摘要
微弧氧化 (PEO) 涂層屬于陶瓷性涂層,表面不具有催化活性,需使用金屬Pd活化后,再進(jìn)行化學(xué)鍍鎳。為替代昂貴的Pd活化工藝,分別開發(fā)了Cu活化和Ag活化方法。利用場發(fā)射掃描電鏡對浸鍍后Cu/Ag活化復(fù)合涂層的鍍層表面和截面形貌觀察可見,Ag活化后PEO涂層表面鍍層更加均勻致密,且厚度更大。經(jīng)電化學(xué)測試表明,Ag活化復(fù)合涂層與傳統(tǒng)Pd活化復(fù)合涂層的耐蝕性能相近,且明顯優(yōu)于Cu活化復(fù)合涂層。因此,Ag活化方法在保證復(fù)合涂層的耐蝕性能的同時(shí),降低了活化成本。
關(guān)鍵詞: AZ91D鎂合金 ; Cu/Ag活化 ; 微弧氧化 ; 化學(xué)鍍 ; 復(fù)合涂層
鎂合金具有低密度、高的比強(qiáng)度、尺寸穩(wěn)定性好、優(yōu)良阻尼特性、導(dǎo)熱導(dǎo)電性能好等眾多優(yōu)點(diǎn),已成為裝備制造業(yè)輕量化發(fā)展的首選材料;而且,無論在儲量、特性、應(yīng)用范圍、循環(huán)利用以及節(jié)能環(huán)保等方面,鎂合金均展現(xiàn)出了其獨(dú)特的優(yōu)越性[1,2]。近些年,依靠上述優(yōu)點(diǎn)鎂合金在航空航天、汽車及電子通訊等領(lǐng)域的消耗量在快速增長,已成為最受關(guān)注的金屬材料之一[3,4]。然而,Mg的化學(xué)性質(zhì)活潑,有較大的腐蝕傾向,腐蝕過程中存在析氫反應(yīng),具有“一點(diǎn)擊破,全盤崩潰”的特點(diǎn),并且鎂合金表面生成的氧化膜疏松多孔,無法阻隔腐蝕介質(zhì)的滲入,嚴(yán)重地限制了鎂合金的應(yīng)用范圍[5,6]。為擴(kuò)大鎂合金的應(yīng)用范圍,通常采用制備防護(hù)涂層的方式來應(yīng)對鎂合金的腐蝕,目前主要的表面防護(hù)手段有化學(xué)鍍、陽極氧化、微弧氧化和化學(xué)轉(zhuǎn)化膜[7-10]。
鎂合金在航空航天電子設(shè)備和通訊設(shè)備等領(lǐng)域的應(yīng)用,對鎂合金防護(hù)涂層提出了一些功能性要求,而兼顧導(dǎo)電性、耐磨性和低磁性特征的化學(xué)鍍涂層最容易同時(shí)滿足工業(yè)界的要求。但是,在使用過程中,由于化學(xué)鍍層與鎂合金基體之間電勢差較大,且結(jié)合力較低,一旦鍍層部分區(qū)域發(fā)生磨損脫落,鎂合金會受到嚴(yán)重的電偶腐蝕[9,11]。為解決化學(xué)鍍層電偶腐蝕風(fēng)險(xiǎn)高和附著力較差的問題,可采用微弧氧化 (PEO) 涂層作為基體與化學(xué)鍍層的中間物理阻隔層,構(gòu)造化學(xué)鍍復(fù)合涂層。然而,化學(xué)鍍層必須沉積在具有催化活性的材料表面上,PEO涂層是陶瓷性涂層,其表面不具有催化活性,需進(jìn)行活化處理,在涂層表面形成具有催化活性的位點(diǎn),誘導(dǎo)鍍液中鎳離子的沉積[12]。
PEO涂層的傳統(tǒng)活化方法為金屬Pd活化,但是鈀成本較高,不適合大規(guī)模使用[13]。近期研究顯示,相關(guān)學(xué)者采用混合酸活化、TiB2環(huán)氧活化等方法來代替Pd活化法,但是混合酸活化法采用HF和H3PO4對PEO涂層進(jìn)行處理,極大地?fù)p害了PEO涂層的完整性,而TiB2環(huán)氧活化法引入了新的中間環(huán)氧層,導(dǎo)致鍍層結(jié)合力下降[14]。因此,現(xiàn)階段亟需開發(fā)一種價(jià)格低廉、不損傷PEO涂層、結(jié)合力較高且活化效果好的PEO涂層活化方法。
