金屬材料的疲勞、應力腐蝕、高溫氧化等力學、物理和化學性能,很大程度上取決于材料的表面完整性。所謂表面完整性是指表面粗糙度、表層殘余應力、表層顯微組織、表層致密度和表面形貌等狀態的完好程度。大量的航空零件失效分析表明,屬于疲勞失效的零件約占80%,而材料的表面完整性是影響材料疲勞性能的重要因素之一。
噴丸強化技術是一種材料表面機械冷加工方法,借助高速運動彈丸流或高能沖擊波撞擊材料的表面,使材料表層發生彈塑性變形,呈現較好的表面完整性,從而提高材料的抗疲勞強度、微動疲勞抗力及損傷容限性能的一種表面強化方法。
在航空工業中,航空零件的表面完整性直接影響其使用性能和服役能力,特別是零件的疲勞使用性能。噴丸強化技術通過改變材料表面完整性顯著提高各類航空零部件的疲勞性能,且具有成本低、適應性強和操作方便等優點,在航空領域應用廣泛。
表層殘余應力
噴丸強化在材料表層引入殘余應力場,其中靠近受噴材料表面一側呈現為殘余壓應力,板材單面噴丸強化后的表層殘余應力分布特征曲線如圖1 所示。普遍認為殘余壓應力是提高工程材料抗疲勞性能和抗應力腐蝕性能的重要強化機制,而且殘余壓應力值大小、壓應力層深度對工件疲勞強度或壽命影響顯著。因此,如何實現殘余應力分布特征的調控是該領域重要研究內容之一。
殘余應力分布特征曲線包括5個主要特征參數:表面殘余應力值、殘余壓應力深度、最大殘余壓應力及其位置、最大殘余拉應力。彈丸撞擊材料表面時,通常與材料表面產生近似的赫茲接觸,形成的最大彈性應力出現在材料次表面,所以通常噴丸強化最大殘余壓應力位于次表面。在某些情況下,殘余應力分布特征發生變化,例如噴丸強化采用低密度的玻璃彈丸介質時,由于入射動能小,其噴丸強化鈦合金和鋁合金的最大殘余壓應力值出現在表面。當噴丸強化工藝為濕式噴丸強化時,硬質合金或鈦合金也會出現表面殘余壓應力值最大的現象,因為濕式噴丸強度一般相對較低(為干噴丸強度的1/3~1/4),且陶瓷丸介質密度相對較小,但隨著噴丸強度或覆蓋率提高,最大殘余壓應力逐漸向次表面轉移。激光噴丸強化工藝,最大殘余壓應力值通常出現在表面,因為激光噴丸時金屬表面的吸收層吸收激光能量后氣化產生高溫高壓的等離子體,等離子體發生爆炸產生沖擊波作用于材料表面,沒有形成赫茲接觸;高壓空化水射流噴丸,其形成的最大殘余壓應力也出現在受噴材料表面。
殘余應力的大小和分布特征受到噴丸強化工藝類型、工藝參數及材料自身屬性等諸多因素影響。殘余應力數值主要取決于受噴材料自身的屈服強度、晶體結構和加工硬化率。受噴材料屈服強度越高,殘余壓應力值越大。例如,屈服強度450MPa 鋁合金,最大殘余壓應力值在400MPa 左右;屈服強度900MPa 的鈦合金,最大殘余壓應力值在800MPa 左右;屈服強度1631MPa 的高強鋼,最大殘余壓應力值在1500MPa 左右。通常殘余壓應力值小于受噴材料的原始屈服強度,但有研究報道了殘余應力值超過受噴材料屈服強度的現象,研究者認為受噴材料表層在大量彈丸沖擊作用下發生大應變塑性變形,形成明顯的加工硬化或晶粒細化,導致受噴材料表層局部屈服強度升高,從而使產生的殘余應力值超過受噴材料原始屈服強度。受噴材料的強度越高,材料的塑性變形抗力大,入射階段系統動能衰減速度加快,噴丸強化變形層淺,殘余壓應力場深度變淺。具有顯微組織結構特征的受噴材料的殘余壓應力值分布具有方向性,如軋制板材在軋制方向與垂直方向的殘余壓應力值不同。
