隨著汽車制造業發展以及鋼鐵冶金技術的不斷提升, 超輕型高強度汽車用鋼的開發與研究已歷經了3個階段的發展. 從上世紀80年代末開始無間隙原子(IF)鋼的廣泛研究, 隨后發展了低合金高強度(HSLA)鋼、雙相(DP)鋼[
當前在Q&P鋼的生產中, 為保證獲得超高強度以及較多的殘余奧氏體, 采取的是提高鋼中C的添加量的方法, 一般C含量都要在0.3%~0.5% (質量分數)[
因此, 本工作以C-Si-Mn系高強鋼為研究對象, 圍繞提高殘余奧氏體含量及其機械穩定性等關鍵問題, 開展合金元素配分工藝及微觀組織控制的研究. 采用在雙相區保溫+奧氏體化淬火+低溫退火的熱處理工藝, 就Mn元素雙相區配分行為對組織演變及力學性能的影響進行了表征. 對探索合金元素配分的理論和機制有重要意義, 為當前開發適用于汽車輕量化發展需求的先進高強鋼提供實踐基礎.
1 實驗方法
實驗用鋼采用50 kg真空熔煉爐冶煉, 其化學成分(質量分數, %)為: C 0.20, Si 0.37, Mn 1.28, P 0.0032, S 0.0014, B 0.0018, 余量為Fe. 實驗鋼的Ac3=844 ℃, Ac1=718 ℃, Ms=345 ℃(Ac3為加熱時先共析鐵素體全部轉變成奧氏體的終了溫度, Ac1為加熱時珠光體向奧氏體轉變的開始溫度, Ms為冷卻時馬氏體初始轉變溫度). 將冶煉后鋼錠鍛造并剪切成50 mm×50 mm×100 mm方坯, 在二輥熱軋實驗機上軋制得到厚度為3.5 mm的熱軋板坯, 經5道次冷軋得到厚度為1.5 mm鋼板.
圖1a為雙相區保溫后直接淬火(I&Q)的工藝流程圖, 采用雙相區760 ℃進行保溫加熱, 保溫時間為600, 1000, 1300和1500 s, 使之生成一定比例的鐵素體和奧氏體, 通過保溫使Mn元素由鐵素體向奧氏體中進行擴散, 之后水淬到室溫, 通過觀測室溫下Mn元素在鐵素體和馬氏體兩相中的元素分布, 驗證雙相區的元素配分行為. 圖1b為傳統淬火+低溫退火(Q&P)處理工藝流程圖, 將實驗用鋼加熱到奧氏體化溫度(AT=930 ℃)并保溫120 s, 使之完全奧氏體化, 然后采用鹽浴淬火使其快速冷卻到Ms~Mf (Mf為冷卻時馬氏體轉變的終了溫度)之間的某一溫度(奧氏體化后冷卻時淬火溫度QT=220 ℃, 由馬氏體含量計算公式Krauss-Koistinen-Marburger公式[
