鋁及鋁合金是目前應(yīng)用最廣泛、加工技術(shù)最成熟的有色金屬材料。因其具有密度小,強(qiáng)度高及導(dǎo)電、導(dǎo)熱性能好等優(yōu)點(diǎn),在航空航天、電子、建筑及交通等諸多領(lǐng)域應(yīng)用廣泛。
常用的鋁合金表面處理技術(shù)有陽(yáng)極氧化和化學(xué)氧化等。化學(xué)氧化可以提高鋁合金的耐蝕性及漆膜結(jié)合力,在涂漆前處理和復(fù)雜鋁合金零件表面處理中占有重要地位。目前,航空鋁合金化學(xué)氧化普遍采用鉻酸鹽鈍化工藝,該技術(shù)已經(jīng)十分穩(wěn)定成熟。但該工藝中采用的六價(jià)鉻是劇毒材料,在美國(guó)環(huán)境保護(hù)局(EPA)最危險(xiǎn)材料表中排名第17位,對(duì)人體和環(huán)境具有極大的有害性。歐盟環(huán)保條例(日落計(jì)劃)規(guī)定,自2017年9月21日起,交往歐盟的產(chǎn)品不能再含有六價(jià)鉻(允許有4年的緩沖期)。因此,研發(fā)無(wú)六價(jià)鉻的鋁合金化學(xué)氧化工藝勢(shì)在必行。以下就無(wú)六價(jià)鉻化學(xué)氧化工藝的國(guó)內(nèi)外發(fā)展?fàn)顩r和未來(lái)趨勢(shì)進(jìn)行綜述。
01 鋯鹽體系化學(xué)氧化
鋯鹽體系化學(xué)氧化廣泛用于鋁合金表面處理。在化學(xué)氧化成膜過(guò)程中,首先發(fā)生的是鋁的蝕刻反應(yīng),如下式(1)所示;然后,氟鋯酸鹽水解反應(yīng)生成化學(xué)轉(zhuǎn)化膜,如下式(2)~(4)所示。
2Al+6H+→2Al3++3H2 (1)
2Al3++ZrF62-+3H2O→ZrO(OH)2↓+2AlF3+4H+ (2)
4Al3++3ZrF62-+3H2O→3ZrOF2↓+4AlF3+6H+ (3)
2Al(OH)3+ZrF62-→(AlO2OH)2ZrF2↓+2F-+2HF (4)
周琦等用鋯酸鹽處理LY12鋁合金,獲得了厚度適中、耐蝕性較好且結(jié)合力較佳的化學(xué)氧化膜。
王嬌等發(fā)現(xiàn),2024-T3鋁合金表面存在CuAl2等金屬間化合物,所以鋯酸鹽化學(xué)氧化膜易產(chǎn)生裂紋,導(dǎo)致耐蝕性下降,他們用氟鋯酸鉀和偏釩酸鈉對(duì)2024-T3鋁合金進(jìn)行化學(xué)氧化,得到了致密、無(wú)裂紋的釩鋯復(fù)合轉(zhuǎn)化膜。
SHIDA等采用鋯鹽以及1,12-十二烷基二磷酸在1100鋁合金上制備了磷-鋯鹽系化學(xué)轉(zhuǎn)化膜,在鹽霧試驗(yàn)中,該化學(xué)轉(zhuǎn)化膜有效地保護(hù)了鋁基材,顯著提高了其耐蝕性。
02 鉬酸鹽化學(xué)氧化
鉬和鉻為同副族元素,在化學(xué)性質(zhì)上十分相似。但鉬酸鹽毒性較低并且可以和其他物質(zhì)協(xié)同作用,有希望替代六價(jià)鉻成為無(wú)鉻化學(xué)氧化膜。
徐臨超等采用鉬酸鹽和氟硼酸鹽、乙酸鈷在一定條件下得到了黑色化學(xué)氧化膜,其膜層的耐蝕性甚至優(yōu)于鉻酸氧化膜。
