構(gòu)件發(fā)生腐蝕使其正常功能減弱或喪失為腐蝕失效。因此在該構(gòu)件發(fā)生失效時,對腐蝕進行識別同時將腐蝕確定為失效的因素對后續(xù)開展失效分析(腐蝕失效分析)極為關鍵。同時,在開展失效分析不可忽略外部及現(xiàn)場信息變成”盲人摸象”,也不可因現(xiàn)今高科技檢測儀器及手段的普遍化或因商業(yè)目的需求而盲目使用造成浪費。學習和掌握腐蝕失效的一些重要概念和分析思路也是“可靠性工程師”等技術和管理崗位需要的。
1、失效材料的檢測
(1)化學成分分析
包括對失效件金屬材料化學成分、環(huán)境介質(zhì)及反應物、生成物(腐蝕產(chǎn)物)、痕跡物、附著物、殘留物等化學成分的分析。
(2)性能測試
-
力學性能包括失效件金屬材料強度指標、塑性指標、韌性指標、硬度等;
-
化學性能包括金屬材料在所處環(huán)境介質(zhì)中的自腐蝕電位、極化曲線、腐蝕速率等;
-
物理性能包括如環(huán)境介質(zhì)在所處工藝條件下的反應熱、燃燒熱等;
(3)無損檢測
針對失效件的現(xiàn)存狀態(tài)(形狀、尺寸等),選擇有效的無損檢測方法可迅速而可靠地確定構(gòu)件表面或內(nèi)部裂紋和其他缺陷的大小、數(shù)量和位置。金屬構(gòu)件表面裂紋及缺陷常用滲透法及電磁法檢測,內(nèi)部缺陷則多用放射性檢測,聲發(fā)射常用于動態(tài)-無損檢測,如探測裂紋擴展情況。(關注公眾號,后期將對無損檢測的典型方法進行“濃縮介紹”)
(4)組織結(jié)構(gòu)分析
組織結(jié)構(gòu)分析包括金屬材料表面和心部的金相組織或缺陷。
常用金相法分析金屬的顯微組織是否正常、是否存在晶粒粗大、脫碳、過熱、偏析等缺陷;夾雜物的類型、大小、數(shù)量及分布;晶界上有無析出物,裂紋的數(shù)量、分布及其附近組織有無異常,是否存在氧化或腐蝕產(chǎn)物等。
圖 20G鋼內(nèi)表面脫碳現(xiàn)象(脫碳層)
(5)應力測試及計算
構(gòu)件殘余應力的測定是在無外加載荷的作用下進行測定,目前多用X射線應力測定法。
2、失效件的取樣及處理
(1)失效件的保護
斷口保護主要是防止機械損傷或化學損傷。對于機械損傷的防止,應當在斷裂事故發(fā)生后馬上把斷口保護起來。在搬運時將斷口保護好,在有些情況下還用襯墊材料,盡量使斷口表面不要相互摩擦和碰撞。有時斷口上可能沾上一些油污或臟物,千萬不可用硬刷干刷斷口,并避免用手指直接接觸斷口。對于化學損傷的防止,主要是防止來自空氣和水或其他化學藥品對斷口的腐蝕。一般可采用涂層的方法,即在斷口上涂防腐物質(zhì),原則是涂層物質(zhì)不使斷口受腐蝕及易于被完全清洗掉。
(2)失效件的取樣
在有必要開展全面地的失效分析時,需要制備各種試樣,如力學性能試樣、化學分析試樣、斷口分析試祥、電子探針試樣、金相試樣、表面分析試樣和模擬試驗用試樣等。這些試樣要從有代表性的部位上有計劃性地截取。在截取的部位,用草圖或照相記錄,標明是哪種試樣,以免弄混而導致錯誤的分析結(jié)果。
通常在開展腐蝕失效分析前,撰寫并準備好詳細的腐蝕失效分析方案和記錄文件樣式可提高開展失效分析的邏輯性和準確度。
(3)失效件的清洗
清洗的目的是為了除去保護用的涂層和斷口上的腐蝕產(chǎn)物及外來沾污物如灰塵等。
