摘要 鋼材由于具有高強度和耐熱性等優異性能而廣泛應用于各種零構件,在服役過程中通常面臨較為嚴重的腐蝕問題。CO2腐蝕是鋼材應用領域中較為常見的一種腐蝕失效方式。通常,CO2對鋼的腐蝕行為表現為其溶于水后產生的碳酸腐蝕,但在高溫環境中,CO2可直接使鋼表面氧化,同時伴隨滲碳現象發生,鋼的力學性能與耐腐蝕性能均會因此大幅下降。然而,目前關于鋼在高溫CO2環境中的腐蝕行為研究缺乏相關系統總結。綜述有關高溫CO2環境下鋼的腐蝕機理,總結高溫CO2環境中溫度、壓力以及環境中存在的其他雜質氣體對腐蝕方式及機理的影響規律,歸納已有的高溫CO2氧化與滲碳腐蝕模型的發展狀況,概述目前關于抗高溫CO2腐蝕的鋼材涂層類型及其防護效果。研究表明,由于含Cr鋼在高溫CO2環境中形成的Cr2O3層相較于Fe氧化物層更加致密,Cr元素的存在通常有利于鋼的耐腐蝕性能。而環境中,溫度與壓力的升高以及雜質氣體的存在往往會加重鋼的CO2腐蝕,但這些因素的影響規律會隨著鋼的種類及服役環境的變化而變化。目前關于鋼的CO2腐蝕模型主要為單一的高溫氧化模型或者滲碳模型,可預測氧化物層厚度或滲碳深度,但無法準確預測同時發生氧化和滲碳行為的鋼的腐蝕壽命。綜述相關研究現狀不僅能指出現有研究的不足及未來研究的展開方向,還可為高溫環境中鋼材抗CO2腐蝕防護措施的選擇及其長周期安全服務壽命評價提供全面理論依據。
前言 鋼材由于其高強度、耐熱性、相對成本較低等特點廣泛應用于油氣采集、CO2捕捉運輸管道以及超臨界CO2火電機組等諸多部件。然而,這些鋼材部件通常是在CO2環境中服役,導致其使用壽命容易因CO2腐蝕而降低,特別是在高溫下,CO2可在無H2O等其他物質參與的情況下對鋼造成腐蝕。目前,有關高溫下鋼的CO2腐蝕的研究工作重點在于評估不同鋼種在不同CO2腐蝕環境下的腐蝕動力學及機理,這些研究工作比較零散,缺乏系統總結。 高溫環境下,CO2對鋼的腐蝕表現為氧化與滲碳作用。具體而言,CO2會與鋼表面的Fe、Cr元素反應生成Cr2O3 、Fe3O4、(Fe, Cr)2O3等氧化物,這些氧化產物層通常具備對鋼的保護作用。而由于Cr2O3對于氧化與滲碳防護性能優于Fe3O4,不同鋼種的Cr元素含量對其耐腐蝕性能至關重要。伴隨氧化過程發生的滲碳作用會同時降低鋼的耐腐蝕性能與力學性能:碳化物的形成會消耗參與形成保護性氧化層的合金元素(如Cr元素)以及氧化層與金屬基體界面處存在的無定形碳累積層會導致氧化層與基體的附著力降低,進而導致保護性氧化層發生剝落;滲碳后產生的碳化物會降低鋼的延展性,從而削弱鋼的抗疲勞與抗蠕變能力。此外,CO2對鋼的腐蝕作用受到服役環境中的諸多因素影響。其中,溫度對腐蝕的影響在于能改變氧化速率或氧化層成分,而壓力則主要影響滲碳作用,溫度與壓力的提升通常會促進CO2對鋼的腐蝕作用。當腐蝕環境中存在其他雜質氣體,如H2O、O2,鋼的CO2腐蝕行為會不同于純CO2環境下,且它們的影響規律會隨著腐蝕環境條件和鋼種的變化而變化 。 準確評估高溫CO2環境下鋼的腐蝕速率對設備的設計與維護十分重要:預設較低的腐蝕速率可能導致相關部件在服役過程中突然失效以及設備損壞,而過高的腐蝕速率的評估可能導致不必要的成本。然而,目前關于高溫下金屬材料CO2腐蝕行為的預測模型的研究進展較慢。部分研究人員分別針對氧化與滲碳作用進行研究,實現了對一定腐蝕時間的氧化物厚度或滲碳深度、濃度的預測計算,但尚未有研究考慮氧化與滲碳的耦合作用,從而無法準確預測鋼的CO2腐蝕壽命。因此,高溫下鋼的CO2腐蝕預測模型亟待進一步系統研究。同時,由于高溫下鋼在CO2環境中的耐腐蝕性低于Ni基合金等材料,部分研究者試圖通過優化鋼的制備工藝或對鋼材進行表面處理等方式提高其耐蝕性。涂層被認為是提高鋼的耐蝕性而不顯著降低其機械性能的一種經濟有效的解決方案,因此大量科研人員成功采用可提高材料耐腐蝕性能的 Ni、Al、Cr等金屬元素為主要成分制備了一系列涂層,有效提高了鋼在高溫環境下的抗氧化與滲碳性能。 鑒于以上研究背景,本文綜述了高溫下鋼的CO2氧化滲碳腐蝕機理,闡述了腐蝕環境中多種因素包括溫度、壓力及其他雜質氣體對鋼的CO2腐蝕的影響規律,歸納了目前已有CO2腐蝕模型的發展狀況及應用背景,總結了目前關于抗CO2腐蝕的鋼材涂層類型及其防護效果,以期為高溫環境中鋼材的抗CO2腐蝕防護措施的選擇及其長周期安全服務壽命評價提供全面理論依據。
2. CO2高溫氧化滲碳腐蝕機理
當服役溫度達到400℃及以上時,鋼在CO2環境下的腐蝕行為通常是由氧化滲碳導致的。具體而言,CO2首先會與鋼表面的Fe、Cr等金屬元素(N)反應生成金屬氧化物并釋放CO或C,而CO可進一步分解為C和CO2或O。這些反應過程所產生的C往往積聚在氧化層與基體界面,在高溫下可擴滲入鋼體內部,形成碳化物。氧化滲碳相關反應式如下:
