過/再熱器部件是超超臨界機(jī)組鍋爐中負(fù)責(zé)回收燃煤煙氣能量、加熱蒸汽、實(shí)現(xiàn)能量轉(zhuǎn)化的關(guān)鍵部件,是鍋爐中承受壓力最大、溫度最高、服役環(huán)境最苛刻的部分。由于國內(nèi)外尚無可供600/620/620 ℃二次再熱超超臨界機(jī)組選用的合金,奧氏體鋼仍是機(jī)組末級(jí)過/再熱器的首選材料之一,它能滿足在650 ℃蒸汽條件下服役的力學(xué)性能要求,但過高的蒸汽氧化速率限制了奧氏體鋼在更高溫度下服役的可能。相比開發(fā)更高等級(jí)的受熱面材料,表面技術(shù)可以在不降低合金基體力學(xué)性能的基礎(chǔ)上顯著提高抗氧化性能。
為提高合金的抗蒸汽氧化性能,目前一般采取細(xì)化晶粒和內(nèi)壁噴丸技術(shù)。這兩項(xiàng)技術(shù)通過改變管內(nèi)壁組織結(jié)構(gòu),使合金能快速生長出抗氧化所需的Cr2O3膜。但Cr2O3膜在高于600 ℃蒸汽中的穩(wěn)定性較差,揮發(fā)性產(chǎn)物造成的氧化膜疏松問題會(huì)引發(fā)氧化膜剝落,并進(jìn)一步導(dǎo)致堵管、爆管事故;另外,合金基體中的Cr 含量比較低,隨著服役時(shí)間的增加,當(dāng)生長氧化膜所需的Cr 含量得不到補(bǔ)充時(shí),合金的抗氧化性能也會(huì)急劇下降。因此,這兩項(xiàng)技術(shù)只能在服役初期短時(shí)間內(nèi)提高合金的抗氧化性能,并不能從根本上解決合金的氧化和氧化膜剝落問題。
表面涂層技術(shù)因能顯著提高合金的抗氧化性能,在航空、航天、石化等領(lǐng)域得到廣泛應(yīng)用,針對(duì)超(超) 臨界鍋爐用奧氏體鋼管內(nèi)表面涂層技術(shù)研究相對(duì)較少。Agüero 等[14]在P92 基體上制備了Cr 化物涂層,在650 ℃、30 MPa蒸汽下進(jìn)行氧化1500 h,發(fā)現(xiàn)Cr 化物涂層試樣雖然氧化膜較薄,在超臨界環(huán)境下,純Cr 化物涂層是不穩(wěn)定的,并不是650 ℃級(jí)蒸汽發(fā)電站的最佳優(yōu)化方案。氧化鋁在水蒸汽中的穩(wěn)定性遠(yuǎn)高于氧化鉻,羅新民等將1Cr18Ni9Ti 不銹鋼鍋爐管試樣在730 ℃鋁浴中浸鍍5 min 先獲得良好的熱浸鍍鋁層,然后以NH4Cl 為活化劑,在960 ℃密封擴(kuò)散6 h,獲得了與基體結(jié)合良好的擴(kuò)散滲鋁層,發(fā)現(xiàn)奧氏體不銹鋼經(jīng)擴(kuò)散滲鋁后的抗高溫氧化性能優(yōu)于未處理態(tài)。但是單一鋁化物涂層一般脆性較高,Agüero 等制備了鐵鋁料漿涂層,發(fā)現(xiàn)其在600~650 ℃實(shí)驗(yàn)室環(huán)境下具有優(yōu)良的抗蒸汽氧化性能,但現(xiàn)場實(shí)驗(yàn)中涂層氧化物剝落時(shí)間較短,這是因?yàn)殍F鋁涂層氧化物二者的熱膨脹系數(shù)相差較大,鍋爐啟停過程會(huì)產(chǎn)生較大應(yīng)力。因此,目前還沒有一種合適的表面涂層材料及技術(shù)可以完全解決超(超) 臨界鍋爐用奧氏體合金的氧化問題。
本論文采用料漿法在18-8 系奧氏體鋼TP347HFG 合金表面制備硅改性的鋁化物涂層,通過對(duì)TP347H FG-AlSi 涂層的飽和蒸汽氧化行為的研究,并以更高等級(jí)的高鉻HR3C合金為參比對(duì)象,分析不同耐蝕元素Al、Cr 對(duì)降低合金氧化速率的控制措施及機(jī)理,為現(xiàn)役18Cr 奧氏體合金管能繼續(xù)服役于620~650 ℃二次再熱機(jī)組及下一代鍋爐機(jī)組提供技術(shù)參考。
1 實(shí)驗(yàn)方法實(shí)
