風能以其環保、廉價以及制造技術成熟度較高等優點,被譽為可再生能源中最具潛力的能源,已在世界各國得到大力開發應用。作為風電機組的關鍵部件,風電葉片的造價占整個風電機組的20% 以上,其安全、耐用性是整個機組安全經濟運行的保障。
隨著風電制造與運行技術的成熟,風電機組功率不斷增大,相應葉片尺寸不斷增大,由于葉片的維護與修復均在高空進行,一旦葉片質量出現問題,將會產生巨大的修復或更換費用,還會影響機組的穩定性。因此,在葉片制造成型后或安裝前檢測其是否存在缺陷是十分必要的。目前葉片出廠前的檢測方法一般有目視法、敲擊法、疲勞測試、雷擊測試、靜力學測試等常規的物理檢測方法,并不能精確地檢測出其近表面或深層缺陷。風電葉片大都采用玻璃鋼或碳纖維材質,采用真空灌注工藝(VARIM) 制成,受制造工藝以及隨機因素的影響,葉片內部難免會出現氣泡、夾雜、裂紋、分層、脫粘等結構缺陷,這些缺陷在葉片運行中反復遭受動/靜載荷、疲勞、環境因素的影響,將會導致缺陷的積累及擴展,最終使葉片失穩破壞。
筆者主要對風電葉片在制造、運輸、運行中常見的缺陷進行了分析,并介紹了超聲波無損檢測、紅外熱成像技術、射線成像技術以及磁檢測技術四種靜態無損檢測方法在風電葉片缺陷檢測中的應用。
1、風電葉片結構及其常見缺陷
1.1風電葉片的結構
風力發電機葉片一般為復合材料蒙皮與主梁構成的中空薄壁結構,由葉根、外殼和主梁三部分組成,根部一般為金屬板卷筒結構,外殼及主梁采用玻璃鋼或碳纖維等具有比強度高、比模量高、輕質、耐腐蝕等性能的復合材料,其在整個風電葉片中的質量一般占到90% 以上。葉片制造過程中一般先在各專用模具上分別成型葉片的上下外殼、抗剪切腹板,然后再將上下外殼和主梁粘接形成一體。圖1 為風電葉片截面圖。
1.2風電葉片常見缺陷
風力發電機葉片常見缺陷的來源可分為三類:制造過程、運輸及安裝過程、運行過程。
(1) 制造過程。
據統計,近50% 風電葉片故障來自于制造過程。由于葉片尺寸龐大以及制造工藝的局限性,在葉片成型以及合模粘結過程中經常會出現缺膠、多膠、分層、孔隙、纖維斷裂、夾雜等情況。缺膠將會造成蒙皮與蒙皮或加強筋間粘結不牢靠,達不到運行所需強度。多膠則會影響固化,產生微裂紋,除此之外還會使葉片質量不平衡,導致運行失穩。分層是指由于樹脂用量不足、真空泄壓以及二次成型等造成的纖維層合板間分層、芯材與纖維層合板間分層的現象,分層缺陷將使材料的壓縮強度和剛度降低,加之運行受到交變載荷作用,會使其擴展、傳播,到達一定程度后將造成葉片的斷裂。孔隙主要包括纖維層內的空隙、纖維層與層間的空隙。孔隙的存在將會大大降低材料的剪切、彎曲、拉伸與壓縮等力學性能強度,其形成原因主要有樹脂真空灌注過程當中引入氣泡、樹脂與復合材料纖維之間浸漬不良或葉片制造過程中氣泡不完全排出等工藝缺陷。夾雜是指在葉片制造過程中掉落或混入的非結構材料物質,多發生在纖維鋪設、樹脂真空灌注等工藝過程。有關實驗研究表明,復合材料夾雜會大大降低材料的斷裂韌性、剪切強度等力學性能。
(2) 運輸及安裝過程。
由于葉片尺寸龐大,在吊裝、長途運輸過程中不免會與其它物體碰撞、刮擦,可能會在葉片內部形成嚴重損傷,如分層或粘接處微裂開以及葉片表面微裂紋,這些缺陷從表面很難被發現。若不能及時修復,在葉片運行中受到周期載荷的作用會使缺陷得到擴展、積累,嚴重影響葉片的使用壽命以及運行安全。
(3) 運行過程。
