目前,微波組件殼體的材料主要有Kovar(可伐)合金(Fe-29%Ni-17%Co,質量分數)、鋁合金、無氧銅以及硅鋁合金等。鋁合金是一種很好的工程應用材料,具有質量輕、抗拉強度大、比剛度大和導熱效率高等優點,是微波組件殼體較理想的材料。鋁殼體外表面一般采用鍍覆鎳和金作為防護層和可焊層。國內外針對不同型號鋁合金的腐蝕行為做了大量研究,馮海濤等人采用干濕周浸加速法研究了五種質量分數不同的NaCl溶液對2A12鋁合金的腐蝕行為與規律。陳珊 [5] 等人用電化學試驗法系統研究了在不同pH值時質量分數3%的NaCl溶液中5083鋁合金的點蝕點位、自腐蝕點位及腐蝕質量損失,但對于鍍覆鎳和金鋁殼體的微波組件腐蝕行為卻鮮有報道。
本文通過電鏡觀察和成分分析系統研究了微波組件鍍覆鎳/金鋁殼體的腐蝕行為,詳細討論了微波組件生產和裝配過程中可能產生腐蝕的原因以及環境因素的影響。通過對腐蝕過程反應方程和腐蝕產物的研究闡明了微波組件鋁殼體鍍覆層開裂或剝落機理。通過對微波組件鋁殼體和鍍覆層的處理改善了鍍覆層的抗變色性和耐腐蝕性,從而對微波組件鋁殼體起到很好的腐蝕防護作用。
1 實驗過程與現象
本文微波組件鋁殼體材料為5A05鋁合金,其化學成分見表1。
加工好的5A05鋁合金殼體經清洗、烘干處理后進行電鍍鎳、金處理。電鍍完成的鍍覆層按照GJB1941-94《金電鍍層規范》對金鍍層進行高溫結合力試驗,結合力試驗合格的殼體經檢驗后進入裝配工序。某型號的微波組件鋁殼體裝配工藝工序包括:電路板貼裝、元器件貼裝、電子裝配以及芯片裝配。裝配完成后對微波組件進行初調,調試前鏡檢發現殼體鍍層有腐蝕斑點,鍍層明顯破壞,如圖1所示。
圖2為開裂鍍層處掃描電鏡照片,由圖2可以看出破壞點中心有大量白色粉末狀物質,周圍鍍層被頂起開裂或剝離。
2 結果與分析
腐蝕主要有三種:
1)一般性腐蝕。有害元素或離子接觸金屬部分直接腐蝕,如氧氣直接腐蝕。2)與水共同作用的腐蝕。腐蝕性元素在水的作用下對金屬進行腐蝕,如Clˉ金屬腐蝕,首先是Clˉ與金屬作用形成氯化物,氯化物水解后Clˉ又與金屬作用。3)電化學腐蝕。兩金屬電極在電場、介質和可電離離子的條件下,陽極金屬被逐步腐蝕,其中一種是原電池腐蝕,另一種是外電場作用的腐蝕。因此,本文主要從以下三個方面來分析微波組件鋁殼體的腐蝕行為:1)鍍覆工藝異常或鍍層厚度不達標,造成鍍層和基材之間結合力不牢,或鍍層厚度太薄造成抗腐蝕性不足;2)鍍后沾污,殼體鍍后在傳遞過程中人為污染,或后道工序造成腐蝕性介質附著在殼體鍍覆表面;3)產品暴露在高溫高濕環境中,加劇腐蝕。
2.1 鍍層分析
檢查電鍍過程中人、機、料、法、環各個環節,操作人員和設備都是固定的,電鍍液維護記錄顯示沒有異常,電鍍參數無變化,電鍍后對鍍層進行260~270 ℃100%烘烤檢驗,鍍層沒有起皮、起泡、色斑等異?,F象,鍍層結合力檢測無異常,由此可以看出,該產品鍍覆工藝正常,鍍層合格。對該失效產品失效區域(內腔上臺面)用熒光測厚儀對鍍層進行厚度分析,數據見表2。
由以上測厚數據可知,鍍層厚度正常。掃描電鏡對金鍍層進行了細致的微觀組織觀察,如圖3所示。由圖3可以看出,金鍍層微觀組織較為均勻、致密,但存在一定的孔隙,在一定條件下液體易通過孔隙滲透鍍覆層到鋁殼體本體。從鍍層結合力、鍍層厚度以及鍍層微觀組織三方面綜合分析表明,鋁殼體鍍層質量合格。
2.2 過程沾污分析
微波組件鋁殼體鍍覆日期為2016年6月18日,鍍后外觀檢驗正常,沒有發現鍍液殘留造成的色斑,因金鍍層對比度很高,清洗不完全造成的很少殘留都會在鍍層上留下明顯色斑,尤其是形狀復雜工件的邊角處更是會因為積液而形成色斑。該產品外觀檢驗正常,車間入檢也正常,因此可以說明鍍后清洗干凈,表面無鍍液殘留。該產品交付車間日期為6月20日,車間交付模電部為7月13日以后,在此期間車間進行如圖4所示的工作。
檢驗合格的殼體進入工藝裝配工序。由產品裝配過程可知,從鋁板材到微波組件產品經過多道工藝工序、多人參與并由多部門配合完成,產品的實現是依靠自動、半自動、手動結合的方式。微波組件鋁殼體在加工、電鍍、二次加工、裝配、調試、轉移和傳遞等各個環節,在殼體保護措施執行不徹底的情況下,有可能存在裸手觸摸殼體的現象,水、汗漬等多余物會沾污殼體表面,特別是鍍覆后殼體表面。因此對圖2中A和B區域進行成分分析,分析結果如圖5所示。