在氧化滲碳作用下,鋼在高溫CO2環境中腐蝕后會由外到內形成多層氧化層以及滲碳區。其中氧化層的成分與結構會強烈受到鋼中Cr元素含量的影響,如圖1所示。一般而言,當Cr元素含量為9wt.%~12wt.%以及更低時,氧化層主要由較為疏松的Fe3O4 、Fe2O3等Fe氧化物外層、Fe3-xCrxO4等FeCr復合氧化物內層以及內部氧化區(Internaloxidation zone,IOZ)組成,如圖1a所示。然而,即使氧化物層的成分相同,鋼成分中Cr元素含量更高往往會導致內層的FeCr氧化物層中Cr元素濃度更高,有效減緩鋼基體中的Fe元素向外擴散,從而導致更低的氧化速率。當Cr元素含量大于17wt.%時,鋼的氧化產物以表面Cr2O3層為主,而在更高的腐蝕溫度或更長的腐蝕時間下,Cr2O3層部分區域會出現Fe氧化物或FeCr氧化物形核,如圖1b所示。表1總結了相近腐蝕條件下不同Cr元素含量對鋼氧化層的影響結果。對于滲碳層而言,碳往往與基體中的Cr元素反應產生Cr3C、Cr7C3和Cr23C6等碳化物,這一過程會阻礙Cr元素向外擴散,且這些脆性碳化物會使氧化層容易脫落,進而導致鋼的耐腐蝕性降低。此外,在疲勞或蠕變載荷下,碳的沉積與晶間碳化物的形成會成為裂紋的潛在來源。可見,Cr元素含量很大程度上決定了鋼在高溫CO2環境中的耐腐蝕性能:高Cr鋼所形成的Cr2O3層相較于Fe氧化物層更加致密,對氧化及滲碳作用的防護性更好。而鋼中的Mn、Si等其他元素是否對其耐腐蝕性能存在一定影響,有待進一步研究。 3. 影響CO2腐蝕的因素 通常,影響高溫CO2腐蝕的因素包括溫度、壓力以及服役環境中不可避免的H2O、O2等雜質氣體。其中,溫度和壓力是影響CO2腐蝕最重要的參數,通常高溫高壓會促進氧化與滲碳作用,而 H2O這些雜質氣體在較高溫下可主導CO2腐蝕進程。然而,這些因素對鋼的CO2腐蝕的影響規律并不確定,會隨著鋼的種類及服役環境的變化而變化。 3.1.溫度 當溫度低于400℃時,鋼與純凈的CO2很難發生反應,只有在其他雜質參與下才會發生腐蝕。而當溫度高于400℃時,純凈的CO2可直接腐蝕鋼,且升高溫度會促進腐蝕進程。例如,FURUKAWA等研究了400~600℃下12Cr鋼在壓力為20MPa的CO2環境中的腐蝕性能,發現盡管溫度增加會加劇12Cr鋼的氧化腐蝕程度,但是其表面氧化層結構變化甚微,主要由厚度為 50μm的Fe3O4外層、50μm左右厚的復合氧化物 (Fe1-x , Crx)2O3內層以及厚度小于10μm的IOZ組成。可見,對于12Cr鋼而言,溫度由400℃升高至600℃主要影響了鋼的氧化速率,并未使得鋼表面氧化層成分及結構發生明顯改變。但有研究表明,溫度對鋼的CO2腐蝕的影響規律會隨著鋼中Cr元素含量變化而變化。如ZHU等通過研究Cr元素含量為2.25wt.%的鐵素體鋼T22與Cr元素含量為8.63wt.%的鐵素體-馬氏體雙相鋼P92在550和600℃、15MPa下的CO2腐蝕行為,發現在不同溫度下兩種鋼的氧化層成分相似,均由外層Fe3O4和內層(Fe, Cr)3O4組成。不同的是,隨著溫度由550℃升高至600℃,具有更高Cr元素含量的P92鋼中,FeCr氧化物內層的Cr元素會抑制Fe離子的擴散速度,降低氧化速率,表現出更好的耐蝕性能。但隨著氧化時間的延長,P92鋼表面氧化層出現局部脫落,鋼被再次腐蝕氧化,所生成的氧化層仍由Fe3O4外層與(Fe, Cr)3O4內層組成。可見,對于主要氧化產物為Fe氧化物的鋼,溫度主要影響其腐蝕后的氧化層厚度,對其氧化層成分影響不大。而其中Cr元素含量相對較高的鋼材受溫度的影響較小,通常具備更低的腐蝕速率。同時值得注意的是,在更高的環境溫度下,氧化物與基體之間較大的熱膨脹系數差異會促進氧化層的脫落,進而導致鋼材被再次氧化,顯著增加其腐蝕程度。 對于高Cr(>17 wt.%)含量的鋼種而言,其被腐蝕后形成的氧化層以Cr2O3為主,溫度會顯著影響氧化層成分。例如,在550℃下,316不銹鋼的氧化腐蝕表面主要被較薄(<1μm)的單層富Cr氧化物覆蓋,但局部區域會存在5μm 左右厚的Fe氧化物,而在750℃下,316不銹鋼腐蝕程度明顯加重,但其腐蝕產物主要為3~5μm厚的Fe3O4層,且部分區域存在成分為Fe氧化物與FeCr復合氧化物的雙相結構形核。因此,盡管溫度對鋼腐蝕的影響主要在于溫度升高會加快鋼的氧化速率。但對于高Cr鋼而言,較高溫度下Fe3O4等Fe氧化物生長速度通常大于Cr2O3生長速度,其表面氧化物會由富Cr向富Fe轉變。YANG等對比研究了500~600℃下T91鋼與316鋼的CO2腐蝕行為,發現在相同腐蝕時間下,溫度升高會導致T91鋼氧化層厚度增加以及更多孔洞和裂紋等缺陷形成,但對其氧化層成分影響不大,如圖2所示。相比之下,316鋼在500℃腐蝕后的表面氧化產物為50~80nm厚的Cr2O3層,僅部分區域存在少量簇狀Fe氧化物,而316鋼在600℃下的腐蝕產物是由成分為Fe2O3與Fe3O4的外層和含Cr2O3的內層組成的約2μm厚的雙層結構。由于Fe2O3與Fe3O4等Fe氧化物層相較于Cr2O3層對基體防護作用較差,因此可根據鋼在不同溫度下的氧化行為決定其適用溫度范圍,并將鋼的成分與工作溫度作為參數納入腐蝕模型以便后續研究。