為此,本研究嘗試性開發(fā)了PEO涂層Cu活化方法和Ag活化方法。同時(shí),通過電化學(xué)測試方法,探究了兩種方法誘導(dǎo)沉積的鍍層相對于傳統(tǒng)金屬Pd活化法誘導(dǎo)沉積的鍍層在耐蝕性能方面的表現(xiàn)。
1 實(shí)驗(yàn)方法
本文所用的材料為商用鑄態(tài)AZ91D鎂合金,其化學(xué)成分采用電感耦合等離子發(fā)射光譜法 (ICP-OES) 測得,成分 (質(zhì)量分?jǐn)?shù),%) 為:Fe 0.0014,Cu 0.0018,Mn 0.21,Al 9.23,Si 0.029,Zn 0.73,其他元素<0.05,Mg余量。
將AZ91D鎂合金切成20 mm×20 mm×5 mm的矩形試樣。依次用400#、600#、1000#的SiC砂紙打磨矩形試樣的表面,后用酒精沖洗試樣,冷風(fēng)吹干。
PEO涂層樣品制備:將打磨后的AZ91D鎂合金置于20.0 g/L Na2SiO4·9H2O、2.0 g/L NaOH和4.0 g/L KF·2H2O的堿性電解液中,在脈沖模式下進(jìn)行微弧氧化處理,處理時(shí)電壓為500 V、電流密度為2 A/dm2、占空比為30%,制備時(shí)間20~30 min。
PEO-Cu/Ag/Pd涂層樣品制備過程為:(1) Cu分步活化,先將PEO涂層試樣置于10 g/的CuSO4·5H2O溶液中進(jìn)行敏化處理 (30 ℃,15~20 min),隨后在去離子水中浸洗,最后在10.0 g/L NaBH4和2.0 g/L NaOH的溶液中進(jìn)行活化 (50 ℃,10~20 min);(2) Ag分步活化,先將PEO涂層試樣置于2.0 g/L的AgNO3溶液中進(jìn)行敏化處理 (25 ℃,30~60 s),隨后在去離子水中浸洗,最后在10.0 g/L NaBH4和2.0 g/L NaOH的溶液中進(jìn)行活化 (28 ℃,30~60 s);(3) Pd分步活化,先將PEO涂層試樣置于1 g/L PdCl2和1 g/L α-吡啶胺混合溶液中進(jìn)行敏化處理 (25 ℃,30~60 s),隨后在去離子水中浸洗,最后在30 g/L的NaH2PO2溶液中進(jìn)行活化 (28 ℃,30~60 s)[15]。
將活化后的PEO-Cu/Ag/Pd涂層樣品浸入堿性預(yù)鍍液中進(jìn)行預(yù)鍍處理,去離子水沖洗,隨后浸入酸性化學(xué)鍍液中進(jìn)行化學(xué)鍍處理,最終得到PEO-Cu/Ag/Pd-EN復(fù)合涂層,強(qiáng)鍍液的成分 (g/L) 為:NiSO4·6H2O 20.0~30.0,NaH2PO2·H2O 30.0~50.0,Na3C6H5O7·2H2O 20.0~30.0,Na2CO3 20.0~35.0,NH4HF 9.0~14.0 pH 8.8~9.2,60 ℃,15~20 min,鍍液的成分 (g/L) 為:NiSO4·6H2O 20.0~25.0,NaH2PO2·H2O 20.0~35.0,Na3C6H5O7·2H2O 20.0~40.0,CH3COONa·3H2O 20.0~30.0,NH4HF 9.0~15.0,C18H29NaO3S 0.01~0.15,pH 4.8~5.2,80 ℃, 80~120 min。
