劉敏1,朱華*, 1,汪的華1,甘復(fù)興1, 2
1武漢大學(xué)資源與環(huán)境科學(xué)學(xué)院環(huán)境工程系,武漢,中國(guó),430072
2中國(guó)科學(xué)院金屬腐蝕與防護(hù)國(guó)家重點(diǎn)實(shí)驗(yàn)室,沈陽(yáng),中國(guó),110015
Email: zhuhua333@126.com
作者簡(jiǎn)介:
劉敏,女,1986年9月出生于湖北省孝感市,成長(zhǎng)于湖北省黃石市。2004年考入武漢大學(xué)資源與環(huán)境科學(xué)學(xué)院就讀環(huán)境工程專(zhuān)業(yè),由于成績(jī)優(yōu)異,2008年9月保送武漢大學(xué)資源與環(huán)境科學(xué)學(xué)院,材料與環(huán)境電化學(xué)實(shí)驗(yàn)室攻讀碩士學(xué)位,因科研能力突出,于2009年10月由導(dǎo)師推薦而提前攻讀博士學(xué)位,現(xiàn)為博士二年級(jí)研究生,致力于水性涂料成膜樹(shù)脂改性研發(fā)以及相關(guān)性能方面的研究,在該領(lǐng)域已有四年左右的研發(fā)經(jīng)驗(yàn)。除了在高分子樹(shù)脂合成方面有著豐富的實(shí)際經(jīng)驗(yàn)外,在涂膜性能的電化學(xué)測(cè)試及分析方面、尤其是腐蝕電化學(xué)測(cè)試技術(shù)方面,同樣具備扎實(shí)的知識(shí)基礎(chǔ)與熟練的操作技能。
在武漢大學(xué)多年的求學(xué)生涯中,連續(xù)六年獲得校級(jí)優(yōu)秀學(xué)生獎(jiǎng)學(xué)金,任班級(jí)班長(zhǎng)職務(wù)、參與學(xué)院辯論隊(duì)等社團(tuán)活動(dòng),均有出色表現(xiàn)。多次參加國(guó)際性及全國(guó)性學(xué)術(shù)會(huì)議,曾獲得2009年全國(guó)金屬腐蝕大會(huì)青年學(xué)者講評(píng)會(huì)二等獎(jiǎng)、2010年全國(guó)腐蝕電化學(xué)及測(cè)試方法學(xué)術(shù)年會(huì)優(yōu)秀論文獎(jiǎng)第三名、2011年中國(guó)腐蝕與防護(hù)學(xué)會(huì)優(yōu)秀論文獎(jiǎng)一等獎(jiǎng)。目前研究項(xiàng)目仍在進(jìn)行中,該項(xiàng)目受?chē)?guó)家自然科學(xué)基金資助,已發(fā)表中文核心期刊文章2篇、EI檢索文章1篇,擁有國(guó)家專(zhuān)利1項(xiàng),并與江蘇相關(guān)涂料企業(yè)進(jìn)行了一系列產(chǎn)學(xué)研技術(shù)開(kāi)發(fā)合作項(xiàng)目。
摘 要:采用二步酯化工藝,以雙酚A環(huán)氧樹(shù)脂及不同品種的丙烯酸酯類(lèi)單體為原料,制備水性丙烯酸環(huán)氧酯樹(shù)脂。該工藝將聚合反應(yīng)與環(huán)氧基開(kāi)環(huán)酯化反應(yīng)分步實(shí)施,從而實(shí)現(xiàn)對(duì)復(fù)合改性樹(shù)脂的分子量與羧基含量的控制。利用酸值及環(huán)氧值滴定結(jié)果確定一步酯化反應(yīng)進(jìn)行的程度;采用凝膠滲透色譜證明改性樹(shù)脂的接枝成功;此外,對(duì)不同分子量與羧基含量的改性樹(shù)脂水性涂料的水溶性、交聯(lián)度及吸水率進(jìn)行了考察;同時(shí),應(yīng)用鹽霧腐蝕測(cè)試及交流阻抗測(cè)試技術(shù)檢測(cè)了其涂膜的耐蝕性能。結(jié)果表明,通過(guò)該工藝制得的環(huán)氧丙烯酸樹(shù)脂水溶性良好、交聯(lián)度高、耐水耐蝕性能佳。