噴丸強化工藝參數,如噴丸強度、噴丸時間、彈丸介質和彈丸流量的選取對殘余應力值大小與分布的影響明顯。較高噴丸強度下,彈丸入射階段具有更大動能,接觸區受噴材料應力集中程度更大、變形層更深,所以最大殘余壓應力值提高、殘余壓應力層變深,但噴丸強度過大可能獲得相反的效果,主要由于應力松弛和表面剝層等因素的影響。噴丸時間作用主要局限于飽和時間內,最大殘余應力值和應力層深度隨噴丸時間延長而增加,達到飽和后數值基本穩定不變。彈丸流量直接影響到彈丸動能和100%覆蓋率時間,在一定噴丸氣壓下,彈丸流量大則噴丸飽和時間短,噴丸強度下降,進而影響殘余壓應力的大小及分布。彈丸直徑越大,噴丸強化越容易產生更深的殘余壓應力層。同濟大學高玉魁等研究了噴丸強度、噴丸時間、入射角度、彈丸種類等干噴丸強化參數對A-100 鋼殘余應力場分布的影響規律。
噴丸強化工藝類型也顯著影響最大殘余壓應力值和殘余壓應力層深度。以TC4 鈦合金為例,通常傳統機械噴丸最大殘余壓應力值約800MPa,壓應力層深度約0.25mm ;濕式噴丸最大殘余壓應力值和干式接近,但壓應力層深度較淺約為0.15mm ;激光噴丸最大殘余壓應力值約400MPa,壓應力層深度通常1mm 左右;高壓空化水射流噴丸強化殘余壓應力值達到1000MPa,殘余壓應力層深度約0.1mm。超聲噴丸包括彈丸式和撞針式,彈丸式形成的殘余壓應力分布特征和傳統機械噴丸接近,撞針式可能形成更大的殘余壓應力值和殘余壓應力層深度。
顯微組織結構
噴丸強化變形層是提高工程材料抗疲勞性能的另一個主要強化機制。在噴丸強化過程中,材料表層組織發生塑性變形,其顯微組織結構中的晶粒尺寸、物相結構、位錯密度和晶面取向等發生變化,構成變形組織強化層。變形強化層的組織呈梯度分布,由表面到內部基體,以雙相鈦合金TC17 為例,典型的組織分布為表面層的納米晶層、亞表面的細晶層、內部變形晶層和無應變的晶粒基體。
金屬材料組織的細化程度與噴丸強化過程中材料表面的應變和應變速率有關,噴丸強化層發生不均勻塑性變形,受噴材料表面應變和應變速率最大,沿著深度方向應變和應變速率逐漸降低,所以強化層組織呈梯度分布特征。變形強化層的組織細化作用對疲勞加載過程中材料晶體的應變起到阻礙作用,從而能夠提高材料的抗疲勞性能。此外,噴丸強化層中微納米組織中含有高體積分數的晶界,以及大量的位錯、空位、亞晶界等非平衡結構及能量貯存,有利于降低原子擴散激活能、提高原子擴散系數、促進原子化學反應。因此,噴丸強化技術也用于材料表面改性,也有益于改善金屬材料的擴散連接、滲氮(碳)等工藝性能。
噴丸強化層的組織細化機理通常認為是由于彈丸循環撞擊作用下接觸應力超過屈服強度,受噴材料表層產生位錯、孿晶、層錯和剪切帶等缺陷,缺陷交互作用后演變成微納米尺度胞狀組織、亞晶和晶粒。干式噴丸、超聲噴丸、激光噴丸和濕式噴丸等技術強化的受噴材料,都能夠在材料表面變形強化層形成納米晶層。噴丸強化層厚度和變形組織細化程度,受到材料自身屬性、噴丸工藝類型及其工藝參數影響。
對于傳統噴丸強化工藝,通過提高彈丸硬度、彈丸直徑、彈丸速度、覆蓋率以及噴丸強度來提高金屬材料的細化程度。對于超聲噴丸強化工藝,通過提高彈丸直徑、振動頻率、噴丸時間來提高表面的細化程度和變形層深度。對于激光噴丸強化工藝,激光噴丸的脈沖能量、激光噴丸次數、覆蓋率等均影響表面組織的細化程度。