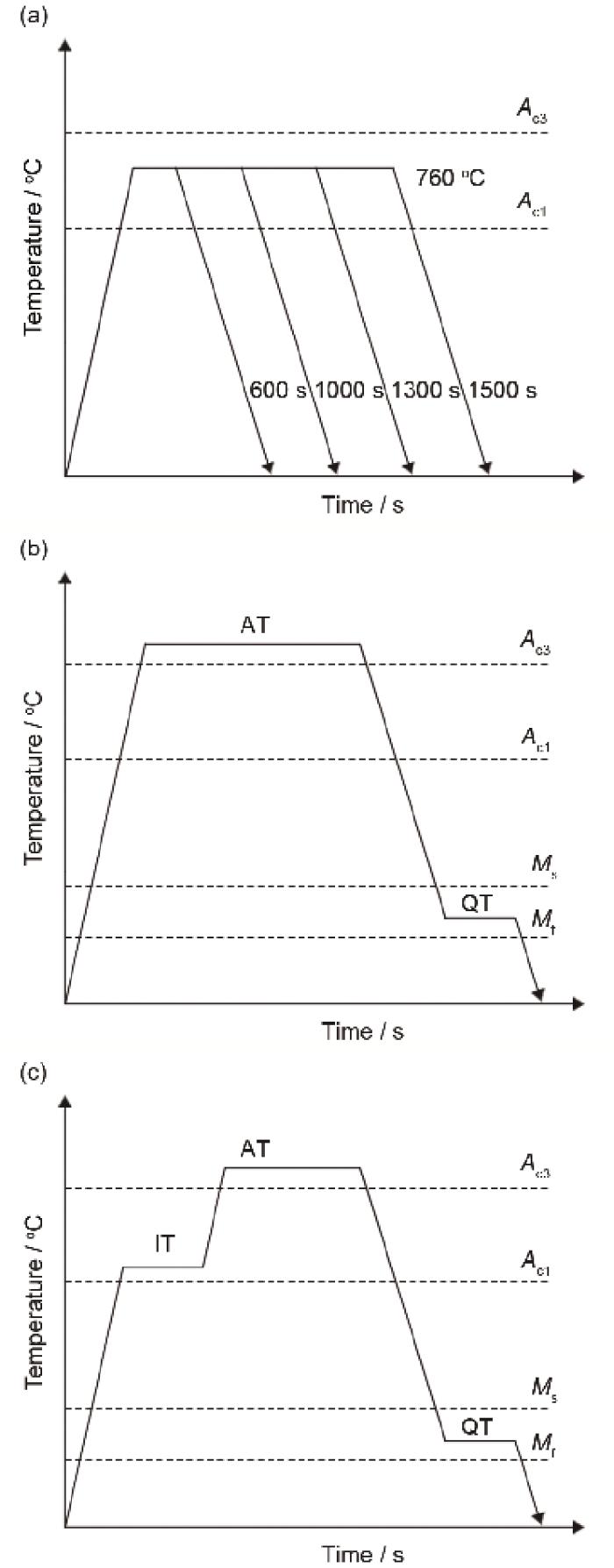
圖1
Fig.1 不同熱處理工藝流程圖
將試樣經不同工藝處理, 經過研磨、拋光和4%硝酸酒精(體積分數)浸濕后, 采用Axiovert200MAT光學顯微鏡(OM)和S-4800場發射掃描電鏡(SEM)進行顯微組織觀察及分析; 采用線切割按照GB/T228-2002標準制取拉伸實驗樣品, 在WBW-600B液壓萬能試驗機上進行拉伸實驗; 利用D/MAX2500PC X射線衍射儀(XRD)分析實驗用鋼中的殘余奧氏體, 實驗參數為: Cu靶, 步寬0.02°, 功率40 V, 電流150 mA, 實驗角度范圍60°~100°, 速度10 °/min, 測定精確的衍射角2θ和積分強度I, 按國標GB8362-87對殘余奧氏體的體積分數進行分析, 利用奧氏體(220)γ, (200)γ, (311)γ和馬氏體(211)α′, (220)α′晶面的積分強度通過直接比較法[
2 實驗結果及分析
2.1 I&Q工藝Mn元素配分行為
圖2為雙相區760 ℃保溫并淬火后鋼的SEM像. 由圖可知, 試樣的原始組織為鐵素體(F)和珠光體(P)組織, 經雙相區保溫并淬火后, 試樣的室溫組織主要由鐵素體(F)和板條馬氏體(M)組成, 隨著雙相區保溫時間的延長, 室溫馬氏體體積分數逐漸增多, 當保溫時間達到1000 s時, 室溫馬氏體體積分數達到最大值55%, 如圖2d所示. 當保溫時間進一步延長時, 馬氏體和鐵素體兩相趨于平衡, 室溫馬氏體體積分數隨不同保溫時間的變化曲線如圖3所示, 說明在雙相區進行保溫時, 雙相區中奧氏體體積分數會隨著保溫時間的延長逐漸增多直至達到飽和, 之后隨著保溫時間進一步延長, 奧氏體和鐵素體兩相趨于平衡.
