01
表面形變強化是通過機械手段(滾壓、噴丸等)在金屬表面產生壓縮變形,使表面形成硬化層,形變硬化層深度可達0.15-1.5mm,表面形變強化的方法主要有:噴丸強化、表面滾壓技術、孔擠壓強化。壓縮過程中,形變硬化層中將產生以下兩種變化:
(1)從組織結構上看,強化層內位錯的密度極高,晶格的畸變度大,在交變應力的作用下,符號相反的位錯相遇后會相互抵消,符號相同的位錯將重新排列。此時,強化層內位錯密度雖有下降,但會逐漸形成更加細小的亞晶粒。
(2)從應力狀態上看,由于表層與內層的金屬變形程度不平衡,表層金屬向四周塑變延伸時,會受到內層金屬的阻礙,在強化層內形成了較高的宏觀殘余壓應力。
噴丸強化,又稱受控噴丸強化,是將高速彈丸流噴射到零件表面,使零件表層發生塑性變形,從而形成一定厚度的強化層,由于零件表面壓應力的存在,當零件承受載荷時可以抵消一部分應力,從而提高零件的疲勞強度。噴丸強化如圖1所示。
圖1 噴丸強化過程示意圖
在室溫下利用高速噴射的細小硬質彈丸打擊工件表面,使表面層在再結晶溫度下產生彈性、塑性變形,如圖2所示,并呈現較大的殘余壓應力,因為當每顆鋼丸撞擊金屬零件上,宛如一個微型棒褪敲打表面,捶出小壓痕或凹陷。為形成凹陷,金屬表層必定會產生拉伸。表層下,壓縮的晶粒試圖將表面恢復到原來形狀,從而產生一個高度壓縮力作用下的半球,無數凹陷重疊形成均勻的殘余壓應力層,從而提高表面疲勞強度和抗應力腐蝕的能力。
圖2 噴丸表面得塑性變形
噴丸也可以用來清除厚度不小于2mm或不要求保持準確尺寸及輪廓的中型、大型金屬制品以及鑄鍛件上的氧化皮、鐵銹、型砂及舊漆膜,是表面涂(鍍)覆前的一種清理方法。噴丸強化是一個冷處理過程,它被廣泛用于提高長期服役于高應力工況下的金屬零件,如飛機引擎壓縮機葉片、機身結構件、汽車傳動系統零件等的抗疲勞屬性。
噴丸按射出彈丸的速度分為普通噴丸和超音速表面噴丸,超音速噴槍射出的彈丸速度為300~500m/s,并隨著零件的轉動,可實現對整個零件表面的噴丸強化。
(1)噴丸強化的設備
按驅動彈丸的方式,可將噴丸強化機分為機械離心噴丸機和氣動噴丸機兩大類。此外噴丸機又有干噴和濕噴之分,干噴式噴丸機工作條件差,濕噴式噴丸機是將彈丸混合成懸浮狀,然后噴出彈丸,因此工作條件有所改善。
①機械式離心噴丸機彈丸在高速旋轉的葉片和葉輪離心力的作用下被加速拋出。該型噴丸機噴丸功率小,制造成本高,主要用于噴丸強度高、品種少、批量大、形狀簡單、尺寸較大的工件,如圖3所示。
1-葉輪;2-葉輪轉向;3-接觸葉片前的彈丸;
4-彈丸輸送管;5-漏斗;6-壓縮空氣;7-噴射管;
8-90°彎曲噴管;9-彈丸
圖3 機械離心式噴丸機
②氣動離心噴丸機以壓縮空氣為驅動力,將彈丸加速到較高速度后,隨后彈丸撞擊工件的受噴表面。該型噴丸機可通過控制氣壓來控制噴丸強度,操作靈活,一臺機器可噴多個零件,適用于噴丸強度低、品種多、批量小、形狀復雜、尺寸較小的零部件,但功耗大、生產效率低,如圖4所示。
1-零件;2-閥門;3-空氣過濾器;4-管道;
5-噴嘴;6-導丸管;7-儲丸箱;8-排塵管;9-轉換口
圖4 氣動離心式噴丸機
(2)彈丸的種類
鋼絲線切割丸:常用鋼絲直徑d=0.4~1.2mm,硬度以45~50HRC為最佳,組織最好是回火M或者B。
鑄鋼丸:彈丸尺寸為0.2~1.5mm,經退火處理,硬度為30~57HRC,易碎,耗量大,但價格便宜。鑄鋼丸的品質與含碳量有關,一般含碳量在0.85%~1.2%,錳含量在0.65% ~ 1.2%。
玻璃彈丸:含60%的SiO?,硬度為46~50HRC,脆性大,適用于零件硬度低于彈丸的硬度的場合。
陶瓷彈丸:彈丸硬度高,但脆性大,噴丸后可獲得較高的殘余壓應力。
液態噴丸:包括SiO?顆粒和Al?O?顆粒。噴丸時用水混合SiO?顆粒,利用壓縮空氣濺射。
表面滾壓技術是在一定壓力作用下,滾球或輥軸對被加工零件表面進行滾壓或擠壓,使其發生塑性變形,形成強化層的工藝過程,如圖5所示。
圖5 表面滾壓強化示意圖
表面滾壓技術的表面改性層深度可達到5mm以上,僅適用于一些形狀簡單的平板類零件、軸類零件和溝槽類零件等,對形狀復雜的零件表面無法應用。表面滾壓技術具有很多無法比擬的優點,如表面滾壓技術僅改變了材料的物理狀態,并未改變材料的化學成分;表面滾壓技術采用的工具和工藝比較簡單,加工效率高;滾壓滾壓技術是一種無切削加工工藝,在加工過程中不會產生廢屑、廢液,對環境的污染少,符合“綠色制造”的發展理念。此外,表面滾壓技術可消除零件表面因切削加工引起的拉應力,并使零件表面處于壓應力狀態,殘余的壓應力既可以使裂紋尖端閉合又可以抑制裂紋尖端的擴展,從而進一步提高零件的疲勞壽命,該技術在工業中得到了廣泛的應用,產生了巨大的經濟效益。
(1)作用機理
①微觀組織機理。經過切削加工之后,金屬的表面都殘留有刀具的切削痕跡,在微觀下觀察可以看見金屬的表面呈現出凹凸不平之狀。滾壓加工是一種壓力光整加工,在滾刀的作用下金屬表面會發生強烈的塑性變形。根據工程材料的相關理論,金屬發生塑性變形的基本方式是滑移,即晶體沿某一晶面和晶向相對于另一部分發生相對滑移。在外力的作用下,晶體不斷滑移,晶粒在變形過程中逐步由軟取向轉動到硬取向,晶粒之間互相約束,阻礙晶粒的變形。由于工業所用金屬多為多晶體,故金屬能承受較大的塑性變形而不會被破壞。金屬內部晶粒的不斷滑移會使得晶粒的位錯密度增加、晶格發生畸變,符號相反的位錯相互抵消,符號相同的位錯則重新排列行成更加微小的亞晶粒。晶粒越細小,位錯密度越高,產生的變形分散就越多,因而不易產生局部的應力集中,使得滾壓后的金屬材料的屈服強度和疲勞性能得到顯著提高。