一般葉片的設計壽命為20 a,需要經歷1×108 次以上的疲勞交變,如果葉片中存在微裂紋、氣泡等微小缺陷,這些缺陷將在交變載荷的作用下擴展為疲勞損傷,如出現分層、粘接區域脫膠開裂、葉片斷裂等。除此之外,葉片暴露在大氣環境中運行,還要遭受酸、堿、鹽、濕氣、雨水、紫外線、風沙等的侵蝕,表面不可避免會造成沙眼、鼓包、膠衣損壞等缺陷。若不及時發現修復,葉片損傷將進一步積累擴展,使得葉片前緣磨損嚴重、后緣開裂、防雷能力下降、氣動特性下降、葉片質量不平衡而失穩等一系列故障,大大減少了葉片運行使用壽命。
2 風電葉片全尺寸檢測方法
2.1超聲波檢測技術
超聲波檢測法是無損檢測方法中發展最為成熟的一種,其主要是利用聲波在不同材質中傳播特性的差異對構件中缺陷進行定量識別,進而根據本體材料特征以及實際探傷經驗確定缺陷類別。針對風電葉片結構尺寸特征,可用于風電葉片缺陷的超聲波檢測方法有:脈沖回波法、空氣耦合超聲波檢測法以及激光超聲法。
脈沖回波法是通過分析進入材料內部聲波的反射回波特征來定性、定量分析缺陷,其檢測靈敏度高、耦合方式簡單(風電葉片的檢測過程中一般采用噴水耦合),是風電葉片檢測最常用的一種無損檢測方法,但需要不斷移動探頭,且檢測效率較低、覆蓋面積小,其原理如圖2 所示。近年來,國內外相關機構進行了大量試驗。王曉寧等 利用超聲相控陣設備采用脈沖回波法成功對風電葉片蒙皮內部的分層、缺膠、富膠、干絲等缺陷進行了識別,且檢測缺陷尺寸與真實值相差較小,結果理想。安靜等應用脈沖回波法對風電葉片梁冒與腹板粘接處進行了掃查,并接收到了粘接區域的回波信息,證明了脈沖回波法對厚度較大梁冒粘接區域缺陷檢測的可行性。Li Suwei 等利用人工制造缺陷試件,分別對風電葉片內典型缺陷聲強反射系數進行了計算分析與對比,證明了缺陷聲強反射反射系數可作為某一缺陷定性分析的唯一依據,并提出建立風電葉片典型缺陷的物理模型樣本,在實際檢測中與實際缺陷的聲強反射系數進行對比,可對缺陷類型進行精確定性分析。
針對設備檢測效率低、覆蓋面積有限等缺點,目前,各大葉片研究機構及檢測設備公司都在積極研制適用于風電葉片檢測的設備,并取得了較大突破。Force Technology 公司開發的專用于風電葉片檢測的移動式超聲掃查儀AMS–46 與AMS–57,可快速對整個葉片進行檢測。奧林巴斯公司開發的專用于葉片檢測的設備組件:OmniScan MX2 超聲相控陣探傷儀、風電葉片檢測專用探頭和專用于曲面復合材料的GLIDER( 滑動) 掃查器,可大面積對風電葉片進行缺陷的掃描。除此之外,奧林巴斯公司還開發出了一款專用于復合材料構件檢測的相控陣輪式探頭Roller FORM,輪胎由獨特材料制成,可以確保完成與水浸檢測相仿的高質量超聲檢測,檢測時只需稍微用力就可獲得優質的耦合效果,獲得清晰的圖像。
空氣耦合式超聲波檢測是以空氣作為耦合介質的一種非接觸無損檢測方法。由于空氣與被檢復合材料聲阻抗的巨大差異、檢測適用波的頻率范圍較低以及波在空氣中的衰減極大等原因,在風電葉片的檢測中除了需要采用特殊機制( 高靈敏度探頭與合適的前置放大器相結合,將接收信號增幅) 來改善外,一般采用空氣耦合式超聲波導波法,其原理如圖3 所示。國內外相關研究機構已對人工制造復合材料中的分層、缺膠等多種缺陷進行了識別。結果表明,空氣耦合式超聲波導波法可很好地對風電葉片中的多種缺陷進行定性識別,但對于微小的內部缺陷如微裂紋很難檢測。E. Jasiuniene 等 利用人工制造缺陷的風電葉片樣本試件,分別應用空氣耦合式超聲波導波法、超聲波脈沖回波法、射線檢測法三種檢測方法對其進行了檢測并將結果將對比,驗證了空氣耦合式超聲波導波法在風電葉片缺陷檢測中的可行性。常俊杰等 利用同側檢測法對存在沖擊損傷的玻璃纖維復合材料進行了成像檢測,證實了空氣耦合式超聲波可廣泛應用于復合材料損傷的檢查。李立兵 等研制出一套基于MATLAB 空氣耦合超聲波檢測系統,經試驗驗證該系統可行可靠,并能將系統檢測過程進行分解,還可對MATLAB 系統軟件進行二次開發,非常適用于教學和科研。