利用XL-30FG場發(fā)射掃描電鏡 (FE-SEM) 和X射線能譜儀 (EDS) 對涂層的微觀形貌、元素分布及組成進(jìn)行分析。利用PW1700配備銅靶的X射線衍射儀 (XRD) 對涂層相組成進(jìn)行分析,參數(shù)設(shè)置為:λ=0.15406 nm,30 mA,40 kV,掃描角度為10°~80°,掃描速度4°/min。
利用X射線光電子能譜儀 (XPS,Thermo Fisher Scientific) 對樣品的成分進(jìn)行分析,射線源為Al-Ka (1486.6 eV) 射線,施加電流為1 μA,電壓為1 kV,測試面積為300 μm×700 μm。
利用Zahner電化學(xué)工作站,在 (30±1) ℃的3.5%(質(zhì)量分?jǐn)?shù)) NaCl溶液中對試樣進(jìn)行動電位極化和電化學(xué)阻抗測試。測試采用三電極體系,其中對電極為鉑電極,參比電極為飽和甘汞電極 (SCE),試樣為工作電極。
測試時(shí)陰、陽極極化曲線分開進(jìn)行測量。待測樣品在3.5%NaCl溶液中浸泡15 min,待開路電位 (OCP) 穩(wěn)定后,進(jìn)行動電位極化曲線測試,陰極極化測試由OCP開始掃描至相對開路電位-300 mV,陽極極化測試由OCP開始掃描至電流密度達(dá)到1 mA/cm2即停止,掃描速率為0.333 mV/s。電化學(xué)阻抗譜測試的頻率范圍為105~10-2 Hz,擾動幅度為10 mV。為保證測試的準(zhǔn)確性,每組實(shí)驗(yàn)至少重復(fù)3次。
鹽霧實(shí)驗(yàn)參照ASTM B117-03標(biāo)準(zhǔn)進(jìn)行,實(shí)驗(yàn)過程中鹽霧試驗(yàn)箱采用連續(xù)噴霧模式,噴霧溶液為5% (質(zhì)量分?jǐn)?shù)) NaCl溶液,溶液pH為6.5~7.2,箱內(nèi)溫度設(shè)置為 (35±2) ℃,經(jīng)24 h噴霧后,80 cm2水平面積的收集器中的鹽霧沉降速度為1.0~2.0 ml/h。測試過程中試樣待測表面與垂直方向成15°~30°,每種樣品放置3個(gè)平行樣,并使用相機(jī)記錄腐蝕過程中的宏觀形貌。
2 結(jié)果與討論
2.1 PEO涂層活化后表面的微觀結(jié)構(gòu)與成分
2.1.1 微觀形貌與EDS分析結(jié)果
圖1為PEO涂層的表面宏觀形貌和SEM形貌。PEO涂層宏觀表面呈灰白色,SEM圖像顯示涂層表面存在大量的微孔,微孔呈典型的“火山口”微觀結(jié)構(gòu),尺寸在0.5 μm至10 μm之間。“火山口”狀微孔的形成可能是微弧氧化過程中的火花放電以及表面氣泡排出導(dǎo)致。利用SEM對PEO涂層的截面進(jìn)行觀察發(fā)現(xiàn),部分微孔縱向貫穿了PEO涂層 (圖1d),而這些微孔為腐蝕介質(zhì)穿透涂層進(jìn)入基體提供了通道,使PEO涂層部分區(qū)域喪失了對基體的防護(hù)作用。
圖1 PEO涂層的宏觀形貌,表面SEM像和截面SEM像
圖2顯示了PEO涂層進(jìn)行Cu敏化和Cu活化處理后的表面宏觀形貌和SEM形貌。PEO涂層經(jīng)過硫酸銅溶液敏化處理后,涂層由灰白色轉(zhuǎn)變?yōu)榈{(lán)色 (圖2a)。利用SEM觀察表面可見,PEO涂層表面生成了大量棒狀的顆粒,長度在1~2 μm之間,除PEO孔隙外其他區(qū)域幾乎被棒狀的顆粒完全覆蓋 (圖2b,c)。
圖2 Cu敏化和Cu活化處理后PEO涂層的表面宏觀形貌和SEM像
利用EDS對PEO涂層表面的元素和棒狀顆粒組成分析表明 (表1),PEO涂層主要成分包括O、Mg、Al、Si,而硫酸銅敏化液處理后的PEO涂層中除O、Mg、Al、Si外,還含有Cu和S。利用EDS對棒狀物質(zhì) (點(diǎn)A) 進(jìn)行點(diǎn)分析可見,PEO涂層表面生成的棒狀顆粒主要由Cu和S構(gòu)成。