常用以下幾種方法:
-
用干燥壓縮空氣吹斷口,清除粘附在上面的灰塵以及其他外來贓物,用柔軟的毛刷輕輕擦斷口,有利于把灰塵清除干凈。
-
對斷口上的油污或有機涂層,可以用汽油、石油醚、苯、丙酮等有機溶劑進行清除,清除干凈后用無水酒精清洗后吹干。
-
超聲波清洗能有效地清除斷口表面的沉淀物,且不損壞斷口。
-
應用乙酸纖維膜復型剝離。通常對于粘在斷口上的灰塵和和疏松的氧化腐蝕產(chǎn)物可采用這種方法,就是用乙酸纖維脂反復覆在斷口上2~5次,可以剝離斷口上的臟物。該方法操作簡單,既可去掉斷口上的油污,對斷口又無損傷。
-
使用化學或電化學方法清洗。這種方法主要用于清洗斷口表面的腐蝕產(chǎn)物或氧化層,但可能破壞斷口上的一些細節(jié),所以使用時必須十分小心。一般只有在其他方法不能清洗掉的情況下經(jīng)備用試樣試用后才使用。可參考國標GB/T 16545開展。
3、失效分析的基本技能
(1)斷口分析
斷口上記錄了金屬斷裂的全過程,即裂紋的產(chǎn)生、擴展直至開裂。外部因素對裂紋萌生的影響及材料本身的缺陷對裂紋萌生的促進作用。同時也記錄著裂紋擴展的途徑、擴展過程及內(nèi)外因素對裂紋擴展的影響。
斷口分析的依據(jù)
-
斷口的顏色與色澤,觀察斷口表面光澤與顏色時主要觀察有無氧化色、有無腐蝕的痕跡、有無夾雜物的特殊色彩與其他顏色;紅銹、黃銹或是其他顏色的銹蝕;是否有深灰色的金屬光澤、發(fā)藍顏色(或呈深紫色、紫黑色金屬光澤)。根據(jù)疲勞斷口的光亮程度,可以判斷疲勞源的位置。如果不是腐蝕疲勞,則源區(qū)最光滑。
-
斷口上的花紋,疲勞斷裂斷口宏觀上有時可見沙灘條紋,微觀上有疲勞輝紋。脆性斷裂有解理特征,斷口宏觀上有閃閃發(fā)光的小刻面或人字、山形條紋,而微觀上有河流條紋、舌狀花樣等。韌性斷裂宏觀有纖維狀斷口,微觀上則多有韌窩花樣等。
-
斷口上的粗糙度,斷口的表面實際上由許多微小的小斷面構(gòu)成,其大小、高度差決定斷口的粗糙度。不同材料、不同斷裂方式,其斷口粗糙度也不同。一般來說,屬于剪切型的韌性斷裂的剪切唇比較光滑;而正斷型的纖維區(qū)則較粗糙。屬于脆性斷裂的解理斷裂形成的結(jié)晶狀斷口較粗糙,而準解理斷裂形成的瓷狀斷口則較光滑。疲勞斷口的粗糙度與裂紋擴展有關,擴展速率越快,斷口越粗糙。
-
斷口與最大正應力的交角,韌性材料的拉伸斷口一般呈杯錐狀或呈45°切斷的外形,其塑性變形是以縮頸的方式表現(xiàn)。即斷口與拉伸軸向最大正應力交角是45°。脆性材料的拉伸斷口一般與最大拉伸正應力垂直,斷口表面平齊,斷口邊緣通常沒有剪切"唇口"。斷口附近沒有縮頸現(xiàn)象。韌性材料的扭轉(zhuǎn)斷口呈切斷型。斷口與扭轉(zhuǎn)正應力交角也是45°。材料的扭轉(zhuǎn)斷口呈麻花狀,在純扭矩的作用下,沿與最大主應力垂直的方向分離。
-
斷口上的冶金缺陷,夾雜、分層、晶粒粗大、白點、氧化膜、疏松、氣孔、撕裂等,常可在失效件斷口上經(jīng)宏觀或微觀觀察而發(fā)現(xiàn)。
斷口的觀察
-
宏觀觀察,指用肉眼、放大鏡、低倍率的光學顯微鏡OM或掃描電鏡SEM來觀察斷口的表面形貌。通過宏觀觀察收集斷口上的宏觀信息,可初步確定斷裂的性質(zhì),可以分析裂源的位置和裂紋擴展方向,可以判斷冶金質(zhì)量和熱處理質(zhì)量等。
-
