0 引言
溶劑型涂料在生產(chǎn)過程和施工過程中釋放大量VOC(揮發(fā)性有機(jī)化合物),污染了環(huán)境,危害了生產(chǎn)和施工工作人員的身體健康,同事在施工、貯運(yùn)過程中存在易燃、易爆等安全隱患,有鑒于此,水性化將是發(fā)展的必然趨勢(shì)水性涂料在金屬防銹涂料的市場(chǎng)份額將不斷提高,逐步占領(lǐng)溶劑型涂料的市場(chǎng)。
水性涂料涂覆于噴砂處理后的鋼板,容易使鋼板產(chǎn)生閃蝕現(xiàn)象,閃蝕的產(chǎn)生會(huì)減少鋼板的使用壽命。因此,許多車橋生產(chǎn)廠家都采用漆前磷化工藝以提高漆面的耐腐蝕性、裝飾性等指標(biāo)。但是,大量的磷化處理會(huì)導(dǎo)致廢氣、廢渣、廢液的產(chǎn)生,對(duì)環(huán)境造成污染,并且處理“三廢”的成本較高。
本研究在基料樹脂丙烯酸樹脂中直接引入磷酸基團(tuán),以期在涂層成膜的過程中引入磷化作用,從而做到清潔生產(chǎn),節(jié)約能源。
本研究采用預(yù)乳化工藝,半連續(xù)種子聚合方法,以甲基丙烯酸甲酯、丙烯酸丁酯等為共聚單體,引入環(huán)氧丙烯酸酯及具有抗閃蝕功能的磷酸酯功能單體,成功制備了水性含磷丙烯酸防銹乳液。
1 試驗(yàn)部分
1.1 含磷丙烯酸乳液的制備
1.1.1 合成原料及基本配方
合成原料及基本配方見表1。
1.1.2 丙烯酸乳液制備工藝
1)預(yù)乳液的制備:向裝有攪拌裝置的三口燒瓶中加入乳化劑、去離子水、磷酸酯功能單體和環(huán)氧丙烯酸酯,待攪拌融解均勻后,加入和混合單體(MMA、BA、MAA、HEA),攪拌30 min使其均勻融解。
2)聚合物乳液的制備:向裝有攪拌裝置、回流冷卻器及滴液漏斗的三口燒瓶中加入乳化劑、去離子水、碳酸氫鈉,攪拌使其融解并將三口燒瓶放入60 ℃ 的水浴鍋中,邊攪拌邊加入過硫酸銨溶液及10%的預(yù)乳液,升溫至80 ℃后,待乳液泛藍(lán)光時(shí),在3.5 h內(nèi)同時(shí)加入剩余預(yù)乳液及過硫酸銨溶液,保溫1 .5 h,降溫至40 ℃ 以下并調(diào)節(jié)pH為7~8,用100目的絲網(wǎng)過濾,出料,即得到聚合物乳液。
1.2 水性防銹涂料的制備
將分散劑、潤(rùn)濕劑、消泡劑、pH 調(diào)節(jié)劑、抗閃銹劑、顏填料依序加入去離子水中,經(jīng)高速分散制得色漿,然后在低速攪拌下將色漿、含磷丙烯酸乳乳液、成膜助劑混合攪拌均勻,將pH 控制在8左右,過濾出料。水性防銹涂料配方見表2。
1.3 性能測(cè)試
1)固含量:采用質(zhì)量法測(cè)定。
2)轉(zhuǎn)化率:由⑴測(cè)出的固含量與理論固含量之比即得轉(zhuǎn)化率。
3)Ca2+穩(wěn)定性:將乳液與5%的CaCl2 水溶液以5 ∶1 的質(zhì)量比混合均勻。將混合液倒入試管中,靜置48 h后觀察,如發(fā)現(xiàn)分層、絮凝、沉淀等現(xiàn)象,則為不通過。
4)凝膠率:聚合反應(yīng)結(jié)束后,用300 目濾布過濾,將凝聚物水洗后于100 ℃烘干(約2 h),稱質(zhì)量,計(jì)算凝聚物占單體總量的百分?jǐn)?shù)。