由圖5(a)成分分析可以看出鍍覆層剝落后5A05鋁合金處的成分除Al外含有大量的C、O、Na、Cl、Si等元素,其中C元素是由于污染造成。由圖2(b)掃描電鏡照片可以看出A區域鍍層剝落后呈粉末狀,這說明此區域產生化學反應有新物質生成。從整個生產、裝配過程來看Na、Cl等元素來源于汗液。
2.3 環境因素分析
操作間正常裝配環境:溫度18~28 ℃ ,濕度30%~70% RH。生產、裝配、調試等過程是在6月-8月進行,外部環境處于高溫、高濕狀態,產品在轉移等過程中多有暴露在外部高溫、高濕環境中。
3 機理分析
鋁及鋁合金在大氣中就能形成一層致密的 Al 2 O 3膜,一旦有水或大量水蒸氣存在, Al 2 O 3 外層轉化為薄層AlOOH,薄層AlOOH會轉化為Al(OH) 3 。薄液膜下的電化學腐蝕的陰、陽極反應分別如下:
陽極反應:Al - 3e - →Al 3+
陰極反應:O 2 + 2H 2 O + 4e - →4OH - (中性或堿性溶液)
O 2 + 4H + + 4e - →2H 2 O (酸性溶液)
Al(OH) 3 在一定條件下會水解為 Al 2 O 3 或在酸性條件下與H + 反應生成 Al 2 O 3 。當有Clˉ存在時,Clˉ會吸附在氧化膜表面,尤其是氧化膜不完整或缺陷處吸附更強。吸附的Clˉ與氧化膜發生化學反應,引起氧化膜的減薄以及金屬基體的直接溶解。鋁腐蝕成粉末狀氧化鋁后體積膨脹數倍,腐蝕產物相對疏松,較同質量的金屬體積更大,因此會引起鍍層的鼓起。當鍍層不能承受因腐蝕產物持續增多而引起的變形時,鍍層發生開裂或剝落。
3.31 改進措施
以某型號的微波組件為例,采取以下措施來提高鋁殼體鍍層的耐腐蝕性,從而對微波組件鋁殼體起到很好的腐蝕防護作用。
1)對鋁殼體組件鍍前進行磁針拋光處理、改善材料的表面狀態以提高鍍層結合力。
2)電鍍后組件應盡快徹底干燥,儲存在相對干燥的環境中,取用檢驗等過程中不要沾污,縮短檢驗傳遞等暴露時間并預浸SSC鍍層保護劑。某型號帶有鍍覆層的微波組件鋁殼體在不浸鍍層保護劑和預浸SSC鍍層保護劑后,按照GJB360(方法103)進行48 h和96 h穩態濕熱試驗,其結果見表3。
由表3可以看出,鋁殼體鍍覆層表面浸SSC鍍層保護劑后經48 h穩態濕熱試驗,鍍層依然完好,96 h后鍍層表面有輕微色斑。鍍覆層表面波導和輻射板相互位置精度。
3.3.2 真空釬焊夾具設計
合理的裝夾是保證零件獲得高質量釬焊接頭和平面精度的必要手段,其中最重要的是基準平板的設計。天線陣面高溫焊接過程中輻射板與輻射腔始終處于貼合狀態,以保證輻射板的焊接質量,要求基準平板能夠在高溫下保持足夠高的剛度和強度。因此,基準平板選用不銹鋼作為平板材料。同時,平板采用高筋狀網格框架和板狀工作面的釬焊結構。
4 實際應用效果
大尺寸高集成度機載平板裂縫天線的制造過程涉及工藝技術種類多,過程實現難度大。按照本文介紹的工藝方法,我們完成了某機載平板裂縫天線的零件精密加工、水道成型和整體精密焊接,經三坐標測量機和X-Ray設備檢測證明,輻射板、輻射腔和功分腔的精度和表面質量均達到設計要求,水道焊接滿足相關要求,天線焊縫釬著率高,天線焊接后面陣基本無變形,陣面均方根誤差小于0.1 mm,陣面扼流槽深度滿足設計使用要求。
5 結束語
本文提出了一種大尺寸高集成度機載平板裂縫天線的集成制造技術。首先介紹了該天線的一種集成制造流程,并重點研究了低剛性、高精度、薄板類零件精密加工技術、冷板深孔鉆及熔焊封堵技術以及天線真空釬焊及其夾具研制等三種關鍵工藝技術。最后,通過某天線的成功研制,驗證了本文介紹的研制思路的可行性,可為今后類似產品的研制提供借鑒。
更多關于材料方面、材料腐蝕控制、材料科普等方面的國內外最新動態,我們網站會不斷更新。希望大家一直關注中國腐蝕與防護網http://www.ecorr.org
責任編輯:殷鵬飛
投稿聯系:編輯部
電話:010-62313558-806
中國腐蝕與防護網官方 QQ群:140808414
免責聲明:本網站所轉載的文字、圖片與視頻資料版權歸原創作者所有,如果涉及侵權,請第一時間聯系本網刪除。
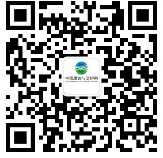
官方微信
《中國腐蝕與防護網電子期刊》征訂啟事
- 投稿聯系:編輯部
- 電話:010-62316606-806
- 郵箱:fsfhzy666@163.com
- 中國腐蝕與防護網官方QQ群:140808414