對于高溫CO2腐蝕過程中的滲碳行為而言,BRITTAN等發現P92鋼在450℃下滲碳深度超過 200μm,而550℃下滲碳深度約為100μm。對于此,BRITTAN等提出這是因為較高溫度下碳化物的析出與生長更快,從而導致碳元素難以擴散至更深位置。并且金屬與氧化物界面附近的碳密度較高、碳化物粗化更明顯,使得該區域容易萌生裂紋,進而導致P92鋼力學性能明顯下降。然而,由于溫度對于CO2腐蝕的影響主要體現在改變氧化速率與氧化成分,因此目前有關溫度對于滲碳行為的影響規律的相關報道較少,有待進一步展開。 3.2.壓力 (PCO2) 高溫腐蝕環境的壓力(PCO2)對鋼的CO2腐蝕也具有重要影響。通常,壓力增加會促進滲碳作用,對氧化作用的直接影響較小 。例如,PINT等對比了同一溫度不同壓力(0.1、30MPa)下鋼的CO2腐蝕行為,發現壓力的改變對于氧化增重以及氧化層的厚度幾乎沒有影響。相比之下,通過研究0.1、5和10MPa下CrMoV鋼的CO2腐蝕氧化行為,BIDABADI等發現,當環境壓力從0.1MPa增加到5MPa時,CrMoV鋼的氧化產物成分相似,外層均為Fe3O4,內層則為Fe3-xCrxO4與Fe2-xCrxO3。但5MPa條件下,其表面氧化物更加均勻致密,且碳沉積行為更加明顯,進而降低了氧化速率。當壓力10MPa時,CrMoV鋼的表面氧化層由外層的 Fe2O3與Fe3O4 、內層的碳單質及少量Fe3-xCrxO4和Fe2-xCrxO3組成。此外,三種壓力條件下CrMoV鋼的滲碳區均存在非晶態碳,而石墨則主要存在于5和10MPa下的滲碳區,且氧化層內積碳通過限制Fe元素向外擴散與氧化氣體向內輸運而降低氧化速率。可見,隨著壓力的提高,鋼的滲碳作用更加明顯,碳積累加強,有利于阻止進一步腐蝕。此外,在較低的壓力范圍內,CO2壓力提高可提供足夠的氧分壓,進而促進更具保護性與穩定性的氧化物生長 。然而,其他研究中卻發現了不同結果,ROUILLARD等研究發現,隨著壓力從0.1MPa上升到25MPa,550℃下T91鋼的氧化程度變化不大,但其滲碳速率則提高了50%~60%,進而導致氧化物層中有更多孔洞形成,如圖3所示。該研究工作認為較高的孔洞密度與IOZ下方較高的碳化物密度有關。可見,在較低壓力范圍內,CO2壓力的提升可通過促進形成保護性氧化物及基體內部少量碳累積而有效阻止氧化,但壓力提高對于腐蝕的主要影響仍在于較高的CO2壓力可促進鋼基體與氧化物內部的滲碳作用,并且大量碳化物及非晶碳的累積會使得氧化層孔洞明顯增加。此外,CO2作為碳單質的重要來源,CO2壓力的增加會使氧化物/基體界面的碳積累更明顯,但對滲碳深度的影響規律還有待進一步研究。
此外,溫度與雜質氣體等其他環境因素也可能改變壓力對腐蝕的影響作用。BIDABADI等研究了溫度(500~600℃)和壓力(0.1、10MPa)對CrMoV鋼滲碳行為的影響,發現在0.1MPa不同溫度下CrMoV鋼的內氧化層的碳沉積濃度相差不大,而10MPa下的碳沉積濃度隨著溫度從500℃增加至550℃而增加,但會隨著溫度繼續升高至600℃時而降低。這是因為在550℃、10MPa條件下,CrMoV腐蝕產物中含有富Fe的M3C碳化物,且氧化物/鋼界面下的鋼晶粒也會被分解為富Fe顆粒,而M3C碳化物和富Fe顆粒會作為CO2分解產生碳反應的活性催化劑,促進碳沉積。總之,CO2壓力增加會導致滲碳速率提高,而盡管滲碳累積在一定程度上會通過阻礙鋼內部元素擴散而進一步降低鋼的氧化速率,但滲碳行為會影響鋼材本身性能以及可能導致氧化層脫落,因此較高壓力下鋼材的使用壽命反而會被較大程度縮減。此外,在高溫環境下,壓力升高至CO2的臨界壓力時,CO2狀態將轉變為超臨界CO2,其物理性質也將發生一定改變,因此對于相關研究中所觀察到的結果是否與CO2狀態的改變有一定關聯,仍有待進一步探究。 3.3.雜質氣體 3.3.1 O2 O2可能主導鋼的CO2腐蝕進程,但其影響規律較為復雜。通常,O2可以促進氧化物的生成,增加氧化層厚度。例如,在有無空氣兩種條件下,LEHMUSTO等發現盡管31鋼表面形成的氧化層結構均為典型的Fe氧化物-FeCr氧化物雙層結構,但少量空氣的存在會使得316鋼的氧化增重增加。同時,在純CO2環境中,316鋼的氧化內層與外層厚度比為1∶1,而存在殘余空氣時,外氧化層變得更厚,內層則變得更加均勻。與之相反,SS310鋼在有無O2的CO2環境氛圍下的氧化表面均覆蓋較薄的Cr2O3層,且存在少量成分為Fe3-xCrxO4的氧化物,但含O2環境下形成的Cr2O3層更薄、FeCr氧化物較少。如圖4所示,O2的存在使得滲碳深度由4μm 減少至 1.5μm,并導致氧化層與再結晶層界面處的碳層幾乎消失。這是因為在純CO2環境下形成 Cr2O3時,鋼的晶界處存在碳偏析,進而限制了Cr2O3的生長,導致Cr2O3晶粒細化,從而有更多晶界為氧化性氣體提供擴散路徑,最終形成更厚的氧化層 。相比之下,CO2的存在會降低O2−空位的密度,這有利于表面均勻的Cr2O3形成,增加其穩定性,進而抑制表面氧化物形核。
