徐學武
(中海石油(中國)有限公司湛江分公司,湛江524057)
海底管道作為海上油氣集輸的大動脈,相對于其他運輸方式,由于具有更加經濟、安全、節能、快捷的優勢,正發揮著日益重要的作用。然而海洋環境惡劣,作業支持困難、修復難度大且成本高,一旦發生油氣泄漏事故不僅會造成經濟損失,而且有可能導致火災爆炸、環境污染。據統計,中國海洋石油總公司所屬海底油氣管道(以下簡稱海管)從1995年至2012 年共發生故障38 起,其中內腐蝕原因11起,占28。9%,且有日益增長的趨勢。開展海管內腐蝕機理與防護技術的研究對延長其使用壽命、保障油氣田安全生產有十分重要的意義。
1 內腐蝕原因分析
海管腐蝕形式與其所處的海洋環境和采取的防護措施密切相關,按腐蝕位置分為管內腐蝕與管外腐蝕。管內腐蝕一般發生在油氣水混輸管道,原因可歸納為主觀和客觀兩大類:主觀原因包括防腐蝕收稿日期:2013-08-15通信作者:徐學武(1979-),工程師,碩士,從事管道防腐蝕相關工作,13726911122,xxwchinergy@163。com措施、施工質量、運營管理等;客觀原因包括管道所處環境、輸送介質的化學組成及其腐蝕性、輸送工藝的物理因素等。原因按主次順序概括為:
(1)腐蝕性介質 主要有CO2、H2S、SO2、O2、Cl-、水、細菌、酸堿鹽、固體沉凝物等。它們都可能在管內引發化學和電化學腐蝕,引起管壁減薄、坑蝕、氫鼓泡、氫脆或應力腐蝕開裂,從而導致管體破壞。此外,腐蝕產物還會污染管輸介質。
(2)輸送工藝和物理因素 輸送流體的溫度、壓力、流速、流量等工藝參數的變化,夾帶的固體顆粒、振動、沉淀、砂磨等因素的相互作用都會對管道內壁腐蝕起到不同程度的促進作用。例如,HZ26-1北為氣舉井,采出的原油含有砂粒,從水平段到立管彎頭后由于流速的變化造成沖蝕穿孔。
(3)防腐蝕設計缺陷 根據生產經驗,很多油氣田投產后發現原油天然氣實際物性和ODP(總體開發方案)的原始設計差異較大。比如,文昌油田某海管原設計CO2含量僅為7。48%,且不含H2S,投產后CO2含量最高達到20%,且存在少量H2S,發生腐蝕穿孔事件。
(4)運營階段防腐蝕管理不當 海管投用后,作業者沒有根據生產工況篩選化學藥劑;未采取新技術進行有效的腐蝕監測、檢測;除氧、脫水和露點控制等工藝措施不到位等,從而導致腐蝕加劇。
(5)施工質量不高 管道制作及安裝過程存在焊接、除銹、涂裝、固化等質量問題及補口、維修未完全按防腐蝕標準和規范執行,都可埋下腐蝕隱患。在環焊縫處或者覆蓋層缺陷造成的裸露部位,會造成大陰極小陽極的不利面積比,加速該部位腐蝕穿孔。帶有防腐蝕內涂層的管道,在管接頭焊接時受高溫影響,使熱影響區的內涂層失效,造成腐蝕電流集中。另外,由于管端無防水帽密封或者損壞導致水進入保溫層,保溫失效后會引發管內細菌腐蝕。
2 內腐蝕分析
2.1 CO2腐蝕
隨著深層含CO2油氣井的開發、含水量的增加以及注CO2強化采油工藝的應用,CO2腐蝕已成為目前亟待解決的重要課題之一。CO2腐蝕最典型的特征是管道的局部產生點蝕、蘚狀腐蝕和臺面狀腐蝕,后者是腐蝕過程最嚴重的。當管道中存在游離態水時,CO2溶入水生成碳酸,在相同pH 下,碳酸對低碳鋼的腐蝕速率可達3~6mm/a。其腐蝕產物碳酸鹽(FeCO3、CaCO3)或結垢產物膜在鋼鐵表面不同區域的覆蓋程度不同,這種差異形成了自催化作用很強的腐蝕電偶,極易造成CO2局部腐蝕。
