-
0 前言
-
電磁軌道發射是利用電磁能替代機械能和化學能進行發射的新型發射技術,它突破了傳統意義上火炮的局限性,能實現超過 2 km/s 的極高速度,具有發射速度快、射程遠、安全性能高、可控性強等優點,應用前景廣闊[1]。
-
電磁軌道發射裝置由儲能系統、脈沖功率調節系統、電磁軌道發射器和遠程遙控系統組成[2],如圖1 所示。儲能系統在發射過程中,通過脈沖功率調節系統將積蓄的能量調節為瞬時超大功率電能輸出給電磁軌道發射器,從而激發磁場,電樞在洛倫茲力的作用下,推動負載加速發射以達到預定速度,遠程遙控系統通過信息指令實現對能量的控制。其中,電磁軌道發射器由電樞、軌道以及絕緣支撐體組成,如圖2 電磁軌道發射樞軌載流摩擦副及裝配彈丸示意圖所示。電樞和軌道是主要運動接觸部件,常稱為樞軌載流摩擦副。
-
圖1 電磁軌道發射裝置組成示意圖
-
Fig.1 Schematic diagram of the composition an electro-magnetic rail launcher
-
圖2 電磁軌道發射樞軌載流摩擦副及裝配彈丸示意圖
-
Fig.2 Schematic diagram of electromagnetic rail launching armature rail carrier friction pair and assembled projectile
-
由于電-磁-熱-力多場耦合條件下的極端服役工作環境,即有大電流(~MA 級)、強磁場(~T 級)、高熱量(~103 K 級)、強作用力(~106 N 級)通過樞軌接觸表面,樞軌載流摩擦副不可避免地會產生一定的損傷。其中,電樞將彈丸推動至超高速,以較小的電流通流面積導通回路中的所有電流,承擔著發射系統產生的大部分能量,是系統中將電能轉化為彈丸動能的關鍵部件,表面狀態會直接影響樞軌載流摩擦副的服役性能,并與發射裝置的效率和精度密不可分,其損傷不僅導致電樞自身性能的下降,同時會降低軌道的使用壽命,制約其發展前景[2]。
-
為解決發射過程中電樞損傷問題,研究者將研究重點放在電樞損傷機理和損傷防護技術上。目前,對于電樞損傷的試驗驗證研究主要是通過對發射后電樞進行回收,觀察其經過一個服役過程后的表面形貌,從而判斷是否出現損傷以及損傷的嚴重程度; 對于電樞損傷的模擬與仿真主要是通過調節不同的參量,包括過盈量、電流密度以及電流波形等,分析其在服役過程中各項性能的變化,進而推導出服役過程后的損傷情況。
-
本文綜述了近年來國內外研究者對電磁軌道發射電樞損傷的研究進展。從典型損傷特征及其影響因素,損傷機制和改進手段等方面進行闡述,歸納了電樞損傷的分類和特征,總結了對應的理論分析,梳理了不同的防護優化技術。可以發現,電樞損傷研究發展至今,針對其損傷機理的探究仍不夠深入,尚不具備一套完整的理論體系,損傷防護處理技術尚不成熟。
-
1 典型損傷
-
1.1 載流摩擦磨損
-
載流摩擦磨損是指在導入電流后,兩金屬表面相互接觸并由于發生相對運動出現一系列摩擦學行為而產生的磨損[3]。由于電樞自身的機械屬性和預緊力條件下的電接觸特征,在大電流、高運動速度的極端服役過程中會不可避免地產生載流摩擦磨損。這種損傷主要是由于樞軌間接觸斑點在預緊力、溫度升高和電磁壓力增大下產生黏著,而后在摩擦力的作用下相互磨損導致的,即損傷發生于舊接觸斑點損壞而消失,新接觸斑點不斷形成的循環往復過程中。區別于一般的機械磨損,載流摩擦磨損不僅要受到電樞自身機械結構的影響,其還處于大電流場中,受到電流熱效應的制約,同時間在發射過程中會出現短暫分離的接觸特性導致電樞存在嚴重的電弧磨損,因此,電樞的載流摩擦磨損主要包括機械磨損、電流磨損及電弧磨損等形式。
-
1.1.1 機械磨損
-
GAO 等[4]在考慮了預緊力和電磁壓力的共同效應下,采用 Archard 磨損模型對樞軌接觸進行有限元仿真,研究預緊力和電磁壓力(洛倫茲力在法向上的分力)對電樞磨損的影響,結果表明,在發射過程中,電磁壓力提供了大部分的樞軌接觸力,并發現最大接觸壓力分布于電樞尾翼兩側,這也是電樞磨損集中的區域。MERRILL[5]建立了樞軌接觸界面的熔化潤滑模型,嚴格控制焦耳熱的影響,重點對發射過程中電樞產生的機械磨損進行研究,其結果顯示,法向載荷的增加會加劇電樞的磨損。主要是因為法向載荷的增大會導致樞軌間機械混合層厚度逐漸增加,并在發射過程中產生裂紋。當裂紋擴展至一定程度后,一部分電樞基體材料就會和樞軌間機械混合層一起剝落,從而導致嚴重的損傷。因此,電樞的機械磨損主要是由其復雜的受力條件導致,主要發生在樞軌接觸的低速階段。
-
1.1.2 電流磨損
-
電流磨損通常指電接觸材料在導入電流后,由于滑動摩擦以及電阻而引起的熱量和磨損現象,熱量的產生會導致溫度升高,進而引起材料發生熱膨脹、熱應力、氧化等現象[6-7]。一方面,升溫會導致表面氧化物的生成,造成電接觸材料間接觸電阻的增大和潤滑性的降低;另一方面,電流產生的焦耳熱會造成材料表面層軟化,降低摩擦層與基體的結合程度,從而影響材料的摩擦學性能[8]。電樞在 MA 級大電流作用下在軌道間高速滑動,樞軌間摩擦界面溫度迅速升高。電流磨損成為電樞載流摩擦磨損的重要特征之一。SENOUCI 等[9]在進行滑動電接觸摩擦磨損試驗中對比了是否通入電流的磨損情況,結果表明,電流的加入會加劇材料的磨損。這是由于通入電流會在樞軌摩擦副中產生電流熱效應,釋放熱量破壞表面潤滑膜,導致樞軌界面粗糙度增加,磨料性能提升,力學性能下降,發生電流磨損,磨損率增大。WATT[10]對不同電流條件下發射后電樞進行回收處理,通過電樞質量損失測定和表面磨損機械輪廓測定兩種方法確定電樞損傷量,如圖3 所示。可以發現,電樞損傷量與電流值的大小近似成一階線性正比。