關(guān)鍵詞:水性環(huán)氧丙烯酸;水性防腐涂料;交聯(lián)度;吸水率;二步酯化;分子量
1 引言
通常,成膜樹(shù)脂的水性化通過(guò)在體系中引入極性基團(tuán)來(lái)實(shí)現(xiàn)。然而,高分子樹(shù)脂實(shí)現(xiàn)水性化后,往往會(huì)導(dǎo)致一些性能上的不足,如固化涂層附著力、耐水耐蝕性等相關(guān)性能的下降。因此,如何在提高樹(shù)脂水溶性的同時(shí),保證固化涂層的耐蝕性,成為了水性工業(yè)防腐涂料開(kāi)發(fā)的關(guān)鍵問(wèn)題[1-2]。近年來(lái),許多研究者開(kāi)展了多種樹(shù)脂的復(fù)合研究,即采用接枝、酯化或聚合等化學(xué)反應(yīng)將兩種以上的樹(shù)脂進(jìn)行復(fù)合,取長(zhǎng)補(bǔ)短,以期進(jìn)一步提高水性成膜樹(shù)脂的綜合性能。
環(huán)氧樹(shù)脂與丙烯酸樹(shù)脂作為使用量大,互補(bǔ)性能強(qiáng)的兩類(lèi)樹(shù)脂,其復(fù)合技術(shù)被廣泛關(guān)注[3-6]。根據(jù)Matthews[7]等人的研究,通過(guò)酯化接枝,將聚合后的丙烯酸樹(shù)脂在叔胺的參與下與環(huán)氧樹(shù)脂反應(yīng),得到的環(huán)氧丙烯酸樹(shù)脂分子量更大,幾乎沒(méi)有游離的小分子,且該方法工藝簡(jiǎn)單,具有工業(yè)化前景。但是,若反應(yīng)條件控制不當(dāng),易導(dǎo)致形成三維網(wǎng)絡(luò)而出現(xiàn)凝膠化,限制了其工業(yè)推廣。而Ting、SpenCevrl[8-9]等研究者認(rèn)為控制聚合反應(yīng)條件,可以控制酯化反應(yīng)程度而避免凝膠。
因此,本文主要研究了能避免凝膠化,從而成功將聚丙烯酸酯與環(huán)氧樹(shù)脂進(jìn)行接枝,同時(shí)過(guò)程穩(wěn)定可控的二步酯化工藝的實(shí)現(xiàn),以及通過(guò)該工藝制備出來(lái)的不同分子量及羧基含量的丙烯酸酯改性環(huán)氧樹(shù)脂作為水性涂料成膜樹(shù)脂的相關(guān)性能。性能測(cè)試結(jié)果證實(shí)自制的環(huán)氧丙烯酸水性樹(shù)脂具備良好的耐水耐蝕性能。
2 實(shí)驗(yàn)部分
2.1 實(shí)驗(yàn)材料
雙酚A型環(huán)氧樹(shù)脂,湖南岳陽(yáng)化工廠;正辛酸,分析純;α-甲基丙烯酸(MAA),分析純;甲基丙烯酸甲酯(MMA),分析純;丙烯酸正丁酯(BA),分析純;N,N-二甲基乙醇胺,分析純;偶氮二異丁腈(AIBN),化學(xué)純,上海試四赫維化工有限公司;正十二硫醇,化學(xué)純,成都科龍化工;正丁醇,分析純;丙二醇甲醚,分析純;乙酸丁酯,分析純;乙酸乙酯,分析純;
2.2改性樹(shù)脂的合成
將摩爾比為1:1的雙酚A環(huán)氧樹(shù)脂E-20與正辛酸置于三頸燒瓶?jī)?nèi),加入同等質(zhì)量的正丁醇與丙二醇甲醚作為溶劑,及一定量的二甲基乙醇胺作為催化劑,通過(guò)恒溫磁力攪拌器控制溫度為105 ℃,攪拌速度為15 r/s,進(jìn)行酯化反應(yīng),體系酸值降到5mgKOH/g即為反應(yīng)終點(diǎn)。此外,將一定質(zhì)量比例的MAA、MMA、BA置于另一三頸燒瓶中,加入一定量的正丁醇、丙二醇甲醚、乙酸丁酯作為溶劑,及AIBN作為引發(fā)劑、正十二硫醇作為鏈轉(zhuǎn)移劑,采用恒流泵控制轉(zhuǎn)速在70 r/min將丙烯酸單體等滴加入內(nèi)置溶劑的三頸燒瓶反應(yīng)器里,反應(yīng)溫度為85 ℃,滴加時(shí)間為2.5 h,之后恒溫2 h。