1 引言
近年來(lái),汽車消費(fèi)者和生產(chǎn)企業(yè)對(duì)汽車腐蝕問(wèn)題日益重視。車身腐蝕不僅有礙汽車美觀性,而且會(huì)導(dǎo)致強(qiáng)度下降,影響到行車的安全性。車身防腐性能提升的途徑主要有:一使用耐腐蝕性能好的車身板材,如鍍鋅板等;二增加防腐輔助工藝,如空腔注蠟、噴蠟等。三優(yōu)化電泳結(jié)構(gòu)設(shè)計(jì),保證車身電泳涂層厚度,使之具有充分的耐腐蝕能力。其中第三者在車身防腐過(guò)程中充當(dāng)著十分重要的角色,是防止車身發(fā)生由內(nèi)至外腐蝕的主要手段。作為車身設(shè)計(jì)部門的工程師,第三者也是關(guān)注的重點(diǎn)。
車身的內(nèi)腔具有復(fù)雜的結(jié)構(gòu),往往也是電泳涂層厚度不足問(wèn)題的高發(fā)區(qū)域。工程上為了檢驗(yàn)車身電泳后內(nèi)腔的漆膜厚度,以評(píng)估電泳結(jié)構(gòu)設(shè)計(jì)的可行性,采用的方法一般是通過(guò)試制樣車,電泳烘干后進(jìn)行切割解剖,然后使用測(cè)厚儀器進(jìn)行人工逐點(diǎn)測(cè)量、記錄。當(dāng)發(fā)現(xiàn)風(fēng)險(xiǎn)區(qū)域,發(fā)生結(jié)構(gòu)更改,再次驗(yàn)證時(shí)仍需重復(fù)試制-電泳-割車-測(cè)量步驟。這種“試制-糾錯(cuò)”的模式耗費(fèi)了大量的人力、物力,并且時(shí)間周期長(zhǎng),不利于產(chǎn)品開(kāi)發(fā)的快速迭代。近年來(lái)電泳虛擬仿真技術(shù)的發(fā)展使得在設(shè)計(jì)階段就同步驗(yàn)證車身電泳涂層厚度成為了可能,這一技術(shù)的應(yīng)用有效減少了實(shí)車試制、切割次數(shù),解放了人的重復(fù)勞動(dòng),節(jié)約了開(kāi)發(fā)的成本,縮短了驗(yàn)證的周期。
2 基于仿真技術(shù)的車身電泳涂層驗(yàn)證及優(yōu)化
2.1 電泳涂層的仿真技術(shù)目前各汽車企業(yè)采用的大多是陰極電泳工藝,高分子帶電微粒在電場(chǎng)的作用下向陰極運(yùn)動(dòng)并沉積在車身表面形成電泳漆膜。電泳仿真是通過(guò)數(shù)值計(jì)算的方法,基于法拉第電沉積理論實(shí)現(xiàn)電泳膜厚模擬的。
2.1.1電泳涂層計(jì)算原理電泳過(guò)程伴隨流體運(yùn)動(dòng)、能量轉(zhuǎn)換、能量傳輸、電場(chǎng)作用等一系列動(dòng)態(tài)變化的過(guò)程,很難通過(guò)直接觀測(cè)的方法得到電泳工藝的準(zhǔn)確行為特征,而數(shù)值分析可基于一定的數(shù)學(xué)模型得到完整的流場(chǎng)、電場(chǎng)及化學(xué)特性參數(shù)信息。
車身電泳過(guò)程中,涂料粒子在電流的作用下運(yùn)動(dòng),在陰極表面沉積成膜,而電泳涂膜本身是存在電阻的,漆膜厚度增長(zhǎng),涂膜電阻也隨之增大,當(dāng)電阻達(dá)到一定值后,膜厚便不再增加。在對(duì)車身電泳的仿真中,電流分布的計(jì)算在每個(gè)時(shí)間步可以看作是一個(gè)準(zhǔn)穩(wěn)態(tài)問(wèn)題。仿真計(jì)算原理如下。
初始時(shí)刻,即車身進(jìn)入電泳槽瞬間,時(shí)間為0,膜厚為0,槽液中電壓為電極電壓:
通過(guò)有限元法計(jì)算得到整個(gè)車身的電場(chǎng)分布狀態(tài),進(jìn)而可以得到初始時(shí)刻車身表面各處的電流密度:
其中Rs表示電阻。
由法拉第定律推導(dǎo)的電泳涂膜厚度理論計(jì)算式可知,時(shí)刻的電泳涂膜厚度可由時(shí)刻的電流密度和涂料化學(xué)物理特性決定,即:
其中,涂料的化學(xué)物理參數(shù)通過(guò)涂料參數(shù)標(biāo)定實(shí)驗(yàn)獲得。
ti+1時(shí)刻的電阻受ti時(shí)刻的涂膜厚度影響:
進(jìn)而可以得到ti+1時(shí)刻車身表面各處的電流密度:
重新計(jì)算電場(chǎng)分布,進(jìn)行下一輪迭代,直到電泳結(jié)束。
2.1.2電泳仿真過(guò)程ECoatMaster 是一款能實(shí)現(xiàn)整車宏觀分析和局部分析的電泳仿真軟件,目前在多家汽車企業(yè)得到應(yīng)用,功能強(qiáng)大,界面友好。
運(yùn)用ECoatMaster軟件電泳仿真分析首要任務(wù)是建立常用參數(shù),即涂料參數(shù)、電泳槽模型、工藝參數(shù),接著輸入車體的3D數(shù)據(jù),劃分網(wǎng)格,設(shè)置邊界條件,搭建有限元模型,最后提交計(jì)算,得出分析結(jié)果。
1)涂料參數(shù)測(cè)試。
對(duì)于車身電泳膜厚,準(zhǔn)確的計(jì)算及模擬必須以實(shí)驗(yàn)為基礎(chǔ),受到電泳涂料化學(xué)物理特性的影響,陰極電泳沉積效率一般低于100%。為得到實(shí)際電泳沉積效率,獲得用于電泳仿真分析的沉積參數(shù),首先進(jìn)行了福特盒實(shí)驗(yàn)以確定電泳漆的基本泳透能力,然后以車身材料圓片試樣為實(shí)驗(yàn)對(duì)象進(jìn)行了簡(jiǎn)化模型的電泳實(shí)驗(yàn),以獲得實(shí)際電泳涂料沉積相關(guān)參數(shù)并用于車身電泳膜厚仿真計(jì)算。
實(shí)驗(yàn)參數(shù)標(biāo)定方法見(jiàn)圖1。首先搭建電泳實(shí)驗(yàn)平臺(tái)進(jìn)行實(shí)驗(yàn),記錄實(shí)驗(yàn)過(guò)程中膜厚及電流;然后設(shè)定初始沉積參數(shù)集,建立實(shí)驗(yàn)仿真模型,將仿真結(jié)果與實(shí)驗(yàn)結(jié)果比較,若吻合度滿足要求,則參數(shù)標(biāo)定合格。否則,修改沉積參數(shù),進(jìn)一步仿真計(jì)算,反復(fù)迭代,直到仿真結(jié)果與試驗(yàn)結(jié)果吻合良好。
電泳試驗(yàn)操作平臺(tái)如圖2所示。
2)電泳槽模型,如圖3所示。
包括電泳槽幾何尺寸、電極截面形狀、電極尺寸、電極安裝位置及數(shù)量。
3)工藝參數(shù)。
主要包括:電泳有效時(shí)間、車身輸送軌跡、電泳電壓程式等。
4)網(wǎng)格劃分及邊界條件設(shè)置。
對(duì)整車模型自動(dòng)劃分網(wǎng)格,設(shè)置邊界條件,搭建有限元模型。
5)提交計(jì)算。
先進(jìn)行整車宏觀運(yùn)算,然后在宏觀計(jì)算結(jié)果基礎(chǔ)上截取關(guān)注區(qū)域進(jìn)行局部精算。
6)后處理。
將計(jì)算結(jié)果導(dǎo)入XPlorer軟件中,進(jìn)行可視化處理,獲得車身表面電泳膜厚分布云圖,拾取關(guān)鍵點(diǎn)獲得電泳膜厚精確數(shù)值。
2.2 車身電泳結(jié)構(gòu)