-
圖3 不同電流條件下電樞質量損失和表面磨損量[10]
-
Fig.3 Armature mass loss and surface wear under different current conditions[10]
-
1.1.3 電弧磨損
-
電樞在軌道間非全約束條件下進行的高速飛升,常導致電樞與軌道發生短暫分離而形成電弧。 NAGASAWA 等[11]重點關注電弧磨損導致的載流摩擦磨損,研究表明電弧產熱是導致材料熱熔化的主要來源之一。CHEN 等[12]利用高速攝像機記錄了電弧磨損的全過程,結果表明磨損率與累計電弧放電能量近似成正比,但在合理范圍內加大法向力以增加摩擦副接觸面積,可以有效降低電弧磨損帶來的影響。可以發現,以弧光形式散發的熱量會導致樞軌接觸界面溫度急劇升高,導致材料發生嚴重熔化剝落。
-
目前研究者認為載流摩擦磨損是在載流條件下,機械能和電能相互耦合,二者互相影響共同作用下的結果。圖4 展現了 Al-Zn-Mg-Cu 系電樞在高速載流試驗過程中所表現出的“三階段”典型載流摩擦磨損形貌。可以看到,在電流較小的上升階段,表面形貌主要以犁溝為主;在電流最大的峰值階段,表面形貌主要為犁溝、熔融狀組織等;在電流下降階段,樞軌間出現電弧,熱量急劇增加,表面形貌主要為熔融狀組織等。
-
圖4 “三階段”載流摩擦磨損形貌
-
Fig.4 “Three-stage” current-carrying friction and wear morphology
-
1.2 熱熔化
-
在電磁軌道發射過程中,由于樞軌接觸面間的接觸電阻和電樞自身體電阻,當電流經軌道流向電樞時會產生焦耳熱。另一方面,為保證樞軌間良好的電接觸性能,樞軌間需緊密配合,存在預緊力。電樞在磁場中還要承受極大的電磁擴張力,發射過程中,隨著樞軌間相對運動速度呈指數增長,二者相互摩擦而產生大量的機械摩擦熱。在兩種不同形式的熱量疊加作用下,電樞表面溫度陡然增加。當表面溫度高于自身熔點時,電樞表層會向熔融態轉變,發生熱熔化,并在樞軌接觸面間形成一層液態金屬膜(Liquid Metal Film,LMF)。
-
李鶴等[13]開展了電磁軌道發射電樞接觸界面溫度場仿真研究,結合試驗數據,初步揭示了焦耳熱和摩擦熱對電樞溫度場分布的影響規律,為電樞表面熔化過程提供了基礎理論。CHEN 等[14]設計電樞的相關結構,使得樞軌接觸表面全部轉化為熔體磨損,建立了熔體磨損與發射參數、材料參數之間的構效關系。在電樞高速運動的同時,液態金屬膜厚度也在不斷增加,其本身也會產生粘滯熱,加劇電樞表面的熱熔化。STSFANI 等[15]在考慮液態金屬膜的影響下研究了固體電樞表面的熔化波侵蝕,發現電樞表面經歷了一個快速加熱和熔化過程。同時,不同發射階段下樞軌接觸狀態不同,引發電樞熱熔化的熱源占比會發生改變,電樞表面不同位置的熔化深度也不同。CHEN 等[16]基于電磁軌道炮的三維多物理場耦合模型,通過建立仿真模型和進行縮比試驗,對電樞熔化區域的熱源占比、最大熔化深度位置演變以及電樞損傷形貌進行了分析,如圖5 所示。可以發現,接觸電阻和電樞的體電阻產生的焦耳熱是電樞熔化的主要因素,熔化深度最大位置基本保持不變,為最先開始熔化區域。該仿真模型能為后續研究電樞熱熔化過程和預測電磁軌道發射過程中的全尺寸溫度特性提供幫助。
-
目前,關于電樞熱熔化產熱來源的研究理論已相對成熟,主要是摩擦熱和焦耳熱。但對于電樞運動過程中不同熱源產熱量的變化及其對電樞表面熱熔化影響程度大小的時空演化特性研究尚淺,缺乏系統的理論指導。
-
圖5 電樞熔化區域熱源占比、最大熔化深度位置演變及電樞典型損傷形貌示意圖[16]
-
Fig.5 Schematic diagrams of the heat source percentage in the melting region of the armature, the evolution of the location of the maximum melting depth and the typical damage morphology of the armature[16]
-
1.3 轉捩燒蝕
-
由于樞軌載流摩擦副自身結構的局限性,在極端服役工況下,電樞在發射過程中產生輕微垂直振動,與軌道發生失接觸或者接觸壓力不足,使樞軌間的接觸方式由“固-固”或“固-液-固”轉變為 “固-等離子體-固”,這種轉變稱之為轉捩[17],如圖6 所示。轉捩的產生會導致樞軌接觸面上產生電弧擊穿現象,在電樞表面引起嚴重燒蝕,從而加劇電樞的熱熔化損傷,破壞電樞的效能。典型的轉捩燒蝕損傷形貌如圖7 所示[18]。
-
圖6 轉捩燒蝕產生示意圖
-