激光超聲無損檢測技術是利用高能量激光脈沖與被檢構件表面的瞬時熱作用,從而在構件內部產生超聲波,通過超聲波的傳播及衰減特征來表征缺陷。其具有非接觸、遠距離、頻帶寬、適應性強以及靈敏度高等優點,可在惡劣環境下對各種復雜構件的缺陷快速進行定性與定量檢測,激光超聲檢測系統如圖4 所示。近年來,國內外相關研究機構對風電葉片復合材料試件進行了一系列的試驗,證明了激光超聲無損檢測技術可對大型風電葉片內的多種缺陷進行精確識別。劉松平等 利用激光超聲技術對碳纖維復合材料中常見缺陷的信號特征與識別評估方法進行了試驗分析與研究,結果表明,利用縱波可有效識別復合材料構件內部的多種缺陷。周正干等 利用激光超聲C 型成像成功的檢測出了碳纖維增強環氧樹脂基復合材料層壓板中的夾雜、分層缺陷等人工制造缺陷。J. Hyomi利用移動激光超聲系統對750 kW 風電葉片的一部分進行了檢測,檢測結果表明,激光超聲系統可快速地對風電葉片進行全尺寸掃描,并能夠對葉片內部的多種缺陷進行定性與定量的識別。
2.2紅外熱成像技術
紅外熱成像技術是近年來新興的一種無損檢測方法,該技術是利用材料本身與缺陷對熱流傳導的時間差異將被檢構件結構特征轉化為可見圖像,通過熱成像圖可直觀地判斷構件內部有無缺陷以及缺陷的詳細信息。對于檢測風電葉片這類與所處環境基本沒有溫度差的構件,只能采用主動激勵方式進行檢測。根據對被檢構件熱激勵方式的不同可分為脈沖激勵、紅外激勵、激光激勵、熱風激勵等幾種方式,除激勵源不同外,其成像原理均相同,如圖5 所示。肖勁松等通過數值模擬,以脈沖激勵成像方式檢測葉片內部氣孔為例,得到了葉片內部及表面任意時刻溫度場及熱流場,進而得出了材料內部缺陷越大、埋深越淺,越容易檢出的理論檢測依據。岳大皓等利用脈沖激勵紅外成像技術對風電葉片中合模膠粘狀態、沙眼、白斑、纖維布褶皺等缺陷進行了檢測試驗,結果表明紅外熱成像技術可快速、直觀地對上述缺陷進行識別。孟梨雨等通過人工制造缺陷,使用紅外熱成像檢測系統,對不同厚度蒙皮與腹板間的缺膠脫粘進行了試驗,結果表明,蒙皮厚度越小,粘膠寬深比越大,檢測效果越好。P. Meinlschmidt 等成功利用脈沖主動激勵熱成像技術對三個包含分層、氣泡、缺膠、纖維布浸漬不良等缺陷的玻璃纖維試件進了缺陷識別。Tao Liang 等 利用渦流脈沖激勵熱成像法對在4 J 能量沖擊下的碳纖維試件進行檢測,對生成的圖像利用小波變換與主成分分析法進行冗余信息分離、重建圖像,結果表明,此方法可提高缺陷檢測的分辨率,使更小的缺陷得以識別。
2.3射線成像技術
射線檢測技術是利用射線在不同材質中衰減程度差異,從而改變透射射線強度,記錄在膠片或在探測器上得以體現的一種直觀檢測方法,對構件材質適用范圍較廣,可對復合材料構件進行缺陷檢測。由于風電葉片尺寸大、厚度大且為中空結構等特點,常規的膠片形式射線檢測并不能很好地用于風電葉片的檢測。隨著計算機以及信號處理/轉換技術的發展,射線實時成像技術、康普頓背散射技術等射線檢測技術可很好地用于風電葉片的檢測。