5)乳液防銹性能測(cè)試:將乳液與成膜助劑攪拌混合均勻后,涂刷在經(jīng)打磨、溶劑處理過的馬口鐵板上,烘干后用石蠟、松香的混合物進(jìn)行封邊,浸泡于3%的NaCl 水溶液中,觀察鐵板表面何時(shí)起泡及生銹。附著力均按涂料測(cè)定標(biāo)準(zhǔn)測(cè)定。
2 結(jié)果與討論
2.1 乳化劑用量對(duì)乳液性能的影響
實(shí)驗(yàn)選用的是陰離子型乳化劑壬基酚乙氧基化合物磷酸酯(RE-610),可以通過雙電層的排斥作用起到一定的穩(wěn)定作用,即陰離子部分先吸附在乳液粒子表面,在乳液粒子與液體截面間形成一負(fù)電層。在液相中,此負(fù)電層又吸一帶電的電子層,從而形成雙電層。此雙電層能有效地使乳液粒子相互排斥,支配聚合體系的穩(wěn)定性。在本試驗(yàn)中,考察不同乳化劑用量(相對(duì)于單體總量)對(duì)乳液及涂膜性能的影響。結(jié)果見表3。
由表3結(jié)果可知,隨著乳化劑用量的增大,聚合穩(wěn)定性先變好然后變差,固含量先增大后減小,乳液的黏度逐漸增大,同時(shí)涂膜的吸水率逐漸增大。當(dāng)乳化劑用量繼續(xù)增加時(shí),體系中生成的膠束數(shù)目增多,乳膠粒徑減小,大大增加了粒子間碰撞的機(jī)會(huì),易出現(xiàn)凝膠,使體系穩(wěn)定性下降。由表1還可看出隨著乳化劑用量的增大,膠膜的吸水率逐漸增加。綜合考慮乳液和涂膜性能,確定乳化劑用量為單體總量的3%。
2.2 交聯(lián)單體用量對(duì)乳液性能的影響
本實(shí)驗(yàn)采用分階段加入交聯(lián)單體自制環(huán)氧丙烯酸酯/MAA的方法,將交聯(lián)官能團(tuán)固定在不同的層中,實(shí)驗(yàn)保證兩種官能團(tuán)比例1:1的情況下,考察交聯(lián)單體用量變化(以環(huán)氧丙烯酸酯為例)對(duì)乳液聚合穩(wěn)定性、漆膜的交聯(lián)度、耐鹽水性的影響。結(jié)果見表4。
由表4可知,隨環(huán)氧丙烯酸酯用量的增加,吸水率逐漸下降,附著力及耐鹽水性有所提高。由于環(huán)氧丙烯酸酯本身具有附著力強(qiáng)的優(yōu)良性能,因此涂膜的附著力隨著環(huán)氧樹脂用量的增加而提高。但一定量乳化劑條件下,過多的環(huán)氧丙烯酸酯就會(huì)使體系趨于不穩(wěn)定而分層。綜合各項(xiàng)性能,選定環(huán)氧丙烯酸酯用量為單體總量的4%。
2.3 磷酸酯功能單體用量對(duì)乳液性能的影響
借鑒磷化處理的原理,為了提高涂層對(duì)金屬表面的濕附著力,在乳液中引入了磷酸酯單體。磷酸酯單體中磷羥基與金屬表面有較強(qiáng)的螯合作用,可以與多價(jià)金屬作用形成磷酸鹽絡(luò)合物,并以共價(jià)鍵的形式把聚合物牢固地連接到金屬基材上,在提高乳膠漆在各種金屬基材附著力的同時(shí)也能起到抗閃蝕作用。本研究考察了磷酸酯單體用量對(duì)乳液及漆膜性能影響,結(jié)果見表5。