Fig.6 Schematic diagram of transition erosion generation
-
圖7 典型的轉捩燒蝕損傷形貌[18]
-
Fig.7 Typical transition erosion damage topography[18]
-
為達到電磁軌道發射過程中樞軌摩擦副間無電弧接觸的狀態要求,以確保其精確性和安全性,開展對于樞軌間發生轉捩的內在機理性研究是十分有必要的。研究者從樞軌接觸界面材料熱應力、熔化波燒蝕模型以及過盈壓力和電磁壓力等方面展開了分析,當電樞因各種外界因素發生輕微形變或者材料損失時,轉捩產生的幾率將大大增加。關曉存等[19] 在假設電樞磨損主要為熔化磨損的前提下,通過仿真分析和試驗驗證研究了電樞表面磨損區域分布和磨損量大小,為建立材料損失與轉捩的關系奠定了理論基礎。朱仁貴等[20]研究了樞軌接觸間過盈壓力和電磁壓力大小在電樞運動過程中的變化,發現由于電樞的載流摩擦磨損,過盈壓力不斷減小,當二者合力降低到一定闕值時,轉捩發生概率增加。在現有理論基礎上,轉捩燒蝕在發射參數表現為膛口電壓的突然升高,炮口電阻增大,脈沖電流處于下降階段。陳允等[21]在研究發射過程中滑動電接觸特性的試驗中,對炮口電壓和電樞電流進行了測量,研究表明:轉捩經常發生于電流下降至峰值電流 80%~90%的時刻。在此基礎上,王志恒等[22]利用有限元軟件 ANSYS Workbench 對電樞轉捩過程進行了模擬仿真,分析了電流下降段電樞內部通流情況,電流下降段電樞內部和表面的電流分布如圖8 所示,可以看出在電流下降段電樞內部會產生渦流,內表面電磁力發生反轉,導致樞軌間接觸壓力不足,電弧放電,發生轉捩;進而分析了電流下降率的影響,結果表明:電流下降率越大,電樞發生轉捩的可能性越大,但是此試驗未能考慮電樞運動對電流分布的影響。
-
圖8 電流下降段電樞內部和表面的電流分布
-
Fig.8 Current distribution inside and on the surface of the armature in the current drop section
-
國內外研究者對轉捩燒蝕的產生機理提出了許多看法,包括電樞材料載流摩擦磨損過大且損傷區域不均一導致樞軌間無法共面接觸,脈沖電流在下降階段產生的渦流使內部磁力反轉導致的電樞尾部離開軌道表面等。從其定義本身來看,發生轉捩燒蝕時必然伴隨著樞軌間的失接觸,產生由等離子體填充的空間間隙,而這種空間間隙極大程度上是載流摩擦磨損帶來的,其帶給電樞材料的物質損失直接導致樞軌間空間間隙的存在,從而引起失接觸位置產生電弧擊穿現象,導致轉捩的發生,其產生機理目前尚不能用單一一種理論體系成功加以說明。
-
2 典型損傷影響因素
-
為了研究電樞載流摩擦磨損,熱熔化以及轉捩燒蝕等典型損傷形式的影響因素,近年來,大量研究者采用試驗現象分析和數值模擬兩種方法相結合,分別從服役變量和電樞自身參數進行對比試驗論證。
-
2.1 服役變量
-
針對服役變量,研究者們以電流波形、界面液層厚度、軌道通流長度、極性、滑行距離以及摩擦因數等因素為切入點,通過調節不同的外界影響量進行電樞損傷試驗和仿真,探究其損傷程度的大小。
-
LI 等[23]根據接觸面金屬液態膜(LMF)和 Reynolds 方程,在溫度、應力和電磁場耦合作用下,建立了熱彈性磁流體力學模型,分析了電流波形對表面熱熔化速率和 LMF 厚度的影響,結果表明:電流波形越平滑,電樞表面熱熔化速度越慢,最小 LMF 厚度越薄;張寶[24]舍棄常規研究,認為樞軌接觸界面溫度相同的非真實條件,在考慮真實具體的界面溫度分布下,建立了界面液層磁場、熱場以及潤滑流場等多物理場耦合模型,分析了不同厚度液層的基本流體屬性及其降溫作用,在一定程度上還原了電樞與軌道間在高速相對滑動時產生的載流摩擦磨損,但未考慮引入液層后電接觸性能的變化; 李天亮等[25]在基于面電流假設,建立了電樞電磁感應強度場計算模型和電樞所受電磁力模型,以軌道通流長度這一參數為變量進行研究,觀察電樞所受到的電磁力和磨損情況,綜合各項性能要求提出了 “4 倍口徑法則”。但該模型假設條件苛刻,不能完全運用于實際電樞運行過程;宋聯美等[26]在自制的載流電弧試驗機上進行了極性對載流電弧的演化過程和燒蝕影響試驗,結果表明:不同極性條件下的載流電弧能量不同,陽極材料蒸發氣化是電弧燃蝕的主要因素,抑制陽極材料的蒸發氣化,縮短樞軌間電弧存在時間能有效減輕電樞電弧磨損,這為保護電樞和減少電樞耗材提供了理論思路。但是該試驗未考慮客觀磁場的存在以及電樞高速運動下的機械摩擦熱對試驗結果的干擾。張玉燕等[27]在傳熱學理論的基礎上建立了電接觸摩擦副的二維有限元模型,并進行電接觸構件表面溫度測量試驗,以電樞為研究對象,觀察了電樞最高溫度出現的時間點以及隨電流、滑行距離以及接觸面摩擦因數等等參量的變化趨勢,探究了電樞高溫升的因素,為高速載流滑動電接觸中電樞材料的選取及如何降低溫升、提高電接觸性能提供了參考依據。但是該試驗和模擬模型都以單一變量進行研究,未考慮諸如接觸面摩擦因數在滑動過程的動態變化對試驗結果的影響。綜合以上研究可以發現,全面考慮服役多因素耦合的研究仍然存在不足。
-
2.2 電樞自身參數
-