其后,將制成的環(huán)氧正辛酸酯與丙烯酸酯類(lèi)聚合產(chǎn)物以固含質(zhì)量比為3:7的比例置于三頸燒瓶反應(yīng)器內(nèi),以二甲基乙醇胺作為催化劑進(jìn)行第二步酯化反應(yīng),控制反應(yīng)溫度為105 ℃,反應(yīng)時(shí)間90min。最終生成的二步酯化反應(yīng)終產(chǎn)物為丙烯酸改性環(huán)氧樹(shù)脂,加入二甲基乙醇胺中和酸值后,添加二次水即制成白色乳液狀水性涂料。
2.3改性樹(shù)脂的性能測(cè)試
2.3.1 GPC測(cè)定改性樹(shù)脂數(shù)均分子量
采用凝膠滲透色譜(GPC: Gel Permeation Chromatography)測(cè)定樹(shù)脂的分子量分布,測(cè)定條件如下:采用Waters 2690D Separations Module Waters, 2410 Refractive Index Detector,溶劑:四氫呋喃,流速:0.3 mL/min,標(biāo)準(zhǔn)樣品:Polystyrene Standard,溫度:313 K,探測(cè)器:308 K。
2.3.2 樹(shù)脂涂膜的交聯(lián)度測(cè)試
將涂料涂覆固化后,置于索式抽提器中用2-丁酮洗滌、萃取約8 h,除去涂層中未交聯(lián)固化的小分子物質(zhì),抽提實(shí)驗(yàn)前后稱(chēng)量G1和G2,及涂覆基底物質(zhì)G,則涂層交聯(lián)度C(Cross-linking Degree)為:
2.3.3 樹(shù)脂涂膜的吸水率測(cè)試
按漆膜吸水率測(cè)定法HG2-1612-1985測(cè)定吸水率,其方法是漆膜烘干后常溫浸蒸餾水500 h,浸水前后分別稱(chēng)重G1和G2,其底板重G,吸水率W。
2.3.4 鹽霧腐蝕測(cè)試涂層耐蝕性
依照《色漆和清漆 耐中性鹽霧性能的測(cè)定》 GB/T 1771-2007/ISO 7253:1996測(cè)定涂層耐蝕性能。
3 二步酯化工藝制備改性樹(shù)脂
在實(shí)驗(yàn)中采用的是Matthew是報(bào)道過(guò)的方法,即先將丙烯酸類(lèi)單體進(jìn)行自由基聚合,得到含有多個(gè)羧基的丙烯酸酯聚合物,再將該聚合物與環(huán)氧樹(shù)脂進(jìn)行開(kāi)環(huán)酯化,將羧基引入環(huán)氧分子鏈實(shí)現(xiàn)水性化。但是,將丙烯酸單體聚合產(chǎn)物與環(huán)氧樹(shù)脂進(jìn)行酯化時(shí),同樣會(huì)發(fā)生凝膠,這是由于雙酚A環(huán)氧分子上含有兩個(gè)環(huán)氧端基,官能度為2,而丙烯酸聚酯中至少含有兩個(gè)以上的羧基,其官能度不小于2,則反應(yīng)過(guò)程中的活性位點(diǎn)過(guò)多,凝膠現(xiàn)象難以避免。
因此,本研究采用減少官能度的方法來(lái)避免酯化凝膠現(xiàn)象的出現(xiàn)。首先,利用正辛酸與環(huán)氧樹(shù)脂進(jìn)行酯化來(lái)封閉環(huán)氧分子上的一個(gè)環(huán)氧端基,此為第一步酯化反應(yīng);同時(shí),不同組成的丙烯酸類(lèi)單體進(jìn)行自由基聚合反應(yīng),調(diào)控其工藝條件,控制丙烯酸聚酯的分子量與羧基含量;最后,利用環(huán)氧正辛酸酯上殘留的另一個(gè)環(huán)氧端基與丙烯酸聚酯上的羧基進(jìn)行第二步酯化反應(yīng)。這樣,即使丙烯酸聚酯分子上有多個(gè)羧基,但是只有一個(gè)環(huán)氧基團(tuán)能與其中的一個(gè)羧基酯化,形成鏈狀結(jié)構(gòu),而不會(huì)環(huán)化凝膠。#p#副標(biāo)題#e#
