1概述
不銹鋼冷軋帶鋼在不銹鋼領域占有十分重要的地位,約70%的不銹鋼轉化成了冷軋帶鋼,成為市場消費的主要產品形式。不銹鋼冷軋帶鋼具有強度高、加工硬化快、品種規格多等特點,而且表面質量要求極其苛刻,其工藝復雜,生產難度大。國際上普遍采用單機架多輥可逆軋機(或連軋機組)、退火酸洗機組、精整機組等多工序組合生產。其特點是工序分散、物流遲滯、生產周期長、效率低、成本高。
近年來,隨著原材料價格不斷上漲,資源、能源的短缺,環境保護的壓力,加之產品結構的升級,高端產品市場供給能力不足等,不銹鋼冷軋帶鋼突出顯示效率低、質量穩定性差、成本高、利潤空間狹小等問題。開發不銹鋼冷軋帶鋼制造新工藝、新技術、新裝備成為行業提升質量、提高效率、降低成本的迫切愿望。
太鋼在國家專項資金支持下,歷時七年,對不銹鋼冷軋帶鋼流程進行大膽革新,創造性地把各個獨立的不銹鋼冷軋生產單元有機集成在一條生產線上,解決了多工序工藝匹配優化設計、鐵素體等特殊品種高質量生產、全線高效精準運行及智能控制等一系列難題,實現了不銹鋼冷軋帶鋼全連續生產線技術集成與創新。該工程設計工藝先進,布置緊湊,物流高效,裝備國產化率高,成本低,質量優。項目獲得2016年度全國冶金行業優秀工程設計一等獎,2016-2017年度國家優質工程獎。
太鋼不銹鋼全連續冷連軋生產線共設計有兩條機組,包括鉻鋼(400系列)專用生產線一條和鎳鋼(300系列)專用生產線一條,產能共計100萬噸/年。產品填補多項國內空白,替代進口。產品覆蓋300和400系不銹鋼30多個品種,覆蓋大部分鐵素體和奧氏體不銹鋼,包括430、409、410、429、439、441、443、304、316、301等。產品已廣泛應用于國防、建筑、家電、汽車、航天、鐵路等各領域,為不銹鋼民族工業發展作出了貢獻。產品的表面質量均勻一致,性能、尺寸精度、板形等質量指標達到國際領先水平。2018年相關技術獲得“冶金科學技術獎”一等獎。
該生產線將“五機架連軋機、退火、酸洗、平整、拉矯、縱切”等單一的生產機組有機地集成在一條線上,建成了不銹鋼冷軋帶鋼“六位一體”的全連續生產線,為世界首創。經過一次上卷和一次卸卷即可產出成品,減少了生產過程環節,簡化了流程,提高生產效率,降低工藝介質消耗。該生產線由于工序高度集成化,設備運行極其復雜,技術要求高,控制難度大,代表了當今世界不銹鋼生產的最高技術水平。2017年入選工業和信息化部“智能制造試點示范項目”。
該生產線投資低、占地面積小、低耗節能、綠色環保。與傳統單工序生產相比,投資減少18%、占地減少65%、崗位減少50%、效率提高40%、成材率提高4%、能耗降低7%、成本降低21%、制造周期由2-3天縮短到4h。
該生產線擁有多項自主知識產權,授權專利48件,其中發明專利26件,企業專有技術49件。經專家評價,總體技術達國際領先水平。
太鋼不銹鋼冷軋帶鋼全連續生產線對不銹鋼冷軋帶鋼生產方式具有巨大推動作用,為高質量、高效率、低成本的不銹鋼冷板制造提供了新模式。作為山西省“十二五”規劃重點項目,有效地促進了我國不銹鋼結構升級和綠色轉型發展,成為世界不銹鋼冷軋生產技術的標桿,對不銹鋼冷軋規模化發展有引領和示范作用。
2主要工藝及裝備