對于電樞自身參數,研究者們通過調整不同的電樞尺寸,包括口徑高度、尾部長度、尾翼傾角等,設計樞軌間過盈尺寸、接觸方式等,觀察電樞在不同自身參數和差異化樞軌間狀態下的損傷。
-
LI 等[28]通過試驗研究了電樞口徑高度對電樞尾部沖蝕的影響,總結了不同線電流密度下電樞電流熔體侵蝕的研究結果,并利用有限元軟件 COMSOL 分析了樞軌間的初始接觸位置及其接觸界面的電流密度分布;LI 等[23]根據接觸面金屬液態膜(LMF)和 Reynolds 方程,在溫度、應力和電磁場耦合作用下,建立了熱彈性磁流體力學模型,分析了電樞尾部長度和角度對表面熔化速率和 LMF 厚度的影響,結果表明:一定范圍內電樞尾翼長度越大,電樞表面熔化速度越慢,最小 LMF 厚度越薄; 杜翔宇等[29]通過樞軌間一般的電接觸特性設計了樞軌間理想的接觸壓力,基于反向加載法改進了電樞的過盈尺寸和形態,并對裝配過盈電樞和非過盈電樞的發射器進行仿真研究,觀察發射過程中某些典型時刻電樞內部電流和焦耳熱集中情況。該研究為電樞的結構尺寸設計提供了新的思路,但其研究適應性不強,試驗觀察結果沒有連續性,只適用于某些特殊時刻。CHENG 等[30]采用 ANSYS 與試壓紙相結合的方法對電樞材料接觸特性進行了研究,結果表明:樞軌接觸特性在一定范圍內與電樞材料強度成正比。LIU 等[31]為研究樞軌間接觸方式對電磁軌道發射性能的影響,采用有限元法分別計算了 C 型電樞在不同接觸面積和接觸位置下的電磁推力、電磁壓力和電流密度,并對不同接觸方式下的計算結果進行了比較,結果表明:電樞尾部與軌道的分離會導致電磁壓力急劇下降,電樞尾部與軌道需要保持緊密接觸,以保證穩定的電流傳遞,實現電樞與軌道完全接觸的電氣性能,這對改善樞軌接觸特性以及有效減輕甚至是防止電樞發生電弧磨損具有參考價值。
-
3 典型損傷機制模擬與仿真趨勢分析
-
電樞發生損傷是電-磁-熱-力多場耦合服役環境下的結果。在電磁軌道發射過程中,各種內外界因素的交互作用導致電樞的服役效能下降,其中接觸應力集中、電流密度集中以及熱量集中是電樞發生損傷的三種主要原因。國內外研究者們基于此,通過不同的機制模擬與仿真展開了深入研究。
-
3.1 接觸應力集中
-
樞軌載流摩擦副接觸界面兼具摩擦接觸和電接觸的特性,其共面性和粗糙性導致了損傷機制的多場耦合性,是一種特殊的電接觸形式。宏觀上光滑的接觸表面在微觀上是粗糙不平的,其粗糙度一般使用平均斜度 masp 和平均高度 σasp 進行表證,其中 σasp,u與 σasp,d分別為接觸面上、下兩側凸起的平均高度,masp,u 與 masp,d 分別為接觸面上、下兩側表面的平均斜度。微觀接觸表面示意圖如圖9 所示[32],可以看出微觀有效接觸面是由一個個離散的接觸點構成,以此形成的接觸面為有效接觸面。研究指出有效接觸面積僅為名義接觸面積的 1%左右[3]。這些接觸點承擔著電流傳導和應力承載的作用。
-
圖9 樞軌微觀有效接觸界面示意圖[32]
-
Fig.9 Schematic diagram of the microscopic effective contact interface of the pivot rail[32]
-
一方面,樞軌在加載裝配后會導致接觸應力集中于電樞局部區域。另一方面,預緊力和電磁壓力在發射過程中集中加載于樞軌界面的接觸點,從而帶來接觸應力集中。電樞表面接觸應力集中分布區域如圖10 所示,可以看出有部分區域接觸應力為 0,即失接觸,接觸應力集中于某一塊區域[33]。田振國等[34]在考慮了樞軌間摩擦和電磁熱效應的基礎上,利用 Ansys 軟件分析了樞軌間接觸應力分布隨電樞運動的變化特性。侯俊超[35]基于“Marshall 法則”,利用 ANSYS LS-DYNA 有限元軟件模擬出樞軌間的機械預緊力和電磁壓力,建立了電樞所受接觸應力的理論計算模型。范薇等[36]提出“安克法則”的瞬態應用方法,指出電樞在運動過程中所受接觸力大小應超過“1 g/1 A”,以此規避電樞接觸失效問題。
-
圖10 電樞裝配后表面接觸應力分布[33]
-
Fig.10 Surface contact stress distribution after armature assembly[33]
-
電樞和軌道自身的結構尺寸參數對樞軌間的接觸狀態影響巨大,間接地決定著接觸應力集中的位置。研究者們從電樞和軌道的形狀,大小以及樞軌間匹配性等方向進行思考,研究了避免接觸應力集中的最優結構尺寸參數。白春艷等[37]利用數值分析的方法,研究了 V 形、U 形以及 Saddle 形 3 種不同形狀電樞在發射過程中的接觸應力分布情況,研究表明,在相同的電磁軌道發射系統條件下,V 形電樞的服役接觸應力值最大,Saddle 形電樞的服役接觸應力值最小,故 Saddle 形電樞為最優選擇。馮登等[33]利用 ABAQUS 有限元分析軟件,對固體 C 形電樞各結構參數對接觸應力分布的影響,研究表明減小電樞尾翼長度和增大電樞肩部厚度能促進接觸應力分布的均勻性。李鶴等[38]設計并比較了凸形和凹形兩種不同截面形狀軌道對樞軌接觸特性的影響,其結果顯示凸形軌道具有更好的機械和電流特性。在此基礎上,劉峰等[39]對電樞力學模型進行有限元分析,設計了一種新型 H 形電樞,并通過簡化的懸臂梁模型確定過盈尺寸,以此分析改進前后樞軌界面接觸應力的分布情況,如圖11 所示,可以看到,改進后電樞模型所承受的等效應力由 538 MPa 減小到 446 MPa,接觸應力集中的情況得到改善。馮建源等[40]通過正交試驗分析研究了樞軌間過盈裝配中電樞各結構尺寸參數的匹配性,并對其影響程度進行了排序,其結果顯示,影響程度依次為:翼根寬度>過盈量>尾翼長度>翼尖寬度>肩部高度。