②表面質量機理。金屬表面質量的好壞常用表面粗糙度來衡量,表面粗糙是造成應力集中的主要因素之一,粗糙的表面易形成尖端切口,造成應力集中,而疲勞源則往往出現在應力集中處,在交變應力的作用下,應力集中促使疲勞裂紋的形成和擴展。表面越粗糙、尖端切口越尖銳,應力集中就越嚴重。滾壓強化就是利用滾輪對工件表面的滾壓作用,使工件表層金屬產生塑性流動,填入到原始殘留的低凹波谷中,從而降低工件表面的粗糙度,消除殘留刀痕,減少應力集中,進而提高工件的疲勞壽命。
③殘余壓應力機理。早在20世紀30年代人們就發現,讓零件表面產生殘余壓應力可以延長工件的疲勞壽命。金屬材料表面的裂紋擴展的條件是外加交變載荷達到某一界限(即應力強度達到材料本身的臨界應力強度時)。而滾壓則可以減少表面原有的微觀裂紋,還可以產生殘余壓應力,從而提高零件的疲勞壽命。
(2)影響滾壓效果的工藝參數
影響表面滾壓效果的工藝參數主要有:滾壓力、滾壓次數和滾壓速度等。滾壓力即為滾輪壓到工件表面上的力,其對工件的疲勞強度有很大的影響,但目前對其研究還不夠成熟,沒有數學公式能夠準確地計算出最佳滾壓力。最佳滾壓力還與零件本身強度、零件尺寸、滾輪直徑等因素有關,生產中則是通過工藝試驗來確定最佳滾壓力;滾壓次數即為滾輪壓過工件同一位置的次數,它對工件的疲勞強度有很大影響,次數較少時,工件表面未能達到應有的塑性變形,次數較多時,工件會產生接觸疲勞,嚴重時會使表面脫落;滾壓速度即為滾壓加工時工件的轉動速度,其對工件的疲勞強度影響不大,但影響滾壓加工的效率,若轉速過高,則會引起較大的塑性變形,轉速過慢又會降低生產效率。在生產中需要根據實際情況來確定合適的滾壓速度。
(3)孔擠壓強化
孔擠壓強化是利用特定的工模具(棒、襯套、開合模具等)對工件的孔壁或周邊進行連續、緩慢、均勻的擠壓,使其形成一定厚度的塑性變形層,達到提高表面疲勞強度和抗應力腐蝕能力的一種表面強化工藝。
常采用的工藝方法:棒擠壓、襯套擠壓、壓印模擠壓、旋壓擠壓,如圖6所示。
(a)1-液壓機;2-夾頭;3-擠壓棒;4-零件;5-底座
(b)1-零件;2-襯套;3-擠壓棒;4-拉拔槍
(c)1-液壓機;2-壓印模;3-零件;4-底座
(d)1-孔臂鉆;2-夾頭;3-擠壓頭;4-零件;5-底座
圖6 孔擠壓強化的工藝方法
孔擠壓強化主要針對內孔有抗疲勞要求或其他方法無法實現的工件,如飛機上的重要零件;壓印模擠壓適用于大型零件及蒙皮等關鍵承載件的強化;旋壓擠壓適用于起落架等大型零件的內孔強化等。
等離子體是由大量的自由電子和離子組成且在整體上表現為近似電中性的電離氣體。等離子化學熱處理技術,又稱等離子體擴滲技術(PDT)或粒子轟擊擴滲技術,是利用低真空環境中氣體輝光放電產生的離子轟擊工件表面,使金屬表面成分、組織結構及性能發生變化的工藝過程。
與普通氣體熱擴滲技術相比,離子熱擴滲具有如下特點:
(1)離子轟擊濺射將會去除工件表面的氧(鈍)化膜或雜質,提高工件表面活性,使其易于吸附被滲元素,加快熱擴滲速度;
(2)等離子體可激活反應氣體,降低化學反應溫度;
(3)可通過調節工藝參數控制熱擴滲層的組織以及滲層的厚度;
(4)對環境無污染,是一種環境友好型的處理工藝。
等離子體可分為高溫等離子體和低溫等離子體。極光、日光燈、電弧、碘鎢燈等屬于低溫等離子體,聚變、太陽核心等屬于高溫等離子體。
低溫等離子體(也稱非平衡等離子體)中的重粒子溫度接近常溫,而電子溫度高達10³~10?K。
使氣體由絕緣體變成導體的現象稱為氣體放電。氣體放電的條件是:有一定的電場強度;氣體中存在帶電粒子。
在電場中,帶電粒子發生定向運動。帶電粒子與氣體原子、帶電粒子與電極之間發生一系列的物化變化,即帶電粒子之間發生碰撞引起氣體激發和電離;碰撞使原子中的電子從正常能級躍遷到較高能級,變成亞穩態的受激原子;受激電子返回基態時,將能量以光子的形式釋放出來(輝光),若帶電粒子撞擊的能量較大,可能會將原子中的某個電子撞離原子(電離)。
(1)Kolbel離子濺射滲氮模型
高能氮離子轟擊陰極使Fe原子濺射出陰極表面,Fe原子與N原子結合形成FeN,并重新沉積在工件表面(背散射),處于亞穩態的FeN按FeN→Fe?-?N→Fe?N的順序依次分解,分解出的活性N原子滲入鋼的表面或近表面,同時鋼表面從外到內形成由Fe?-?N(ε相)和Fe?N(γ’相)的滲氮層。如圖7所示。
圖7 Kolbel離子濺射滲氮模型
(2)新的離子滲氮模型
新的直流離子滲氮模型如圖8所示,離子滲氮裝置如圖9所示。
圖8 新的直流離子滲氮模型
1-直流電源;2-真空室;3-工件;4-溫控儀;
5-真空計;6-真空泵;7-流量計;8-供氣系統
圖9 離子滲氮裝置示意圖
(1)將清洗好的工件放入離子滲氮爐內,抽真空至1Pa左右;
(2)通入少量含氮氣體,接通直流高壓電源,使氣體產生輝光并放電;
(3)濺射、凈化被處理工件表面;
