涂料工業: 冷噴涂技術的工作原理是:將高壓氣體(氮氣、氦氣、空氣或混合氣體)經過氣體加熱器進入縮放的拉瓦爾噴嘴,形成超音速氣體流碰撞基體,帶動粉末粒子在低溫(一般低于600 ℃)下進入拉瓦爾噴嘴,使粉末粒子發生強烈的塑性變形,從而沉積在基體表面形成沉積層。冷噴涂技術的噴涂效果主要取決于噴涂速度的選擇,噴涂速度應在臨界沉積速度與侵蝕速度之間。侵蝕速度是粒子噴涂速度的上限,噴涂速度如果超過侵蝕速度,就會出現沖蝕,而顆粒不會黏著。只有當撞擊速度大于臨界速度,小于侵蝕速度時,粒子才能與基體結合沉積形成涂層。 冷噴涂涂層形成過程包含2個不同階段的相互作用。第1階段主要為顆粒與基體間的相互作用:顆粒與基體碰撞后,在碰撞界面處產生凹陷,導致顆粒與基體接觸表面處的氧化膜破裂,暴露出潔凈的表面,兩者結合形成基體層,這便是前期涂層形成的關鍵,且與最終基體和涂層之間的結合強度有密切關系。第2階段主要為顆粒與已沉積涂層間的相互作用:后續顆粒對已沉積涂層中的部分顆粒的錘擊作用促使其發生變形,顆粒間孔隙被消除,結合更緊密,這關系到涂層厚度的增加和自身結合強度。當前的研究主要集中在顆粒與基體的結合機理上,對顆粒高速沖擊引起的基體表面殘余壓應力變化、顆粒撞擊基體過程中顆粒之間的結合機理研究則相對較少,需要進一步深入探索和研究,為高性能涂層的制備提供理論基礎。 與傳統的熱噴涂技術(火焰噴涂、爆炸噴涂、電弧噴涂等)不同,冷噴涂顆粒加熱溫度低,而且顆粒仍然保持著固態,固態顆粒在極高應力、應變和應變速度條件引發“絕熱剪切失穩”狀態,顆粒通過劇烈機械變形等過程,最終在工件上實現沉積。 相對于熱噴涂技術而言,冷噴涂的優勢包括:噴涂溫度低,對基體的影響較小;可制備的材料較為廣泛,如鋅、鋁、銅等金屬、合金材料如不銹鋼、青銅等、金屬陶瓷或金屬基復合材料等;噴涂的涂層殘余應力較低;噴涂涂層光滑致密,孔隙率低,強度較高,能滿足航空、航天等高負荷領域的使用;沉積效率高、粉末利用率高;環境污染小,操作簡單、安全,無輻射。 不過,冷噴涂同樣存在著它的劣勢:涂層的延展性較差,這主要是由顆粒的塑性沉積引起的,可以通過熱處理和優化冷噴涂工藝參數進行改善。且噴涂顆粒能否有效沉積以及制備涂層是否穩定,取決于顆粒與基材的特性。此外對于制備一些高溫合金涂層必須使用氦氣,耗氣量會很大,價格會偏貴。 冷噴涂技術能夠制備出孔隙率低、結合強度高、厚度可控的涂層,為基體材料提供了卓越的抗腐蝕性能。因此,冷噴涂技術在防腐涂層領域具有廣闊的應用前景,尤其在航空航天和海洋環境中飛機、艦艇、輪船等各領域的關鍵機械部件的腐蝕防護上,冷噴涂技術為它們的表面改性研究、長久高效防腐、快速修補等帶來了新的解決方案。 此外,冷噴涂涂層具有低殘余應力(主要為壓應力),可制備單一金屬涂層或含有陶瓷顆粒增強相的復合涂層,這類涂層的耐磨性往往更好,因此冷噴涂技術可用于制備多種耐磨涂層材料,包括減磨合金(如錫青銅、鋁合金、鋅合金)、金屬基材料以及金屬陶瓷復合材料。這其中,金屬陶瓷復合材料結合了金屬相(韌性和可加工性好)和增強陶瓷相(硬度和耐磨性好)的特點,使得涂層具備出色的耐磨性、耐蝕性、力學性能等優點,廣泛應用于各種重要的工業領域。目前,冷噴涂已在各種耐磨材料表面制備涂層中得到廣泛應用,成為不可或缺的耐磨涂層制備技術。 目前,圍繞冷噴涂技術在防腐涂層和耐磨涂層的應用研究,主要聚焦涂層的復合與改性、工藝參數的調節等來進行性能提升。而對于一些嚴苛服役工況(如重載荷、重腐蝕、高振動環境),對涂層的耐蝕、耐磨、防污、機械性能等的要求也日益提高,僅憑現已掌握的冷噴涂技術提升手段仍有較大的改進空間。對于冷噴涂技術中的沉積與結合機理、物理力學效能、關鍵因素影響等,仍需要更多更全面的研發來推動系統化理論體系的完善,并逐步克服冷噴涂的涂層延展性較差、有效沉積效率低等缺點,從而讓冷噴涂技術走向成熟,擁有更廣闊的應用與市場。
免責聲明:本網站所轉載的文字、圖片與視頻資料版權歸原創作者所有,如果涉及侵權,請第一時間聯系本網刪除。
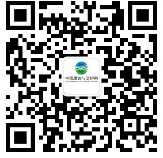
官方微信
《腐蝕與防護網電子期刊》征訂啟事
- 投稿聯系:編輯部
- 電話:010-62316606
- 郵箱:fsfhzy666@163.com
- 腐蝕與防護網官方QQ群:140808414