3.1 二步酯化工藝實(shí)現(xiàn)的關(guān)鍵點(diǎn)
二步酯化工藝實(shí)現(xiàn)的關(guān)鍵點(diǎn)在于:在第一步酯化過(guò)程中,環(huán)氧樹(shù)脂必須保留近一半未開(kāi)環(huán)的環(huán)氧基,使之能在第二步酯化過(guò)程中與丙烯酸聚酯上的羧基發(fā)生環(huán)氧基開(kāi)環(huán)酯化反應(yīng),生成復(fù)合樹(shù)脂。若第一步酯化反應(yīng)時(shí)環(huán)氧基開(kāi)環(huán)過(guò)度,即環(huán)氧樹(shù)脂上的環(huán)氧基團(tuán)全部開(kāi)環(huán),則第二步酯化將無(wú)法進(jìn)行,不可能將丙烯酸聚合物酯化到環(huán)氧分子鏈上去。
圖1 第一步酯化反應(yīng)的環(huán)氧當(dāng)量與酸值監(jiān)測(cè)結(jié)果
因此,在進(jìn)行第一步酯化反應(yīng)時(shí),需要選擇合適的催化劑濃度,既要保證適當(dāng)?shù)姆磻?yīng)速率,又要保證適當(dāng)?shù)姆磻?yīng)程度。經(jīng)過(guò)對(duì)催化劑濃度、反應(yīng)時(shí)間等相關(guān)影響因素的探索[10]后,確定較合適的工藝條件。
圖1為以E-20為環(huán)氧單體,正辛酸為封端劑,二甲基乙醇胺為催化劑,濃度為反應(yīng)物總質(zhì)量的0.2%時(shí),反應(yīng)體系酸值和環(huán)氧值隨時(shí)間的變化。E-20的環(huán)氧當(dāng)量(簡(jiǎn)稱(chēng)EE)為539,若一酯反應(yīng)產(chǎn)物保留一半環(huán)氧基團(tuán),則反應(yīng)終點(diǎn)時(shí),體系EE增大一倍,即為1078。從圖中可以看出,當(dāng)EE值為1078時(shí),體系的酸值正好接近0,即可以認(rèn)為在環(huán)氧基團(tuán)開(kāi)環(huán)一半時(shí),正辛酸反應(yīng)完全。由此可知,在本實(shí)驗(yàn)確定的工藝條件下,經(jīng)過(guò)第一步酯化反應(yīng)后,生成的環(huán)氧正辛酸單酯產(chǎn)物上,有一半的環(huán)氧端基保持在未開(kāi)環(huán)狀態(tài),為第二步酯化反應(yīng)提供了充足的接枝位點(diǎn)。
3.2. 第二步酯化反應(yīng)的接枝成功
圖2 GPC測(cè)試結(jié)果 (a)改性環(huán)氧丙烯酸樹(shù)脂 (b)聚丙烯酸酯 (c) 環(huán)氧正辛酸單酯
圖2即為二步酯化過(guò)程的反應(yīng)物及產(chǎn)物的GPC譜。可以看出,經(jīng)過(guò)第二步酯化反應(yīng)后,酯化產(chǎn)物相較于兩種反應(yīng)物,其流出曲線明顯左移,即流出時(shí)間變短,表明產(chǎn)物分子量明顯增大。由于第二步酯化過(guò)程中,作為反應(yīng)物的環(huán)氧正辛酸單酯上一個(gè)環(huán)氧端基已被正辛酸封閉,而丙烯酸聚酯上的雙鍵也在自由基聚合過(guò)程中完全消失,故能進(jìn)行反應(yīng)的位點(diǎn),僅為另一環(huán)氧端基及丙烯酸聚酯上的羧基。因此,二酯產(chǎn)物分子量的增大表明在第二步酯化過(guò)程中,反應(yīng)物之間的酯化接枝得以按預(yù)期方式進(jìn)行。