驗(yàn)用TP347H FG、HR3C為供貨態(tài)鍋爐管,合金成分見表1。試樣尺寸為10 mm×10 mm×2 mm,線切割加工后經(jīng)過粗砂紙依次磨光至2000#細(xì)砂紙,使得試樣表面光滑,沒有明顯表面缺陷,且具有統(tǒng)一的粗糙度和整潔度。采用料漿法在TP347H FG表面制備鋁硅涂層,Al∶Si 配比為5∶1,將噴涂試樣置于950 ℃的管式爐中,并在Ar氣保護(hù)下熱處理60 min。圖1 為TP347H FG-AlSi 涂層的截面形貌,滲層出現(xiàn)了明顯的分層,表現(xiàn)為外層與內(nèi)層兩層,外層為約20 μm 的FeAl 層、內(nèi)層為Fe-Al 擴(kuò)散層,深度約為30 μm。內(nèi)、外層之間為富Al 雜質(zhì),外層Al 含量為30%左右,內(nèi)層Al含量為10%左右。
蒸汽氧化實(shí)驗(yàn)在流動(dòng)的100%水蒸汽環(huán)境中進(jìn)行,動(dòng)態(tài)水蒸氣是通過將溶解氧含量為5~7 mg/L 的超純水(電阻率約為18.25 MΩ·cm) 泵入預(yù)熱裝置(300 ℃) 獲得連續(xù)的水蒸汽,進(jìn)而通入反應(yīng)爐。反應(yīng)爐體內(nèi)的蒸汽參數(shù)為:溫度650 ℃,壓力0.1 MPa,蒸汽流速100~120 mL/s,氧化時(shí)間為1000 h。采用精度為0.01 mg的電子天平稱量樣品隨氧化時(shí)間的質(zhì)量變化,繪制TP347H FG、TP347H FG-AlSi、HR3C在650 ℃純水蒸汽環(huán)境下氧化1000 h 的氧化動(dòng)力學(xué)曲線。采用ZEISS εigma HD掃描電子顯微鏡(SEM)觀察樣品的形貌特征,采用Oxford 能譜儀(EDS)對(duì)樣品進(jìn)行成分分析,采用D/MAX-RA 型X 射線(XRD) 對(duì)實(shí)驗(yàn)特征樣品表面進(jìn)行物相結(jié)構(gòu)分析。
2 結(jié)果與討論
2.1 氧化動(dòng)力學(xué)
HR3C合金在650 ℃純水蒸汽環(huán)境下氧化1000 h 的氧化動(dòng)力學(xué)曲線。可以看出,在650 ℃純水蒸汽環(huán)境下氧化時(shí),氧化初期(0~350 h) TP347H FG的氧化增重與氧化時(shí)間近似呈拋物線關(guān)系,擬合的拋物線速率常數(shù)為0.0058 mg2·cm- 4·h- 1;當(dāng)氧化時(shí)間超過350 h 后,高溫與水蒸氣的共同作用使得氧化膜穩(wěn)定性變差,此時(shí)開始發(fā)生剝落,而在600 h 后開始大量剝落,氧化增重曲線明顯下降,氧化1000 h 后增重為- 2.91814 mg·cm- 2。TP347H FG- AlSi 涂層在650 ℃純水蒸汽環(huán)境下氧化1000 h 的氧化增重很少,氧化1000 h 后增重為0.06157 mg·cm-2,說明在TP347H FG基體上制備AlSi 涂層,可顯著提高基體材料的抗蒸汽氧化性能。相同條件下,TP347H FG合金在650 ℃純水蒸汽環(huán)境下氧化1000 h 后增重為TP347H FG-AlSi 涂層的47 倍。相比之下,HR3C合金在650 ℃純水蒸汽環(huán)境下氧化1000 h 后增重亦很小,氧化1000 h 后增重為:0.08163 mg·cm- 2。說明HR3C合金在650 ℃純水蒸汽環(huán)境下同樣具有良好的氧化性能。圖2b 為TP347H FG-AlSi、HR3C合金的氧化增重曲線放大圖,由圖可知,HR3C 合金在200 h 之前的氧化動(dòng)力學(xué)曲線遵從拋物線,擬合的拋物線速率常數(shù)為3.464×10-5 mg2·cm-4·h-1,200 h 之后氧化增重基本穩(wěn)定。TP347H FG-AlSi 涂層的氧化動(dòng)力學(xué)遵從拋物線規(guī)律,擬合的拋物線速率常數(shù)為3.790×10-6 mg2·cm-4·h-1,且曲線位于HR3C 合金下方,說明在650 ℃飽和水蒸汽中TP347H FG-AlSi 的抗氧化性能優(yōu)于HR3C合金。
2.2 氧化產(chǎn)物形貌分析