全連續生產線主要裝備包括開卷機、激光焊機、入口活套、五機架連軋機、軋機出口活套、退火爐、酸洗段、酸洗出口活套、平整機、拉矯機、平整出口活套、切邊剪、剪切出口活套、卷取機。設備總長750m,全線帶鋼最大長度7900m。機組下卷產品可直接包裝交庫。設計寬度1000-1650mm,設計厚度0.5-3.0mm最大卷重40t。其設備布置如圖1所示。
2.1激光焊機
激光焊機具有焊接精度高、生產效率高、自動化程度高等優點,采用高純CO2作為激光發射介質,從工作側到驅動側焊接,可選擇填絲焊接和無填絲焊接,主要焊機參數如表1所示。
激光焊機焊縫可保證生產的鐵素體不銹鋼和奧氏體不銹鋼可連續承受五機架最大83%變形量、最大1000kN張力和在最小彎曲半徑16mm連續206次正反彎曲等苛刻條件而不斷帶。
激光焊接后有在線退火,能夠使焊縫的晶相組織得到較好的回復,保證焊縫的強度和韌性。配置了在線焊縫檢測系統,能夠對焊縫高度、平坦度等進行在線檢測,有問題的進行報警,方便操作人員進行焊縫質量的精確判斷。同時配置了杯突試驗機和彎曲試驗機,能夠對焊縫進行破壞性的檢測,對判斷焊縫質量的好壞提供依據。
2.2連軋機
針對鐵素體不銹鋼和奧氏體不銹鋼軋制變形抗力和加工硬化差異,兩條專業化生產線采用了不同的軋機配置的五機架連軋機,如表2所示
五機架連軋機可實現最大變形量83%,配有智能化的測量與控制系統,測厚儀、測速儀、測寬儀、張力計、板形儀等,可實現厚度和板形等重要參數動態高精度控制,厚度精度達到±0.01mm,板形精度達到±8I。400系專業生產線測控系統配置如圖2所示,300系專業生產線測控系統配置如圖3所示。焊縫通過軋機有全軋模式、半軋模式、不軋模式三種,可滿足不同生產需要。
根據兩條專用線軋機機型差異,軋制潤滑與冷卻自主開發了兩種不同的軋制潤滑液,實現軋制過程穩定和帶鋼表面質量良好。潤滑液循環系統分A、B兩個系統,1-3#機架由A系統供液,4-5#機架由B系統供液。每個循環系統配有磁過濾、平床過濾器及加熱冷卻系統,循環油箱一備一用。
連軋機后配有事故剪和焊機,以供軋制發生斷帶事故時應急處置,事故處理時間大大縮短,作業率得到有效提高。
事故焊機后配有軋后脫脂清洗機,主要包括脫脂段、刷洗段、最終清洗段和烘干段。脫脂段用來清洗軋機軋制后帶鋼表面的油脂,為后續工藝段處理做準備。軋機脫脂設備采用統一的電氣自動化系統進行控制,通過自動化系統控制實現了傳動、工藝功能和儀表相關的過程控制、工藝參數控制和過程監視。操作工通過HMI輸入的數據,過程信息、機組狀態和各種測量值以符號和圖表的形式在HMI畫面上顯示。主要過程參數,即溫度,壓力、流量、液位等在控制室中顯示出來,而重要的操作參數都自動由PLC系統自動控制。帶鋼在脫脂段的最大運行速度達370m/min,經過脫脂處理后的帶鋼表面殘油量維持在0.25mg/m2以下,均達到國內外領先水平。
2.3退火爐
退火爐根據大型化的特點,采用退火爐分段,設置兩段預熱段,既可節約能耗,也可避免爐體過長帶來的擦劃傷弊端。退火爐采用世界先進的二級加熱模式,有效地提高了帶鋼在退火過程中的穩定性,對不銹鋼的性能提升起到至關重要的作用,同時此退火爐的爐體采用整體砌筑模式,大大地提高了爐體自身的蓄熱能力,使天然氣的熱利用效率提高了1%,為節約能源創造了條件。