不同噴丸強化方法的組織細化程度和影響層深度不一致。以鈦合金為例,通常傳統噴丸強化影響層深度約在200~500μm,納米層深度約在20~30μm。激光噴丸強化影響層深度可達1mm 左右,納米層深度約10μm左右。超聲噴丸強化通過調整適當的強化參數也可以使影響層深度達1mm,納米層則深達30μm。因此,超聲噴丸強化目前在材料表面實現變形組織細化的效果較為顯著,廣泛應用在Fe、Cu、Ti、Al、Mg 等合金以及非晶合金等表面納米化的研究中。
表面粗糙度
噴丸強化過程中高速彈丸撞擊受噴材料表面引起塑性變形,并在其表面形成凹坑,大量彈丸的撞擊和相互疊加作用使受噴材料表面形貌發生變化。通常噴丸強化使受噴材料的表面粗糙度變大,而且不當工藝參數甚至造成表面開裂、脫層、褶皺、破碎彈丸嵌入等表面損傷,損害金屬零件的抗疲勞性能。因此,噴丸強化處理受噴材料的表面粗糙度是一項重要控制指標。噴丸強化表面粗糙度影響因素、變化規律和后續處理工藝在工業領域受到廣泛關注。噴丸強化對材料表面粗糙度的影響,與材料屬性及表面狀態、噴丸工藝類型及參數、彈丸介質等多種因素相關。
噴丸強化工藝參數對材料表面粗糙度有顯著影響。噴丸強度越高,表面粗糙度越大。隨著噴丸時間增加,表面粗糙度值上升到峰值后逐漸下降,如圖3 所示。研究人員認為,初始階段表面局部變形顯著,材料表面變形不均勻,導致粗糙度增加;隨著噴丸時間增加,表面應變量增加,加工硬化嚴重,表面變形均勻化,導致粗糙度降低并趨向穩定。彈丸高速撞擊受噴材料后,材料表面受擠壓發生嚴重塑性變形,形成材料的凸起和凹陷,即形成了許多“峰”和“谷”。隨著噴丸時間的延長,彈丸對材料的覆蓋率增加,表面的凹坑數量增加,合金的表面粗糙度則繼續增加進而達到峰值。繼續延長噴丸時間,材料表面形成的“峰”和“谷”交替轉換,材料表面粗糙度則開始下降。當彈丸在材料表面產生的“峰”和“谷”達到平衡后,材料表面更趨于平整,表面粗糙度也達到穩定值。長時間噴丸雖然可以降低粗糙度,但容易誘發材料表面發生剝層或褶皺缺陷,不利于材料抗疲勞性能的提高。
另外,在噴丸強化過程中噴射角度越大(噴嘴入射方向垂直于受噴材料表面時入射角為0°),彈丸速度的法向分量越小,彈坑越淺,彈丸的切向速度越大,彈丸對表面的研磨作用就越大,表面粗糙度值就越小。彈丸介質的選取也是調控表面粗糙度的重要因素,如彈丸直徑、圓整度、彈丸硬度等。通常直徑小、圓整度好的彈丸,容易獲得均勻光滑的表面,光滑表面有利于維持殘余應力穩定性,增加抗疲勞性能,如微粒噴丸強化技術、復合噴丸強化技術等。
從噴丸工藝類型角度,相對于傳統干式噴丸,激光噴丸、濕式噴丸、高壓水射流噴丸和超聲噴丸(彈丸式)的表面粗糙度較小。例如,7050 鋁合金在常規S110 彈丸噴丸強化下表面粗糙度Ra 值超過4μm,而激光噴丸強化表面粗糙值降為1μm。在相同噴丸強度下,如圖4 所示(Ra 為平均粗糙度,Rmax 為最大粗糙度深度,Rz為平均峰谷深度),超聲噴丸強化的粗糙度值為傳統干式噴丸的1/3 甚至更低。超聲噴丸設備使用的丸粒與傳統方式不同,噴射介質除傳統形狀的丸粒外還有兩端為不同曲率半徑的噴針,丸粒材質一般選用硬度較高的鎢碳鋼或軸承鋼等,對丸粒的圓度和表面光潔度要求也更高,在噴丸室內丸粒的速度方向隨機,而且速度較低,這些因素都使超聲噴丸處理后的工件表面粗糙度值下降。空軍工程大學研究表明,表面光滑不銹鋼(Ra 值為0.419μm)經激光噴丸強化處理后Ra 值為0.584μm,激光噴丸強化后受噴材料表面粗糙度值增加較小。濕式噴丸由于加入了液體潤滑,有效地降低了彈丸與受噴材料表面的干摩擦,表面粗糙度較傳統干式噴丸強化也明顯改善,大連理工大學陳國清等利用“干式噴丸+ 濕式噴丸”的復合噴丸工藝,既實現了在鈦合金表層形成較深的殘余壓應力層,又有效控制了材料表面粗糙度。