-
同時,接觸應力集中會導致電樞在裝配后各區域載荷不一,出現某塊區域載荷過大或者過小的現象。載荷過小,樞軌載流摩擦副接觸應力不足,發生失接觸或者接觸不良,引起電火花導致電弧磨損和轉捩燒蝕的產生。載荷過大,樞軌載流摩擦副表面接觸點所需承受的壓力增大,在高運動速度下剪切力增大,磨損率提高,摩擦熱和焦耳熱也隨之增加,導致材料熱熔化程度加深,造成電樞損傷情況嚴重。因此,在保證樞軌間基本接觸應力的前提下,找到樞軌損傷率最低的最優載荷值意義重大。 YASAR 等[41]的摩擦磨損試驗結果表明,隨著載荷的增加,載流摩擦因數和磨損率呈現先降低后升高的相同變化趨勢,30~50 MPa 的接觸應力區間內為輕度磨損;50~120 MPa 的接觸應力區間內為中度磨損;小于 30 MPa 和大于 120 MPa 的接觸應力區間為重度磨損。趙曉非等[42]的研究證明了載流摩擦副存在一個最優接觸應力值,但其研究未能形成適用于不同載流條件下最優接觸應力值的系統理論和變化規律。
-
圖11 樞軌間接觸應力分布[39]
-
Fig.11 Contact stress distribution between armature rails[39]
-
3.2 電流密度集中
-
區別于傳統電接觸,電磁軌道發射裝置表現出工作時間短,電流振幅高,電流密度大等特點,具有特殊的電流密度分布特性。這對電樞上電磁力分布和熱場的分布狀態都有一定的影響,是電樞設計不可忽視的一環。
-
分布均勻的電流密度會使電樞在服役工作中表現出更好的力學性能和電接觸性能。然而在實際發射過程中,電樞上瞬態電流密度的分布往往是不均勻的,呈現出在局部區域上電流密度高度集中的態勢,這會加劇電樞局部熱熔化和增加轉捩燒蝕發生的可能性。由于電樞發射時間較短(ms 級),目前對于電樞瞬態電流密度分布特性的研究主要采用數值分析和仿真模擬等手段,利用 COMSOL 建立非理想樞軌接觸界面磁擴散模型和利用 ANSYS 建立樞軌接觸界面電流密度分布計算模型進行計算分析。由此建立了一系列導致電樞上電流集中的物理效應,包括電流趨膚效應(Current skin effect,CSE)、速度趨膚效應(Velocity skin effect,VSE)以及臨近效應(Proximity effect,PE)等[32,43-44],如圖12 所示。
-
圖12 穩態電流分布與三種電流集中的物理效應
-
Fig.12 Physical effects of steady state current distribution with three current concentrations
-
XIA 等[45]研究表明電流趨膚效應在電流熔體侵蝕(CME)中的影響不可忽略。鞏飛等[46]在考慮 VSE 的影響下,通過建立電流熔化波燒蝕的計算模型分析了電流熔化波的形成及傳播過程,在電樞表面得到了一個 U 型燒蝕面。ZHOU 等[47]通過觀察發射過程中的磁熱耦合現象,分析了不同速度下 VSE 對電流密度分布的影響,研究結果顯示,隨著速度的增大,VSE 帶來的電流集中現象愈加明顯,但同時存在一定的速度闕值。LOU 等[48]指出臨近效應加劇了軌道相鄰側電流密度的集中,提出適當增加軌道間距等減小臨近效應的方法,這對降低發射過程中的電樞損傷具有一定的幫助。曹昭君等[49]在結合趨膚效應和臨近效應等相關理論,模擬出靜態電樞電流密度分布特性,其結果表明電流密度主要集中在樞軌接觸界面頭部和電樞邊沿的中部,如圖13 所示[49]。
-
圖13 電樞電流密度集中區域[49]
-
Fig.13 Concentration area of armature current density[49]
-
3.3 熱量集中
-
目前對樞軌載流摩擦副產熱大和溫升高帶來損傷失效問題的研究主要集中在電樞。這是由于在發射過程中,運動電樞與發射出口方向未通過的軌道部分沒有電流通過,相比于電樞溫度較低,在一定程度上能夠傳導部分熱量,起到散熱降溫作用。而電樞一直有大電流通過,且始終與軌道緊密接觸,幾乎不存在散熱功能,是系統的主要熱源之一。因此,電樞溫度能客觀直接地反映電磁軌道發射器內溫度。由于樞軌間自身機械結構和裝配的特殊性,在電磁軌道連續快速發射下電樞溫度隨時間和空間分布不均勻,使得熱量在一定時空內聚集,進而導致電樞損傷。
-