(4調整氣壓和電壓,將工件加熱到所需要的處理溫度,開始滲氮;
(5)保溫一定時間,達到滲氮層要求的厚度;
(6)斷電、工件在真空中冷至200℃以下,出爐滲氮后的工件表面呈銀灰色。
在小于590℃(共析溫度)的溫度環境下進行滲氮,隨著氮勢的增加,滲氮層的組織自外向內依次為:ε→ε+γ’→γ’+擴散層→α擴散層,如圖10所示。
圖10 38CrMoAl鋼滲氮后表面組織形貌(560℃×5h)
影響離子滲氮層的主要因素如下:
(1)滲氮溫度:隨溫度升高,滲層厚度增加。當溫度<550℃,γ’相比例隨溫度提高而增加;當溫度>550℃后,ε相比例隨溫度提高而增加。
(2)滲氮時間:滲氮初期(<30min)滲速遠大于氣體滲氮速度,隨時間延長,滲速減慢,逐漸接近氣體滲氮速度。
(3)滲氮氣體:常用的有氨、氮氣+氫氣等。
(4)滲氮氣壓、電壓和電流密度:氣壓越大,滲氮層越厚;放電功率越大,滲氮層越厚;電流密度越大,滲氮層越厚。
評價離子滲氮層的性能的指標主要包括以下幾個方面:
(1)硬度:滲氮層的硬度取決于滲氮溫度、鋼中合金元素種類和鋼種。
(2)疲勞強度:滲氮可以提高工件的疲勞強度,并隨擴散層厚度的增加而提高。
(3)韌性:滲氮層中,僅有擴散層的部分韌性最好,有單相化合物層(ε相或γ’相)的次之,γ’+ε相混合相的最差。
(4)耐磨性:與其他滲氮方法相比,離子滲氮對滾動摩擦的耐磨性最好。
常用鋼種的離子滲氮工藝見表1。
表1 常用鋼種的離子滲氮工藝
激光表面處理技術是指利用激光束特有的性能特點,對材料表面進行處理并形成一定厚度的處理層,可以顯著改善材料表面的力學性能、冶金性能、物理性能,從而提高零件、工件的耐磨、耐蝕、耐疲勞等性能,是一種高效且成熟的表面處理技術。
(1)激光束處理后,材料表面的化學均勻性很高,晶粒細小,因而表面硬度高,耐磨性好,在不損失韌性的情況下獲得了高的表面性能。
(2)輸入熱量少,熱變形小。
(3)能量密度高,加工時間短。
(4)處理部位可以任意選擇,如深孔、溝槽等特殊部位均可采用激光進行處理。
(5)工藝過程無需真空,無化學污染。
(6)激光處理過程中,表層發生馬氏體轉變而存在殘余壓應力,提高了其疲勞強度。
激光表面處理設備包括:激光器、功率計、導光聚焦系統、工作臺、數控系統和軟件編程系統。
激光是一種相位一致、波長一定、方向性極強的電磁波,激光束是由一系列反射鏡和透鏡來控制,所以激光束可以聚焦成直徑很小的光束(直徑只有0.1mm),從而可以獲得極高的功率密度(10?~10?W/cm²)。按激光強度和輻射時間可將激光與金屬之間的互相作用分吸收光束、能量傳遞、金屬組織的改變和激光作用的冷卻等階段。
激光表面處理技術是采用大功率密度的激光束,以非接觸性的方式加熱材料表面,依靠材料表面自身的導熱性達到冷卻的目的,從而實現其表面強化的工藝方法。它在材料加工中的如下優點:
(1)能量傳遞方便,可以對被處理工件表面進行有選擇性的局部強化;
(2)能量作用集中,加工時間短,熱影響區小,激光處理后,工件變形小;
(3)能夠處理表面形狀復雜的工件,且容易實現自動化;
(4)改性效果比普通方法更顯著,速度快,效率高,成本低;
(5)通常只能處理一些薄板金屬,不適宜處理較厚的板材。
由于激光加熱速率極快,相變過程是在很大的過熱度下進行的,所以晶核的形核率很大。因加熱時間短,碳原子的擴散及晶粒的長大均受到限制,所以得到的奧氏體晶粒較小。冷卻速率也比使用任何淬火劑都快,因而易得到隱針或細針馬氏體組織。通過對組織類型的觀察,可將激光束處理后的鋼表面進行區分,低碳鋼可分為兩層:外層是完全淬火區,組織是隱針馬氏體;內層是不完全淬火區,保留有鐵素體。中碳鋼可分為四層:外層是白亮的隱針馬氏體,硬度達800HV,比一般淬火硬度高出100以上;第二層是隱針馬氏體加少量屈氏體,硬度稍低;第三層是隱針馬氏體加網狀屈氏體,再加少量鐵素體;第四層是隱針馬氏體和完整的鐵素體網。高碳鋼也可分為兩層:外層是隱針馬氏體;內層是隱針馬氏體加未溶碳化物。鑄鐵大致可分為三層:表層是熔化一凝固所得的樹枝狀結晶,此區隨掃描速度的增大而減小;第二層是隱針馬氏體加少量殘留的石墨及磷共晶組織;第三層是較低溫度下形成的馬氏體。
(1)激光相變硬化
激光相變硬化又稱激光淬火,是指以高能密度的激光束照射工件表面,使得需要硬化的部位瞬間吸收大量光能,并將其立即轉化為熱能,從而使激光作用區的溫度急劇上升,組織類型迅速轉變為奧氏體,經快速冷卻后,獲得極細小馬氏體和其他組織,其特點如下:
①材料表面可高速加熱和高速自冷。加熱速度可達10?~10?℃/s,冷卻速度可10?℃/s,這就有利于提高掃描速度及生產效率。
②激光淬火處理后的工件表面硬度高,一般來說比常規淬火硬度高5%~20%,處理結束后可獲得極細的硬化層組織。
③由于激光加熱速度快,因而熱影響區小,淬火應力及變形小。一般認為激光淬火處理幾乎不產生變形,而且相變硬化可以使表面產生大于4000MPa的壓應力,有助于提高零件的疲勞強度;但厚度小于5mm的零件其變形仍不可忽視。
④可以對形狀復雜的零件以及不能用其他常規方法處理的零件進行局部硬化處理,如具有溝槽的零件。
⑤激光淬火工藝周期短,生產效率高,工藝過程易實現計算機控制,自動化程度高,可納入生產流水線。