3.3.2 H2O H2O的存在往往會促進高溫下鋼的CO2腐蝕進程。LI 等發現,高溫下H2O的存在會使得SS310鋼表面的腐蝕產物Cr2O3轉化為易揮發的CrO2(OH)2 ,導致Cr元素損失,進而促進氧化以及滲碳,相關反應式如式(5)所示 ,但在僅含H2O作為雜質的CO2環境中,H2O可以阻斷鋼表面氧化層上對CO2/CO等物質的一些吸附位點,因此其對于滲碳作用存在一定抑制作用。此外,H2O的存在會對鋼表面形成的Fe3O4氧化層存在破壞作用,如式(6)所示。而當O2與H2O同時存在時,鋼的CO2腐蝕將變得更加嚴重。例如,通過研究9Cr鋼、12Cr鋼和316H鋼在不同溫度下(450~650 ℃)含有1%O2和 0.1%H2O的CO2環境中的氧化腐蝕行為,PINT等發現450℃下三種鋼的氧化層成分與純CO2環境下相同,但它們的氧化層變厚、氧化增重更加明顯。而當溫度為650℃時,三種鋼的氧化層成分發生明顯改變。其中,316鋼表面的腐蝕產物由較薄的Cr2O3層轉變為Fe2O3、Fe3O4等Fe氧化物層,而9Cr鋼和12Cr鋼表面的腐蝕產物則為內層Fe3O4 、(Fe,Cr)3O4和最外層Fe2O3層組成的三層氧化結構。相反,KUNG等發現在有無O2與H2O作為雜質氣體的兩種環境中,Grade 91(Gr. 91)鋼表面的氧化層均由外層 Fe3O4和內層(Fe,Cr)3O4組成,且內外層厚度相近,但在含雜質氣體的CO2環境下,該氧化層總厚度約為15μm,而在純CO2環境中腐蝕300h后,Gr. 91鋼氧化層總厚度增加至30μm,氧化增重與滲碳深度均有所增加。這是因為O2和H2O共存時,較高的氧分壓有利于更多保護性氧化物的形成,進而導致氧化層厚度降低。然而,目前有關H2O的影響研究主要集中在H2O與其他雜質氣體共存環境,而針對于單一H2O作為雜質氣體存在于高溫CO2環境中的研究較少,有待進一步展開。
3.3.3 SO2 SO2的存在對鋼的CO2腐蝕也有重要影響。OLEKSAK等通過在含H2O 、O2的CO2環境中添加0.1%SO2研究了SO2對鋼腐蝕的影響規律,發現SO2的影響機理會隨著鋼中Cr元素含量變化而變化。對于Cr元素含量低于9wt.% 的Gr. 91鋼而言,其表面氧化層在有無SO2條件下均由外層Fe2O3/Fe3O4和內層Fe3-xCrxO4組成,而SO2的存在會使得氧化層內部存在少量硫化物,導致與H2O和CO2相關的腐蝕剝落、氧化以及滲碳行為程度有所降低,但其氧化速率并無顯著變化。而對于Cr元素含量高于9wt.%的347H鋼與310S鋼而言,二者在不含SO2的腐蝕環境中會形成薄的Cr2O3層,而SO2的存在會導致硫元素通過氧化物的局部滲透Cr2O3層,進而促進Fe3O4等富Fe氧化物的形成,如圖5所示。此外,通過對比不同SO2濃度下FeCr合金在CO2-H2O環境中的腐蝕行為, YU等發現在不含SO2環境下,FeCr合金內部較深處有晶間碳化物形成,并滲透到整個試樣,而0.1%SO2的存在則會對合金滲碳行為有著明顯抑制作用,但隨著SO2濃度從0.1%增加至1% , FeCr合金氧化物層下的晶間滲碳速率略有增加,這是由于增加的硫化物 - 氧化物相界為碳擴散提供了更多路徑。表2總結了部分鋼在不同雜質氣體環境中的氧化增重速率。
3.3.4 多種雜質氣體環境 如前所述,O2、H2O 、SO2作為CO2高溫腐蝕環境中主要存在的雜質氣體,對腐蝕進程的影響并不相同。其中,O2主要作為氧化過程中氧元素的直接來源,能促進鋼表面氧化層形成,但其作用會因溫度升高而變化。將H2O作為單獨的雜質氣體進行討論則較少,通常是將其與O2或SO2共同討論。如式(6)所示,H2O對Fe3O4保護層可能存在破壞作用,并且QUADAKKERS等研究中提到,H2O對保護性Cr2O3氧化層形成的不利影響相較于CO2更為明顯。同時,由于H2O氣體分子在Cr2O3上的吸附趨勢高于CO2,H2O作為雜質氣體對滲碳作用存在抑制效果。相比之下, SO2對CO2腐蝕進程的影響主要體現在其對高Cr鋼表面Cr2O3氧化層形成的阻礙作用:SO2的存在可促使氧化物由富Cr向富Fe轉變,且在雜質氣體含量較低的情況下,SO2對于鋼的CO2腐蝕程度影響相較于H2O與O2更加明顯。例如, OLEKSAK等發現在95%CO2、4%H2O、 1%O2 、 0.1%SO2的環境下,盡管SO2含量更低,但由于硫元素推動氧化物由富Cr向富Fe轉變,顯著提升了奧氏體鋼的氧化速率,而H2O和O2對所有Fe合金氧化行為的影響相對較小。 事實上,在CO2腐蝕環境中,雜質氣體往往多種并存,且由于氣體間相互協同效應,其影響作用可能發生改變,甚至相反。如前所述,H2O與O2同時存在時可能發生式(5)代表的反應,進而破壞Cr2O3氧化層。類似地, YU等發現在CO2環境中單獨添加H2O或SO2作為雜質氣體, FeCr合金腐蝕程度均更為嚴重,而當加入H2O與SO2的混合氣體時,FeCr合金表層的氧化層不再分離脫落,說明混合氣體對其具備一定保護作用。這是因為當SO2作為雜質氣體時,硫元素容易吸附于氧化層,晶界處CrSx的形成促進Cr元素向外擴散,加速氧化物層的形成,鉻化物生長無法持續下去,進而造成鉻化物氧化層分離。而氣體環境中同時含有H2O和SO2時,H2O會與CO2和SO2競爭合金表面與氧化物晶界內的吸附位點,同時H2O的衍生物將進入氧化層,改變硫元素在氧化層中的化學性質,降低了硫元素的吸收程度。在此情況下,相應的CrSx形成水平會大幅降低,導致Cr元素向外擴散的增強作用非常小,因此氧化物生長較慢,合金元素的擴散可以支持氧化物的持續生長。但值得注意的是,該研究在對H2O與SO2的協同效應進行探究時,H2O含量高達20%,因此較低的H2O含量與SO2氣體是否仍存在較為明顯的協同效應有待進一步研究。