針對電磁軌道發射系統膛內熱效應和發射過程中電樞溫度分布情況,研究者在結合樞軌載流摩擦副中非完全式接觸(Imperfect electric contacts, ImPEC)這一實際接觸模型的基礎上,以電流產熱和摩擦生熱作為樞軌系統中熱量的主要來源進行探索。KIM 等[50]采用電磁有限元軟件 EWAP3D 對樞軌接觸面處電流產熱導致的溫度分布情況進行了仿真模擬,進而推導出熱量集中區域,其結果顯示,電樞最大溫度分布出現在 1 ms 時刻,而非 4 ms 出口時刻。同時,接觸界面以下電樞內部 0.5 mm 處溫升要大于電樞表面。原因在于軌道在發射過程中會起到冷卻降溫的作用。婁建勇等[51]基于 COMSOL 有限元仿真軟件建立了電磁發射裝置動態計算模型,并以此模擬了電樞在發射過程中溫度分布的時空演變過程,如圖14 所示,可以看出,高溫區主要集中在電樞尾端,熱量集中導致電樞尾端率先熔化。王昊 [52] 針對樞軌間溫度場利用有限元軟件 COMSOL 建立了三維模型,研究了溫度分布時空特性,并探討了發射次數、峰值電流和材料電導率對熱量集中的影響。同時,由于樞軌接觸特性,軌道溫度及其熱量會通過傳導間接影響電樞,導致電樞處熱量集中,溫度升高,其表面熱熔化程度也隨之加深。徐偉東等[53]研究發現軌道溫度升高會增加樞軌間接觸電阻,降低電樞初速,使得電樞在低速階段持續時間過長,加劇了電樞的載流摩擦磨損。
-
圖14 發射過程中電樞溫度云圖[51]
-
Fig.14 Temperature cloud diagram of armature during launching process[51]
-
4 電樞損傷防護優化
-
現如今,對于樞軌載流摩擦副時空演化過程的研究采用的是追溯性模式,即對發射后的電樞進行靜態分析,結合發射動力學模擬,推測實際發射過程中摩擦副的時空演化行為。
-
針對接觸應力集中、電流密度集中以及熱量集中等機制模擬與仿真模型,國內外研究者分別從結構防護、材料防護以及表面防護等方面進行研究,通過優化電樞自身結構和改善材料以達到減輕甚至是避免發射過程中的電樞損傷,以提高樞軌系統的效率和使用壽命。
-
4.1 結構防護
-
在結構防護方面,通過設計電樞自身結構參數及其裝配結構剛度,獲得更加緊密的樞軌結構和更加平整的接觸界面,以此減少樞軌接觸面的粗糙度和電樞尾翼部分的接觸應力集中、電流集中以及熱量集中,從而降低摩擦和燒蝕等損傷的出現。
-
研究者們大多以改善樞軌間的接觸特性和降低電樞發生轉捩燒蝕的可能性為出發點,在縮比試驗和有限元三維模擬仿真中,通過調整電樞形狀、長度、尾翼傾角、頸部角度等參數以及設計電樞內部結構,觀察電樞在極端條件下的服役效能,以此比較出各個參數在不同匹配機制下的最佳值。GUO 等[54]在電樞脈沖電流產生的沖力特性基礎上,對常見的 C 形電樞和新設計的凹形電樞分別進行仿真和試驗驗證,對比了兩種電樞在相同電流服役環境下的力學性能,試驗結果顯示新設計的凹形電樞具有更好的力學性能,損傷率低。隨后,以此結果探索電樞結構設計時應考慮的方面,包括機械設計、電流和熱量分布、推動有效負載的機械結構優化以及質量最小化等。這對于后續研究電樞的穩定性以及防止電樞在發射過程中發生轉捩和燒蝕具有一定的參考價值。
-
LIU 等[55]在分析電樞內電流和電動勢的分布后,通過電磁-結構耦合的方法進行一系列的仿真分析,得到了不同長度電樞接觸參數與接觸效率之間的關系,并且提出了一種“反向加載”的方法設計電樞結構,如圖15 所示,將傳統的直線型電樞替換為彎曲型電樞,結果表明彎曲型電樞的接觸效率大大提高。CHEN 等[56]研究了矩形口徑軌道炮單片 C 型電樞的幾個關鍵參數,在分析電樞質量、電樞與軌道的電磁接觸力、電樞尾部機械強度和電感梯度的基礎上,提出了矩形口徑軌道炮單片 C 型電樞關鍵參數的關系,結果表明:尾翼傾角的增大可以減小電樞質量,提高電樞尾部的機械強度,但會降低電樞與導軌之間的電磁接觸壓力。減小電樞高度與電樞寬度之比可以顯著提高電感梯度,進而提高發射系統效率。
-
圖15 “反向加載”電樞結構示意圖[55]
-
Fig.15 Schematic diagram of the "reverse loaded" armature structure[55]
-
LIU 等[57]在樞軌過盈配合的計算結果上建立了多物理場耦合模型,以溫度和熱應力等方面為出發點,提出了一種兩端干涉的新型電樞結構設計,并通過試驗比較,新型電樞能夠在發射過程中保持較好的穩定性,大大降低了熱應力對電樞發射性能的影響。TANG 等[58]通過仿真模擬,對凹弧表面 C 形電樞(ASCA)的表面弧的半徑(r)和中心角(θ) 進行研究,得到了在不同電流密度下的最優值。同時,還有研究者以電樞內部結構為研究對象,設計出在電樞內部放置一個潤滑物儲蓄池,通過慣性作用,在發射過程中不斷將潤滑物質釋放到樞軌接觸位置,以確保在每一次發射以及在發射全過程位置上均存在此潤滑物質,其發射前與發射中狀態如圖16 所示[59]。
-
圖16 潤滑物儲蓄池電樞[59]
-
Fig.16 Lubricant savings pool armature[59]
-
4.2 材料防護
-
在材料防護方面,研究者以電樞所需優異性能為出發點,包括高導電性、高硬度、高導熱性、高耐磨性、耐高溫、抗電弧燒蝕性和質量低等,聚焦于金屬材料,通過對比研究各種電樞材料在電磁交互復雜環境下的性能優劣,同時考慮與軌道材料間的匹配性,以此減少在發射過程中樞軌摩擦副的損傷。
-