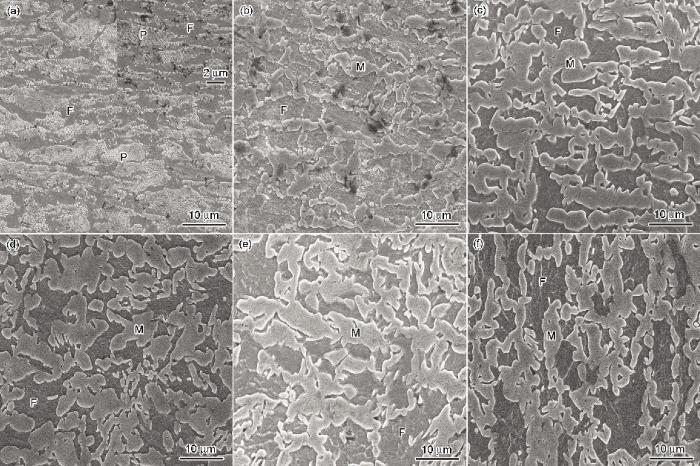
圖2
Fig.2 760 ℃保溫不同時間并淬火后鋼的SEM像
圖4和5為雙相區760 ℃保溫并直接淬火后鋼的EBSD像及Mn元素分布的EMPA像. 由圖可知, 在原始組織中(圖4a), Mn分布均勻, 鐵素體與珠光體中Mn含量基本相等, 當加熱到760 ℃保溫300 s并淬火后, 室溫組織中出現少量馬氏體組織, Mn開始出現不均勻分布現象, 馬氏體中Mn含量稍高于鐵素體, 說明此時雙相區中Mn已經發生了從鐵素體向奧氏體中的擴散. 當保溫時間達到600 s時, 試樣的室溫組織已呈現出典型的馬氏體和鐵素體兩相組織, 由EMPA像中能明顯看到馬氏體中的Mn含量高于鐵素體中的Mn含量. 隨著保溫時間的延長, 向奧氏體中擴散的Mn含量逐漸增多, 當保溫時間增至1300 s時, Mn在鐵素體與奧氏體兩相中化學勢達到平衡, 不再進行兩相間的擴散, 并且當保溫時間為1300 s時雙相區奧氏體中Mn含量達到最大值2.51%, 而隨著時間的進一步延長, 奧氏體和鐵素體兩相雖趨于平衡, 但雙相區組織仍呈現長大趨勢, 使得Mn在奧氏體中含量相對減少, 鋼中馬氏體的Mn含量變化趨勢如圖6所示.

圖3
Fig.3 不同保溫時間對馬氏體體積分數的影響
2.2 Q&P和I&Q&P工藝處理后鋼的微觀組織
圖7為經不同工藝處理后鋼的SEM像. 由圖7a可知, 經Q&P工藝處理后, 室溫組織主要由少量板條狀馬氏體、少量板條間彌散分布的碳化物顆粒和極少量的殘余奧氏體組成, 還存在較多的塊狀組織, 這是經最終淬火時未轉變奧氏體發生馬氏體轉變, 形成的二次淬火馬氏體(M2)或殘余奧氏體(RA), 呈規則幾何形狀, 無明顯析出物. 在傳統Q&P工藝奧氏體化鹽浴淬火過程中, 將得到一定量的板條狀一次淬火馬氏體(M1), 此時C元素由一次淬火馬氏體向未轉變的奧氏體擴散使之趨于穩定, 由于鹽浴淬火冷卻速度較低, 配分過程中一次淬火馬氏體會發生自回火分解, 馬氏體板條邊界較模糊, 產生顆粒狀白色碳化物析出, 而較低的Si含量對碳化物抑制作用較小, 致使最終室溫下鋼的延展性能變差; 之后經水淬至室溫時, 由于冷速較快且C配分對奧氏體的穩定性影響較小, 一部分未轉變的奧氏體發生馬氏體轉變, 室溫組織中出現部分二次淬火馬氏體或殘余奧氏體. 由圖7b可知, 經I&Q&P工藝處理后, 室溫組織主要由大量板條狀馬氏體、少量板條間彌散分布的碳化物顆粒和殘余奧氏體組成, 存在少量的塊狀組織. 經雙相區加熱保溫時, 鐵素體中Mn元素隨著保溫時間的延長向奧氏體中逐漸擴散直至達到化學勢平衡, 之后加熱至奧氏體化溫度, 此時由鐵素體轉變成的奧氏體組織中Mn元素的含量大大降低, 再經鹽浴淬火時, 此部分奧氏體全部轉變為一次淬火馬氏體, 而未轉變的奧氏體由于其Mn元素含量較高, 能穩定到室溫, 而之后經水淬至室溫時, 只有少量Mn元素含量較少的未轉變奧氏體發生馬氏體轉變, 其余則保留至室溫, 而雙相區保溫時, 鐵素體中的C元素由于較高的自由能, 使得其在較短的時間已經完成了向奧氏體的擴散, 而QT階段得到的一次淬火馬氏體由于其C元素含量較低, 致使自回火產生的白色碳化物顆粒較少, 從而室溫組織中板條馬氏體量較多.