影響CO2腐蝕的因素比較多,溫度、水分、CO2分壓、流速、合金元素、Cl-、HCO3-、Ca2+ 和Mg2+、細菌、Fe3C濃度、FeCO3溶解度、保護膜、管材的熱處理及顯微組織等對腐蝕都有一定的影響[1]。
2.2 H2S腐蝕
H2S是油氣水混輸介質中含有的酸性氣體,在溫度、壓力、流速以及交變應力等多種因素的影響下,具有較強的腐蝕性,通常表現為點蝕。
腐蝕產物FeS的溶解度非常低,通常黏著于金屬表面成為產物膜。當FeS致密且與金屬基體結合緊密時,對腐蝕具有一定的減緩作用,反之,可與金屬基體形成電位差為0。2~0。4V的強電偶,在腐蝕產物膜的缺陷處加速腐蝕,造成很深的點蝕。腐蝕速率隨H2S濃度的變化主要與輸送介質的含水量和相應的腐蝕產物有關。含水量低時,腐蝕產物主要由FeS和FeS2組成,晶粒直徑小于0。02μm,這將阻止Fe2+ 的擴散,起到一定的保護作用;含水量較高時,腐蝕產物主要為Fe9S8,其晶格不完整,不能阻止Fe2+ 的擴散,從而導致管道嚴重腐蝕。
H2S作為陰極去極化劑,不僅由于電化學腐蝕造成點蝕,還經常由于氫原子進入金屬而導致硫化氫應力開裂(SSC)和氫致開裂(HIC)。當溶液中或金屬基體表面有硫化物存在時,一定程度上阻止了氫離子結合成氫分子,使氫原子在金屬表面不斷集結并進入金屬內部,當遇到管材內部初始裂紋、空隙、夾雜、晶格層間錯斷等缺陷時,氫原子就會在這些缺陷部位結合成氫分子,而氫分子的體積是氫原子的20倍。由于體積膨脹,在金屬內部產生很大的應力,致使管材產生微裂紋。在外加拉應力、殘余應力的共同作用下,便會發生硫化物應力腐蝕開裂[2]。
2.3 CO2、H2S共存環境下的腐蝕
經驗表明,不同的H2S與CO2比例,形成的腐蝕產物膜有所不同。當H2S含量相對CO2較低時,以CO2腐蝕為主,腐蝕產物膜中只有少量FeS,因而其力學性能較低。反之,以H2S腐蝕為主,產物膜主要由非化學計量的FeS組成,因此其力學性能進一步提高。繼續增大H2S含量,局部腐蝕反而受到抑制。在同時含有高濃度H2S、CO2的體系中,CO2對H2S腐蝕過程的影響國內外尚無統一認識。一般認為,CO2的存在對腐蝕起促進作用,H2S的存在既能通過陰極反應加速CO2腐蝕,又能通過FeS沉淀減緩腐蝕。
CO2和H2S共存環境下影響腐蝕的因素主要有H2S濃度、pH、溫度、壓力,介質中的離子、暴露時間、H2S與CO2含量之比,介質流速、介質載荷、管道材質等。
2.4 Cl- 腐蝕
由于氯離子淌度大半徑小,很容易穿透腐蝕產物向腐蝕孔內遷移,形成FeCl2,其水解后孔內H+濃度增大,產生“自催化作用”,加大孔內外的電勢差,使孔迅速深挖生長,從而誘發點蝕和應力腐蝕,促進縫隙腐蝕。
2.5 多相流腐蝕
