本文介紹了萊鋼銀山型鋼煉鋼廠生產鈦微合金鋼Q355B不同生產環節氮含量變化情況,分析了生產流程各因素對鋼中氮含量的影響,其中轉爐終點碳氧含量、出鋼溫度,LF進站鋼液溫度、電極電耗、底吹氬氣、埋弧效果,連鑄保護澆注等對鋼水增氮有較大影響。提出了相應的優化措施,通過轉爐終點碳含量、出鋼溫度、精煉渣成分控制等措施,達到了穩定控制氮含量在40×10-6以下的效果。 1 前言
通常氮是鋼中有害元素,鋼中氮含量高會使鋼材產生應力失效,降低鋼的成形性及高溫韌性和塑性,并影響鋼的焊接性能,氮還會與鋼中的鈦、鋁等元素形成鏈狀夾雜物群,造成板坯角裂,引起鋼的表面質量惡化,降低成材率等。對于鈦微合金鋼,[Ti]含量高,若[N]含量控制不當,含Ti 鋼中TiN夾雜在鋼液中容易碰撞聚合,形成TiN團簇,對鋼表面質量和力學性能產生不利影響。本研究以萊鋼銀山型鋼煉鋼廠生產鈦微合金鋼Q355B為研究對象,系統分析了轉爐、精煉、連鑄過程氮含量變化,明確了冶煉過程中增氮的關鍵因素,為氮含量降低提供有效控制措施。
2 煉鋼全流程氮含量調研
鈦微合金鋼Q355B化學成分如表1所示。 為研究鈦微合金鋼Q355B生產流程各因素對鋼中氮含量的影響,明確控氮的關鍵環節,對轉爐煉鋼終點、LF精煉不同階段、連鑄不同工序的鋼液進行取樣,利用氧氮分析儀檢測鋼液氮含量變化。其中,LF1代表LF進站,樣1代表造白渣后,樣2代表喂鈣線前,LF4代表軟吹前。 圖1為鈦微合金鋼Q355B不同生產環節氮含量變化情況。轉爐終點鋼中氮含量為(12~26)×10-6,不同爐次之間氮含量波動較大,轉爐到精煉破殼階段鋼中增氮量波動不定,增氮量(-5~7)×10-6不等,精煉階段氮含量顯著增加。增氮范圍(7~13)×10-6,連鑄階段鋼中氮含量保持穩定,波動維持在2×10-6以內,結晶器鋼水中氮含量(32~45)×10-6。
3 各工序對鋼水增氮的影響
3.1 轉爐工序 轉爐脫氮效果與吹煉過程的脫碳反應速度密切相關,特別是脫碳反應劇烈的時間段內,由于轉爐內產生大量的CO/CO2氣泡,當CO氣泡到達鋼液表面時,CO氣泡既與鋼液接觸,也有一部分與爐渣接觸。當熔池中CO氣泡上升過程中與金屬液滴之間發生大量的碰撞后進入爐渣,這些氣泡會在熔池內形成相對密閉的“真空泵”,每個氣泡顯著降低了氮氣分壓,在碰撞的過程中氣泡和金屬液滴之間可以發生脫氮反應,達到了良好的脫氮效果。 3.1.1 碳氧含量 圖2為轉爐終點C含量對鋼中N含量的影響。從圖2中可以看出,轉爐終點C含量在0.065%~0.095%,轉爐終點碳氧反應減弱。隨著C含量的降低,鋼中N含量逐漸增大,表明碳氧反應的減弱使CO等爐氣產生量不斷減少,爐口壓差降低,空氣易卷入,爐內氮氣分壓增大,造成鋼水吸氮。 圖3為轉爐終點O含量對鋼中N含量的影響。從圖3中可以看出,隨著O含量的增大,鋼中N含量逐漸下降,說明隨著碳氧反應的進行,脫碳逐步深入,作為表面活性元素的O含量也有所增加。氧和FeO在鋼液表面富集,降低了氣-液反應界面,降低鋼液吸氮速度,抑制了鋼液吸氮。 3.1.2 出鋼溫度 圖4為轉爐終點出鋼溫度對鋼中N含量的影響。隨著溫度升高,鋼中N含量不斷增加。其原因是鋼液吸氮是一個吸熱反應,溫度越高,氮氣越利于溶入鋼中成為游離氮原子;另一方面,高溫有利于增強脫硫熱力學條件,弱化了硫作為表面活性元素抑制鋼液吸氮的效果,造成增氮。 3.2.1 進站溫度 圖5所示的是LF進站溫度對鋼中N含量的影響。由圖5可知,不同爐次之間進站溫度差異較大,最大可達30℃,且進站溫度越低,鋼中N含量越高。進站溫度較低的鋼包頂渣化不開、流動性不好,覆蓋效果差,送電過程中電弧不能埋于渣中,電弧區鋼液極易吸氮,造成增氮。因此,轉爐終點出鋼應控制終點成分、合理調整合金加入量,盡量縮短出鋼及破殼等待時間,減少出鋼溫降、避免強吹致使鋼液液面裸露,以減少LF送電次數,縮短處理時間,控制增氮。 3.2.2 電極電耗 圖6為精煉總電耗與進站溫度的關系。從圖6中可以看出,精煉電耗為3000~4000kW·h,與進站溫度成反比。進站溫度越低,需要對鋼水進行溫度補償。精煉電耗越高,并且較低的進站溫度不利于早期化渣、造渣等操作,易造成爐渣結殼嚴重,需要在LF進站后進行較長時間的大流量攪拌,造成鋼液和空氣接觸的機率增大;同時,對于較低溫度的爐次,需要先對其進行送電加熱提溫操作,未完全化開的渣在電弧高溫作用下易使鋼液裸露吸入周圍電離的氮原子,增大鋼液增氮的概率,還延長了精煉工序時間。因此,LF鋼包進站溫度不宜過低。 