微觀觀察,用顯微鏡對斷口進行高放大倍率的觀察,用金相顯微鏡及掃描電鏡SEM的為多。斷口微觀觀察包括斷口表面的直接觀察及斷口剖面的觀察。通過微觀觀察進一步核實宏觀觀察收集的信息,確定斷裂的性質(zhì)、裂源的位置及裂紋走向、擴展速度,找出斷裂原因及機理等。
-
剖面觀察,裁取剖面要求有一定的方向,通常是用與斷口表面垂直的平面來截取,垂直于斷口表面有兩種切法:平行裂紋擴展方向截取,則可研究斷裂過程;垂直于裂紋擴展方向截取,在一定位置的斷口剖面上,可研究某一特定位置的區(qū)域。
(2)裂紋分析
裂紋分析的目的是確定裂紋的位置及裂紋產(chǎn)生的原因。裂紋形成的原因往往很復雜,如選材不當、材質(zhì)不良、制造工藝不當以及維護和使用不當?shù)染锌赡軐е铝鸭y的產(chǎn)生。裂紋分析往往需要從原材料的冶金質(zhì)量、材料的力學性能、構(gòu)件成型的工藝流程和工序工藝參數(shù)、構(gòu)件的形狀及其工作條件以及裂紋宏觀和微觀的特征等方向做綜合的分析。其中牽涉到多種技術方法和專門知識,如無損探傷、化學成分分析、力學性能試驗、金相分析、X射線微區(qū)分析等。
金屬裂紋的基本形貌特征
-
裂紋兩側(cè)凹凸不平,耦合自然。其耦合特征是與主應力性質(zhì)相關;若主應力屬于切應力則裂紋一般呈平滑的大耦合;若主應力屬拉應力則裂紋一般呈鋸齒狀的小耦合。
-
除某些沿晶裂紋外,絕大多數(shù)裂紋的尾端是尖銳的。
-
裂紋具有一定的深度,深度與寬度不等,深度大于寬度,是連續(xù)性的缺陷。
-
裂紋有各種形狀,直線狀、分支狀、龜裂狀、輻射狀、環(huán)形狀、弧形狀,各種形狀往往與形成的原因密切相關。
金屬裂紋的檢查
-
裂紋的宏觀檢查的主要目的是確定檢查對象是否存在裂紋。裂紋的宏觀檢查,除通過肉眼進行直接外觀檢查和采取建議的敲擊測音法外,通常采用無損探傷法,如X射線、磁力滲透著色、超聲波、熒光等物理探傷法檢測裂紋。
-
裂紋的微觀檢查是指檢查裂紋形態(tài)特征,確定裂紋的分布是穿晶的,還是沿晶的,主裂紋附近有無微裂紋和分支。裂紋處及附近的晶粒度有無顯著粗大或細化或大小極不均勻的現(xiàn)象,晶粒是否變形,裂紋與晶粒變形的方向相平行或相垂直。
-
裂紋附近是否存在碳化物或非金屬夾雜物,其形態(tài)、大小、數(shù)量及分布情況,裂紋源是否產(chǎn)生于碳化物或非金屬夾雜物周圍,裂紋擴展與夾雜物之間有無聯(lián)系。
-
裂紋兩側(cè)是否存在氧化和脫碳現(xiàn)象,有無氧化物或脫碳組織;產(chǎn)生裂紋的表面是否存在加工硬化層或回火層;裂紋萌生處及擴展路徑周圍是否有過熱組織、魏氏組織、帶狀組織以及其他形式的組織缺陷。
裂紋產(chǎn)生部位分析
-
構(gòu)件結(jié)構(gòu)形狀引起的裂紋,由于構(gòu)件結(jié)構(gòu)上的需要或由于設計上的不合理,或加工制造過程中沒有按設計要求進行,或在運輸過程中碰撞而導致在構(gòu)件上往往有尖銳的凹角、凸邊或缺口,截面尺寸突變或臺階等"結(jié)構(gòu)上的缺陷" ,這些結(jié)構(gòu)上的缺陷在構(gòu)件制造和使用過程中將產(chǎn)生很大的應力集中并可能導致裂紋。所以,要注意裂紋所在部位與構(gòu)件結(jié)構(gòu)形狀之間的關系分析。
-