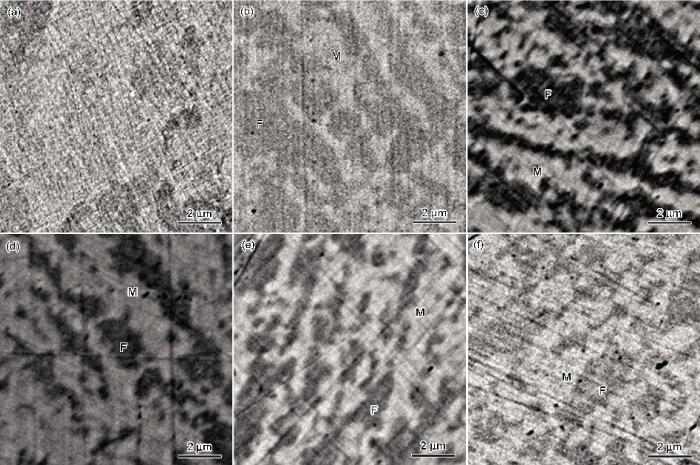
圖4
Fig.4 760 ℃保溫不同時間并淬火后鋼的EBSD像
圖8為經I&Q&P處理后鋼的室溫組織中馬氏體和殘余奧氏體的Mn元素分布情況. 由圖可見, 實驗用鋼經I&Q&P處理后通過EMPA能觀察到Mn元素在室溫組織的馬氏體和殘余奧氏體中較為明顯的不均勻分布情況, 薄膜狀殘余奧氏體在室溫中存在于馬氏體板條間. 從圖8中A和B位置可以看出, 位于馬氏體板條間的殘余奧氏體中Mn元素含量明顯高于馬氏體基體, 這是由于當Mn元素在雙相區達到化學勢平衡時, 雙相區奧氏體中Mn元素含量達到最大值, 又經淬火+低溫退火處理后, 這部分富Mn的奧氏體經鹽浴淬火時可以穩定下來, 該部分未轉變的奧氏體由于較高的Mn元素含量使得大部分能夠保留到室溫形成殘余奧氏體, 只有少量會發生馬氏體轉變. 可見, I&Q&P工藝對穩定鋼中殘余奧氏體以及提高室溫殘余奧氏體含量起到了良好的作用, 而這種軟硬搭配的多相組織結構也可為實驗鋼提供更高的強度和塑性.