LIANG等采用鉬酸鹽溶液處理AA8021鋁箔樣品,通過(guò)掃描電子顯微鏡、X射線能譜儀和X射線光電子能譜研究了鉬酸鹽轉(zhuǎn)化涂層的微觀結(jié)構(gòu)和組成。結(jié)果發(fā)現(xiàn),鉬酸鹽轉(zhuǎn)化涂層主要由MoO3,(MoO3)x(P2O5)y和Al2(MoO4)3組成。此外,他們通過(guò)電化學(xué)阻抗譜和電化學(xué)極化曲線評(píng)估了氧化處理過(guò)的鋁箔的耐蝕性。結(jié)果表明,所有具有鉬酸鹽轉(zhuǎn)化涂層的鋁箔比裸鋁箔具有更好的耐蝕性,而且處理溫度為40 ℃時(shí),鋁箔表現(xiàn)出最佳的耐蝕性。
03 鈦系化學(xué)氧化
鈦的性質(zhì)與鉻也十分相近,在空氣中與氧氣有較強(qiáng)的親和力,在一定條件下可形成氧化膜,具有一定的耐蝕性。
XIA等采用H2TiF6溶液對(duì)鋰電池中的復(fù)合鋁箔進(jìn)行化學(xué)氧化處理,并且通過(guò)掃描電子顯微鏡、X射線能譜儀、X射線光電子能譜、原子力顯微鏡等表征其組成、生長(zhǎng)過(guò)程和最終形態(tài),再通過(guò)鹽霧試驗(yàn)測(cè)試其耐腐蝕性能。結(jié)果表明:H2TiF6溶液處理得到的轉(zhuǎn)化膜層是一種多組分膜層,主要由金屬氧化物(TiO2和Al2O3)和金屬氟化物(AlF3)組成。鹽霧試驗(yàn)結(jié)果表明,經(jīng)過(guò)鈦系化學(xué)氧化處理的鋁箔比未經(jīng)處理和經(jīng)過(guò)堿清洗的鋁箔具有更好的耐蝕性。盡管未經(jīng)處理的鋁箔和經(jīng)堿清潔的鋁箔由于加工而存在彎折,但這些鋁箔都顯示出較光滑的表面,而經(jīng)過(guò)H2TiF6處理的鋁箔表面除了彎折造成的褶皺之外,還存在許多針狀結(jié)構(gòu),導(dǎo)致其表面更粗糙。因此,鈦系化學(xué)氧化是一種有效提高鋰離子電池組件中鋁/聚合物復(fù)合膜耐蝕性和剝離強(qiáng)度的方法。
LIU等采用鈦/鋯鹽和氨基三亞甲基磷酸對(duì)7A52鋁合金進(jìn)行化學(xué)氧化,得到了表面粗糙度較大、耐蝕性較好的無(wú)鉻化學(xué)轉(zhuǎn)化膜,并且基體和環(huán)氧底漆之間的黏結(jié)強(qiáng)度從未氧化時(shí)的7.97 MPa增加到16.23 MPa,結(jié)合力得到顯著提高。在未經(jīng)氧化處理的鋁合金表面觀察到一些微小的白色斑點(diǎn)及一些凹坑,白色斑點(diǎn)為金屬間顆粒,凹坑的出現(xiàn)與鋁局部溶解引起的金屬間顆粒剝落有關(guān)。經(jīng)過(guò)化學(xué)氧化處理后,鋁合金表面形成均勻而致密的轉(zhuǎn)化膜,轉(zhuǎn)化膜層主要由形狀不規(guī)則的顆粒組成。這些顆粒的平均直徑在3 μm以下,每個(gè)顆粒與其周圍的顆粒緊密結(jié)合。這種結(jié)構(gòu)的形成可能歸因于合金元素的電化學(xué)或催化作用。此外,轉(zhuǎn)化膜上還有一些細(xì)小的裂紋,這是由干燥脫水過(guò)程中產(chǎn)生的相互應(yīng)力引起。顆粒的隆起和凹陷有利于增大鋁合金表面粗糙度,提高鋁合金與漆膜間的結(jié)合力。
ZUO等使用單寧酸作為鈦/鋯鹽化學(xué)轉(zhuǎn)化液中的促進(jìn)劑在6063鋁合金表面制備了新型化學(xué)轉(zhuǎn)化膜,并使用電化學(xué)測(cè)試研究轉(zhuǎn)化膜在3.5% NaCl溶液中的腐蝕行為。結(jié)果表明:與傳統(tǒng)的Ti-Zr處理(TZ)轉(zhuǎn)化膜相比,改性的Ti-Zr基轉(zhuǎn)化膜(MTZ)顯示出更光滑和更密集的形態(tài);MTZ膜是一種多組分化學(xué)轉(zhuǎn)化膜,其主要由金屬氧化物(TiO2,ZrO2,V2O5,Al2O3),氟化物(AlF3和ZrF4)和金屬有機(jī)配合物組成;與TZ膜相比,MTZ膜具有更好的耐腐蝕性能。