圖3 為TP347H FG、TP347H FG-AlSi、HR3C 合金在650 ℃飽和水蒸汽環(huán)境下分別氧化50,500 和1000 h 后的表面形貌圖??梢钥闯?,在650 ℃純水蒸汽環(huán)境下,TP347H FG基體合金氧化50 h 后表面覆蓋致密氧化膜,局部出現(xiàn)了瘤狀氧化物,且瘤狀氧化物尺寸較小。隨著氧化時(shí)間延長至500 和1000 h后,TP347H FG 基體表面氧化膜開始發(fā)生剝落,1000 h 后出現(xiàn)大面積剝落。在650 ℃純水蒸汽環(huán)境下,TP347H FG-AlSi 涂層表面均形成顆粒狀氧化物。而HR3C 合金氧化50,500 和1000 h 后表面均被氧化物所覆蓋,氧化膜平整致密,并存在少量瘤狀氧化物,且瘤狀氧化物尺寸較小。隨著氧化時(shí)間延長至500 和1000 h 后,合金表面瘤狀氧化物的尺寸有所增大,數(shù)量有所增加,氧化1000 與500 h 相比,表面瘤狀氧化物尺寸、數(shù)量變化不大。
圖4 為TP347H FG、TP347H FG-AlSi、HR3C 合金在650 ℃純水蒸汽環(huán)境下氧化50,500 和1000 h后的截面形貌圖??梢钥闯?,TP347H FG 基體在650 ℃純水蒸汽環(huán)境下氧化50 h 后的氧化膜均勻致密,厚度為1 μm左右。隨著氧化時(shí)間延長,試樣表面氧化膜下方局部出現(xiàn)內(nèi)氧化,與試樣表面瘤狀氧化物形成了雙層結(jié)構(gòu)氧化膜。氧化500 h 后,外層氧化物較為疏松,出現(xiàn)了裂紋、空洞,局部已出現(xiàn)破碎;氧化1000 h 后,發(fā)生嚴(yán)重內(nèi)氧化,形成一層內(nèi)氧化物,厚度為50 μm左右,此時(shí)外層表面瘤狀氧化物發(fā)生剝落,與表面形貌結(jié)果一致。TP347H FG-AlSi 涂層在650 ℃純水蒸汽環(huán)境下氧化50,500 和1000 h后涂層外層結(jié)構(gòu)完整,并有一層極薄的氧化膜;內(nèi)層則與合金基體發(fā)生互擴(kuò)散,使得涂層Fe-Al 擴(kuò)散區(qū)變厚,氧化1000 h 后Fe-Al 擴(kuò)散區(qū)約為60 μm。相比之下,HR3C合金在650 ℃純水蒸汽環(huán)境下氧化50,500 和1000 h 的氧化膜整體均勻、完整致密,并隨著氧化時(shí)間增長,保護(hù)性氧化膜厚度增厚,氧化1000 h厚度為1 μm左右。
2.3 氧化產(chǎn)物成分及結(jié)構(gòu)
圖5為合金在650 ℃純水蒸汽環(huán)境下氧化1000 h后的元素面分布圖,圖6 為合金在650 ℃純水蒸汽環(huán)境下氧化1000 h 后的XRD圖譜。TP347H FG 合金基體在650 ℃純水蒸汽環(huán)境下氧化后形成的瘤狀氧化物富集Fe、O元素,而平整區(qū)的氧化物富集Cr、Fe、O元素,以及少量的Mn。結(jié)合XRD表征結(jié)果,可推知瘤狀氧化物由Fe3O4構(gòu)成,而平整區(qū)的氧化物的組成為(Cr,Mn)2O3。TP347H FG 合金氧化后,試樣表面氧化膜下方局部發(fā)生的內(nèi)氧化,其氧化物為FeCr2O4,與試樣表面瘤狀氧化物Fe3O4形成了雙層結(jié)構(gòu)氧化膜。TP347H FG-AlSi 涂層表面顯示較暗的區(qū)域的主要成分是Al,較亮的區(qū)域主要是富鋁氧化物,說明高溫氧化1000 h 后Al 并未被完全氧化成Al2O3 (對(duì)應(yīng)的XRD中顯示出比較強(qiáng)的基體峰,同時(shí)出現(xiàn)部分Al2O3衍射峰),富鋁層還可以為表面生成致密的Al2O3膜提供充足的Al 源,很好地阻擋O對(duì)基體的侵蝕。HR3C 合金氧化后,主要形成保護(hù)性Cr2O3氧化膜,并含有Mn元素。