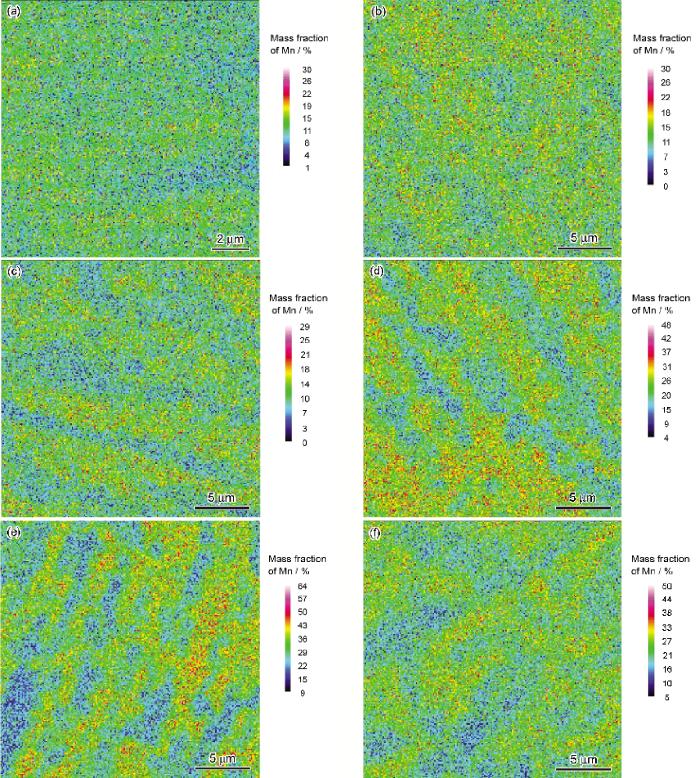
圖5
Fig.5 760 ℃保溫不同時間并淬火后鋼中Mn元素分布的EMPA像
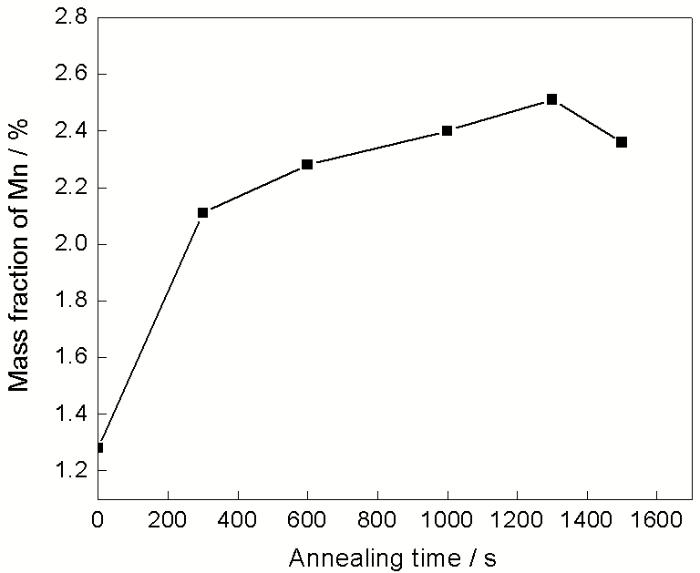
圖6
Fig.6 760 ℃保溫不同時間并淬火后鋼中馬氏體的Mn含量變化趨勢
2.3 Q&P和I&Q&P工藝處理后鋼中殘余奧氏體含量和力學性能
圖9為實驗鋼經Q&P工藝和I&Q&P工藝處理后殘余奧氏體的XRD譜. 由圖可知, 直接經Q&P處理的試樣中有2個奧氏體峰, 且峰值強度偏低, 而經I&Q&P處理后的試樣的XRD譜中明顯觀測到在60°~100°間又出現了2個晶面的奧氏體衍射峰, 分別是(311)γ和(220)γ, 說明雙相區Mn元素的擴散對奧氏體起到良好的穩定作用, 從而使室溫下保留了更多的殘余奧氏體, 提高了鋼的塑性.
經Q&P和I&Q&P工藝處理后鋼的力學性能見表1. 由表可知, 實驗鋼的原始力學性能中, 抗拉強度為640 MPa, 延伸率為26.0%, 其原始組織為鐵素體和珠光體組織. Q&P工藝處理后, 其抗拉強度為1560 MPa, 延伸率為8.3%, 強塑積為12948 MPa·%, 而經I&Q&P處理后, 與Q&P工藝相比, 鋼的抗拉強度略有降低為1310 MPa, 延伸率有顯著提高為12.0%, 強塑積為15720 MPa·%, 強塑積比Q&P工藝下提高了約20%.