04 鋰鹽化學(xué)氧化
20世紀(jì)90年代,研究人員發(fā)現(xiàn)利用堿性鋰鹽溶液可以制備鋰-鋁轉(zhuǎn)化膜,對(duì)鋁基材進(jìn)行保護(hù)。
鄭輔養(yǎng)等用鋰鹽代替鉻酸鹽對(duì)鋁合金進(jìn)行化學(xué)氧化處理。結(jié)果發(fā)現(xiàn):鋰離子有利于鋁在堿性碳酸鹽溶液中的鈍化,成膜離子在鋁基體表面共沉積形成鋰鹽轉(zhuǎn)化膜,其實(shí)質(zhì)是由Al3+、Li+、OH-和CO32-等離子組成的復(fù)合鹽。在3.5% NaCl溶液中的浸泡腐蝕試驗(yàn)結(jié)果表明,堿性鋰鹽溶液化學(xué)氧化處理可明顯提高基體的耐蝕性。
MARCOEN等采用鋰鹽作為2024-T3鋁合金有機(jī)底漆涂料的腐蝕抑制劑,使用人工劃線對(duì)鋁合金表面進(jìn)行破壞,并將其暴露在中性鹽霧中,然后通過(guò)飛行時(shí)間二次離子質(zhì)譜分析(ToF-SIMS)研究該保護(hù)層的組成和生長(zhǎng)規(guī)律,并分析了鋰基保護(hù)層的形成機(jī)理。ToF-SIMS成像技術(shù)成功監(jiān)測(cè)到人工1 mm劃線區(qū)域浸出鋰鹽的橫向擴(kuò)散:當(dāng)劃線區(qū)暴露在中性鹽霧中時(shí),鋰鹽浸出,進(jìn)入涂層缺陷中,誘導(dǎo)2024-T3鋁合金基體上含鋰水合氧化鋁表面層(假勃姆石層)的生長(zhǎng)。隨著在中性鹽霧中暴露時(shí)間的延長(zhǎng),缺陷中的鋰鹽含量以及局部pH增加,表面層開(kāi)始通過(guò)鋁的陽(yáng)極溶解發(fā)生部分降解,與此同時(shí),Al-Li層狀雙氫氧化物層開(kāi)始生長(zhǎng)并最終覆蓋在2024-T3鋁合金表面,對(duì)其起到保護(hù)作用。基于ToF-SIMS獲得的結(jié)果,他們將鋰基保護(hù)層的形成分為5個(gè)階段,如圖1所示。
圖1 保護(hù)層生長(zhǎng)階段示意圖
階段Ⅰ:
劃線區(qū)首先暴露于中性鹽霧中,水性電解質(zhì)引起鋰鹽從有機(jī)涂層浸入劃線區(qū),鋰鹽浸出導(dǎo)致劃線區(qū)pH增加至堿性,在氯化物存在的情況下引起鋁的陽(yáng)極溶解。
階段Ⅱ:
鄰近有機(jī)涂層的保護(hù)層開(kāi)始形成,金屬表面附近的局部pH為9~10,這種堿性條件導(dǎo)致假勃姆石層的形成,并且其中摻入了少量鋰后,鋰-假勃姆石層(L-PB)開(kāi)始形成。
階段Ⅲ:
隨著鋰鹽進(jìn)一步浸入劃線區(qū),L-PB層向劃線區(qū)的中心橫向生長(zhǎng),此過(guò)程相對(duì)較快。當(dāng)鋰鹽含量超過(guò)有機(jī)涂層附近的某個(gè)閾值后,層狀雙氫氧化物(LDH層)開(kāi)始形成。
階段Ⅳ:
在中性鹽霧中暴露較長(zhǎng)時(shí)間后,劃線區(qū)中心鋰離子含量增加,這使得LDH層也可以在劃片的中心生長(zhǎng)。
階段Ⅴ:
圓柱狀的LDH層在表面橫向生長(zhǎng),以犧牲下面的L-PB阻擋層為代價(jià),直到劃痕完全被LDH層覆蓋。
05 稀土金屬化學(xué)氧化
鋁合金稀土金屬化學(xué)氧化膜的制備在很早就開(kāi)始研究。