表1 EDS分析結(jié)果
圖2d為Cu活化處理后PEO-Cu涂層的表面宏觀形貌,經(jīng)Cu活化處理后,涂層由淡藍(lán)色轉(zhuǎn)變?yōu)榉奂t色。SEM觀察可見,PEO-Cu涂層表面的棒狀顆粒消失,生成了大量尺寸不均勻的球狀顆粒,且直徑大多不超過1 μm (圖2e,f)。利用EDS對球狀物質(zhì) (點(diǎn)B) 進(jìn)行點(diǎn)分析可見,涂層經(jīng)Cu活化處理后表面生成的球狀顆粒含38.20%Cu。利用EDS對Cu活化后涂層的元素分布進(jìn)行分析,結(jié)果如圖3所示。PEO-Cu涂層主要由O、Mg、Al、Si和Cu組成,且Cu集中分布于球狀顆粒處,這與EDS點(diǎn)分析結(jié)果一致 (表1)。
圖3 經(jīng)Cu活化處理后PEO涂層表面主要元素分布圖
圖4為PEO涂層Ag敏化和Ag活化處理后的表面宏觀形貌和SEM像。經(jīng)過Ag敏化處理后,PEO涂層樣品表面宏觀顏色沒有發(fā)生明顯變化。SEM觀察發(fā)現(xiàn),PEO涂層表面也生成了大量棒狀的顆粒,長度約為1 μm,但是由于Ag敏化處理時(shí)間相對Cu敏化較短,表面棒狀顆粒的密度較Cu敏化后更小。利用EDS對棒狀顆粒 (點(diǎn)C) 的元素組成進(jìn)行點(diǎn)分析發(fā)現(xiàn),棒狀顆粒除含有O、Mg、Al、Si外,還含有6.99%Ag (表1)。
圖4 Ag敏化和Ag活化處理后PEO涂層的表面宏觀形貌和SEM像
圖4d為Ag活化處理后PEO-Ag涂層的表面宏觀形貌,經(jīng)Ag活化處理后,涂層由灰白色轉(zhuǎn)變?yōu)榘迭S色。SEM觀察表明,PEO-Ag涂層表面的棒狀顆粒消失,生成了亞微米級球狀顆粒 (圖4e,f)。利用EDS對球狀物質(zhì) (點(diǎn)D) 進(jìn)行點(diǎn)分析表明,其含Ag為9.50 %。利用EDS對Ag活化后涂層的元素分布進(jìn)行分析,結(jié)果如圖5所示。PEO-Ag涂層主要由O、Mg、Al、Si和Ag組成,且Ag集中分布于亞微米級球狀顆粒處,這與EDS點(diǎn)分析的結(jié)果一致。
圖5 Ag活化處理后PEO涂層表面主要元素分布圖
經(jīng)對比發(fā)現(xiàn)Cu活化處理后的PEO涂層表面Cu含量 (6.70 %) 較高,而Ag活化處理后PEO涂層表面Ag含量 (1.72%) 略低,這歸因于Ag敏化處理時(shí)間較短,以避免處理過程中Ag+發(fā)生置換反應(yīng)。
2.1.2 XRD測試結(jié)果
利用XRD對PEO涂層和Cu/Ag活化處理后的涂層表面進(jìn)行物相分析,結(jié)果如圖6所示。PEO涂層主要由MgO與Mg2SiO4構(gòu)成,由于PEO涂層的多孔結(jié)構(gòu)以及存在的通孔,X射線可穿透膜層到達(dá)基體,XRD譜線中可觀察到大量的鎂基體的特征峰[16]。經(jīng)Cu活化處理后,PEO的XRD譜線中出現(xiàn)單質(zhì)Cu的特征峰,結(jié)合EDS結(jié)果分析,PEO涂層表面生成的球狀顆粒應(yīng)主要為單質(zhì)Cu。經(jīng)Ag活化處理后,PEO涂層的XRD譜線上卻沒有發(fā)現(xiàn)Ag的特征峰,這主要?dú)w因于PEO膜層上Ag的含量較低,低于XRD儀器的靈敏度。
圖6 PEO涂層及不同活化處理后PEO涂層的XRD圖譜
