催化劑失活、床層壓降上升。
02強化過程控制,防止催化劑結焦還原
催化劑干燥階段,干燥介質禁止含烴,干燥過程中不得出現竄油、竄氣事故。
催化劑硫化階段,不得選擇烯烴含量過高的硫化油,升溫注硫速度不得過快,控制好各床層溫度。硫化結束后,應進行初活穩定或鈍化,不得直接進原料油。因初期活性較高,直接進原料油會導致催化劑快速結焦。
正常生產過程中,循環氫純度、氫油比、氫分壓、空速等指標不得低于設計值,監控原料中硫、氮、殘炭、烯烴、稠環芳烴等雜質含量,防止催化劑結焦。
裝置異常停電、停機等事故應急過程中,應盡快降低床層溫度、防止催化劑快速結焦。
裝置停工階段,對循環氫中的H2S濃度進行監測,一般要求不小于500?g/g,以防止催化劑還原。
03原料系統設置氮封
原料與空氣接觸,會發生氧化、生產膠質、瀝青質,進入反應器后,這些膠質會沉積在催化劑床層上,增加床層壓降,縮短裝置運轉周期。因此,原料油要采用氮封隔絕空氣。
04監測控制新氫雜質含量,防止甲烷化反應
新氫作為補充氫進入反應系統,其雜質CO+CO2過高、一方面降低了新氫純度,另一方面會在反應器內發生氫解脫氧(甲烷化)反應,放出大量反應熱,將引起反應器床層溫度波動,甚至會造成反應器床層超溫。一般CO+CO2含量規定不得大于30mL/m3。
05監測控制原料水含量
水對催化劑的活性和強度都會造成影響,嚴重時影響催化劑壽命。水汽化會增加裝置系統壓力,引起壓力波動。進反應器原料油中的含水量最大值為500 mg/kg,一般要求小于300 mg/kg。
06優化自動反沖洗過濾器運行
原料油中的各種雜質,會污染催化劑或使催化劑結垢、結焦,降低催化劑活性,造成床層壓降升高,縮短運轉周期。
通過自動反應洗過濾器的優化運行,可去除20?m的固體顆粒,完全去除掉原料油中的機械雜質和銹焊渣等雜質,同時過濾掉一部分大分子質量的膠質、瀝青質及焦炭等物質進入反應器,保護催化劑,防止床層壓降增大。
07焦化裝置采用無硅消泡劑
為減少焦化塔頂泡沫層的高度,在焦化塔中需注入消泡劑。若消泡劑含硅,其焦化汽油會攜帶硅進入加氫裝置,硅在加氫條件下生產易揮發的硅化物,在床層中遷移而穿透床層。催化劑上沉積3-5%SiO2時,就能封閉活性中心,使催化劑失活。因此,焦化裝置應采用無硅消泡劑。
08加氫裝置采用無磷阻垢劑
隨著生產周期的延長,原料油/反應產物換熱器管束內壁易生產一層結垢物,主要成分是稠環芳烴,難溶于水、油、酸、堿等溶液,影響長周期運行。為解決這個問題,通常在反應進料泵入口注入阻垢劑。若阻垢劑含磷化物,在加氫條件下會生產PH3引起催化劑中毒,使催化劑活性下降。因此,加氫類裝置加阻垢劑應采用無磷阻垢劑。
免責聲明:本網站所轉載的文字、圖片與視頻資料版權歸原創作者所有,如果涉及侵權,請第一時間聯系本網刪除。
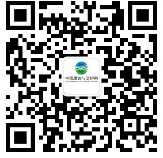
官方微信
《中國腐蝕與防護網電子期刊》征訂啟事
- 投稿聯系:編輯部
- 電話:010-62313558-806
- 郵箱:fsfhzy666@163.com
- 中國腐蝕與防護網官方QQ群:140808414