射線實時成像技術原理是以專用探測器代替傳統膠片對透射過材料的射線進行吸收,并轉化( 光電轉換) 為圖像信息,進而經A/D 轉換( 模/數轉換) 將圖像信息輸入計算機,經處理后顯示缺陷的基本信息。受限于風電葉片的結構尺寸,可將射線實時成像技術應用于風電葉片制造合模前的大面積檢測。有關研究表明射線成像技術能夠快速、有效地檢測復合材料構件中的氣孔、夾雜、纖維布褶皺、樹脂聚集等體積型缺陷,對于內部裂紋、分層等平行于表面的缺陷,可將射線源傾斜一定角度對風電葉片的半模進行透照。康普頓背散射成像技術是一種新型的射線成像技術,其原理是利用射線與物質相互作用產生的非相干散射效應,入射射線將部分能量傳遞給被檢構件的自由電子,自身改變方向成為散射光子,經專用探測器收集處理生成圖像。其具有非接觸、單面照射、不受構件尺寸結構限制以及對復合材料等低密度材料有較高的對比度等優點,使其能夠對風電葉片等大型復合材料構件進行檢測。國外已在很多領域得到了應用,如飛機機翼、復雜精密儀器或零件等復合材料構件的檢測,實踐結果表明,康普頓背散射成像技術可對復合材料構件中的氣孔、夾雜、缺/富膠等常見缺陷進行有效識別。
2.4磁檢測技術
磁檢測技術是基于穩定地磁場下的一種檢測方法,其不需要激勵源,主要是利用缺陷區域與材料本體間地磁感應強度的差異來進行缺陷特征分析,若材料本身連續均勻且無缺陷存在,磁感應線將均勻穿過材料,反之則會影響磁感應線的疏密程度,引起磁場強度的變化。對于纖維復合材料這類非鐵磁性材料來說,其本身具有弱順磁特性,磁導率大于1,若基體中有缺陷存在,則會使穩定地磁場強度發生微弱變化,通過高精度磁敏傳感器可對其微弱變化進行捕捉,通過分析捕捉到的微弱磁變化信號來進行缺陷識別,故磁檢測法可用于纖維復合材料風電葉片的缺陷檢測,檢測原理如圖6所示。張欣瑩等 提出將磁法檢測應用于纖維復合材料的檢測當中并利用自主研發的磁檢測系統分別對有人工制造缺陷的碳纖維材料、玻璃纖維材料試件進行了試驗,將采集到的磁場信號進行了分析與處理得到了試件缺陷檢測二維圖像,并與超聲檢測進行了對比,試驗表明,磁檢測技術可對纖維復合材料中的分層、氣泡、孔隙、夾雜等缺陷進行定性與定位識別,進一步驗證了磁檢測技術在非鐵磁性復合材料缺陷檢測中的可行性。
3 結語
受制造工藝、自身結構以及運行環境等因素的影響,風電葉片在制造、安裝、運輸及運行難免產生缺陷,若不及時發現修復,加之交變載荷以及環境因素的影響,將使缺陷積累擴展,從而造成一系列事故。所以,在葉片成型后和安裝前對整體進行無損檢測可在較大程度上降低風電機組的事故率。可用于風電葉片無損檢測方法有很多,但大都需要復雜的操作以及嚴格的檢測環境,且檢測速度緩慢。近年來隨著國內外各大研究機構的努力,超聲波無損檢測技術、紅外熱成像技術、射線成像技術以及磁檢測技術在風電葉片檢測中取得了重大突破,上述幾種無損檢測技術可快速對葉片進行靜態全尺寸檢測,從而保障風電機組安全經濟地運行。
更多關于材料方面、材料腐蝕控制、材料科普等等方面的國內外最新動態,我們網站會不斷更新。希望大家一直關注中國腐蝕與防護網http://www.ecorr.org 責任編輯:王元 《中國腐蝕與防護網電子期刊》征訂啟事
投稿聯系:編輯部
電話:010-62313558-806
郵箱:ecorr_org@163.com
中國腐蝕與防護網官方 QQ群:140808414
免責聲明:本網站所轉載的文字、圖片與視頻資料版權歸原創作者所有,如果涉及侵權,請第一時間聯系本網刪除。
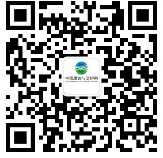
官方微信
《中國腐蝕與防護網電子期刊》征訂啟事
- 投稿聯系:編輯部
- 電話:010-62316606-806
- 郵箱:fsfhzy666@163.com
- 中國腐蝕與防護網官方QQ群:140808414