由表5可知,隨著磷酸酯單體用量增大,凝膠率先下降后升高,這是因?yàn)楹铣傻牧姿狨误w本身良好的乳化性,所以在前期隨著磷酸酯單體的增加,乳液的凝膠率下降,聚合穩(wěn)定性增加。但隨著磷酸酯單體用量的繼續(xù)增多,體系的pH下降,大大增加了粒子間碰撞的機(jī)會(huì),進(jìn)而產(chǎn)生凝膠和細(xì)渣,體系不穩(wěn)定。由表5還可看出,隨著磷酸酯用量的增多,漆膜在金屬底材上的附著力、耐鹽水性及抗閃蝕性得到明顯提高。由表5綜合分析,當(dāng)丙烯酸磷酸酯單體用量為單體總量的4%時(shí),反應(yīng)體系穩(wěn)定,且附著力均達(dá)到1級(jí),耐鹽水性最好。
2.4 防腐涂料的性能測(cè)試
漆干膜厚度要求達(dá)到80 ~ 150 μm,底漆干燥后打磨,噴涂葉片面漆,干膜厚度要達(dá)到100 ~ 150 μm。防腐涂料的性能見表6。
3 結(jié)語
1)當(dāng)乳化劑用量、環(huán)氧丙烯酸酯用量、丙烯酸磷酸酯單體用量分別為單體總量的2.6%、0.5%、4%、4.5%時(shí),乳液及涂膜的綜合性能最佳,耐鹽水700h,附著力1級(jí)。
2)解決了普通水性防銹乳液易出現(xiàn)閃蝕的問題單組分烤漆很好的解決了涂料利用率低的問題,省去了基材表面需要磷化處理的工序,不會(huì)產(chǎn)生磷化處理廢液,作為水性防腐涂料很好的符合了鋼板彈簧涂層防腐質(zhì)量與環(huán)保的新要求。
3)通過粒徑分析、紅外光譜、透射表征手段對(duì)乳液進(jìn)行分析表明,得到的乳膠粒平均粒徑為100 nm左右,粒徑分布窄,且具有核殼結(jié)構(gòu);聚合單體反應(yīng)完全,得到的乳液性能穩(wěn)定。
4)通過加入防銹顏料、填料、分散劑、叔丙乳液制備的水性防腐涂料,具有良好的性能,對(duì)金屬底材有較好的保護(hù)作用。
更多關(guān)于材料方面、材料腐蝕控制、材料科普等方面的國(guó)內(nèi)外最新動(dòng)態(tài),我們網(wǎng)站會(huì)不斷更新。希望大家一直關(guān)注中國(guó)腐蝕與防護(hù)網(wǎng)http://www.ecorr.org
責(zé)任編輯:王元
《中國(guó)腐蝕與防護(hù)網(wǎng)電子期刊》征訂啟事
投稿聯(lián)系:編輯部
電話:010-62313558-806
郵箱:fsfhzy666@163.com
中國(guó)腐蝕與防護(hù)網(wǎng)官方 QQ群:140808414
免責(zé)聲明:本網(wǎng)站所轉(zhuǎn)載的文字、圖片與視頻資料版權(quán)歸原創(chuàng)作者所有,如果涉及侵權(quán),請(qǐng)第一時(shí)間聯(lián)系本網(wǎng)刪除。
-
標(biāo)簽: 溶劑型涂料, 磷環(huán)氧丙烯酸防腐乳液, 合成及其涂料的制備
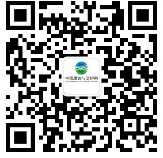
官方微信
《中國(guó)腐蝕與防護(hù)網(wǎng)電子期刊》征訂啟事
- 投稿聯(lián)系:編輯部
- 電話:010-62313558-806
- 郵箱:fsfhzy666@163.com
- 中國(guó)腐蝕與防護(hù)網(wǎng)官方QQ群:140808414