根據力學和化學的相對支配作用的強弱程度,多相流腐蝕可以劃分為兩類:①沖刷腐蝕,主要是由于多相流體的力學作用導致金屬表面材料的損傷和減薄。是金屬表面與腐蝕流體之間由于相對高速運動而引起的金屬損壞現象;②流動促進腐蝕,主要是流動促進反應介質或腐蝕產物傳質速率加快或金屬表面反應速率加快,導致材料表面快速腐蝕。一般而言,隨著流速增加,腐蝕介質到達管壁表面的速度增加,腐蝕產物離開金屬表面的速度也增加,還會使緩蝕劑不能充分到達管道表面而影響其發揮作用,因而腐蝕速度加快。最具腐蝕性的流態是段塞流、層流、霧狀流,當流速增加促進液體到達湍流狀態時,能擊穿緊貼金屬表面的幾乎靜止的邊界層,并對金屬表面產生很高的切應力、剝除保護膜。所以,較高的流速往往導致較高的腐蝕速率,如果介質中含有固體顆粒,則將加劇沖刷腐蝕,因此必須控制流速的上限。但是,如果流速太低,也可造成管道底部積液而發生水線、垢下等腐蝕。
2.6 微生物腐蝕
凡是同水、土壤或濕潤空氣相接觸的金屬設施,都可能遭到微生物腐蝕。與腐蝕有關的微生物主要是細菌類,因而也成細菌腐蝕。其中最主要的是直接參與自然界硫、鐵循環的微生物。按其生長發育中對氧的需求分為嗜氧性及厭氧性兩類,前者在有氧存在時才能生長繁殖,如硫氧化細菌、鐵細菌等;硫氧化細菌能將硫及硫化物氧化成硫酸;鐵細菌,有桿菌、球菌和絲狀菌等形狀。后者主要是在缺氧的條件下生存的硫酸鹽還原菌(SRB)。SRB造成的腐蝕類型呈點蝕等局部腐蝕。腐蝕產物通常是黑色的帶有難聞氣味的硫化物。SRB具有的氫化酶能移去陰極區的氫原子,促進了腐蝕過程中的陰極去極化反應,或生成硫化物而加速金屬的腐蝕[3]。
3 全生命周期完整性管理下的管內腐蝕防護措施
在分析了海管內腐蝕及常見影響因素后,為了確保管道在服役期間的安全可靠,很有必要從全生命周期的完整性管理角度出發,對其進行設計、制造、安裝、運營等全過程進行內防腐蝕控制。一般情況下,海管內腐蝕的防護措施有:增加管壁厚作為腐蝕裕度來減少腐蝕泄漏;對輸送介質脫水、脫氧等來抑制腐蝕;在輸送介質中添加緩蝕劑來阻止和減緩腐蝕速度。另外,在管道內壁噴涂液體涂料、固體涂料和砂漿涂層以及采用耐腐蝕金屬合金內襯等也是常見的防腐蝕措施[4]。
3.1 設計選材
常用管型有:直縫電阻焊管(ERW),直縫埋弧焊管(LSAW),無縫管(SMLS),螺旋縫埋弧焊鋼管(SSAW),高鋼級、大口徑、厚壁鋼管。常用管材有普通碳鋼(16Mn,Q235 等)、管線鋼(X52,X60,X 70,X80等)、不銹鋼(對H2S、CO2、Cl-、微生物等耐蝕性)。提高材料自身的抗腐蝕能力是保證管道本質安全的關鍵:
(1)整體采用耐蝕合金鋼:可靠、方便但是成本高 一般采用馬氏體、鐵素體、奧氏體、雙相不銹鋼。
國外在含CO2條件下通常采用含鉻鐵素體不銹鋼管(9%~13%鉻);在CO2和Cl- 共存的嚴重腐蝕條件下選用含鉻、錳、鎳的不銹鋼(22%~25%鉻)。
(2)耐蝕鋼/合金為襯里的雙金屬復合管:可靠、方便、經濟 襯管可根據腐蝕環境不同選用相應薄壁耐蝕合金材料(普通/特種不銹鋼、鈦/鋁、銅合金等),保證良好的耐腐蝕性能;基管采用碳鋼管(無縫或焊接鋼)或其他合金管,保證優異的機械力學性能。雙金屬復合管性價比較高,已成為海管茍刻腐蝕環境中應用較多的防腐方式。
(3)普通鋼+非金屬涂層或襯里:經濟、可靠性一般 采用內壁涂層或襯里雖然價格便宜,但處理工藝復雜,一旦有涂層剝落等缺陷,容易導致嚴重的局部腐蝕。另外,涂層破損的幾率也比較大,特別是補口處。