⑥激光淬火依靠自身的導熱性,由表及里的傳導自冷,無需冷卻介質,對環境無
污染。
(2)激光表面熔敷激光表面熔敷是在激光束作用下將合金粉末或陶瓷粉末與基體表面迅速加熱并熔化,當光束移開后自冷卻的一種表面強化方法。其特點如下:
①冷卻速度快(高達10?℃/s),組織具有快速凝固的典型特征;
②熱輸入和畸變較小,涂層稀釋率低(一般小于5%),與基體呈冶金結合;
③粉末選擇幾乎沒有任何限制,特別是低熔點金屬表面熔敷高熔點合金;
④能進行選區熔敷,材料消耗少,具有卓越的性能價格比;
⑤光束瞄準可以使難以接近的區域熔敷;
⑥工藝過程易于實現自動化。
(3)激光表面合金化
激光表面合金化是指在高能量激光束的照射下,使基體材料表面薄層與外加合金元素同時快速熔化、混合,形成厚度為10~1000μm的表面熔化層,熔化層在凝固時獲得的冷卻速度可達10?~10?℃/s,相當于急冷淬火技術所能達到的冷卻速度,又由于熔化層液體內存在著擴散作用和表面張力效應等物理現象,可使材料表面在很短時間(50μs~2ms)內形成具有預定深度及化學成分的表面合金層。
激光表面合金化工藝的最大特點是僅在熔化區和很小的影響區內發生成分、組織和性能的變化,對基體的熱效應可減少到最低限度,引起的變形也極小。該種工藝既可滿足表面的使用需要,同時又不犧牲結構的整體特性。
熔化深度由激光功率和照射時間來控制。在基體金屬表面可形成厚度為0.01~2mm的合金層。由于冷卻速度高,使偏析最小,并顯著細化晶粒。
(4)激光沖擊硬化
當短脈沖(幾十納秒)、高峰值、高功率密度(>10W/cm²)的激光束輻射金屬靶材時,金屬表面吸收層吸收激光能量并發生爆炸性地汽化蒸發,產生高溫(>10000K)、高壓(>1GPa)的等離子體,該等離子體受到約束層的約束時,將產生高強度壓力沖擊波,并作用于金屬表面,隨后向金屬內部傳播。當沖擊波的峰值壓力超過被處理材料的動態屈服強度時,材料表層就產生應變硬化現象,其內部將殘留很大的壓應力。這種新型的表面強化技術就是激光沖擊強化,由于其強化原理類似噴丸,因此也稱作激光噴丸。
激光沖擊強化具有應變影響層深,沖擊區域和壓力可控,對表面粗糙度影響小,易于自動化等特點。與噴丸強化相比,激光沖擊處理獲得的殘余壓應力層可達1mm,是噴丸強化的2~5倍。而擠壓、撞擊強化等強化技術只能對平面或規則回轉面進行。另外,激光沖擊強化能很好地保持強化位置的表面粗糙度和尺寸精度。
(5)激光表面非晶化
激光表面非晶化是利用激光熔池所具有的超高速冷卻條件,使某些成分的合金表面形成具有特殊性能的非晶層。與其他非晶化方法比較,激光非晶化可以在工件表面大面積地形成非晶層,而且形成非晶的成分也可擴大。
利用高能電子束轟擊材料表面,使其溫度升高并發生成分、組織結構的變化,從而達到所需性能的工藝方法,稱為電子束表面處理。它是以電場中高速移動的電子作為載能體,電子束的能量密度最高可達10?W/cm²。電子束表面處理的特點是:由于電子束具有更高的能量密度,所以加熱的尺寸范圍和深度更大;設備投資較低,操作較簡單(無須像激光束處理那樣在處理前進行“黑化”);因需真空條件,故零件的尺寸受到限制。
電子束就是高能電子流,這些電子是由陰極燈絲產生。帶負電荷的電子束高速飛向高電位正極的過程中,經過加速器加速,又通過電磁透鏡聚焦,電子束的功率得到提高,再經二次聚焦,其能量密度高度集中,并以極高的速度沖向工件表面極小的面積上,電子束攜帶的動能大部分轉化為熱能,所以材料表面的被沖擊部分在幾分之一微秒內,溫度將會升至幾千攝氏度,使材料瞬間熔化甚至氣化。
電子束表面處理技術的設備由以下五個系統組成:
①電子槍系統發射高速電子流;
②真空系統保證系統所需的真空度;
③控制系統控制電子束的大小、形狀、和方向;
④電流系統供給高低壓穩壓電流;
⑤傳動系統控制工作臺移動。
①將工件置于真空室中加熱,沒有氧化、脫碳,表面相變強化無需冷卻介質,依靠基體自身的冷卻行為,可實現“綠色表面強化”。
②電子束的能量轉換率約為80%~90%,能量集中,熱效率高,可實現局部相變強化和表面合金化。
③由于熱量集中,熱作用點小,在加熱時形成的熱應力小,又由于硬化層淺,組織應力小,表面相變強化畸變小。
④電子束表面處理設備一次性投入比激光少(約為激光的1/3),電子束使用成本也只有激光的一半。
⑤設備結構簡單,電子束靠磁偏轉動、掃描,不需要工件轉動、移動和光傳輸機構。
⑥電子束表面處理的適用范圍寬,可適用于各種鋼材、鑄鐵和其他材料的表面處理,而且也適用于形狀復雜的零件。
⑦電子束易激發X射線,使用過程中應注意保護。
電子束表面處理技術的分類如圖11所示。
圖11 電子束表面處理技術的分類
(1)電子束表面相變強化
對于有馬氏體相變過程的金屬,其工藝過程的關鍵是參數控制:電子束斑平均功率密度在10?~10?W/cm²,加熱速度為10³~10?℃/s,冷卻速度可達10?~10?℃/s。
電子束快速熔凝造成過飽和固溶強化,并形成超細馬氏體,硬度增大,表面呈殘余壓應力,從而提高了材料的耐磨性。
(2)電子束表面重熔處理
電子束重熔可使合金的化學元素重新分布,降低某些元素的顯微偏析程度,從而改善工件表面的性能。由于電子束重熔是在真空條件下進行的,有利于防止表面的氧化,因此電子束重熔處理特別適用于化學活性高的鎂合金、鋁合金等的表面處理。