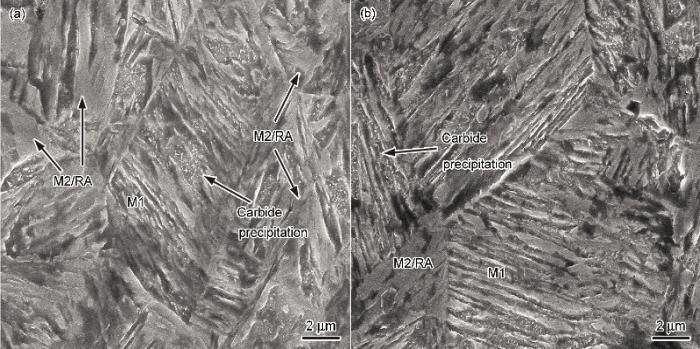
圖7
Fig.7 不同工藝處理后鋼的SEM像
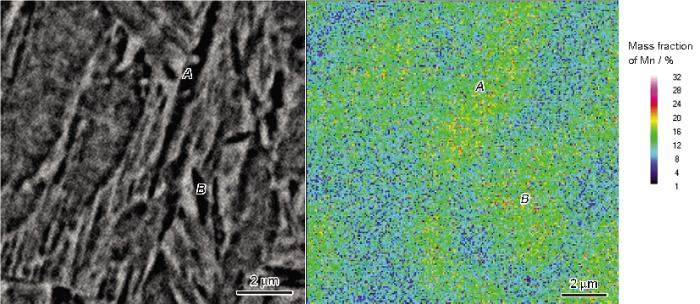
圖8
Fig.8 I&Q&P處理后鋼中馬氏體和殘余奧氏體的Mn元素分布
3 I&Q&P工藝各階段組織演變分析討論
圖10為I&Q&P工藝各階段鋼的組織演變模型. γI為雙相區奧氏體,γA表示雙相區鐵素體在AT階段轉變而成的奧氏體, γ′表示為雙相區奧氏體在AT階段轉變而成的奧氏體, γ″表示為穩定到室溫的殘余奧氏體, M1表示為鹽浴淬火階段先形成的一次淬火馬氏體, M2表示為最終水淬階段形成的二次淬火馬氏體. 由圖可知, 實驗用鋼經冷軋后室溫組織主要為鐵素體和珠光體, 其中各相Mn元素含量相同. 加熱到雙相區進行保溫時, 珠光體首先轉變為奧氏體γI, 隨著保溫時間的延長, 雙相區奧氏體逐漸增多直至達到兩相平衡, 而鐵素體中Mn元素也會伴隨時間的延長向奧氏體中發生擴散, 直至達到化學勢平衡, 此時鋼的組織為鐵素體和奧氏體, 且奧氏體中Mn元素含量明顯高于鐵素體. 隨后升溫至奧氏體化(AT)進行保溫時, 雙相區的鐵素體轉變為Mn元素含量較少的奧氏體γA, 而雙相區的奧氏體γI轉變為富Mn的奧氏體γ′, 之后鹽浴淬火至QT階段時, 奧氏體γA由于其穩定性元素Mn含量較少使得其在淬火時全部轉變為一次淬火馬氏體M1, 而富Mn的奧氏體γ′在此階段則大部分可以保留下來, 只有少量發生馬氏體轉變, 且未轉變的奧氏體γ′中Mn元素含量高于一次淬火馬氏體. 最后經水淬至室溫的過程中, 奧氏體γ′由于較高Mn元素含量最終能夠穩定到室溫, 得到殘余奧氏體γ″, 只有少量發生二次馬氏體轉變, 而殘余奧氏體γ″中Mn元素含量也明顯高于鋼中馬氏體的Mn元素含量.