2.1.3 XPS測試結(jié)果
為了進(jìn)一步確定Cu和Ag活化過程中PEO涂層表面Cu和Ag的價(jià)態(tài)變化,分別對Cu和Ag敏化處理和活化處理后的PEO涂層進(jìn)行XPS測試,利用XPS-Peak軟件對各峰進(jìn)行分析擬合,測試結(jié)果如圖7所示。經(jīng)CuSO4溶液敏化處理后,PEO涂層中Cu主要以Cu2+的形式存在 (圖7a),其中CuSO4為溶液中溶質(zhì)物理吸附于PEO涂層表面產(chǎn)生。由于敏化過程中,涂層中MgO會與H2O反應(yīng)生成OH-,因而溶液Cu2+與OH-結(jié)合生成了Cu(OH)2,反應(yīng)方程如式 (1, 2) 所示。圖7b為Cu敏化PEO涂層經(jīng)Cu活化處理后的XPS譜,結(jié)合XRD譜分析,932.4和952.45 eV兩處的較強(qiáng)峰應(yīng)為Cu單質(zhì),而953.70、943.00 和934.60 eV處的較弱峰為CuO,由于其含量較低,因而XRD測試時(shí)并未發(fā)現(xiàn)CuO。Cu活化處理后,PEO涂層表面的Cu2+被活化液中BH4-大量還原為Cu單質(zhì),其反應(yīng)方程如 式 (3) 所示。
圖7 經(jīng)過不同敏化/活化處理后,PEO涂層的XPS圖譜
圖7c為PEO涂層在AgNO3溶液中進(jìn)行Ag敏化處理后的XPS圖譜,經(jīng)AgNO3溶液敏化處理后,PEO涂層表面出現(xiàn)大量Ag2O。在Ag敏化過程中,涂層中MgO和H2O反應(yīng)生成的OH-與Ag+結(jié)合生產(chǎn)Ag(OH)2,Ag(OH)2隨后水解產(chǎn)生Ag2O,反應(yīng)方程如式 (1)、(4) 和 (5) 所示。圖7d為Ag敏化PEO涂層經(jīng)Ag活化處理后的XPS測試結(jié)果,涂層表面的一價(jià)Ag被BH4-還原為Ag單質(zhì),如 式 (6) 所示。
2.2 不同活化方法對后續(xù)化學(xué)鍍層生長過程的影響
為探究不同活化方法對后續(xù)化學(xué)鍍鎳涂層生長過程的影響,分別對Cu活化處理、Ag活化處理和Pd活化處理后的PEO涂層進(jìn)行化學(xué)鍍鎳處理,利用SEM對不同浸鍍時(shí)間 (3、10和30 min) 的鍍層表面形貌和浸鍍30 min的鍍層截面形貌進(jìn)行了觀察。
如圖8所示,浸鍍3 min后,Cu活化處理的涂層表面生成了許多花椰菜狀結(jié)節(jié),結(jié)節(jié)分布不均且大小不一,未能覆蓋整個(gè)表面。然而,經(jīng)Ag活化處理和Pd-活化處理的涂層浸鍍3 min后,除孔洞處未被覆蓋,剩余位置被均勻細(xì)小的結(jié)節(jié)覆蓋。浸鍍10 min后,Cu活化處理的涂層表面結(jié)節(jié)直徑增大,但結(jié)節(jié)的直徑依然相差較大,同時(shí)有少量區(qū)域未被結(jié)節(jié)覆蓋。此時(shí),Ag活化處理和Pd活化處理的涂層表面被鍍層完全覆蓋,PEO涂層表面的孔洞被完全填充,結(jié)節(jié)直徑明顯增大,但結(jié)節(jié)之間存在縫隙。在化學(xué)鍍30 min后,3種活化方法處理的涂層表面結(jié)節(jié)直徑進(jìn)一步增大,且結(jié)節(jié)之間縫隙消失。但是,通過觀察浸鍍30 min鍍層的截面SEM圖發(fā)現(xiàn),Cu活化處理后涂層表面的鍍層較薄 (3 μm) 且不均勻,且未能完全填充PEO涂層孔隙。而Ag活化處理和Pd活化處理的涂層表面的鍍層厚度更厚 (5 μm左右),且更加致密均勻。因此,Ag活化處理后PEO涂層的表面活性和Pd活化處理處理后PEO涂層的表面活性相近,并優(yōu)于Cu活化處理后PEO涂層的表面活性,以Ag活化處理方法誘導(dǎo)沉積的化學(xué)鍍層結(jié)節(jié)均勻,致密性好。