(4)玻璃鋼、塑料等非金屬材料:強度和承壓能力差 玻璃鋼管道目前在國外應用廣泛,但在國內不多。塑料管材不僅耐腐蝕而且制造工藝簡單,環保性好。目前使用最多的是聚乙烯管材,主要有兩種類型:①加內襯鋼管,由聚乙烯管在鋼管內拔制而成;②強力聚乙烯管,由纏繞柔韌材料(金屬絲、帶、纖維)的玻璃鋼外殼和加金屬的內壁制成。
在這一類內腐蝕防護措施中,優先推薦采用耐蝕合金鋼及以耐腐蝕/合金為襯里的雙金屬復合管。其中,含H2S、CO2環境耐蝕鋼/合金選材指南見圖1。此外,為了避免電偶腐蝕,管道系統盡量選用單一材料,如必須選用復合材料時,應選擇電極電位相近的材料。
圖1 耐蝕鋼/合金選材指南
Fig.1 Selection guide of anticorrosion steels/alloys
3.2 制管
管道加工制造階段如果由于焊接工藝、施工質量不過關也會對后續服役帶來腐蝕隱患。比如,焊縫缺陷往往導致裂紋而使海水滲進管內或者加劇管道輸送介質對內壁的腐蝕、破壞。
(1)直縫電阻焊鋼管(ERW) 采用電阻接觸焊,防止電弧燒傷。內外毛刺應清理干凈。最危險的缺陷是產生冷焊,原因是無填充金屬、焊速高、在線超聲波很難發現。主要控制措施:①在線壓扁試驗,檢查試驗樣品是否有冷焊;②每根鋼管都必須嚴格實行靜水壓試驗;③實行全焊縫離線超聲波手探。
(2)無縫鋼管(SMLS) 常見缺陷包括層皮、氧化皮、異金屬壓入、折疊。無損探傷時應進行表面全管體100%超聲波和渦流探傷,防止分層、裂紋、凹坑等。
(3)熱煨彎管(Hot Bend) 彎管母管的機械性能(強度、韌性)在彎制熱處理后有所降低,應考慮足夠余量。主要控制外弧壁厚減薄量及內弧皺褶不超標、加熱區過燒。易造成外表面銅污染并導致表面裂紋形成,通過超聲檢測、磁粉檢測嚴格把關。
3.3 涂層和內襯
內涂層與襯里不僅可以有效的減緩內腐蝕,節約管材和維修費,還能顯著提高輸送效率,并防止天然氣水合物堵塞管道,減少清管次數。非金屬涂層絕大多數是隔離性涂層,主要作用是把金屬材料與腐蝕介質隔開。可供含H2S、CO2的酸性油氣田選用的有機涂層和襯里有環氧樹脂、聚氨酯以及環氧粉末等。內噴涂質量控制過程有:原材料入廠的嚴格檢驗;鋼管表面處理:包括灰塵污染度、錨紋深度、除銹等級的嚴格控制,如不合格將造成批量涂層防腐等級下降;涂敷過程的鋼管加熱溫度;成品檢驗過程中:涂層厚度、涂層剝離強度、涂層抗沖擊強度、陰極剝離強度的嚴格把關,等。
玻璃鋼內襯管具有強度高,耐強酸、堿、鹽和鹵水腐蝕,電和熱絕緣性好以及保溫等優點,其防腐性能比內涂層要好,尤其適合用做溫度和壓力較高的集輸管道。由于內涂層或襯管不可避免的存在針孔或受到損傷,所以使用防腐層的同時通常要添加適量的緩蝕劑[6]。
3.4 安裝
管道吊裝前應保證每根鋼管兩端管端保護器完整以保護鋼管坡口。吊裝過程中應避免磕碰造成管體及涂層損傷。對于雙層保溫管,外管伸出的一端須使用吊鉤,內管伸出的一端使用吊帶吊裝,不可使用鋼絲繩。海管鋪設主要包括入船檢驗、焊口組對、焊接、檢驗(外觀、無損)、節點涂敷、入水等階段。組對不合格會影響焊接質量和自動超聲波評判。焊接過程須嚴格控制夾渣、燒穿、未熔合、表面等缺陷。
3.5 運營維護
3.5.1 緩蝕劑篩選及評價