材料缺陷引起的裂紋,金屬材料本身的缺陷,特別是表面缺陷,如夾雜、斑疤、劃痕、折疊、氧化、脫碳、粗晶以及氣泡、疏松、偏析、白點、過熱、過燒等,不僅其本身直接破壞了材料的連續(xù)性,降低了材料的強度與塑性,而且往住在這些缺陷的尖部,造成應力集中使得材料在很低的平均應力下產(chǎn)生裂紋并擴展,最后導致斷裂。
-
受力狀況引起的裂紋,在金屬材料質(zhì)量合格、構(gòu)件形狀設計合理的情況下,裂紋將在應力最大處形成或有隨機分布的特點。在這種情況下,為判別裂紋起裂的真實原因要特別側(cè)重對應力狀態(tài)的分析。尤其是非正常操作工況下構(gòu)件的應力狀態(tài), 如超載、超溫等。
主裂紋的判別方法
-
T形法,將散落碎片按相匹配的斷口合并在一起,其裂紋成T形。在一般情況下橫貫裂紋首先開裂,主裂紋一般阻止二次裂紋擴展。
-
分枝法,將散落碎片按相匹配斷口合并在一起,其裂紋成“樹枝”形:在斷裂失效中,往往出現(xiàn)一個裂紋后,產(chǎn)生很多分叉或分枝裂紋。裂紋的分叉或分枝方向通常為裂紋的局部擴展方向,其相反方向指向裂源,即分枝裂紋為二次裂紋,匯合裂紋為主裂紋。
-
變形法,將散落碎片按相匹配斷口合并在一起,構(gòu)成原來構(gòu)件的幾何外形,測量其幾何形狀的變化情況,變形量較大的部位為主裂紋,其他部位為二次裂紋。
-
氧化法,在受環(huán)境因素影響較大的斷裂失效中,檢驗斷口各個部位的氧化程度,其中氧化程度最嚴重為最先斷裂即主裂紋所形成的斷口,因氧化嚴重說明斷裂的時間較長。
金屬裂紋走向分析
-
應力原則,在金屬脆性斷裂、疲勞斷裂、應力腐蝕斷裂時,裂紋的擴展方向一般都垂直于主應力的方向,當韌性金屬承受扭轉(zhuǎn)載荷或金屬在平面應力的情況下,其裂紋的擴展方向一般平行于切應力的方向,如韌性材料切斷斷口。
-
強度原則,指裂紋總是傾向沿著最小阻力路線,即材料的薄弱環(huán)節(jié)或缺陷處擴展的情況。有時按應力原則擴展的裂紋,途中突然發(fā)生轉(zhuǎn)折,顯然這種轉(zhuǎn)折的原因是由于材料內(nèi)部的缺陷。在這種情況下, 在轉(zhuǎn)折處常常能夠找到缺陷的痕跡或者證據(jù)。
一般情況下, 當材質(zhì)比較均勻時,應力原則起主導作用,裂紋按應力原則進行擴展,而當材質(zhì)存在著明顯不均勻時,強度原則將起主導作用,裂紋將按強度原則進行擴展。裂紋擴展方向到底是沿晶的還是穿晶的, 取決于在某種具體條件下, 晶內(nèi)強度和晶界強度的相對比值。應力腐蝕裂紋、氫脆裂紋、回火脆性、磨削裂紋、焊接熱裂紋、冷熱疲勞裂紋、過燒引起的鍛造裂紋、鑄造熱裂紋、蠕變裂紋、熱脆等晶界是薄弱環(huán)節(jié),因此這些裂紋是沿晶界擴展的;而疲勞裂紋、解理斷裂裂紋、淬火裂紋,焊接裂紋及其他韌性斷裂的情況下,晶界強度一般大于晶內(nèi)強度,因此它們的裂紋為穿晶型,這時裂紋遇到亞晶界、晶界、硬質(zhì)點或其他組織和性能的不均勻區(qū)時,往往會改變擴展方向。因此認為晶界能夠阻礙疲勞裂紋的擴展, 這就是常常用細化晶粒的方法來提高金屬材料的疲勞壽命的原因之一。
(3)痕跡分析
構(gòu)件失效時,由于力學、化學、熱學、電學等環(huán)境因素單獨或協(xié)同地作用,并在構(gòu)件表面或表面層留下了某種標記,稱為痕跡。
痕跡分類
-