3.2.3 底吹氬氣 LF操作過程中需要進行吹氬,精煉大氣量攪拌有益于深脫硫、促進夾雜物上浮、均勻成分和溫度,但同時會造成鋼水裸露吸氮。通過計算得到精煉工序不同階段的攪拌功。精煉工序中破殼階段攪拌功最大,達到200.98W;精煉階段較造渣階段攪拌功略大,為56.02W左右;軟吹階段攪拌功最小,僅為25.73W。其中,各階段任務要求不同,所需氬氣流量、攪拌功大小也不盡相同。LF精煉工序攪拌功偏小,造渣和白渣精煉階段,既可以保證不吹開渣層造成鋼液面裸露吸氮,又可以預防鋼液溫降過大,吹氬量較為合適。 3.2.4 埋弧效果 經統計,9爐次精煉溫度在1550℃左右,為了研究埋弧效果對鋼液增氮量的影響,選取1550℃下造完白渣后的渣樣,探討發泡指數與鋼中氮含量之間的關系。圖7是發泡指數與增氮量間的關系。 由圖8可知,隨著精煉渣發泡性的改善,鋼液中的氮含量逐漸降低,說明在一定范圍內,提高精煉渣的發泡指數,有利于鋼液氮含量 控制。這是因為發泡性的改善相對增加了渣層厚度,利于實現埋弧操作。一方面降低了鋼液表面裸露面積;另一方面減少了電弧裸露長度,使電弧電離空氣產生的氮原子大幅減少,進入鋼液的概率也大大降低。LF精煉渣組分、物相、熔化特性、黏度等影響鋼液覆蓋效果,決定爐渣發泡性能、夾雜物吸收能力、鋼液精煉效果,進而對鋼中氮含量變化起作用。 3.3 連鑄工序 連鑄過程采用保護澆鑄,在中間包鋼液面投加覆蓋劑,大包水口、中間包水口密封、氬氣流量的適當控制、減少換包過程中鋼水裸露時間等能有效控制鋼水增氮。表2為連鑄過程中氮含量變化。由表2中可以看出,連鑄過程中鋼液增氮<2×10-6,說明保護澆鑄效果良好。
4 工藝優化
為實現鈦微合金鋼Q355B氮含量穩定控制在40×10-6以下的目的,并同時兼顧生產成本,對其進行了工藝優化,轉爐終點碳含量控制在0.06%~0.10%,出鋼溫度維持在1630~1640℃。精煉渣成分控制:造渣階段堿度維持在3.0~5.0,Al2O3含量保持在20%~30%,TFe含量低于1.0%。連鑄保護效果好,維持原工藝不變。 采用優化工藝方案生產后,Q355B不同生產環節氮含量變化如圖8所示。結晶器氮含量為(27~36)×10-6,達到了穩定控制氮含量在40×10-6以下的效果。當轉爐終點碳溫控制在一定范圍內,采用工藝優化方案轉爐終點鋼液氮含量為(11~19)×10-6,與原冶煉工藝轉爐終點(12~26)×10-6相比,氮含量穩定控制范圍大幅縮小。將轉爐終點氮含量控制在20×10-6以下,有利于緩解后續LF精煉環節控氮的壓力。優化方案下,出鋼與精煉兩個工序的增氮量合計為(6~16)×10-6,而優化前增氮量為(6~20)×10-6,說明優化方案實際增氮量也大幅減少,從而使結晶器氮含量穩定控制在40×10-6以下。 原工藝LF進站溫度為1537~1565℃,能耗為3000~4000kW·h;工藝優化后LF 進站溫度為1550~1570℃,能耗為2000~3000kW·h;優化前后LF進站溫度總體提高約20℃,電耗降低約1000kW·h。有利于避免長時間底吹大流量攪拌和提溫操作,可有效降低增氮量,進站溫度的提高不僅節約能源成本,還縮短了工序時間。
5 結論
原工藝終點碳含量為0.066%~0.094%、出鋼溫度為1631~1642℃、氮含量為(12~26)×10-6,優化方案終點碳含量為0.062%~0.083%、出鋼溫度為1627~1635℃、氮含量為(11~19)×10-6。碳含量和出鋼溫穩定控制使得氮含量下降7×10-6,控氮效果較好。 原工藝出鋼與精煉環節增氮量為(6~20)×10-6,優化方案下出鋼與精煉兩個工序的增氮量合計為(6~16)×10-6,縮小了增氮量,從而使結晶器氮含量穩定控制在40×10-6以下。 工藝優化前后LF進站溫度總體提高約20℃,電耗降低約1000kW·h。有利于避免長時間底吹大流量攪拌和提溫操作,可有效降低增氮量,節約了能源成本,縮短了工序時間。 連鑄階段目前保護效果較好,在目前生產條件下,不是導致增氮的關鍵性環節,可穩定控制結晶器鋼液氮含量<40×10-6。
免責聲明:本網站所轉載的文字、圖片與視頻資料版權歸原創作者所有,如果涉及侵權,請第一時間聯系本網刪除。
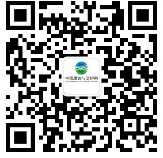
官方微信
《腐蝕與防護網電子期刊》征訂啟事
- 投稿聯系:編輯部
- 電話:010-62316606
- 郵箱:fsfhzy666@163.com
- 腐蝕與防護網官方QQ群:140808414