對于三種氣體共存作為雜質氣體環境時,目前相關研究認為H2O與O2對CO2腐蝕進程具有一定促進作用,而SO2的加入則會導致氧化層中形成硫化物,從而阻礙腐蝕氧化進程及氧化層的脫落。 3.4.多條件綜合影響因素 盡管O2、H2O 、SO2對鋼腐蝕過程中的滲碳行為均存在一定的抑制作用,但這三種雜質氣體對鋼腐蝕的影響主要表現在作為鋼的氧化過程中的部分氧元素來源,特別在雜質氣體含量較低的條件下。例如,ROUILLARD等在550℃、 25MPa的CO2環境中對T91鋼進行氧化試驗時發現,環境中含有0.6×10−3%H2O與0.2×10−3%O2,而在T91鋼表面形成的20µm厚的氧化層中,僅有約0.25µm 厚的氧化物中的氧元素來源于O2與H2O。此外,由于鋼的氧化速率與表面氧化物生成速率在不同溫度下差異較大,不同溫度下雜質氣體的影響作用可能完全不同。例如,在兩種溫度(350 、 650℃)與兩種氣體環境(研究級CO2(RG-CO2, > 99.999% )、工業級CO2(IG-CO2 ,>99.98% ))下對多種鋼材進行的腐蝕試驗中, WALKER等發現多種鋼在兩種溫度條件下所得的氧化增重結果完全相反:350℃下鋼在IG-CO2中質量變化略大于RG-CO2環境,而650℃下鋼在RG-CO2中質量變化反而略大于IG-CO2環境。這可能是因為較低溫度下雜質氣體對鋼腐蝕進程的促進作用更為明顯,同時表明不同溫度下雜質氣體對鋼的CO2腐蝕的影響與其含量也密切相關。此外,QUADAKKERS等發現在沒有添加O2的CO2-H2O氣氛中,310N奧氏體鋼在550~700℃下腐蝕時均會有極薄且粘附良好的富Cr氧化層形成,而當加入3%的O2后,550與600℃下310N鋼的腐蝕產物仍為富Cr氧化層,但其在650~700℃下的腐蝕產物則出現了局部富Fe氧化層。可見,即使雜質氣體成分相同,由于氣體間交互協同作用,多種氣體共存情況下溫度改變對鋼腐蝕進程造成的影響也會存在差異。 如前所述,在純CO2環境中,壓力對鋼腐蝕過程中的氧化行為影響較小,而當環境中存在較高含量的雜質氣體時,壓力對鋼的氧化過程影響會變得更為明顯,并且此時壓力的影響也會隨溫度與鋼材種類變化而變化。例如,在雜質氣體含量較低的RG-CO2與IG-CO2環境中,PINT等發現304H、310H等多種鋼的腐蝕速率與腐蝕產物隨著環境壓力從0.1MPa增加至30MPa并無明顯變化,而在含有1%O2、0.25%H2O的CO2環境中,30MPa的環境壓力下304H 、310H等鋼材的腐蝕速率明顯高于RG-CO2與 IG-CO2兩種環境。此外,研究發現環境壓力不僅能改變雜質氣體對鋼腐蝕過程中氧化行為的影響,較高的壓力還會促進H2O與O2存在時Cr2O3的揮發行為,從而破壞致密的Cr2O3氧化層,這可能導致Cr2O3層無法有效阻礙CO2等氣體滲入鋼材內部,進而促進鋼腐蝕過程中的氧化與滲碳行為。類似地,當環境壓力達到CO2的臨界壓力,即在超臨界CO2環境中,高溫下部分雜質氣體一定程度上能溶于CO2流體中,進而導致雜質氣體對鋼腐蝕進程的影響發生變化,而目前關于超臨界環境或其他壓力條件下雜質氣體對鋼的CO2腐蝕的影響研究仍然較少。綜上所述,在多種雜質氣體共存的高溫CO2環境中,溫度、壓力和雜質氣體含量等諸多因素對鋼的CO2腐蝕的影響規律及機理仍不明晰,亟待進一步研究。 4. CO2氧化滲碳腐蝕模型 事實上,高溫下鋼的CO2腐蝕行為會涉及到氧化與滲碳同時發生。基于大量試驗數據,科研工作者觀察到氧化物生長速率與滲碳速率符合拋物線動力學,進而建立了高溫氧化模型和滲碳模型等數學模型來預測鋼的氧化與滲碳行為。 4.1.高溫氧化模型 如前所述,高溫下鋼的CO2腐蝕過程中氧化行為通常是鋼中的Fe和Cr元素被氧化,其氧化增重速率符合拋物線動力學。因此,通過在400~600℃下對9Cr鋼和12Cr鋼進行了長達8000h的氧化增重試驗, FURUKAWA等將試驗所得的增重數據與根據拋物線方程計算得出的近似曲線進行對比,觀察到良好的一致性,相關拋物線方程如下:
式中, ?W為增重(g/m2), K p 為氧化系數(g /(m2 · s−1/2) ),t 為時間(s)。氧化系數主要與溫度有關,與壓力無關:
式中, K0為常數, Q為表觀活化能(J/mol), R 為氣體系數(J/(K·mol)), T為絕對溫度(K)。基于模型和試驗結果, FURUKAWA等認為9Cr鋼與12Cr鋼表面的雙層氧化層的外層是由金屬元素向外擴散形成,而內層是由O2向內擴散形成,且體積擴散比為1:1。由于O2向內部擴散的腐蝕效果等同于鋼表面氧化前的金屬損失,因此認為可通過所測得的氧化增重來計算鋼表面腐蝕量Lm,計算公式如下:
式中, Cp為重量增加與氧化物厚度之間的比例常數,Rc為金屬損失厚度與氧化物厚度比值。雖然這一計算無法包括表面氧化層的滲碳與剝落引起的性能退化,但預測結果可作為初步設計的參考指標。值得注意的是,由于這一模型是基于試驗中所觀察到的增重數據符合拋物線方程的現象而建立的,因此當腐蝕環境中存在較高含量雜質氣體影響腐蝕進程時,其預測結果可能存在偏差。此外,如前所述,當碳累積于氧化物層中,基體合金元素向外擴散的行為會受到阻礙,其氧化速率進而降低,而該模型中并未將這一因素考慮在內,模型準確性有待提高。對于氧化產物主要為Cr2O3氧化層的鋼種,腐蝕壽命預測可以通過分離氧化時間tB評估,即Cr元素耗盡界面達到鋼一半厚度界面的時間, GUI等認為可通過計算Cr元素的體積擴散系數和拋物線生長速率常數來計算分離氧化時間。在拋物線型氧化層生長動力學的前提下,可根據菲克第二定律推導出t時刻在氧化物與基體界面下z深度處的Cr元素濃度 C(t, z) ,計算公式為:
式中, Cc為試樣一半厚度處Cr元素的濃度( wt.% ),Mcr為Cr的原子質量(kg), Ma為原子質量(kg),Vs為氧化物占合金的體積比, KC為氧化物生長速率(g/m2·s-1/2),Dcr為Cr元素的擴散系數,n為常數,z為深度(cm), w為試樣厚度的一半(cm)。 GUI等利用該模型對兩種鋼不同深度的Cr元素濃度進行擬合并計算腐蝕量,擬合結果與試驗結果誤差較小,進而判斷此模型可將分離氧化時間作為預估壽命進行預測。然而,由于較高溫度下高Cr 鋼的表面氧化物可能由富Cr向富Fe轉變,因此該模型僅限于一定溫度范圍內使用。此外,即使鋼表面主要形成氧化物為Cr2O3,但當其Cr元素含量較低時, Fe氧化物形成后同樣具備一定保護性,而該模型僅考慮材料中Cr元素含量對于基體的防護作用,這將導致模型預測結果與實際壽命相差較大,僅可作為壽命極限的保守估計。 GONG等提出了如圖6所示的氧化物生長模型(Oxide growth model, OGM)。圖中,υmag 、 υsp為對應Magnetite 、Spine氧化物層界面相對于原始合金 / 氣體界面的速度,C表示圖中對應Fe、Cr、O元素的濃度。該模型認為Fe元素向外擴散形成外層Fe3O4層,O2向基體擴散形成內層尖晶石層,但由于O2分壓較低,因此, CO2將替代O2在這一過程發揮作用。各氧化層厚度計算公式如下:
式中,Cki和Jki分別是i元素在相態k的體積固定參照系中的界面濃度(wt.%)與界面通量(kg/s ),且sp代表Spine層, mag代表Magnetite層,μki 為i元素對應 k 界面的化學勢(J/mol ), A代表圖中Spine氧化物層與合金界面,B代表氣體與Magnetite層界面,Xmag 、 Xsp分別為對應Magnetite 、Spine氧化物層厚度(µm)。MO、 MFe為對應元素的相對原子質量,t為時間(s)。 同時,由于觀察到的內層是多孔的, GONG等進一步提出氣相分子輸運可作為可用空間模型的一部分,且CO2通過氣孔與分離氣孔的氧化物晶界傳輸。該模型計算得到的氧化層厚度與試驗結果較吻合,且由模型圖可看出,該模型適用于形成雙層Fe氧化物層的低Cr鋼。
針對涉及到氧化物剝落的腐蝕行為, KUNG等進一步優化了已有的電力研究協會(Electric powerresearch institute, EPRI)氧化剝落模型 ,進而成功將用于S-CO2布雷頓功率循環的熱交換器設計中常見參數作為模型的相關參數。這些參數包括額外的材料特性、流動通道的物理構型、相關的傳熱和流體流動標準。KUNG等通過模型成功預測了氧化膜脫落質量,進而認為在 S-CO2熱交換器流道表面生長的氧化層是無應力的,但合金基體與氧化層之間的熱膨脹系數差異會導致低溫下二者之間存在應力。此外,合金幾何特征引起的機械約束和系統壓力變化也會導致應力產生。而當產生的應力超過某個臨界值,且氧化產物足夠厚時,氧化產物可能被破壞,進而發生剝落。目前,針對鋼在高溫CO2環境中的氧化模型主要是基于對其他環境中已有模型進行優化而得,較為依賴試驗所得數據,因此后續相關研究中有待將溫度、壓力等環境參數與材料成分等因素納入模型,以理論基礎結合實際所得數據綜合評估鋼在高溫CO2環境下腐蝕情況,進而較準確地進行壽命預測。 4.2.滲碳模型 ROUILLARD等提出高溫下鋼的CO2腐蝕過程中滲碳行為是由元素擴散控制的,通常發生在氧化物與金屬界面,具體是由CO2/CO通過氧化物層的擴散速率和CO2與金屬的反應速率共同控制。基于此, GHENO等采用局部平衡模型來描述碳氧活性,并將這一模型應用于氧勢較低的氧化物/合金界面,成功預測出了足夠高的碳活度值,進而提出CO2分子在氧化層的任意點存在熱力學平衡。而內部滲碳深度可用穩態拋物線動力學描述:
式中, Xc為滲碳深度(cm),K(i)p為內部滲碳速率(cm2/s),t 為時間(s)。其中K(i)p的評估是基于所有Cr元素不進行擴散而均以碳化物形式析出的前提計算得到的,其計算公式如下:
式中, Dc為碳擴散系數(cm2/s),N(s)c為合金表面溶質碳的摩爾分數,N(o)Cr為原始合金Cr元素的摩爾分數, v為碳化物CrCv的化學計量系數, ε為擴散阻塞因子。而在外部氧化物層存在時,碳的表面分數N(s)c被界面分數N(i)c所替代。 然而,YOUNG等發現上述模型計算的低溫下碳活度相較于試驗測得數據高幾個數量級,因此認為上述的熱力學平衡并不存在。YOUNG等進而在氧化物 - 金屬界面處增加了一個有限的碳注入速率,即碳注入金屬的速率與平衡濃度和實際碳溶質濃度之間的差成正比,用來描述將碳的擴散考慮為碳化物析出時造成的損失,進一步作出結論:由于碳向金屬相的轉移相對緩慢,滲碳反應是一種非穩態行為。YOUNG等利用溶質碳在金屬相內的正常擴散、碳化物的快速析出以及碳在金屬相和析出相之間的平衡分配等規律,成功解釋了觀察到的碳滲透的拋物線動力學和碳轉移的線性動力學:
式中,CMC溶質碳的濃度(wt.%), t為時間(s), D為擴散系數(cm2/s), Xc為滲碳深度(cm), β為常數。雖然該模型可根據氧化物/金屬界面碳活度對形成碳化物數量進行一定準確度預測,但并未涉及對于滲碳深度的預測以及滲碳程度對鋼性能的影響。目前針對S-CO2環境下滲碳的相關討論較少,且大多數研究者關注點在于滲碳環境的產生以及碳轉移通道等方面,因此,有關滲碳模型的相關研究亟待進一步展開,并且研究重點應在于滲碳程度對于鋼材力學性能的影響以及由于滲碳導致氧化層脫落的臨界點,進而打破由于滲碳作用而無法準確評估導致鋼在高溫CO2環境下腐蝕壽命的限制。 表3總結了上述高溫下鋼的CO2腐蝕氧化與滲碳模型及應用條件。可見,目前相關工作往往只建立了單一的氧化或滲碳模型。雖然這些模型可對氧化物層厚度、滲碳深度等進行預測,但由于腐蝕過程中氧化與滲碳同時發生,這些模型未能較為準確地預測高溫CO2腐蝕環境中鋼材的腐蝕壽命,因此建立同時涵蓋氧化與滲碳共同作用的模型亟待進一步展開。 5. CO2腐蝕防護 涂層是提高鋼在高溫CO2腐蝕環境中服役壽命的有效途徑。科研工作者對金屬涂層的成分和制備工藝等因素進行了充分研究,并同時制備了復合涂層以達到更好的防護效果。由于Cr 、Al等元素在高溫下形成的氧化物層可有效提高基體耐蝕性能,這些元素因而常被用作涂層的主要成分。 5.1.Al 涂層 鍍Al是最常用的金屬涂層之一。制備鍍Al涂層過程中生產的氧化鋁熔點高達2054℃,具備很好的高溫穩定性,因此具有良好的抗高溫腐蝕性能。例如, SCHULZ等采用溶膠-凝膠法在X20鋼表面制備了氧化鋁層,并分別在CO2-H2O-O2與空氣環境下對其進行腐蝕測試,發現氧化鋁層表現出良好的耐腐蝕性。然而,朱明等研究表明溶膠-凝膠法制備的防護涂層與基體的熱膨脹系數不匹配,進而容易發生剝落和開裂,因此涂層與基體連接的緊密性也應作為涂層性能的重點因素進行研究。基于此, SCHULZ等提出可以考慮通過浸涂或噴涂的方式制備涂層。 KIM等采用磁控濺射法在一種氧化物分散強化鐵素體-馬氏體雙相鋼(Oxide dispersionstrengthened ferritic-martensitic, ODS-FM)表面沉積Al與Ni-Al兩種涂層,并進行擴散熱處理,發現兩種涂層表面的Al2O3層均表現出良好的耐蝕性。其中Al涂層的氧化增重低于Ni-Al涂層,但Al涂層表面比較疏松且存在較多孔洞,導致Al2O3層易剝落,而Ni-Al涂層的表面較均勻,能夠有效抑制Al元素向基體的擴散。KIM等在316不銹鋼表面制備Al涂層與Ni-Al涂層過程中也發現類似結果,但由于650℃下形成氧化鋁為過渡氧化鋁,不能有效阻止滲碳反應的發生,導致碳可以穿透氧化鋁層形成含碳層,如圖7所示。基于此, KIM等對涂層進行了900℃的預氧化處理,使涂層內部在預氧化后形成更具保護性的α-Al2O3,進而獲得耐腐蝕性能與防滲碳性能更優的涂層。相對于Al涂層,Ni-Al涂層中的Ni元素一定程度上可作為有效屏障而抑制Al元素向基體擴散,進而使得表面Al2O3更加穩定,顯著提升涂層耐腐蝕性能,但有研究者認為通過在Ni-Al層與基體間添加中間層而制備的雙層涂層可更加有效阻礙Al元素擴散。
ZHAO等和LI等采用電鍍制備Ni-Al涂層,并添加一層Ni-Re層作為基體與涂層之間的中間層,以期抑制高溫下Ni-Al層與基體之間相互擴散形成互擴散區(Interdiffusion zone , IDZ),進而避免涂層因Al元素含量過低而失效。在650℃下CO2環境中進行氧化試驗后發現,無Ni-Re中間層的Ni-Al涂層中Cr和Fe元素的存在提高了Ni2Al3層與擴散區界面處Al元素的活性,導致內部Al2O3析出,同時脆性相(Cr, Al)、(Fe, Al)加速了裂紋與孔洞的形核和生長,從而加劇了擴散區(Diffusionzone , DZ)內部氧化的發生,導致涂層出現水平裂紋與斷裂。而Ni-Re中間層起到了擴散屏障的作用,有效延緩了涂層與基體之間的相互擴散,減少了內部氧化物的形成,同時Ni-Re中間層的添加導致Ni-Al層與鋼基體之間形成(NiAl)-Re結構,顯著抑制了滲碳,如圖8所示。因此,通過制備Ni-Al/Ni-Re涂層并進行預氧化處理,Al涂層的耐腐蝕性能有望進一步提高,但這種涂層與基體連接是否良好仍有待探究,同時可探究不同制備方式對涂層性能的影響。