WANG等采用氨基酸和稀土作為AA5052鋁合金的化學(xué)氧化劑。結(jié)果發(fā)現(xiàn):在AA5052鋁合金表面上形成了L-半胱氨酸和硝酸鈰的復(fù)合轉(zhuǎn)化膜,通過(guò)電化學(xué)測(cè)試發(fā)現(xiàn)有機(jī)稀土復(fù)合轉(zhuǎn)化膜可以減少陽(yáng)極極化,抑制析氫,提高陽(yáng)極利用率,有效阻止了AA5052鋁合金在NaOH溶液中的自腐蝕,顯著提高了堿性鋁-空氣電池的使用壽命。
VALDEZ等采用氯化鈰或硝酸鈰作為主鹽,以H2O2為輔助物質(zhì),在6061-T6鋁合金上制備了鈰基轉(zhuǎn)化膜層。結(jié)果發(fā)現(xiàn):在H2O2和CeCl3·7H2O的體系中化學(xué)氧化10分鐘即可得到致密性好、孔隙率較低、耐蝕性較好的化學(xué)轉(zhuǎn)化膜層,H2O2在生產(chǎn)中具有重要作用,其羥基離子可以催化鈰氫氧化物/氧化物的沉積。
YU等在LY12鋁合金表面制備了雙層含鈰轉(zhuǎn)化膜,并通過(guò)電化學(xué)阻抗譜檢測(cè)轉(zhuǎn)化膜層的耐蝕性。結(jié)果表明:該膜層降低了腐蝕的驅(qū)動(dòng)力,增強(qiáng)了鋁合金的耐蝕性。膜層由不同尺寸的球形顆粒層組成,并且逐漸生長(zhǎng)、覆蓋鋁合金表面,該膜層是無(wú)定形膜層,主要由氧化鈰(Ⅲ和Ⅳ)和氫氧化鈰(Ⅲ和Ⅳ)組成。
06 高錳酸鹽體系化學(xué)氧化
鋁合金在高錳酸鹽溶液中經(jīng)適當(dāng)處理可形成具有一定耐腐蝕能力的轉(zhuǎn)化膜。
KULINICH等在含有KMnO4和Na2B4O7的化學(xué)轉(zhuǎn)化液中制備了2024-T3鋁合金高錳酸鹽轉(zhuǎn)化膜,研究了時(shí)間和溫度對(duì)高錳酸鹽轉(zhuǎn)化膜的生長(zhǎng)影響。結(jié)果發(fā)現(xiàn):室溫下浸泡1~5分鐘時(shí),僅在第二相金屬間化合物之間形成MnO2沉積物,但浸泡5~10分鐘后,膜層開(kāi)始在鋁基體表面上發(fā)展,然后緩慢形成,并在約15分鐘后停止。提高溫度會(huì)使膜層的沉積速度加快,例如68 ℃時(shí),約3分鐘后反應(yīng)就已停止了。
YOGANANDAN等使用含有Mn/Mo的堿性化學(xué)氧化液,在2024鋁合金(2024包鋁和非包鋁)上制備了高錳酸鹽的轉(zhuǎn)化膜(PCC)。結(jié)果發(fā)現(xiàn):轉(zhuǎn)化膜層在2024包鋁和非包鋁表面的形態(tài)分別表現(xiàn)為光滑和泥裂,非包鋁上轉(zhuǎn)化膜的過(guò)快沉積可能是導(dǎo)致其開(kāi)裂的原因。兩個(gè)膜層表面上均存在MnxOy(Mn3O4和Mn2O3),MnO2,KMnO4,MoOx(MoO2,MoO3)以及多鉬酸鹽的化合物,但非包鋁上轉(zhuǎn)化膜中含有更多的Mn(質(zhì)量分?jǐn)?shù)5%~6%)和Mo(質(zhì)量分?jǐn)?shù)0.3%)。此外,包鋁樣品比非包鋁樣品具有更好的耐腐蝕性能。
07 三價(jià)鉻體系化學(xué)氧化