ALTENHOF 等[60]對結構設計相同的鋁、鎂電樞進行了沖擊試驗和耐撞性評價,結果表明:在峰值沖擊載荷近似相等的情況下,鋁電樞比鎂電樞具有更高的能量吸收率。HINAJE 等[61]通過比較鋁、銅、鎢、銀、鎳等 5 種材料的電樞,得出了電樞材料必須具有極高電導率和低密度的結論。付磊等[62]利用同步感應電磁推進系統,使用 MagNet 有限元軟件建立了單級同步感應電磁推進裝置的仿真模型,并對比分析了鋁、銅、鎢、銀、鎳等 5 種材料電樞的基本物理屬性,如表1 所示[62]。可以看出,鋁的電阻率為 2.655×10−8 Ω·m,密度為 2 700 kg·m−3,綜合考慮高導電率和低密度兩種因素下,鋁質材料為最適宜的選擇。因此,對鋁進行合金化以加強其強度、硬度、抗燒蝕以及導電率等各方面的性能,這對于改善電樞效能具有重要意義。
-
表1 電樞制造材料[62]
-
Table1 Armature manufacturing materials[62]
-
鋁合金長期以來在各大領域應用廣泛,特別是飛機和航空航天,鋁合金都占據著重要的地位。然而,電磁軌道發射過程中的極端服役環境對鋁合金的高強度、高導電性、高硬度以及高熔點提出了更高的要求。目前,大多數方法是通過在一定程度上犧牲電導率來提高力學性能,如合金化法和復合材料法。合金化方法是通過固溶強化、析出強化、細晶強化、變形強化等手段對基體進行強化。在高強高導合金的實際生產和應用中,采用單一的強化方法往往是非常有限的,多種強化方式相結合是主流趨勢。復合方法是通過添加第二相顆粒、晶須以及纖維來增強鋁基體。高強度鋁合金是以 Al-Zn-Mg-Cu 系為主的合金。自 20 世紀 30 年代以來,全球許多國家對 Al-Zn-Mg-Cu 系合金進行了大量的研究。發展至 20 世紀 80 年代,隨著快速凝固/ 粉末冶金(RS/PM)工藝的愈發成熟,成功制備出抗拉強度達 700 MPa 以上的 7 系超高強合金,這將 Al-Zn-Mg-Cu 系合金推向了一個更高的水平[63-64]。至今,各國開發出的 Al-Zn-Mg-Cu 系高強合金牌號達幾十種,部分合金成分如表2 所示[63]。其主要的顆粒相為 η-MgZn2、T-Al2Zn3Mg2。LIN 等[65]通過 Johnson-cook 材料模型,在多物理場耦合模型中比較了 7075 鋁合金和 6061 鋁合金在不同電流下的失效時間,如圖17 所示,可以看出,7075 鋁合金具有更高的載流能力,表明其具有更高的屈服強度。同時相關試驗指出,6 系鋁合金具有更高的韌性,在發射出口處得到的電樞不破碎,結構完整性的保持效果更佳。在后續電樞材料的研究中,針對 6 系和 7 系鋁合金的選擇上還有待進一步研究。
-
表2 Al-Zn-Mg-Cu 系高強合金成分表(質量分數/%)[63]
-
Table2 Composition table of Al-Zn-Mg-Cu high-strength alloys (wt.%) [63]
-
通過對 Al-Zn-Mg-Cu 系鋁合金進行合金化以達到增強其各方面物理性能的目的,這對于保障電磁軌道發射過程的完整性和可靠性起到了極大的積極作用。值得注意的是,由于鋁自身低熔點和高化學反應活性的屬性,在發射過程中電樞不可避免地會發生熔化摩擦磨損,進而使得樞軌間產生材料轉移,在軌道表面形成鋁熔凝沉積層[66-67],即軌道黏鋁問題,如圖18 所示。一方面,電樞在發射過程中,其表層材料發生熔化,于銅軌道表面形成液態潤滑層。這會使得樞軌接觸由完全的“固-固”接觸在短時間內轉換為“固-液-固”接觸。該接觸方式在一定程度上能降低電樞與軌道間的粗糙度,有利于減少樞軌系統運動過程中的摩擦損傷;另一方面,在軌道冷卻的作用下,電樞熔化物會與軌道發生機械結合和化學結合,在軌道表面出現機械黏著物和化合物,例如鋁合金、Al2O3 等,使得軌道表面產生大量的微凸起硬質顆粒,惡化樞軌接觸效果導致磨粒磨損增加,降低了樞軌發射系統的精確性和使用壽命。同時,這也會影響脈沖輸出電流的持續性和穩定性,導致電樞的出口速度不能達到預期效果,此影響會隨著發射次數增加而導致的沉積層累積厚度增加而越來越顯著。因此,軌道表面鋁熔凝沉積層對樞軌摩擦副的影響具有雙面性,二者存在競爭關系。在后續電樞材料的選擇中,如何平衡二者的影響效果,減小樞軌接觸面間隙,優化接觸狀態以提高電磁軌道發射系統的效率也是研究重點之一。
-
圖17 電樞在不同電流下的失效時間[65]
-
Fig.17 Failure time of armature at different currents[65]
-
圖18 軌道表面鋁熔凝沉積層
-
Fig.18 Aluminum fusion deposits on the surface of the rail
-
4.3 表面防護
-
在表面防護方面,不同研究者在明晰電樞表面性質的基礎上,根據所需改善電樞的不同物理性能,采取不同的表面強化技術制備了貼合度較高的不同材質表面涂層。DROBYSHEVSKI 等[68]在樞軌接觸界面注入一層液體,在考慮了速度趨膚效應、能量耗散以及熱傳導等因素,研究了液態涂層對樞軌間滑動電接觸性能的影響,結果表明:液態涂層可以顯著抑制速度趨膚效應,減少接觸界面的焦耳熱和摩擦熱,但對于如何保持液態涂層的完整性和防止流失方面的研究不夠深入。
-