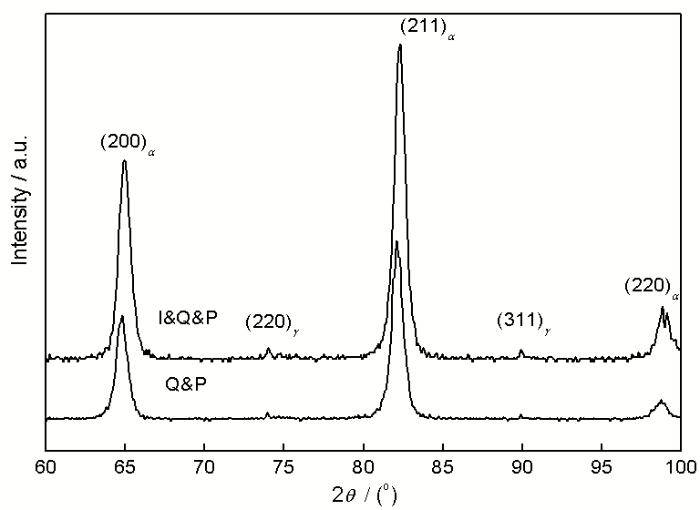
圖9
Fig.9 不同工藝下鋼的XRD譜
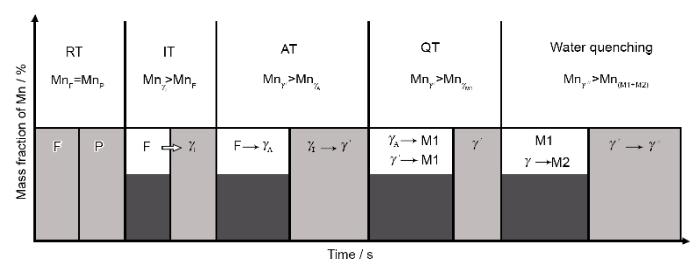
圖10
I&Q&P工藝各階段組織演變過程模型
值得指出的是, 經Q&P工藝處理的試樣只含有少量由C配分作用穩定的殘余奧氏體, 而I&Q&P工藝處理后的試樣其室溫殘余奧氏體由富Mn的殘余奧氏體和經C配分作用穩定的殘余奧氏體共同組成, 富Mn的殘余奧氏體其尺寸往往很小, 且Mn元素含量較高, 從而使高強鋼具備了更優異的塑性.
4 結論
(1) 實驗用鋼經雙相區保溫時, 隨著保溫時間延長, 奧氏體體積分數逐漸增多, 保溫時間為1000 s時, 室溫馬氏體體積分數達到最大值55%; 而鐵素體中向奧氏體擴散的Mn元素含量也逐漸增多直至其在兩相間達到化學勢平衡, 并且當保溫時間為1300 s時, 奧氏體中Mn元素含量達到最大值2.51%.
(2) 經Q&P工藝處理后, 室溫組織為大量塊狀馬氏體、少量板條狀馬氏體、少量板條間彌散分布的碳化物顆粒和極少量的殘余奧氏體, 而經I&Q&P工藝處理后, 室溫組織中塊狀馬氏體含量大幅減少, 主要為板條狀馬氏體形貌, 而殘余奧氏體含量顯著增多, 達到4.3%, 抗拉強度為1310 MPa, 延伸率為12.0%, 強塑積達到15720 MPa·%以上.
(3) Q&P工藝處理后鋼中只含有少量由C配分作用穩定的殘余奧氏體, 而I&Q&P工藝處理后鋼中殘余奧氏體由富Mn的殘余奧氏體和經C配分作用穩定的殘余奧氏體組成, 顯著提高室溫下鋼中殘余奧氏體的含量和機械穩定性, 從而提高高強鋼的室溫成形能力.
免責聲明:本網站所轉載的文字、圖片與視頻資料版權歸原創作者所有,如果涉及侵權,請第一時間聯系本網刪除。
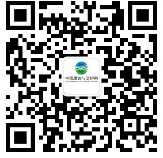
官方微信
《腐蝕與防護網電子期刊》征訂啟事
- 投稿聯系:編輯部
- 電話:010-62316606
- 郵箱:fsfhzy666@163.com
- 腐蝕與防護網官方QQ群:140808414