氧化初期TP347H FG 合金表面形成一層致密保護(hù)性Cr2O3氧化膜,隨氧化繼續(xù),F(xiàn)e 通過氧化膜與缺陷向氧化膜/水蒸氣界面擴(kuò)散形成瘤狀Fe3O4,與此同時(shí),水蒸汽通過這些缺陷向內(nèi)擴(kuò)散氧化基體,發(fā)生內(nèi)氧化,內(nèi)氧化物與試樣表面瘤狀氧化物形成雙層結(jié)構(gòu)氧化膜。合金外層瘤狀氧化物Fe3O4為疏松層,其間有空洞與裂紋,容易開裂脫落,加之氧化過程中內(nèi)外層界面處會(huì)形成孔洞,最終導(dǎo)致外氧化層和內(nèi)氧化層之間形成剝離空隙,在熱應(yīng)力作用下,發(fā)生剝落。對(duì)于高Cr 含量的HR3C來說,合金中較高的Cr 含量促使HR3C在較短的熱暴露時(shí)間內(nèi),表面即形成致密連續(xù)的Cr2O3膜。氧化膜的生長由Cr3+等陽離子的向外擴(kuò)散控制,氧化動(dòng)力學(xué)遵循拋物線規(guī)律。隨氧化時(shí)間延長,氧化膜不斷增厚。
TP347H FG合金涂覆鋁硅涂層后具有良好的抗氧化性能。這主要是因?yàn)椋趸跗谒魵馀c涂層中Al 元素發(fā)生選擇性氧化,生成單分子氧化膜,其后是以電化學(xué)反應(yīng)實(shí)現(xiàn)膜的生長,且生長速度較慢,Al 并未被完全氧化成Al2O3,富鋁層還可以為表面生成致密的Al2O3膜提供充足的Al 源,很好地阻擋O對(duì)基體的侵蝕。氧化初期起主導(dǎo)作用的是界面反應(yīng)。隨著氧化膜的形成,反應(yīng)物質(zhì)的擴(kuò)散速度成為氧化速度的控制因素。一方面,形成的Al2O3膜可降低元素?cái)U(kuò)散系數(shù);另一方面,未被完全氧化成Al2O3的富鋁層還可以為合金繼續(xù)生成Al2O3膜提供充足的Al 源,兩方面原因使得TP347H FG-AlSi 涂層具有優(yōu)良的抗蒸汽氧化性能。
3 結(jié)論
(1) 氧化初期(0~350 h) TP347H FG的動(dòng)力學(xué)曲線遵循拋物線關(guān)系,拋物線速率常數(shù)為0.0058 mg2·cm-4·h-1,氧化600 h 后外層氧化膜發(fā)生嚴(yán)重剝落,氧化1000 h 后增重為:-2.91814 mg·cm-2。外層疏松層瘤狀氧化物Fe3O4與試樣表面氧化膜下方內(nèi)氧化物FeCr2O4呈雙層結(jié)構(gòu)。
(2) Al-Si 涂層試樣氧化1000 h 的氧化動(dòng)力學(xué)曲線遵循拋物線規(guī)律,氧化增重為:0.06157 mg·cm-2,試樣表面形成保護(hù)性Al2O3 氧化膜,可顯著提升TP347H FG鋼抗蒸汽氧化能力,較基體的抗蒸汽氧化性能提高47倍。
(3) HR3C 合金在200 h 之前的氧化動(dòng)力學(xué)曲線遵從拋物線規(guī)律,拋物線速率常數(shù)為3.464×10- 5 mg2·cm- 4·h- 1,200 h 之后氧化增重基本穩(wěn)定。HR3C合金中較高的Cr 含量促使HR3C在較短時(shí)間內(nèi),表面即形成致密連續(xù)的Cr2O3膜,在650 ℃純水蒸汽環(huán)境下具有良好的抗氧化性能。
(4) TP347H FG-AlSi 涂層抗蒸汽氧化性能與HR3C 相當(dāng),氧化1000 h 內(nèi)氧化增重略低于HR3C。Cr 元素是提高合金抗氧化性能的關(guān)鍵,表面涂層亦可降低合金氧化速率,兩種途徑可為現(xiàn)役及下一代鍋爐機(jī)組提供技術(shù)支撐。
免責(zé)聲明:本網(wǎng)站所轉(zhuǎn)載的文字、圖片與視頻資料版權(quán)歸原創(chuàng)作者所有,如果涉及侵權(quán),請(qǐng)第一時(shí)間聯(lián)系本網(wǎng)刪除。
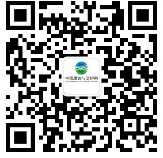
官方微信
《中國腐蝕與防護(hù)網(wǎng)電子期刊》征訂啟事
- 投稿聯(lián)系:編輯部
- 電話:010-62313558-806
- 郵箱:fsfhzy666@163.com
- 中國腐蝕與防護(hù)網(wǎng)官方QQ群:140808414