近年來(lái),三價(jià)鉻化學(xué)轉(zhuǎn)化膜已被用作六價(jià)鉻鹽化學(xué)轉(zhuǎn)化膜的替代品。三價(jià)鉻轉(zhuǎn)化膜是由納米顆粒組成的致密層,其具有兩層結(jié)構(gòu),外層為鋯-鉻混合氧化物,內(nèi)層為氧化鋁或氟氧化物。三價(jià)鉻化學(xué)轉(zhuǎn)化膜厚度一般為40~120 nm,比不含鉻的鋯基化學(xué)轉(zhuǎn)化膜厚得多,該膜層通過(guò)充當(dāng)保護(hù)性阻擋層來(lái)抑制鋁合金表面的氧化還原反應(yīng),從而給2024-T3鋁合金提供腐蝕保護(hù)。
VIROULAUD等通過(guò)X射線光電子能譜(XPS)、飛行時(shí)間二次離子質(zhì)譜(ToF-SIMS)研究了表面預(yù)處理(脫脂和酸洗)對(duì)純鋁和2024-T3鋁合金上三價(jià)鉻化學(xué)轉(zhuǎn)化膜的影響。結(jié)果發(fā)現(xiàn):脫脂預(yù)處理降低了兩種基材上的氧化物厚度,使銅在2024-T3鋁合金表面富集,在Al-Cu金屬間化合物頂部形成更多銅聚集物顆粒。酸洗預(yù)處理也大大降低了原生氧化物厚度,使純鋁和2024鋁合金表面產(chǎn)生氟化鋁,鋁合金表面與金屬銅同質(zhì)富集。拋光或脫脂后鋁合金表面形成的三價(jià)鉻轉(zhuǎn)化膜厚度為50~80 nm,添加酸洗預(yù)處理后形成的三價(jià)鉻轉(zhuǎn)化膜更厚(厚度為100 nm)且不連續(xù),說(shuō)明酸洗預(yù)處理會(huì)導(dǎo)致膜層生長(zhǎng)過(guò)快,鋁氧氟化物的存在會(huì)導(dǎo)致鋁合金表面形成更易于開(kāi)裂的三價(jià)鉻轉(zhuǎn)化膜。
CHEN等發(fā)現(xiàn)化學(xué)氧化液中硫酸鉻的含量變化對(duì)三價(jià)鉻轉(zhuǎn)化膜的微觀結(jié)構(gòu)和耐蝕性有很大影響。含有鉻氧化物或氫氧化物的膜層比沒(méi)有鉻氧化物的膜層具有更薄和更致密的結(jié)構(gòu)。當(dāng)硫酸鉻濃度為0.01 mol/L時(shí),鋁基體發(fā)生均勻腐蝕,三價(jià)鉻轉(zhuǎn)化膜表現(xiàn)出最優(yōu)異的耐蝕性。
此外,研究發(fā)現(xiàn)在0.01 mol/L Cr(III)溶液中氧化處理5分鐘得到的轉(zhuǎn)化膜是光滑和連續(xù)的,但是當(dāng)氧化時(shí)間延長(zhǎng)至10分鐘時(shí),膜層表面會(huì)產(chǎn)生許多明顯的裂縫。所以CHEN等還研究了化學(xué)氧化時(shí)間對(duì)5052鋁合金上Cr(III)轉(zhuǎn)化膜形成的影響。SEM和TEM分析結(jié)果表明:膜層生長(zhǎng)時(shí)間主要為30~300秒,在浸泡時(shí)間300秒內(nèi)形成的膜層具有均勻的結(jié)構(gòu),當(dāng)浸泡時(shí)間延長(zhǎng)到600秒時(shí),膜層表面會(huì)產(chǎn)生許多明顯的裂縫。因?yàn)樵谀愚D(zhuǎn)化期間,溶解和沉積反應(yīng)同時(shí)進(jìn)行,溶解反應(yīng)連續(xù)進(jìn)行,但是沉積反應(yīng)速率逐漸減慢,所以在膜層上產(chǎn)生大量裂縫。
單一的三價(jià)鉻化學(xué)轉(zhuǎn)化膜難以達(dá)到六價(jià)鉻化學(xué)轉(zhuǎn)化膜的耐蝕性,一般要在其氧化液中加入Ti、Zr等金屬形成性能更好的復(fù)合膜。