優(yōu)化流程車身結(jié)構(gòu)設(shè)計(jì)是一個(gè)多次迭代開(kāi)發(fā)的過(guò)程,常常伴隨多次結(jié)構(gòu)更改及優(yōu)化才能鎖定最終的數(shù)模數(shù)據(jù)。對(duì)車身進(jìn)行防腐性能開(kāi)發(fā),進(jìn)行電泳結(jié)構(gòu)優(yōu)化時(shí),必須兼顧車身強(qiáng)度、剛度等其他性能要求,將電泳同步分析融入車身開(kāi)發(fā)流程體系當(dāng)中,圖4為車身開(kāi)發(fā)過(guò)程中電泳結(jié)構(gòu)優(yōu)化流程。
電泳同步工程分析的合理介入,在設(shè)計(jì)階段就能對(duì)方案進(jìn)行可行性評(píng)估,減少了實(shí)車驗(yàn)證的次數(shù),加快了車身開(kāi)發(fā)迭代的速度,極大節(jié)約成本和縮短驗(yàn)證周期,同時(shí)提升了產(chǎn)品質(zhì)量。
3 某車型大梁電泳涂層驗(yàn)證及優(yōu)化
實(shí)例3.1 某車型大梁電泳仿真實(shí)例分析
大梁內(nèi)腔結(jié)構(gòu)復(fù)雜,鈑金間隙小,電泳液流動(dòng)不暢,局部腔體電泳液甚至無(wú)法進(jìn)入,或腔體形成電磁屏蔽,電場(chǎng)強(qiáng)度很弱,導(dǎo)致內(nèi)表面電泳漆膜厚度薄。再加上大梁位于車身底部,工作環(huán)境潮濕,容易受到泥水侵蝕。薄弱的電泳涂層無(wú)法抵御腐蝕的發(fā)生,使大梁內(nèi)腔成為腐蝕的高發(fā)區(qū)。圖5為某車型大梁,實(shí)車觀測(cè)生銹主要發(fā)生在大梁中段。
在整車宏觀計(jì)算的基礎(chǔ)上截取大梁區(qū)域進(jìn)行電泳仿真精算,仿真結(jié)果如圖6所示。
從分析結(jié)果看,大梁中段加強(qiáng)板下表面電泳漆膜厚度為0.01~3.86μm,電泳涂層未達(dá)到膜厚要求,不足以抵御腐蝕的發(fā)生。仿真結(jié)果預(yù)示生銹區(qū)域與實(shí)車生銹觀測(cè)結(jié)果吻合一致,說(shuō)明了電泳仿真模型的正確性。
3.2 某車型大梁電泳結(jié)構(gòu)優(yōu)化電泳仿真結(jié)果為設(shè)計(jì)人員指明了結(jié)構(gòu)缺陷,明確了結(jié)構(gòu)更改的區(qū)域范圍。對(duì)仿真結(jié)果進(jìn)行進(jìn)一步工程分析可發(fā)現(xiàn):存在問(wèn)題區(qū)域電場(chǎng)強(qiáng)度較弱,不足以保證充分的涂料電沉積作用;電泳工藝孔距離過(guò)大,內(nèi)腔電泳液流動(dòng)不充分;電泳時(shí)排氣受阻,易產(chǎn)生氣泡。上述因素導(dǎo)致了電泳上漆困難。
為此,提出針對(duì)性的更改措施,對(duì)結(jié)構(gòu)進(jìn)行優(yōu)化:加強(qiáng)板側(cè)面增加筋條,保證與大梁側(cè)面離空5mm,形成5x10mm通道,同時(shí)增加一φ20mm電泳孔,確保電泳過(guò)程中液體流動(dòng)通暢;在加強(qiáng)板底部增加5個(gè)φ16mm排氣孔,消除氣泡的影響,同時(shí)有利于消除電磁屏蔽,保證電泳充分。優(yōu)化后大梁加強(qiáng)板結(jié)構(gòu)如圖7所示。
泳膜厚為3.51~11.8μm,相比原結(jié)構(gòu)膜厚有所提升,但仍存在小塊面積漆膜厚度偏薄,未能滿足防腐要求。