表層硬度
硬度是顯微組織加工硬化程度的一種表征,與噴丸變形層組織存在對應關系。噴丸變形層的硬度呈梯度分布,表面硬度值最高,沿深度方向硬度值逐漸降低,最終趨向基體硬度。噴丸應變硬化效果主要取決于微觀組織細化程度,同時與位錯密度、固體相變程度相關。
噴丸強度是調控硬度層分布特征的直接有效手段,如圖5 所示,噴丸強度越高,表面硬度值和硬度層深度越大。在循環硬化- 軟化作用下,硬度存在極限值,見圖6。鎂合金通過噴丸強化處理,表面硬度從60HV提高到135HV。對于300M 鋼噴丸,噴丸強化后表層殘留奧氏體發生相變,轉變為馬氏體組織,硬度大幅度提高。在一定噴丸強度下,隨噴丸時間增加表面硬度值和硬度層深度逐漸變大,在循環軟化- 硬化作用下,硬度值最終趨于穩定,其大小取決于彈丸入射階段的動能。但噴丸強化時間過長又可能誘發剝層、裂紋、破碎彈丸嵌入、零件翹曲等現象。大尺寸彈丸有利于增加硬度層深度,如圖7 所示,鄭海忠等研究報道了當彈丸尺寸從1mm 變為4mm 時,變形層深度從600μm 增至1600μm。
展望
隨著表面噴丸強化技術的快速發展, 噴丸強化表面完整性對材料及零件性能影響的重要性也越來越受到重視,針對噴丸強化表面完整性的研究也逐漸深入, 為實際工程的應用提供了參考和依據。國內目前針對噴丸強化表面完整性的基礎研究還有待深入,對表面完整性的評估與檢測體系尚不完善,因此,針對噴丸強化表面完整性的研究還有以下幾個方面有待加強:
(1) 深入開展噴丸強化加工表面完整性的應用基礎研究,揭示噴丸強化表面完整性特征的形成及產生的機理,建立噴丸強化表面完整性的理論模型及其評判體系;
(2)在航空航天等領域的抗疲勞零部件制造技術中,拓展噴丸強化加工表面完整性技術的應用,依據實際服役性能的需求,綜合調控表面完整性各因素,實現所需性能的最優化;
(3)基于表面完整性控制,開發新型表面噴丸強化技術,獲得更大的表面完整性調控區間與更優的效果,適應新材料、新結構和更復雜零部件的表面強化需求。
更多關于材料方面、材料腐蝕控制、材料科普等等方面的國內外最新動態,我們網站會不斷更新。希望大家一直關注中國腐蝕與防護網http://www.ecorr.org
責任編輯:龐雪潔
《中國腐蝕與防護網電子期刊》征訂啟事
投稿聯系:編輯部
電話:010-62313558-806
郵箱:ecorr_org@163.com
中國腐蝕與防護網官方 QQ群:140808414
免責聲明:本網站所轉載的文字、圖片與視頻資料版權歸原創作者所有,如果涉及侵權,請第一時間聯系本網刪除。
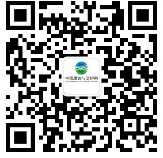
官方微信
《中國腐蝕與防護網電子期刊》征訂啟事
- 投稿聯系:編輯部
- 電話:010-62316606-806
- 郵箱:fsfhzy666@163.com
- 中國腐蝕與防護網官方QQ群:140808414