4 改性樹(shù)脂性能研究
4.1 改性樹(shù)脂的水溶性
經(jīng)過(guò)二步酯化工藝成功地將丙烯酸聚酯引入到環(huán)氧樹(shù)脂上,制備的丙烯酸酯改性環(huán)氧樹(shù)脂具備良好的水溶性。將改性樹(shù)脂加堿中和、加水分散后形成的水性清漆中(固含量為40%),水的用量超過(guò)整個(gè)溶劑體系的68%,即100g 涂料中,有機(jī)溶劑用量低于20g(最低可達(dá)16.67g)。且該清漆存放8個(gè)月以上未出現(xiàn)分層,表現(xiàn)出良好的存放穩(wěn)定性。
4.2改性樹(shù)脂的耐水性
通過(guò)控制聚合反應(yīng)中單體的種類(lèi)與數(shù)量(本次研究主要是甲基丙烯酸(MAA)用量),可以調(diào)整丙烯酸聚酯中羧基的含量;通過(guò)控制聚合反應(yīng)中引發(fā)劑與鏈轉(zhuǎn)移劑用量,可以調(diào)整丙烯酸聚酯的分子量分布[11]。對(duì)所制備的不同分子量分布及羧基含量的改性樹(shù)脂水性清漆涂膜的交聯(lián)度與吸水率進(jìn)行了測(cè)定,結(jié)果如表1所示。
表1。改性樹(shù)脂交聯(lián)度與吸水率
樹(shù)脂種類(lèi) | 聚合反應(yīng)中MAA用量/% | 數(shù)均分子量(Mn) | 交聯(lián)度/% | 吸水率/‰ |
EA-1-13 | 13 | 6362 | 97.470 | 6.53 |
EA-2-13 | 13 | 3816 | 89.251 | 8.78 |
EA-3-13 | 13 | 3289 | 87.211 | 9.39 |
EA-2-20 | 20 | 3816 | 92.034 | 8.04 |
EA-1-20 | 20 | 6362 | 99.276 | 5.33 |
EA-2-27 | 27 | 3816 | 87.23 | 37.65 |
EA-2-27(s) | 27 | 3816 | 85.07 | 11.03 |
4.2.1 分子量對(duì)改性樹(shù)脂耐水性的影響
通過(guò)交聯(lián)固化成膜,涂層形成三維網(wǎng)狀結(jié)構(gòu),可以將樹(shù)脂上的極性基團(tuán)包裹或屏蔽在非極性分子鏈內(nèi),減少或阻斷膜內(nèi)輸水通道,從而提高涂膜耐水性。涂膜交聯(lián)度越高,其耐水性越好。
從表1中顯示的結(jié)果進(jìn)行比較可知,隨著改性樹(shù)脂分子量的增大,涂膜交聯(lián)度逐漸提高,涂膜的吸水率逐漸降低。這可能是由于分子量較大時(shí),涂膜內(nèi)部交聯(lián)結(jié)構(gòu)更完全,阻水效果更明顯。若分子量再進(jìn)一步增大,雖然交聯(lián)度仍較高,但是交聯(lián)形成的涂膜的自由體積增大,其輸水通道相應(yīng)增大,吸水率反而會(huì)增大。
4.2.2 羧基含量對(duì)改性樹(shù)脂耐水性的影響
聚合反應(yīng)中甲基丙烯酸的用量決定了引入改性樹(shù)脂中的羧基的含量。由表1可以看出,各涂膜交聯(lián)度均高于86%,其中控制聚合反應(yīng)MAA含量為丙烯酸類(lèi)單體總質(zhì)量的20%時(shí),交聯(lián)度最大。可達(dá)到99%;但繼續(xù)提高羧基含量(即提高M(jìn)AA含量),交聯(lián)度反而下降,這可能是由于固化時(shí)所采用的固化劑氨基樹(shù)脂量一定,羧基含量更高時(shí),由于固化劑用量不足反而導(dǎo)致交聯(lián)固化不夠完全,未顯示出交聯(lián)度的提高。