同時,在表面涂層的設計過程中,還應避免涂層材料在發射過程中因摩擦和熔化而丟失過快造成樞軌間的接觸不良。GHASSENMI 等[69]采用了一種新型的電樞設計,將具有良好導電性的銦液膜添加到電樞表面,研究了該涂層對樞軌界面間熱感應及磁感應分布的影響,結果表明:使用液態銦涂層不僅提高了樞軌界面間的導電性,還減少了摩擦并遲緩了電樞的熔化。LI 等[70]從材料熔點和硬度的角度出發,提出鎢可以作為電樞表面的涂層材料,設計了涂層的形狀和厚度,通過計算涂層與基體之間的剪切力,確定最佳涂層成形工藝,并分析了涂層對電接觸性能、系統效率和彈丸刨削閾值速度的影響,結果表明:涂層與基體之間的最大剪切力在 171 MPa 以上,激光熔覆技術可以滿足工藝要求,涂層處理后,樞軌間的接觸電阻增加了 6%。
-
陳建偉等[71]利用錫合金的高導熱性、低膨脹系數和高導電性等優點,制備了錫合金導電鍍層,并計算了鍍層電樞/軌道的接觸電阻,分析了錫合金在電流作用下的特性以及對電樞運動特性的影響,結果表明:錫合金鍍層電樞較普通 U 型電樞的炮口速度提高大約 15%。杜傳通等[72]制備了一層石墨烯涂層在電樞表面,并進行了相關理論分析和仿真研究,結果表明:石墨烯涂層不僅能改善樞軌界面間的電接觸狀態,在提高電樞速度、減少界面間熱量產生等方面具有一定的積極影響。如圖19 所示是普通電樞與添加石墨烯涂層后電樞的發射試驗對比,可以看出石墨烯涂層具有抗電弧燒蝕和潤滑的作用。 LIU 等[73]從復合涂層材料的角度出發,以 Cu 作為硬底材、Sn-GE 作為軟導電潤滑膜,在電樞用鋁合金表面制備了一層復合涂層,并通過載流試驗檢測其各項性能,結果表明:該復合涂層在降低摩擦因數和減少電弧燒蝕等方面均有一定幫助。
-
圖19 電樞發射試驗前后對比[71]
-
Fig.19 Before and after armature emission experiment[71]
-
綜合以上研究者的研究成果,可以看出,滿足樞軌載流摩擦副材料應用化需求的電樞表面涂層應具有以下性能:
-
(1)具有良好的導電性和較高的熔點,以減少接觸界面產生的焦耳熱導致的電樞熔化。
-
(2)具有較高的硬度,以減少電樞表面的機械磨損。
-
(3)在設計表面涂層的形狀和制備方法等因素時,應綜合考慮磨損情況以及樞軌間的抗剪切強度,防止在發射過程中涂層因摩擦等不利因素而導致脫落。
-
(4)涂層材料與電樞表面之間應具有較大的親和力。
-
(5)對于復合涂層材料,應從“硬底材-軟導電潤滑膜”結合模式綜合考慮,以此保證涂層兼具硬度高、潤滑性、高導電等性能。
-
對于表面涂層的制備,現階段常用的方法為:電鍍、化學鍍、真空鍍、粉末噴涂、磁控濺射、激光熔覆等。其中,激光熔覆技術冷卻速度快、涂層稀釋率低、熱輸入和畸變較小、熔覆層的厚度范圍大,是一種應用前景廣闊的表面處理技術。目前,相關鋁合金電樞涂層的制備工藝、應用條件及微觀機理的研究不夠成熟,特別是在發射過程的極端工況服役環境下,存在各種物理量耦合場,表面涂層的各項抗沖擊性能和其他物理性能能否達標的相關檢測試驗仍然缺乏系統性的指導。
-
5 結論與展望
-
從國內外研究者對電磁軌道發射用電樞損傷的研究進展可以發現,針對電樞載流摩擦磨損、熱熔化以及轉捩燒蝕等典型損傷,已構建相應的規律體系和理論分析體系,并結合分析模型做出了對應的防護優化,取得了較好的試驗和仿真效果。但對于電樞損傷的形貌演變規律、仿真復現手段以及與軌道損傷特征的對應關系等的研究還不夠深入。主要原因如下:
-
(1)受限于當前的技術手段,對電樞和軌道的損傷探究都是基于發射后的結果進行。而電樞損傷是單次發射后產生的結果,軌道損傷是多次發射后累積產生的結果,這導致電樞與軌道的分析對象不匹配,所得到的表面損傷機制不具有統一性和相關性。
-
(2)電磁軌道發射過程中,樞軌接觸界面各項性能參數是否變化以及變化趨勢的數據實時顯現手段尚不完備,這導致樞軌載流摩擦副的損傷對發射性能的影響難以量化。
-
(3)電磁軌道發射裝置處于電-磁-熱-力極端工況下,電樞與軌道間的材料轉移不可避免,轉移過程受到樞軌載流摩擦副損傷的嚴重影響。而針對損傷與樞軌間結構變化目前沒有準確高效的三維重構模型以說明兩者間本征關系。
-
對于上述難點和問題,依據電磁軌道發射相關技術要求,未來電樞損傷的研究應著力于以下幾個方面:
-
(1)理清電磁發射極端工況下各物理量場的深度耦合關系,追溯發射過程中電樞形貌演變規律。
-
(2)明晰電磁軌道發射行為的關鍵物理量及其影響機制,包括接觸電阻、摩擦因數等,探索發射過程中樞軌間接觸狀態的變化。
-
(3)構建電磁軌道發射苛刻工況三維分析模型,研究仿真復現技術,探明處于電-磁-熱-力多場耦合下樞軌材料的物性演化。
-
(4)現有防護優化手段尚不能滿足極端服役環境下的結構和性能保持需求。開展新型樞軌材料及其結構的研發是未來的研究重點之一。
免責聲明:本網站所轉載的文字、圖片與視頻資料版權歸原創作者所有,如果涉及侵權,請第一時間聯系本網刪除。
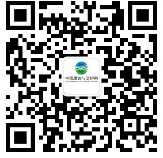
官方微信
《腐蝕與防護網電子期刊》征訂啟事
- 投稿聯系:編輯部
- 電話:010-62316606
- 郵箱:fsfhzy666@163.com
- 腐蝕與防護網官方QQ群:140808414