YU等通過(guò)使用硫酸鉻和硫酸氧鈦(IV)在6063鋁合金上制備三價(jià)鉻-鈦(Cr(III)-Ti)化學(xué)轉(zhuǎn)化膜,以改善其耐蝕性,并使用偏振曲線和電化學(xué)阻抗譜(EIS)研究不同硫酸氧鈦含量下形成的Cr(III)-Ti基轉(zhuǎn)化膜的電化學(xué)特性。極化曲線結(jié)果表明:在2.5~4.5 g/L的硫酸氧鈦(IV)溶液中形成的Cr(III)-Ti基轉(zhuǎn)化膜比不含鈦的三價(jià)鉻化學(xué)轉(zhuǎn)化膜和鋁合金具有更好的耐蝕性。
STOICA等采用含有過(guò)氧化氫和鑭鹽的后處理液對(duì)沉積在2024-T3鋁合金上的三價(jià)鉻轉(zhuǎn)化膜(TCP)進(jìn)行處理。飛行時(shí)間二次離子質(zhì)譜和輝光放電-光發(fā)射光譜深度剖面顯示,后處理時(shí)間對(duì)TCP的厚度及其雙層結(jié)構(gòu)沒(méi)有影響,轉(zhuǎn)化膜由富含鋯和氧化鉻的外層和富含氧化鋁和氟氧化物的內(nèi)層組成。深度分析表明:鑭主要存在于TCP轉(zhuǎn)化膜的外部,其含量隨著后處理時(shí)間的延長(zhǎng)而增加。電化學(xué)阻抗測(cè)試結(jié)果表明,延長(zhǎng)后處理時(shí)間,能夠提高TCP轉(zhuǎn)化膜的耐蝕性。
08 結(jié)束語(yǔ)
鋁合金化學(xué)氧化發(fā)展至今,各種無(wú)六價(jià)鉻化學(xué)氧化技術(shù)已經(jīng)取得了長(zhǎng)足的發(fā)展。有些轉(zhuǎn)化膜如稀土金屬轉(zhuǎn)化膜、Ti-Zr基轉(zhuǎn)化膜的耐蝕性甚至接近于六價(jià)鉻化學(xué)轉(zhuǎn)化膜的耐蝕性。但由于化學(xué)氧化液的成本過(guò)高、化學(xué)氧化工藝復(fù)雜而且成膜效率較低,這些技術(shù)還難以應(yīng)用于實(shí)際生產(chǎn)。
三價(jià)鉻轉(zhuǎn)化膜更環(huán)保,其耐蝕性不弱于六價(jià)鉻轉(zhuǎn)化膜的耐蝕性,所以三價(jià)鉻化學(xué)氧化被認(rèn)為是最有希望替代六價(jià)鉻化學(xué)氧化的環(huán)保型化學(xué)氧化工藝。目前,世界各國(guó)都在積極開(kāi)展以三價(jià)鉻為體系的化學(xué)轉(zhuǎn)化液。美國(guó)海軍部門(mén)已研發(fā)出多代三價(jià)鉻化學(xué)轉(zhuǎn)化液,其氧化工藝已相當(dāng)成熟,在中性鹽霧試驗(yàn)中,三價(jià)鉻轉(zhuǎn)化膜最長(zhǎng)可以堅(jiān)持336小時(shí)以上。長(zhǎng)期以來(lái),我國(guó)在無(wú)六價(jià)鉻化學(xué)氧化方面一直受制于人,因此開(kāi)發(fā)耐蝕性優(yōu)異的環(huán)保鋁合金化學(xué)氧化工藝成為我國(guó)表面處理工作者急需解決的問(wèn)題。
免責(zé)聲明:本網(wǎng)站所轉(zhuǎn)載的文字、圖片與視頻資料版權(quán)歸原創(chuàng)作者所有,如果涉及侵權(quán),請(qǐng)第一時(shí)間聯(lián)系本網(wǎng)刪除。
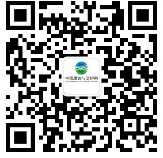
官方微信
《腐蝕與防護(hù)網(wǎng)電子期刊》征訂啟事
- 投稿聯(lián)系:編輯部
- 電話:010-62316606-806
- 郵箱:fsfhzy666@163.com
- 腐蝕與防護(hù)網(wǎng)官方QQ群:140808414