當(dāng)聚合反應(yīng)單體中MAA含量介于13-20%時(shí),各涂膜吸水率均保持在1%以下,最低僅為5.33‰,表明樹(shù)脂的交聯(lián)反應(yīng),可以很好的屏蔽極性基團(tuán);但當(dāng)MAA含量繼續(xù)提高到27%時(shí),涂膜的吸水率顯著增大。一方面可能是由于固化不足導(dǎo)致,另一方面可能是因?yàn)轸然鶠橛H水性官能團(tuán),涂膜內(nèi)部羧基含量越多,水分子在膜層內(nèi)部聚集的位點(diǎn)越多,輸水通道越易形成,則涂膜吸水率相應(yīng)提高。尤其值得關(guān)注的是,在MAA含量為27%時(shí),其水性涂膜為溶劑型的吸水率3.32倍,這應(yīng)該是由于親水性官能團(tuán)過(guò)多存在,可能導(dǎo)致固化時(shí)膜層內(nèi)部水分殘留等原因,使得涂膜對(duì)水的屏蔽作用大大削弱,涂膜耐水性降低。#p#副標(biāo)題#e#
4.3 改性樹(shù)脂的耐蝕性
4.3.1 中性鹽霧腐蝕測(cè)試
圖4 鹽霧腐蝕測(cè)試照片(A)鍍鋅板,測(cè)試24小時(shí)后;(B)覆有改性清漆涂層的鍍鋅板,測(cè)試500小時(shí)后,涂覆厚度23微米
對(duì)上述樹(shù)脂的耐水性測(cè)試表明,控制聚合反應(yīng)的MAA含量為單體總量的20%,及分子量介于6000-7000左右時(shí)所得到的改性樹(shù)脂(即表1中的“EA-1-20”),其具有較高的交聯(lián)度與較低的吸水率,表現(xiàn)出良好的耐水性能。為了進(jìn)一步證實(shí)該樹(shù)脂具有較好的耐蝕性,將該樹(shù)脂所制得的水性清漆涂覆在鍍鋅板上,按照GB/T 1771-2007/ISO 7253:1996中規(guī)定的測(cè)試條件,對(duì)涂層進(jìn)行鹽霧腐蝕測(cè)試。如圖4所示,原鍍鋅板在測(cè)試后24小時(shí)內(nèi)即大面積出銹;而表面涂覆了改性樹(shù)脂水性清漆涂層的鍍鋅板,經(jīng)過(guò)500小時(shí)鹽霧腐蝕測(cè)試后,涂層表面并未出現(xiàn)明顯的變化,無(wú)腐蝕跡象顯現(xiàn),其防腐性能優(yōu)良。由此可知,自制的水性樹(shù)脂在高交聯(lián)度與低吸水率的同時(shí),也具備良好的耐蝕性能。
4 結(jié)論
本次研究采用使用量大、性能互補(bǔ)的環(huán)氧樹(shù)脂與丙烯酸樹(shù)脂制備復(fù)合改性樹(shù)脂,深入研究其復(fù)合工藝,確定了穩(wěn)定進(jìn)行二步酯化工藝制備目標(biāo)水性樹(shù)脂的條件,在該二步酯化工藝的保障下,實(shí)現(xiàn)了對(duì)改性樹(shù)脂分子量羧基含量的控制。
該改性樹(shù)脂易水性化,VOC含量可控,能進(jìn)一步降低其水性涂料VOC;其水性清漆涂覆性能佳,穩(wěn)定存放時(shí)間長(zhǎng);樹(shù)脂交聯(lián)度高,吸水率低,表現(xiàn)出良好的耐水性;經(jīng)過(guò)鹽霧腐蝕測(cè)試證實(shí)其涂層的耐蝕性已達(dá)到防腐涂層的要求。
利用二步酯化工藝自制高性能丙烯酸酯改性環(huán)氧水性樹(shù)脂,控制樹(shù)脂的分子量分布與極性官能團(tuán)數(shù)量,這為精確控制成膜樹(shù)脂分子結(jié)構(gòu)提供了途徑,為深入研究水性涂料耐水耐蝕性較差的致因提供了思路,也是實(shí)現(xiàn)依據(jù)所需性能進(jìn)行成膜樹(shù)脂分子設(shè)計(jì)這一思想的基本保證。
致 謝
本研究在朱華老師的精心指導(dǎo)下完成。汪的華教授與甘復(fù)興教授對(duì)實(shí)驗(yàn)的設(shè)計(jì)及實(shí)現(xiàn)提出了許多寶貴的建議與支持。謹(jǐn)在此對(duì)老師們表示崇高的敬意與由衷的感謝!