圖8 Cu/Ag/Pd活化處理后浸鍍3、10和30 min后鍍層表面和浸鍍30 min后鍍層截面的SEM像
對Cu/Ag/Pd活化誘導(dǎo)沉積30 min的化學(xué)鍍復(fù)合涂層進(jìn)行XRD測試,結(jié)果如圖9所示。測試結(jié)果表明,3種復(fù)合涂層表面的鍍層均由Ni單質(zhì)組成,呈微晶或非晶的結(jié)構(gòu)。
圖9 PEO-Cu-EN、PEO-Ag-EN和PEO-Pd-EN復(fù)合涂層的XRD圖譜
2.3 不同活化方法對化學(xué)鍍復(fù)合涂層耐蝕性的影響
2.3.1 動電位極化測試
通過電化學(xué)測試方法,對比了AZ91D鎂合金和PEO-Cu-EN、PEO-Ag-EN、PEO-Pd-EN3種復(fù)合涂層在耐蝕性能方面的表現(xiàn)。圖10為鎂合金基體和三種復(fù)合涂層的動電位極化測試曲線。根據(jù)極化曲線可以得到膜層的自腐蝕電流密度 (Icorr)、自腐蝕電位 (Ecorr)。為避免鎂合金的負(fù)差數(shù)效應(yīng)帶來的誤差,Icorr的數(shù)值由極化曲線陰極部分Tafel外推法確定[17],表2匯總了極化曲線的擬合結(jié)果。與AZ91D鎂合金相比,PEO-Cu-EN、PEO-Ag-EN和PEO-Pd-EN復(fù)合涂層的自腐蝕電位有了顯著提升,自腐蝕電流密度也出現(xiàn)明顯下降,這表明化學(xué)鍍復(fù)合涂層提高了鎂合金的耐腐蝕性能。在3種復(fù)合涂層中,PEO-Cu-EN復(fù)合涂層的自腐蝕電流密度略高于PEO-Ag-EN和PEO-Pd-EN復(fù)合涂層,同時(shí),其自腐蝕電位又略低于PEO-Ag-EN和PEO-Pd-EN復(fù)合涂層,而PEO-Ag-EN和PEO-Pd-EN復(fù)合涂層的自腐蝕電位和自腐蝕電流密度相接近。因此,Ag活化得到的PEO-Ag-EN涂層耐蝕性能與傳統(tǒng)Pd活化得到的PEO-Pd-EN涂層耐蝕性相近,優(yōu)于Cu活化得到的PEO-Cu-EN涂層。
圖10 鎂合金及不同涂層的動電位極化測試曲線
表2 圖10中動電位極化曲線的擬合結(jié)果
2.3.2 電化學(xué)阻抗譜
圖11為AZ91D鎂合金和PEO-Cu-EN、PEO-Ag-EN、PEO-Pd-EN三種復(fù)合涂層的電化學(xué)阻抗譜。電化學(xué)阻抗數(shù)據(jù)采用如圖12所示的等效電路進(jìn)行擬合計(jì)算,擬合結(jié)果如表2所示。
圖11 鎂合金及不同涂層的電化學(xué)阻抗譜
圖12 擬合電化學(xué)阻抗譜的等效電路
當(dāng)交流電干擾信號的頻率無窮大和無窮小時(shí),阻抗與實(shí)軸的交點(diǎn)為極化電阻 (Rp),而其倒數(shù) (1/Rp) 與腐蝕速率成正比[18,19]。根據(jù)表3中的擬合結(jié)果,可利用公式 (7)、(8) 求得AZ91D鎂合金和PEO-Cu-EN、PEO-Ag-EN、PEO-Pd-EN三種復(fù)合涂層的極化電阻 (Rp)[20],得到1/Rp的遞減次序?yàn)椋篈Z91D (1.39×10-3 Ω-1·cm-2)>>PEO-Cu-EN (3.50×10-5 Ω-1·cm-2)>PEO-Pd-EN (2.12×10-5 Ω-1·cm-2)≈PEO-Ag-EN (2.05×10-5 Ω-1·cm-2)。因此,PEO-Pd-EN和PEO-Ag-EN復(fù)合涂層耐蝕性能相接近,并優(yōu)于PEO-Cu-EN復(fù)合涂層,這與極化曲線得到的結(jié)果一致。因此,使用Ag活化方法替代傳統(tǒng)Pd活化方法活化PEO涂層,可以在保證化學(xué)鍍復(fù)合涂層的耐蝕性能的同時(shí),降低了活化成本。