機械接觸痕跡,構(gòu)件之間接觸的痕跡,包括壓入、撞擊、滑動、滾壓、微動等單獨作用或聯(lián)合作用,這種痕跡稱為機械接觸痕跡,其特點是塑性變形或材料轉(zhuǎn)移、斷裂等,集中發(fā)生于接觸部位,并且塑性變形極不均勻。
-
腐蝕痕跡,由于構(gòu)件材料與周圍的環(huán)境介質(zhì)發(fā)生化學或電化學作用而在構(gòu)件表面留下的腐蝕產(chǎn)物及構(gòu)件材料表面損傷的標記,稱為腐蝕痕跡。
圖 點腐蝕穿孔
-
電侵蝕痕跡,由于電能的作用,在與電接觸或放電的構(gòu)件部位留下的痕跡稱為電侵蝕痕跡。
-
熱損傷痕跡,由于接觸部位在熱能作用下發(fā)生局部不均勻的溫度變化而留下的痕跡。金屬表面層局部過熱、過燒、熔化、直至燒穿、表面保護層的燒焦都會留下熱損傷痕跡。不同的溫度有不同的熱損傷顏色(如,不同溫度下的回火著色),且構(gòu)件材料表面層成分結(jié)構(gòu)會發(fā)生變化,表面性能有所改變。
-
加工痕跡,對失效分析有幫助的主要是非正常加工痕跡,即留在構(gòu)件表面的各種加工缺陷,如刀痕、劃痕、燒傷、變形約束等。
-
污染痕跡,各種外來污染物附著在構(gòu)件表面而留下的痕跡是污染痕跡(如附著物、殘留物)。
痕跡分析主要內(nèi)容
-
痕跡的形貌,特別是塑性變形、反應產(chǎn)物、變色區(qū)、分離物和污染物的具體形狀、尺寸、數(shù)量及分布;
-
痕跡區(qū)以及污染物、反應產(chǎn)物的化學成分;
-
痕跡顏色的種類、色度和分布、反光性等;
-
痕跡區(qū)材料的組織和結(jié)構(gòu);
-
痕跡區(qū)的表面性能(耐磨性、耐蝕性、顯微硬度、表面電阻、涂鍍層的結(jié)合力等)
-
痕跡區(qū)的殘余應力分布;
-
從痕跡區(qū)散發(fā)出來的各種氣味;
-
痕跡區(qū)的電荷分布和磁性等。
4、失效現(xiàn)場信息的重要性
除了以上幾個部分提到的內(nèi)容,腐蝕失效分析需要關注失效件現(xiàn)場信息,包括失效件所屬設備和/或作業(yè)點的信息收集和分析、失效件失效時的運行數(shù)據(jù)收集和分析、失效件使用工況歷史數(shù)據(jù)收集和分析等。在重點關注失效實物件分析的同時,進一步更多地關注失效現(xiàn)場信息的收集和分析將有助于失效分析的開展,對識別某一類型的失效分析、提供有效的預防措施、避免此類失效事故的再次發(fā)生有重要幫助。
5、失效分析參考標準
開展腐蝕失效分析的參考標準文件有:GB/T 16545、HB 7739、GB/T 38803、ASTM G161、SY/T 6945-2013、DB51/T 1723-2014、ASTM G1、JB/T 7901等。
免責聲明:本網(wǎng)站所轉(zhuǎn)載的文字、圖片與視頻資料版權(quán)歸原創(chuàng)作者所有,如果涉及侵權(quán),請第一時間聯(lián)系本網(wǎng)刪除。
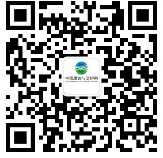
官方微信
《腐蝕與防護網(wǎng)電子期刊》征訂啟事
- 投稿聯(lián)系:編輯部
- 電話:010-62316606
- 郵箱:fsfhzy666@163.com
- 腐蝕與防護網(wǎng)官方QQ群:140808414