合理使用緩蝕劑是防止和減緩油氣管道內腐蝕的有效手段。按照成分可以分為無機和有機緩蝕劑兩類。其防腐蝕效果與井況、緩蝕劑類型、注入量、加注周期、加注工藝、緩蝕劑濃度等因素有關。對緩蝕劑的要求除了具有較高的緩蝕效率以減少緩蝕劑用量外,還應具備極好的后效性能以延長緩蝕劑保護周期。氣田緩蝕劑注入量設計主要考慮海管形成緩蝕劑保護膜的厚度與持續添加保持。國內有研究認為,管壁上形成緩蝕劑膜厚度在100μm 左右,可達較好的應用效果。海管越長、內表面積越大所需維持其成膜厚度的藥劑量越大,并需通過持續加注藥劑維持因沖刷和消耗而減薄的緩蝕劑膜厚度。
海管投產后,隨著輸送介質組分、工藝參數等的變化,需要對加注的緩蝕劑進行篩選、評價。篩選試驗的條件應注重于會影響緩蝕劑效率的主要因素如介質的濃度、溫度、流速及金屬基材的材質等。通過初步篩選被列為優良的緩蝕劑,應再進行中間模擬試驗,中試合格后再投入工業試驗系統做進一步評價,并進行配方和實用技術的完善,取得成效后方可推廣生產應用。測試評定方法主要有失重試驗、電化學測定和物理分析技術等[7]。
緩蝕劑評價的主要參考標準有GB10124-1988(金屬材料實驗室均勻腐蝕全浸試驗方法),NACE RP-0775-1991(腐蝕評判標準),ASTMA923C(不銹鋼點蝕試驗方法)等。通常情況下,中性介質中多使用無機緩蝕劑,以鈍化型和沉淀型為主。酸性介質使用的緩蝕劑大多為有機物,以吸附型為主。但是單一的緩蝕劑往往無法滿足要求,需考慮復配使用。此外,還應綜合考慮與殺菌劑、破乳劑、防蠟劑、除垢劑等其他種類化學藥劑的配伍性,并根據介質組分和腐蝕產物化驗結果,及時開展藥劑效果評估。
3.5.2 工藝處理
水是產生管內腐蝕的直接因素,主要來源有:從地層開采出來的石油天然氣中包含的游離態水、氣態水;管道頂部濕氣凝結水。可以通過捕集器、分離器、管道分液器等最大限度的降低含水率,也有必要向管內注入乙二醇、甲醇以沖淡游離水并防止水合物的生成,從而降低腐蝕速率。天然氣的干燥度是避免內腐蝕關鍵因素,應充分保證天然氣脫水設備工作的可靠性,并持續監測天然的水露點。對于含CO2、H2S的油氣,由于水分的存在會形成強腐蝕性的酸液,對集輸管道和設備造成腐蝕,必須通過脫碳、脫硫等工藝進行處理,同時還應控制pH,溫度、壓力等工藝參數。對于出砂嚴重的油氣井必須采取有效的除砂工藝措施。
3.5.3 流態控制
管輸介質的流速應控制在腐蝕最小范圍,流速的下限應使雜質懸浮在管輸介質中,使管道內積存的腐蝕性雜質為最少。例如,HZ19-2/3油田海管存在平緩段,由于低流速導致沉砂,不僅影響了緩蝕劑效果,而且溫度適合細菌生長,在CO2和細菌的共同作用下,在砂底部形成明顯的垢下腐蝕。流速的上限應使磨蝕、沖蝕、汽蝕為最小。界限流速可以根據試驗結果及實踐經驗來確定。此外,還應盡量避免間歇流,否則應控制管輸介質的流速足以沖掃掉間歇期間積聚在管內低處的水和沉積物,如磨蝕產物、固體顆粒、泥沙、灰塵、垢等。
3.5.4 內腐蝕監測與檢測
為了跟蹤海底管道輸送介質的動態變化,及時分析各種內腐蝕因素影響的嚴重程度,需要采取多種手段進行腐蝕監測與檢測,從而為制定合理有效的腐蝕防護措施提供決策支持。
