涂料工業: 隨著環保要求的提高和“雙碳”目標的提出,制造業在實現綠色轉型中扮演著重要角色,也面臨著前所未有的節能減排壓力。農機涂裝是整車制造過程中高能耗、重污染的環節,在整車制造過程中貢獻了較多的碳排放量。為了實現企業的“雙碳”目標,農機涂裝線新建或改造需要采用綠色前處理、環保涂料、自動化噴涂、余熱回收利用、智慧能源管理等綠色低碳技術減少能耗、降低“三廢”等污染物的產生和排放。 1.1. 環保型涂料 傳統溶劑型涂料在生產和使用過程中會產生大量的污染物,對環境造成嚴重影響;近些年,依環保要求國家鼓勵使用水性、高固分、粉末涂料等低VOCs含量的環保型涂料替代傳統溶劑型涂料,降低涂料自身所產生的污染。不同涂料的各項性能對比如表1所示: 表1 不同涂料的各項性能對比 近些年較多農機涂裝線改造將溶劑油性漆切換成水性漆。在生產運行中,發現產生的VOC廢氣濃度雖然降低了,但是對于環保標準比較嚴苛的城市來說,仍需要加廢氣處理設施,且水性漆對施工的溫濕度較為敏感,噴漆室在生產階段需要啟動空調控制溫濕度,這些無疑增加了動能能耗、設備維護及運行成本;對于增加的動能能耗會帶來較多的碳排放量,不利于實現低碳環保的要求。隨著粉末涂料在制造業的廣泛應用,粉末涂料價格逐步降低,且具有粉末回收利用率高、無“三廢”產生及處理設施、綜合能耗低的優點,因此在農機結構件涂裝線正在逐步推廣應用。 1.2. 環保型低溫脫脂劑 涂裝前處理使用的傳統脫脂劑的槽液溫度一般為50~55 ℃,在生產過程中隨著對工件的清洗將會帶走部分槽液熱量,因此脫脂劑槽液需要一直加熱保持工作溫度,能耗較高。低溫脫脂劑多數為環保型,其工作溫度通常為25~45 °C,針對油污較重的場合的工作溫度稍微高些為40~45 ℃,在該溫度下也能達到與傳統脫脂劑相當的效果,減少能耗約20%,具有明顯的節能降碳作用。 2.1. 前處理綠色技術 (1) 短流程工藝 傳統的脫脂和磷化工藝需要在50~60 ℃的溫度下進行,消耗大量能源。隨著綠色低碳發展要求,更環保、低能耗的硅烷或新型防安途工藝正在逐步取代傳統磷化工藝。硅烷或新型防安途不僅無毒無磷無重金屬離子無沉渣,而且工作溫度較低或常溫,無需加熱達到節能降碳的目的,還可以簡化工藝流程、縮短處理時間、獲取更優異的防腐蝕性能。其磷化、硅烷、防安途等工藝流程如圖1所示,各項性能對比如表2所示。 圖1 多種形式前處理工藝流程圖 表2 不同前處理工藝的各項性能對比 (2) 電泳廢水回收EDRO技術 電泳工藝段主要包括電泳、后沖洗工序,電泳采用全浸及出槽UF水噴淋相結合的方式。傳統的電泳系統采用UF過濾回收技術,如圖2所示,實現電泳及UF液水系統的封閉循環,但最后一級純水洗有新鮮純水噴淋補加,純水槽會產生溢流排放,造成電泳系統有大量廢水排放,若直接排放不僅污染環境,且造成涂料流失。電泳系統采用EDRO技術,是以超濾液作為處理原液,進行電泳反滲透(EDRO)處理,產生的“水”代替新鮮純水作為工件噴淋用,噴淋液逆序返回至電泳槽,產生的濃縮液返回到UF2槽,電泳漆利用率達99%以上,實現高效節約的閉路循環利用和廢水零排放,如圖3所示。 圖2 電泳后沖洗UF過濾回收技術方案 圖3 電泳后沖洗EDRO反滲透技術方案 2.2. 噴漆室綠色技術 噴漆室是涂裝車間最大的耗能設備,其能量消耗占涂裝線耗能的50%以上。近幾年,循環風、干式噴漆室、機器人自動噴涂等綠色低碳技術逐步推廣應用。 (1) 循環風技術 傳統水性漆噴漆室往往采用全新風的空調送風方式,噴漆室全新風一般風量較大、且需要調溫、調濕,以致于空調耗能較大。為了降低噴漆室能耗,可將采用漆霧捕集裝置的擦凈室、氣封室和人工補漆室的排風作為循環風,用于機器人噴漆室循環一次后進行排放;或者機器人噴漆室采用自循環風,自循環過程中需要抽取一定量風進行排風進入廢氣處理裝置,并往機器人噴漆室補充一定量新風,在機器人噴漆室安裝有機溶劑濃度檢測報警裝置,實現噴漆室新風量動態精確控制和確保自循環風中的有機溶劑濃度始終低于其爆炸下限的25%。 (2) 干式噴漆室 前些年,國內涂裝線大都采用水簾、文丘里、水旋等濕式噴漆室,僅有少數汽車線使用干式噴漆室,采用石灰粉、靜電等干式處理漆霧技術,石灰粉吸附漆霧后雖然理論上可以作為建材使用,但現實中處理困難;靜電吸附漆霧技術尚未國產化。近幾年,隨著紙盒干式漆霧捕集裝置技術的快速發展,在投資運行成本及能耗等方面占明顯優勢,使紙盒式干式噴漆室正在涂裝線上逐步推廣應用,紙盒干式噴漆室與傳統濕式噴漆室相比,具有不用消耗水、也無廢水產生,因此也不需要水循環系統及除渣系統,降低設備投資、減少設備占地面積、操作維護簡單無需專業人員維護等優點。不同形式的干式噴漆室對比如表3所示。 表3 不同形式的干式噴漆室對比分析 (3) 拖動示教噴涂機器人 在農機行業上,每條涂裝線上均要滿足多品種、復雜工件噴涂,就意味著編程人員需要進行大量的編程工作才能滿足實際生產的需要,為了降低編程的復雜性和多樣性,在底盤涂裝線上采用新型的拖動示教機器人。在復雜的底盤工件噴涂時,操作人員通過操作機器人末端的拖動手柄,根據工人的操作習慣和噴涂工藝要求,完成復雜底盤表面噴涂作業,機器人自動記錄人工拖動噴涂過程生成的噴涂軌跡程序,即完成程序編制。拖動示教編程方式的優點是無需掌握編程語言和仿真軟件,噴漆工人通過簡單培訓即可完成程序編制,生產過程中2~3人配合,5 min可實現新產品的程序編制,該編程方式比較適用于多品種、生產線切換比較頻繁的工件噴涂。 2.3. 前處理綠色技術 (1) RTO尾氣余熱利用 涂裝噴漆室、烘干爐的尾氣處理裝置RTO需常年運行,一直有高溫煙氣排出,這不僅造成環境局部變暖,而且浪費了大量寶貴能源,造成企業運行成本居高不下。在RTO煙氣排放口安裝“氣-水”余熱回收系統,使凈化后的尾氣經余熱回收裝置與前處理工藝回水交換熱量,進水溫度由75 ℃加熱到90 ℃,尾氣排放溫度由約200 ℃降至120 ℃,工藝回水被加熱后回到燃氣熱水機組,從而減少熱水機組天然氣耗量,達到節能降碳的目的。 (2) 熱泵技術 隨著雙碳政策的出臺以及高效熱泵技術的發展,越來越多的涂裝線前處理與烘干爐上應用高效熱泵。針對前處理的預脫脂槽液、脫脂槽液及低溫水性漆烘干爐的溫度較低,可以采用熱泵加熱式代替燃氣或電加熱方式,熱泵吸收空氣中的低品位熱量產生較高品位的熱量可以用來烘干工件、加熱脫脂槽液,在夏季時,熱泵排出的低溫風送至上下件、遮蔽等人工操作崗位,改善員工工作環境,這種冷熱聯供形式提高了熱泵的綜合能效,與傳統的電、燃氣加熱相比降低40%~60%的能耗。若在谷電、平電階段使用熱泵,其運行成本與傳統的電、燃氣加熱相比有明顯降低;若在峰電階段使用熱泵,其運行成本與傳統的電、燃氣加熱相比降低不明顯。 涂裝線首先是能耗大戶,再者生產中需要電、天然氣、蒸汽、壓空、水等能源、資源種類較多,人工抄表工作量大、難免遺漏,不利于生產過程的能源管理。新的能源管理方式應完善能源三級計量智能儀器儀表,通過搭建能源管理數字化平臺系統,可實時統計與分析日耗量、月耗量、年度耗量及單車能耗,并及時給出能耗超標預警提示;便于實現能耗指標的統計、追溯、分析;使能源成本細化。 通過對能源數據進行長期跟蹤,及時發現涂裝線節能潛在機會。 涂裝線噴漆室控溫控濕、烘干爐加熱、機運系統等電耗量較大,越來越多的企業自建分布式光伏發電系統,所產生的綠電可以“自己自足”,也可以通過與電網并網,以“多交少補”的形式靈活用電,降低了煤電用電量,進而逐步達到節能降碳、零碳涂裝線的目的。 綠色涂裝技術在農機涂裝線中正逐步推廣應用,通過源頭減碳、清潔生產、過程減碳、綠色技術應用以及能源管理和能源結構優化等措施,農機生產企業可以顯著降低生產過程中的能耗和碳排放,提高產品質量和生產效率。
免責聲明:本網站所轉載的文字、圖片與視頻資料版權歸原創作者所有,如果涉及侵權,請第一時間聯系本網刪除。
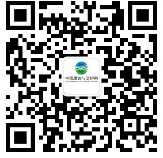
官方微信
《腐蝕與防護網電子期刊》征訂啟事
- 投稿聯系:編輯部
- 電話:010-62316606
- 郵箱:fsfhzy666@163.com
- 腐蝕與防護網官方QQ群:140808414