對(duì)結(jié)構(gòu)進(jìn)行深入分析發(fā)現(xiàn),雖然大梁加強(qiáng)板增加了電泳工藝孔,但大梁底部未開(kāi)孔仍形成封閉結(jié)構(gòu),因此第二次結(jié)構(gòu)優(yōu)化在大梁底部增加3個(gè)φ16進(jìn)液孔,大梁側(cè)面增加2個(gè)φ16錯(cuò)位孔,保證電泳液順暢進(jìn)出大梁內(nèi)腔,如圖9所示。
第二次優(yōu)化后仿真結(jié)果如圖10所示。大梁加強(qiáng)板電泳漆膜厚度為8.93~14.44μm,漆膜厚度到達(dá)了防腐目標(biāo)要求。
優(yōu)化后結(jié)構(gòu)經(jīng)評(píng)估同時(shí)滿足車身強(qiáng)度、剛度等其他性能要求。數(shù)模鎖定后,進(jìn)行實(shí)車試制驗(yàn)證,在加強(qiáng)板上選取10個(gè)測(cè)量點(diǎn),使用漆膜測(cè)厚儀測(cè)量膜厚,仿真結(jié)果與實(shí)測(cè)結(jié)果如圖11所示,數(shù)據(jù)吻合性較好。
經(jīng)過(guò)工程分析,提出優(yōu)化方案,先經(jīng)仿真驗(yàn)證,最后實(shí)車驗(yàn)證,漆膜厚度達(dá)到設(shè)計(jì)要求。說(shuō)明改進(jìn)措施有效,可以實(shí)施,確保大梁內(nèi)腔區(qū)域防腐蝕性能良好,提高了使用壽命。
4 總結(jié)
本文主要介紹了在設(shè)計(jì)階段引入電泳仿真技術(shù)進(jìn)行同步分析的一種新的電泳涂層驗(yàn)證手段。實(shí)踐證明這種手段是卓有成效的。利用電泳仿真同步分析技術(shù),能在設(shè)計(jì)階段就暴露出電泳結(jié)構(gòu)設(shè)計(jì)缺陷,為結(jié)構(gòu)優(yōu)化指明方向;通過(guò)電泳仿真手段對(duì)結(jié)構(gòu)更改的可行性進(jìn)行驗(yàn)證,能夠減少傳統(tǒng)模式“試制-割車”次數(shù),從而減少人力、物力耗費(fèi),節(jié)約開(kāi)發(fā)成本;同時(shí)能夠縮短驗(yàn)證的周期,加快產(chǎn)品開(kāi)發(fā)迭代速度,并能保證產(chǎn)品的質(zhì)量,為企業(yè)贏得競(jìng)爭(zhēng)力。
更多關(guān)于材料方面、材料腐蝕控制、材料科普等方面的國(guó)內(nèi)外最新動(dòng)態(tài),我們網(wǎng)站會(huì)不斷更新。希望大家一直關(guān)注中國(guó)腐蝕與防護(hù)網(wǎng)http://www.ecorr.org
責(zé)任編輯:王元
《中國(guó)腐蝕與防護(hù)網(wǎng)電子期刊》征訂啟事
投稿聯(lián)系:編輯部
電話:010-62313558-806
中國(guó)腐蝕與防護(hù)網(wǎng)官方 QQ群:140808414
免責(zé)聲明:本網(wǎng)站所轉(zhuǎn)載的文字、圖片與視頻資料版權(quán)歸原創(chuàng)作者所有,如果涉及侵權(quán),請(qǐng)第一時(shí)間聯(lián)系本網(wǎng)刪除。
-
標(biāo)簽: 防腐蝕, 電泳結(jié)構(gòu), 流程方法, 電泳仿真, 同步分析
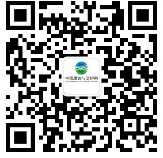
官方微信
《中國(guó)腐蝕與防護(hù)網(wǎng)電子期刊》征訂啟事
- 投稿聯(lián)系:編輯部
- 電話:010-62316606-806
- 郵箱:fsfhzy666@163.com
- 中國(guó)腐蝕與防護(hù)網(wǎng)官方QQ群:140808414