(3)電子束表面合金化
一般選擇W、Ti、B、Mo等元素及其碳化物作為合金元素提高材料耐磨性;選擇Ni、Cr等元素可提高材料的抗腐蝕性能;而適當添加Co、Ni、Si等元素能改善合金化效果。
(4)電子束表面非晶化處理
將電子束的平均功率密度提高到10?~10?W/cm²,作用時間縮短至10-?s左右,使金屬在基體與熔化的表層之間產生很大的溫度梯度,在停止電子束照射后,金屬表面快速冷卻速率(10?~10?s-¹)遠遠超過常規制取非晶的冷卻速率(10³~10?s-¹),所獲非晶的組織形態致密,抗疲勞及抗腐蝕性能優良。
(5)電子束表面薄層退火
當電子束作為表面薄層退火的熱源使用時,所需要的功率密度要較上述方法低很多,以此降低材料的冷卻速度。對于金屬材料,此法主要應用于薄帶的表面處理。另外,電子束退火還成功地應用于半導體材料上。
模具鋼經電子束表面強化后,材料的最表層發生熔化,表面重熔層的厚度達到10μm左右,熔化造成其表層顯微硬度降低;表面碳化物顆粒溶解,基體固溶鉻和能量增加,造成過飽和固溶強化,并形成超細化馬氏體,試樣顯微硬度從955.2HK提高到1169HK,相對耐磨性提高了5.63倍、轟擊次數越多,影響區越深,顯微硬度提高幅度越大。
電火花表面處理技術的基本原理是儲能電源通過電極,以10-2000Hz的頻率在電極與零部件之間產生火花放電,并將作為電極的導電材料熔滲到工件表面,形成合金化表面強化層,改善工件表面的物理及化學性能。
電火花表面強化層的性能主要取決于基體材料本身和電極材料,通常用的電極材料有TiC、WC、ZrC、NbC、Cr?C?、硬質合金等。
圖12是電火花表面處理技術過程示意圖。當電極與工件之間的距離較大時,電源經電阻R對電容充電,電極在振動器的帶動下向工件靠近,如圖12(a)所示;當電極與工件之間的間隙接近到某個距離時,間隙中的空氣在強電場的作用下電離,產生火花放電,如圖12(b)所示;當電極和工件在發生放電部分的金屬局部熔化甚至汽化時,電極繼續接近工件并與工件接觸,這時火花放電停止,在接觸點流過短路電流,使該處繼續加熱,由于電極以適當壓力壓向工件,使熔化的材料相互粘接、擴散而形成合金或者新的化合物,如圖12(c)所示;電極在振蕩器的作用下離開工件,如圖12(d)所示。
圖12 電火花表面強化過程示意圖
(1)高溫高壓下的物理化學冶金過程。電火花放電所產生的高溫使電極材料和工件表面的基體材料局部熔化,氣體受熱膨脹產生的壓力以及稍后電極機械沖擊力的作用,使電極材料與基體材料熔合并發生物理和化學的相互作用,電離氣體元素如氮、氧等的作用,使基體表面產生特殊的合金。
(2)高溫擴散過程。擴散過程既發生在熔化區內,也發生在液-固相界上。由于擴散時間非常短,液相元素向基體的擴散量有限的,擴散層很淺,但是基體與合金層也能達到較好的冶金結合。
(3)快速相變過程。由于熱影響區的急劇升溫和快速冷卻,使工件基體熔化區附近部位經歷了一次奧氏體化和馬氏體化轉變,細化了晶粒,提高了硬度,并產生了殘余壓應力,對提高疲勞強度有利。
(1)優點
①設備簡單,造價低;
②強化層與基體的結合非常牢固;
③工件內部不升溫或者升溫很低,無組織和性能變化,工件不會退火和變形;
④能耗低,材料消耗少;
⑤對處理對象無大小限制,尤其適合大工件局部處理;
⑥表面強化效果顯著;
⑦可用來修復磨損超差的工件;
⑧操作簡單,容易掌握。
(2)缺點
①表面強化層較淺,一般深度僅0.02~0.5mm;
②表面粗糙度不會很低;
③小孔、窄槽難處理,表層強化層均勻性連續性較差。
電鍍是通過電解的方法在固體表面上獲得金屬沉積層的過程。其目的在于改變固體材料的表面特性,改善外觀,提高耐蝕性、抗磨性、減摩性能:制成特定成分和性能的金屬覆蓋層,提供特殊的電、磁、光、熱等表面特性和其他物理性能等。目前電鍍已經應用于機械、交通、能源、航空、船舶、儀表行業以及輕工日用品的生產制造中。
電鍍原理:將待鍍工件和直流電源的負極相連,將電鍍金屬和直流電源的正極相連,然后把它們一起放入盛有含欲鍍覆的金屬離子鹽溶液的鍍槽中,當工件和電鍍金屬間通入直流電流時,鍍液中的金屬離子將移向陰極,在陰極金屬離子得到電子產生還原反應,沉積在工件表面上。作為陽極的電鍍金屬將逐漸溶解,不斷補充鍍液中的金屬離子,使電鍍繼續下去,電鍍原理如圖13所示。
圖13 電鍍原理圖
電鍍的目的:獲得不同于基體材料,且具有特殊性能的表面層,提高表面的耐腐蝕性及耐磨性。
鍍層厚度一般為幾微米到幾十微米。
電鍍的特點:電鍍工藝設備較簡單,操作條件易于控制,鍍層材料廣泛,成本較低,因而在工業中廣泛應用,是材料表面處理的重要方法。
鍍層種類很多,按使用性能分類如下:
(1)防護性鍍層:電鍍金屬有鋅、鎘、錫及其合金,如鋅鎳、鋅鐵、鋅錫、鋅鈦、錫鎳等,主要用于鋼鐵件在大氣和其他環境中的防銹及防腐蝕。
(2)防護-裝飾性鍍層:這類鍍層除要求有較高的耐蝕性外,對表面裝飾性也有較高要求如汽車、摩托車、機床、日用品等表面電鍍銅鎳鉻、鎳鉻、雙層鎳鉻、三層鎳鉻和鎳鍍層上鍍仿金等。例如Cu-Ni-Cr鍍層等,既有裝飾性,亦有防護性。
(3)裝飾性鍍層:例如Au及Cu-Zn仿金鍍層、黑鉻、黑鎳鍍層等。
(4)耐磨和減磨鍍層:例如硬鉻鍍層、松孔鍍層、Ni-Sic鍍層,Ni-石墨鍍層、Ni-PTFE復合鍍層等。