References(參考文獻(xiàn))
[1] JOHN Y. K., KIM J. H. Chain Extension Study of Aqueous Polyurethane Dispersions[J]. Colloids and Surface A: Physicochemical and Engineering Aspect, 2001, (179): 712-781.
[2] WALKER F. H. Amide-containing self-emulsified epoxy curing agent: US, 5489630[P]. 1996.
[3] Jianbo Lv, Xiaocong Liang. The present development situation of water based anti-corrosive coatings[J]. Information Recording Materials, 2009, 10(3) (Ch)
呂建波,梁笑叢. 水性防腐涂料的發(fā)展現(xiàn)狀[J]. 信息記錄材料,2009,10(3).
[4] WOO J. T. K., ALAN T. Water-based epoxy-acrylic graft co-polymer[J]. Prog. Org. Coatings, 1993, 21(4): 371-385.
[5] HEGEDUS C. R. Waterborne acrylic-epoxy coatings[J]. Coat Technol., 2002, 74 (927): 31-39.
[6] Xinyan Xiao, Caicheng Hao. Synthesis of Waterborne Epoxy Acrylate[J]. Journal of South China University of Technology (Natural Science Edition), 2009, 37(6): 47-51.
肖新顏,郝才成. 水性環(huán)氧丙烯酸樹(shù)脂的合成[J]. 華南理工大學(xué)學(xué)報(bào)(自然科學(xué)版),2009,37(6):47-51.
[7] MATTHEWS J F, SOMMERFELD E G. Water-borne coating composition made from epoxy resin polymer acid and tertiary amine: US 4247439 [P]. 1981.
[8] TING V W, MAREINKO R M. Aqueous epoxy ester emulsions: US 4480058 [P]. 1984.
[9] SPENCER ARTHUR T. Aqueous coating compositions: US 5296525 [P]. 1994.
[10] Min Liu, Hua Zhu, Yinwen, Lin, Fuxing Gan. Study on Optimized Synthetic Process of Acrylate Modified Waterborne Epoxy Resin[J]. PAINT & COATING INDUSTRY, 2011, 41(2): 42-45(Ch).
劉敏,朱華,林怡雯,甘復(fù)興. 丙烯酸改性環(huán)氧水性樹(shù)脂合成工藝的優(yōu)化研究[J]. 涂料工業(yè),2011,41(2):42-45.
[11] Min Liu, Yang Song, Hua Zhu. Study on influential factors of performance of waterborne Acrylic Modified Epoxy resin[J]., SHANFHAI COATINGS, 2010, 48(11): 13-17(Ch).
劉敏,宋洋,朱華. 水性丙烯酸改性環(huán)氧樹(shù)脂性能的影響因素研究[J]. 上海涂料,2010,48(11):13-17.
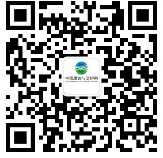
官方微信
《中國(guó)腐蝕與防護(hù)網(wǎng)電子期刊》征訂啟事
- 投稿聯(lián)系:編輯部
- 電話:010-62313558-806
- 郵箱:fsfhzy666@163.com
- 中國(guó)腐蝕與防護(hù)網(wǎng)官方QQ群:140808414