表3 電化學(xué)阻抗譜的擬合結(jié)果
2.3.3 中性鹽霧實(shí)驗(yàn)
利用中性鹽霧實(shí)驗(yàn)綜合評估了PEO-Cu-EN和PEO-Ag-EN兩種復(fù)合涂層的耐蝕性能,測試結(jié)果如圖13所示。經(jīng)鹽霧實(shí)驗(yàn)336 h后,PEO-Cu-EN涂層表面已出現(xiàn)黑色的腐蝕點(diǎn),并且可觀察到較為明顯的腐蝕產(chǎn)物堆積,而此時(shí)PEO-Ag-EN涂層表面仍未出現(xiàn)腐蝕點(diǎn)。在經(jīng)受鹽霧672 h后,PEO-Ag-EN涂層表面發(fā)生腐蝕,出現(xiàn)腐蝕產(chǎn)物堆積。結(jié)合中性鹽霧實(shí)驗(yàn)和前文中電化學(xué)測試的結(jié)果,可以得出PEO-Ag-EN復(fù)合涂層耐蝕性能優(yōu)于PEO-Cu-EN涂層
圖13 兩種涂層在中性鹽霧過程中的宏觀形貌
對Cu、Ag活化處理后涂層的表面形貌進(jìn)行SEM觀察表明,Cu活化處理后表面的含Cu球狀顆粒大小不一、且分布不均 (圖2和3),而Ag活化處理后表面的含Ag棒狀顆粒較為細(xì)小并分布均勻 (圖4和5);Cu、Ag活化處理后涂層表面的化學(xué)鍍層生長過程進(jìn)行觀察表明,Cu活化處理后表面生成的鍍層結(jié)節(jié)分布不均勻,結(jié)節(jié)直徑相差較大,浸鍍30 min后,仍未完全填充PEO涂層的孔隙,而Ag活化處理后表面生成了均勻致密的鍍層結(jié)節(jié),完整地覆蓋了PEO涂層 (圖8)。因此,經(jīng)Ag活化處理后,PEO涂層表面分布均勻、細(xì)小的含Ag棒狀顆粒可促進(jìn)鍍層均勻生長,形成了耐蝕性能更為優(yōu)異的化學(xué)鍍復(fù)合涂層。
3 結(jié)論
(1) 對不同浸鍍時(shí)間PEO-Cu/Ag/Pd涂層表面的鍍層形貌和浸鍍30 min后鍍層的厚度分析表明,Ag活化處理的PEO表面和傳統(tǒng)Pd活化處理的PEO表面活性相近,且均優(yōu)于Cu活化處理的PEO表面活性。
(2) PEO-Ag-EN復(fù)合涂層耐蝕性能優(yōu)于PEO-Cu-EN涂層,同時(shí)與PEO-Pd-EN涂層耐蝕性相近。因此,使用Ag活化處理替代傳統(tǒng)Pd活化處理PEO涂層,可以在保證鎂合金表面化學(xué)鍍復(fù)合涂層的耐蝕性能的同時(shí),降低了活化成本。
參考文獻(xiàn): 略
免責(zé)聲明:本網(wǎng)站所轉(zhuǎn)載的文字、圖片與視頻資料版權(quán)歸原創(chuàng)作者所有,如果涉及侵權(quán),請第一時(shí)間聯(lián)系本網(wǎng)刪除。
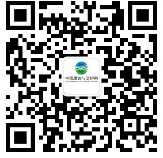
官方微信
《腐蝕與防護(hù)網(wǎng)電子期刊》征訂啟事
- 投稿聯(lián)系:編輯部
- 電話:010-62316606-806
- 郵箱:fsfhzy666@163.com
- 腐蝕與防護(hù)網(wǎng)官方QQ群:140808414