退火爐采用連續水平式退火爐,主要由預熱段、加熱段和冷卻段組成,全長303m。預熱段和加熱段采用分割式,包括兩個加熱段和兩個預熱段,每個加熱段前有一個預熱段。加熱段共分18個加熱區,每個加熱區有14個或16個加熱燒嘴。采用天然氣作為燃料,空氣作為助燃氣體,輻射加熱帶鋼。冷卻段分為空氣冷缺段和霧冷段,空氣冷缺段分12個區,霧冷段分2個區。退火爐主要參數如表3所示。
根據加熱曲線設計,272個燒嘴加熱能力設計范圍為0.371-1.62GJ/h。退火爐配有54個熱電偶、6個高溫輻射計對爐內氣氛溫度和帶鋼溫度進行監測和控制。為保證爐內氣氛穩定和熱量利用,爐壓采用5-20Pa微正壓控制。
為防止帶鋼在爐內跑偏和劃傷,張力不宜過小,但張力過大會造成帶鋼拉窄,甚至斷帶。由于退火爐較長,張力控制難度較大,退火爐內配有三處糾偏裝置,并自主開發并采用了獨特的彈跳輥設計,可實現爐內張力高精度穩定控制。
2.4酸洗
酸洗采用世界先進的電解中性鹽+淺槽紊流酸洗模式,比傳統不銹鋼表面鈍化效率提高70%,同時降低介質消耗,不僅節約了成本,而且也減少了廢棄物的排放,減少對環境的污染。
酸洗采用電解酸洗和化學酸洗相結合的方式,根據不同鋼種可對酸洗介質進行選擇。電解酸洗包括中性鹽電解酸洗和酸電解酸洗,中性鹽采用硫酸鈉,酸電解采用硝酸,化學酸洗采用硝酸和氫氟酸混合酸。酸洗參數如表4所示。
采用淺槽紊流酸洗方式,最大酸洗速度170m/min。在中性鹽電解酸洗、酸電解酸洗和混合酸洗后分別配有刷洗機,可避免各部分酸洗介質相互污染,保證了介質穩定性。在混合酸洗刷洗機之后配有最終清洗和烘干機,保證了帶鋼除鱗后表面清潔。
2.5在線平整機和拉矯機
設置在線平整機和在線拉矯機,其主要作用通過壓力、張力的作用以達到改善不銹帶鋼表面的光亮度和提高其使用性能的目的。在線同時集成平整機和拉矯機,可以滿足不銹鋼不同表面等級的精整要求,同時可大幅度減少離線平整拉矯造成的成材率損失和工序成本,且有效降低了投資。
在線平整機和拉矯機串聯配置,可實現2B、2D兩種表面產品消除屈服平臺,提升板形精度的個性化需求。平整采用兩輥干式平整機,其主要參數如表5所示。拉矯機為一拉兩矯式,共3對輥盒,上輥盒可以活動,下輥盒固定,分為三輥輥盒和六輥輥盒。六輥輥盒包括1根工作輥,2根中間輥和3根支撐輥。三輥輥盒包括1工作輥和2個支撐輥。其中1號輥盒為六輥,2、3號為三輥。
2.6在線縱切剪采用了快速剪刃更換技術、高精度焊縫跟蹤技術、入口高精度糾偏控制技術、廢邊特殊導槽入導向設計技術、無張力廢邊卷取緩沖技術等,創造性地實現了在大規模生產線上集成在線切邊功能。
在線切邊采用世界上先進的雙頭360°快速旋轉模式,同時對不銹鋼在切邊過程中容易產生下勾的問題增加螺旋修磨技術,對于連軋機出現部分區域厚度變化的特點采用切邊間隙自動調節等控制專利技術,有效地提高了切邊利用效率。在線縱切剪克服了在線高速連續生產時焊縫精準定位識別、剪刃快速更換、帶鋼中心對準精度等難題,實現切邊寬度精度控制在±0.5mm以內。采用雙頭旋轉刀頭,實現快速在線換刀,設計了專用的連續廢邊快速處置系統,保證了帶鋼切邊高效連續穩定運行。