(5)電性能鍍層:例如Au鍍層、Ag鍍層等,既有高的導電率,又可防氧化,可避免增加接觸電阻。
(6)磁性能鍍層:例如軟磁性能鍍層有Ni-Fe鍍層、Fe-Co鍍層;硬磁性能有Co-P鍍層、Co-Ni鍍層、Co-Ni-P鍍層等。
(7)可焊性鍍層:例如Sn-Pb鍍層、Cu鍍層、Sn鍍層、Ag鍍層等。可改善可焊性,在電子工業中應用廣泛。
(8)耐熱鍍層:例如Ni-W鍍層、Ni鍍層、Cr鍍層等,熔點高,耐高溫。
(9)修復用鍍層:一些造價較高的易磨損件,或加工超差件,采用電鍍修復尺寸,可節約成本,延長使用壽命。例如可電鍍Ni、Cr、Fe層進行修復。
若按鍍層與基體金屬之間的電化學性質可將其分為:陽極性鍍層和陰極性鍍層。當鍍層相對于基體金屬的電位為負時,鍍層是陽極,稱為陽極性鍍層,如鋼上的鍍鋅層;當鍍層相對于基體金屬的電位為正時,鍍層呈陰極,稱為陰極性鍍層,如鋼上的鍍鎳層、鍍錫層等。
若按鍍層的組合形式分,鍍層可分為:單層鍍層,如Zn或Cu層;多層金屬鍍層,例如Cu-Sn/Cr鍍層、Cu/Ni/Cr鍍層等;復合鍍層,如Ni-Al?O?鍍層、Co-SiC鍍層等。
若按鍍層成分分類,可分為單一金屬鍍層、合金鍍層及復合鍍層。
電鍍工藝過程一般包括鍍前預處理、電鍍及鍍后處理三個階段:
(1)鍍前預處理
鍍前預處理是為了得到干凈的金屬表面,為最后獲得高質量鍍層做準備,主要進行脫脂、去銹蝕、去灰塵等工作。步驟如下:
1)使表面粗糙度達到一定要求,可通過表面磨光、拋光等工藝方法來實現。
2)去油脫脂可采用溶劑溶解以及化學、電化學等方法來實現。
3)除銹。可用機械、酸洗以及電化學方法除銹。
4)活化處理。一般在弱酸中浸蝕一定時間進行鍍前活化處理
(2)鍍后處理
1)鈍化處理。鈍化處理是指在特定的溶液中進行化學處理,在鍍層上形成堅實細密穩定性高的薄膜表面的處理方法。鈍化使鍍層耐蝕性大大提高,并增加表面光澤和提高抗污染能力。這種方法用途很廣,鍍鋅、鍍銅及鍍銀等后,都可進行鈍化處理。2)除氫處理。有些金屬如鋅,在電沉積過程中,除自身沉積外,還會析出,這部分氫滲入鍍層中,使鍍件產生脆性,甚至斷裂,所以鍍后應進行除氫處理,防止氫脆。
主鹽沉積金屬的鹽類主要有:單鹽,如硫酸銅、硫酸鎳等;絡鹽,如鋅酸鈉、氰鋅酸鈉等。
配合劑與沉積金屬離子形成配合物,其主要作用是改變鍍液的電化學性質和控制金屬離子沉積的電極過程,配合劑是鍍液的重要成分,對鍍層質量有很大影響。常用配合劑有氰化物、氫氧化物、焦磷酸鹽、酒石酸鹽、氨三乙酸、檸檬酸等。
導電鹽其作用是提高鍍液的導電能力,降低槽端電壓提高工藝電流密度。例如鍍鎳液中加入Na?SO?。導電鹽不參加電極反應,酸或堿類也可作為導電物質。
緩沖劑在弱酸或弱堿性鍍液中,pH值是重要的工藝參量。加入緩沖劑,使鍍液具有自行調節pH值能力,以便在施鍍過程中保持pH值穩定。緩沖劑要有足夠量才能有效控制酸堿平衡,一般加入30~40g/L,例如氯化鉀鍍鋅溶液中的硼酸。
陽極活化劑在電鍍過程中金屬離子被不斷消耗,多數鍍液依靠可溶性陽極來補充,從而使金屬的陰極析出量與陽極溶解量相等,保持鍍液成分平衡。加入活性劑能維持陽極活性狀態,不會發生鈍化,保持正常溶解反應。例如鍍鎳液中必須加入Cl-,以防止鎳陽極鈍化。
表1 鍍鉻液配方及工藝條件
表2 鍍鎳液的配方及工藝條件
特殊添加劑為改善鍍液性能和提高鍍層質量,常需加入某種特殊添加劑。其加入量較少,一般只有幾克每升,但效果顯著。這類添加劑種類繁多,按其作用可分為:
(1)光亮劑—可提高鍍層的光亮度。
(2)晶粒細化劑—能改變鍍層的結晶狀況,細化晶粒,使鍍層致密。例如鋅酸鹽鍍鋅液中,添加環氧氯丙烷與胺類的縮合物之類的添加劑,鍍層就可從海綿狀變為致密而光亮。
(3)整平劑—可改善鍍液微觀分散能力,使基體顯微粗糙表面變平整。
(4)潤濕劑—可以降低金屬與溶液的界面張力,使鍍層與基體更好地附著,減少針孔。
(5)應力消除劑—可降低鍍層應力。
(6)鍍層硬化劑—可提高鍍層硬度。
(7)掩蔽劑—可消除微量雜質的影響。
電鍍過程的基本步驟包括:液相傳質、電化學還原、電結晶。
(1)鍍液:主鹽溶度、配離子、附加鹽;pH值;析氫;電流參數:電流密度、電流波形;添加劑;溫度;攪拌;基體金屬:性質、表面加工狀態;前處理。
(2)電鍍方式:掛鍍。不能從水溶液中單獨電鍍的W、Mo、Ti、V等金屬可與鐵族元素(Fe,Co,Ni)共沉積形成合金;從而獲得單一金屬得不到的外觀。
(3)沉積合金的條件:
①兩種金屬中至少有一種金屬能從其鹽的水溶液中沉積出來。
②共沉積的兩種金屬的沉積電位必須十分接近。
化學鍍是指在沒有外電流通過的情況下,利用化學方法使溶液中的金屬離子還原為金屬,并沉積在基體表面,形成鍍層的一種表面加工方法。
化學鍍時,還原金屬離子所需的電子是通過化學反應直接在溶液中產生。完成過程有以下三種方式。
利用被鍍金屬M?(如Fe)比沉積金屬M?(如Cu)的電位更負,將沉積金屬離子從溶液中置換在工件表面上,工程中稱這種方式為浸鍍。當金屬M?完全被金屬M?覆蓋時,則沉積停止,所以鍍層很薄。鐵浸鍍銅,銅浸汞,鋁鍍鋅就是這種置換沉積。浸鍍難以獲得實用性鍍層,常作為其他鍍種的輔助工藝。