(1)監測方法與要求 采用常用的腐蝕掛片、電阻探針、旁路腐蝕監測管段、線性極化電阻法、場指紋檢測(FSM)、腐蝕產物分析、輸送介質組分變化分析等。其中組分分析最為關鍵,主要有油樣全分析(含水、含硫、運動及動力粘度、密度、凝固點等)、水樣全分析(溶解性氣體、總鐵及二價鐵含量、細菌等)、天然氣積液分析、H2S和CO2含量及分壓、海管通球后組分分析。監測手段應用最多的是腐蝕掛片分析:表面腐蝕狀態(如斑狀、坑狀、均勻態等)和失重分析。還可以委托具有獨立資質的第三方進行。最后形成評估報告。
(2)檢測內容與要求 海管內檢測內容有內部金屬損失、凹坑、變形、裂紋、氣泡、夾渣、管壁分層等。檢測前應進行可行性研究,編制詳細的實施方案與應急預案。可選用幾何變形檢測、漏磁、超聲波、電磁超聲檢測等智能檢測技術。檢測周期和頻率可根據風險評估要求及生產影響因素確定,應在試運行前進行內部基線檢測,在投運后兩年內進行一次內檢測,以后根據上次評估結果調整檢測周期。此外,對于通球檢測風險較大或者不便停輸的海管可以采用內腐蝕直接評估法。
4 結束語
管道防腐蝕工作目的是最大限度的延長其使用壽命從而實現經濟和社會效益最大化。綜合國內外先進管理經驗和良好實踐,需要采取系統化、全生命周期的完整性管理模式開展管道內防腐蝕工作,以達到經濟性和可靠性的最佳平衡。設計時就應通盤考慮全生命周期成本最小化、管道結構完整性以及后續防腐蝕的便利性和有效性。施工時應考慮環境與施工因素的有機結合。投產初期應及時進行基線評估;運營期應根據生產實際工況與設計條件的對比,根據每條海管的具體特點采取差異化的精細防腐蝕措施,有計劃的開展通球清管、化學藥劑篩選、腐蝕監測、檢測、分析評估。最后,還應利用腐蝕管理數據庫等各種信息管理系統建立腐蝕防護質量評估體系,實現動態跟蹤、控制并做到持續改進。
參考文獻:
[1] 胡鵬飛,文九巴,李全安。國內外油氣管道腐蝕及防護技術研究現狀及進展[J]。河南科技大學學報:自然科學版,2003,24(2):100-101。
[2] 王引真,熊偉,王彥芳。油氣管道選材[M]。北京:中國石化出版社,2010。
[3] 楊啟明,李琴,李又綠。石油化工設備腐蝕與防護[M]。北京:石油工業出版社,2010。
[4] 姜信德,李言濤,杜芳林。海底管線腐蝕與防護的研究進展[J]。材料保護,2010,43(4):65-66。
[5] NACE MR0175/ISO 15156 石油和天然氣工業-油氣開采中用于含H2S環境材料[S]。
[6] 崔斌,臧國軍,趙銳。油氣集輸管道內腐蝕及內防腐蝕技術[J]。石油化工設計,2007,24(1):53-54。
[7] 高榮杰,杜敏。海洋腐蝕與防護技術[M]。北京:化學工業出版社,2011。
責任編輯:王元
免責聲明:本網站所轉載的文字、圖片與視頻資料版權歸原創作者所有,如果涉及侵權,請第一時間聯系本網刪除。
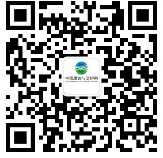
官方微信
《中國腐蝕與防護網電子期刊》征訂啟事
- 投稿聯系:編輯部
- 電話:010-62316606-806
- 郵箱:fsfhzy666@163.com
- 中國腐蝕與防護網官方QQ群:140808414