3關鍵技術與創新以“五機架連軋機+退火線+酸洗線+平整機+拉矯+縱切”為核心的“六位一體”的全連續不銹鋼冷軋帶鋼生產線,涉及工藝、裝備、產品、控制等多個技術領域,對全流程的銜接和匹配技術,裝備的功能和精度控制,全線的高效穩定運行,一體化的產品質量和生產管理等提出了更高的要求。太鋼冷連軋技術團隊通過開發一系列的關鍵技術與創新,成功地實現了全連續生產線的穩定高效運行和產品質量的持續提升。
3.1開發出多活套高精度雙保護緩沖控制、爐區彈跳輥高精度張力控制、在線快速定寬切邊等關鍵技術,實現了“連軋+退火+酸洗+平整+拉矯+縱切”六位一體全連續生產線技術集成創新。
該系列關鍵技術為全線的整體穩定連續高效運行創造了條件。
活套的主要作用首先是儲存足夠的帶鋼,在全線工藝焊接、工藝換輥或工藝換刀時,帶鋼仍能連續運行;其次是張力緩沖,由于不同工藝設備之間靠活套柔性連接,活套設計應當滿足多工序串聯集成條件下緩沖張力最優。太鋼開發了多活套高精度雙保護緩沖控制技術,實時采集現場速度信息及時降低活套張力,實現了高集成度下各工序之間的柔性連接。
切邊剪在線高速定寬切邊,其難度就大大增加。具體表現為焊縫精準定位識別難、剪刃快速更換難、廢邊快速處置難、要求帶鋼中心對準精度高、剪刃間隙需要動態補償等。為此,開發了圓盤剪在線快速更換、廢邊在線處理等技術,實現了在線快速定寬切邊功能和在線高速切邊。業內首次實現將縱切集成在大規模連續生產線上。
對于全長300m的超長退火爐,存在不同品種和規格的工藝過渡,爐區的張力無法固定,傳統的生產線依靠手動調整張力以適應這種變化。太鋼開發了爐區彈跳輥高精度張力控制,實現了在速度或規格變換時爐內張力的穩定。
3.2開發出厚規格窄熱影響區高效激光焊接、基于軋制力與變形量控制模型的品種規格快速切換、超純鐵素體不銹鋼快速加熱分級冷卻等關鍵技術,實現了300系、400系不銹鋼冷軋帶鋼多規格、高效率、低成本的穩定生產。
該系列關鍵技術體現在厚規格鐵素體鋼焊接、不同規格品種過渡段軋制、熱處理工藝技術等方面,解決了連續生產條件下焊接、品種規格快速切換、全線穩定通板等難題。
與其他焊接工藝不同的是,焊縫的強度和塑性首先必須滿足五機架連軋機83%大變形的要求,其次能夠承受全線206次以上的正彎、背彎等反復彎曲(最大彎曲180°)而不至于發生斷裂。尤其是厚規格鐵素體不銹鋼,由于其焊接性能較差,保證焊縫質量尤為重要。開發了厚規格超窄熱影響區鐵素體鋼焊接技術等確保了焊縫的通板能力。
在連續生產線上,不同品種、不同厚度和寬度之間的切換很頻繁,其切換時確保焊縫穩定軋制又不損傷軋輥輥面是最基本的要求,通過基于軋制力與變形量控制模型的軋制技術解決了這一難題。對階梯型焊縫實行優化軋制,實現了多品種規格快速切換的軋制控制模式,使全連續生產線能夠滿足多品種、多規格、小批量生產。
鐵素體不銹鋼,尤其是超純鐵素體熱處理工藝窗口很窄,對快速加熱和冷卻速率有極為苛刻的要求,對此開發了超純鐵素體不銹鋼快速加熱分級冷卻技術解決了這一難題。通過控制熱處理溫度、保溫時間和分級冷卻速度,提高了產品的延伸率,降低了屈強比,有效地提高產品的加工性能,極大地滿足了以汽車排氣管為代表的對產品復雜加工的特殊變形要求。