除了被鍍金屬M?和沉積金屬M?外,還有第三種金屬M?。在含有M?離子的溶液中,將M?-M?兩金屬連接,電子從電位高的M?流向電位低的M?,使M?還原沉積在M?上。當接觸金屬M?也完全被M?覆蓋后,沉積停止。在沒有自催化性的功能材料上進行化學鍍鎳時,常用接觸沉積引發鎳沉積起鍍。
由還原劑被氧化而釋放的自由電子,將金屬離子還原為金屬原子的過程稱為還原沉積。
其反應方程式如下:
還原劑氧化
Rn+ → 2e- + R(n + 2)+
金屬離子還原
M2+ + 2e- → M
工程上所講的化學鍍也主要是指這種還原沉積化學鍍。
化學鍍的條件是以下幾個方面:
(1)鍍液中還原劑的還原電位要顯著低于沉積金屬的電位,使金屬有可能在基材上被還原而沉積出來。
(2)配好的鍍液不產生自發分解,當與催化表面接觸時,才發生金屬沉積過程。
(3)調節溶液的pH值、溫度時,可以控制金屬的還原速率,從而調節鍍覆速率。
(4)被還原析出的金屬也具有催化活性,這樣氧化還原沉積過程才能持續進行,鍍層才能連續增厚。
(5)反應生成物不妨礙鍍覆過程的正常進行,即溶液有足夠的使用壽命。
化學鍍鍍覆的金屬及合金種類較多,如Ni-P、Ni-B、Cu、Ag、Pd、Sn、In、Pt、Cr及多種Co基合金等,但應用最廣的是化學鍍鎳和化學鍍銅。化學鍍層一般具有良好的耐蝕性、耐磨性、釬焊性及其他特殊的電學或磁學等性能,所以該種表面處理工藝能很好的完善材料的表面性能。
熱噴涂技術、熱噴焊技術都是利用熱能(如氧-乙炔火焰、電弧、等離子火焰等)將具有特殊性能的涂層材料熔化后涂敷在工件上形成涂層的技術。具有可以制備比較厚的涂層(0.1~10mm)的特點,主要應用在制造復合層零件修復。
(1)熱噴涂技術原理與特點
采用各種熱源使涂層材料加熱熔化或半熔化,然后用高速氣體使涂層材料分散細化并高速撞擊到基體表面,從而形成涂層的工藝過程,如圖14所示。
圖14 熱噴涂的基本過程示意圖
熱噴涂過程主要包括:噴涂材料的熔化;噴涂材料的霧化;噴涂材料的飛行;粒子的沖擊、凝固。
(2) 涂層材料
熱噴涂對涂層材料有一定的要求,需滿足的條件:有較寬的液相區,在噴涂溫度下不易分解或揮發;熱穩定性好;使用性能好;潤濕性好;固態流動性好(粉末);熱膨脹系數合適。涂層材料按照噴涂材料的形狀可分為線材和粉末。
(3) 熱噴涂涂層的結合機理
①機械結合:熔融態的粒子撞擊到基材表面后鋪展成扁平狀的液態薄層,嵌合在起伏不平的表面,并形成機械結合。
②冶金結合:涂層與基體表面出現擴散和焊合,稱為冶金結合。
③物理結合:當高速運動的熔融粒子撞擊基體表面后,若界面兩側的距離在原子晶格常數范圍內時,粒子之間依靠范德華力結合在一起。
(4) 涂層的形成過程
①噴涂材料被加熱到熔融狀態;
②噴涂材料被霧化成微小熔滴并高速撞擊基體表面,撞擊基體的顆粒動能越大和沖擊變形越大,形成的涂層結合越好;
③熔融的高速粒子在沖擊基材表面后發生變形,冷凝后形成涂層。
涂層的形成過程如圖15所示。
圖15 涂層形成過程示意圖
涂層結構是由大小不一的扁平顆粒、未熔化的球形顆粒、夾雜和孔隙組成。孔隙存在的原因:未熔化顆粒的低沖擊動能;噴涂角度不同時造成的遮蔽效應;凝固收縮和應力釋放效應。適當的孔隙可以儲存潤滑劑、提高涂層的隔熱性能、減小內應力以及提高涂層的抗熱震性等,但是過多的孔隙將會破壞涂層的耐腐蝕性能、增加涂層表面的粗糙度,從而降低涂層的結合強度、硬度、耐磨性,所以在涂層的制備過程中應嚴格控制孔隙的數量。
(1)熱噴焊技術的原理及特點
熱噴焊技術是采用熱源將涂層材料在基體表面重新熔化或部分熔化,并凝結于基體表面,形成與基體具有冶金結合的表面層的一種表面冶金強化方法,也稱為熔結。相比于其他表面處理工藝,熱噴焊所得的組織致密,冶金缺陷很少,與基體結合強度高,但是所用材料的選擇范圍窄,基材的變形比熱噴涂大得多,熱噴焊層的成分與原始成分有一定差別等局限性。
(2)熱噴焊技術的分類熱噴焊技術主要有火焰噴焊、等離子噴焊等。
①火焰噴焊:先在基體表面噴粉,再對涂層用火焰直接加熱,使涂層在基體表面重新熔化,基體的表面完全潤濕,界面有相互的元素擴散,形成牢固的冶金結合。
火焰噴焊特點:設備簡單;工藝簡單;涂層與基體的結合強度高;涂層的耐沖蝕磨損性能好。
②等離子噴焊:以等離子弧作為熱源加熱基體,使其表面形成熔池,同時將噴焊粉末材料送入等離子弧中,粉末在弧柱中得到預熱,呈熔化或半熔化狀態,被焰流噴射至熔池后,充分熔化并排出氣體和熔渣,噴槍移開后合金熔池凝固,最終形成噴焊層。
等離子噴焊的特點:生產效率高;可噴焊難熔材料、稀釋率低、工藝穩定性好、易實現自動化、噴焊層平整光滑、成分及組織均勻,涂層厚度更大且試驗過程可精確控制。
(3)熱噴焊技術與熱噴涂技術的區別
①工件表面溫度:噴涂時工件表面溫度<250℃;噴焊要>900℃。
②結合狀態:噴涂層以機械結合為主;噴焊層是冶金結合。
③粉末材料:噴焊用自熔性合金粉末,噴涂粉末不受限制。
④涂層結構:噴涂層有孔隙,噴焊層均勻致密無孔隙。
⑤承載能力:噴焊層可承受沖擊載荷和較高的接觸應力。
⑥稀釋率:噴焊層的稀釋率約5%~10%,噴涂層的稀釋率幾乎為零。
化學轉化膜技術就是通過化學或電化學手段,使金屬表面形成穩定的化合物膜層的工藝過程。