圖8 不同涂層在650℃CO2環境中腐蝕660h后的SEM截面圖像與EDS元素線掃描結果 5.2.Cr涂層 鍍Cr過程中產生的Cr2O3具有與氧化鋁類似的性能特點,從而也廣泛用作金屬涂層制備工藝。NGUYEN等通過膠結充填法在T91鋼分別制備了Cr 、Ni/Cr 、Al 和Ni/Al四種涂層,發現Cr2O3或Al2O3氧化層均能顯著提高T91鋼的抗氧化性,且在650℃下CO2-H2O環境中腐蝕1000h后,Cr涂層與Al涂層增重相近,但Ni/Cr涂層耐腐蝕性遠遠低于Cr涂層,而Al/Ni涂層性能則優于Al涂層。這是因為Ni/Cr涂層由外到內是由Ni-(Cr)、Ni-(Fe, Cr) 、 Fe-(Ni, Cr) 等多層組成,而 Ni-(Cr) 層中的Cr元素濃度會隨著腐蝕時間延長降低到維持Cr2O3保護層增長所需的臨界值以下,導致其性能相較于Cr涂層更差。相比之下, Al涂層中Al元素含量較高,提供于形成Al2O3層的Al元素損失可忽略不計,使得其與鋼基體的相互擴散決定了反應過程中Al涂層的濃度,而Ni/Al涂層中的Ni中間層有效阻止了元素擴散,導致其性能優于Al涂層。此外,由于Al2O3的碳溶解度非常低,因此鍍Al涂層抗滲碳作用明顯優于鍍Cr涂層。 利用磁控濺射法,KIM等在ODS-FM鋼表面沉積制備了Cr涂層,發現其在進行熱擴散處理后會形成一層約4μm厚的富Cr碳化物層及約20μm厚的擴散區。在650℃、20MPa下CO2環境中腐蝕500h后,無涂層的鋼表面形成約100μm厚的氧化層,而涂層試樣的氧化層僅為0.2μm,其掃描投射電子顯微鏡分析(STEM)如圖9所示。同時,無涂層試樣的氧化層下存在約370μm厚的滲碳區,導致鋼幾乎完全失去延性,而Cr涂層鋼中并未觀察到碳化物,可見Cr擴散涂層可以有效減少基體的滲碳。
5.3.其他涂層 除上述涂層外,其他涂層也對鋼在CO2環境下耐腐蝕作用有明顯提升作用。其中,通過在SS316LN不銹鋼表面沉積Si涂層并在900℃對其進行熱處理后, KIM等發現Si涂層在熱處理過程中會與基體相互擴散,形成Fe5Ni3Si2相這一熱力學穩定相,同時基體元素向Si涂層的快速擴散導致Si涂層中存在孔洞,而孔洞附近能觀察到Mo元素的富集,但Si沉積涂層在S-CO2環境下形成了較厚的富Cr氧化內層與較薄的富Si氧化外層,二者仍能有效提高涂層耐腐蝕性。而針對鋼在高溫超臨界CO2環境下的滲碳行為,BRITTAN等在316LN表面制備了不同厚度的Cu涂層,發現氧化腐蝕作用隨涂層厚度增加而減弱,其中100μm以上的涂層可使得316鋼氧化增重與Ni基高溫合金相似,而連續完整的Cu涂層能將初始氧化行為轉變為氧通過涂層的擴散行為,進而延遲了CO2對鋼的氧化,最終減少了碳沉積總量。 可見,有關鋼在高溫CO2環境中腐蝕的研究工作仍集中于不同鋼種及涂層的耐腐蝕性表現,但在實際服役過程中,涂層的其他性能同樣至關重要。因此有關涂層力學性能及其對鋼基體力學性能的影響研究有待展開,同時可通過理論計算與模擬優化涂層結構,為復合涂層制備提供一種新思路。 6. 結論與展望 CO2腐蝕是鋼質結構件服役環境中較為常見的一種腐蝕失效方式。目前,鋼在高溫CO2環境中的腐蝕機理已較為明晰,但不同環境下或不同種類鋼材的腐蝕程度或產物通常存在差異。針對此,科研工作者試圖建立相關模型預測鋼的CO2腐蝕行為,同時研究了不同涂層的制備工藝及防腐效果。綜述了高溫下鋼的CO2腐蝕的相關研究進展,并進行以下結論: (1)溫度與壓力升高通常會加重鋼的CO2腐蝕。其中,溫度升高主要使氧化層更厚和高Cr鋼氧化層成分發生改變,而壓力主要影響其滲碳行為。鋼的服役環境中存在的O2 、H2O 、SO2等氣體雜質對其CO2腐蝕均存在不同程度影響,且這些因素的影響規律會隨著鋼的種類及服役環境的變化而變化。 (2)目前關于鋼的CO2腐蝕過程中氧化與滲碳行為的腐蝕模型研究較少,且大多數模型是基于單一的氧化或滲碳動力學符合拋物線變化趨勢的現象而建立的。雖然這些模型可對氧化物層厚度、滲碳深度等進行預測,但由于腐蝕過程中氧化與滲碳同時發生,這些模型未能較為準確地預測鋼材的腐蝕壽命,因此建立同時涵蓋氧化與滲碳共同作用的模型亟待進一步展開。此外,實際工況中的CO2可能處于流動狀態,這將導致鋼的腐蝕速率加快并促進氧化層脫落,因此未來的腐蝕模型須進一步考慮CO2流動狀態(特別是含氧化物顆粒的CO2流)造成的侵蝕作用。 基于以上總結,為進一步提高鋼在高溫CO2環境中耐腐蝕性,針對目前已有防護涂層研究作出如下展望: (1)目前已有Al、Cr等涂層可有效提高鋼在高溫CO2環境中的抗氧化與抗滲碳性能,但鋼材及涂層在腐蝕環境中的力學性能變化規律也將對其腐蝕行為有著重要影響,亟須深入研究。此外,相比于其他金屬,Ni基合金往往表現出更優異的耐腐蝕性能,但其較為昂貴的成本限制了 Ni 基合金的大規模應用。因此,在對鋼的涂層進行成分設計時,可選擇Ni基合金為涂層主要成分。而引入納米顆粒,并基于模擬計算對涂層成分及結構進行有效調控以改善涂層力學性能與耐蝕性的方法同樣可作為涂層成分選擇的一種研究方向。 ( 2)除改變涂層成分外,有關鋼涂層防護的研究重點還在于提高涂層與鋼材之間的附著強度和界面穩定性,進而確保涂層可牢固地附著于耐熱鋼表面,不易剝落,這離不開對更有效提高涂層的均勻性和致密性的制備工藝的探索。此外,開發可實時監測涂層損傷的系統方法有利于研究人員在合適時機采取恰當的維護措施。
免責聲明:本網站所轉載的文字、圖片與視頻資料版權歸原創作者所有,如果涉及侵權,請第一時間聯系本網刪除。
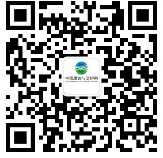
官方微信
《腐蝕與防護網電子期刊》征訂啟事
- 投稿聯系:編輯部
- 電話:010-62316606
- 郵箱:fsfhzy666@163.com
- 腐蝕與防護網官方QQ群:140808414