3.3開發出專用彌散型水基軋制潤滑液、低氧氣氛退火與輕度酸洗等關鍵技術,表面質量要求高的430(2B)產品粗糙度Ra達到0.04μm,實現了不銹鋼高表面質量生產該系列關鍵技術為專用彌散型軋制潤滑液、低氧氣氛退火與輕度酸洗等,解決了連續生產條件下提高不銹鋼冷軋帶鋼質量穩定性和一致性,降低表面粗糙度等難題。
質量控制的目標是實現產品的一致性、均勻性和穩定性。由于全連續生產線7900m長,質量控制點1500多個,要達到這樣的目標難度非常大。針對產品的表面質量,通過對軋制潤滑液的研究,開發了專用彌散型軋制潤滑液與軋制潤滑技術,極大地減少了帶鋼表面色差;通過對爐內氣氛的控制,開發了低氧氣氛退火與輕度酸洗技術,提高了表面的均勻性、一致性;開發了軋輥粗糙度梯度配置技術,實現了430(2B)等產品表面粗糙度Ra達到 0.04μm水平,滿足了高端領域用戶需求,并在此基礎上研發了430系列高檔面板等10余種高端產品,得到用戶高度評價。
3.4開發出環形網絡冗余系統控制技術、大數據智能管理系統、物聯網物料規劃系統等,實現了生產和質量的穩定控制該系列關鍵技術屬于智能控制技術方面,主要是環形網絡冗余技術的開發和應用,它有效地降低了故障頻次,非常適用于設備多樣化、大型化、控制難度高的全連續生產線。
對于集成度如此高的生產線,首先各個單元必須完成單個設備的基礎自動化控制,如順序控制等,并建立所屬的數學模型,如物料跟蹤控制模型等。其次,關鍵模型要具有自適應自學習系統。然后,通過環形網絡冗余技術將各個單元有機統一起來,搭建過程控制平臺,完成過程跟蹤與顯示、模型計算與優化、過程數據采集與處理等。
為了將智能化由設備、運行、生產延伸至決策、管理等環節,還設計開發了基于物聯網的物料規劃系統、基于大數據的智能管理決策系統。保證生產線的平穩高效運行的同時,推動了不銹鋼冷軋技術與智能科技協同發展,開拓了全新的“無人化”與“智能化”的管理模式。
4結語
隨著國民經濟的發展和社會的不斷進步,不銹鋼冷軋帶鋼應用愈發廣泛,但對產品一致性、應用成本要求也更高。太鋼不銹鋼冷軋帶鋼全連續生產線對不銹鋼冷軋帶鋼生產方式具有巨大推動作用,為高質量、高效率、低成本的不銹鋼冷板制造提供了新模式,有效地促進了我國不銹鋼結構升級和綠色轉型發展,成為世界不銹鋼冷軋生產技術的標桿,對不銹鋼冷軋規模化發展有引領和示范作用。
太鋼不銹鋼冷軋帶鋼全連續生產線改變了不銹鋼冷軋工序過程中傳統的單工序生產方式,將冷軋及其后續的所有工序集成,組成一條全連續的生產線,有效地提高了冷軋過程的生產效率,縮短了生產周期,有效降低了資金占用時間;加快訂單交付周期;減少了各工序切損造成的帶鋼損失,提高成材率4%以上;通過集成節省了以前各工序的上卷與下卷裝備,節約設備投資;將各工序集成后,節省了占地面積,提高土地利用率;減少操作人員數量;降低綜合能源消耗,有利于改善生態環境,推動企業綠色發展,具有很好的經濟效益與社會效益。
免責聲明:本網站所轉載的文字、圖片與視頻資料版權歸原創作者所有,如果涉及侵權,請第一時間聯系本網刪除。
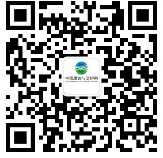
官方微信
《中國腐蝕與防護網電子期刊》征訂啟事
- 投稿聯系:編輯部
- 電話:010-62313558-806
- 郵箱:fsfhzy666@163.com
- 中國腐蝕與防護網官方QQ群:140808414