化學轉化膜技術,主要用于工件的防腐和表面裝飾,也可用于提高工件的耐磨性能等方面。它是利用某種金屬與某種特定的腐蝕液相接觸,在一定條件下兩者發生化學反應,由于濃差極化作用和陰、陽極極化作用等,在金屬表面上形成一層附著力良好的、難溶的腐蝕生成物膜層。這些膜層,能保護基體金屬不受水和其他腐蝕介質的影響,也能提高對有機涂膜的附著性和耐老化性。在生產中,采用的轉化膜技術主要有和磷化處理和氧化處理。
磷化是將鋼鐵材料放入磷酸鹽的溶液中,獲得一層不溶于水的磷酸鹽膜的工藝過程。
鋼鐵材料磷化處理工藝過程如下:化學除油→熱水洗→冷水洗→磷化處理→冷水洗→磷化后處理→冷水洗→去離子水洗→干燥。
磷化膜由磷酸鐵、磷化錳、磷酸鋅等組成,呈灰白或灰黑色的結晶。膜與基體金屬結合非常牢固,并具有較高的電阻率。與氧化膜相比,磷化膜有較高的抗腐蝕性,特別是在大氣、油質和苯介質中均有很好耐腐蝕性,但在酸、堿、氨水、海水及水蒸氣中的耐腐蝕性較差。
磷化處理的主要方法為浸漬法、噴淋法和浸噴組合法。根據溶液溫度不同,磷化又分為室溫磷化、中溫磷化和高溫磷化。
浸漬法適用于高溫、中溫和低溫磷化工藝,可處理任何形狀的工件,并可獲得不同厚度的磷化膜,且設備簡單,質量穩定。厚磷化膜主要用于工件的防腐處理和增強表面的減摩性。噴淋法適用于中溫和低溫磷化工藝,可以處理面積大的工件,如汽車殼體、電冰箱、洗衣機等大型工件作為油漆底層和冷變形加工等。這種方法處理時間短,成膜速度快,但只能獲得較薄和中等厚度的磷化膜。
(1)鋼鐵的氧化處理
鋼鐵的氧化處理也稱發藍,是將鋼鐵工件放入某些氧化性溶液中,使其表面形成厚度約為0.5~1.5μm致密而牢固的Fe3O4薄膜的工藝方法。發藍通常不影響零件的精密度,常用于工具、儀器的裝飾防護。它能提高工件表面的抗腐蝕能力,有利于消除工件的殘余應力,減少變形,還能使表面光澤美觀。氧化處理以堿性法應用最多。
鋼鐵的氧化處理所用溶液成分和工藝條件,可根據工件材料和性能要求確定。常用溶液由為500g/L的氫氧化鈉、200g/L的亞硝酸鈉和余量水組成,在溶液溫度為140℃左右時處理6~9min。
(2)鋁及鋁合金的氧化處理
①陽極氧化法
陽極氧化法是將工件置于電解液中,然后通電,得到硬度高、吸附力強的氧化膜的方法。常用的電解液有濃度為15%~20%的硫酸、3%~10%的鉻酸、2%~10%的草酸。陽極氧化膜可用熱水煮,使氧化膜變成含水氧化鋁,因體積膨脹而封閉。也可用重鉻酸鉀溶液處理而封閉,以阻止腐蝕性溶液通過氧化膜結晶間隙腐蝕基體。
②化學氧化法
化學氧化法是將工件放入弱堿或弱酸的溶液中,獲得與基體鋁結合牢固的氧化膜的方法。主要用于提高工件的抗腐蝕性和耐磨性,也用于鋁及鋁合金的表面裝飾,如建筑用的防銹鋁,標牌的裝飾膜等。
氣相沉積技術是指將含有沉積元素的氣相物質,通過物理或化學的方法沉積在材料表面形成薄膜的一種新型鍍膜技術。根據沉積過程的原理不同,氣相沉積技術可分為物理氣相沉積(PVD)和化學氣相沉積(CVD)兩大類。
物理氣相沉積(PVD)是指在真空條件下,用物理的方法,使材料汽化成原子、分子或電離成離子,并通過氣相過程,在材料表面沉積一層薄膜的技術。物理沉積技術主要包括真空蒸鍍、濺射鍍和離子鍍3種基本方法。
真空蒸鍍是蒸發成膜材料使其汽化或升華沉積到工件表面形成薄膜的方法。根據蒸鍍材料熔點的不同,其加熱方式有電阻加熱、電子束加熱、激光加熱等多種。真空蒸鍍的特點是設備、工藝及操作簡單,但因汽化粒子動能低,鍍層與基體結合力較弱,鍍層較疏松,因而耐沖擊、耐磨損性能不高。
濺射鍍是在真空下通過輝光放電來電離氬氣,產生的氬離子在電場作用下加速轟擊陰極,被濺射下來的粒子沉積到工件表面成膜的方法;其優點是氣化粒子動能大、適用材料廣泛(包括基體材料和鍍膜材料)、均鍍能力好,但沉積速度慢、設備昂貴。
離子鍍是在真空下利用氣體放電技術,將蒸發的原子部分電離成離子,與同時產生的大量高能中性粒子一起沉積到工件表面成膜的方法。其特點是鍍層質量高、附著力強、均鍍能力好、沉積速度快,但存在設備復雜、昂貴等缺點。
物理氣相沉積具有適用的基體材料和膜層材料廣泛;工藝簡單、省材料、無污染;獲得的膜層膜基附著力強、膜層厚度均勻、致密、針孔少等優點。已廣泛應用于機械、航空航天、電子、光學和輕工業等領域制備耐磨、耐蝕、耐熱、導電、絕緣、光學、磁性、壓電、滑潤超導等薄膜。
化學氣相沉積(CVD)是指在一定溫度下,混合氣體與基體表面相互作用而在基體表面形成金屬或化合物薄膜的方法。
化學氣相沉積的特點是:沉積物種類多,可分為沉積金屬、半導體元素、碳化物、氮化物、硼化物等;并能在較大范圍內控制膜的組成及晶型;能均勻涂敷幾何形狀復雜的零件;沉積速度快,膜層致密,與基體結合牢固;易于實現大批量生產。
由于化學氣相沉積膜層具有良好的耐磨性、耐蝕性、耐熱性及電學、光學等特殊性能,已被廣泛應用于機械制造、航空航天、交通運輸、煤化工等工業領域。
免責聲明:本網站所轉載的文字、圖片與視頻資料版權歸原創作者所有,如果涉及侵權,請第一時間聯系本網刪除。
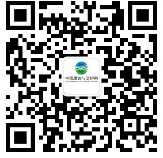
官方微信
《腐蝕與防護網電子期刊》征訂啟事
- 投稿聯系:編輯部
- 電話:010-62316606
- 郵箱:fsfhzy666@163.com
- 腐蝕與防護網官方QQ群:140808414