F-35 是由主承包商洛•馬公司與主合作伙伴諾格公司及BAE系統公司合作開發的。首架F-35 已在2006 年首飛。復合材料一直是其制造工作的重點。
F-35 的制造難點
F-35 的制造難點是要符合預算,即對飛機的每一個零部件必須精心計算以保證成本的優化,特別是碳纖維復合材料構件的制造,因為這種材料的結構占飛機重量的35%,飛機大部分外表面均由此種材料制成。
而F-35 的機身、機翼、尾翼分別由不同國家的供應商制造,最后在洛•馬公司總裝,因此F-35 制造的最大難點是飛機復合材料蒙皮厚度的控制。F-35 各階段的生產因供應商、零部件復雜程度以及其要求各不相同。如ATK公司生產許多機翼蒙皮桁條時用的是自動纖維鋪放工藝,而洛•馬在制造前機身段蒙皮時用的是手工鋪層。
控制F-35 復合材料蒙皮厚度的方法有2 種:一是根據精細的計算對復合材料的鋪層數進行加減;另一種方法是對零件進行切削加工。洛•馬公司及其合作伙伴采用了切削加工和模塑后增加鋪層2種方法來確保蒙皮厚度達標。在洛•馬公司,前機身蒙皮是在Invar35鋼模具上用手工鋪層并在熱壓罐中進行固化的。固化成層合板的鋪層隨后用切削加工法去除余量從而控制蒙皮的厚度。在ATK公司,機翼蒙皮是用纖維鋪放法進行鋪層并固化的,然后用洛•馬公司的制造技術及生產工程人員開發的一種方法精確測量蒙皮的厚度。必要時,增加鋪層,然后對整個結構進行第二次固化,該法稱作固化層合板補償法(CLC)。這樣做的目的是控制厚度,是為成本達標采用的一種策略。
大型切削中心
在洛•馬公司沃斯堡工廠的中心,就有一個體現這種策略的關鍵部門,這就是F-35 的切削及鉆孔中心。它是由德國DST公司建造的,負責F-35 前機身蒙皮、機翼蒙皮以及其他復合材料工件的切削及鉆削。
在DST 切削中心進行的大部分工作,采用的刀具是由AMAMCO工具公司提供的涂覆金剛石的碳化物刀具。AMAMCO 公司為中心設計了DST仿形銑刀具。
卡爾蔡斯IMI公司的測量系統是世界上最大的高精度測量系統,主要用于蒙皮尺寸、邊緣以及孔的精度檢驗。復合材料構件經切削加工后,用該測量系統進行檢測。從2008 年6月開工以來,F-35 的機翼蒙皮采用了MMZ-B Plus龍門式坐標測量機的5m×16m×2.5m 測量包線,也用于風洞模型1:1 的組件以及其他飛機機體零件的測量。
洛•馬公司也用自己開發的無損檢測激光超聲檢驗系統來檢驗復合材料結構的孔洞及其他內部缺陷。將該系統400MHz的激光器對準復合材料結構時,從該激光器發出的信號返回到一傳感器來顯示蒙皮中的孔洞、裂紋、分層等缺陷。激光超聲系統的運轉速度為0.56m2/min,比傳統的噴水超聲系統快10倍,因此是F-35 制造工藝不可缺少的一部分。
鉆孔
在F-35上評估了3種類型的鉆孔,即手工鉆孔、電動鉆孔以及自動化(數控)鉆孔。洛•馬公司采用的大部分是自動化鉆孔。在大多數情況下,F-35 的鉆孔法為垛式鉆孔,即將復合材料蒙皮放在支承結構上,穿過蒙皮和支承結構進行鉆孔。用單一的鉆頭進行鉆孔、鉸孔以及進一步埋頭鉚接而成。F-35 鉆孔中引人注目的是前機身,機身每一邊用自動化龍門式鉆頭鉆出750個孔。
機翼蒙皮是與支承結構堆迭起來,用辛辛那提公司的龍門式系統進行鉆孔的。隨后F-35 的團隊用Virtek Vision 國際公司生產的激光投影系統將緊固件號碼投影到蒙皮表面上, 而無需查找復雜的圖紙即可進行緊固件的安放。當不能自動化鉆孔時,可用樣板進行人工鉆孔。采用投影系統可以大大減少工時和工作量。
刀具更換門檻值的跟蹤
洛•馬公司用的大部分鉆頭采用的馬達為氣動和液壓式。刀具的尖銳角決定鉆削速度的大小。隨著刀具變鈍,切削時間加長。進給系統可測定鉆孔時間的長短。當達到門檻值時,指示燈立即指示工人更換刀具。洛•馬公司正在尋求合適的直徑公差以及特殊的工藝過程控制,從而消滅不合格孔的出現。F-35 鉆孔質量Cpk(過程能力指數)的目標是達到1.3,而目前為1.0,正在改進中。
所有的修邊、切削系統以及鉆孔工藝正在進行效率、成本、質量等因素的評估以便確定整個F-35 復合材料生產的最佳工藝。洛•馬公司已在沃斯堡建立一個鉆削/ 切削卓越中心繼續對刀具及工藝進行開發。隨著F-35 壽命的加長,洛•馬公司及其供應商還有幾十年對復合材料的優化和管理時間。
免責聲明:本網站所轉載的文字、圖片與視頻資料版權歸原創作者所有,如果涉及侵權,請第一時間聯系本網刪除。
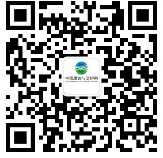
官方微信
《腐蝕與防護網電子期刊》征訂啟事
- 投稿聯系:編輯部
- 電話:010-62316606-806
- 郵箱:fsfhzy666@163.com
- 腐蝕與防護網官方QQ群:140808414